Текст книги "Инструменты бережливого производства II: Карманное руководство по практике применения Lean"
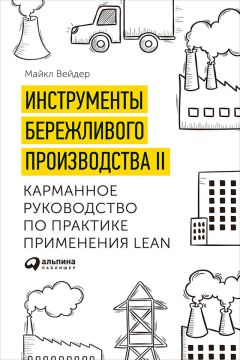
Автор книги: Майкл Вейдер
Жанр: Зарубежная деловая литература, Бизнес-Книги
Возрастные ограничения: +12
сообщить о неприемлемом содержимом
Текущая страница: 1 (всего у книги 5 страниц) [доступный отрывок для чтения: 1 страниц]
Майкл Вейдер
Инструменты бережливого производства II: Карманное руководство по практике применения Lean

Руководитель проекта М. Султанова
Арт-директор Л. Беншуша
Корректор И. Астапкина
Компьютерная верстка К. Свищёв
© Leadership Excellence International, LLC, 2014. All rights reserved.
© Перевод. ООО «Центр Оргпром», 2017
© Оформление. ООО «Интеллектуальная литература», 2017
Все права защищены. Произведение предназначено исключительно для частного использования. Никакая часть электронного экземпляра данной книги не может быть воспроизведена в какой бы то ни было форме и какими бы то ни было средствами, включая размещение в сети Интернет и в корпоративных сетях, для публичного или коллективного использования без письменного разрешения владельца авторских прав. За нарушение авторских прав законодательством предусмотрена выплата компенсации правообладателя в размере до 5 млн. рублей (ст. 49 ЗОАП), а также уголовная ответственность в виде лишения свободы на срок до 6 лет (ст. 146 УК РФ).
* * *
Переработанное издание книги «Инструменты бережливого производства» посвящается моим ученикам в России, которые постоянно задают сложные вопросы о практике применения Лин. Пожалуйста, никогда не переставайте задавать вопросы и критически осмысливать функционирование ваших процессов.
От автора
Настоящая книга в «карманном» формате была впервые написана в 2003 г. и к настоящему времени издана на шести языках в разных странах мира. Она приспособлена для того, чтобы носить ее с собой – в кармане, спецовке, сумке или держать ее в ящике вашего стола. Сейчас, имея более чем 20-летний опыт практического внедрения инструментов бережливого производства в сфере ремонта и техобслуживания, я жалею, что эта книга не была написана 40 лет назад. Это карманное руководство было разработано мною как часть учебного курса, который может применять любой корпоративный тренер, обладающий знанием и опытом использования инструментов бережливого производства, с целью углубления знаний обучающихся и применения этих знаний на производстве. По прошествии 12 лет я готовлю новое издание, в которое включаю многое из того, что просили мои читатели. Целью книги не ставится обучить вас всему, что необходимо для реализации инструментов бережливого производства. Она должна служить кратким справочным пособием, которое поможет вам не забывать то, что вы изучили по методикам бережливого производства на семинарах или курсах. Некоторые из инструментов и методов, предлагаемых в данном мини-руководстве, стали привычными для меня с 1965 г. Но, как это часто случается, некоторые простые инструменты остаются без внимания из-за желания внедрить самые последние и наилучшие системы. Не заблуждайтесь! Старые инструменты действуют и по сей день, и они могут помочь организациям упростить производственные процессы и снизить себестоимость продукции.
Мудрость – это не более чем здравый смысл, обогащаемый познанием нового и опытом.
Неизвестный источник
Благодарности
Это руководство не могло быть написано без помощи моих давних товарищей и коллег-единомышленников. Дон Экенрод и Адриан Эльф сделали важные замечания к материалам и помогли опробовать применение руководства в аудитории и на производстве.
Благодарю Ральфа Хагена за постоянную помощь в графическом оформлении и создании рисунков, способствующих пониманию темы, а также за чувство юмора при иллюстрировании данной серьезной темы.
Благодарю Джин Стейниш за редактирование оригинальной версии, Эрнеста Башкардина, Марию Самсонову и Лидию Фалько за перевод и редактирование русскоязычного издания.
Советы по применению
Эта книга карманного формата написана для того, чтобы снабдить читателя инструментами, необходимыми для практического внедрения системы бережливого производства во всех подразделениях организации. Существуют точки зрения, в соответствии с которыми «раздельное использование этих инструментов может создать путаницу при внедрении». Мы рекомендуем полностью прочитать это руководство, а затем спросить себя и свою команду: «Каковы в действительности наши проблемы, описали ли мы их количественно и качественно, и как мы можем их устранить?» Чтобы определить, какие инструменты применимы в вашем случае и в какой последовательности их следует использовать, прочтите книгу второй раз.
В руководстве выделены 12 ключевых вопросов, без ответа на которые успех при внедрении инструментов окажется невозможным. Эти вопросы обозначены символом «ключ»
Кроме того, представлены образцы семи контрольных листков, которые надо будет разработать в ходе внедрения системы бережливого производства.
В книге вы найдете 17 изображений очков.

Они обозначают этапы, на которых крайне важно осуществлять выход на процессы и наблюдение за ними. В такие моменты невозможно понять, что происходит, не находясь в гембе, т. е. в месте выполнения работы.
Работу лучше всего начать с оценки текущего состояния: определите, насколько в реальности плохо или хорошо организованы процессы на вашем производстве и какова их эффективность. Следующим этапом может стать добросовестное внедрение системы 5С в одном из конкретных процессов. При организации рабочего места обычно вскрываются как избыток незавершенного производства, так и ненужные дополнительные операции. А в процессе построения карты потока создания ценности могут быть определены оптимальные точки, где следует применить канбан и метод «точно вовремя» (JIT). Есть также вероятность обнаружения скрытых потерь, для устранения которых могут оказаться необходимыми использование встроенной защиты от ошибок, быстрой переналадки или зонирования с применением визуального контроля.
Эту книгу можно применять как в качестве учебного пособия в аудитории, так и для отработки навыков и практического внедрения системы бережливого производства непосредственно в цехе, у станка. Положите ее в карман рубашки, в карман спецовки – туда, где она всегда будет под рукой, чтобы помочь вам определить и устранить скрытые потери. Запомните, что инструменты, представленные в книге, должны дополнять друг друга, а не ограничивать и не противоречить друг другу.
Скрытые потери
В любой системе, во всех процессах – от производства и сборки до гостиничного бизнеса, здравоохранения, транспорта и социальных служб – существуют скрытые потери. Определение и устранение этих потерь ежегодно сохраняет миллионы долларов тем организациям, которые регулярно оценивают свою деятельность по стандартам бережливого производства. Скрытые потери подразделяются на семь категорий: потери на 1) перепроизводстве; 2) дефектах; 3) перемещениях; 4) транспортировке; 5) излишних запасах; 6) излишней обработке; 7) ожидании. Эти потери увеличивают издержки производства, не добавляя потребительской ценности, действительно необходимой заказчику. Они также увеличивают срок окупаемости инвестиций и ведут к снижению мотивации рабочих. Для тех, кто стремится к рационализации процессов в промышленности, данные семь скрытых потерь – злейшие враги. Некоторые преподаватели и тренеры выделяют сейчас и восьмой вид скрытых потерь – интеллектуальный капитал, т. е. неиспользование интеллекта работников. Я обычно выделяю семь видов потерь, но не забываю при этом максимально использовать потенциал работников.
Необходимо определить, а затем устранить эти потери. Итак, в каких процессах скрываются потери?

Потери от перепроизводства
Потери от перепроизводства появляются, когда мы производим, собираем или выпускаем больше, чем это необходимо. Мы делаем что-то «просто на всякий случай», вместо того чтобы делать «точно вовремя». Недостатки планирования, большие заделы, большое время переналадки, недостаточно тесный контакт с заказчиками (что мешает пониманию их постоянно изменяющихся требований) приводят к увеличению продолжительности производственных циклов. Мы беспокоимся о том, что наши клиенты могут нуждаться в большем, и в результате страдаем от затрат на производство товаров и услуг, которые не удается продать.

Найдите процессы, в ходе которых производится больше, чем «вытягивает» заказчик, и потому излишки продукции требуют дополнительных мер по организации их хранения между операциями.
Сократите потери путем сокращения времени наладки и переналадки, а также балансировки производственных линий (см. главы «Быстрая переналадка» и «Отчеты по решению проблем в формате А3»).
Потери от дефектов и переделки
Потери из-за дефектов или необходимости переделки возникают, когда нет надежной превентивной системы, включающей методы пока-ёкэ (Poka-Yoke) и встроенной защиты от ошибок. Каждый раз, допустив ошибку при работе с изделием и передав его на следующую операцию процесса или, что еще хуже, покупателю, мы миримся с переделкой как неотъемлемой частью процесса. Мы теряем деньги всякий раз, когда дважды производим, собираем или ремонтируем что-либо, в то время как клиент платит нам за товар или услугу только один раз.

Найдите дефектные или незавершенные продукты или услуги, а также законченные изделия, которые переделываются или которые приходится утилизировать.
Сократите потери путем усовершенствования системы визуального контроля и разработки более полных стандартных операционных процедур. Внедрите встроенную систему защиты от ошибок (пока-ёкэ) там, где скрывается источник ошибок (см. главы «Всеобщее производственное обслуживание (ТРМ)», «Визуальные средства» и «Быстрая переналадка»).
Потери от перемещений
Потери от перемещений – это ненужные передвижения персонала, продукции, материалов и оборудования, которые не добавляют ценности процессу. Часто рабочие совершают лишние перемещения со своего участка до цехового склада и обратно, а также ходят вокруг ненужного им оборудования. Такие перемещения можно устранить и за счет этого ускорить процесс. Это одна из наиболее неприятных потерь и для рядового персонала, и для руководства, так как потраченное время и простои лишают эффективности большинство процессов, утяжеляя труд рабочих. Несмотря на то что большинство производственных процессов изначально разрабатывалось с учетом минимизации лишних движений, в основном это один из крупнейших источников потерь, возникающих незаметно и приводящих к сбоям.

Найдите, когда персонал совершает ненужные передвижения или перемещения, и составьте комплексную схему (диаграмму «спагетти») фактических потоков процесса.
Сократите потери путем построения и изучения карты потока создания ценности и/или карты физических потоков для каждого процесса с последующим сокращением перемещений операторов, оборудования, материалов (см. главу «Выходы в гембу»).

Потери от транспортировки
Транспортные потери возникают, когда персонал, оборудование, продукция или информация перемещаются чаще или на большие расстояния, чем это действительно необходимо. В ходе многоэтапных процессов материалы и персонал перемещаются от процесса к процессу, которые разделены пространством и/или временем. Вместо того чтобы расположить процессы последовательно или рядом, их часто располагают далеко друг от друга, что требует применения автопогрузчиков, конвейеров или других транспортных устройств для перемещения материалов на следующую операцию. Все эти перемещения не добавляют потребительской ценности производимой продукции.

Найдите перемещения персонала, материалов или информации, которые не способствуют процессу создания ценности.
Сократите потери путем минимизации физического расстояния транспортировки материалов и перемещения транспортных средств, выделив зоны и применив перепланировку (см. главу «Канбан»).
С помощью диаграммы спагетти проследите пути транспортировки материалов, чтобы выявить возможности для улучшения.

Потери от излишних запасов
Потери, скрывающиеся в излишних запасах, таят в себе множество неприятных проблем качества, таких как переделка и дефекты, проблемы в планировании рабочей силы и/или производства, завышенное время выполнения заказа, проблемы с поставщиками. Содержать чрезмерные запасы, замораживающие капитал и требующие выплаты банковских процентов, слишком дорого. Излишние запасы снижают отдачу от вложений в рабочую силу и сырье.

Найдите излишние производственные мощности, избыточные запасы сырья, незавершенного производства или готовой продукции с оборачиваемостью менее 10 раз в год.
Сократите потери, применив методику «точно вовремя» и канбан (см. главы «Что такое „точно вовремя“» и «Планировка в виде ячеек»).
Потери от излишней обработки
Потери от излишней обработки возникают при производстве продукции или услуг с более высокими потребительскими качествами, чем это востребовано покупателем и за которые он согласен платить. Добавление функций, не имеющих ценности в глазах потребителя, не улучшает продукт или процесс. Недостаток информации о том, как потребители используют продукцию или услуги, часто ведет к добавлению излишних функциональных возможностей, в которых, по мнению производителя, клиенты нуждаются или желают их (однако точно это неизвестно).

Найдите в возвращенных по гарантии продуктах места, где незаметно следов износа. Опросите потребителей и исследуйте работу продукта в реальных условиях.
Сократите потери, определив, какие функции реально нужны потребителю и за что он готов платить. Для этого нужно хорошо понимать, как именно клиенты применяют ваш продукт или услугу.
Потери от времени ожидания
Потери времени на ожидание возникают, когда люди, операции или частично готовая продукция вынуждены дожидаться дальнейших действий, информации или материалов. Плохое планирование, необязательность поставщиков, проблемы коммуникации и несовершенство управления запасами приводят к простоям, которые стоят нам времени и денег.

Найдите людей или оборудование, которые ожидают завершения предыдущей или начала следующей операции, поступления материалов или информации.
Сократите потери путем выравнивания загрузки производственных линий, используя диаграмму Парето времени цикла / времени такта с целью синхронизации процессов (см. главу «Обучение в промышленности»).
Потери интеллектуального капитала
Некоторые консультанты выделяют восьмой тип скрытых потерь, а именно – потери интеллектуального капитала. Это происходит, когда руководители не используют интеллект работников в целях улучшения процессов. Работники в промышленности и в сфере услуг каждый день заняты в реальных процессах, и они прекрасно понимают, какие улучшения могут быть реализованы. У них есть предложения о том, как можно ускорить процессы и снизить издержки в операциях, но никто их не спрашивает об этом. Инженеры и руководители считают, что они лучше знакомы с процессами, чем рядовые работники, и думают, что сотрудники на низших уровнях не знают, как можно улучшить процессы.

Старайтесь найти тех, кто пытается хорошо выполнять текущие задания и качественно обслуживать клиентов. Те сотрудники, которые высказывают замечания по методам выполнения операций, обычно могут предложить что-то, чтобы их улучшить, их нужно только выслушать. Если у вас есть программа работы с предложениями, найдите тех, кто уже подавал предложения, и попросите их подать новые. Если у вас нет такой программы предложений, вам нужно ее подготовить и тщательно отслеживать все предложения, поступающие от работников самого низкого уровня.
Сократите потери, чаще производя выходы в гембу и беседуя с сотрудниками, которые непосредственно заняты в производстве продукта или оказании услуги. Попросите их участвовать в командах улучшений и дайте им возможность высказывать свои идеи, которые руководители и инженеры должны выслушивать. Их точка зрения о том, что делается неправильно и как можно исправить положение, обычно отличается от точки зрения их руководителей и инженеров.
Аттестация на соответствие принципам бережливого производства
Вам потребуется всесторонняя и объективная аттестация действующего производства на цеховом уровне. Нужно найти все семь видов скрытых потерь и понять, как их устранить. Методика оценки должна быть вполне доступна для цехового персонала и достаточно детальна, для того чтобы руководство могло определить, куда направить усилия по совершенствованию. Правильная аттестация уменьшит затраты, связанные с ошибками, допущенными на начальном этапе реализации проекта, и поможет определить, как достичь наибольшей рентабельности инвестиций (ROI).
Оценка организации должна охватывать также те ее непроизводственные процессы, которые влияют на общие показатели работы компании, включая продажи, обработку заказов, снабжение и послепродажное обслуживание. Потери существуют в каждом подразделении, а не только в производственных цехах.
Оценка не должна проводиться одним человеком, для этого лучше всего подходит межфункциональная команда из двух – трех человек. Следует включать в команду и сотрудников, не работающих там, где производится оценка. Консультанты, специалисты из отделов качества партнерских компаний или других подразделений фирмы в силу своей беспристрастности будут хорошими источниками свежих идей. Когда процесс оценивается непосредственно участвующими в нем людьми, оказывается, что зачастую они «за деревьями не видят леса». Они слишком близки к объекту оценки и поэтому привыкли к существующему положению вещей. А если кто-либо будет постоянно спрашивать: «Почему?», это будет стимулировать дискуссии, которые помогут вскрыть невидимые потери и их первопричины.
Оценка должна производиться лишь в целях установления потенциала скрытых возможностей для усовершенствования и степени их воздействия на производство. Оценка не должна определять, как решать найденные проблемы: она находит возможности, а не решения.
Когда люди, работающие в процессе, оценивают сами себя, они часто «за деревьями не видят леса».
Примеры аттестационных вопросов
1. Стандартизованы ли рабочие инструкции (стандартные операционные процедуры), выполняются ли они?
2. Насколько наглядны и просты для понимания средства визуального контроля, призванные помогать рабочим?
3. Существует ли система частого пополнения межоперационных запасов с целью их сокращения и снижения объема транспортировки?
4. Применяются ли стандартные контейнеры и маркировка как часть системы планирования обеспечения материалами и отслеживания поставок?
5. Спланирована ли последовательность движения материальных потоков таким образом, чтобы обеспечить рациональную организацию потока от начала до конца?
6. Регистрируется ли возврат инструмента по окончании каждой смены, весь ли он правильно маркирован и имеет ли свои места для постоянного хранения?
7. Составляются ли диаграммы статистического контроля процессов работы оборудования для ежедневного контроля его эффективности?
8. Хорошо ли размечены стеллажи, обозначены ли места нахождения всех позиций, их количество, уровни, требующие восполнения запаса?
9. Существует ли НЗП между операциями? Выявлены ли все узкие места и ограничения в потоке производства и работает ли специальная группа по их ликвидации?
10. Производятся ли регулярный замер и контроль расстояний, на которые перемещаются работники и материалы, с целью выявления возможностей улучшений?
11. Имеются ли излишние погрузочно-разгрузочные операции, не добавляющие ценности продуктам? Нет ли случаев повторного прохождения материалами одного и того же места?
12. Вывешен ли на всеобщее обозрение график производства и отслеживается ли он на всех участках? Все ли работники на производстве или в сфере услуг понимают требования производства без обращения к мастеру или непосредственному начальнику?
При проведении аттестации на соответствие принципам бережливого производства необходимо как минимум задавать вопросы по семи типам скрытых потерь и проблемам руководства. Абсолютное количество баллов, которое вы присвоите тем или иным операциям, не играет большой роли при сравнении с другими компаниями или подразделениями вашей компании. Баллы важны как индикатор исходного уровня, указывающий на текущее состояние и на те участки, где необходимо провести улучшения. После проведения первой аттестации нужно и далее использовать ту же самую команду сотрудников для проведения повторных аттестаций через шесть месяцев или через год. Выявляйте те участки, где удалось произвести улучшения, и выставляйте им новые баллы. Определяйте также участки, где улучшения не произошло, и старайтесь найти ответ, почему так получилось.
Книга «Как оценить бережливость вашей компании: Практическое руководство», написанная Майклом Вейдером, – хорошее руководство по проведению Лин-аттестации[1]1
Термин «Лин» (от англ. Lean Production) используется здесь и далее в тексте как эквивалент термина «бережливое производство». – Прим. пер.
[Закрыть]. Там подробно описываются все шаги процесса аттестации, начиная с общего понимания Лин до того, что необходимо искать, какие вопросы задавать и как определить, какие инструменты Лин наилучшим образом подойдут для решения ваших конкретных проблем, выявленных в ходе аттестации. В руководстве по аттестации представлено 117 вопросов в 38 элементах, покрывающих все сферы работы предприятия. Оценка проводится по девяти категориям, по которым определяется, где существует больше всего потерь.
Категории оценки
1. Потери от излишних перемещений
2. Потери от излишней обработки
3. Потери от излишних запасов
4. Потери от транспортировки
5. Потери от перепроизводства
6. Потери от времени ожидания
7. Потери от дефектов, брака и переделок
8. Стратегия лидеров
9. Производственная культура


Внимание! Это не конец книги.
Если начало книги вам понравилось, то полную версию можно приобрести у нашего партнёра - распространителя легального контента. Поддержите автора!Правообладателям!
Данное произведение размещено по согласованию с ООО "ЛитРес" (20% исходного текста). Если размещение книги нарушает чьи-либо права, то сообщите об этом.Читателям!
Оплатили, но не знаете что делать дальше?