Текст книги "Стоимость ≠ ценность. Современные методики картирования потоков создания ценности с применением правила 80/20"
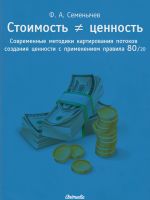
Автор книги: Филипп Семёнычев
Жанр: О бизнесе популярно, Бизнес-Книги
Возрастные ограничения: +12
сообщить о неприемлемом содержимом
Текущая страница: 4 (всего у книги 14 страниц) [доступный отрывок для чтения: 4 страниц]
8.5. Прочие способы выбора
Выше представлены основные и наиболее эффективные и применимые способы выбора продуктов. Как вы успели заметить, в каждом из них прослеживается единая логика выбора – логика АВС анализа и принципа Парето. На самом деле таких способов можно было бы придумать и привести в качестве примера ещё десяток, они все были бы основаны на приведённой выше логике. Каждый из приведённых выше способов можно применять как отдельно, так и комбинировать их друг с другом. Самое главное, на что надо опираться при выборе продукта, это поставленные цели и задачи, которые должны находиться перед глазами и о которых всегда надо помнить, а также здравый смысл, помогающий адаптировать инструмент к рассматриваемому процессу и его особенностям. Прошу не путать здравый смысл с укоренившимися в организации парадигмами (см. приложение 5). Общий алгоритм выбора продукта представлен на схеме (см. рисунок 8.12).

Рис. 8.12
Альтернативными критериями ранжирования могут являться:
– затраты на сырьё и материалы в рублях по различным видам изделий (фокус на оптимизацию наиболее материалоёмких операций);
– статистика по срывам сроков изготовления определённой номенклатуры изделий (фокус на увеличение скорости протекания процесса);
– материалоёмкость изделия, например, масса отливки в литейном производстве (фокус на сокращение затрат на материал и сопутствующих затрат);
– и т. п.
Сам процесс и итоги выбора продукта (семейства продуктов) необходимо визуализировать: расположить на видном месте в виде последовательности таблиц отбора и диаграмм Парето.
Визуализированная последовательность выбора и полное название выбранного продукта (семейства продуктов) будут являться сигналом для начала построения карты текущего состояния.
9. Формирование текущего состояния
Как вы яхту назовёте, так она и поплывёт.
Капитан Врунгель
Первый шаг при формировании текущего состояния КПСЦ заключается в определении самого процесса. Необходимо ответить на вопросы: «как называется процесс, который мы рассматриваем» и «где границы этого процесса?» Формулировка названия процесса сознательно выделена как отдельный подэтап при формировании текущего состояния. От формулировки названия процесса будет зависеть его содержание, границы, и, следовательно, вся дальнейшая работа. Часто работа уходит в другие, не направленные на достижение цели русла, в ходе анализа рассматриваются смежные процессы, перерабатываются данные, не относящиеся к целям, если название процесса было нечётко сформулировано или не было зафиксировано на бумаге. В лучшем случае это приводит к повышенным трудозатратам небольшой демотивации группы, в худшем случае, если никто во время не заметит ошибки, работа может окончательно принять неверное направление, а демотивация группы из-за недостижимости цели будет уже гораздо серьёзней. Перефразируем всё вышесказанное словами классика: «Как вы яхту назовёте, так она и поплывёт!». Собственно, ещё доктор Эдвардс Деминг[12]12
Эдвардс Деминг(1900–1993) – американский учёный, статистик и консультант по теории управления качеством.
[Закрыть] писал о важности операционабельных определений, поэтому не будем на этом останавливаться. После формулирования названия рассматриваемого процесса его необходимо визуализировать, т. е. записать и вывесить в качестве заготовка будущей КПСЦ. Таким образом, формулируется очередное правило: название процесса должно иметь чёткую и однозначную для понимания формулировку, отражающую суть процесса, визуализированную в качестве заголовка КПСЦ текущего состояния.
Далее приступаем к определению входа и выхода рассматриваемого процесса, его продолжительности, то есть мы определяем границы, внутри которых будет рассматриваться выбранный поток. При картировании в масштабах организации границами могут являться внешние Поставщики и Заказчики, если целями и решением руководителей не принято иного решения. В масштабе отдельного производства или цеха границами могут быть определены некоторые внутренние и внешние Поставщики и Заказчики: смежные цеха, производства и т. п. Определение границ необходимо для чёткого направления работы, так как в процессе картирования мы можем увлечься рассмотрением не интересующей и ненужной для достижения цели информации. Таким образом, затратив минимум времени на обозначение границ рассматриваемого процесса, визуализируя эти границы (схематично, либо вместе с названием процесса), мы застрахуем себя от лишней и непродуктивной работы. В различных случаях может быть несколько Поставщиков и Заказчиков. Например, когда для изготовления продукта требуется несколько видов сырья, материалов или заготовок, поставляемых различными поставщиками, вне зависимости от того, внутренние они или внешние, или когда один продукт отгружается нескольким Заказчикам. На практике удобнее для понимания начинать с выходов процесса, а затем, двигаясь обратно по технологической цепочке, определить входы процесса. После определения входов и выходов на пока ещё пустой КПСЦ, под названием процесса появляются Заказчики, Поставщики и пространство между ними для заполнения этапами процессов. Теперь, когда появились границы, можно переходить к определению этапов рассматриваемого процесса, то есть его внутреннего наполнения.
Каждый продукт, как уже говорилось выше, имеет свою технологию и проходит определённые производственные этапы (операции) в процессе его преобразования в продукт. На шаге определения этапов процесса МФГ визуализирует общее наполнение процесса, указывая какие операции (этапы процесса) проходит изделие в процессе его преобразования в готовый продукт.
Здесь стоит остановиться и объяснить, почему употребляются два термина: операция и этап процесса. КПСЦ в зависимости от рассматриваемого процесса может иметь несколько уровней. Один этап процесса крупного масштаба в КПСЦ может быть представлен как КПСЦ меньшего масштаба, в котором входом и выходом будут смежные с рассматриваемым (предыдущий и последующий) этапы процесса крупного масштаба.

Рис. 9.1
Например, КПСЦ автосборочного завода может иметь в качестве внутреннего наполнения (этапов процесса) цеха, либо производства по изготовлению отдельных комплектующих: кабин, рам, шасси и т. п. В то же время, рассматривая отдельный этап процесса через КПСЦ второго уровня (более мелкого масштаба), внутренним наполнением становятся уже более мелкие процессы или операции, такие как штамповка, гибка, сварка и т. п. Этап процесса – более общее название внутреннего наполнения рассматриваемого процесса, а операция – это последовательность действий, выполняемая для совершения какой-либо работы. Различие лишь в масштабах рассматриваемого процесса. Возвращаясь к потоку изготовления велосипеда прокартированная, операция сборки может быть представлена отдельной последовательностью операций (см. рисунок 9.1), ограниченной Поставщиками колёс и рам и Заказчиком – следующей операцией, т. е. техническим контролем. На рисунке 9.1 видно, как один из этапов процесса раскладывается на более мелкие операции в виде «укрупнённого» участка потока.
Наполнение КПСЦ на этом шаге может быть различным, некоторые этапы процесса могут выполняться параллельно, вместе с другими. Задача МФГ состоит в том, чтобы определить все этапы процесса применительно к конкретному выбранному продукту и в рамках рассматриваемого процесса, в соответствии с его формулировкой и границами, а также определить их последовательность (параллельность, если хотите) и наполнить этой информацией текущее состояние КПСЦ, то есть визуализировать информацию.
В качестве примера (см. рисунок 9.2) приводится процесс производства велосипедов. Как видно из рисунка, основные этапы этого процесса – сварка рам велосипедов, их покраска и сушка, сборка колёс, выполняемая параллельно упомянутым операциям (соответственно и расположена на карте), далее сборка велосипедов и технический контроль. Так в первом приближении выглядела бы карта потока производства определённой марки велосипеда.

Рис. 9.2
Следующий шаг – определение параметров этапов процесса. Среди всего разнообразия возможных параметров (см. приложение 3) необходимо выбрать те, которые потребуется изучать на этапе анализа. В данной ситуации необходимо задать себе следующие вопросы: «каковы наши цели и задачи?» и «с помощью каких параметров мы можем на них воздействовать?» Возможно, вам понадобятся уже известные параметры, а, может, вы придумаете свои, специфичные для вашего процесса.
Определённые параметры этапов процесса визуализируются под каждым этапом (см. рисунок 9.3).

Рис. 9.3
В рассматриваемом примере основными показателями являются:
Время цикла операции, за которое производится операция над одой единицей продукции, например, сваривается одна рама велосипеда или собирается один комплект колёс. Используйте единые единицы и масштабы измерения, они существенно упростят задачу. Время создания ценности (Всц), т. е. то самое полезное время, за которое готов платить Заказчик, в течение которого продукт видоизменяется или приобретает необходимые Заказчику свойства. Например, в случае сварки рам время создания ценности – это время одновременного контакта двух свариваемых изделий и сварочного электрода (предполагая, что осуществляется электросварка). Все остальные действия (подготовка, перекладывание, крепление и т. п.) являются потерями.
Количество работников, задействованных в каждой операции. Здесь мы учитываем только тех работников, которые участвуют в преобразовании продукта и процессе добавления ценности. Если другого не оговаривается поставленными задачами, мы не учитываем управляющий и обслуживающий персонал, например мастеров и уборщиц, распределителей работ и т. п., а также персонал логистики, осуществляющий перемещение продукта между этапами процесса.
Время переналадки – это необходимое время для перехода с одного вида изделия на другое, в нашем примере это модели велосипедов, имеющие различную технологию производства и конструкцию.
Процент исправимого и неисправимого брака, т. е. доля деталей, покидающих рассматриваемый поток либо навсегда, либо переходя в начало одной из предыдущих стадий процесса.
В результате то, что получится, должно быть при первом приближении похоже на КПСЦ, по крайней мере, стороннему наблюдателю должны быть понятны стадии изготовления продукта.
Дальше начинается самое интересное. Следующий шаг – обход процесса или Go-Look-See (иди, смотри и замечай). Это один из принципов lean, означающий решение проблем в месте их возникновения, а также принятие решений из места создания ценности, т. е. когда возникает проблема – мы идём и смотрим, получая наиболее достоверную информацию при помощи собственных органов чувств (видим сами, слышим из первых уст). Применительно к картированию основные цели Go-Look-See – увидеть стадии преобразования продукта своими глазами, собрать максимальное количество достоверных данных о рассматриваемом процессе. Самый распространённый вопрос, встречающийся в начале Go-Look-See, – «Зачем куда-то идти, если мы и так всё знаем?». Это наиболее часто встречающаяся парадигма[13]13
Парадигма – призма, через которую человек смотрит на окружающий мир (Р. Кови).
[Закрыть] у руководителей, которая в корне противоречит принципам lean и от которой необходимо постепенно избавляться. Согласно принципам lean, когда возникает проблема, вы идёте в место её обнаружения, оцениваете масштаб проблемы, возможные причины её появления, следуете в место её возникновения и принимаете решения на основе актуальной информации, полученной непосредственно на месте, а не со слов подчинённых, переданных по цепочке. Вы не просто сидите и обсуждаете проблему в кабинете, вы направляете вашу команду идти в производство (место возникновения проблемы).
Как уже неоднократно говорилось, по мере передачи информация искажается, причём не важно, представлена она в словесном формате, либо в виде данных (в случае документирования вероятность искажения значительно падает). Порой менеджер может только догадываться об истинных причинах возникновения той или иной проблемы.
Поэтому только в ходе Go-Look-See мы можем получить наиболее достоверную информацию о состоянии и параметрах потока, его проблемах, представить себя на месте продукта и понять динамику движения в процессе его преобразования. Да, именно представить себя на месте продукта, подумать каково вам сейчас и что можно сделать, чтобы вам стало лучше, удобнее, т. е. чтобы увеличить долю времени, создающего ценность. Очень важно участие всей МФГ, особенно ценными являются наблюдения и мнения участников МФГ, которые ранее не были знакомы с рассматриваемым процессом, не знали его специфики. У таких людей в силу «незамыленности взгляда», больше шансов выявить проблемы и несоответствия в потоке, а также их причины. Таким образом, Go-Look-See начинается с обучения МФГ правилам и задачам, т. е. что мы делаем, куда и как идём, на что обращаем внимание и что спрашиваем. Применительно к КПСЦ можно сформулировать следующие правила Go-Look-See:
1. Go-Look-See проводится непрерывно и в один день (без разрывав по часам, дням и т. п.).
2. Идём вверх по потоку: обратно по технологической цепочки от получения годного продукта до поставки сырья для его изготовления.
3. Пешком проходим всю технологическую цепочку, весь поток от выхода процесса до его входа. Схематично зарисовываем КПСЦ процесса в черновом варианте.
4. Не вникаем в тонкости технологии. Нас интересуют те места и операции, где продукт видоизменяется (добавляется ценность).
5. Обращаем основное внимание на поток и его разрывы (накопление и отсутствие продукта в потоке, остановки потока, например, простои оборудования и операций).
6. Если видим разрыв – задаём вопросы, начинающиеся с «почему».
7. Если видим большие запасы – задаём вопросы, начинающиеся «почему».
8. Если видим проблему – спрашиваем «почему она возникла?».
9. Лично наблюдаем этапы и операции преобразования продукта, считаем запасы.
10. Собираем необходимые данные (параметры этапов процесса) из первоисточников, там, где это необходимо, спрашиваем подтверждение.
11. Задаём вопросы «откуда поступает сигнал на начало производства?».
12. Фиксируем все информационные потоки (формальные и неформальные).
13. Фиксируем виды и методы перемещения изделия между операциями.
14. Фотографируем запасы, проблемы, операции в потоке и всё, что может понадобиться.
Приведённый выше перечень правил, разумеется, не является исчерпывающим, он может дополняться иной необходимой информацией в зависимости от сформулированных целей и задач, однако его можно взять за основу при обучении МФГ и постановку задач непосредственно перед Go-Look-See.
Проясним некоторые моменты изложенных правил. Одной из распространённых ошибок является изучение тонкостей технологии. К примеру, изучение взаимодействия заряженных частиц в процессе химического никелирования является увлекательным занятием. Но нужно ли это для достижения поставленных целей и задач? Технологическая цепочка является неотъемлемой частью КПСЦ только в общем её представлении. Необходимо понимать, что изменяется в продукте по мере прохождения различных этапов процесса (операций), т. е. какая ценность добавляется продукту, не более того. К тому же изучение тонкостей технологии – это изучение её проблем, в которые ни в коем случае не стоит погружаться на данной стадии процесса КПСЦ. Не стесняйтесь задавать вопросы. Поверьте, то, что вы можете узнать у работников, непосредственно занятых в создании ценности, вам вряд ли кто-либо расскажет. Самый распространённый вопрос, гениальный по своей простоте – это «почему». Если вы видите что-либо, не укладывающееся в вашу формирующуюся логическую цепочку преобразования изделия, задайте этот вопрос. Несколько правильных вопросов, начинающихся с «почему?», способны выяснить коренные причины проблем и текущего состояния ситуации в целом.
Пример диалога с использованием «почему»:
– Почему у вас здесь столько скопившихся велосипедных рам?
– Потому что вчера не осуществлялась отгрузка.
– Почему вчера не было отгрузки?
– Не приехал автопогрузчик.
– Почему вчера не приехал автопогрузчик?
– Он не прошёл технический осмотр.
– Почему погрузчик не прошёл технический осмотр?
– Проверка показала недостаток тормозной жидкости.
– Почему тормозной жидкости оказалось недостаточно?
– Никто этого не знал, её заливают только тогда, когда она заканчивается.
На этом диалог можно прекратить, т. к. проблема в отсутствии автономного периодического обслуживания погрузчиков явилась коренной причиной скопления запасов. Проверить это можно, выстроив обратную логическую цепочку: из-за того, что тормозную жидкость заливают только тогда, когда она закончится, её не оказалось во время проверки; из-за того, что тормозной жидкости не оказалось во время проверки, погрузчик не прошёл технический осмотр и т. д.
Таким образом, если логическая цепочка не нарушается, причинно-следственная связь, при помощи вопроса «почему» выстроена правильно.
Разговор на местах может помочь выявить неформальные каналы передачи информации, например, может выясниться, что задание на производство изделий поступает от бригадира на основании текущего состояния оборудования (качества, объёмов незавершённого производства, наличия оснастки, материалов и т. п.), а не от службы планирования, как это предполагалось.
Запасы незавершённого производства должны подсчитываться вручную (указательным пальцем), вы должны видеть то, что считаете, а не использовать данные служб и отделов, которые могут не совпадать друг с другом. В КПСЦ запасы фиксируются на момент проведения Go-Look-See и являются неким срезом, показывающим состояние потока в определённый момент времени, поэтому первое правило (а) требует отсутствия перерывов во время его проведения. Категорически неправильно обходить часть потока в один день, другую часть во второй и т. п., так как поток не стоит на месте и ситуация в нём меняется ежеминутно. Go-Look-See не должен прерываться от начала и до его завершения.
По мере продвижения к началу потока он может разделяться на несколько мелких входящих потоков. В таких случаях следует проходить по основной части потока, а затем возвращаться для прохождения оставшихся ответвлений потока.
Во время обхода необходимо зарисовывать схему и фиксировать данные, это облегчит вам работу при оформлении КПСЦ, т. к. не придётся вспоминать всё увиденное, достаточно лишь будет сравнить показания всех участников МФГ. Отображайте на схеме основные операции и их всевозможные количественные показатели, места прерывания потока, источники сигналов на начало работы каждого этапа процесса (операции). При переходе между этапами процесса (операциями) фиксируйте в чём и посредством чего перемещается изделие, количество изделий в партиях в процессе и при транспортировке. Перечень стандартных параметров этапов процессов представлен в приложении 3. Обратите внимание, по какой системе (вытягивание или выталкивание) происходит работа каждого этапа процесса (операции). Напоминаю, что вытягивание – это система производства, при которой предыдущий этап процесса (операция) не начинает работать (обрабатывать, изготавливать и т. п.) до поступления сигнала о потребности от последующего этапа. Соответственно, выталкивание – система, в которой предыдущий этап процесса работает вне зависимости от потребности последующего. Как правило, в таком случае у каждого этапа процесса есть своё отдельное рабочее задание.
Каждый человек обладает своим уникальным и неповторимым взглядом на окружающий мир: то, на что обращает внимание один человек, другой может просто не заметить. Поэтому после завершения Go-Look-See необходимо собрать группу и коротко обобщить всё увиденное, обменяться информацией. В идеале, сразу же после Go-Look-See необходимо приступать к оформлению текущего состояния КПСЦ, пока информация свежа, а голова не занята другими проблемами. В процессе оформления либо возникнут спорные моменты, либо обнаружится отсутствие какой-нибудь информации, ради которой придётся заново обойти часть рассматриваемого потока. Это нормально, надо быть к этому заранее готовым.
Вначале оформляется материальный поток как более понятный, который уже был самостоятельно пройден и увиден, уточняется недостающая информация, а собранные данные визуализируются. После этого наносятся информационные потоки, с которыми ситуация бывает немного сложнее и запутанней. Возможно, информационные потоки придётся неоднократно уточнять, возвращаться в поток и прослеживать уже информацию. Обращаю внимание на часто встречающуюся ошибку при построении информационных потоков, когда отслеживаются и визуализируются на КПСЦ все потоки, относящиеся и нет к рассматриваемому изделию (семейству продуктов). Такая информация может вводить в заблуждение.
Возвращаясь к примеру с производством велосипедов, в самом упрощённом варианте КПСЦ может выглядеть следующим образом (см. рисунок 9.4).
Уже в таком представлении можно невооружённым глазом увидеть массу источников потерь, начиная с выдаваемого в каждый этап рассматриваемого процесса производственного задания и заканчивая несинхронной работой каждой операции, что подтверждает наличие большого количества незавершённого производства между каждым этапом процесса.
Передача продукта между этапами процесса (операциями) происходит по системе выталкивания, в основном посредством погрузчиков.
Также практически на каждой операции присутствует определённая доля бракованной продукции, что является немаловажным фактором замедления скорости потока.
Отдельно стоит выделить построение диаграммы Спагетти. При работе с КПСЦ диаграммой Спагетти является схема перемещения изделия (в некоторых случаях человека, материалов, и т. п.), нанесённая на планировку участка (завода, цеха, рабочего места и т. п.). Название соответствует линиям на планировке, похожим на тарелку спагетти. Данная диаграмма необходима для визуального представления маршрута и расстояния, которые проделывает рассматриваемое изделие в процессе его преобразования в готовый продукт. Она наглядно показывает потери при транспортировке за счёт неоптимальных маршрутов, расположения точек доставки или операций и позволяет измерить эти потери, рассчитав расстояние. Для построения диаграммы Спагетти необходима планировка или схема участка, на котором физически функционирует рассматриваемый процесс. При картировании в масштабах завода это будет планировка завода, при картировании в масштабе участка – планировка участка. На стадии определения этапов процесса (операций) на планировке отмечаются фактические места расположения соответствующих этапов процесса на основании экспертного мнения МФГ. Для привязки к КПСЦ их необходимо будет соответственно пронумеровать. В ходе Go-Look-See данные планировки проверяются на соответствие с действительностью, в случае несоответствия вносятся корректировки.

Рис. 9.4
Общий алгоритм построения КПСЦ текущего состояния выглядит, как на блок-схеме (см. рисунок 9.5). Результатами работ, как видно из схемы, являются два полных, согласованных и утверждённых документа: диаграмма Спагетти и КПСЦ текущего состояния. Утверждение может заключаться в подписи руководителя, придающей бумаге с цифрами, линиями и схемами статус документа. Данный статус повышает ответственность за содержание материалов как участников МФГ, так и работников, предоставивших данные.

Рис. 9.5
Один из наиболее распространённых вопросов на данном этапе – «в каком виде лучше всего оформлять КПСЦ?» В настоящее время существует множество возможностей, начиная с простого отображения маркерами на большом листе бумаги (быстро, долговечно, но трудно вносить правки), использования стикеров (быстро и просто вносить правки) и заканчивая такими электронными программами, как Microsoft Vision и другими специальными программами. На практике приходится применять те способы, которые нужны в конкретной ситуации. Например, карты потока в электронном виде применяются в случаях длительного согласования и при отдалённом расположении отдельных участников группы (такое тоже часто встречается). Если проводится оперативная работа, то, как правило, применяются первые два способа, потому что для лучшего усвоения информации работа должна выполняться группой своими руками.
Существуют уже устоявшиеся, стандартные символы картирования, которые можно без труда найти во множестве источников интернета, поэтому в настоящей книге мы не останавливаемся на них. Самое основное – вне зависимости от того, какую символику вы применяете для построения карты потока, она должна быть едина для понимания каждого участника группы.
Внимание! Это не конец книги.
Если начало книги вам понравилось, то полную версию можно приобрести у нашего партнёра - распространителя легального контента. Поддержите автора!Правообладателям!
Данное произведение размещено по согласованию с ООО "ЛитРес" (20% исходного текста). Если размещение книги нарушает чьи-либо права, то сообщите об этом.Читателям!
Оплатили, но не знаете что делать дальше?