Текст книги "Санитарно-технические работы"
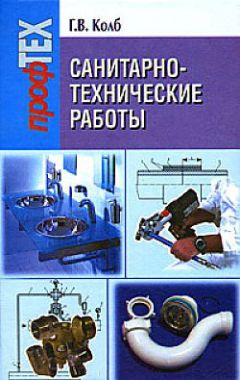
Автор книги: Галина Колб
Жанр: Техническая литература, Наука и Образование
сообщить о неприемлемом содержимом
Текущая страница: 4 (всего у книги 22 страниц) [доступный отрывок для чтения: 7 страниц]
3.4. Соединение чугунных труб
Чугунные трубы соединяются с помощью раструбного соединения (рис. 3.12), для чего их изготовляют с раструбом 2 (уширением) на одном конце. Раструбы бывают гладкие (рис. 3.12, а) и с желобком 5 (рис. 3.12, б). При сборке чугунных труб в раструб 2 одной трубы вставляют гладкий конец 1 другой трубы. Зазор между трубами заполняют уплотнителем.

Рис. 3.12. Раструбное соединение чугунных труб с заполнителем; а – твердеющим; б – эластичным (резиновым); 1 – гладкий конец трубы; 2 – раструб; 3 – цемент; 4 – смоляная прядь; 5 – желобок; 6 – резиновое кольцо
В качестве уплотнителя используют твердеющие (см. рис. 3.12, а) и эластичные (см. рис. 3.12, б) заполнители. Твердеющие заполнители – цемент, асбестоцементная смесь, расширяющийся цемент, сера и т. д. – придают стыку прочность и герметичность. Эластичные заполнители – резиновые кольца, манжеты, шнуры, герметики – обеспечивают высокую гибкость и также герметичность стыка при небольших затратах труда.

Рис. 3.13. Чугунные соединительные (фасонные) части: а – компенсационный патрубок; б – отвод 110, 120, 135°; в – муфта; г – колено; д – двухплоскостная крестовина; е – косая крестовина; ж – прямая крестовина; з – переходной патрубок; и – отступ; к – прямой тройник; л – косой тройник
Присоединение боковых ответвлений, изменение диаметров трубопроводов осуществляют с помощью чугунных соединительных (фасонных) частей (рис. 3.13).
Раструбные соединения труб выполняют в такой последовательности: размечают и отрезают трубы, подготовляют концы труб и собирают соединение. Чугунные трубы размечают так же, как и стальные.

Рис. 3.14. Резка чугунных труб: а – зубилом; б – ручным труборезом, – в – маятниковой пилой; 1 – труба; 2 – подкладки; 3 – режущая цепь; 4 – натяжное устройство; 5,7 – рукоятки; 6 – электродвигатель; 8 – режущий диск; 9 – прижим
Отрезку труб необходимой длины производят их перерубкой. При небольшом количестве трубы перерубают вручную зубилом (рис. 3.14, а) или ручным труборезом ТРР-150/ТРВ-150 (рис. 3.14, б). На сантехмонтажных заводах трубы перерубают механизмом СТД-22014, обеспечивающим 7 – 12 перерубов в минуту. Трубы можно отрезать также на электрической дисковой пиле (рис. 3.14, е), оборудованной абразивным, армированным диском. Плоскость отрезки или перерубки труб должна быть перпендикулярна оси трубы. Допускаются отклонение перпендикулярности торцов труб после отрубки не более 5°, трещины длиной не более 15 мм и волнистость кромок не более 10 мм.

Рис. 3.15. Заделка раструбов труб: а – канализационных безнапорных; б – водопроводных напорных; в-е – последовательность заделки; 1 – гладкий конец трубы; 2 – цемент; 3 – раструб; 4 – смоляная прядь;5 – асбестоцементная смесь; 6 – конопатка; 7 – чеканка
Подготовка труб перед соединением состоит в очистке концов и раструбов от грязи, осмотре и обстукивании их молотком (для обнаружения сколов и трещин). Поверхность труб и раструбов снаружи и внутри должна быть чистой и гладкой, без пузырей, раковин, свищей, шлаковых включений и других дефектов. Трубы с трещинами и отколами концов отбраковывают.
При соединении канализационных труб (рис. 3.15, а) гладкий конец 1 вводят в раструб 3 до упора, а при соединении водопроводных напорных (рис. 3.15, б) между гладким концом 1 и упорной поверхностью раструба 3 оставляют зазор b = 3–9 мм.
Ширина зазора между внутренней поверхностью раструба и наружной поверхностью трубы, вставленной в раструб, должна быть одинакова по периметру трубы.
Заделка раструбов цементом или асбестоцементной смесью зависит от типа труб.
При соединении канализационных труб на гладкий конец трубы 1 (рис. 3.15, в) навертывают смоляную прядь 4, скрученную в жгут диаметром 7–8 мм. Чтобы конец жгута не попал в трубу и не засорил ее, при навертывании первого витка его прижимают, захлестывая сверху очередным витком. Конопаткой 6 (рис. 3.15, г) жгут вгоняют в зазор раструба 3 и уплотняют его. Жгут должен заполнять 2/3 глубины раструба. После уплотнения жгута приготовляют цемент. Для заделки раструба используют цемент марки не ниже 300. Его просеивают, увлажняют водой (10–12 % по массе) и перемешивают. Оставшееся в раструбе место (1/3 его глубины) заполняют с помощью совка увлажненным цементом 2 (рис. 3.15, д) и зачеканивают чеканкой 7 (рис. 3.15, е) до тех пор, пока чеканка не станет отскакивать от цемента. Для получения менее жесткого стыка применяют асбестоцементную смесь, которую приготовляют, перемешивая асбестовое волокно не ниже IV группы (30 % по массе) и портландцемент марки не ниже 400 (70 %). За 30–40 мин до использования асбестоцементную смесь увлажняют, добавляя воду в количестве 10–12 % от массы смеси.
Чтобы обеспечить хорошие условия твердения цемента, раструб сверху закрывают мокрой тканью, которую в жаркую погоду периодически смачивают. В зимнее время для увлажнения цемент или смесь разводят горячей водой, раструбы подогревают, стыки после заделки утепляют. На сантехмонтажных заводах для сборки узлов из чугунных труб диаметром 50 и 100 мм применяют стенд-карусель на шесть рабочих мест с пневмоприжимами. Каждое место подается к рабочему поворотом стола вручную.
При соединении водопроводных труб диаметром до 300 мм раструб заделывают пеньковой прядью на глубину 25 мм и асбестоцементной смесью на глубину 25–30 мм. Для ускорения заделки стыка используют уширенные конопатки и чеканки (рис. 3.16), а также приспособления А.Н. Васильева, К.Г. Козлова и др. Приспособление А.Н. Васильева (рис. 3.17, а) состоит из металлической плиты 3 и шарнирно закрепленной на ней скобы 5 для прижима трубы 1 к плите. Скоба запирается чекой 4, что позволяет удерживать трубу в вертикальном положении, удобном для заделки раструба.

Рис. 3.16. Инструмент для заделки раструбных труб: а – конопатка; б – чеканки; в – уширенная конопатка

Рис. 3.17. Приспособления для заделки раструбов чугунных канализационных труб: а – А. Н. Васильева; б – К. Г. Козлова; 1 – труба; 2, 4 – чека; 3 – плита; 5 – скоба; 6 – защелка; 7 – звездочка; 8 – ось; 9 – винт; 10 – хомут
Приспособление К.Г. Козлова (рис. 3.17, б) более совершенно, так как позволяет укреплять трубу в различных положениях. Труба закрепляется хомутом 10 с зажимным винтом 9. Хомут приварен к оси 8, которая может поворачиваться во втулке. Для установки хомута с трубой в определенном положении на оси насажена и приварена звездочка 7, которая фиксируется защелкой 6, поворачивающейся на оси. Соединения труб с заделкой раструба цементом и асбестоцементной смесью наиболее просты и безопасны, но требуют длительного времени для схватывания цемента.

Рис. 3.18. Стенд-карусель для сборки узлов канализационных трубопроводов
Заделка раструбов расширяющимся цементом. Соединение канализационных труб ведут в такой последовательности. Одну трубу укрепляют раструбом вверх в приспособлении (рис. 3.18). На конец другой или фасонной части наматывают два витка пряди толщиной 5–6 мм, длиной 440 мм – для труб диаметром 50 мм и длиной 760 мм – для труб диаметром 100 мм (рис. 3.19, а). Конец трубы с намотанной прядью вставляют в раструб трубы, укрепленной в приспособлении, и прядь осаживают конопаткой (рис. 3.19, б). Затем трубу, вставленную в раструб, центруют тремя металлическими клиньями так, чтобы ширина кольцевого зазора между трубой и раструбом была везде одинакова, после чего клинья вгоняют легкими ударами молотка (рис. 3.19, в).
Для приготовления раствора в сосуд насыпают расширяющийся цемент. Для труб диаметром 50 мм на один стык требуется 125 г цемента, а для труб диаметром 100 мм – 250 г. Затем в сосуд с цементом наливают воду (55–65 % от массы цемента).

Рис. 3.19. Заделка раструба расширяющимся цементом или серой: а – намотка пряди; б – осадка пряди; в – центровка трубы; г – заливка цементом (серой)
Раствор непрерывно перемешивают, чтобы не было комков и сухих частиц. Раствор приготовляют в таком количестве, чтобы один замес для заливки подготовленных стыков можно было использовать в течение 3–4 мин. Кольцевой зазор стыка заливают раствором за один раз и штыкуют его, чтобы не образовалось раковин и пустот (рис. 3.19, г). Через 40 мин после заливки раструба цементом трубу снимают с приспособления, залитые стыки обертывают мокрой тканью или укладывают на 10–12 ч в ванну с водой температурой не менее 20 °C. Чем выше температура воды в ванне, тем быстрее цемент схватывается: при температуре 40 °C цемент в стыке набирает прочность через 5–6 ч.
После выдержки в ванне из стыков легкими ударами молотка извлекают клинья, а оставшиеся от них отверстия заделывают расширяющимся цементом. Заготовленные узлы трубопроводов можно отправлять на объекты не ранее чем через 20 ч после заделки стыков.
Заделка раструбов расплавленной серой. Стоимость и трудоемкость работ по заделке стыков серой ниже по сравнению с заделкой расширяющимся цементом. Однако герметичность стыка уменьшается из-за водопроницаемости серы. Поэтому такой способ задельем раструбов не следует использовать при скрытой прокладке трубопровода и соединении напорных трубопроводов. Раструбы чугунных труб заделывают технической серой (порошковой или комовой) аналогично заливке расширяющимся цементом. Стык, заделанный серой, жесткий и хрупкий. Чтобы уменьшить хрупкость соединения, в серу добавляют 10–15 % молотого каолина.
Перед соединением канализационных труб серу вместе с каолином разогревают в бачке, который установлен внутри специальной печи и омывается минеральным маслом, нагреваемым до температуры 130–135 °C. Сера разогревается в течение 1,5–2 ч и может храниться в расплавленном состоянии не более 2 ч.
Серу заливают в раструб из ковша вместимостью 0,5 л на удлиненной ручке за один прием, не разрывая струи. Количество серы на один раструб трубы диаметром 50 мм составляет 130 г, диаметром 100 мм – 205 г, диаметром 150 мм – 480 г. Твердение серы после заливки раструбов труб диаметром 50 и 100 мм длится 5 мин; а диаметром 150 мм – 10 мин. После затвердевания ее узлов трубопроводов готовы к транспортированию.
Заделка раструбов резиновым кольцом или манжетой. После очистки поверхностей соединяемых труб и уплотнителя – резинового кольца б, манжеты (см. рис. 3.12, б) от пыли и грязи уплотнитель вставляют в желобок 5 раструба 2. Гладкий конец 1 соединяемой трубы на расстоянии 80 – 100 мм покрывают графитоглицериновой смазкой. Выверяют положение труб в плане и по вертикали. Далее надевают на трубы приспособление для стяжки – винтовое или реечное (рис. 3.20) – и с его помощью плавно сближают трубы, вводя гладкий конец в раструб.
Заделка раструбов герметикой. После осмотра и очистки поверхностей трубы и раструба их зачищают, чтобы они имели шероховатую поверхность. Далее одну трубу центруют таким образом, чтобы ширина раструбной щели в рабочей зоне была одинаковой по всей окружности раструба. Затем вводят виток пряди.
Герметик УТ-37А – полимерный материал вязкой пастообразной консистенции, состоящий из герметизирующей К-1 (100 мае. ч.) и отвердевающей (вулканизирующей) Б-1 (9 – 14 мае. ч.) паст. Компоненты смешивают не более чем за 1 ч до использования герметика, после чего полученную смесь подают по шлангу 2 в полость стыка через специальную насадку 1 (рис. 3.21).

Рис. 3.20. Монтажные приспособления для заделки труб с резиновым кольцом: а – винтовое; б – реечное; 1 – захват; 2 – тяги; 3 – упоры; 4 – винтовой механизм; 5 – рычаг; 6 – реечный механизм

Рис. 3.21. Заделка раструбов герметиком: 1 – насадка; 2 – шланг
При вертикальном расположении стыка заполнение герметиком ведут так же, как заливку раструба серой; при горизонтальном – стык заполняют снизу вверх равномерно с двух сторон трубы. После заполнения стыка к герметику по окружности прижимают накладку, которую снимают после вулканизации герметика (превращение его в резиноподобный материал).
Стыки труб, заделанные герметиком УТ-37А, эластичные и прочные, выдерживают давление до 1,5 МПа.
Контроль качества. После того как уплотнитель затвердеет, соединение осматривают, проверяя плотность заполнения зазора между раструбом и гладким концом. Расслоение, раковины в залитых серой и цементом стыках, а также неполная их заливка не допускаются. Прочность и плотность раструбных соединений проверяют контрольной разборкой нескольких стыков.
3.5. Соединение полимерных труб
Полимерные трубы соединяют сваркой, склеиванием, с помощью раструбов, фланцев, накидных гаек. Выбор соединения зависит от материала труб, условий работы и прокладки трубопроводов. Полимерные трубы соединяют в такой последовательности: размечают и отрезают трубную заготовку заданной длины, подготовляют место соединения труб, выполняют стыковые соединения.
Разметку этих труб производят аналогично стальным, но разметочный инструмент, оставляющий на поверхности трубы риски или надрезы, использовать запрещается.

Рис. 3.22. Резка полимерных труб: а – ножовкой; б – труборезом; в – шаблон для резки
Резку труб выполняют ножовками для резки металла, мелкозубыми ручными пилами по дереву, труборезом. При резке труб под углом используют шаблон (рис. 3.22, в). При резке отклонение от плоскости реза не должно превышать 0,5 мм для труб диаметром до 50 мм, 1 мм – для труб диаметром 50 – 160 мм, 2 мм – для труб большего диаметра.
Соединение сваркой. При соединении полимерных труб применяют контактную стыковую или раструбную сварку, а также сварку нагретым газом с применением присадочного материала.
Подготовка труб к сварке начинается с осмотра труб и подборки их по диаметрам, толщинам и партиям поставки. Трубы с дефектами, овальностью более 10 %, трещинами, задирами, царапинами глубиной более 0,5 мм отбраковывают. Трубы с овальностью более допустимой (10 %), ведущей к смещению кромок при сборке более чем на 10 % от толщины стенок, но не более 1,2 мм можно исправить путем калибровки на специальном приспособлении.
Трубы с трещинами или другими дефектами на концах могут быть использованы только после отрезки поврежденных участков. Причем место отрезки должно находиться на расстоянии не менее 50 мм от края повреждения.
Для соединения отбирают трубы из одной партии поставки, что позволяет уменьшить влияние свойств материала на качество сварки и подобрать трубы со стабильными размерами. Недопустимо соединять трубы из полиэтилена высокой (ПВП) и низкой (ПНП) плотности, полиэтилена и полипропилена (ПП).

Рис. 3.23. Устройство для торцовки и снятия фасок полимерных труб
Следующий этап подготовки труб к сварке – очистка концов труб от грязи, масла, краски, а также поверхности труб снаружи и внутри на расстоянии от конца не менее чем на 30 мм. Грязь удаляют водой с применением волосяных щеток и последующей протиркой. Соскабливать загрязнения металлическими щетками и инструментом не допускается. Затем концы труб обезжиривают ацетоном (ГОСТ 2768-84*), уайт-спиритом (ГОСТ 3134-78*).
Поврежденный и подвергшийся старению поверхностный слой выравнивают и снимают зачисткой торцов (торцовкой) путем обрезки или фрезерования острым инструментом или специальным устройством (рис. 3.23). Толщина удаляемого слоя – не менее 1–3 мм. Торцы зачищают непосредственно перед сваркой (но не ранее чем за 6–8 ч до сварки), чтобы свариваемые поверхности не окислялись и не загрязнялись.
Контактную стыковую и раструбную сварку выполняют путем нагревания до расплавления материала с последующим сдавливанием соединяемых поверхностей и охлаждением стыка под давлением. Контактную сварку выполняют при температуре воздуха не ниже – 10 °C для ПНП и ПВП и 0 °C – для ПП.
Контактную стыковую сварку осуществляют следующим образом. После подготовки трубы укладывают и центрируют, далее вводят нагревательный элемент, который оплавляет торцы труб. Затем нагревательный элемент удаляют и трубы соединяют под давлением, выдерживая их до охлаждения стыка.
Контактную сварку разделяют на механизированную и ручную.
Механизированную выполняют на сварочных установках, обеспечивающих высокую точность поддержания технологического режима и высокое качество сварки. Сварочная установка (рис. 3.24, а) состоит из зажимов для закрепления концов труб 2 больших диаметров и нагревательного элемента 3, подвижно закрепленного на установке. Нагревательный элемент, как правило, снабжен электрическим нагревом. Для этого в диск вмонтирован тепловой электрический элемент (ТЭЭ), который питается от блока напряжением 36 В. Постоянная температура элемента поддерживается терморегулятором.

Рис. 3.24. Контактная стыковая сварка полимерных труб: а – механизированная; б – ручная; 1 – зажимы; 2 – трубы; 3 – нагревательный элемент; 4 – блок питания
При ручной сварке (рис. 3.24, б), применяемой в малоудобных местах (подвалах, колодцах, траншеях), используют нагревательный элемент, устройства для торцовки и центровки труб (рис. 3.25). Устройство для центровки труб небольшого диаметра состоит из зажимов 2, которыми захватываются трубы, и рычагов 7, сжимающих их после оплавления торцов труб.

Рис. 3.25. Устройство для центровки труб:1 – рычаги; 2 – зажимы
При сварке после закрепления в зажимах торцы труб приводят в соприкосновение; при этом зазор между ними не должен превышать 0,5 мм для труб диаметром до 110 мм и 0,7 мм – для труб большего диаметра. Если это условие не достигается, производят дополнительную обработку торцов труб.
Затем трубы разводят и в зазор между ними вводят нагревательный элемент (рис. 3.26, а). Температуру элемента, зависящую от материала трубы, контролируют термометром. При его отсутствии температуру можно определить приблизительно, проведя куском материала, отрезанным от свариваемой трубы, по нагретой поверхности элемента: он должен плавиться, но не должен дымиться.

Рис. 3.26. Технологическая последовательность соединения полимерных труб контактной стыковой сваркой: а – введение нагревательного элемента; б – оплавление концов труб; в – удаление нагревательного элемента; г – соединение (осадка) труб; 1 – трубы; 2 – нагревательный элемент; 3 – валик из расплавленного материала; 4 – сварной шов
Оплавление концов труб (рис. 3.26, б) производят путем плотного и равномерного прижатия их торцов к нагревательному элементу. Время нагрева зависит от толщины стенки трубы и материала. Давление при нагреве поддерживают до тех пор, пока не будет достигнут полный контакт между свариваемыми поверхностями и инструментом. С появлением валика 3 из расплавленного материала давление постепенно снижают, а нагрев продолжают до образования валика высотой 2–2,5 мм при толщине стенки трубы до 5 мм и не более 3–5 мм при большей толщине.
После окончания оплавления трубы разводят и извлекают элемент (рис. 3.26, в), а затем не более чем через 2–3 с после того, как извлекли инструмент, плотно соединяют оплавленные концы труб (осадка труб) (рис. 3.26, г). Трубы прижимают одну к другой под давлением осадки 0,1–0,25 МПа, при этом образуется прочный шов. Сварное соединение охлаждают, не снижая давления осадки, в течение 3 – 10 мин в зависимости от толщины стенки и вида материала труб. При охлаждении не допускается перемещать и вращать концы труб в зоне сварного шва.
Контактную раструбную сварку выполняют в такой последовательности. После подготовки труб нагревательный элемент вводят между их концами, которые затем сближают таким образом, чтобы они соприкасались с нагревательным элементом. После оплавления соединяемых поверхностей трубы разводят, удаляют нагревательный элемент и быстро вставляют гладкий конец трубы в раструб, выдерживая соединяемые детали в неподвижном состоянии до охлаждения.
Преимущества контактной раструбной сварки по сравнению со стыковой состоят в следующем: не образуются наплывы материала, которые мешают свободному движению жидкости в трубопроводе; создается прочное соединение – за счет большой площади соприкосновения; не требуется усилий для центровки и сжатия труб при их соединении.
Раструбное соединение (рис. 3.27, а) обычно выполняют с помощью раструбных соединительных деталей: тройников 4 (рис. 3.27, б), муфт 5 (рис. 3.27, в). При отсутствии соединительных деталей сварку производят в раструб 1 (рис. 3.27, г), отформованный на гладком конце трубы 3. Внутренний диаметр соединительной детали или раструба должен быть меньше наружного диаметра соединяемой трубы.

Рис. 3.27. Контактная раструбная сварка (а) в литой тройник (б), муфта (в), раструб (г):1 – раструб; 2 – нагревательный элемент; 3 – гладкий конец трубы; 4 – тройник;5 – муфта
Нагревательный элемент 2 (см. рис. 3.27, а), используемый для контактной раструбной сварки, по конструкции проще, чем для стыковой. Однако в зависимости от диаметра соединяемых труб следует применять определенный нагревательный элемент или сменные насадки. Нагревательный элемент изготовляют из сплавов алюминия или нержавеющей стали. Поверхности инструмента, соприкасающиеся с материалом труб, должны быть отполированы и покрыты материалом, к которому не прилипает расплавленная пластмасса.

Рис. 3.28. Технологическая последовательность контактной раструбной сварки;а – введение нагревательного элемента; б – оплавление концов труб; в – соединение труб; 1 – раструб; 2 – дорн; 3 – нагревательный элемент; 4 – гильза; 5 – гладкий конец трубы; 6 – хомут
При сварке труб небольшого диаметра на строительной площадке элемент нагревают паяльной лампой или газовой горелкой. При этом температуру элемента контролируют термокарандашом или куском материала, отрезанным от свариваемой трубы.
При нагреве и оплавлении труб нагревательный элемент 3 помещают между концами соединяемых труб так, чтобы дорн 2 (рис. 3.28, а) находился напротив раструба 7, а гильза 4 – напротив гладкого конца трубы 5. Чтобы ограничить глубину входа гладкого конца трубы 5 в нагревательный элемент на расстоянии, равном глубине гильзы 4, устанавливают ограничительный хомут 6. Раструб 1 и гладкий конец трубы 5 быстро надвигают на нагревательный элемент 3 (рис. 3.28, б). Время нахождения концов труб на нагревательном элементе должно обеспечить равномерное оплавление всей площади соприкасающихся поверхностей без потери формы и жесткости деталей. Если надвигание производить медленно, то концы соединяемых труб могут прогреться на всю толщину стенки или большую часть ее и потерять форму.
Процесс оплавления продолжают до тех пор, пока у кромок раструба и на трубе по всему периметру не появится валик оплавленного материала высотой 1–2 мм. После этого быстро раздвигают соединяемые трубы и удаляют нагревательный элемент из зоны соединения. Затем, не более чем через 2–3 с, трубы соединяют, вводя гладкий конец трубы 5 в раструб 7 (рис. 3.28, в) и выдерживая их под осевой нагрузкой 20–30 с до начала отверждения материала. После соединения труб их нельзя поворачивать и смещать относительно друг друга.
Сварку нагретым газом с применением присадочного материала (рис. 3.29) выполняют путем разогрева кромок соединяемых труб (деталей) 1 и прутка 2 присадочного материала с помощью горелки 3 и последующего заполнения шва материалом прутка, который вдавливают в разогретые поверхности. Этот способ универсален, так как позволяет производить сварку в любом положении шва, не требует точной подгонки деталей и сложного инструмента.

Рис. 3.29. Сварка полимерных труб нагретым газом с применением присадочного материала:1- трубы; 2 – пруток из присадочного материала; 3 – горелка; 4 – шланг для подачи газа; 5 – провод
В горелки 3, используемые для подогрева стыка, газ подается от компрессора по шлангу 4. Газ нагревается электрической спиралью, питаемой током по проводу 5, и через сопло подается в зону сварки.
Сварка труб нагретым газом может быть стыковой или раструбной. Прочность стыкового соединения на растяжение выше, чем раструбного, а на изгиб – наоборот. Сварку труб нагретым газом ведут в такой последовательности: подготовляют пруток присадочного материала к сварке, подбирают горелку и включают ее, контролируют температуру нагретого газа и производят сварку.
При подготовке труб к сварке зачищают и обезжиривают места сварки. При стыковой сварке труб толщиной 2–5 мм снимают фаску под углом 60–65°. Материал прутка выбирают в соответствии с материалом свариваемой трубы, его толщиной, формой шва, прочностью соединения. Для сварки используют пруток простого (круглого) и сложного (двойного) профиля толщиной 3–4 мм. Пруток простого профиля используют при сварке труб толщиной до 5 мм, сложного профиля – при большей толщине. Конец прутка обрезают под углом 30°. Горелку подбирают так, чтобы диаметр ее сопла был на 1 мм больше диаметра прутка. Подача газа – 3–7 м3/ч при давлении перед горелкой до 0,04 МПа. Температура газа на выходе из сопла зависит от вида материала: для ПВХ, ПНП – 230–270 °C; ПВП, ПП – 250–300 °C. Горелку включают и выводят на расчетный режим следующим образом. Открывают вентиль подачи сжатого воздуха и включают питание спирали. Через 3–5 мин после прогрева горелки окончательно устанавливают температуру газа, регулируя его подачу: при уменьшении подачи температура повышается, при увеличении – уменьшается. Температуру контролируют термометром или путем теплового воздействия на контрольные образцы. При этом на кусочке, отрезанном от свариваемого изделия и размещенном на расстоянии 6–8 мм от сопла, через 5 с должно появиться матовое пятно, а белая бумага, поднесенная к соплу, должна окраситься в темно-бурый цвет.
Нагретый газ должен быть чистым: не содержать пыли, масла и других веществ, ухудшающих качество шва. Чистоту нагретого газа проверяют, размещая на пути потока белый кусок хлопчатобумажной ткани или бумаги: на них не должно появляться черных пятен или точек.
При сварке полимерных труб 1 (см. рис. 3.29) струю горячего газа направляют попеременно круговыми или колебательными движениями горелки 3 на пруток 2 и свариваемые кромки до образования матовой поверхности. Расстояние между наконечником горелки и поверхностью свариваемого шва должно быть в пределах 5–8 мм. По мере размягчения прутка и свариваемых труб пруток с усилием (для прутка диаметром 3 мм – 18–22 Н, а диаметром 4 мм – до ЗО Н) вдавливают в разделку стыка. При этом его следует держать по отношению к оси трубы под углом 60–90° при стыковой сварке и 45° – при раструбной. Сопло горелки должно составлять с осью трубы угол 15–25° – для труб толщиной стенки до 5 мм и 30–45° – свыше 5 мм в направлении, противоположном общему направлению сварки.
При сварке пруток держат в левой руке между большим и указательным пальцами на расстоянии 70–80 мм от поверхности сварки, а горелку – в правой руке. Пруток укладывают в шов в определенном порядке, обеспечивая равномерное распределение напряжений в шве. По мере укладки прутка пальцы передвигают равномерно вверх. Перехватывать пруток следует плавно, не прерывая процесса сварки. При этом следят, чтобы при укладке первого валика часть прутка выступала с внутренней стороны шва на 0,5–1 мм, а в раструбных соединенях, катет углового шва по периметру трубы должен быть равен толщине стенки раструба.
При размягчении прутка на расстоянии более 20–30 мм от точки сваривания сварку приостанавливают и пруток охлаждают. При смене или обрыве прутка конец приваренного прутка нагревают и срезают под углом 20–30°, затем к полученному срезу внахлестку приваривают также подготовленный новый пруток. Необходимо, чтобы на шве расстояние между стыками прутков было не менее 8 мм.
Соединение полимерных труб на клею. Этот способ используют для соединения раструбных труб и фасонных частей из ПВХ с зазором и без зазора.
При склеивании труб без зазора, когда разность диаметров склеиваемых элементов менее 0,1 мм, применяют клей, состоящий из перхлорвиниловой смолы (14–16 мае. ч.) и метилхлорида (86–84 мае. ч.). При склеивании труб диаметром более 100 мм, а также труб различных диаметров при повышенных температуре (более 25 °C) и скоростях движения воздуха в зоне монтажа используют Белей, состоящий из перхлорвиниловой смолы (14–16 мае. ч.), метилхлорида (76–72 мае. ч.), циклогексаната (10–12 мае. ч.).
Для склеивания труб с зазором, когда разность диаметров склеиваемых элементов менее 0,6 мм, используют зазорозаполняющий клей ГИПК-127, состоящий из тетрагидрофурана (растворитель ПВХ), поливинилхлоридной смолы, оксида кремния. Трубы СБелеивают при температуре воздуха не ниже 5 °C. Рабочее место должно быть защищено от ветра и атмосферных осадков. СБелеивание труб производят в такой последовательности: размечают посадочную длину, подготавливают склеиваемые поверхности, наносят клей, соединяют трубы.
Разметку посадочной длины (рис. 3.30, а) выполняют линейкой, складным метром 3 и карандашом 2. Длина посадочной части равна длине нахлеста клеевого соединения, которая должна быть на 6 мм больше наружного радиуса трубы.

Рис. 3.30. Последовательность соединения полимерных труб на клею: а – разметка посадочной длины; б – очистка склеиваемых поверхностей гладкого конца и раструба; в – проверка консистенции клея; г – нанесение клея на раструб и гладкий конец трубы; д – соединение труб; 1 – гладкий конец трубы; 2 – мягкий карандаш; 3 – складной метр; 4 – раструб; 5 – шлифовальная шкурка; 6 – палочка; 7 – клей;8 – кисть
Подготовка склеиваемых поверхностей заключается в зачистке гладкого конца трубы 1 и внутренней поверхности раструба 4 шлифовальной шкуркой 5 (рис. 3.30, б). Затем зачищенные поверхности обезжиривают органическими растворителями (метиленхлоридом). Перед склеиванием труб без зазора проверяют плотность сопряжения деталей. При плотном сопряжении клей наносят одним слоем, при свободном сопряжении – двумя слоями (второй наносят после просыхания первого слоя до отлипа). Клей наносят кистью из натуральной щетины. Перед нанесением клея проверяют его консистенцию (рис. 3.30, в), обмакивая палочку 6 в клей 7: Белей должен стекать с палочки ровной струей (консистенция сметаны). Густой клей разбавляют растворителем. Сначала Белей наносят кистью 8 на внутреннюю поверхность раструба 4 (рис. 3.30, г), а затем на гладкий конец трубы 1.
При склеивании труб без зазора клей наносят на 2/3 глубины раструба и на всю длину калиброванного конца трубы равномерным тонким слоем. При сбелеивании с зазором на раструб наносят тонкий слой, а на конец трубы – толстый слой Белея. Гладкие концы труб из ПВХ с раструбами, имеющими желобки под резиновое кольцо, склеивают только зазорозаполняющими іелеями. На поверхность желобка клей не наносят.
Соединяют трубы (рис. 3.30, д) сразу после нанесения клея, вдвигая гладкий конец трубы 1 в раструб 4. Лишний клей, вытесняемый из зазора, немедленно удаляют.
Правообладателям!
Данное произведение размещено по согласованию с ООО "ЛитРес" (20% исходного текста). Если размещение книги нарушает чьи-либо права, то сообщите об этом.Читателям!
Оплатили, но не знаете что делать дальше?