Текст книги "Круглопильные и ленточнопильные станки"
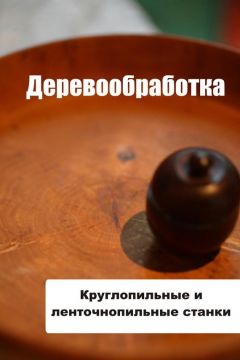
Автор книги: Илья Мельников
Жанр: Хобби и Ремесла, Дом и Семья
Возрастные ограничения: +12
сообщить о неприемлемом содержимом
Текущая страница: 1 (всего у книги 2 страниц) [доступный отрывок для чтения: 1 страниц]
Илья Мельников
Круглопильные и ленточнопильные станки
Классификация станков
По назначению деревообрабатывающие станки подразделяют на три группы: универсальные, имеющие широкое распространение в различных деревообрабатывающих производствах; специализированные, предназначенные для выполнения только определенных видов работы с переналадкой станка, и специальные для определенной обработки без переналадки станка.
Деревообрабатывающие станки могут быть цикловые – с прерывистым движением детали или режущего инструмента и проходные – с непрерывным перемещением детали. У проходных станков деталь непрерывно перемещается относительно рабочих органов и при этом обрабатывается.
В зависимости от способа обработки древесины и вида технологической операции различают станки круглопильные, ленточнопильные, фуговальные, рейсмусовые, четырехсторонние, фрезерные, шипорезные, сверлильно-пазовальные, токарные, шлифовальные и др.
Для обозначения вида и станков принята буквенно-цифровая индексация. Первая буква обозначает тип станка: Л – ленточный, Ц – круглопильный, С – четырехсторонний продольно-фрезерный, фуговальный, рейсмусовый, фрезерный, Ш – шипорезный, СВ – сверлильный, Шл – шлифовальный и т. д.
Цифры после первой буквы указывают на количество рабочих органов или агрегатов станка: например С2Ф – фуговальный станок с двумя (горизонтальным и вертикальным) режущими инструментами и т. п.
Вторая и третья буквы характеризуют технологические особенности станка: ЛС – ленточнопильный столярный, ЦДК – круглопильный для продольной распиловки с конвейерной подачей, СР – рейсмусовый, ФС – фрезерный средний, СВПГ – сверлильно-пазовальный горизонтальный и т. д.
Цифры после букв индекса характеризуют главный параметр станка либо номер модели станка: СР6-9 – станок рейсмусовый, ширина стола 630 мм, девятая модель и т. д.
Основные агрегаты станков
Различаясь технологическим назначением и способом обработки детали, деревообрабатывающие станки имеют подобные конструктивные элементы и функциональные механизмы. Использование в разных станках повторяющихся нормализованных элементов и деталей называют нормализацией.
Иногда станки полностью состоят из одинаковых составных частей и отличаются один от другого только взаимным расположением рабочих органов. Такое заимствование элементов называют унификацией.
Когда станки собирают из отдельных агрегатов, которые выпускаются специализированными заводами, такие станки называют агрегатными.
Элементы станков разделяют по выполняемым функциям. Для установки и монтажа всех составных частей станка служит станина. Она устанавливается на фундамент или специальные виброизолирующие опоры. На станине располагаются корпусные детали, которые воспринимают нагрузки от рабочих органов и образуют контур станка – основания, стойки, поперечины, траверсы, кронштейны и т. д. Корпусные детали не перемещаются в ходе работы, но в ряде случаев их положение можно менять до начала обработки изделия.
Требование к станине и корпусным деталям – точность и жесткость, так как эти показатели влияют качество обработки деталей.
Агрегаты станка, обеспечивающие главное движение, называют механизмом резания. Механизм резания выполняют в виде ножевого вала, шпинделя или пильного вала. На них крепят режущий инструмент.
Следующий агрегат – механизм подачи. Он предназначен для обеспечения подачи заготовки. Выполняется в виде конвейера, вальцов или роликов. (В цикловых станках механизмом подачи является подвижный стол или каретка.)
Расположение заготовки относительно режущего инструмента устанавливается специальными устройствами. Они включают базовые элементы станка: столы, направляющие линейки, угольники, упоры, прижимные приспособления. С помощью их достигается устойчивое положение обрабатываемой детали в проходных станках. Прижимы делают в виде клиновых ремней или лент.
На позиционных станках используются зажимы в виде колодок и пластин. Для предотвращения порчи детали рабочие элементы зажимов оснащаются съемными резиновыми накладками.
Для обеспечения настроечных перемещений служат суппорты, которые могут переставляться вручную или от механического привода. У суппорта точно обработанные поверхности, которые называют направляющими. Такие же направляющие есть на станине или корпусной детали, на них и устанавливается суппорт.
Оградительные и предохранительные устройства. Они бывают в виде колпаков, кожухов, крышек. Эти части станка предохраняют рабочего от случайного касания движущихся механизмов станка. (Ограждения блокируют с приводом станка, чтобы при их снятии станок автоматически выключался.)
Управляются станки с помощью маховиков, педалей, рукояток, кнопок и переключателей. В сложных станках органы управления выполняются в виде пульта, на котором расположены кнопки включения и выключения рабочих органов.
И последнее – вспомогательные элементы. К ним относят устройства для смазывания трущихся частей станка: масленки, шприцы, насосы для подачи масла.
Базирующие устройства служат для обеспечения качественной обработки детали – с их помощью осуществляется ориентирование, базирование и закрепление заготовки в нужном положении относительно рабочих органов станка. Ориентирование заготовки производится вручную или специальным ориентирующим устройством: винтовыми роликами, диском, отклоняющим щитком.
Базирование – ответственный этап механической обработки, так как качество его выполнения определяет точность обработанной детали. Правильная взаимная ориентировка детали и рабочих инструментов в станке определяется назначением технологических баз. Технологическая база – это совокупность базирующих поверхностей, используемых для придания заготовке заданного положения относительно режущего инструмента.
Обрабатываемые детали бывают прямолинейные с профильным поперечным сечением, в виде тела вращения или сложной пространственной формы. Базирующими поверхностями призматической заготовки являются ее пласть, кромка и торец, которые соответственно называются главная, направляющая и упорная поверхности. При базировании эти поверхности соприкасаются с опорными элементами станка. В зависимости от вида контакта заготовки с элементами различают подвижное и неподвижное базирование.
При подвижном базировании заготовка находится с опорным элементом в состоянии подвижного контакта. При неподвижном базировании заготовка в процессе обработки неподвижна относительно опорных элементов станка.
Элементы базирования деталей бывают разных конструкций. Это столы, направляющие линейки, упоры, патроны, планшайбы токарных станков.
Столыдля неподвижного базирования деталей представляют собой массивные плиты с плоской рабочей поверхностью. Стол для подвижного базирования детали должен иметь гладкую поверхность с низким коэффициентом трения. Кромка стола, примыкающая к режущему инструменту, в процессе эксплуатации обычно изнашивается и эту часть стола обычно оснащают съемной стальной накладкой. На столе монтируют направляющие линейки или угольники.
Иногда столы оснащают роликами или делают в виде роликового конвейера. Если ролики приводные, то они являются не только установочными элементами, но и служат средством для транспортировки деталей.
В зоне движения режущего инструмента на столе монтируют деревянную плиту с пазом, которая обеспечивает устойчивое положение отпиливаемых кусков материала.
Направляющие линейки станков исполняются в виде бруса с гладкой поверхностью. Концы линейки, обращенные к пиле, оснащают съемными накладками. Иногда направляющие линейки оснащают вращающимися роликами, что снижает сопротивление подачи обрабатываемого материала.
Упорыслужат для точного базирования детали по длине. Они бывают утапливаемыми и откидными. Упор должен иметь достаточную жесткость, иначе при повторяющихся ударных нагрузках он может сместиться, что приведет к браку.
Правильное положение заготовки относительно стола и направляющей линейки при проходной обработке достигается боковым и верхним прижимами. Прижимы делают в виде колодки, подпружиненного башмака, или гибких пластин со скользящей рабочей поверхностью. Для уменьшения трения скольжения применяют роликовый прижим.
На станках с поперечной подачей деталей прижимное устройство выполняют в виде двух параллельных агрегатов, оснащенных бесконечными клиновыми ремнями. Ремни приводятся в движение силами трения о заготовку. Натяжение ремня можно регулировать, смещая ось шкива относительно корпуса прижима.
Наладка и настройка станков
Геометрическая точность станка, правильность наладки и настройки его оказывает существенное влияние на качество обработки деталей.
Деревообрабатывающие станки по точности выполняемых работ подразделяют на четыре класса: особой точности (О), обеспечивающие точность обработки по 10-12-му квалитетам; повышенной точности (П), обеспечивающие точность обработки по 11-12-му квалитетам (фрезерные, четырехсторонние и т. п.); средней точности (С), обеспечивающие обработку по 13-15-му квалитетам (токарные, сверлильные и т. п.); нормальной точности (Н), обеспечивающие точность обработки по 14-18-му квалитетам (ленточнопильные, круглопильные и т. п.).
Рассмотрим основные причины возникновения погрешностей при механической обработке древесины.
Геометрическая неточность станка и его износ. Не секрет, что детали станков часто изготовляют с погрешностями. В процессе сборки станка эти погрешности суммируются, таким образом точность расположения исполнительных поверхностей станка нарушается. На точность станка влияет также износ деталей в процессе эксплуатации.
Искажение формы режущей кромки резца при его заточке, погрешность при установке и закреплении режущего инструмента, а также его биение.
Зажимные и установочные элементы приспособления имеют погрешности даже при самом тщательном изготовлении. При установке заготовки в приспособление возникают погрешности базирования. В приспособлении под действием зажимных усилий и усилий резания возникают упругие деформации, которые также снижают точность обработки.
Недостаточная жесткость системы станок-приспособление-инструмент-деталь (СПИД). Жесткостью этой системы называют способность обеспечивать необходимую точность обработки при нагрузках, возникающих в процессе работы станка.
При обработке партии заготовок силы резания изменяются в зависимости от величины припуска на обработку, степени затупления инструмента и механических свойств древесины, что вызывает упругие деформации технологической системы СПИД. Деформации нарушают расположение установочных поверхностей станка и точность обработки снижается.
Ошибки при настройке станка. Ошибки возникают из-за неправильного отсчета показаний, погрешности измерения пробных деталей, неточности контрольно-измерительного инструмента. Эти ошибки и погрешности образуют результирующую погрешность механической обработки.
Наладка станка – это регулирование и согласование взаимодействия всех элементов станка, установление режимов обработки, пробный пуск и контроль обработанных деталей.
Размерной настройкой станка называют действия по обеспечению требуемой точности расположения режущего инструмента относительно установочных элементов станка (столов, упоров).
Статическая настройка с использованием встроенных в станок измерительных устройств заключается в том, что станочник перемешает рабочий орган на требуемый настроечный размер и одновременно контролирует величину перемещения по отсчетному устройству.
Статическая настройка станка по эталону (шаблону) заключается в регулировке положения инструмента до касания его лезвий рабочей поверхности шаблона. Допускаемое отклонение на настроечный размер должно быть меньше допускаемого отклонения на размер детали, подлежащей обработке. (Часто в качестве эталона используют ранее изготовленную на станке деталь.)
Эталоны применяют при настройке многошпиндельных станков и в тех случаях, когда надо одновременно учитывать несколько настроечных размеров или взаимных положений режущих инструментов, обрабатывающих деталь сложной формы.
Настройка по эталону не всегда обеспечивает необходимую точность. После обработки некоторого количества деталей необходимы дополнительное регулирование и поднастройкастанка.
Статическую настройку станка с помощью универсальных измерительных приборов используют в станках, которые налаживают на один настроечный размер или в станках, не имеющих встроенного отсчетного устройства. В качестве измерительного инструмента применяют магнитные стойки, микрометры, штангенциркули. Контроль перемещения рабочего органа в момент его регулировки позволяет достичь высокой точности настройки.
Статическая настройка с помощью настроечно-измерительных приспособлений обеспечивает высокую точность. Эти приспособления конструируют для конкретного станка и изготовления конкретной детали.
Нередко настраивают станок, изготовляя пробные детали. В этом случае станок настраивают сначала с помощью встроенного измерительного устройства или других средств. Предварительную настройку выполняют с меньшей точностью, чем статическую. Обычно величина первоначального настроечного размера существенно отличается от величины среднего размера детали и выбирается такой, чтобы при обработке деталей размер их получался несколько большим, чем нужно, что исключает выпуск неисправимого брака. После предварительной грубой настройки обрабатывают пробные заготовки, детали проверяют калибром или измерительным инструментом.
Эту настройку с контролем деталей предельным калибром осуществляют тем же рабочим калибром, который используют в дальнейшем при контроле деталей всей партии. Если размер пробной детали находится в пределах допуска, настройка считается правильной.
Настройка по пробным деталям позволяет определить по результатам измерений среднее значение размера трех-пяти пробных деталей и поле рассеяния соразмеров. В результате поднастройки получают новое значение настроечного размера. Если этот размер находится в пределах допуска, обрабатывают всю партию деталей.
Этот метод расчета величины поднастройки применяют при обработке небольшой партии деталей, когда износ инструмента невелик и не может оказать существенного влияния на точность обработки.
Круглопильные станки
Технологическую операцию раскроя древесных материалов выполняют на круглопильных станках. Раскрой может быть предварительный и чистовой.
Применяются следующие виды раскроя на круглопильных станках.
Торцевание досок и брусковых заготовок производят на станках для поперечного раскроя. Они бывают одно– или многопильные, на которых можно выпиливать одновременно несколько заготовок.

Рис. Универсальный круглопильный станок Ц6-2:
1 – пильный вал, 2 – стол, 3 – передвижной упорный угольник, 4 – ограждение, 5 – направляющая линейка
Продольный раскрой пиломатериалов и заготовок осуществляют на круглопильных станках для продольного раскроя. На многопильных станках производят выпиловку из одной широкой заготовки за один проход нескольких брусков или реек. Пильные валы этих станков могут иметь до пяти и более пил.
Когда требуется распилить материал не только в поперечном и продольном направлениях, но и под косым углом, такой раскрой выполняют на универсальных круглопильных станках.
Раскрой листовых материалов и плит на щитовые детали производят на раскроечных станках, кромки опиловывают на форматно-обрезных. Если нужны детали с профильными кромками, форматно-обрезные станки оснащаются профильными фрезами для выполнения этой работы.

Рис. Прирезной станок ЦДК4-3:
1 – стол, 2 – гусеничная цепь, 3 – корпус суппорта прижимного устройства, 4 – ролики, 5 – пила, 6 – электродвигатель, 7 – маховичок механизма настройки пильного вала по высоте, 8 – то же, прижимного устройства, 9 – направляющая линейка, 10 – фиксатор линейки, 11, 13 – звездочки, 12 – редуктор
По расположению пилы относительно материала различают станки с нижним и верхним расположением пилы. Расположение пилы и направление ее вращения выбирают с таким расчетом, чтобы сила пиления прижимала заготовку к базирующим элементам станка.
В одних конструкциях станков заготовку подают на пилу, в других пилу двигают на заготовку.
Основными параметрами круглопильных станков являются наибольшая ширина и наименьшая или наибольшая длина распиливаемого материала, эти параметры определяют и габаритные размеры станка.
Толщину распиливаемого материала определяет мощность привода механизма резания.
К материалу, поступающему на круглопильные станки, предъявляются определенные требования относительно размеров и формы. Нестандартные сечения или сильно покоробленный материал могут быть причиной брака и даже поломки механизмов станка.
Режущий инструмент круглопильного станка – круглые пилы. Пилы круглые для поперечного пиления с разводом зубьев используют для торцевания детали. Для закрепления на шпинделе пила имеет посадочное отверстие, диаметр которого зависит от диаметра диска и толщины пилы. Число зубьев пилы – 48, 60 или 72. Зубья имеют боковую заточку по передней и задней граням и отрицательный передний контурный угол, равный -25°. Угол заострения боковых режущих кромок зуба должен быть 45° при распиловке хвойных пород древесины и 55° при распиловке твердой древесины.
Пилы с пластинами из твердого сплава применяют для поперечной обработки. Зубья выполнены с наклонной задней поверхностью. В зависимости от наклона различают пилы левые, правые или с симметричным чередующимся наклоном.
Пилы для смешанного пиления должны иметь зубья, передний контурный угол которых равен 0°.
Для обеспечения высокого качества пиления используют строгальные пилы с отрицательным передним углом или твердосплавные пилы с чередующимся симметричным наклоном задней поверхности зубьев.
Подготовка к работе пил включает правку, заточку и развод зубьев. Пилы должны соответствовать следующим требованиям. Количество зубьев и профиль должны отвечать виду распиловки. Диск пилы должен быть плоским, отклонение от плоскостности на каждой стороне диска диаметром до 450 мм должно быть не более 0,1 мм. (Пилы проверяют поверочной линейкой или на специальном приспособлении.) Заточенные зубья пилы не должны иметь блеска на углах, образованных пересечением рабочих граней резца. Блеск говорит о том, что при заточке с зуба сошлифован недостаточный слой металла. Разница по величине передних углов и углов заострения допускается не более +2°.
Зубья заточенной пилы должны быть без заусенцев, надломов и заворотов. Заусенцы с боковых граней зубьев удаляют мелкозернистым шлифовальным бруском. Качество заточки пил проверяется универсальным угломером или шаблоном для контроля угловых элементов зубьев. Вершины зубьев должны располагаться на одной окружности с отклонением не более 0,15 мм. Зубчатый венец по высоте и ширине зубьев выравнивается фугованием, при котором сошлифовывают материал с кончиков выступающих зубьев при вращении пилы на рабочей частоте.
После заточки зубья пил разводят – отгибают кончики соседних зубьев в разные стороны на 1/3 их высоты. Величину отгиба каждого зуба устанавливают в зависимости от режима резания и пород древесины. Точность развода проверяется индикаторным разводомером или шаблоном.
Круглые пилы с пластинами из твердого сплава готовят иначе. Подготовка включает припайку пластин, заточку и доводку зубьев, затем следует балансировка. Неуравновешенность дисков может вызвать потерю устойчивости пильного диска, сильное биение шпинделя и неудовлетворительное качество распиловки.
Заточку и доводку пил, оснащенных пластинами из твердого сплава, выполняют на полуавтоматах повышенной точности. Сначала заточку производят абразивными кругами, затем точат и доводят алмазными кругами. Балансировка осуществляется на специальном приспособлении.
Станки для поперечного раскроя. Различают круглопильные станки для предварительной торцовки досок по длине и окончательной чистовой торцовки.
В зависимости от характера подачи пилы и расположения ее относительно распиливаемого материала станки бывают с нижним расположением пилы, с верхним расположением и прямолинейным перемещением пилы или с шарнирно-рычажной подвеской пилы.
Торцовочный станок с прямолинейным перемещением пилы – ЦПА40. Кроме поперечной распиловки досок, брусьев и щитов, он служит также для выработки пазов. В верхней части станка на подшипниковых опорах-роликах установлен суппорт. Колонка переставляется по высоте маховичком и крепится рукояткой. Пильный суппорт подается нажатием на педаль. К суппорту прикреплен электродвигатель, на вал которого установлена круглая пила. Заготовки базируются на столе с роликами, направляющей линейкой и торцовыми упорами.

Рис. Торцовочный станок ЦПА40:
1 – маховичок механизма установки суппорта по высоте, 2 – педаль включения подачи, 3 – стакан станины, 4 – колонка, 5 – винт подъема колонки, 6 – электродвигатель, 7 – ограждение, 8 – пила, 9 – гидрораспределитель, 10 – суппорт, 11 – опорные ролики
Станки для чистовой торцовки деталей бывают концеравнительные с одновременной обработкой двух торцов заготовки (Ц2К12-1, Ц2К20-1) и с фрезерными головками для выборки профиля на кромках щитовых деталей (Ц2К12Ф-1, Ц2К20Ф-1}.
На станках для предварительной торцовки досок используют преимущественно плоские круглые пилы с разведенными зубьями. Когда требуется высокое качество раскроя, используют пилы с пластинами из твердых сплавов. Их используются для раскроя древесины, древесностружечных и столярных плит, оклеенных шпоном щитов, клееной древесины.
Для станков ЦПА40 и Ц2К12-1 пила должна иметь начальный диаметр 400 мм, толщину 2,5 мм и 72 зуба. Перед установкой пилы проверяют качество ее подготовки. Осматривают состояние прижимной шайбы и посадочной шейки вала. Опорные поверхности шайб должны быть чистыми и перпендикулярны оси вращения шпинделя. Торцовое биение поверхности шайбы допускается не более 0,02 мм на диаметре 100 мм. Пилу надевают на вал электродвигателя и крепят гайкой. Пильный суппорт регулируют по высоте, чтобы зубья пилы располагались на 5-6 мм ниже рабочей поверхности стола. Настроечное перемещение осуществляют маховичком, при этом колонки совместно с суппортом поднимаются или опускаются. После настройки по высоте колонку фиксируют стопорным устройством.
Рабочий ход пильного суппорта регулируется перестановкой упоров-ограничителей. Ограничители устанавливают в зависимости от ширины торцуемой доски, чтобы холостой пробег пилы был минимальным.
Затем следует размерная настройка станка. Различают торцовку по предварительной разметке и с установкой заготовки по шкале на направляющей линейке, или по упору. Опыт свидетельствует, что установка заготовки по меткам не обеспечивает получение точного размера и может применяться только для предварительной торцовки досок. Базирование заготовок по упору предпочтительнее.
Часто при торцовке деталей разной длины используют несколько упоров с ручным или автоматическим управлением. Упоры могут переставляться на заданную длину. Для точного перемещения упоров пользуются шкалой, прикрепленной к направляющей линейке или штанге. Расстановку упоров проверяют путем контроля длины деталей, полученных при пробной распиловке.
Скорость подачи в станках с гидроприводом регулируют изменением числа ходов суппорта в минуту. Число ходов устанавливают в зависимости от породы древесины и сечения заготовки. При торцовке древесины твердых пород используют меньшее число ходов суппорта, чем при раскрое древесины мягких пород.
Наладив станок и убедившись в свободном и правильном вращении пилы, приступают к пробной распиловке. Полученные детали должны удовлетворять следующим требованиям: отклонение от перпендикулярности торца к пласти и кромке детали допускается не более 0,2 мм на 100 мм длины; шероховатость поверхности резания должна быть не более 320-500 мкм. Перпендикулярность проверяют угольником.
Концеравнительные станки настраивают иначе. Подвижную колонку с конвейерной цепью и пильным суппортом перемещают на расстояние, приблизительно равное длине детали. Тогда в зависимости от толщины заготовки регулируют по высоте пильные суппорты и прижимные устройства, затем – положение пил на требуемую длину детали. После этого торцуют пробные заготовки и при необходимости поднастраивают станок.

Рис. Двухпильный концеравнитель Ц2К12Ф-1:
1 – станина, 2 – маховичок перемещения суппорта по горизонтали, 3 – пильные суппорты, 4 – маховичок вертикальной настройки, 5 – магазин-питатель, 6 – направляющая стрела
Торцовочный станок обычно обслуживают двое рабочих. Станочник низшего разряда принимает с разборочного конвейера доску и ориентирует ее на роликовом столе. Включает привод роликов и следит за движением доски к станку. Второй рабочий принимает доску и подает ее к пиле.
Если станок с механизированной подачей пилы, поток раскраиваемых досок идет справа и станочнику удобнее находиться справа от пилы. Он прижимает доску к направляющей линейке и упору и, нажимая на педаль, включает подачу пилы. Доска должна быть перпендикулярна пиле, а кромка доски касаться направляющей линейки, иначе не будет достигнута перпендикулярность торца. Второй рабочий должен следить за работой разборочного конвейера и своевременно включать или выключать его, ориентируясь на темп работы напарника.
При механизированной загрузке и выгрузке деталей станочник должен следить за правильной работой всех механизмов и своевременно регулировать их.
Станки для продольного раскроя. Для продольного раскроя пиломатериалов на заготовки применяют круглопильные станки с роликодисковой и конвейерной подачей. Станки с роликодисковой подачей служат для чернового раскроя. Станки с конвейерной подачей бывают однопильные прирезные и многопильные с пятью или десятью пилами.
Станок с роликодисковой подачей ЦА-2А предназначен для пиления кромок у необрезных досок или реек и продольного раскроя пиломатериалов на заготовки. Станок состоит из станины, шпинделя с пилой, стола и механизма подачи. Вальцы механизма подачи размещены под столом и незначительно выступают над его поверхностью. Сверху на станине смонтированы два качающихся рычага, на концах которых установлены передний зубчатый диск и задний рифленый ролик с расклинивающим диском увеличенного диаметра. Расклинивающий диск входит в пропил и разводит в стороны отпиливаемые части заготовки.
Для выпиловки деталей требуемой ширины служит переставная направляющая линейка. Станок позволяет устанавливать вторую пилу на расстоянии 10-50 мм от коренной. Если установлена вторая пила, на верхнем механизме подачи монтируют дополнительно передний зубчатый и задний расклинивающий диски.
Станки оснащают круглыми плоскими пилами с разведенными зубьями. Величина развода на одну сторону зубьев пил должна быть при распиловке древесины хвойных пород с абсолютной влажностью до 30% в любое время года – 0,50-0,60 мм, свыше 30% летом – 0,60-0,70 мм, зимой – 0,50-0,60 мм, твердых лиственных пород – 0,40-0,50 мм.
Диаметр посадочного отверстия пилы равен 50 мм. Пила должна иметь внешний начальный диаметр диска 400 мм, число зубьев 48 и толщину 2,5 мм. Целесообразно применять пилы с возможно меньшим диаметром, что повышает качество распиловки.
Наименьший диаметр принимают таким, чтобы зубья пилы выступали над заготовкой примерно на 10 мм.
Перед установкой пилу необходимо тщательно проверить. Необходимо также проверить состояние прижимных шайб и посадочной шейки шпинделя.
Пилу надевают так, чтобы зубья при вращении были направлены против подачи распиливаемого материала. Разность диаметров посадочной шейки шпинделя и отверстия пилы должна быть не более 0,1 мм. При значительных зазорах ось вращения пилы не будет совпадать с осью шпинделя, что вызовет радиальное биение зубьев и неудовлетворительное качество распиловки. После установки прижимной шайбы пилу закрепляют зажимной гайкой с резьбой, обратной вращению пилы.
При установке на шпинделе двух пил между коренной и второй пилой ставят набор шайб. Шайбы набирают так, чтобы общая толщина набора была больше ширины выпиливаемой детали на величину удвоенного развода зубьев на одну сторону. Пилы подбирают так, чтобы они имели одинаковый диаметр, толщину и развод зубьев.
Положение нижних подающих вальцов регулируют в зависимости от влажности и породы древесины. При распиловке древесины мягких хвойных пород величина выступа нижних вальцов над столом равна 2-3 мм, твердых лиственных пород – 1-2 мм. Точность положения вальцов проверяют контрольным бруском и щупом.
При установке направляющей линейки перемещают ее на расстояние, равное ширине отпиливаемой детали. При этом пользуются шкалой мерительной линейки на столе станка. Направляющую линейку фиксируют в заданном положении маховичком зажимного устройства.
При нормальной работе всех механизмов распиливают пробные заготовки. Скорость подачи зависит от породы, толщины и влажности древесины. При распиловке досок лиственных пород толщиной 80 мм пользуются наименьшей скоростью подачи, мягкой древесины толщиной 20-30 мм – наибольшей. Скорость устанавливают рукояткой переключателя многоскоростного электродвигателя.
Многопильные станки отличаются от однопильных наличием блока пил, установленных на одном валу. Расстояние между пилами определяет толщину выпиливаемых деталей, а регулируется установкой между пилами шайб требуемой толщины.
Для распиловки доски на всю толщину и возможности свободной смены пил применяют "ныряющий" конвейер. Конвейер скользит по двум направляющим, которые имеют небольшой изгиб в зоне пильного вала и обеспечивают соответствующее углубление звеньев конвейера под пилами.
В прирезных станках с конвейерной подачей применяют круглые плоские пилы с разведенными зубьями. Величина развода зубьев пил должна быть при распиловке древесины хвойных пород с абсолютной влажностью до 30% в любое время года 0,30-0,50 мм, свыше 30% летом – 0,60-0,70 мм, зимой – 0,40-0,60 мм, твердых лиственных пород – 0,30-0,50 мм.
На прирезных станках можно использовать строгальные пилы, а также пилы, зубья которых оснащены пластинами из твердого сплава.
Устанавливают и закрепляют пилы на шпинделе прирезного станка так же, как в станках с роликодисковой подачей.
При работе строгальными пилами или пилами, оснащенными пластинами из твердого сплава, шпиндель станка должен удовлетворять повышенному требованию к точности вращения. Торцовое биение опорной шайбы допускается не более 0,04 мм на радиусе 50 мм. Пилу устанавливают на шпиндель так, чтобы ее вращение было направлено против движения конвейера.
Внимание! Это не конец книги.
Если начало книги вам понравилось, то полную версию можно приобрести у нашего партнёра - распространителя легального контента. Поддержите автора!Правообладателям!
Данное произведение размещено по согласованию с ООО "ЛитРес" (20% исходного текста). Если размещение книги нарушает чьи-либо права, то сообщите об этом.Читателям!
Оплатили, но не знаете что делать дальше?