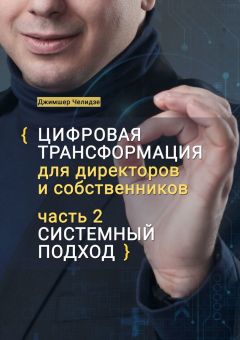
Автор книги: Наталья Люнгрин
Жанр: О бизнесе популярно, Бизнес-Книги
Возрастные ограничения: +12
сообщить о неприемлемом содержимом
Текущая страница: 4 (всего у книги 16 страниц) [доступный отрывок для чтения: 5 страниц]
Муда, мура, мури и виды потерь
Муда, мура, мури – странные слова, неправда ли? При этом суть их проста.
Давайте разберемся с этими основными понятиями.
Муда – это потери двух видов:
1. Действия, не создающие ценность, но без которых невозможно обойтись. Например, транспортировка, оформление документов – их невозможно удалить из процесса, но необходимо стремиться сокращать, скажем, автоматизацией подготовки обязательной отчетности. В моем опыте был случай, когда с помощью обычного Экселя получилось снизить трудозатраты на обязательный и никому не нужный отчет с 8 часов в месяц до 30 минут.
2. Действия, не создающие ценности вообще, и их нужно исключать из процесса полностью. Например, ожидание, запасы, брак и т. д.
Мура – неравномерность. При неравномерном спросе образуются очереди, увеличивается время исполнения. Требуются дополнительные материалы и запасы для выполнения пикового спроса. Работа в авральном режиме утомляет людей и снижает их эффективность и качество работы.
Все это тоже порождает потери – брак, ожидание, лишние запасы, необходимость переделки.
Мури – перегрузка людей или оборудования.
Мы заставляем машины или людей работать на пределе возможностей. Перегрузка людей угрожает их безопасности и вызывает проблемы с качеством. Перегрузка оборудования ведет к авариям и дефектам, что в итоге тоже приводит к потерям.
Эти три «М» представляют собой единую систему.
Часто корень проблем – «Мура», так как неравномерность приводит к перегрузке «Мури», которая в свою очередь порождает множество других потерь («Муда»).

Иллюстрация муда, мура, мури
Напомню, что цель цифровизации, автоматизации и трансформации – снижение потерь, в основном, в работе с информацией. И, прежде чем инициировать какой-то проект, надо понять, какие потери мы хотим устранить.
1. Перепроизводство
Самая распространенная проблема, которая является причиной большинства других. Помните пример в теории ограничения систем, когда отдел продаж продавал больше, чем может предоставить производство? Или когда мы делаем пять копий документов, хотя нужна всего одна? Все это перепроизводство. Это приводит и к перегрузу подразделений, и к высоким запасам незавершенного производства или готовой продукции на складах, что в том числе увеличивает количество брака.
Причины – производство большими партиями и неизученность спроса, долгая переналадка / перестройка.
Здесь могут помочь и системы планирования, и глубокая аналитика рынка через сбор больших данных.
2. Ожидание
Это все время, в течение которого люди или оборудование ожидают ресурсов, технологической операции, данных, ненужных согласований. В том числе устранять эти потери призваны проекты по внедрению электронного документооборота. Вот только в таких проектах часто забывают делать пересборку процессов, и тогда электронный документооборот начинает усложнять жизнь сотрудникам.
Причины возникновения – нарушение в логистической системе. Например, уехал начальник, а документы можно подписывать только вручную. Или поломка оборудования, отсутствие указаний руководства, отсутствие планирования.
3. Запасы
Многие закупщики любят приобретать большие партии, чтобы получить скидку, даже если им пока не нужно столько материала. Излишние запасы замораживают в себе деньги, плюс все это где-то надо хранить, требуются большие склады. Кроме того, на складе может возникать брак сырья. В этом виде потерь скрываются проблемы планирования производства и неравномерность процессов.
Причины возникновения – неравномерность производства и плохо отлаженные связи с поставщиками материалов, не учитывается спрос на продукцию или сырье, материалы.
Пример: хранение большого объема материалов, необходимого для производства в течение полугода, без учета стоимости обслуживания склада, или выпуск новогодних товаров без учета сезонного спроса.
4. Излишняя транспортировка
Перемещения материалов или товаров между подразделениями, которые не добавляют ценности конечному продукту или услуге. Это приводит и к простою / ожиданию оборудования, и к лишнему браку.
Причины возникновения – нерациональное использование производственных / офисных площадей, лишние промежуточные зоны хранения, неудобное размещение оборудования, неоптимизированные бизнес-процессы.
Пример: расположение склада запчастей и производства на большем расстоянии друг от друга.
5. Излишнее перемещение людей
Ненужные перемещения персонала или хаотичность организации рабочих мест. Эта потеря зачастую сочетается с предыдущей, особенно в офисе. Вот вам пример. В организации есть система электронного документооборота, но людям все равно необходимо каждую заявку распечатывать и относить в архив вручную. В итоге лишнее перемещение и документов, и людей. Если же мы говорим про производство, то пока человек ходит по цеху, он может повредить другие изделия.
Причины возникновения – нерациональная организация рабочего пространства, отсутствие стандартов работы, отсутствие визуализации, нарушение трудовой дисциплины.
Пример: поиск необходимого для работы инструмента по всему участку, незнание сотрудниками зон ответственности и хождение, выяснение, кто должен выполнять ту или иную операцию, отсутствие визуальных стандартов, которые облегчают поиск необходимых инструментов и материалов.
Поможет тут, например, система по работе с бизнес-процессами, датчики больших данных и геолокации по перемещению людей в рамках бизнес-процессов.
6. Брак
Брак опасен тем, что это не только списание сырья и рабочего времени машин и людей в утиль, но еще и репутация у клиентов.
Причины возникновения – отсутствие контроля на разных этапах производственного процесса, отсутствие встроенной системы «Защита от дурака» (Пока-йоке), несоответствие квалификации людей или проблемы с оборудованием.
Возвращаясь к цифровизации, самое распространенное решение здесь – системы с машинным зрением, которые анализируют процесс и изделие.
7. Излишняя обработка
Здесь имеются в виду все те действия, когда мы стараемся сделать лучше, чем нужно потребителю.
Причины возникновения – неизученный спрос или недостаток входящей информации.
Если мы еще раз вернемся к статистике проектного и продуктового управления, то лишь 16% продуктов оказываются полностью успешными. Почему?
Один из факторов – излишние количество возможностей в продуктах. Только 20% заложенного функционала востребовано регулярно, 30% – изредка, а 50% – практически никогда. Чтобы было еще нагляднее, давайте вспомним современные приложения, например, банковские. Чем вы действительно пользуетесь? А стало ли удобнее использовать ваше банковское приложение в сравнении с тем, что было лет 5 назад? Лично мне нет. Микросервисные решения становятся все более функциональными, но менее удобными и востребованными. А ведь их разработка стоит денег.
Если упростить пример, то вспомните пульт для телевизора с набором дополнительных функций, которые не нужны потребителю.
8. Неиспользованный человеческий потенциал
Финальный, по мнению Тойоты, вид потерь – неиспользованный или нереализованный человеческий потенциал. Как следует из названия, это исключение личных качеств, знаний, умений и навыков сотрудника из выполняемой им работы. Потери нереализованного человеческого потенциала чаще всего возникают, когда от сотрудника ждут исключительного выполнения рутинных операций, руководитель не прислушивается к подчиненным, а любая деятельность жестко регламентируется внутренними стандартами, правилами или должностными обязанностями.
И, как показывает практика, это одно из самых распространенных явлений. В самом начале книги я говорил, что одно из ограничений – это мышление руководителя, а топ-менеджеры – как правило, это яркие и авторитарные предприниматели, которые любят микроменеджмент и не доверяют обычному персоналу, не готовы слышать мнения, отличные от своего. Хотя иногда это умело маскируют. В итоге мы и получаем этот вид потерь. А если руководитель находится еще и в крупной компании с бюрократической структурой и культурой, то вообще беда.
Причины возникновения – неэффективная система мотивации, высокая конкуренция среди персонала, излишний контроль со стороны руководства, отсутствие мотивации или даже наказание за проявление инициативы.
Также часто встречается выполнение сотрудником непрофильных заданий, работа за себя, за коллегу и еще за Ивана.
Все эти потери актуальны для любой рабочей системы, как производства, так и в офисе.
Ключевые инструменты
Kaizen
Кайдзен – японская философия, которая фокусируется на непрерывном совершенствовании процессов небольшими шагами. Её суть в том, что исполнители на местах лучше всех знают, что можно улучшить в работе. Этот инструмент был и в СССР, но назывался системой рационализаторских предложений.
Чтобы это работало, необходимо:
– постоянно собирать обратную связь и внедрять изменения, а если они неприменимы, то надо объяснять инициатору, что именно не так;
– нужно обучать людей, чтобы они направляли не просто хотелки, а рациональные предложения, плюс это позволит не тратить время на долгие разговоры.
Это не только улучшает процессы, но и мотивирует сотрудников.
В моей практике самые лучшие инициативы (наименее затратные и наиболее эффективные) приходили именно от обычных сотрудников.
Примеры:
1. Во время производства может возникать брак или не весь заказ получается изготовить (не успели, не пришли компоненты). В итоге упаковщики долго объясняют детали начальнику производства, а он – отделу планирования и продаж.
Решение от упаковщиков – ставить номер у каждой детали в самом чертеже. Реализация в 1С – пару дней.
В итоге:
– планировщики просто отдают отчет и чертежи
– планировщик сразу знает, что надо перезаказать, и говорит, когда придет недостающая деталь;
– отдел продаж ясно понимает, когда будет готов заказ.
2. Обратная связь от операторов.
Изменив расположение расходников, удалось снизить время на переналадку между заказами на 50%: просто стало не нужно идти в другой конец цеха, по пути еще и задевая другие заказы.
Как вы думаете, сочетание такого подхода и цифровых инструментов даст больший эффект, чем покупка дорогих систем управления, но с хаосом в обычной работе?
Для цифровизации это вообще «волшебная пилюля». Как только люди примут, что они могут изменять рабочий процесс, и получат необходимые компетенции, они сами начнут упрощать свою работу, в том числе автоматизировать и пересобирать процессы. Главное – не «поощрять» их еще большей рутинной.
Хорошо, не все сотрудники, но 10—15% активных новаторов способны все перевернуть. Именно их и надо выделять и обучать системному подходу.
Если мы посмотрим на опыт японских компаний, то в каждом производственном цехе стоит планшет, где каждый сотрудник может оставить предложение.
Система Канбан
«Канбан» в переводе с японского означает «знак», «сигнал» или «карточка». Изначально это инструмент с карточками для запроса сырья в производственном цеху.
Сейчас это ИТ-решения для организации работы. Их суть – создание «вытягивающей системы», когда работа берется только после завершения предыдущей, а также визуализация рабочего процесса, недопущение перегрузки людей или подразделений, выявление проблем на раннем этапе и совершенствование процесса. Мы подробнее рассмотрим этот инструмент в главе про проектное управление, так как он один из основных в гибких подходах.
Метод «5 почему»
«5 почему» – метод поиска причин возникших потерь и проблем, который позволяет построить причинно-следственные связи. Я впервые столкнулся с этим инструментом в одном проекте, где работали с ИКЕА: при поставке бракованной продукции, тебя заставляют провести расследование и оформить его в формате «5 почему».
Суть инструмента – необходимо 5 раз ответить на вопрос «Почему это произошло?», чтобы дойти до системных причин. И чем более оцифрованы бизнес-процессы и все этапы, тем проще, быстрее и эффективнее проводить такой анализ.
Пример такого алгоритма.
Проблема: товар пришел с царапинами, при этом на выходном контроле все было отлично.
Шаг 1. Почему это происходит? Потому что изделия повреждаются в пути, царапаясь друг о друга.
Шаг 2. Почему оно повреждается в пути? Потому что транспортировка идет на машине и возможны боковые перегрузки.
Шаг 3. Почему во время транспортировки на машине упакованный груз все равно повреждается? Потому что технология упаковки не обеспечивает должную защиту.
Шаг 4. Почему технология упаковки не обеспечивает защиту во время транспортировки? Потому что технология упаковывания имеет недостатки.
Шаг 5. Почему технология упаковки имеет недостатки? И вот тут имеется разветвление. Первый вариант – раньше не было выходного контроля, и все списывалось на подразделение, никто не проводил расследование причин. Второй – раньше компания не имела дела с такой доставкой, и эта технология упаковки не была отработана.
Проблема данной методики в том, что необходимо поддерживать критичность и легко уйти в неверные выводы. Причем выше приведен реальный пример. Как думаете, какой из итоговых вариантов верный?
7 шагов практического решения проблем
В Тойоте метод «5 почему» является одним из элементов более высокоуровневого алгоритма, который они называют «практическим решением проблем». Перед тем как приступать к анализу по методу «5 почему», необходимо выяснить, в чем состоит проблема, или, проще говоря, «оценить ситуацию».
Вообще, внедряя бережливое производство и любые другие инструменты, менеджеры зачастую фокусируются на формальных инструментах, забывая про людей. Так вот, по мнению Тойоты, решение проблем – это на 20% инструменты и на 80% размышления, осмысление.
5S – система наведения и поддержания порядка
5S – инструмент в экосистеме бережливого производства, метод, который направлен на:
– повышение эффективности операционки;
– устранение накопившегося хлама и мусора, в том числе в ИТ-решениях, и исключение его появления в дальнейшем;
– сокращение потерь на поиск ответов на вопросы «где находится инструмент?», «как получить к нему доступ?»;
– улучшение корпоративной культуры через изменение условий и формирование новых привычек.
Японцы считают, что всегда первым делом нужно «рассеять туман», сделать так, чтобы все было понятно, подписано, разложено по местам. Тогда все потери становятся видимыми, а отклонения очевидными, и могут быть быстро исправлены до перехода в состояние проблемы.
Если на рабочем месте беспорядок, то все «покрыто туманом», где рождаются потери.
При этом суть системы 5S – не только разовое наведение порядка на рабочем месте, но и поддержание такого порядка всегда.
5S алгоритм:
1. Сортировка: все предметы на рабочем месте разделяются (сортируются) на нужные и ненужные. Ненужные предметы удаляются с рабочего места. В ИТ так же: все лишнее убирается с рабочего стола системы.
2. Соблюдение порядка: предметы раскладываются по местам так, чтобы ими было легко и удобно пользоваться. Здесь мы говорим про UX-дизайн.
3. Содержание в чистоте: все предметы и рабочее место чистятся, моются, красятся, удаляется грязь, пыль и мусор, ненужные элементы графики.
4. Стандартизация: составляется визуальный стандарт расположения предметов: контуры предметов, подписи на местах их расположения, регламент уборки, макеты рабочих столов.
5. Совершенствование: разрабатывается система постоянного совершенствования предыдущих шагов и рабочего места. Но без стандартов и «точек отсчетов» все свалится в хаос.
Это не полный список инструментов бережливого производства. Есть еще:
– TQC – всеобщий контроль качества
– TQM – всеобщее управление качеством
– TPM – всеобщий уход за оборудованием
– Just-in-time – точно вовремя
– Отчет А3
Подробнее о них вы сможете прочитать по QR-коду или ссылке.

Бережливое производство. Часть 1
Недостатки бережливого производства
Проблемы поставок сырья и ресурсов
Ограничения запасов делает вас уязвимыми от поставщиков, как внешних, так и внутренних. Например, если сотрудник заболел, где-то задержки в логистике могут стать фатальными. А как показывает опыт работы, продавцы очень редко хотят или вообще способны организовать надежные поставки небольшими партиями по жесткому графику. Если на это наложить текущий мировой хаос с логистикой, то…
Репутационные потери
Это следствие предыдущего пункта. Если из-за поставщиков будут нарушаться технологические процессы, то клиенты не смогут получать свой товар вовремя. А это удар по репутации.
Высокие затраты
Если внедрять бережливое полностью, то может возникнуть необходимость и в реконструкции объектов, замене оборудования, что очень дорого. Кроме того, внедрение всех ритуалов и инструментов потребует долгого обучения сотрудников. Малый и средний бизнес в итоге может очень долго окупать все эти затраты.
Сопротивление сотрудников
Внедрение бережливого производства, как и цифровизация в целом, в основном вызывает стресс и жесткое сопротивление среди персонала. Как это преодолевать, мы разбирали в первой книге.
6 сигм
6 сигм – это американский подход к управлению производством, где ключевая задача – снизить количество брака до уровня 3,4 единицы на 1 млн единиц готовой продукции.
И, что свойственно американской культуре управления, этот инструмент базируется на обработке статистических данных, работы с измеримыми показателями. Здесь говорят так: «правильный процесс дает правильные результаты».
Главный эффект от применения 6 сигм – возможность выделить границы управляемого процесса. А в случае выявления проблемы понять, где системная ошибка, а где частный случай, что позволяет не лечить форс-мажор излишними мерами в отношении всей системы. Если один сотрудник пришел в обед, это не значит, что надо всем вводить штрафы за опоздание на 5 минут. А также этот инструмент позволяет выявить благоприятные события, проанализировать их и внедрить для улучшения процесса в целом.
Правило 3 сигм
Так что за «сигмы» такие, о чем речь?
Сигма (σ) – буква греческого алфавита, которой в математике обозначают стандартное отклонение, то есть, когда показатели не соответствуют этому отклонению, они являются аномалией.
Правило 3 сигм гласит (в упрощенной формулировке): практически все значения и результаты, которые можно считать нормальными для этого процесса, лежат в интервале +– 3 сигм от среднего значения. Если погрузиться в расчеты, то получается, что все нормальные для процесса результаты будут в этих 3-х сигмах с вероятностью 99,73%.

Распределение отклонения по сигмам
Алгоритм расчета 6 сигм:
– Складываем все измеренные значения и рассчитываем среднее арифметическое значение.
– Считаем разность между максимальным и минимальным значением, например, за месяц.
– Считаем такую же разность за еще, например, 5 месяцев.
– Считаем среднее арифметическое этой разницы за 6 месяцев.
– В контрольных картах Шухарта (ГОСТ Р 50779.42—99) находим показатель d2, и берем значение для выборки, в нашем примере это 6 месяцев, значит d2 = 2,534.
– Берем нашу среднюю разницу между максимум и минимум и делим на d2.
– Получаем сигму.
– Теперь от среднего значения из пункта 1 откладываем 3 сигмы вверх и вниз. Получаем 6 сигм, которые показывают границы нашего управляемого процесса. Что не внутри – это отклонения. Выясняем причины и работаем с ними. А если нас не устраивают границы процесса, работаем системно.
Конечно, в жизни не всегда нужно использовать все инструменты в полном соответствии.
Вот практический пример из моей практики.
Что есть на входе: таблица с данными о бурении скважин. Записей в ней около двухсот.

И на основе этих данных необходимо понять, что вообще происходит? Какие есть проблемы? К сожалению, интервью с людьми провести нельзя.
Что ж, давайте пройдемся по простому алгоритму:
– Делаем небольшую табличку, в которой считаем продолжительность ключевых периодов

– Рассчитываем абсолютные показатели

– Дальше строим графики Парето (с некоторой очисткой от аномалий), смотрим, какое в среднем ожидание между бурением и освоением (простой).
– Расчет и построение графика 6 сигм (но это уже необязательно, все необходимые данные и так есть). Определение границ управляемого процесса и его текущее состояние. Выясняем, необходимо делать корректирование процесса или его полную перестройку?
– Определяем причины отклонений, выпадающих за границы процесса, в том числе используя методику «5 почему». Определяем необходимость внесения изменений в процессы (например, закупка ЗИП).
– Также изучаем причины лучших примеров, определяем возможность корректировки процессов и установления новых целевых значений, стандартов. Также изучаем ситуацию с самыми большими простоями, смотрим, кто реализовывал, что пошло не так, из-за чего. Вполне возможно, что тут есть одни и те же люди, и надо работать локально с ними, например, проводить их обучение.
Но какие выводы можно было сделать, даже без глубоких расчетов?
– Согласно графику Парето, мы увидели, что в более чем 75% случаев ожидание находилось в пределах до 73 дней, а в 85% случаев – до 154 дней. Конечно, лучше оптимально провести расчет сигм, но и в текущем варианте видны границы управляемости процесса. Соответственно, для первого приближения можно использовать средние арифметические.
– Мы не имеем информации о глубинах скважин и не можем оценить эффективность рабочего процесса. Однако мы можем сопоставить время простоя между окончанием бурения и началом освоения. Так, средний срок ожидания от момента окончания бурения до начала освоения – 76 дней. При этом среднее ожидание начала освоения превышает средний срок освоения более чем в 3,5 раза и сопоставим по времени со всем процессом бурения. Суммарно потери ожидания составляют 42% времени от всего цикла с момента начала бурения до окончания освоения. Это генерирует как упущенную прибыль, так и прямые потери.
– Причина – системные проблемы процесса планирования, необходим детальный аудит.
– Возможные ограничения системы:
– система контроля и оповещения о прохождении технологических этапов;
– отсутствие системы прогнозирования завершения этапов бурения;
– отсутствие регламентов и целевых значений продолжительности каждого этапа, сроков уведомления, поставки и готовности оборудования для перехода к освоению.
Вот как из одной таблицы можно с помощью расчетов и знаний прийти к определенным выводам. Как показало неформальное общение, это были верные заключения. Но в дальнейший проект я уже не пошел: ТОПы проводили согласование почти полгода, а по моим убеждениям, если не умеют быстро работать наверху, то что-то менять снизу бессмысленно. Все идет с головы. В этом я убеждаюсь в каждом проекте, поэтому и начинаю всегда работать с первого лица. Сначала готовим его, а потом работаем с командой, только такой подход дает результат.
Правообладателям!
Данное произведение размещено по согласованию с ООО "ЛитРес" (20% исходного текста). Если размещение книги нарушает чьи-либо права, то сообщите об этом.Читателям!
Оплатили, но не знаете что делать дальше?