Текст книги "Практика цифровизации промышленности. Выпуск 1"
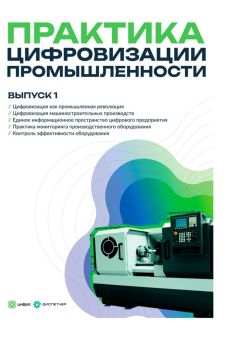
Автор книги: Денис Лямшев
Жанр: Компьютеры: прочее, Компьютеры
Возрастные ограничения: +12
сообщить о неприемлемом содержимом
Текущая страница: 2 (всего у книги 8 страниц)
Получать и обрабатывать большие массивы данных невозможно без современных технологий интернета вещей, больших данных и облачных вычислений. Следовательно, эффективная работа ИИ возможно только совместно с новыми технологиями.
Использование ИИ в промышленности накладывает на эту технологию соответствующую специфику. ИИ в первую очередь требуется использовать там, где надо решать относительно простые для человека задачи, но чрезвычайно сложные для традиционных логических алгоритмов. Например, распознавание образов, без чего невозможно создание промышленных роботов.
Уже сегодня промышленные компании используют технологии ИИ для прогнозирования обслуживания и ремонтов оборудования, контроля и прогнозирования качества изготовления продукции, оптимизация запасов и цепочек поставок.
Аналитика
Использовать потенциал больших данных возможно только представив их в доступной и простой для пользователя форме. Стоит задача преобразования Больших данных в «умные» данные (Smart data), чтобы оставить только полезную информацию, которую можно эффективно использовать для решения бизнес-задач. Для получения «умных» данных существуют различные способы, включая методы искусственного интеллекта.
Анализ и предоставление данных пользователю выполняется при помощи аналитических сервисов. Существует следующие виды аналитики:
– описательная аналитика, предоставляет отчеты с использованием различных данных;
– диагностическая аналитика, предоставляет пользователю информацию «почему что-то произошло»;
– предиктивная (предсказательная) аналитика, выполняет прогноз на основе анализа данных;
– предписывающая аналитика говорит, что требуется сделать.
Визуализация собранных и обработанных данных в виде аналитических отчетов осуществляется с помощью панелей управления, различных приложений, которыми пользуются работники управленческих звеньев предприятия.
Оборудование цифрового производства
Рассматривая оборудование цифрового производства, мы не заглядываем в фантастическое будущее, а говорим о сегодняшнем дне или недалеком завтра.
Оборудование цифрового производства – это высокоавтоматизированное оборудование, обладающее возможностью подключения к сети Интернет, развитыми межмашинным (М2М) и человеко-машинным (М2Н) интерфейсами. Оборудование обеспечивает высокую производительность и качество выпускаемой продукции, имеет низкое энергопотребление, высокую надежность.
Возможность интеграции оборудования с системами подготовки и управления производством, межмашинное взаимодействие позволяет реализовать автономный процесс управления производственными системами или децентрализованное управление, которое является частью концепции Индустрии 4.0.
На предприятиях организуется работа так называемых гибких производств (ГПС): от гибкого производственного модуля (ГПМ, рис. 6) до гибкого автоматизированного цеха (ГАЦ).
Гибкие системы позволяют организовать автономную работу и выпуск продукции в течение длительного периода в том числе по индивидуальным заказам. На управляющий компьютер ГПС приходят наряды на производство определенных деталей, автоматически на станки с ЧПУ передаются требуемые УП, загружается нужный инструмент, устанавливаются соответствующие заготовки.

Рис. 6. Гибкий производственный модуль
В цифровом производстве широко используются производственные роботы, в первую очередь коллаборативные (коботы), способные работать рядом с человеком. Это роботы-манипуляторы, которые, например, выполняют действия аналогичные функциям человеческой руки (рис. 7). Они заменят человека на однообразных простых операциях, а также на вредных и опасных участках. Это обслуживание станков, сварка, пайка, покраска, резка, сборка и разборка.

Рис. 7. Робот-манипулятор на станке с ЧПУ
Для перевозки деталей, заготовок, инструмента в цехах и на складских участках используются транспортные роботы, робототехнические тележки. На некоторых производствах возможно для транспортных задач использование и квадрокоптеров.
С использованием технологий Индустрии 4.0 эффективность использования роботов значительно возрастает, в частности за счет мониторинга их работы в реальном времени и сокращения время переналадки. При этом стоимость роботов уменьшается. За последние 30 лет средняя цена робота уменьшилась в 2 раза, а если сравнивать с ценой труда, то еще больше. Например, робот-манипулятор для станка с ЧПУ, как правило, не превышает 10% стоимости станка.
Широкое распространение цифровых технологий в области проектирования и механообработки стимулировало взрывной характер развития аддитивных технологий или технологий 3D-печати.
Аддитивные технологии – обобщенное название технологий, предполагающих изготовление изделия по данным цифровой модели (CAD-модели) методом послойного добавления. Получение изделия происходит послойно, шаг за шагом, путем формирования тем или иным способом слоя материала, отверждения или фиксации этого слоя в соответствии с конфигурацией сечения СAD-модели и соединения каждого последующего слоя с предыдущим.
В результате появилось оборудование нового класса (рис. 8).

Рис. 8. Аддитивное промышленное оборудование
3D-принтер или AM-машина (Additive Manufacturing) – станок с числовым программным управлением, использующий метод послойной печати детали.
Сегодня производятся различные типы и модели станков, использующих аддитивные технологии:
– дешевые 3D-принтеры, ориентированные на создание макетов и простых деталей из пластмассы;
– станки, предназначенные для создания прототипов деталей с различной степенью точности и/или функциональности;
– установки высокого класса для производства полимерных, металлических и керамических деталей.
Заменить на производстве все станки на современные в одночасье невозможно. Согласно опубликованным данным коэффициент обновления станочного парка даже в развитых странах не превышает 10% в год. В отличие от предыдущих промышленных революций, четвертая позволяет использовать устаревшее оборудование при сравнительно низких требованиях к его модернизации.
Человек в цифровом производстве
Существующие мнение, что компьютер и роботы скоро устранят людей из промышленного производства явно преувеличено.
Цифровое производство не тождественно повсеместному превращению цехов в полностью автоматизированные, фактически, безлюдные. Наряду с созданием безлюдных производств важнейшей целью цифровой трансформации является создание условия для активного участия человека в управлении производством. Это предусматривает непосредственную или косвенную вовлеченность человека в процессы, осуществляемые или обеспечиваемые при помощи цифровых рабочих мест.
В результате такой вовлеченности можно значительно увеличить эффективность использования работающего на предприятии оборудования, подключив его в локальную сеть предприятия и установив на рабочем месте дополнительное устройство человеко-машинного интерфейса (терминал, дисплей, пульт, панель) или подключив мобильное компьютерное средство (планшет, смартфон).
Образовавшееся при этом цифровое рабочее место (рис. 9 и 10) позволит за счет недорогой модернизации выполнять сбор данных о работе оборудования, передавать на станок по сети управляющие программы и другую технологическую информацию. Таким образом, старые станки можно встроить в структуру, где работает современное оборудование. Низкая производительность старых станков компенсируется высоким коэффициентом загрузки и низкими затратами на их эксплуатацию. Кроме того, получение достоверной информации о работе и простоях позволяет принимать решения о дальнейшей модернизации или замене оборудования.

Рис. 9. Цифровое рабочее место оператора

Рис. 10. Цифровое рабочее место монтажника
Как указано выше, участие человека в процессе управления оборудованием обеспечивает человеко-машинный интерфейс (ЧМИ или M2H) в виде различных компьютерных устройств. Цифровое производство основано в значительной степени на создании сети сбора и обработки данных реального времени. Полученные данные будут доступны дистанционно, а для некоторых производственных специалистов сами их «рабочие места» станут мобильными.
Несмотря на внедрение технологий Индустрии 4.0, включая реальное межмашинное взаимодействие, справиться с увеличивающейся сложностью управления оборудованием можно только под контролем квалифицированных специалистов.
Человек скорее заметит неполадку в работе автономно работающих систем, чем автоматизированные системы. Например, оператор станка или ГПС – это ключевая фигура самоорганизующегося производственного процесса, в котором именно оператор следит за корректностью выполнения работы на оборудовании.
На производстве цифровые рабочие места могут быть организованы для сборщиков, слесарей, работников ОТК и других специалистов, не эксплуатирующих оборудование и занятых, в основном, ручным или маломеханизированным трудом. На таких рабочих местах вместе с инструментом, оснасткой, компьютерным оборудованием используется программное обеспечение, с помощью которого сотрудники регистрируются, получают сменные задания, интерактивные инструкции по выполнению технологических операций и отчитываются по завершению заданий. С помощью данного ПО можно контролировать фактическое время работы по отдельным операциям и получать реальную фотографию рабочего дня сотрудников. На ряде рабочих мест могут эффективно использоваться технологии дополненной реальности.
Для обеспечения оптимального и бесперебойного управления производством собранные и обработанные данные нужно соответствующим образом интерпретировать, что может привести к необходимости корректировки процесса. Таким образом, при взаимодействии киберфизической производственной системы и человека как раз человек и выполняет функцию вышестоящей организации.
В результате четвертой промышленной революции многие профессии исчезнут, но возникнут новые, произойдет перераспределение работников внутри организаций. Это обусловливает необходимость своевременно модернизировать систему образования, инвестировать в профессиональную подготовку и непрерывное обучение, чтобы сформировать мобильную рабочую силу, способную воспользоваться новыми возможностями.
ЦИФРОВИЗАЦИЯ
МАШИНОСТРОИТЕЛЬНЫХ ПРОИЗВОДСТВ11
Статья опубликована в журнале «Автоматизация в промышленности» №5, 2024 г.
[Закрыть]
В статье изложен сквозной взгляд на проблемы предприятий, теорию MES и практику реализации проектов внедрения от ГК «Цифра».
Сформулированы типовые проблемы автоматизации и цифровизации машиностроительных предприятий: почему зачастую проекты внедрения цифровых технологий не приводят к повышению эффективности бизнеса, какие ограничения присутствуют в системах организационного управления производственными предприятиями. Кратко приводится история развития MES. Рассматриваются конкретные примеры внедрения и использования MES «Диспетчер».
Ключевые слова: MES, автоматизация, цифровизация, машиностроительные предприятия.
Введение
Решение задач повышения эффективности производственных процессов является ключевым фактором роста экономики и развития страны в целом. Особенно важно обеспечить повышение эффективности в тех отраслях промышленного производства, которые непосредственно влияют на технологический суверенитет, обороноспособность страны и обеспечивают импортозамещение ключевых компонентов. Это станкостроение, авиастроение, производство робототехнических комплексов, компонентной базы, печатных плат, БПЛА, систем ПВО, а также ракетно-космическая отрасль и транспортное машиностроение. Объединяет все эти отрасли то, что все они относятся к дискретному позаказному производству сложных высокотехнологичных изделий. А соответственно проблемы развития и внедрения различных методов повышения эффективности на данных производствах схожи.
Существуют различные пути повышения эффективности производств, такие как:
– внедрение системы управления запасами (внедрение методологии управления запасами с синхронным развертыванием и настройкой под данную методологию систем класса ERP, SCM и WMS). Оптимизация уровня запасов сырья и готовой продукции поможет избежать дефицита или избыточных запасов;
– внедрение технологий Industry 4.0: Industrial Internet of Things (IIoT), аналитики данных, искусственного интеллекта, сервисов, основанных на машинном обучении, и др. Оптимизация процессов производства, выявление различных трендов, зависимостей, разработка и запуск предсказательных сервисов поможет увеличить прибыль и уменьшить издержки;
– применение методов Lean, Six Sigma: методологии, направленные на устранение излишков и повышение качества производимой продукции (бережливое производство);
– обучение и развитие персонала: повышение квалификации сотрудников и обучение новым методам и технологиям;
– внедрение PLM/PDM-систем и систем автоматизированного проектирования (CAD/CAM/CAE): ускорение и повышение эффективности конструкторско-технологической подготовки производства;
– внедрение систем производственного планирования (стратегического и объемно-календарного) и управления заказами (с применением APS-систем). Эффективное планирование производственных заказов и управление заказами помогут избежать простоев и задержек, повысить укомплектованность заказов с одновременной минимизацией запасов;
– использование управленческой идеологии Just-in-Time (JIT): минимизация запасов за счет точной поставки материалов и компонентов в нужное время;
– разработка идеологии и применение инструментов гибкой производственной системы: возможность быстро переключаться между различными заказами и изменять производственные линии под новые требования;
– автоматизация рутинных задач: применение роботизированных систем для выполнения монотонных и рутинных операций, повышение скорости и качества обработки предметов производства;
– постоянный контроль и анализ производственных данных с применением BI-систем, систем мониторинга и управления большими данными: сбор данных и мониторинг ключевых показателей эффективности производства помогают контролировать загрузку производства и персонала и принимать необходимые управленческие решения;
– внедрение системы управления качеством (TQM). Система управления качеством и система контроля качества продукции на всех этапах производства позволяют организовать производство с минимизацией дефектов и отклонений как производимых полуфабрикатов, так и конечной продукции;
– внедрение систем управления производственными процессами (MES). Системы MES повышают эффективность оперативного управления производственными процессами и создают единое информационное пространство управления и контроля от определения потребности до отгрузки продукции.
В данной статье рассматриваются варианты повышения эффективности производства, в том числе за счет применения систем управления производством, относящихся к классу MES.
Часто многие специалисты, в том числе с многолетним опытом и наличием успешно завершенных проектов в области ERP, PLM/PDM, а также CAD/CAM/CAE и прочих цифровых систем и сервисов, аргументированно утверждают, что именно на системах класса MES необходимо делать акцент при развертывании средств цифровизации производственных процессов. Основной приводимый ими аргумент: внедрение ERP (в части управления заказами, стратегического и объемно-календарного планирования, управления складским хозяйством и производственной логистикой), PLM (в части управления конструкторским и технологическим составом изделия) и САПР (в части проектирования электронного облика изделия и получения полного набора спецификаций изделия в реальном масштабе времени) создает необходимый фундамент для дальнейшего «правильного» внедрения систем управления производством. Это сильный аргумент, если бы у нас было время ждать, пока будут внедрены указанные системы и цифровизованы основные процессы.
Но, во-первых, такие внедрения на средних предприятиях могут длиться до 2 лет, на крупных же предприятиях со сложными изделиями и полным набором всех технологических переделов, с десятком-другим производственных цехов – 5…10 лет. Не нужно тратить сотни миллионов на внедрение ERP и/или PLM/САПР и ждать много лет, откладывая на потом непосредственно повышение эффективности производства, нужно повышать эффективность производства здесь и сейчас.
А во-вторых, не менее важный аспект, на который необходимо обращать внимание, это то, что раз за разом проявляется одна и та же системная ошибка в организации процессов внедрения ERP и PLM/САПР систем – забывается то, что внутренним целевым потребителем выхода данных систем как раз является MES. И именно под требования MES и процессов, которые MES цифровизирует, необходимо ориентировать внедрение и требования к созданию перечисленных систем и соответствующих процессов.
На практике же часто процессы организованы наоборот – отдельно определяют требования к ERP, к PLM и САПР и реализуют их, а потом пытаются «прикрутить» рядом MES. В результате получаются сценарии, когда необходимые для операционного планирования данные отсутствуют в электронных технологических процессах, не предусматривается оперативное резервирование на складах производственных партий, не указываются номера изделий в электронных извещениях о внедрении. Это происходит в силу естественных причин – процессы внедрения ERP/PLM/САПР начаты раньше, и они «заточены» под одного потребителя, например, бухгалтерский, финансовый блок или технологов, MES же считается «дополнительной нагрузкой».
Типовые проблемы систем организационного управления и ограничения существующих практик цифровизации предприятий
Современное промышленное предприятие – это сложная организационная структура, которая занимается преобразованием материалов, комплектующих и предметов собственного производства в готовую продукцию, удовлетворяющую потребности клиентов. Для обеспечения эффективности работы предприятия без значительных инвестиций в оборудование, персонал или технологии развивается система организационного управления.
Организации с позаказным типом управления производством – это предприятия дискретного производства, которые разрабатывают, проектируют и/или изготавливают продукцию на заказ. При этом может выпускаться как опытная единичная продукция, так и серийная. Как правило, опытное производство использует те же ресурсы, что и серийное без разделения мощностей. Это требует синхронного управления заказами на серийную продукцию и заказами на производство единичных образцов, а также управления технологической, инструментальной подготовкой производства, материальным обеспечением и выпуском изделий.
Еще одна важная характеристика предприятия – значительная доля задач осуществляется в рамках проектирования и освоения новых изделий, поэтому необходимо учитывать и контролировать ожидаемые сроки проектирования изделия и/или отдельных его элементов.
Проблема 1. Сроки. При большой сложности изделий возникают трудности, связанные с управляемостью проекта. В первую очередь, это длительные сроки и огромная трудоемкость актуализации и синхронизации графиков освоения (строительства) изделий с номенклатурными планами производства и снабжения, графиками выпуска конструкторской и технологической документации, планами инструментального производства, выпуском технологической документации и т. д.
Проблема 2. Обеспечение ресурсами. Для запуска конкретных партий в конкретный срок, в план реализации и в товарный план включаются изделия, как правило, без гарантии обеспечения материальными и производственными ресурсами. Конечно, планирование осуществляется, но обычно оно финансово-номенклатурное. Гарантии того, что в конкретный момент времени конкретные позиции материалов будут доступны для запуска в производство, по-прежнему отсутствуют.
Проблема 3. Методология планирования и отчетности производства. Цеха и участки работают по дискретно-формируемым планам, обычно это месячные, квартальные, годовые планы по выпуску изделий, номенклатуры предметов производства, оснастки, инструмента и т. д. Цеха регулярно закрывают сдачу товара, но на сборочном производстве постоянно отсутствует необходимая номенклатура. Аналогично осуществляется попериодное (год, квартал, месяц) планирование снабжения. При этом на складах накапливаются многомесячные запасы материала, а нужного для запуска в настоящий момент материала нет. Все это приводит к частым переносам и срывам срока выпуска изделий.
Причины возникновения проблем
1. Методология так называемого попериодного управления, которая применяется на всех производственных предприятиях постсоветской эпохи. Она подразумевает под собой разделение на периоды или «дискреты» планирования, и в рамках каждого такого периода происходит накопление и выполнение заказов, принятых решений и их фиксация до следующего периода.
Раз в месяц формируются номенклатурные планы цехов, а в конце месяца отчитываются о выпуске товарной продукции. Соответственно, есть показатели выполнения цехами своих работ: объем выпуска товарной продукции и объем выпуска обязательной номенклатуры. Для такой системы попериодного планирования не важно, когда производственные цеха выпустили свою продукцию, важно только выполнение плана в конце месяца.
Такая система планирования отрицательно влияет на эффективность производства. То же самое происходит с принятием решений по извещениям об изменениях, когда они в течение определенного периода времени накапливаются, а потом разово вбрасываются в производство. Это приводит к образованию излишних запасов и неликвидов в узлах цепи поставок или к задержкам в принятии управленческих решений. Как правило, приходится ждать следующей точки и планировать производство дополнительной партии деталей для того, чтобы восполнить потерю брака.
2. Автоматизация производственных процессов без их оптимизации. Почему система автоматизации не приводит к повышению эффективности? Почему предприятие не начинает производить и продавать больше продукции? Это при том, что речь идет не просто о лоскутной автоматизации, когда для автоматизации финансовых, учетных, договорных и прочих задач используются разные системы, в том числе самописные, а о комплексных проектах, когда внедряется одна ERP-система, интегрируемая с PDM-системой, которая, в свою очередь, интегрирована с САПР.
Все дело в том, что:
– во-первых, не была правильно выстроена цепочка «цели предприятия» — «задачи автоматизации». Чаще всего она вообще не бывает выстроена, потому что заказчики и потребители системы покупают ее функции, а не достижение своих целей, то есть оценивают выбираемые системы по наличию тех или иных функций;
– во-вторых, предприятия, как правило, не оценивают свой уровень организационной готовности к изменениям: они не хотят менять свои управленческие модели и последовательно проводить преобразования организационных структур;
– самое главное, что забываются целевые, системные задачи, для решения которых и была необходима автоматизированная система. Например, сокращение времени от выпуска извещений об изменении до принятия решения запуска в производство, увеличение объема производства, сокращение необеспеченных заказов на сборке и т. п. К сожалению, такие задачи не являются ни целями, ни задачами проекта и поэтому не решаются.
3. Противоречие между целями и задачами управления заказами на производственных предприятиях и целями и задачами каждого отдельно взятого подразделения. Например, в производстве стремятся к накапливанию определенного объема работ, укрупнению партий и их «пакетной обработке». Это может привести к задержкам в реализации заказов и созданию очередей в производстве. Каждое подразделение хочет достичь максимальной локальной эффективности, но в совокупности это не приводит к повышению эффективности всего предприятия.
Все это усугубляется отсутствием необходимого инструментария автоматизации управления. Существующие системы управления заказами и управления производственными подразделениями оперируют разными понятиями, имеют разные цели, разные показатели оценки эффективности, что приводит к разрыву между управлением заказами и деятельностью производственных подразделений.
История развития концепции MES
Для оперативного управления производственными процессами используются системы класса MES (manufacturing execution system). Это специализированное программное обеспечение, предназначенное для решения задач оперативного планирования, контроля, анализа и диспетчеризации процессов выпуска продукции. На рис. 1 представлена иерархия процессов управления производством по ГОСТ Р МЭК 62264.

Рис. 1. Иерархия процессов управления производством по ГОСТ Р МЭК 62264
Верхний уровень, четвертый в классификации по ГОСТ Р МЭК 62264 – это уровень планирования и управления производством и поставками по кооперации в рамках групп предприятий, связанных процессами производства продукции, а также уровень планирования и управления производственными процессами и логистикой отдельных промышленных предприятий. Горизонты принятия решений здесь – от нескольких лет до дней.
Третий уровень управления – это уровень построения расписаний и оперативного управления производственными процессами цехов, участков с горизонтом управления от дней до секунд в зависимости от характера производства.
Второй, первый и нулевой уровни можно представить одним уровнем управления и мониторинга процессов технологических линий и производственного оборудования с горизонтом управления от часов до долей секунд.
Каждому уровню управления соответствуют свои классы информационных систем, обеспечивающих и поддерживающих реализацию процессов управления на данном уровне.
На верхнем (четвертом) уровне управления – это системы класса ERP, которые обеспечивают стратегическое и тактическое управление производственными процессами, управление финансами, логистикой, ресурсами и кадровым капиталом. Также для решения задач управления производством по кооперации в настоящее время на рынке выделяется новый класс систем – cooperation management или «управление кооперацией». Такие системы призваны решать специфические задачи: формирование и планирование сквозных сетевых графиков производства-поставок продукции, интеграция в единое информационное пространство множества разнородных систем управления предприятий-кооперантов, синхронизация и контроль производственных и логистических процессов кооперантов всех уровней в рамках единого пакета заказов в реальном масштабе времени, аналитика и поддержка принятия решений по отклонениям.
Нижние уровни управления (с нулевого по второй включительно) покрываются АСУТП, где используются SCADA (Supervisory Control And Data Acquisition), MDC (Machine Data Collection), PLC (Programmable Logic Controller) и ряд других решений, обеспечивающих мониторинг, диспетчеризацию и управление технологическими процессами.
Для автоматизации на уровне управления производственными процессами традиционно используются системы класса MES, дословно «производственные исполнительные системы». Системы данного класса направлены на преобразование сформированных на вышестоящем уровне управления планов в конкретные задания производству с учетом имеющихся ресурсов, их состояния и доступности с целью получения требуемой продукции в указанные сроки и требуемого качества. Системы класса MES обеспечивают поддержку управления и реализацию всех необходимых функций для третьего уровня – построение расписаний, оперативный контроль выполнения, диспетчеризация производственных процессов цехов, участков.
Идея MES или ее целевое предназначение – дать в реальном времени ответ на три связанных между собой вопроса: что выпускать? (какие заказы, в какой последовательности); где выпускать? (на каком оборудовании); и кто это будет делать? (какой производственный персонал должен выполнять соответствующие операции и процессы производственных заказов).
Базовым нормативным документом для MES является стандарт ISA-95, который был переведен на русский язык и утвержден как российский ГОСТ Р МЭК 62264 «Интеграция систем управления предприятием». Стандарт определяет функциональную иерархию управления производственной деятельностью от уровня стратегического планирования и логистики до уровней непосредственного управления технологическими процессами и оборудованием с выделением так называемого управления производственными операциями, для автоматизации которого и используются системы класса MES. Также стандарт определяет основные объекты модели управления производственными операциями, их атрибуты, связи между ними для обеспечения обмена данными между уровнями управления, то есть между уровнями ERP и MES.
Функциональная модель MES
На вопрос, какие функции должна выполнять MES, наиболее развернутый ответ представлен в моделях MES, разрабатываемых ассоциацией MESA International (Manufacturing Enterprise Solutions Association), основанной в 1992 г. В настоящее время в нее входит более 1000 компаний по всему миру, в том числе ведущие разработчики систем класса MES. Первая функциональная модель MES, состоящая из 11 функций, была разработана этой ассоциацией в 1996 г. (рис. 2).

Рис. 2. Функциональная модель MESA 11 – 1996 г.
В связи с развитием и появлением на предприятиях большого числа информационных систем для автоматизации деятельности в разных сферах управления предприятием (в области бюджетирования и финансов, управления снабжением и поставками, планирования и управления производством, взаимоотношений с заказчиками, проектирования, разработки и управления жизненным циклом изделия) возникла также потребность их интеграции в единое информационное пространство.
Эти изменения предопределили появление в 2004 г. функциональной модели c-MES, где все функции MES существуют уже не сами по себе, взаимодействуя только друг с другом, они существуют также в рамках взаимодействия с внешними информационно-управляющими системами и задачами предприятия. При этом в рамках новой модели c-MES число основных функций MES было укрупнено до восьми (рис. 3).
Развитие MES как части единого информационного пространства предприятия предопределило переход в новое качество: MES перестала быть просто локальной системой, которая автоматизирует существующие производственные процессы на предприятии, а стала инструментом, интегрированным в системное окружение, позволяющим совершенствовать и развивать процессы производства с целью повышения качества и эффективности бизнеса в целом.

Рис. 3. Функциональная модель MESA8 (2004 г.)
В 2008 г. MESA International сформулировала модель стратегических инициатив для связи стратегии предприятия с операционной деятельностью. Модель включает семь стратегических инициатив, в рамках которых предприятия могут формировать стратегические цели, которые должны преобразовываться в конкретные задачи и воздействовать сверху-вниз, начиная от уровня предприятия (уровня ERP) и до уровня управления производственными процессами (уровня MES) (рис. 4):
Правообладателям!
Это произведение, предположительно, находится в статусе 'public domain'. Если это не так и размещение материала нарушает чьи-либо права, то сообщите нам об этом.