Текст книги "Сварочные работы. Практический справочник"
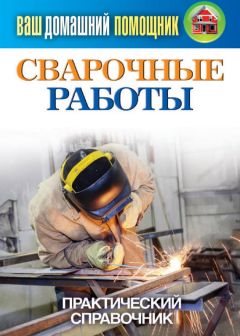
Автор книги: Сергей Кашин
Жанр: Хобби и Ремесла, Дом и Семья
Возрастные ограничения: +16
сообщить о неприемлемом содержимом
Текущая страница: 3 (всего у книги 11 страниц) [доступный отрывок для чтения: 3 страниц]
Газовая сварка
Общие сведения
Газопламенная обработка металлов (ГОМ), к которой относятся газовая сварка, резка и газотермическое напыление, широко распространена в промышленности. На долю этих процессов приходится примерно 80 % различных видов ГОМ. Особое место среди них занимает газовая сварка металлов, к достоинствам которой относятся следующие факторы:
1) достаточная простота работы;
2) отсутствие потребности в дорогостоящем оборудовании и источнике электрической энергии;
3) широкий диапазон выбора режимов сварки;
4) разнообразнейший спектр применения, поскольку газовая сварка находит применение:
✓ при изготовлении и ремонте конструкций и изделий из тонколистовой стали, чугуна, бронзы, силумина;
✓ при монтаже и ремонте трубо-, водо– и газопроводов из труб диаметром до 50 мм;
✓ при сварке изделий из цветных металлов (меди, алюминия, свинца, латуни);
✓ при наплавке на детали из стали и чугуна.
Из недостатков необходимо отметить следующие факторы:
✓ сравнительно небольшая скорость нагрева металла;
✓ значительная зона термического влияния, состояние и ширина которой определяют механические характеристики сварного соединения;
✓ большой участок, подвергающийся разогреву, что увеличивает риск коробления металла;
✓ замедленный нагрев металла и довольно невысокая концентрация тепла, снижающие производительность сварки при увеличении толщины металла. По этой причине газовая сварка стали толщиной более 4 мм не используется;
✓ достаточно высокая стоимость расходных материалов, в частности ацетилена и кислорода, что делает газовую сварку более затратной, чем дуговая;
✓ невозможность механизации и автоматизации процесса.
Несмотря на достаточно внушительный список недостатков, газовая сварка является процессом, который достоин изучения, тем более что с ее помощью можно сваривать практически все применяемые в технике металлы.
Оборудование и материалы
Газовая сварка и резка металлов осуществляются с помощью различных газов, их смесей, паров бензина и керосина.
Кислород при обычных температуре и давлении – это прозрачный газ, имеющий следующие физические характеристики:
✓ без вкуса, запаха, цвета;
✓ масса 1 м3 при 20 °C и атмосферном давлении составляет 1,33 кг;
✓ при нормальном давлении горит при температуре 182,9 °C.
Химическая активность кислорода очень высока: он взаимодействует со всеми химическими элементами, за исключением инертных газов, причем эти реакции относятся к экзотермическим.
Для сварки и резки применяют технический кислород, который в зависимости от содержания чистого кислорода (остальное приходится на азот и аргон) различается по сортам:
✓ I сорт – содержание чистого кислорода составляет 99,7 %;
✓ II сорт – не менее 99,5 %; ✓ III сорт – 99,2 %. Чистота кислорода – это очень важный показатель, особенно для резки металлов. При его повышении улучшается качество обработки металла и снижается расход самого газа.
Кислород требует осторожного обращения, поскольку при контакте с органическими веществами (маслами, угольной пылью и проч.) он склонен к самовоспламенению и взрыву в результате их быстрого окисления. Кроме того, он может взаимодействовать с горючими газами и парами, что тоже может закончиться взрывом.
Ацетилен (C2H2) относится к горючим газам и чаще всего используется при газовой сварке. При горении в кислороде его температура повышается до 3050–3150 °C. Физические характеристики ацетилена:
✓ бесцветный газ с резким запахом;
✓ легче воздуха (масса 1 м3–1,09 кг);
✓ сжижается при температуре –82 °C;
✓ переходит в твердое состояние при температуре –85 °C;
✓ взрывоопасен (температура самовоспламенения – 240–630 °C; при повышении давления она может быть и ниже, если, например, при давлении 0,3 МПа температура воспламенения составляет 530 °C, то при давлении 2,2 МПа – 350 °C), особенно в смеси с кислородом или воздухом.
Технический ацетилен производят двумя способами – из карбида кальция либо из природного газа, нефти или угля. Причем второй вариант обходится гораздо дешевле (примерно на 30–40 %).
3. Пропан-бутановая смесь, или технический пропан (бесцветный газ, с резким неприятным запахом, несколько тяжелее воздуха), количество бутана в котором составляет 5–30 %. Эту смесь получают в процессе газодобычи или переработки нефти.
Температура, которую дает пропан-бутановая смесь, составляет 2400 °C, поэтому ее применяют при сварке стали толщиной не более 3 мм (в этом отношении она не уступает по результативности ацетилену), в противном случае металл не удается прогреть до такой степени, чтобы получить прочное соединение. Но низкотемпературное пламя применяют при резке, правке и очистке металла. Для сварочных работ пропан-бутановая смесь доставляется в баллонах в жидком состоянии. В верхней части емкости он самопроизвольно меняет свое агрегатное состояние на газообразное.
4. Природный газ, 77–98 % которого составляет метан (газ без цвета и запаха), остальное количество приходится на бутан, пропилен, пропан и др. Так как температура метан-кислородной смеси составляет 2100–2200 °C, сфера ее применения достаточно узкая.
5. Водород (H2) – самый легкий газ, горючий, не имеет ни цвета, ни запаха. В смеси с кислородом становится взрывоопасным, поэтому его применение при сварочных работах требует строжайшего соблюдения техники безопасности.
Кроме перечисленных веществ, в сварке находят применение и другие горючие газы, например коксовый газ, городской газ, нефтяной газ, пары бензина и керосина.
Для осуществления газовой сварки необходимо специальное оборудование.
Ацетиленовый генератор, предназначенный для получения ацетилена в процессе взаимодействия карбида кальция с водой. Согласно ГОСТу 5190–78 такие устройства различаются по следующим параметрам:
✓ давление получаемого газа (генераторы низкого и среднего давления – до 0,02 МПа и 0,02– 0,15 МПа соответственно);
✓ способ установки (стационарные и передвижные);
✓ производительность (стационарные – 5, 10, 20, 40, 80, 160, 320 или 640 м3/ч, а передвижные – 1,25 и 3 м3/ч). Чаще всего используют генераторы производительностью 1,25 м3/ч;
✓ характер взаимодействия карбида с водой. Различаются генератора типов КК («карбид в воду»), ВК («вода на карбид»), К (контактный), ВВ («вытеснение воды»), ВК + ВВ (комбинированный).
Независимо от системы функционирования все генераторы состоят из газообразователя, газосборника, предохранительного затвора и автомата для регулировки вырабатываемого ацетилена. В качестве примера можно привести ацетиленовый генератор ГВР-1,25 М, конструкция которого представлена на рис. 13.
Технические характеристики передвижных ацетиленовых генераторов наиболее распространенных марок представлены в табл. 2.
2. Предохранительные затворы, устанавливаемые на ацетиленовые генераторы для предупреждения обратного удара, возникающего при попадании в трубопроводы и шланги, через которые поступают горючие газы, взрывной волны и пламени. Если это происходит с высокой скоростью, то удар может дойти до генератора и вызвать его взрыв.
Таблица 2
Технические параметры некоторых передвижных ацетиленовых генераторов производительностью 1,25 м3/ч

Предохранительные затворы бывают сухими и жидкостными (обычно водяными) (рис. 14). Последние распространены в большей степени.
Для генераторов низкого давления предназначены затворы открытого типа, для генераторов среднего давления – закрытого типа. Принцип действия такого устройства заключается в том, что взрывная волна и пламя, не доходя до потока горючего газа, либо стравливаются в атмосферу, либо гасятся внутри затвора.
3. Баллоны для сжатых газов. Принципиальное отличие баллонов для ацетилена от баллонов для других горючих газов состоит в том, что этот газ содержится в ацетилен-ацетоновом растворе, поглощенном специальной пористой массой (активированным углем марки БАУ-А (ГОСТ 6217–74)), которой и заполнен весь баллон. Это позволяет безопасно хранить, транспортировать и использовать ацетилен. Сейчас все чаще применяют литую пористую массу на основе силикатов.

Рис. 14. Предохранительные затворы: а – жидкостного типа ЗСГ-1,25–4: 1 – корпус; 2 – колпачок обратного клапана; 3 – гуммированный клапан; 4 – корпус обратного клапана; 5 – сетка; 6 – пробка для слива воды из обратного клапана; 7 – ниппель для ввода ацетилена в затвор; 8 – пробка; 9 – контрольная пробка; 10 – пламяпреградитель; 11 – штуцер; 12 – накидная гайка; 13 – ниппель; б – сухого типа ЗСН-1,25: 1 – корпус; 2 – мембрана; 3 – крышка; 4 – отсечный сферический клапан; 5 – стакан; 6 – уплотнитель; 7 – обратный клапан
Вентиль для баллона под ацетилен сделан из стали и выдерживает давление 25 кгс/см2. Маховик у него отсутствует (с ним нельзя было бы надеть присоединительный хомут с натяжным винтом). Для открывания и закрывания вентиля используется специальный ключ, надевающийся на шпиндель. На седле в корпусе вентиля имеется эбонитовый уплотнитель, который открывает и блокирует выход ацетилена.
Баллоны для ацетилена бывают разного объема, но, как правило, используют баллоны емкостью 40 л (5,5 м3 ацетилена, с пористой массой – 7 м3). Баллон для пропан-бутановой смеси сваривается из листовой стали толщиной 3 мм и имеет один продольный и два кольцевых шва. Сверху приварена горловина, внизу – башмак, обеспечивающий устойчивость. Баллон заполняется смесью примерно на 85 %.
Вентиль для пропанового баллона изготовлен из стали и, в отличие от других конструкций, имеет запорное устройство в виде мембраны, выполненной из пружинной стали. Если стоит неметаллический уплотнитель, то вся шпиндельная система вентиля уплотняется ниппелем.
Кислородный баллон – это цилиндр с выпуклым днищем и сферической горловиной, в которой имеется сквозное отверстие с конической резьбой, куда вкручивается запорный вентиль. Производятся баллоны малой (до 12 л) и средней (12–40 л) вместимости с условным давлением 200 кгс/м2.
Корпус кислородного вентиля сделан из латуни. Его герметичность обеспечивают сальник и прокладка (сейчас чаще всего используют капроновую).
Основные характеристики баллонов для горючих и сжатых газов представлены в табл. 3.
4. Редуктор. Это прибор, функции которого заключаются в понижении давления газа из баллона (газопровода) до рабочего и поддержании его на таком уровне. Редукторы бывают одно-и двухкамерными. В последних давление понижается сначала до промежуточного значения (с 15 до 4 МПа), потом до рабочего – 0,3–1,5 МПа. Двухкамерные редукторы имеют более сложную конструкцию, стоят дороже, но способны поддерживать давление практически на постоянном уровне.
Таблица 3
Основные характеристики баллонов под горючие и сжатые газы


В настоящее время производят семнадцать типов редукторов. Обозначение марок редукторов включает в себя:
✓ буквы: Б (баллонный), С (сетевой), Р (рамповый), А (ацетилен), В (водород), К (кислород), М (метан), П (пропан), О (одна ступень с пружинным заданием), Д (две ступени с пружинным заданием), З (одна ступень с пневматическим задатчиком);
✓ цифры, по которым судят о максимальной пропускной способности редуктора.
Параметры некоторых наиболее часто применяемых редукторов приведены в табл. 4.
Корпус редуктора имеет такой же цвет, что и баллоны, т. е. для кислорода – голубой, для ацетилена – белый, для пропана – красный.
Таблица 4
Основные технические характеристики некоторых типов редукторов

5. Сварочная горелка с комплектом сменных наконечников, которые по ГОСТу 1077–79 классифицируются:
1) по роду используемого газа или жидкости:
✓ для ацетилена;
✓ для газов-заменителей;
✓ для водорода;
✓ для горючих жидкостей;
2) по назначению:
✓ универсальные (для сварки, резки и проч.);
✓ специализированные;
3) по способу подачи газа и кислорода в смеситель:
✓ инжекторные;
✓ безынжекторные (в нашей стране производятся только горелки микромощности);
4) по количеству пламени:
✓ однопламенные;
✓ многопламенные;
5) по мощности пламени:
✓ микромощные (расход ацетилена 5–50 л/ч) Г1;
✓ малой мощности (25–600 л/ч) Г2;
✓ средней мощности (50–2200 л/ч) Г3;
✓ большой мощности (2200–7000 л/ч) Г4;
6) по способу использования:
✓ ручные;
✓ машинные. Горелки выпускают с набором наконечников от 0 до
7. Горелки Г1 и Г4 используются редко, поэтому наконечники к ним поставляются по специальному заказу. Наибольшим спросом пользуются малые и средние горелки. В комплект входят наконечники:
✓ Г2 – № 1, 2, 3 (№ 0 – по заказу);
✓ Г3 – № 3, 4, 6 (№ 1, 2, 5, 7 – по заказу).
Конструкция инжекторной горелки наглядно представлена на рис. 15.
6. Шланги (рукава) для подачи газа в горелку или резак. Рукава с нитяным каркасом изготавливаются по ТУ и в соответствии с назначением делятся на следующие классы:
✓ для подачи ацетилена, пропана, бутана или городского газа под давлением 0,63 МПа;
✓ для подачи жидкого топлива (керосина, бензина А-72 и др.) под давлением 0,63 МПа;
✓ для подачи кислорода под давлением 2 МПа.

Рис. 15. Устройство инжекторной горелки: 1 – мундштук; 2 – наконечник; 3 – смесительная камера; 4 – инжектор;
5 – кислородный вентиль; 6 – ниппель; 7 – ацетиленовый вентиль
Таблица 5
Основные параметры резиновых рукавов

Условное обозначение «Рукав I-16–0,63 ГОСТ 9356–74» расшифровывается следующим образом:
✓ I – класс;
✓ 16 – внутренний диаметр (выражен в мм);
✓ 0,63 – рабочее давление (МПа);
Отсутствие какой-либо буквы перед обозначением ГОСТа указывает на то, что рукав предназначен для использования в умеренном климате; если перед ним стоит буква Т – в тропическом; если буквы ХЛ – в холодном.
Рукав, так же как баллоны и редукторы, окрашивают в определенный цвет:
✓ красный – для рукавов I класса для ацетилена, пропана, бутана и городского газа;
✓ желтый – для рукавов II класса для жидкого топлива;
✓ синий – для рукавов III класса для кислорода.
Допускается использование черного цвета (для резиновых рукавов любого класса, предназначенных для работы в названных выше климатических условиях) или двух резиновых цветных полосок (для работы в любых климатических поясах).
7. Присадочный материал. Проволоку поставляют в мотках, поэтому ее разрезают на части необходимой длины. Как правило, присадочная проволока и свариваемый металл близки по химическому составу. Ее поверхность должна быть свободна от различных загрязнений (ржавчины и т. п.), расплавляться равномерно, с минимальным разбрызгиванием и давать однородный наплавленный металл без посторонних включений.
8. Флюсы (порошки, пасты). Чаще всего применяют буру, борный шлак, борную кислоту и т. д. При газовой сварке флюсом покрывают присадочную проволоку или пруток и вводят его в сварочную ванну. Состав флюса определяется видом и свойствами металла и подбирается так, чтобы он расплавлялся раньше металла, растекался, не воздействовал негативно на шов и качественно очищал металл от окислов.
По отраслевым стандартам каждому флюсу присваивается определенный номер, по которому становится понятным состав данного материала (табл. 6).
9. Сварочный стол.
10. Приспособления для сборки изделий.
11. Инструменты и принадлежности (очки и проч.).
Таблица 6
Флюсы, используемые при газовой сварке сталей

Сварочное пламя
При сгорании смеси горючего газа (это могут быть и пары горючей жидкости) с кислородом образуется так называемое сварочное пламя, свойства которого определяются двумя факторами:
✓ что используется в качестве горю чего;
✓ в каком соотношении находятся горючая смесь и кислород.
При варьировании количества кислорода, поступающего в горелку, получают пламя разного характера:
✓ нормальное;
✓ окислительное;
✓ науглероживающее.
Количественное соотношение между кислородом и ацетиленом выражается следующими формулами:
✓ для нормального пламени —

✓ для окислительного —

✓ для науглероживающего —

В каждом из них отчетливо различаются (рис. 16):
✓ зона ядра пламени. Его длина зависит от скорости истечения газовой смеси, она же определяет и устойчивость горения пламени (при недостаточной скорости оно сопровождается хлопками, а при чрезмерной – выталкивает металл из сварочной ванны);

Рис. 16. Разновидности ацетиленокислородного сварочного пламени: а – окислительное; б – нормальное; в – науглероживающее; 1 – зона ядра; 2 – восстановительная зона; 3 – окислительная зона
✓ восстановительная зона, которая, в отличие от других зон, окрашена в более темный цвет. Она простирается примерно на 20 мм от конца ядра. За счет этой зоны происходит нагревание и расплавление металла при сварке. Максимальная температура в ней сосредоточена в 2–6 мм от конца ядра;
✓ окислительная зона (факел), состоящая из углекислого газа, азота и водяных паров. Температура этой зоны более низкая, чем предыдущая.
В восстановительной зоне нормального пламени нет свободного углерода и кислорода; все зоны отчетливо выражены; ядро резко очерчено, на конце закругляется и имеет ярко светящуюся оболочку. Размер ядра может быть различным, что определяется рядом факторов: составом горючей смеси, ее расходом и скоростью истечения.
Для окислительного пламени характерен избыток кислорода, т. е. оно возникает, когда объем этого газа, поступающего в горелку, более чем в 1,3 раза превышает объем ацетилена.
Ядро окислительного пламени бывает более бледным, коротким и отличается конусовидной формой. Все пламя окрашено в синевато-фиолетовый цвет и сопровождается характерным звуком. Несмотря на то что его температура выше, чем у нормального пламени, для сварки сталей оно не подходит, поскольку вследствие окисления делает шов пористым и хрупким. Сфера его применения – сварка латуни и пайка твердыми припоями.
Если количество ацетилена превосходит количество кислорода, возникает науглероживающее пламя. Четкость очертаний для его ядра не свойственна, кончик ядра окрашен в зеленый цвет. Восстановительная зона настолько светлая, что практически сливается с ядром и имеет желтоватую окраску. Науглероживающее пламя коптит – сказывается избыток углерода. Это негативно сказывается на качестве металла шва.
Различные материалы свариваются конкретным видом пламени (окислительным, восстановительным или науглероживающим), который сварщик должен устанавливать на глаз.
Для выполнения газовой сварки требуется, чтобы пламя обладало необходимой тепловой мощностью, выбор которой определяется толщиной свариваемого металла и его физическими характеристиками. Мощность теплового пламени зависит от количества ацетилена, которое проходит через горелку. Для его регулировки используются наконечники.
Техника газовой сварки
Газовая сварка – способ универсальный, но при ее выполнении необходимо помнить, что нагреванию подвергается достаточно большой участок вокруг сварного соединения. Поэтому нельзя исключить возникновение коробления и развитие внутренних напряжений в конструкциях, причем они более значительные, чем при других способах сварки. В связи с этим газовая сварка в большей степени подходит для таких соединений, для которых достаточно небольшого количества наплавленного металла и малого нагрева основного металла. Прежде всего речь идет о стыковых, угловых и торцовых соединениях (независимо от их пространственного положения – нижнего, горизонтального, вертикального или потолочного), в то время как тавровых и нахлесточных следует избегать (хотя они тоже могут осуществляться).
Чтобы сварной шов отличался высокими механическими свойствами, требуется выполнить следующие действия:
✓ подготовить кромки металла;
✓ подобрать соответствующую мощность горелки;
✓ отрегулировать пламя горелки;
✓ взять необходимый присадочный материал;
✓ правильно сориентировать горелку и определить траекторию ее перемещения по выполняемому шву.
Как и при дуговой сварке, при газовой кромки свариваемого металла нужно подготовить. Их очищают (на 20–30 мм с каждой стороны) от ржавчины, влаги, масла и проч. Для этого достаточно прогреть кромки. В случае сварки цветных металлов используют механические и химические способы очистки.
При осуществлении стыковых соединений (табл. 7) следует помнить о некоторых правилах разделки кромок:
✓ при сваривании тонколистового металла (до 2 мм) присадки не используют – достаточно выполнить отбортовку кромок, которые потом расплавляются и дают валик сварного шва. Возможен и такой вариант: сварить кромки встык без разделки и зазора, но с применением присадочного материала;
Таблица 7
Предварительная подготовка кромок свариваемого металла при выполнении стыковых соединений


Примечание: a – величина зазора; a1 – величина притупления; S и S1 – толщина металла.
✓ при сваривании металла толщиной менее 5 мм можно обойтись без скоса кромок и вести одностороннюю газовую сварку;
✓ при соединении металла толщиной более 5 мм кромки скашивают под углом в 35–40°, чтобы общий угол раскрытия шва составлял 70–90°. Это позволит проварить металл на всю толщину.
При выполнении угловых соединений присадочный материал не используют, а шов формируют расплавлением кромок металла.
Нахлесточные и тавровые соединения допускаются исключительно при сварке металла толщиной до 3 мм, поскольку при большей толщине локальный нагрев металла бывает неравномерным, что приводит к развитию значительных внутренних напряжений и деформаций, а также к появлению трещин как в металле шва, так и в основном металле.
Чтобы в процессе сварки детали не сдвигались и зазор между ними не изменялся, их фиксируют либо специальными приспособлениями, либо прихватками. Длина, количество и промежуток между последними зависят от толщины металла, длины и конфигурации шва:
✓ если металл тонкий, а швы короткие, длина прихваток составляет 5–7 мм при интервале между ними в 70–100 мм;
✓ если металл толстый, а швы длинные, то длину прихваток увеличивают до 20–30 мм, а расстояние между ними – до 300–500 мм.
В процессе сварки пламя горелки направляют на металл таким образом, чтобы он попадал в восстановительную зону и находился в 2–6 мм от ядра. При сварке легкоплавких металлов пламя горелки в основном ориентируют на присадочный материал, а зону ядра отодвигают на еще большее расстояние от сварочной ванны.

Рис. 17. Способы регулировки скорости нагрева и плавления металла путем изменения: а – угла наклона мундштука; б – траектории движения мундштука и проволоки; 1 – при сварке тонколистового металла;2, 3 – при сварке толстолистового металла
При сварке необходимо регулировать скорость нагрева и плавления металла. Для этого прибегают к таким действиям (рис. 17):
✓ изменяют угол наклона мундштука;
✓ манипулируют самим мундштуком.
При сварке необходимо следить за тем, чтобы:
✓ ядро пламени не контактировало с расплавленным металлом, поскольку последний может от этого науглероживаться;
✓ сварочная ванна была защищена зоной факела и восстановительной зоной, иначе металл будет окисляться атмосферным кислородом.
В процессе использования газовой горелки необходимо соблюдать правила обращения с ней:
1. Если горелка находится в исправном состоянии, то пламя, которое она дает, бывает устойчивым. В том случае, если наблюдаются какие-либо отклонения (горение нестабильное, пламя отрывается или гаснет, случаются обратные удары), надо обратить особое внимание на узлы горелки и отрегулировать ее.
2. Чтобы проверить инжекторную горелку, подсоединяют кислородный рукав, к корпусу крепят наконечник. После затягивания накидной гайки аккуратно откручивают ацетиленовый вентиль, кислородным редуктором устанавливают соответствующее давление кислорода, после чего открывают кислородный вентиль.
3. Если приставленный к ацетиленовому ниппелю палец присасывается, это означает, что кислород создает разряжение. Если этого не происходит, возможно, засорились инжектор, смесительная камера или мундштук. Их следует прочистить.
4. Повторить проверку на разряжение (подсос). Его величина определяется зазором между концом инжектора и входом в смесительную камеру. Выкручивая инжектор, зазор регулируют.
5. Категорически запрещено использовать неисправные горелки.

Рис. 18. Способы газовой сварки (стрелкой указано направление сварки): а – левый; б – правый; 1 – присадочная проволока; 2 – сварочная горелка
Различают два способа газовой сварки (рис. 18):
✓ левую сварку, при которой горелку перемещают справа налево и держат позади присадочной проволоки. При этом сварочное пламя ориентировано на еще не сваренный шов. Этот способ не позволяет в достаточной степени защитить металл от окисления, сопровождается частичной потерей тепла и дает низкую производительность сварки;
✓ правую сварку, при которой горелку перемещают слева направо и держат впереди присадочной проволоки. В этом случае пламя ориентировано на законченный шов и конец присадочной проволоки. Такой способ дает возможность направить на расплавление металла сварочной ванны большее количество теплоты, а колебательные поперечные движения мундштука и проволоки осуществляются реже, чем при левом способе. Кроме того, конец присадочной проволоки оказывается постоянно погруженным в сварочную ванну, поэтому им можно перемешивать ее, что способствует переходу окислов в шлак.
Правый способ обычно применяют, если толщина свариваемого металла превышает 5 мм, тем более что при этом сварочное пламя по бокам ограничено кромками изделия, а сзади – валиком наплавленного металла. Благодаря этому потери теплоты снижаются, и она используется более эффективно.
Левый способ имеет свои преимущества, поскольку, во-первых, шов все время находится в поле зрения сварщика и он может регулировать его высоту и ширину, что имеет особое значение при сварке тонколистового металла; во-вторых, при сварке пламя может растекаться по поверхности металла, снижая риск пережога.
При выборе того или иного способа сварки нужно руководствоваться и пространственным положением сварного шва:
✓ при выполнении нижнего шва следует учитывать толщину металла. Его можно накладывать и правым, и левым способом. Данный шов наиболее легкий, поскольку сварщик может наблюдать за процессом. Кроме того, жидкий присадочный материал стекает в кратер и не выливается из сварочной ванны;
✓ для горизонтального шва предпочтителен правый способ. Чтобы не допустить вытекания жидкого металла, стенки сварочной ванны делают с некоторым перекосом;
✓ для вертикального шва на подъем – и левый, и правый, а для вертикального шва на спуск – только правый способ;
✓ потолочный шов легче накладывать правым способом, поскольку поток пламени направлен на шов и не дает жидкому металлу вытечь из сварочной ванны.
Способом, гарантирующим высокое качества сварного шва, является сварка ванночками (рис. 19).
Данный метод применяют для сварки тонколистового металла и труб из низкоуглеродистых и низколегированных сталей облегченными швами. Им можно воспользоваться и при сварке стыковых и угловых соединений при толщине металла до 3 мм.

Рис. 19. Сварка ванночками: 1 – направление сварки; 2 – траектория движения присадочной проволоки; 3 – траектория движения мундштука
Процесс сварки ванночками протекает следующим образом:
1. Расплавив металл диаметром 4–5 мм, сварщик помещает в него конец присадочной проволоки. Когда ее конец расплавится, он вводит его в восстановительную зону пламени.
2. Одновременно с этим сварщик, чуть сместив мундштук, совершает им круговые движения, чтобы образовать очередную ванночку, которая должна несколько (примерно на треть диаметра) перекрывать предыдущую. При этом проволоку надо продолжать держать в восстановительной зоне, чтобы не допустить ее окисления. Ядро пламени нельзя погружать в сварочную ванну, иначе произойдет науглероживание металла шва.
При газовой сварке швы бывают одно– или многослойными. Если толщина металла составляет 8–10 мм, швы наваривают в два слоя, при толщине более 10 мм – три слоя и более, причем каждый предыдущий шов предварительно очищают от шлака и окалины.
Многопроходные швы при газовой сварке не практикуют, поскольку наложить узкие валики очень тяжело.
При газовой сварке возникают внутренние напряжения и деформации, поскольку участок нагрева оказывается более обширным, чем, например, при дуговой сварке. Для уменьшения деформаций необходимо принимать соответствующие меры. Для этого рекомендуют:
✓ равномерно нагревать изделие;
✓ подбирать адекватный режим сварки;
✓ равномерно распределять наплавленный металл по поверхности;
✓ придерживаться определенного порядка наложения швов;
✓ не увлекаться выполнением прихваток.
Для борьбы с деформациями применяют разные способы:
1. При выполнении стыковых соединений сварной шов накладывают обратноступенчатым или комбинированным способом, разделив его на участки длиной 100–250 мм (рис. 20). Поскольку теплота равномерно распределяется по поверхности шва, основной металл практически не подвержен короблению.
2. Уменьшению деформаций способствует их уравновешивание, когда последующий шов вызывает деформации, обратные тем, которые вызвал предыдущий шов.
3. Находит применение и способ обратных деформаций, когда перед сваркой детали укладывают так, чтобы после нее в результате действия деформаций они заняли нужное положение.

Рис. 20. Последовательность наложения шва при сварке стыковых соединений: а – от кромки; б – от середины шва
4. Бороться с деформациями помогает и предварительный нагрев соединяемых изделий, в результате чего достигается меньшая разность температур между сварочной ванной и изделием.
Этот способ хорошо работает при ремонте чугунных, бронзовых и алюминиевых изделий, а также в том случае, если они изготовлены из высокоуглеродистых и легированных сталей.
5. В ряде случаев прибегают к проковке сварного шва (в холодном или горячем состоянии), что улучшает механические характеристики шва и снижает усадку.
6. Термическая обработка – еще один способ устранения развившихся напряжений. Она бывает предварительной, проводится одновременно со сваркой или ей подвергают уже готовое изделие. Режим термической обработки определяют форма деталей, свойства свариваемых металлов, условия и проч.
Внимание! Это не конец книги.
Если начало книги вам понравилось, то полную версию можно приобрести у нашего партнёра - распространителя легального контента. Поддержите автора!Правообладателям!
Данное произведение размещено по согласованию с ООО "ЛитРес" (20% исходного текста). Если размещение книги нарушает чьи-либо права, то сообщите об этом.Читателям!
Оплатили, но не знаете что делать дальше?