Текст книги "Работы по металлу"
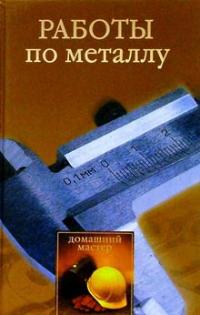
Автор книги: Наталья Коршевер
Жанр: Техническая литература, Наука и Образование
сообщить о неприемлемом содержимом
Текущая страница: 4 (всего у книги 20 страниц) [доступный отрывок для чтения: 7 страниц]
Виды слесарных работ
Гибка металлаСлесарю очень часто приходится выполнять операцию, связанную с пластическим деформированием металла, – гибку. Ни одна слесарная работа, пожалуй, без нее не обходится. При сгибании металла его волокна испытывают одновременно и сжатие и растяжение. Поэтому в ходе гибки нужно соблюдать определенные правила, чтобы пластическая деформация изгиба не перешла в разрыв:
– не следует выбирать радиус загиба меньше, чем толщина заготовки, это может привести к тому, что на металле появятся трещины или он сомнется на внутренней стороне загиба;
– не стоит гнуть заготовки из стального прутка диаметром больше 10 мм. Полосовую сталь для такой операции лучше выбрать толщиной до 7 мм, а стальные листы – до 5 мм.
Известно, что листовой металл легче гнуть, если его предварительно подогреть. А что делать, если такой возможности нет? Можно обойтись и без подогрева. На внешней поверхности в зоне сгиба необходимо нанести поперечные риски – лист согнется значительно легче.
Гнуть слесарю чаще всего приходится либо полосовую сталь, либо трубы. Приемы работы с этими двумя видами металла существенно различаются.
Гибка полосовой стали
Полосовую сталь удобнее всего гнуть в слесарных тисках. Для этого нужно установить заготовку таким образом, чтобы сторона с нанесенной на нее риской места загиба была обращена к неподвижной губке тисков. Риска должна выступать над губкой примерно на 0,5 мм. Удары наносить следует тоже в направлении неподвижной губки тисков (рис. 18).

Рис. 18. Приемы гибки полос: а – порядок гибки; б – гибка острого угла.

Рис. 18 (продолжение). Приемы гибки полос: в – изготовление скобы; г – изготовление хомутика.
Для того чтобы загнуть полосу под острым углом, необходимо воспользоваться оправкой, которая соответствует требуемому углу загиба. Ее нужно зажать в тисках вместе с заготовкой, расположив высокой стороной к ней, и загнуть ударами молотка.
Для изготовления из полосовой стали скобы применяется брусок-оправка, равный по толщине проему скобы. Его нужно зажать в тисках вместе с полосой стали и легкими ударами молотка загнуть одну сторону скобы. Затем вложить брусок внутрь скобы и, снова зажав в тисках, отогнуть другую сторону.
Для крепления труб и металлических стержней различного назначения часто используется хомут из полосовой стали. Он также изготавливается на тисках. Для этого нужно взять круглую оправку нужного диаметра, зажать ее в тисках и двумя плоскогубцами загнуть на ней полоску стали необходимой ширины и длины.
Затем оправку нужно освободить из губок тисков и, зажав в них отогнутые концы хомутика, придать ему окончательную форму. Лучше наносить удары молотком не по самому хомутику (чтобы не оставить на нем забоев, вмятин и царапин), а через медную пластинку небольшой толщины, которая хорошо перераспределяет усилие удара. Если нужен хомутик полуоткрытый, то его доводку удобно производить на плите.
Полосовая гибка часто применяется при гибочных соединениях деталей. Они носят самый различный характер и применяются достаточно широко. Соединение может быть целиком гибочным, когда крепежное усилие создается изгибом одной или обеих деталей, а может играть вспомогательную роль и усиливать, например, резьбовое соединение, как стопорная шайба или шплинт в соединении гайка-болт (рис. 19).

Рис. 19. Примеры гибочных соединений при сборке.
Если домашняя мастерская оборудована настольным ручным прессом, имеющим усилие 5–10 кН, то его можно оснастить очень производительными штампами, с помощью которых легко придавать металлическим листам изгиб нужного профиля. На основание пресса устанавливают матрицу с заранее выбранным профилем, а верхнюю силовую часть пресса оборудуют пуансоном, соответствующим форме матрицы (рис. 20).

Рис. 20. Гибка заготовок с помощью гибочного штампа.
При изготовлении штампов следует помнить, что ширина пуансона должна быть меньше ширины «ручья» матрицы на удвоенную толщину металлической заготовки.
В тех случаях, когда требуется изогнуть стальную полосу на ребро, используется роликовое приспособление (рис. 21).

Рис. 21. Гибка стальной полосы на ребро.
При работе с ним следует учитывать, что верхняя прорезь бруска основания должна точно соответствовать размерам полосы. Кроме того, верхнюю часть полосы, которая будет испытывать деформацию растяжения, а также рабочий ролик нужно смазать маслом.
Заготовки из стальных прутков удобно гнуть на простейшем приспособлении, которое представляет собой два штифта различного диаметра, ввернутых в металлическую плиту-основание. Пруток нужно вставить в промежуток между штифтами и оборачивать его вокруг штифта большего диаметра. При необходимости можно использовать молоток (если пруток слишком толстый или короткий). Недостаток этого приспособления в том, что оно позволяет получать изгибы только одного диаметра (соответствующего диаметру большого штифта). Впрочем, при желании его можно усовершенствовать, сделав штифты сменными.
Гибка труб
При слесарных работах часто требуют замены всякого рода трубочные соединения, которые используются для подвода к различным механизмам масла, воздуха, топлива или воды. Кроме того, домашнему слесарю порой приходится производить ремонт и замену коммуникационных трубопроводов (или сооружение новых, например на дачном участке). При этом в трубопроводах не всегда удается избежать острых и тупых углов (прямой угол можно собрать с помощью всевозможных сгонов, муфт и т. д.), а это значит что придется заниматься гибкой труб.
Трудность этой операции заключается в том, что труба при изгибании может сломаться, смяться и заготовка придет в негодность. Чтобы этого не случилось, трубу (если она не оцинкованная) предварительно забивают наполнителем (мелкий сухой песок или расплавленная канифоль) и нагревают в месте изгиба. В некоторых случаях можно наполнить трубу водой и заморозить (естественно, без последующего нагревания). Вместо наполнителя иногда используются плотно навитые стальные пружины, которые загоняются внутрь трубы на место изгиба. Но следует все же учесть, что в нагретом состоянии трубы гнутся значительно легче.
До какой температуры нужно нагревать трубы перед тем, как их гнуть? Как ее измерить? Никаких приборов для измерения температуры нагрева не требуется, она определяется визуально, на глаз. Стальные трубы следует нагревать до ярко-красного цвета, алюминиевые – до тех пор, пока не начнет обугливаться приложенная к трубе бумага. Вопрос о том, нужно ли в каждом конкретном случае использовать наполнитель или нет, решается в зависимости от того, какого радиуса изгиб нужно получить. Если радиус меньше 50 мм, то трубы диаметром до 20 мм можно гнуть без наполнителя и в холодном состоянии. Медные и латунные трубы перед гибкой необходимо отжечь в зоне загиба. Если приходится гнуть сварную трубу, то сварной шов (как наиболее уязвимую ее часть) следует расположить так, чтобы он не пришелся ни на растянутую, ни на сжатую сторону.
Самое простое приспособление для изгибания труб – металлическая плита с отверстиями, в которых располагаются штифты таким образом, чтобы получить трубу нужной конфигурации, а изгиб – подходящего радиуса. Это напоминает приспособление для гибки металлического прутка. Однако у этого приспособления имеются два очень значительных минуса. Во-первых, не всегда можно добиться чистого изгиба в одной плоскости. А во-вторых, если сгибаемая труба слишком коротка, то может просто не хватить физической силы.
Более совершенное приспособление для гибки труб представляет собой вертикально установленную двойную плоскопараллельную пластину, которая имеет кривизну необходимого загиба (рис. 22, а).

Рис. 22. Приспособления для гибки труб: а – плоскопараллельная пластина: 1 – плита; 2 – пластина; 3 – хомут; 4 – труба; б – станок Вольнова: 1 – металлический верстак; 2 – изгибаемая труба; 3 – хомут; 4 – съемный ролик-шаблон; 5 – подвижный ролик; 6 – рукоятка со скобой.
Трубу необходимо зажать в хомутике и гнуть вниз по пазу пластины, ширина которого соответствует внутреннему диаметру трубы.
Ну и, пожалуй, самым совершенным приспособлением для гибки труб в домашних условиях является специальный станок Вольнова, который не только не даст «убежать» трубе в трехмерное измерение, но и благодаря подвижному ролику и нескольким съемным роликам-шаблонам различных радиусов позволит производить практически все типы изгибов (рис. 22, б). Работает станок Вольнова следующим образом: длинную сторону трубы надо заложить под хомутик верстака, изгибаемое место смазать любым смазочным маслом (для лучшего скольжения подвижного ролика) и загибать короткую сторону.
Необходимо отметить, что гибка труб, особенно большого диаметра, ручным способом – операция малопроизводительная и тяжелая, и если есть возможность обойтись без изогнутых труб, то лучше ею воспользоваться.
Рубка металлаЕще одна довольно распространенная слесарная операция – рубка металла (вырубка в заготовке отверстий, прорубка смазочных канавок или просто отсечение лишнего слоя металла от заготовки). Производится рубка на наковальне или на массивной металлической плите. Более мелкие детали для рубки зажимаются в тисках.
Следует заметить, что при рубке невозможно достичь высокой точности обработки, ее применяют или для черновой обработки заготовки, или в тех случаях, когда точность обработки не требуется.
При работе с зубилом (основным рубящим инструментом) и молотком, в зависимости от цели работы, применяются три вида ударов:
– кистевой удар используется для удаления тонкого слоя металла, незначительных неровностей, а также в тех случаях, когда требуется перерубить лист тонкой стали. Кистевые удары следует выполнять в темпе 50–60 ударов в минуту; движется при этом только кисть руки. При замахе рекомендуется разжимать пальцы кисти, удерживая ручку молотка только указательным и большим пальцами, а при ударе кисть сжимать;
– локтевой удар имеет большую силу по сравнению с кистевым. Темп ударов чуть замедленный – 40–50 ударов в минуту. При замахе руку рекомендуется сгибать в локте до отказа, безымянный и средний пальцы слегка разжимать. Применяются локтевые удары для прорубания канавок и пазов, а также для снятия слоя металла средней толщины;
– плечевой удар наиболее мощный. Сила удара достигается большим замахом, при котором рука движется в плечевом суставе. Пальцы, кисть и локоть должны работать, как и при кистевом и локтевом ударах, но при замахе максимально согнутую в локтевом суставе руку следует поднять таким образом, чтобы кисть оказалась на уровне уха. Темп ударов должен быть еще более замедленным – 30–40 ударов в минуту. Применяются такие удары для обработки больших поверхностей, рубке толстого металла, а также в тех случаях, когда требуется удалить за один проход зубила большой припуск.
Качество рубки и безопасность производящего ее слесаря зависят и от того, как держится инструмент. Пальцы на рукоятке молотка должны располагаться на расстоянии 15–30 мм от ее конца, при этом большой палец наложить на указательный. Зубило нужно держать на расстоянии 20–30 мм от его головки, пальцы плотно сжимать не следует. Вероятность соскакивания молотка с головки зубила значительно снижается, если на ее верхнюю часть надеть резиновую шайбу диаметром 50 мм и толщиной примерно 10 мм.
При выполнении этого вида слесарных работ важно соблюдать и правильную постановку зубила относительно обрабатываемой заготовки (рис. 23):
– при направлении рубки вдоль плоскости губок тисков угол между осью зубила и плоскостью губок должен составлять примерно 45°;
– при направлении рубки перпендикулярно к плоскости губок тисков угол наклона зубила относительно заготовки должен быть 30–35°: если угол наклона будет большим, то зубило при ударе уйдет вглубь металла, создав значительную неровность обрабатываемой поверхности; при меньшей величине угла зубило будет скользить по поверхности металла, а не рубить его.

Рис. 23. Положение зубила при рубке заготовки в тисках.
Существенное замечание: неопытные слесари при ударе молотком по зубилу смотрят, как правило, на головку последнего, по которой ударяет молоток. Это грубая ошибка, приводящая к снижению качества работы: смотреть нужно на режущую кромку зубила, чтобы контролировать угол наклона и видеть результат каждого удара.
Располагая заготовку в тисках, надо следить за тем, чтобы разметочные риски находились точно на уровне губок и не имели перекоса.
Вся срубаемая часть металла (стружка) должна быть расположена над уровнем губок тисков.
Срубание слоя металла по широкой плоской поверхности
В тех случаях, когда предстоит срубать металл на широкой плоской поверхности, располагать заготовку следует таким образом, чтобы разметочные риски выступали над плоскостью губок тисков на 5–10 мм. В данном случае операцию рубки нужно начинать с прорубания канавок шириной 8–10 мм с помощью крейцмейселя (см. рис. 4, б). Он за один проход должен снимать стружку толщиной от 0,5 до 1 мм.
Канавки должны быть расположены таким образом, чтобы между ними оставались промежутки шириной в 4/5 длины режущей кромки зубила.
После прорубки канавок промежутки между ними вырубаются с помощью зубила. Толщина стружки при этом должна составлять от 1,5 до 2 мм.
Осторожности требует рубка хрупких металлов – таких как, чугун, бронза и др. Рубку не следует доводить до края заготовки, так как произойдет скол, если удар будет направлен от центра заготовки к ее краю. Избежать такого дефекта можно двумя способами: во-первых, недорубленное место дорубают с противоположной стороны, направляя зубило острием в сторону заготовки, а головкой к себе, во-вторых, заранее обработав края и сделав скос под углом в 45°. При рубке вязких металлов (мягкая сталь, медь, латунь), режущую кромку зубила рекомендуется смазывать мыльной эмульсией или машинным маслом.
Вырубание криволинейных канавок
Пазы и криволинейные смазочные канавки нужно прорубать по нанесенным заранее разметочным рискам. Для этого используют крейцмейсель, которым вырубают по 1,5–2 мм металла за каждый проход. Неровности, оставшиеся после работы крейцмейселем, можно удалить канавочником, придав пазам одинаковую ширину и глубину.
Некоторые особенности имеет работа при рубке металла по криволинейному контуру. Лучше для такого вида работы использовать крейцмейсель или зубило с закругленным лезвием.
Прежде всего необходимо надрубить легкими ударами контур, отступая от разметочных рисок на 2–3 мм, а затем сильными ударами снять металл в пределах контура. Если позволяет толщина листа, то заготовку можно через некоторое время перевернуть и рубить с противоположной стороны, ориентируясь на контур, обозначенный первыми ударами.
Резка металлаВ тех случаях, когда операцию по отделению части металла от заготовки невозможно (или нецелесообразно) производить рубкой, прибегают к резанию.
Выбор инструмента для этой операции зависит от вида обрабатываемого металла. Листовой металл толщиной до 0,5 мм (листы латуни и алюминия до 1 мм) можно резать ручными ножницами. Лезвия ножниц при этом следует разводить примерно на три четверти их длины, а лист металла нужно располагать перпендикулярно к плоскости режущих кромок ножниц. При сжатии ручек ножниц лезвия до конца сводить не следует, так как это приводит к разрыву металла в конце разреза. Для круглых заготовок резать металл целесообразнее против часовой стрелки, для чего заготовку следует поворачивать по часовой стрелке.
Если толщина разрезаемого листа несколько больше (0,7–1,5 мм), то можно воспользоваться теми же ручными ножницами, но одну из рукояток зажать в тисках, а на другую надавливать рукой сверху (рис. 24).

Рис. 24. Прием резания листового металла ножницами: а – ручными (с помощью тисков); б – силовыми; в – рычажными.
Металл толщиной свыше 0,7 мм (а латунь и алюминий свыше 1,5 мм) обычными ручными ножницами разрезать не удастся. В этих случаях следует применить силовые ножницы. Рукоятку, не снабженную пластмассовым наконечником, закрепляют в тисках, а рабочую рукоятку (с пластмассовым наконечником) захватывают рукой. Сила резания за счет применения рычага увеличивается примерно в 2 раза по сравнению с обычными ручными ножницами. Ножи на силовых ножницах можно менять, это предусмотрено их конструкцией. Кроме того, на силовых ножницах обычно имеется приспособление для резки металлических прутков диаметром до 8 мм.
Если в мастерской имеются рычажные ножницы, то можно довольно быстро (и относительно легко) разрезать листовую сталь толщиной до 4 мм, а также латунь и алюминий до 6 мм. Перед работой рычажными ножницами необходимо позаботиться о том, чтобы их основание было надежно прикреплено к столешнице слесарного верстака, для этого на них предусмотрены болты. Резание металла происходит в результате движения рукоятки (рычага), к которой и прикреплен один из ножей ножниц, вниз.
Нажимать на рукоятку рычажных ножниц нужно плавно, без рывков. На них (в отличие от ручных и силовых) резка металла возможна только по прямой линии.
При работе с толстыми листами полосового или профильного металла, а также в том случае, если нужно не распилить металл, а прорезать паз или шлиц, ножницы может заменить ножовка (лобзик по металлу). Но прежде чем приступить к работе с этим инструментом, его предварительно следует правильно настроить.
Во-первых, нужно выбрать полотно для ножовки. Оно подбирается в зависимости от вида металла (см. главу о свойствах металлов и сплавов).
Во-вторых, полотно нужно правильно натянуть в рамке ножовки; степень натяжения легко проверить легким нажатием сбоку на полотно: если оно не прогибается, значит, натяжение достаточное.
Наиболее удобное положение рук при работе ножовкой следующее: конец рукоятки упирается в середину ладони правой руки, а пальцы левой руки обхватывают натяжной винт подвижной головки (рис. 25).

Рис. 25. Положение ножовки во время работы.
Движения ножовкой нужно производить плавные, без рывков; частота движений – 30–60 двойных ходов (от себя – на себя) в минуту; при этом должно работать не менее 2/3 длины полотна. Полотно ножовки должно быть строго перпендикулярно относительно оси обрабатываемой заготовки.
В том случае, если нужно разрезать ножовкой тонкий металл, его помещают между двумя деревянными брусками, этот «сэндвич» зажимают в тиски, и резку производят вместе с брусками.
Особо следует сказать о резке металлических труб. При резании их ножовкой всегда есть опасения (особенно если слесарь недостаточно опытен), что полотно ножовки «уйдет» в сторону и срез получится в виде не окружности, а овала. Во избежание этого трубы предпочтительнее резать не ножовкой, а специальным приспособлением – труборезом (см. рис. 5, д), помимо того что он дает ровный срез, работа им еще и довольно производительна. Техника резки такова: трубу зажимают в тиски, на нее на расстоянии 80–100 мм от губок тисков надевают неподвижные диски трубореза (на разметочную риску), устанавливают труборез перпендикулярно к оси трубы, поворотом рукоятки-винта закрепляют труборез на трубе, врезав тем самым подвижный режущий ролик в толщу металла, плавными короткими движениями рукоятки трубореза по часовой стрелке – против часовой стрелки делают полный оборот вокруг трубы, поворачивают винт на 1/4 оборота, вновь делают полный круг труборезом и так далее до полного отрезания трубы. Для облегчения работы неподвижные диски желательно смазать мыльной эмульсией или машинным маслом.
Опиливание и зачистка металлических деталейЛюди, мало сведущие в слесарных работах, зачастую путают эти две операции – опиливание и зачистку, а между тем у них есть существенная разница: опиливание связано с изменением размера деталей (напильником снимается слой металла), а зачистка – с изменением шероховатости (удаление царапин, рисок и пр.). Опиливание производится с помощью напильников и надфилей; зачистка чаще всего осуществляется абразивными кругами, брусками, шкурками, иногда используются проволочные щетки.
Процесс опиливания заключается в основном в опиливании деталей по контуру, для удаления заусенцев, забоин, образовавшихся при рубке (резке), в устранении дефектов на плоскостях (если технические условия позволяют такие исправления), снятии припусков под размер, опиливании плоскостей сложных поверхностей, выступов, пазов при подгонке деталей во время сборки. Но в любом случае после опиливания поверхности подвергаются зачистке.
В том случае, если нужно удалить слой металла более 0,2 мм, опиливание считается грубым; от 0,1 до 0,2 мм – средним; до 0,1 мм – тонким.
От того, какая обработка требуется, зависит выбор напильника по номерам (см. главу, посвященную слесарному инструменту).
Выбор напильника по длине зависит от величины детали: он должен быть длиннее обрабатываемой плоскости, как минимум, на 150 мм.
Выбор формы напильника зависит от поверхности: ровные поверхности опиливают плоскими напильниками, сопряженные (углы между ними) – квадратными, ромбическими, треугольными, криволинейные – круглыми и полукруглыми (см. рис. 9).
Плоские напильники (см. рис. 9, а) применяются для опиливания наружных или внутренних плоских поверхностей и для пропиливания шлицев и канавок.
Полукруглые напильники (см. рис. 9, б) предназначены для обработки криволинейных поверхностей и углов более 30°.
Квадратные напильники (см. рис. 9, в) применяют для пропиливания квадратных, прямоугольных и многоугольных отверстий.
Трехгранные напильники (см. рис. 9, г) используются для опиливания углов 60° и более как с внешней стороны детали, так и в пазах, отверстиях и канавках.
Круглые напильники (см. рис. 9, д) применяются для пропиливания круглых и овальных отверстий и вогнутых поверхностей небольшого радиуса.
Для более качественной обработки (и для повышения производительности) опиливание лучше всего производить перекрестными проходами (рис. 26, а).

Рис. 26. Опиливание поверхностей и контроль за качеством работ: а – перекрестное опиливание; б – контроль отклонений от плоскости и прямолинейности; в – контроль отклонений от параллельности; г – контроль отклонений от перпендикулярности; д – контроль криволинейных поверхностей по шаблону.
В том случае, если с поверхности детали нужно снять лишь выступающие части, опиливание производится круговыми движениями.
Во время работы рукоятка напильника должна опираться на центр ладони правой руки, а пальцы левой руки нужно расположить поперек напильника на расстоянии 20–30 мм от его носика (будет удобнее, если пальцы слегка согнуть, но не свешивать до рабочей плоскости напильника) (рис. 27).

Рис. 27. Правильное положение слесаря (а) и положение его рук при грубом (б) и при чистом (в) опиливании.
Движения напильником должны быть строго горизонтальными относительно обрабатываемой поверхности (рабочий ход – вперед, от себя, холостой ход – назад, к себе); темп движений – от 40 до 60 поступательно-возвратных движений в минуту. Производить движения следует обеими руками, распределяя силу давления на инструмент следующим образом:
– начало рабочего хода – основной нажим левой рукой, правая лишь поддерживает напильник в горизонтальном положении;
– середина рабочего хода – сила нажима обеими руками одинакова;
– конец рабочего хода – левая рука поддерживает напильник в горизонтальном положении, а основная нагрузка приходится на правую руку;
– холостой ход – напильник от опиливаемой поверхности не отрывается, но сила нажима минимальная.
Если во время работы напильник скользит, надо прочистить его стальной щеткой вдоль насечек.
Деталь, подлежащую опиливанию, зажимают между накладками тисков так, чтобы обрабатываемая поверхность выступала над губками на высоту 5–10 мм. При опиливании тонкой детали ее следует крепить на деревянном бруске деревянными пластинками, обеспечивающими неподвижность детали (рис. 28).

Рис. 28. Опиливание детали из тонкого металла.
Существенное значение имеет положение слесаря в момент опиливания по отношению к обрабатываемой детали. Он должен располагаться сбоку тисков на расстоянии около 20 см от верстака так, чтобы корпус был прямым и повернутым под углом 45° к продольной оси тисков (см. рис. 27, а). Упор нужно делать на левую ногу.
В ходе операции опиливания периодически осуществляют проверку качества поверхностей. Контроль опиливания производится обычно с помощью проверочных линеек и проверочных плит методом «световой щели» или «на краску» (см. рис. 26, в, г).
Опиливание плоскопараллельных поверхностей
Сначала об опиливании кромок деталей из листового металла. Слесарям хорошо известно, что на их зачистку уходит времени в 30–40 раз больше, чем на то, чтобы его разрезать.
Время, уходящее на эту операцию, можно значительно сократить, саму операцию сделать менее трудоемкой и более безопасной, если в работе использовать небольшое приспособление, изготовленное из двух напильников (рис. 29).

Рис. 29. Приспособление для опиливания кромок деталей из листового металла: 1 – напильники; 2 – деревянная ручка; 3 – болты.
Плоские напильники нужно обрезать на необходимую длину так, чтобы остались только рабочие поверхности, и просверлить в них отверстия для крепления. Затем вырезать из дерева ручку (в виде бруска), соответствующую длине напильников. В ручке необходимо вырезать прямоугольную выемку и прикрутить к ее сторонам напильники таким образом, чтобы они плотно прилегали друг к другу под прямым углом. Крепежные винты не должны выходить за плоскость рабочей поверхности напильника, их надо утопить чуть глубже. Таким модернизированным двойным напильником зачищать кромку стального листа очень легко и быстро. Кроме того, значительно уменьшается опасность травмирования об его острые кромки во время работы.
Прежде чем опиливать деталь, имеющую плоскопараллельные поверхности (например, в виде бруска, плиты), следует выбрать основную измерительную базу – как правило, это одна из наиболее широких поверхностей. Ее следует опилить окончательно, с проверкой плоскости и прямолинейности. Затем с помощью штангенциркуля проверяют параллельность широких поверхностей и толщину заготовки, определяя при этом подлежащий удалению припуск, замеры производят в 3–4 местах. После чего обрабатывают напильником вторую широкую сторону.
Если, помимо широких поверхностей, требуется обработка и узких, то из них выбирается одна из более длинных сторон (она принимается за вспомогательную базу). После ее полной обработки опиливаются короткие поверхности, примыкающие к ней под углом 90°, с обязательной проверкой перпендикулярности относительно вспомогательной базы. В завершение опиливается вторая длинная сторона.
При опиливании плоских поверхностей может применяться механический напильник (рис. 30).

Рис. 30. Механический напильник: 1 – наконечник; 2 – эксцентрик; 3 – плунжер.
В этом напильнике при вращении наконечника от гибкого вала через червячную передачу получает вращение эксцентрик, сообщающий возвратно-поступательное движение плунжеру, к которому крепится напильник.
Можно сократить время опиловочных работ с помощью шлифовальных машинок, к которым крепятся абразивные круги (рис. 31).

Рис. 31. Шлифовальные машинки: а – электрическая; б – пневматическая.
Опиливание сопряженных плоских поверхностей
Чаще других слесарю приходится опиливать поверхности сопряженные, расположенные по отношению друг к другу под определенным углом. Наружные углы, как правило, обрабатываются плоскими напильниками, внутренние, в зависимости от их величины, трехгранными, квадратными, ромбическими, а если угол очень острый, то и надфилями.
Как и при опиливании плоскопараллельных поверхностей, первой окончательно обрабатывают измерительную базу (наиболее длинную или широкую сторону). Затем проверяют угол между базой и необработанной поверхностью (с помощью угломера) и опиливанием доводят его до соответствия с требуемой величиной.
Особой тщательности требует обработка мест сопряжения внутренних плоскостей угла, ибо именно там чаще всего выявляются погрешности обработки.
Опиливание криволинейных поверхностей
Криволинейные поверхности подразделяются на выпуклые и вогнутые. Обработка таких поверхностей обычно связана со снятием относительно большого слоя металла (припуска).
Выпуклые криволинейные поверхности сначала размечают, затем снимают лишний металл ножовкой или зубилом, а потом опиливают плоскими напильниками: основной припуск снимают напильником № 0, оставляя припуск до разметочной риски в 0,8–1 мм; далее напильником № 4 или № 5 снимают оставшийся припуск до риски.
Сила нажима на напильник во время рабочего хода практически не меняется, а изменение его положения относительно обрабатываемой детали – балансировка – напоминает качели (в случае если деталь закреплена в тисках в горизонтальном положении) (рис. 32):
– в начале рабочего хода носик напильника направлен вниз, а рукоятка приподнята;
– в середине рабочего хода напильник располагается горизонтально;
– в конце рабочего хода приподнятым должен быть носик напильника, а рукоятка – опущенной.

Рис. 32. Приемы опиливания выпуклых криволинейных поверхностей.
Если же деталь закреплена в тисках в вертикальном положении, то движение напильника будет иным:
– в начале рабочего хода носик напильника направлен несколько вверх и влево;
– в конце рабочего хода напильник носиком смотрит прямо вперед.
В ходе опиливания деталь периодически освобождают из тисков и поворачивают относительно ее оси на небольшой угол (приблизительно на 1/5 оборота). Качество работы проверяют с помощью шаблона.
Обработку вогнутых криволинейных поверхностей также начинают с нанесения разметки контура детали на заготовке.
Большую часть лишнего металла можно удалить зубилом, ножовкой (при этом используется ножовка без рамки) или одновременно высверливанием и выпиливанием, оставив небольшой припуск, а затем полукруглым или круглым напильником спилить припуск до разметочной риски (рис. 33).

Рис. 33. Приемы обработки вогнутых криволинейных поверхностей.
При выборе напильника следует учесть, что радиус его сечения должен быть несколько меньше радиуса опиливаемой поверхности. Во время работы сочетают два вида движений напильником: прямолинейное (от себя – на себя) и вращательное. Качество работы контролируется наложением шаблона.
Правообладателям!
Данное произведение размещено по согласованию с ООО "ЛитРес" (20% исходного текста). Если размещение книги нарушает чьи-либо права, то сообщите об этом.Читателям!
Оплатили, но не знаете что делать дальше?