Текст книги "Информационная структура предприятия"
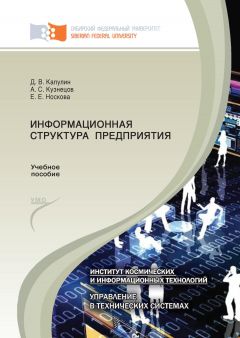
Автор книги: Александр Кузнецов
Жанр: Учебная литература, Детские книги
сообщить о неприемлемом содержимом
Текущая страница: 2 (всего у книги 12 страниц) [доступный отрывок для чтения: 3 страниц]
1.2. Информационные системы и уровни управления предприятием
Функционирование современных промышленных предприятий невозможно без технологий информационной поддержки производственных процессов, осуществляемых с помощью автоматизированных систем управления (АСУ). В классическом определении АСУ – это «совокупность экономико-математических методов, технических средств и организационных комплексов, обеспечивающих рациональное управление предприятием или технологическим процессом» [17].
Наиболее важная цель построения всякой АСУ – резкое повышение эффективности управления объектом (производственным, административным и т. д.) на основе роста производительности управленческого труда и совершенствования методов планирования и гибкого регулирования управляемого процесса. Разработка АСУ, порядок их создания и направления эффективного использования базируются на следующих принципах (впервые сформулированных В. М. Глушковым) [17]:
1. Принцип новых задач. АСУ должны обеспечивать решение качественно новых управленческих проблем, а не механизировать приемы управления, реализуемые неавтоматизированными методами. На практике это приводит к необходимости решения многовариантных оптимизационных задач на базе экономико-математических моделей большого объема (масштаба). Конкретный состав подобных задач зависит от характера управляемого объекта. Например, для машино– и приборостроительных предприятий обычно наиболее важными оказываются задачи оперативно-календарного и объемно-календарного планирования. Максимальный эффект достигается в том случае, когда осуществляется точное согласование во времени всех сменных заданий, как производственных, так и обеспечивающих (например, материально-техническое снабжение и др.), определяются оптимальные объемы партий продукции и производится оптимизация загрузки оборудования. В ряде случаев на первый план выдвигаются задачи подготовки производства, управления проектно-конструкторскими работами. На транспорте важнейшее значение приобретает оптимизация маршрутов и расписаний движения, а также погрузочно-разгрузочных работ. В системах управления отраслью первостепенное значение имеют оптимальное планирование работы предприятий, точное согласование сроков взаимных поставок, а также проблемы перспективного развития отрасли и задачи прогнозирования.
2. Принцип системного подхода. Проектирование АСУ должно основываться на системном анализе как объекта, так и процессов управления им. Это означает необходимость определения целей и критериев эффективности функционирования объекта (вместе с системой управления), анализа структуры процесса управления, вскрывающего весь комплекс вопросов, которые необходимо решить для того, чтобы проектируемая система наилучшим образом соответствовала установленным целям и критериям. Этот комплекс охватывает вопросы не только технического, но также экономического и организационного характера. Поэтому внедрение АСУ дает принципиально новые возможности для коренного усовершенствования системы экономических показателей и экономического стимулирования.
3. Принцип непрерывного развития системы. Основные идеи построения, структура и конкретные решения АСУ должны позволять относительно просто настраивать систему на решение задач, возникающих уже в процессе ее эксплуатации в результате подключения новых участков управляемого объекта, расширения и модернизации технических средств системы, ее информационно-математического обеспечения и т. д. Математическое обеспечение АСУ строится таким образом, чтобы в случае необходимости можно было легко менять не только отдельные программы, но и критерии, по которым ведется управление.
4. Принцип единства информационной базы. Необходимая информация накапливается (и постоянно обновляется) для решения не какой-то одной или нескольких задач, а всех задач управления. При этом в так называемых основных (генеральных) массивах исключается неоправданное дублирование информации, которое неизбежно возникает, если первичные информационные массивы создаются для каждой задачи отдельно. На уровне предприятий основные массивы должны содержать самую подробную информацию обо всех элементах производства: кадровые данные на всех работающих; сведения об основных фондах (земля, помещения, оборудование со всеми характеристиками, необходимыми для принятия решений по их использованию, перераспределению и т. п.); данные о запасах, включая запасы на промежуточных складах и незавершенное производство; информацию о состоянии оборудования; нормативы (трудовые и материальные) и технологические маршруты (последовательности производственных операций, необходимых для изготовления деталей, узлов и готовых изделий); планы (включая заявки на материально-техническое снабжение); цены и расценки; сведения о текущем состоянии банковских счетов предприятия и др. Система обработки первичных документов, а также система автоматических датчиков должны быть организованы таким образом, чтобы данные о любом изменении, происходящем на предприятии, в минимально короткий срок вводились, а затем автоматически или по указанию оператора периодически распределялись по основным массивам. При этом также необходимо сохранение состояния готовности системы выдать любую информацию об объекте.
5. Принцип комплексности задач и рабочих программ. Большинство процессов управления взаимосвязаны и поэтому не могут быть сведены к простому независимому набору отдельных задач. Например, задачи материально-технического снабжения органически связаны со всем комплексом задач оперативно-календарного и объемно-календарного планирования; задание на материально-техническое снабжение составляется исходя из задач планирования производства, а при срывах в снабжении (по срокам и по номенклатуре) возникает необходимость в трансформации планов.
Функциональный состав АСУ включает информационное, техническое, математическое, программное, организационное обеспечение.
В настоящее время в мировой практике для обозначения АСУ, используемых предприятиями, применяют следующие названия [16]:
• MRP (Material Requirement Planning) – планирование материальных потребностей;
• MRP II (Manufacturing Resource Planning) – планирование производственных ресурсов;
• ERP-система (Enterprise Resource Planning) – планирование ресурсов предприятия;
• ERP II и CSRP (Customer Synchronized Relationship Planning) – планирование ресурсов, синхронизированное с потребителем продукции;
• APS (Advanced Planning & Scheduling) – концепция синхронного производственного планирования (оптимальное календарное планирование).
Какая-либо однозначная и общепринятая общая классификация информационных технологий предприятий отсутствует. Возможный вариант обобщенной структуры современных информационных технологий, внедряемых на промышленных производствах различного типа, показан на рис. 1.3, на котором приведены следующие общепринятые сокращения (часть из них представлена выше) [16]:
• MES (Manufacturing Execution System) – производственная исполнительная система;
• САПР – системы автоматизированного проектирования / изготовления (Computer Aided Design/Computer Aided Manufacturing – CAD/CAM);
• АСТПП – автоматизированные системы технологической подготовки производства (Computer Aided Engineering – CAE);
• АСУТП – автоматизированные системы управления технологическими процессами (Supervisory Control And Data Acquisition – SCADA);
• АСУП – комплексная автоматизированная система управления предприятием (Enterprise Resource Planning – ERP);
• LAN – локальные вычислительные сети (Local Area Net);
• WAN – глобальные (внешние) сети и телекоммуникации (Wide Area Net).
Системы классов ERP, APS и MES являются общепризнанными решениями в области управления производством. При построении системы автоматизации процессов управления предприятием должны быть идентифицированы и проанализированы проблемы и задачи, подлежащие автоматизации. С точки зрения внедрения информационных систем все предприятия можно разделить на два больших класса: с дискретным типом производства (дискретное производство) и с непрерывным производством (непрерывное производство).
В отличие от систем классов ERP и APS, MES-системы являются предметно-ориентированными: для машиностроения, деревообработки, полиграфии и пр. Поэтому они максимально полно отражают особенности технологии конкретных производственных процессов и зачастую включают в себя развитые средства поддержки технологической подготовки того или иного типа производства. Очень часто MES-системы имеют средства интеграции с системами САПР технологических процессов и АСТПП.
Автоматизированные системы технологической подготовки производства начинают оказывать значительное влияние на организацию производства за счет повышения роли технологической подготовки производства. Задачи такой подготовки значительно расширяются в сторону технологических расчетов и моделирования технологических процессов, а их внедрение в непрерывное производство практически невозможно организовать без соответствующих расчетов и моделирования.

Рис. 1.3. Обобщенная структура информационных технологий предприятия
Внедрение MES на предприятии не только обеспечивает составление детальных производственных расписаний, но также положительно влияет на управление качеством и уровень обслуживания технологического оборудования. На рынке существуют решения как для систем с дискретным характером выпуска продукции, так и для производств с непрерывным характером. Наиболее сложными с точки зрения точности планирования и выполнимости планов следует считать системы первого вида, особенно с «позаказным» типом производства [18].
Наряду с системами ERP, APS и MES в контур управления производственными процессами входят автоматизированные системы управления технологическими процессами (АСУТП, HMI/SCADA), которые отвечают за функции контроля и выполнения технологических процессов. От эффективности SCADA-систем напрямую зависит эффективность производства.
Функции автоматизированных систем управления выполняются информационными системами на нескольких уровнях управления (рис. 1.4) [18]. При этом каждый уровень выполняет свою основную управленческую функцию:
• верхний уровень управления предприятием (административно-хозяйственный) решает стратегические задачи, а соответствующая ERP-система обеспечивает управление ресурсами в масштабе предприятия в целом, включая часть функций поддержки производства (долгосрочное планирование и стратегическое управление в масштабе: годовое, квартальное, месячное);
• средний уровень управления (производственный) решает задачи оперативного управления процессом производства, а соответствующая автоматизированная система обеспечивает эффективное использование ресурсов (сырья, энергоносителей, производственных средств, персонала), а также оптимальное исполнение плановых заданий (сменное, суточное, декадное, месячное) на уровне участка, цеха, предприятия;
• низшие уровни технологического управления решают классические задачи управления технологическими процессами.
Каждый уровень управления характеризуется своей интенсивностью циркулирующей информации, масштабом времени и набором функций [18]. Контур управления уровня технологических процессов является самым интенсивным по объему информации и самым жестким по времени реакции, которое может составлять секунды и даже миллисекунды. В верхнем уровне слоя АСУТП – в SCADA-системах – происходит накопление и обработка большого числа технологических параметров и создается информационная база исходных данных для MES-уровня.
Контур управления уровня MES (оперативно-производственный) опирается на отфильтрованную и обработанную информацию, поступающую как от АСУТП, так и от других служб производства. Интенсивность информационных потоков здесь существенно ниже и связана с задачами оптимизации заданных производственных показателей. Типовое время циклов управления – минуты, часы, смены, сутки. Оперативное управление производством в этом контуре управления осуществляется специалистами, которые более детально, чем высший менеджмент, владеют производственной ситуацией.

Рис. 1.4. Уровни управления
В этом случае контур управления уровня ERP (стратегический) освобождается от решения оперативных задач производства и обеспечивает поддержку бизнес-процессов предприятия в целом. Поток информации от производственного блока становится минимальным и включает в себя агрегированную управляющую и отчетную информацию по стандартам ERP с типовым временем контроля (декада, месяц, квартал), а также аварийные сигналы, требующие немедленного вмешательства высшего менеджмента предприятия.
Однако прежде чем запустить производство в «автоматическом» режиме работы, необходимо синтезировать управляющие программы для технологического оборудования, которые в свою очередь должны быть получены как результат конструкторского проектирования. Для оперативного внесения конструкторско-технологических изменений с целью корректировки производственных планов при смене стратегий производства или позиционирования продукции в состав контура управления производственным предприятием (уровня MES) должно быть включено взаимодействие с информационной системой поддержки процесса проектирования – интегрированной САПР (CAE/CAD/CAM-системой). Таким образом, на оперативно-производственный уровень управления должна поступать информация с конструкторского и технологического этапов проектирования, содержащаяся в CAE/CAD/CAM-системах.
Из изложенного очевидно, что информационными системами, определяющими информационную структуру предприятия как взаимодействие трех основных уровней управления, являются ERP-, MES– и SCADA-системы.
Приведем основные функции MES-систем [20, 21]:
1. RAS (Resource Allocation and Status) – контроль состояния и распределение ресурсов. Управление ресурсами: технологическим оборудованием, материалами, персоналом, обучением персонала, а также другими объектами, такими как документы, которые должны быть в наличии для начала производственной деятельности. Обеспечивает детальную историю ресурсов и гарантирует, что оборудование соответствующим образом подготовлено для работы. Контролирует состояние ресурсов в реальном времени. Управление ресурсами включает резервирование и диспетчеризацию для достижения целей оперативного планирования.
2. ODS (Operations/Detail Scheduling) – оперативное/детальное планирование. Обеспечивает упорядочивание производственных заданий, основанное на очередности, атрибутах, характеристиках и рецептах, связанных со спецификой изделий, таких как форма, цвет, последовательность операций и др., и технологии производства. Цель – составить производственное расписание с минимальными перенастройками оборудования и параллельной работой производственных мощностей для уменьшения времени получения готового продукта и времени простоя.
3. DPU (Dispatching Production Units) – диспетчеризация производства. Управляет потоком единиц продукции в виде заданий, заказов, серий, партий и заказ-нарядов. Диспетчерская информация представляется в той последовательности, в которой работа должна быть выполнена, и изменяется в реальном времени по мере возникновения событий на цеховом уровне. Это дает возможность изменения заданного календарного плана на уровне производственных цехов. Включает функции устранения брака и переработки отходов наряду с возможностью контроля трудозатрат в каждой точке процесса с буферизацией данных.
4. DOC (Document Control) – управление документами. Контролирует содержание и прохождение документов, которые должны сопровождать выпускаемое изделие, включая инструкции и нормативы работ, способы выполнения, чертежи, процедуры стандартных операций, программы обработки деталей, записи партий продукции, сообщения о технических изменениях, передачу информации от смены к смене, а также обеспечивает возможность вести плановую и отчетную цеховую документацию. Кроме того, функция включает управление инструкциями по безопасности, регламентирующими документами (стандартами), контроль защиты окружающей среды и хранит историю прохождения и изменения документов.
5. DCA (Data Collection/Acquisition) – сбор и хранение данных, взаимодействие информационных подсистем в целях получения, накопления и передачи технологических и управляющих данных, циркулирующих в производственной среде предприятия. Функция обеспечивает интерфейс для получения данных и параметров технологических операций, которые используются в формах и документах, прикрепляемых к единице продукции. Данные могут быть получены с цехового уровня как вручную, так и автоматически от оборудования в требуемом масштабе времени.
6. LM (Labor Management) – управление персоналом. Обеспечивает получение информации о состоянии персонала и управление им в требуемом масштабе времени. Включает отчетность по присутствию и рабочему времени, отслеживание сертификации, возможность отслеживания такой непроизводственной деятельности, как подготовка материалов или инструментальные работы, в качестве основы для учета затрат по видам деятельности (Activity Based Costing, ABC). Возможно взаимодействие с функцией распределения ресурсов для формирования оптимальных заданий.
7. QM (Quality Management) – управление качеством. Обеспечивает анализ в реальном времени измеряемых показателей, полученных от производства, для гарантированно правильного управления качеством продукции и определения проблем, требующих вмешательства обслуживающего персонала. Данная функция формирует рекомендации по устранению проблем, определяет причины брака путем анализа взаимосвязи симптомов, действий персонала и результатов этих действий. Может также отслеживать выполнение процедур статистического управления процессом и статистического управления качеством продукции (SPC/SQC), а также управлять выполнением лабораторных исследований параметров продукции. Для этого в состав MES добавляются лабораторные информационно-управляющие системы (LIMS).
8. PM (Process Management) – управление производственными процессами. Отслеживает производственный процесс и корректирует автоматически либо обеспечивает поддержку принятия решений оператором для выполнения корректирующих действий и усовершенствования производственной деятельности. Эта деятельность может быть как внутриоперационной и направленной исключительно на отслеживаемые и управляемые машины и оборудование, так и межоперационной, отслеживающей ход процесса от одной операции к другой. Она может включать управление тревогами для обеспечения гарантированного уведомления персонала об изменениях в процессе, выходящих за приемлемые пределы устойчивости. Она обеспечивает взаимодействие между интеллектуальным оборудованием и MES, возможное благодаря функции сбора и хранения данных.
9. MM (Maintenance Management) – управление техобслуживанием и ремонтом. Отслеживает и управляет обслуживанием оборудования и инструментов. Обеспечивает их работоспособность. Обеспечивает планирование периодического и предупредительного ремонтов, ремонта по состоянию. Накапливает и хранит историю произошедших событий (отказы, уменьшение производительности и др.) для использования в диагностировании возникших и предупреждения возможных проблем.
10. PTG (Product Tracking and Genealogy) – отслеживание и генеалогия продукции. Обеспечивает возможность получения информации о состоянии и местоположении заказа в каждый момент времени. Информация о состоянии может включать данные о том, кто выполняет задачу, компонентах, материалах и их поставщиках, номере лота, серийном номере, текущих условиях производства, а также любых тревогах, сведения о повторных обработках и других событиях, относящихся к продукту. Функция отслеживания в реальном времени создает также архивную запись. Эта запись обеспечивает отслеживаемость компонентов и их использование в каждом конечном продукте.
11. PA (Performance Analysis) – анализ производительности. Обеспечивает формирование отчетов о фактических результатах производственной деятельности, сравнение их с историческими данными и ожидаемым коммерческим результатом. Результаты производственной деятельности включают такие показатели, как коэффициент использования ресурсов, доступность ресурсов, время цикла для единицы продукции, соответствие плану и соответствие стандартам функционирования. Может включать статистический контроль качества процессов и продукции (SPC/SQC). Систематизирует информацию, полученную от разных функций, измеряющих производственные параметры. Эти результаты могут быть подготовлены в форме отчета или представлены в реальном времени в виде текущей оценки эксплуатационных показателей.
Основными функциями MES-систем являются оперативно-календарное планирование и диспетчеризация. Именно они определяют MES-систему как систему оперативного характера, нацеленную на формирование расписаний работы оборудования и оперативное управление производственными процессами в цехе [2]. Одним из основных отличий MES-систем от каких-либо других систем управления производственными процессами является то, что в их основе лежат достаточно сложные и точные с точки зрения адекватности реалиям производственной среды математические модели планирования и диспетчеризации. При отыскании оптимальных и близких к ним решений используются методы многокритериальной оптимизации на Парето-множествах, что позволяет оперировать десятками различных частных критериев и ограничений, учитывать разнообразные производственные ситуации при построении расписаний работы оборудования. Алгоритмы, используемые в MES-системах, позволяют формировать расписания и пересчитывать их в контуре диспетчеризации за минимальное время (от 3 мин до 10 с для задач с размерностью в 2000–5000 операций и 150–200 ед. технологического оборудования) [2, 18].
Весьма привлекательными характеристиками большинства MES-систем являются их стоимость и сроки внедрения в производство, которые в ряде случаев на порядок меньше аналогичных характеристик ERP-систем.
Целью MES-систем является не только выполнение заданных верхним уровнем управления объемов производства, но и, главным образом, оптимизация расписаний работы оборудования, результаты которой позволяют более плотно загрузить технологическое и вспомогательное оборудование (с 40–45 до 80 %), в ряде случаев высвободить некоторые производственные единицы, уменьшить длительность и количество операций по переналадке, сократить объемы незавершенного производства на 30–40 %, сократить общую длительность производственного цикла на 10–15 %. В итоге главными результатами использования MES-систем являются увеличение пропускной способности производственной системы, ускорение оборачиваемости материальных средств и ресурсов, что соответствует одному из основных требований современного производства, характеризующегося мелкосерийным характером выпуска изделий в рамках динамично меняющегося рынка товаров.
На верхнем уровне управления предприятием управление ресурсами в масштабе предприятия обеспечивает ERP-система – интегрированная система класса MRP II с модулем финансового планирования (Finance Requirements Planning – FRP). По определению американского общества по управлению производством и запасами (American Production and Inventory Control Society – APICS) «ERP – это подход для организации, определения и стандартизации бизнес-процессов, необходимых, чтобы предприятие могло использовать внутренние знания для поиска внешнего преимущества».
В основе ERP-систем лежит принцип создания единого хранилища (репозитория) данных, содержащего всю корпоративную бизнес-информацию: плановую и финансовую информацию, производственные данные, данные по персоналу и др. [16]. Наличие единого корпоративного репозитория устраняет необходимость в передаче данных от одной системы к другой (например, от производственной системы к финансовой или к кадровой), а также обеспечивает одновременную доступность информации для любого числа сотрудников предприятия, обладающих соответствующими полномочиями. Целью ERP-систем является не только улучшение управления производственной деятельностью предприятия, но и уменьшение затрат и усилий на поддержку его внутренних информационных потоков.
В основе функционирования ERP-систем лежит стандарт управления промышленным предприятием MRP II, который прошел в своем становлении несколько этапов [1]. Методология MRP является реализацией двух известных принципов («Вовремя заказать» (Order In Time) и «Вовремя произвести» (Kanban)), объединенных в методологию «Вовремя выполнить» (Just In Time – JIT). Для работы MRP-модуля требуются следующие входные данные: данные о состоянии запасов (вся наличествующая номенклатура: запасы, незавершенное производство, полуфабрикаты, готовая продукция, спланированные заказы и заказы в ожидании отгрузки); спецификация изделия (Bill of Material – BOM).
Результатом работы MRP-модуля является график заказов на закупку/производство материалов и комплектующих (Planned Order Schedule) – документ, расписывающий, какое количество сырья, материалов, комплектующих должно быть заказано в каждый период в течение срока планирования. Этот документ определяет внутрипроизводственный план использования комплектующих и план внешних закупок. Изменения к графику заказов на закупку/производство материалов и комплектующих (Changes in Planned Orders) – документ, содержащий корректировки ранее спланированных заказов на закупку/производство материалов и комплектующих. С целью повышения эффективности планирования в MRP-системах была реализована идея воспроизведения замкнутого цикла (Closed Loop Material Requirement Planning), подразумевающая составление согласованной производственной программы и ее контроль на цеховом уровне [1].
Главной задачей MRP-систем является обеспечение наличия на складе и в производственных помещениях необходимого количества требуемых материалов (комплектующих) в любой момент времени в рамках срока планирования, что позволит уменьшить объем постоянных складских запасов за счет оптимизации процесса поставок.
В конце 70-х гг. ХХ в. методология MRP-систем с замкнутым циклом была трансформирована в систему планирования производственных ресурсов в масштабах предприятия (Manufactory Resource Planning), которая получила название MRP II. Этот стандарт был разработан в США и поддерживается APICS. В соответствии с MRP II Standard System, в информационной системе, реализованной на базе стандарта MRP II, должны быть реализованы следующие 16 групп функций [1]:
1. Планирование продаж и производства (Sales and Operation Planning).
2. Управление спросом (Demand Management).
3. Составление плана производства (Master Production Scheduling).
4. Планирование потребностей в материалах (Material Requirement Planning).
5. Спецификация продуктов (Bill of Materials).
6. Управление складом (Inventory Transaction Subsystem).
7. Плановые поставки (Scheduled Receipts Subsystem).
8. Управление на уровне производственного цеха (Shop Flow Control).
9. Планирование производственных мощностей (Capacity Requirement Planning).
10. Контроль входа/выхода (Input/Output Control).
11. Материально-техническое снабжение (Purchasing).
12. Планирование распределения ресурсов (Distribution Resource Planning).
13. Планирование и контроль производственных операций (Tooling Planning and Control).
14. Финансовое планирование (Financial Planning).
15. Моделирование (Simulation).
16. Оценка результатов деятельности (Performance Measurement).
Как правило, ERP-системы строятся по модульному принципу и в той или иной степени охватывают все ключевые процессы деятельности предприятия. Используемый в них программный инструментарий позволяет проводить производственное планирование, моделировать поток заказов и оценивать возможность их реализации в службах и подразделениях предприятия, увязывая его со сбытом.
Основные функции ERP-систем [16]:
• ведение конструкторских и технологических спецификаций, которые определяют состав производимых изделий, а также материальные ресурсы и операции, необходимые для их изготовления;
• формирование планов продаж и производства;
• планирование потребностей в материалах и комплектующих, сроков и объемов поставок для выполнения плана производства продукции;
• управление запасами и закупками: ведение договоров, реализация централизованных закупок, обеспечение учета и оптимизации складских и цеховых запасов;
• планирование производственных мощностей: от стратегии всего предприятия до планов использования отдельных станков и оборудования;
• оперативное управление финансами, включая составление финансового плана и осуществление контроля его исполнения, финансовый и управленческий учет;
• управление проектами, включая планирование этапов и ресурсов, необходимых для их реализации.
Позже в ERP-системы стали включать дополнительный модуль APS (Advanced Planning and Scheduling) – методику планирования, использующую методы математической оптимизации в составлении календарных планов, так как при решении даже простых по постановке задач дискретного планирования для распределенной дистрибьюторской сети обыкновенные алгоритмы становятся неработоспособными из-за большой размерности данных.
В конце 90-х гг. ХХ в. был разработана также методология «Планирование ресурсов предприятия, синхронизированное с запросами потребителя» (Customer Synchronized Resource Planning – CSRP), которая охватывает взаимодействие предприятия с клиентами: оформление заказ-наряда, техническое задание, поддержку клиентов, планирование ресурсов в зависимости от объема и состава клиентских заказов. Если стандарты MRP/MRP II/ ERP ориентированы на управление запасами и мощностями, планирование, производство и продажу продукта, то в CSRP включен полный цикл жизненного цикла изделия – от его проектирования с учетом требований заказчика до гарантийного и сервисного обслуживания после продажи.
Этот новый тип систем стали называть ERP II-системами, основа которых – управление взаимодействием предприятия с внешней средой. Там, где возможно, внутренние и конфиденциальные процессы становятся внешними и открытыми. Излишняя тайна корпоративной информации, которая усложняла деятельность, исчезает. На смену ей приходит четко регламентированная политика в сфере информационной безопасности и безопасности самих информационных систем.
Соединение ERP-системы с технологиями OLAP (Online Analytical Processing – аналитическая обработка в реальном времени), системой сбалансированных показателей (Balanced Score Card) и системой функционально-стоимостного управления привело к появлению и развитию систем BPM (Business Performance Management) – управление эффективностью бизнеса, которые позволяют связывать операционные результаты деятельности предприятия с эффективностью реализации миссии предприятия.
Правообладателям!
Данное произведение размещено по согласованию с ООО "ЛитРес" (20% исходного текста). Если размещение книги нарушает чьи-либо права, то сообщите об этом.Читателям!
Оплатили, но не знаете что делать дальше?