Текст книги "Сварка"
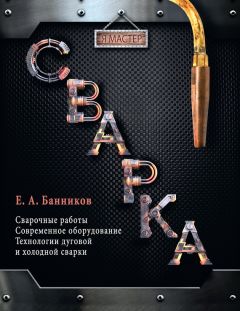
Автор книги: Евгений Банников
Жанр: Руководства, Справочники
Возрастные ограничения: +12
сообщить о неприемлемом содержимом
Текущая страница: 7 (всего у книги 23 страниц) [доступный отрывок для чтения: 8 страниц]
Кристаллическое строение и кристаллизация сплавов
Строение сплавов более сложное, чем строение чистого металла, и зависит от взаимодействия компонентов при кристаллизации.
Компоненты сплава при кристаллизации могут образовывать:
• твердые растворы, когда элементы сплава взаимно растворяются один в другом;
• механическую смесь – при полной взаимной нерастворимости, когда сплав состоит из смеси кристаллов составляющих ее компонентов;
• химическое соединение, при котором компоненты сплава вступают в химическое взаимодействие, образуя новую кристаллическую решетку.
Процесс перехода сплава из жидкого состояния в твердое с образованием кристаллических решеток (кристаллов) называется первичной кристаллизацией. Свойства металлических сплавов зависят от образующейся в процессе кристаллизации структуры. Под структурой понимают наблюдаемое кристаллическое строение сплава. Процесс кристаллизации начинается с образования кристаллических зародышей – центров кристаллизации.
Скорость кристаллизации зависит от скорости зарождения центров кристаллизации и скорости роста кристаллов в прямой зависимости, т. е. чем выше скорость роста кристаллов и больше число образующихся зародышей, тем быстрее протекает процесс кристаллизации сплава. Внутренняя структура сплава зависит от формы ориентировки кристаллических решеток в пространстве и скорости кристаллизации.
Центрами кристаллизации могут быть группы элементарных кристаллических решеток, неметаллические включения, тугоплавкие примеси. Процесс кристаллизации обычно начинается в направлении, противоположном отводу тепла.
Если процесс роста кристаллов не ограничивается, то образуются кристаллы неограниченной длины, в форме дерева или елочек-дендриты (рис. 38).

Рис. 38.
Схема строения поликристалла (а), и дендритный кристалл (б)
Так как процесс кристаллизации происходит в различных направлениях из многих центров кристаллизации, то ветви дендритов обычно искажаются, ограничивая при этом рост других кристаллов. Кристаллы неправильной формы называются зернами, или кристаллитами. В месте соприкосновения кристаллов рост их граней прекращается, и развиваются только отдельные грани. Число центров кристаллизации и скорость роста кристаллов влияют на величину зерна и, следовательно, на свойства металлов. При этом особую роль играет скорость охлаждения и переохлаждения расплавленного металла.
Зерна отличаются размером и ориентацией в кристалле. Они обычно повернуты относительно друг друга на десятки градусов. На границах зерен находится поврежденный переходный слой, порядка нескольких атомных слоев. Свойства и химический состав этого слоя могут сильно отличаться от свойств и состава зерен основного металла или сплава.
Кристаллические решетки могут иметь структурные дефекты: точечные, линейные, поверхностные, возникающие в результате вакансий (перемещения на свободные места) атомов.
При наличии таких дефектов зерно (кристаллит) разделяется на блоки в виде микромозаичной структуры (рис. 38).
При переходе сплава из жидкого состояния в твердое происходит усадка, т. е. уменьшение удельного объема зерен кристаллов. В результате усадки между зернами кристаллов в местах соприкосновения растущих дендритов в междуосных пространствах возникают микропустоты. Пустоты могут заполняться неметаллическими включениями (фосфидами, сульфидами и т. п.) или оставаться в виде раковин, микротрещин, пустот. Такие включения становятся центрами развития трещин, надрывов при приложении нагрузки или нагреве.
Характеристика свойств металлов и сплавов
В настоящее время известно 65 металлов. Но чистые металлы применяют редко, в основном в технике применяются сплавы. Например, сплав железа с углеродом насчитывает более 12 000 железных сплавов, главным образом сталей.
Все металлы и сплавы обладают свойствами, которые разделяют на:
• механические свойства;
• физические свойства;
• химические свойства;
• технологические свойства;
• эксплуатационные свойства.
Механические свойства металлов и сплавовОсновные механические свойства:
• прочность;
• пластичность;
• твердость;
• ударная вязкость.
Приложение внешней нагрузки вызывает в твердом теле напряжение и деформацию.
Напряжение – это нагрузка (сила), отнесенная к площади сечения материала.
Деформация – это изменение форм и размеров при приложении внешних сил.
Деформация может быть упругой, т. е. исчезающей после снятия нагрузки, или пластической, т. е. остающейся после снятия нагрузки.
Прочность – способность твердого тела сопротивляться деформации или разрушению при воздействии внешних сил статического или динамического характера. Прочность определяют с помощью специальных механических испытаний образцов, изготовленных из исследуемого материала.
Пластичность – способность материала получать остаточное изменение формы и размера без разрушения. Пластичность характеризуется относительным удлинением при разрыве.
Твердость – способность материала сопротивляться внедрению в него другого тела. Твердость тесно связана с прочностью.
Ударную вязкость оценивают при динамических испытаниях.
Физические свойства металлов и сплавовК физическим свойствам металлов и сплавов относятся:
• температура плавления;
• плотность;
• температурный коэффициент;
• электросопротивление;
• теплопроводность.
Физические свойства металлов и сплавов обусловлены их составом и структурой.
Химические свойства металлов и сплавовК химическим свойствам относится способность к химическому взаимодействию с агрессивными средами.
Технологические свойства металлов и сплавовТехнологические свойства – это способность материала подвергаться различным методам горячей и холодной обработки.
У металлов и сплавов такими свойствами являются:
• литейные свойства определяются жидкотекучестью, усадкой и т. п.;
• деформируемость – способность принимать форму под нагрузкой без разрушения;
• свариваемость – способность образовывать сварное (неразъемное) соединение требуемого качества;
• обрабатываемость режущим инструментом.
Эксплуатационные свойства металлов и сплавовЭксплуатационные, или служебные, свойства металлов и сплавов определяются условиями работы машин или конструкций, изготовленных из этих материалов.
В зависимости от условий работы выделяют:
• коррозионную стойкость – сопротивление действию агрессивной среды;
• хладостойкость – сохранение свойств пластичности при температуре ниже 0 °C;
• жаропрочность – сохранение механических свойств при высоких температурах;
• жаростойкость – способность сплава сопротивляться окислению в газовой среде при высоких температурах;
• антифрикционность – способность сплава прирабатываться к другому сплаву.
Около 90 % выплавляемой стали и большую часть цветных металлов перерабатывают прокаткой. При прокатке металл в слитках, полученных выплавкой, проходит через специальные вращающиеся валки, деформируется и принимает различные формы в зависимости от вида прокатки и формы валков.
Сортамент проката. Классификация и маркировка сталей
Почти весь сортамент (кроме специального назначения) выпускается в соответствии с ГОСТом (Государственным общесоюзным стандартом). В ГОСТах на сортамент проката приведены площадь поперечного сечения, размеры, масса 1 п. м длины профиля и допустимые отклонения от номинальных размеров.
Форму поперечного сечения прокатанного металла называют профилем.
Совокупность форм и размеров профилей, получаемых прокаткой, называют сортаментом.
Сортамент прокатаСортамент проката делится на 4 основные группы:
• сортовой прокат – профили простой геометрической формы;
• фасонный (швеллер, рельс, уголок, тавр и т. д.);
• листовой прокат – фольга (толщина проката менее 0,2 мм);
• тонколистовой (толщина менее 4 мм);
• толстолистовой (толщина 4–160 мм);
• трубы (трубный прокат) – бесшовные трубы диаметром 30–650 мм;
• сварные (шовные) трубы диаметром 5–2500 мм;
• специальные виды проката – кольца, колеса, шары и т. п.
Классификация сталейСтали классифицируют по назначению, химическому составу, качеству. По химическому составу классифицируют главным образом конструкционные стали.
Конструкционными называют стали, предназначенные для изготовления деталей машин и металлических конструкций. Конструкционные стали делят на углеродистые и легированные.
Углеродистые стали могут быть:
• низкоуглеродистые – с содержанием углерода не более 0,09–0,25 %;
• среднеуглеродистые – с содержанием углерода в пределах 0,25–0,45 %;
• высокоуглеродистые – с содержанием углерода 0,45–0,75 %.
По назначению применения стали подразделяют на:
• строительные стали – углеродистые и низколегированные, обыкновенного качества, т. е. для конструкций общего назначения;
• инструментальные стали для изготовления режущих и измерительных инструментов, штампов и т. п.;
• машиностроительные стали специализированного и общего назначения для изготовления деталей, машин, строительных конструкций;
• стали с особыми свойствами, которые подразделяют на стали с особыми физическими, химическими и технологическими свойствами (магнитные, жаропрочные, коррозионностойкие).
По качеству стали классифицируют на стали обыкновенного качества, качественные, высококачественные, особовысококачественные.
Качество стали определяется условиями металлургического производства и содержанием в них вредных примесей.
Стали классифицируют на группы А, Б, В:
А – стали обыкновенного качества, с механическими свойствами ниже, чем у других групп сталей. Основным элементом, определяющим эти механические свойства, является углерод. Эти стали имеют повышенное содержание серы (до 0,06 %) и фосфора (до 0,07 %).
Б – качественные стали, углеродистые или легированные с содержанием серы и фосфора не более 0,035 %.
В – высококачественные, в основном легированные стали. Содержание серы и фосфора не более 0,025 %.
Особовысококачественные стали. Это стали специального назначения, с содержанием серы и фосфора не более 0,015 %.
По химическому составу стали делят на углеродистые и легированные.
По способу раскисления стали классифицируют на:
• спокойные стали, когда сталь хорошо раскислена марганцем, кремнием, алюминием и ее затвердевание проходит без выделения газов;
• кипящие стали, когда сталь раскислена только марганцем и при ее затвердении происходит бурное выделение углекислого газа, создавая впечатление кипения стали;
• полуспокойные стали – раскислены марганцем и алюминием и занимают промежуточное положение между кипящей и спокойной сталью.
Маркировка сталейПринятая буквенно-цифровая система обозначений сталей является простой и наглядной.
• Стали обыкновенного качества (группа А) обозначают Ст0–Ст6.
• Углеродистые стали.
Углеродистые стали, за исключением сталей обыкновенного качества, маркируют по содержанию углерода.
• Углеродистые качественные конструкционные стали маркируют двухзначным числом, указывающим среднее содержание углерода в стали в сотых долях процента. Например, сталь 40 содержит 0,4 % С и т. д. Если сталь при этом раскислена не полностью, то в обозначении добавляют индексы: «пс» – для полуспокойной стали и «кп» – для кипящей стали. Для спокойных сталей индекс не применяют. Например, сталь 08кп содержит 0,08 % С, это кипящая сталь.
• Углеродистые качественные инструментальные стали маркируют буквой «У», и следующие за ней цифры указывают на среднее содержание углерода в десятых долях процента. Например, сталь У8 содержит 0,8 % С, это качественная инструментальная сталь. Если сталь при этом высококачественная, то в конце следует буква «А». Например, У12А.
• Конструкционные легированные стали. Легирующие элементы вводят в стали специально с целью изменения свойств. Легирующие элементы обозначают русскими буквами. Цифры после буквы указывают примерное содержание данного легирующего элемента, округленного до целого числа процентов.
А – азот, если буква находится в середине марки;
Б – ниобий;
В – вольфрам;
Г – марганец;
Д – медь;
К – кобальт;
М – молибден;
Н – никель;
П – фосфор;
Р – бор;
С – кремний;
Т – титан;
X – хром;
Ц – цирконий;
Ю – алюминий.
Таблица 3
Основные стандартные металлические профили

Цифры после буквы указывают примерное содержание данного легирующего элемента, округленного до целого числа процентов. Если после буквы цифра не поставлена, это означает, что данного элемента не более 1 %.
Две цифры в начале марки стали указывают среднее содержание углерода в сотых долях процента. Например, сталь 40Х содержит 0,33–0,44 % углерода и 0,8–1,1 % хрома. Буква «А» в конце означает, что сталь высококачественная, например, сталь ЗОХГСА содержит примерно 0,3 % углерода и менее 1 % хрома, марганца и кремния, высококачественная.
В легированных инструментальных сталях одна цифра в начале марки указывает на среднее содержания углерода в десятых долях процента. Например, сталь 7ХЗ означает, что углерода содержится примерно 0,7 %, хрома примерно 3 %.
Также при содержании углерода 1 % и более цифру, указывающую содержание углерода в марке, опускают. Например, ХВГ означает, углерода в стали более 1 %, остальных легирующих элементов – хрома, ванадия, марганца – около 1 %.
Некоторые группы сталей содержат дополнительные обозначения, характеризующие тип или группу сталей.
Например, буквы, стоящие впереди марки, означают:
А – автоматные стали (для скоростной обработки на автоматных станках);
Ш (ШХ) – шарикоподшипниковые стали (если буква ставится впереди марки);
Ш – сталь электрошлакового переплава (если буква ставится в конце марки);
Р – быстрорежущие стали (от англ. «rapid» – быстрый);
Е – магнитные стали;
Э – электротехнические, кремнистые стали.
Сложного состава высоколегированные стали на металлургическом заводе иногда обозначают упрощенно, например, ЭИ482 – сталь производства завода «Электросталь», для исследовательских целей. Иногда обозначают номер разработки стали. Например, сталь 40Х15Н7ГФ2МС или ЭП388.
В сварных конструкциях применяют в основном низко-углеродистые стали.
Глава 5
Сварные соединения и швы
Классификация основных типов сварных соединений
Сварка – это процесс получения монолитного неразъемного соединения материалов за счет необратимых термодинамических процессов превращения энергии и вещества в зоне соединения.
Сварным соединением называется неразъемное соединение деталей, выполненное сваркой.
В конструкциях применяются следующие основные типы сварных соединений:
С: стыковое соединение – это сварное соединение двух элементов, примыкающих друг к другу торцовыми поверхностями.
Н: нахлесточное соединение – сварное соединение, в котором сварные элементы расположены параллельно и частично перекрывают друг друга.
Т: тавровое соединение – сварное соединение, в котором торец одного элемента примыкает под углом к боковой поверхности другого элемента.
У: угловое соединение – сварное соединение двух элементов, расположенных под углом и сваренных в месте примыкания их краев.
Когда боковые поверхности сваренных элементов примыкают друг к другу, угловое соединение называют торцовым.
Сварку выполняют при помощи сварных швов.
Сварной шов – этот участок сварного соединения, образовавшийся в результате кристаллизации расплавленного металла или в результате пластической деформации при сварке давлением или сочетанием кристаллизации и давления.
С помощью, например, дуговой или газовой сварки можно выполнить стыковой или угловой шов.
Стыковой шов – это сварной шов стыкового соединения.
Угловой шов – это сварной шов углового, нахлесточного или таврового соединения (ГОСТ 2601–84).
В угловых соединениях стыковой шов чаще всего называют торцовым, а в тавровых соединениях – швом с глубоким противлением.

Рис. 39. Виды сварных соединений:
1 – стыковое; 2– нахлесточное; 3 – тавровое; 4 – угловое


Рис. 40.
Стыковой (а) и угловой (б) сварные швы
Стыковые соединенияСтыковые швы выполняют с разделкой кромок или без разделки кромок.
Стыковые соединения без разделки кромок применяют для листов с толщинами до 12 мм. Кромки листов при этом срезают под прямым углом и при сварке располагают с зазором в 1–2 мм. Листы толщиной до 4 мм сваривают односторонним швом, а 4–12 мм – двухсторонним швом. Стыковое сварочное соединение является наиболее распространенным. Оно имеет высокую прочность при статических и динамических нагрузках. Рационально применять его для соединения листового металла, а также для соединения (стыковки) различных профилей: балок, уголков и т. п.
Разделку кромок для сварки в стык выполняют с целью получения высокопрочного соединения и проварки кромок деталей. По форме кромок разделка соответственно называется: V-образная, К-, Х-, U-образная или с ломанными краями.
Таблица 4
Стандарты на дуговую сварку

Стыковое соединение с V-образной разделкой применяют для сварки металла толщиной 3–60 мм. При этом разделка металла может быть одно– и двухсторонней. При толщинах металла 15–100 мм применяют двухстороннюю V-образную разделку с криволинейным скосом одной или обеих кромок. Стыковые соединения с Х– и К-образными скосами кромок применяют при сварке металла толщиной 8–175 мм. При этом расход электродов и электроэнергии почти в 2 раза меньше, чем при V-образной разделке. Кроме того, такая разделка обеспечивает меньшую деформацию после сварки.
Нахлесточные соединенияСоединение внахлестку применяют при сварке листовых конструкций, разного рода конструкций обшивок, строительных ферм, колонн, мачт и т. п.
Нахлесточные соединения менее прочны, ведут к перерасходу металла. Эти соединения неэкономичны при толщинах металла более 20 мм.
Соединения внахлест применяют при толщинах металла 2–60 мм. Их выполняют наложением одного элемента на другой. Величина перекрытия больше удвоенной суммы толщин свариваемых кромок. Свариваемые поверхности практически не обрабатывают, за исключением зачистки кромок. Листы проваривают с двух сторон, для исключения проникновения влаги в зазор при эксплуатации. Сварку ведут угловым швом.
Тавровые соединенияТавровые сварные соединения применяют для производства балок, стоек, колонн, каркасов зданий и прочих пространственных конструкций. Тавровые соединения могут быть с подготовкой кромок или без нее. В соединениях без подготовки может быть непровар корня шва. Поэтому такие соединения плохо работают при переменных и ударных нагрузках. Одно– или двухсторонний скос обеспечивает полный провар соединяемых элементов. Эти соединения имеют высокую прочность при любых нагрузках.


Рис. 41. Основные положения сварных швов в пространстве:
1 – нижнее; 2 – горизонтальное; 3 – вертикальное; 4 – потолочное
Угловые соединенияКак правило, угловые соединения применяют в качестве связующих элементов. Угловые соединения обычно не рассчитывают.
Классификация основных типов сварных швовУгловые или стыковые сварные швы по положению в пространстве подразделяются (согласно ГОСТ 11969–79) на:
Н, Л – нижнее и в лодочку, соответственно;
Пг – полугоризонтальные;
Г – горизонтальные;
Пв – полувертикальные;
В – вертикальные;
Пп – полупотолочные;
П – потолочные.
По протяженности (рис. 42) различают:
• швы сплошные;
• швы прерывистые (в шахматном порядке, цепные швы).
По отношению к направлению действующих усилий (рис 42б) различают:
• швы продольные;
• швы поперечные;
• комбинированные швы;
• косые швы.
По форме наружной поверхности (рис. 43) стыковые швы могут быть выполнены:
• нормальными (плоскими);
• выпуклыми или вогнутыми.
Выпуклые швы лучше работают при статических нагрузках, а плоские (нормальные) и вогнутые лучше работают при знакопеременных и динамических нагрузках, т. к. нет резкого перехода от основного металла к сварному шву.
По условиям работы сварного узла при эксплуатации изделия сварные швы подразделяют на рабочие, непосредственно несущие нагрузку, и на соединительные (связующие) швы. Связующие швы иногда называют нерабочими швами. Они служат для скрепления частей или деталей. Например, «прихватки» – связующие короткие швы для скрепления деталей перед сваркой.
На чертежах сварные швы в соответствии с ГОСТом 2.312–84 обозначают основными линиями с видимой стороны и штриховыми – с невидимой стороны. К ним подходит односторонняя стрелка с полкой, над которой пишут условное обозначение шва:
1 – место специального знака:
– шов замкнутый, контурный;
– шов монтажный;
– шов контурный, незамкнутый и т. п.;
2 – место стандарта (ГОСТа) – см. табл. 4;
3 – буквенно-цифровое обозначение сварного шва – см. табл. 4;
4 – условное обозначение способа сварки:
А – автоматическая сварка;
П – механизированная сварка;
У – сварка в углекислом газе;
И – сварка в инертном газе; сварка дуговая и ручная не обозначаются;
5 – условный знак профиля шва и его катет (для угловых швов);
6 – длина и расположение участков прерывистых швов.

Рис. 42.
Классификация сварных швов:
по протяженности (а):
1 – сплошной; 2 – цепной; 3 – шахматный;
по направлению действующих усилий (б):
1 – продольный; 2 – поперечный; 3 – комбинированный

Рис. 43.
Классификация сварных швов по форме наружной поверхности:
1 – нормальный шов; 2 – выпуклый шов; 3 – вогнутый шов

Рис. 44. Обозначение позиций сварного шва по ГОСТу 2.312–84.
Пример обозначения сварного таврового соединения Т4, выполненного углекислотным полуавтоматом, для монтажных целей, с незамкнутым контуром и длиной катета шва 4 мм, длина провара 50 мм, шаг сварки 150 мм, изображен на рис. 45.

Рис. 45. Пример обозначения сварочного шва по ГОСТу 2.312–84
Правообладателям!
Данное произведение размещено по согласованию с ООО "ЛитРес" (20% исходного текста). Если размещение книги нарушает чьи-либо права, то сообщите об этом.Читателям!
Оплатили, но не знаете что делать дальше?