Текст книги "Контроль качества сварки"
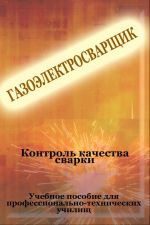
Автор книги: Илья Мельников
Жанр: Хобби и Ремесла, Дом и Семья
Возрастные ограничения: +12
сообщить о неприемлемом содержимом
Текущая страница: 1 (всего у книги 2 страниц) [доступный отрывок для чтения: 1 страниц]
Илья Мельников
Контроль качества сварки
КЛАССИФИКАЦИЯ ДЕФЕКТОВ
В процессе образования сварного соединения в металле шва и зоне термического влияния могут возникать дефекты, т. е. отклонения от установленных норм и требований, приводящие к снижению прочности, эксплуатационной надежности, точности, а также ухудшению внешнего вида изделия. Дефекты сварных соединений различают по причинам возникновения и месту их расположения.
В зависимости от причин возникновения их можно разделить на две группы. К первой группе относятся дефекты, связанные с металлургическими и тепловыми явлениями, происходящими в процессе образования, формирования и кристаллизации сварочной ванны и остывания сварного соединения: горячие и холодные трещины в металле шва и околошовной зоне, поры, шлаковые включения, неблагоприятные изменения свойств металла шва и зоны термического влияния.
Ко второй группе дефектов, которые называют дефектами формирования швов, относят дефекты, происхождение которых связано в основном с нарушением режима сварки, неправильной подготовкой и сборкой элементов конструкции под сварку, неисправностью оборудования, небрежностью и низкой квалификацией сварщика и другими нарушениями технологического процесса. К дефектам этой группы относятся несоответствие швов расчетным размерам, непровары, подрезы, прожоги, наплывы, незаваренные кратеры и др.
Дефекты сварных швов являются следствием неправильного выбора или нарушения технологического процесса, применения некачественных сварочных материалов и низкой квалификации сварщика.
Дефекты разделяются на внешние и внутренние. К внешним относятся: нарушение установленных размеров и формы шва, непровар, подрез зоны сплавления, поверхностное окисление, прожог, наплыв, поверхностные поры, незаваренные кратеры и трещины на поверхности шва. К внутренним дефектам относятся: внутренние поры, неметаллические включения, непровар и внутренние трещины.
Нарушение установленных размеров и формы шва выражается в неполномерности ширины и высоты шва, в чрезмерном усилении и резких переходах от основного металла к наплавленному. Эти дефекты при ручной сварке являются результатом низкой квалификации сварщика, плохой подготовки свариваемых кромок, неправильного выбора сварочного тока, низкого качества сборки под сварку. Дефекты формы шва могут быть и следствием колебания напряжения в сети. При автоматической сварке нарушения формы и размеров шва являются следствием неправильной разделки шва или нарушения режима в процессе сварки – скорости сварки, скорости подачи электродной проволоки, сварочного тока.
Непровар (местное несплавление свариваемых кромок основного и наплавленного металла) – следствие низкой квалификации сварщика, некачественной подготовки свариваемых кромок (малый угол скоса, отсутствие зазора, большое притупление), смещения электрода к одной из кромок, быстрого перемещения электрода по шву.
Подрез зоны (узкие углубления в основном металле вдоль края сварного шва) образуется при сварке большим током или удлиненной дугой, при завышенной мощности горелки, неправильном положении электрода или горелки и присадочного прутка.
Поверхностное окисление – окисление металла шва и прилегающего к нему основного металла. Причины: сильно окисляющая среда, большая длина дуги, чрезмерно большая мощность сварочной горелки или слишком большой сварочный ток, замедленное перемещение электрода или горелки вдоль шва.
Прожог – сквозное отверстие в сварном шве. Основные причины прожога: большой сварочный ток, завышенная мощность сварочной горелки, малая толщина основного металла, малое притупление свариваемых кромок и неравномерный зазор между ними по длине.
Наплывы – результат натекания наплавленного металла на непрогретую поверхность основного металла или ранее выполненного валика без сплавления с ним. Такие дефекты могут быть при низкой квалификации сварщика, недоброкачественных электродах и несоответствии скорости сварки и сварочного тока разделке шва.
Поверхностные и внутренние поры возникают вследствие попадания в металл шва газов (водород, азот, углекислый газ и др.), образовавшихся при сварке. Водород образуется из влаги, масла и компонентов покрытия электродов. Азот в металл шва попадает из атмосферного воздуха при недостаточно качественной защите расплавленного металла шва. Оксид углерода образуется в процессе сварки стали при выгорании углерода, содержащегося в металле. Если свариваемая сталь и электроды имеют повышенное содержание углерода, то при недостатке в сварочной ванне раскислителей и при большой скорости сварки оксид углерода не успевает выделиться и остается в металле шва. Таким образом, пористость является результатом плохой подготовки свариваемых кромок (загрязненность, ржавчина, замасленность), применения электродов с сырым покрытием, влажного флюса, недостатка раскислителей, больших скоростей сварки.
Неметаллические включения образуются при сварке малым сварочным током, при применении недоброкачественных электродов, сварочной проволоки, флюса, загрязненных кромок и плохой очистке шва от шлака при многослойной сварке. При неправильно выбранном режиме сварки шлаки и оксиды не успевают всплыть на поверхность и остаются в металле шва в виде неметаллических включений.
Трещины, наружные и внутренние являются опасными и недопустимыми дефектами сварных швов. Они образуются вследствие напряжений, возникающих в металле от его неравномерного нагрева, охлаждения и усадки. Высокоуглеродистые и легированные стали после сварки при охлаждении закаливаются, в результате чего могут образоваться трещины. Причина возникновения трещин – повышенное содержание в стали вредных примесей (серы и фосфора).
МЕТОДЫ УСТРАНЕНИЯ ДЕФЕКТОВ СВАРНЫХ ШВОВ
Неполномерность швов устраняется наплавкой дополнительного слоя металла. При этом наплавляемую поверхность необходимо тщательно очистить до металлического блеска абразивным инструментом или металлической щеткой. Чрезмерное усиление шва устраняют с помощью абразивного инструмента или пневматического зубила.
Непровар, кратеры, пористость и неметаллические включения устраняют путем вырубки пневматическим зубилом или расчистки абразивным инструментом всего дефектного участка с последующей заваркой. Часто применяют выплавку дефектного участка резаком поверхностной кислородной или воздушно-дуговой резки.
Подрезы заваривают тонкими валиковыми швами. Наплывы устраняются обработкой абразивным инструментом или с помощью пневматического зубила.
Наружные трещины устраняются разделкой и последующей заваркой. Для предупреждения распространения трещины по концам ее сверлят отверстия. Разделку трещины выполняют зубилом или резаком. Кромки разделки зачищают от шлака, брызг металла, окалины и заваривают. Швы с внутренними трещинами вырубают и заваривают заново. При наличии сетки трещин дефектный участок вырезают и взамен сваркой накладывают заплату.
СПОСОБЫ КОНТРОЛЯ СВАРНЫХ СОЕДИНЕНИЙ
Сварные соединения считают качественными, если они не имеют недопустимых дефектов и их свойства удовлетворяют требованиям, предъявляемым к ним в соответствии с условиями эксплуатации сварного узла или конструкции.
Качество сварных соединений контролируют следующими видами контроля:
– предварительным, в процессе которого выполняют проверку качества исходных материалов (свариваемого металла и сварочных материалов), контроль подготовки деталей под сварку и сборку узлов, а также состояния оснастки, сварочного оборудования и приборов, квалификации сборщиков и сварщиков; на стадии предварительного контроля выполняют испытания на свариваемость, включающие в себя механические испытания, металлографические исследования сварных соединений и испытания на сопротивляемость образованию горячих и холодных трещин;
– текущим (в процессе выполнения сварочных работ), предусматривающим проверку соблюдения технологии сварки, зачистки промежуточных швов, заварку кратеров и т. д.;
– окончательным контролем готовых сварных конструкций, который проводится в соответствии с требованиями, предъявляемыми к изделию.
Трудоемкость контрольных операций может доходить до 30% общей трудоемкости изготовления сварной конструкции.
Итак, контроль надо осуществлять, начиная с проверки качества подготовки шва и кончая проверкой полученного сварного соединения. Качество основного металла, электродной проволоки, присадочного металла, флюса и других материалов проверяют по сертификатам и заводским документам. Маркировка и качество должны соответствовать установленным техническим условиям и технологическому процессу сварки. Сборку под сварку и разделку шва проверяют по стандартам и техническим условиям.
Сварное соединение проверяется внешним осмотром, металлографическими исследованиями, химическим анализом, механическими испытаниями, просвечиванием рентгеновскими лучами и гамма-излучением, магнитными методами и с помощью ультразвука. Предварительно сварное соединение очищают от шлака, окалины и металлических брызг.
Внешний осмотр выявляет наружные дефекты шва. Осмотр производят невооруженным глазом или с помощью лупы с десятикратным увеличением. Размеры сварных швов проверяют шаблонами и мерительным инструментом.
Металлографические исследования начинают с засверливания и последующего травления поверхности отверстия в течение 1-3 мин 10 %-ным водным раствором двойной соли хлорной меди и аммония. Осадок меди удаляют водой. Засверленная поверхность должна захватывать шов и основной металл. Протравленную поверхность осматривают невооруженным глазом или с помощью лупы. При этом выявляют качество провара и отсутствие внутренних дефектов. Для ответственных сварных конструкций производят более полные металлографические исследования. Для этой цели приготовляют макро– и микрошлифы из специально сваренных контрольных пластин или из пластин, вырезанных из сварных соединений.
Химический анализ определяет состав основного и наплавленного металла и электродов, а также их соответствие установленным техническим условиям на изготовление сварного изделия. Методы отбора проб для химического и спектрального анализов предусмотрены ГОСТом.
Механические испытания сварного соединения производят либо на специально сваренных контрольных образцах, либо на образцах, вырезанных из сварного соединения. Определяют предел прочности на растяжение, ударную вязкость, твердость и угол загиба.
Рентгенодефектоскопия основана на различном поглощении лучей металлом и неметаллическими включениями. Этим методом обнаруживают поры, трещины, непровары, шлаковые включения. Рентгеновские лучи направляют на сварной шов, а с обратной стороны прикладывают рентгеновскую или фотографическую пленку со светочувствительной эмульсией. Дефектные места шва пропускают лучи с меньшим поглощением, чем сплошной металл. После проявления на пленке хорошо видны очертания дефектов шва.
Рентгеновская трубка изолируется защитным свинцовым кожухом, в котором имеется узкая щель для выхода лучей, направляемых на контролируемое изделие. Для контроля в монтажных условиях очень удобны малогабаритные отечественные рентгеновские аппараты типов РУП-120-5-1, ИРА-1Д, ИРА-2Д, РИНА-ЗД и др. Толщина металла, которая может контролироваться этими аппаратами, 25-100 мм.
Просвечивание гамма-излучением также основано на различном поглощении лучей металлом и неметаллическими включениями. Гамма-излучение действует на пленку так же, как ирентгеновские, показывая очертания дефектов сварного шва. Гамма-излучение получается при ядерном распаде естественных и искусственных радиоактивных веществ (радия, мезатория, кобальта, цезия, иридия и др.). Наибольшее распространение получили более дешевые радиоактивные изотопы кобальта бОСо, цезия 137Cs и иридия 1921г. Гамма-излучение обладает большой проникающей способностью и позволяют контролировать металл толщиной до 350 мм. Гамма-просвечивание значительно проще, чем просвечивание рентгеновскими лучами, однако гамма-излучение вредно для человека. Поэтому ампула с радиоактивным веществом помещается в специальные переносные свинцовые контейнеры или в стационарные аппараты с дистанционным управлением. Контейнер устанавливают против контролируемого участка, а с обратной стороны сварного шва помещают кассету с пленкой. Затем с помощью дистанционного управления выдвигают ампулу из аппарата или открывают щель в контейнере для выхода гамма-излучения.
Магнитные методы контроля основаны на создании неоднородного магнитного поля с образованием потоков рассеяния в местах расположения дефектов шва при намагничивании контролируемого изделия. Применяются метод порошковой дефектоскопии, магнитографический метод, индукционный и др.
Метод порошковой дефектоскопии является наиболее простым, но и менее четким. После намагничивания изделия сварной шов опыливают магнитным порошком из железной окалины или покрывают суспензией магнитного порошка (смесь с керосином, маслом или другими веществами). На поверхности изделия порошок распределяется неравномерно, а по скоплениям порошка определяют расположение дефектов в сварном шве. Для большей наглядности магнитный порошок или суспензию окрашивают в яркие цвета.
Магнитографический контроль применяется при контроле сварных швов магистральных трубопроводов. Метод заключается в следующем: состояние сварного шва записывают на специальную пленку, применяемую для магнитной звукозаписи. Для этого на сварной шов трубы накладывают ферромагнитную пленку, а затем намагничивают шов соленоидом или обкатывают дисковым магнитом. В зависимости от вида и дефектов шва в соответствующих местах пленки будет та или иная степень намагниченности. Для воспроизведения записанных на пленку дефектов ее пропускают через специальное устройство, преобразующее магнитную запись в звуковую (магнитофон) или электрическую (электрофонный осциллограф). Наиболее совершенные аппараты для магнитографического контроля содержат осциллографы, они позволяют проверять сварные швы со скоростью 0,5-1 м/мин. Кроме высокой производительности, этот метод отличается большой точностью (не уступающей рентгеновскому и гамма-просвечиванию), простотой выполнения, дешевизной применяемых материалов, возможностью проверки швов в различных пространственных положениях и безопасностью работы.
Индукционный метод контроля основан на использовании магнитного потока, рассеиваемого в местах расположения дефектов шва, для наведения электродвижущей силы в специальной катушке, передвигаемой вдоль свариваемых кромок изделия. Наведенный индукционный ток усиливается и подается на телефон, сигнальную лампу или специальный магнитоэлектрический прибор. По звуку, отклонению стрелки прибора или зажиганию специальной лампы определяют расположение дефекта. Индукционный контроль производят дефектоскопом типа МД-138.
Ультразвуковой метод контроля основан на способности ультразвуковых колебаний проникать в толщу металла на значительную глубину и отражаться от неметаллических включений и других дефектных участков шва. Ультразвуковые дефектоскопы работают по следующему принципу. Пластинка из кварца или сегнетовой соли под действием переменного электрического поля высокой частоты дает ультразвуковые колебания, которые с помощью щупа направляются на проверяемое сварное соединение. На границе между однородным металлом и дефектом эти волны частично отражаются и воспринимаются второй пластинкой. Под действием переменного давления ультразвуковой волны на гранях этой пластинки появляется переменная разность потенциалов, зависящая от интенсивности отраженной волны. Электрические колебания от граней пластинки усиливаются и направляются в осциллограф. На экране осциллографа одновременно изображаются импульсы излучаемой и отражаемой от дефектов волн. По относительному расположению этих импульсов и по интенсивности отраженного импульса можно судить о местонахождении и характере дефекта в сварном шве.
В настоящее время выпускают ультразвуковые дефектоскопы, работающие на одной пластинке, которая подает короткими импульсами ультразвуковые волны на контролируемый шов. Отраженные волны воспринимаются этой же пластинкой в промежутки времени между импульсами излучения. При этом получается высокая четкость излучаемых и отраженных ультразвуковых волн. Ультразвуковой метод контроля позволяет обнаружить все основные дефекты сварных швов. Кроме того, ультразвуковые дефектоскопы типа УЗД-7н имеют специальное приспособление для настройки на заданную толщину шва и определения глубины расположения обнаруженного дефекта. Недостатками ультразвукового контроля являются трудности проверки швов толщиной менее 10 мм и определения характера дефекта.
ИСПЫТАНИЯ СВАРНЫХ ШВОВ НА НЕПРОНИЦАЕМОСТЬ
Испытание керосином применяют для контроля сварных швов емкостей, работающих без избыточного давления. Сварной шов с внешней стороны покрывают водным раствором мела. После высыхания покрытия шов с внутренней стороны смачивают керосином. При наличии даже мельчайших пор, трещин или неплотностей керосин просачивается через них и на покрытой мелом поверхности появляются темные пятна. Время выдержки (0,5-1 ч) зависит от толщины металла и температуры воздуха. Для ответственных швов время выдержки составляет 12-24 ч.
Испытание сжатым воздухом производят нагнетанием в испытываемый резервуар сжатого воздуха до давления, указанного в технических условиях на изготовление резервуара. Швы покрывают мыльной эмульсией и по мыльным пузырям определяют наличие в них дефектов. Если габариты позволяют погрузить испытываемый резервуар в ванну с водой, то дефекты определяются по пузырькам воздуха. Трубопроводы и большие резервуары испытывают сжатым воздухом на потерю давления за время, установленное техническими условиями.
Вакуум-аппарат применяют при контроле сварных швов, имеющих односторонний доступ, когда невозможно использовать керосин, воздух или воду. Аппарат состоит из камеры с вакуумметром и насоса. Контролируемый сварной шов покрывают мыльной эмульсией, на нее устанавливают камеру и включают насос, который создает вакуум в камере. Для герметичности камера имеет в торце мягкую резиновую прокладку. Если шов имеет дефекты (поры, трещины, неплотности), то образуются мыльные пузыри, которые наблюдаются через стекло, камеры.
Испытание аммиаком производят путем нагнетания в испытываемый резервуар воздуха до рабочего давления или давления, указанного в технических условиях на изготовление изделия. Затем добавляют 1 % аммиака от объема воздуха в резервуаре при нормальном давлении. Контролируемые сварные швы обертывают бумагой, пропитанной 5 %-ным водным раствором азотнокислой ртути. При наличии неплотности (поры, трещины и др.) аммиак проходит через них и, взаимодействуя с азотнокислой ртутью, дает на бумаге черные пятна.
Гидравлическое испытание производят с целью проверки не только плотности швов, но и их прочности. Такому испытанию подвергают сварные трубопроводы, сосуды и резервуары для газа или жидкости, работающие под давлением. Для этой цели все отверстия изделия плотно закрывают заглушками и заполняют его водой. С помощью гидравлического пресса создают давление в 1,5 раза превышающее рабочее давление изделия и выдерживают в течение времени, указанного в технических условиях на изготовление изделия. Затем снижают давление до рабочего значения и проверяют наличие потения и пропусков воды в швах. При этом производят обстукивание изделия молотком на расстоянии 20 мм от сварного шва. Вертикальные цилиндрические резервуары обстукивать при испытании водой не разрешается.
Для контроля сварных соединений магистральных трубопроводов используют передвижную лабораторию РМЛ2В, смонтированную на автомашине. Оборудование состоит из рентгеновской установки, позволяющей просвечивать стыки трубопроводов диаметром 720-1420 мм, гамма-дефектоскопа и установки для магнитографического контроля. За смену лаборатория проверяет при гамма-просвечивании 6 стыков, при рентгеновском – 12; при магнитографическом контроле – до 20.
ТЕХНИКА БЕЗОПАСНОСТИ
ТЕХНИКА БЕЗОПАСНОСТИ ПРИ ЭЛЕКТРИЧЕСКОЙ СВАРКЕ
При электросварочных работах возможны следующие виды производственного травматизма: поражение электрическим током; поражение зрения и открытой поверхности кожи лучами электрической дуги; ожоги от капель металла и шлака; отравление организма вредными газами, пылью и испарениями, выделяющимися при сварке; ушибы, ранения и поражения от взрывов баллонов сжатого газа и при сварке сосудов из-под горючих веществ.
Защита от поражения электрическим током. При исправном состоянии оборудования и правильном выполнении сварочных работ возможность поражения током исключается. Однако в практике возможны поражения электрическим током вследствие неисправности сварочного оборудования или сети заземления; неправильного подключения сварочного оборудования к сети; неисправности электропроводки и неправильного ведения сварочных работ. Поражение от электрического тока происходит при прикосновении к токонесущим частям электропроводки и сварочной аппаратуры.
Напряжение холостого хода источников питания дуги достигает 90 В, а при плазменно-дуговой резке – 200 В. Учитывая, что сопротивление человеческого организма в зависимости от его состояния (утомленность, состояние здоровья, влажность кожи) может изменяться в пределах от 1000 до 20 000 Ом, указанные выше напряжения являются очень опасными для жизни. Поражение током более 0,05 А может вызвать тяжелые последствия и даже смерть.
Опасность поражения сварщика и подсобных рабочих током особенно велика при сварке крупногабаритных резервуаров, во время работы внутри емкостей лежа или полулежа на металлических частях свариваемого изделия или при выполнении наружных работ в сырую погоду, в сырых помещениях, котлованах, колодцах и др.
Во избежание поражения электрическим током необходимо соблюдать следующие условия. Корпуса источников питания дуги, сварочного вспомогательного оборудования и свариваемые изделия должны быть надежно заземлены. Заземление осуществляют медным проводом, один конец которого закрепляют к корпусу источника питания дуги к специальному болту с надписью "Земля", второй конец присоединяют к заземляющей шине или к металлическому штырю, вбитому в землю.
Заземление передвижных источников питания производится до их включения в силовую сеть, а снятие заземления – после отключения от силовой сети.
Для подключения источников сварочного тока к сети используются настенные ящики с рубильниками, предохранителями и зажимами. Длина проводов сетевого питания не должна быть более 10 м. Для того чтобы нарастить провод, применяют соединительную муфту с прочной изоляционной массой или провод с электроизоляционной оболочкой. Провод подвешивают на высоте 2,5-3,5 м. Спуски заключают в заземленные металлические трубы. Вводы и выводы должны иметь втулки или воронки, предохраняющие провода от перегибов, а изоляцию – от порчи.
Сварочное оборудование должно находиться под навесом, в палатке или в будке для предохранения от дождя и снега. При невозможности соблюдения таких условий сварочные работы не производят, а сварочную аппаратуру укрывают от воздействия влаги.
Присоединять и отсоединять от сети электросварочное оборудование, а также наблюдать за их исправным состоянием в процессе эксплуатации обязан электротехнический персонал. Сварщикам запрещается выполнять эти работы.
Все сварочные провода должны иметь исправную изоляцию и соответствовать применяемым токам. Применение проводов с ветхой и растрепанной изоляцией категорически запрещается.
При сварке швов резервуаров, котлов, труб и других закрытых и сложных конструкций необходимо пользоваться резиновым ковриком, шлемом и галошами. Для освещения следует пользоваться переносной лампой напряжением 12 В.
Все сварочные установки при работе в условиях, требующих особой электробезопасности, должны иметь устройство для автоматического отключения сварочной цепи или снижения напряжения холостого хода при обрыве дуги до 12 В с выдержкой не более 5 с. Большое применение получили устройства типа УСНТ (УСНТ-05, УСНТ-06 и др.). При холостом ходе первичная обмотка трансформатора питается через ограничительные резисторы типа УСНТ и напряжение питания снижается до 60-80 В, а вторичное напряжение холостого хода до 12 В. При возбуждении дуги коротким замыканием резисторы шунтируются тиристорами и на трансформатор подается полное сетевое напряжение. После прекращения сварки через 0.5-1 с снова включаются ограничительные резисторы и напряжение холостого хода снижается до 12В.
При работах внутри резервуара или при сварке сложной конструкции, а также при сварке емкостей из-под горючих и легковоспламеняющихся жидкостей к сварщику назначается дежурный наблюдатель, который обязан обеспечить безопасность работ и при необходимости оказать первую помощь.
При поражении электрическим током пострадавшему необходимо оказать первую помощь: освободить его от электропроводов; обеспечить доступ свежего воздуха и, если пострадавший потерял сознание, немедленно вызвать скорую медицинскую помощь. При необходимости, до прибытия врача надо производить искусственное дыхание.
Защита зрения и открытой поверхности кожи от лучей электрической дуги. Горение сварочной дуги сопровождается излучением видимых ослепительно ярких световых лучей и невидимых ультрафиолетовых и инфракрасных лучей.
Яркость видимых лучей значительно превышает норму, допускаемую для человеческого глаза, и поэтому, если смотреть на дугу невооруженным глазом, то она производит ослепляющее действие. Ультрафиолетовые лучи даже при кратковременном действии в течение нескольких секунд вызывают заболевание глаз, называемое электрофтальмией. Оно сопровождается острой болью, резью в глазах, слезотечением, спазмами век. Продолжительное облучение ультрафиолетовыми лучами вызывает ожоги кожи.
Инфракрасные лучи при длительном воздействии вызывают помутнение хрусталиков глаза (катаракту), что может привести к временной и даже полной потере зрения. Тепловое действие инфракрасных лучей вызывает ожоги кожи лица.
Для защиты зрения и кожи лица от световых и невидимых лучей дуги электросварщики и их подручные должны закрывать лицо щитком, маской или шлемом, в смотровые отверстия которых вставлено специальное стекло – светофильтр. Светофильтр выбирают в зависимости от сварочного тока и вида сварочных работ.
Для защиты окружающих лиц от воздействия излучений в стационарных цехах устанавливают закрытые сварочные кабины, а при строительных и монтажных работах применяются переносные щиты или ширмы.
Защита от брызг металла и шлака. В процессе сварки и при уборке и обивке шлака капли расплавленного металла и шлака могут попасть в складки одежды, карманы, ботинки, прожечь одежду и причинить ожоги. Во избежание ожогов сварщик должен работать в спецодежде из брезента или плотного сукна, в рукавицах и головном уборе. Куртку не следует заправлять в брюки. Карманы должны быть плотно закрыты клапанами. Брюки надо носить поверх обуви. При сварке потолочных, горизонтальных и вертикальных швов необходимо надевать брезентовые нарукавники и плотно завязывать их поверх рукавов у кистей рук. Зачищать швы от шлака и флюса следует лишь после их полного остывания и обязательно в очках с простыми стеклами.
Защита от отравлений вредными газами. Особенное загрязнение воздуха вызывает сварка электродами. Состав пыли и газов определяется содержанием покрытия и составом свариваемого и электродного (или присадочного) металла. При автоматической сварке количество газов и пыли значительно меньше, чем при ручной сварке.
Сварочная пыль (аэрозоль) представляет собой смесь мельчайших частиц окислов металлов и минералов. Основными составляющими являются оксиды железа (до 70 %), марганца, кремния, хрома, а также фтористые и другие соединения. Наиболее вредными веществами, входящими в состав покрытия, флюса и металла электрода, являются хром, марганец и фтористые соединения. Кроме аэрозоли, воздух в рабочих помещениях при сварке загрязняется различными вредными газами, например оксидами азота, углерода, фтористым водородом и др. На рабочем месте допускаются следующие предельные концентрации веществ в воздухе (мг/м3): марганец и его соединения – 0,3; хром и его соединения – 0,1; свинец и его соединения – 0,01; цинковые соединения – 5,0; оксид углерода – 20,0; фтористый водород – 0,5; окись азота – 5,0; бензин, керосин – 300,0.
Концентрация нетоксичной пыли более 10 мг/м3 не допускается. Однако если содержание кварца в пыли превышает 10 %, то концентрация нетоксичной пыли допускается только до 2 мг/м3.
Удаление вредных газов и пыли из зоны сварки, а также подача чистого воздуха осуществляется местной и общей вентиляцией. При оборудовании сварочных кабин обязательно предусматривается местная вытяжная вентиляция с верхним, боковым или нижним отсосом, удаляющая газы и пыль непосредственно из зоны сварки. Общая вентиляция должна быть приточно-вытяжной, производящей отсос загрязненного воздуха из рабочих помещений и подачу свежего. В зимнее время воздух подогревают до температуры 20-22 °С с помощью специального нагревателя-калорифера.
При сварке в закрытых резервуарах и замкнутых конструкциях необходимо обеспечить подачу свежего воздуха под небольшим давлением по шлангу непосредственно в зону дыхания сварщика. Объем подаваемого свежего воздуха должен быть не менее 30 м3/ч. Без вентиляции сварка в закрытых резервуарах и конструкциях не разрешается.
Вентиляционные устройства должны обеспечить воздухообмен при ручной электродуговой сварке электродами с качественными покрытиями 4000-6000 м3 на 1 кг расхода электродов, при автоматической сварке под флюсом – около 200 м3 на 1 кг расплавляемой проволоки, при сварке в углекислом газе до 1000 м3 на 1 кг расплавляемой проволоки.
Предотвращение взрывов. Взрывы возможны при неправильных транспортировке, хранении и использовании баллонов со сжатыми газами, при сварочных работах в различных емкостях без предварительной тщательной их очистки от остатков горючих веществ.
Баллоны транспортируют с навернутыми предохранительными колпаками на подрессоренном транспорте или на специальных тележках. При этом толчки и удары недопустимы. Нельзя устанавливать баллоны вблизи нагревательных приборов или под солнечными лучами. На рабочем месте баллоны должны быть надежно укреплены в вертикальном положении, так чтобы исключалась всякая возможность ударов и падений. Категорически запрещается отогревать влагу в редукторе баллона с углекислотой и любых баллонов со сжатым газом открытым пламенем, так как это безусловно вызывает взрыв баллона. Отогревать можно только тряпками, смоченными горячей водой.
Внимание! Это не конец книги.
Если начало книги вам понравилось, то полную версию можно приобрести у нашего партнёра - распространителя легального контента. Поддержите автора!Правообладателям!
Данное произведение размещено по согласованию с ООО "ЛитРес" (20% исходного текста). Если размещение книги нарушает чьи-либо права, то сообщите об этом.Читателям!
Оплатили, но не знаете что делать дальше?