Текст книги "История и направления развития исследований и технологий индукционного нагрева в Беларуси"
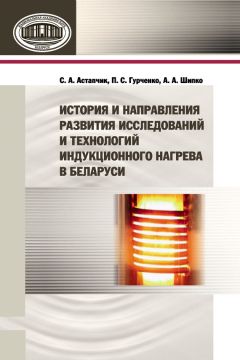
Автор книги: Павел Гурченко
Жанр: Техническая литература, Наука и Образование
сообщить о неприемлемом содержимом
Текущая страница: 1 (всего у книги 4 страниц) [доступный отрывок для чтения: 1 страниц]
Станислав Александрович Астапчик
Павел Семенович Гурченко
Алексей Алексеевич Шипко
История и направления развития исследований и технологий индукционного нагрева в Беларуси
© Астапчик С. А., Гурченко П. С., Шипко А. А., 2015
© Оформление. РУП «Издательский дом «Беларуская навука», 2015
* * *
Введение
Оборудование и технологии нагрева деталей токами высокой частоты (под закалку, отпуск, обработку давлением, пайку) относятся к наиболее энергозатратному виду производства на предприятиях машиностроения – термическому. На заводах машиностроения Беларуси насчитывается около 2000 нагревательных и термических печей, их коэффициент полезного действия редко превышает 10 %, а возраст «средней» печи составляет более 30 лет. Темп же ввода в эксплуатацию более современных печей составляет около 10 шт. в год. Вместе с тем индукционные технологии термической обработки и нагрева под обработку металлов давлением – эффективное средство модернизации термических производств.
Индукционный нагрев токами высокой частоты стальных и чугунных изделий с каждым годом занимает все более важное место в технологии современного машиностроения благодаря своим неоспоримым преимуществам. При нагреве под ковку и штамповку решающие преимущества индукционного нагрева заключаются в возможности значительного повышения скорости нагрева и отсутствии длительного периода разогрева оборудования (первые заготовки разогреваются до заданной температуры уже через 3–5 мин после включения оборудования без необходимости разогрева многотонной массы печей, так как нагреву подвергаются только сами обрабатываемые изделия). По этой же причине нет ограничений и потерь, связанных с жаропрочностью, жаростойкостью и теплопроводностью материалов нагревательных устройств. При индукционном нагреве благо даря высоким скоростям нагрева отсутствуют окалина и угар металла на обрабатываемых изделиях.
Поверхностная закалка при индукционном нагреве более экономична и менее трудоемка и по качеству упрочнения не уступает, а в ряде случаев и превосходит процессы печной обработки. При закалке ТВЧ (токами высокой частоты) вместо цементации в сотни раз сокращается длительность процесса, резко уменьшаются термические деформации, трудоемкость и стоимость упрочнения, в десятки раз снижаются затраты электроэнергии, отпадает необходимость использования природного газа, минеральных масел, асбеста, жаропрочных и жароупорных материалов, устраняются выбросы в окружающую среду вредных веществ и продуктов их распада. Загрузка и выгрузка изделий в индукционных нагревателях автоматизируются, и они встраиваются в автоматизированные комплексы при высокой культуре производства.
Об истории развития технологий индукционного нагрева в нашей стране авторы уже рассказывали в статьях [1, 2] и в докладе на Международной научно-технической конференции «Со временные методы и технологии создания и обработки материалов» в Физико-техническом институте НАН Беларуси [3]. В настоящей работе мы постарались обобщить ранее опубликованные материалы, назвать имена замечательных людей – первопроходцев освоения индукционных технологий, рассказать о годах расцвета их деятельности в республике, привести хронологию развития исследований и разработок, сформулировать направления дальнейших работ.
Минский тракторный завод – первое предприятие Беларуси, освоившее нагрев ТВЧ
Технологии индукционного нагрева на МТЗ, как, впрочем, и на МАЗе, во времена Советского Союза были освоены благодаря специалистам ВНИИ ТВЧ (Всесоюзного научно-исследовательского института токов высокой частоты). Уже во второй половине 1930-х годов В. П. Вологдиным, М. Г. Лозинским, Г. И. Бабатом создавались первые установки. Затем сразу после войны был создан Всесоюзный НИИ ТВЧ, который оказал серьезную помощь трактористам в освоении индукционных технологий (Н. П. Глуханов, А. Н. Шамов, С. Е. Рыскин, С. Н. Перовский, В. Г. Шевченко и др.). Во ВНИИ ТВЧ прошли обучение практически все специалисты службы ТВЧ МТЗ. Поэтому уже в 1946 г., когда готовилось производство трактора «Кировец Д-35», был предусмотрен нагрев ТВЧ деталей двигателя и для пайки резцов [1].
Первые закалочные станки на МТЗ заработали 65 лет назад, когда были закалены детали пускового двигателя, а в 1950 г. – создан участок ТВЧ. Организационных изменений было много, но наиболее крупным подразделением была БЛЭН – базовая лаборатория электронагрева, одна из 54, созданных в БССР по решению Совнархоза (1959 г.). В ней тогда работало 75 человек, из которых 45 – ИТР (инженерно-технические работники). Затем было существенное сокращение, но об этом ниже. Назовем некоторые вехи развития работ.
Хроника развития технологий индукционного нагрева на МТЗ:
1946 г. – под производство трактора «Кировец Д-35» предусмотрено применение ТВЧ для закалки деталей двигателя, коленвала, пайки резцов;
1948 г. – начало применения индукционного нагрева на Минском тракторном заводе при закалке деталей пусковых двигателей, затем дизеля и деталей трактора;
1950 г. – создан участок ТВЧ, преобразованный затем в цех ТВЧ (1952 г.), отделение электронагрева (1954 г.), лабораторию электронагрева (1956 г.), базовую лабораторию электронагрева (1959 г.), проблемную лабораторию электронагрева (1976 г.), проектно-технологический отдел электронагрева ТВЧ (1988 г.); после существенного сокращения отдел вошел составной частью в общий термический отдел (1996 г.);
1950 г. – начало освоения поверхностной закалки газопламенным нагревом шеек коленчатого вала дизеля Д-35;
1951 г. – нагреву ТВЧ подвергали ведущие звездочки, цилиндры, валы, шлицевые втулки, вилки КПП (коробки перемены передач) трелевочного трактора КТ-12, производство которого было передано с ленинградского Кировского завода;
1952 г. – внедрение автоматических и полуавтоматических установок ТВЧ;
1954 г. – начало подготовки производства по применению индукционного нагрева в кузнечном производстве;
1956 г. – освоена ВЧ (высокочастотная) закалка распредвала и гильзы цилиндров;
1957 г. – получено первое авторское свидетельство на изобретение автоматического устройства для закалки колец тяги;
1959 г. – начало работ по созданию централизованной преобразовательной подстанции (мощность станка увеличена до 250 кВт), первая разработка блока автоматического регулирования напряжения, проведены опыты по поверхностной закалке бортовых шестерен;
1960 г. – закалка ТВЧ деталей из легированных сталей со спрейерным охлаждением маслом, широкое внедрение нагрева ТВЧ в кузнице;
1965 г. – начало подготовки производства по термообработке деталей оборонной техники;
1966 г. – начало разработки технологии «чулочной» закалки задней полуоси трактора сложной формы;
1967 г. – начало использования индукционного нагрева под горячую резку дисковыми пилами (вместо резцов) вращающихся труб (в несколько раз повышена стойкость инструмента);
1974 г. – внедрение в производство установки для индукционного нагрева стержневой заготовки торсиона подвески сидения; под получение сферического набора металла на конце за готовки;
1975 г. – термообработка дисков турбин дробеметных машин, звездочек конвейеров, тяговых конвейерных цепей и других деталей вспомогательного оборудования;
1979 г. – ВЧ закалка гнезд клапанов головок блока;
1984 г. – нагрев заготовки полуоси с последующей высадкой двух участков с одного нагрева;
1987 г. – создание тиристорного АРН (автоматического регулирования напряжения) МТЗ;
1990 г. – начало применения ЭВМ в делопроизводстве, а затем – в проектировании оснастки;
1993 г. – состоялась встреча ветеранов – энтузиастов индукционного нагрева Минского тракторного завода;
2005–2010 гг. – создание установки для термической обработки балки плуга (филиал МТЗ, г. Сморгонь).
Начиная с четырех простейших деталей в 1949 г., в 1990-е годы обрабатывались уже сотни наименований деталей в 20 цехах, а мощность оборудования достигала 20 тыс. кВт. Как видно из вышеприведенного, сначала это были шейки коленвала, звездочки, втулки, цилиндры, а позже – детали оборонной техники из легированных сталей, полуоси сложной формы, диски турбин дробеметных машин, конвейерные цепи и т. п. детали. В основном использовали машинные генераторы мощностью до 100 кВт и частотой 8 кГц. Поэтому уже в 1959 г. потребовалось создание централизованной преобразовательной подстанции, при этом мощность станка была увеличена до 250 кВт. Затем быстро появились ламповые генераторы частотой 66 кГц.
Приведем примеры разработок Минского тракторного завода, предоставленные нам Л. С. Космовичем и В. С. Барановым.
Весьма удачной разработкой наших первопроходцев является блок автоматического регулирования напряжения [4] (рис. 1).

Рис. 1. Блок автоматического регулирования напряжения АРН (МТЗ)
Он был создан в 1987 г. на основе разработки инженера Я. Е. Добиса (1959 г.) и представляет собой тиристорный электронный регулятор, которым были укомплектованы все машинные генераторы (преобразовательные подстанции) ТВЧ МТЗ и автоматические регуляторы напряжения ВНИИ ТВЧ, выпускаемые впоследствии электротехнической промышленностью СССР. Он получил медаль ВДНХ и до настоящего времени применяется на машинных преобразователях МТЗ, заводе шестерен, МАЗе. Позволяет с точностью до 1 % поддерживать напряжение на шиносборке преобразовательной подстанции. Документация передана 24 предприятиям и организациям. Применяется на большинстве машинных преобразователей МТЗ и других предприятий.
А вот следующая история просто уникальна. Сейчас это может вызвать улыбки, когда новейшие транзисторные генераторы имеют частоту до 70 кГц, а тогда… В 1958 г. В. С. Барановым, Л. С. Космовичем, Е. С. Лисковым были начаты эксперименты по закалке бортовых шестерен [5]. Завершены работы были в 1975 г. при содействии М. Н. Бодяко и С. А. Астапчика (рис. 2). Это был предварительный подогрев детали в шахтной печи, а затем в течение 5 с одновременный нагрев мощностью 1000 кВт на частоте 8 кГц всей зубчатой поверхности. Для этого и понадобилось параллельно включить 10 преобразователей по 100 кВт каждый. Правда, включать их можно было только по выходным, иначе останавливалось производство. Все получилось, твердость хорошая, результаты стендовых испытаний хорошие. Но цементация оказалась сильнее и процесс не пошел. Это ли сейчас главное. Главное – смелость и большое творческое желание осилить эту «неподъемную» деталь.
Следующая работа – снова удачная. Работы, начатые в 1966 г. В. С. Барановым, В. Ф. Волчком, Л. С. Космовичем и другими тракторозаводчанами, завершились внедрением [6].

Рис. 2. Поверхностная закалка зубчатой поверхности бортовых шестерен: общий вид установки (а) и распределение твердости в сечении зуба в шестерне из стали 50ХГТР после поверхностной закалки (б)
Это не совсем обычная непрерывно-последовательная «чулочная» закалка (рис. 3), при которой несколько спрейеров охватывают изделия с разными углами охвата (270°, 180° и 90°). Деталь, естественно, вращается. В процессе ее перемещения от спрейера к спрейеру импульсный цикл активного охлаждения уменьшается. В момент выхода изделия из первого спрейера его температура в течение 4 с повышалась до 370 °C. Далее в течение 4 с закаливаемый участок охлаждался во втором спрейере до температуры 180 °C, а по выходу из него в течение 8 с температура достигала 320 °C, далее этот участок попадает в третий спрейер, угол охвата которого составляет 90°. В нем поверхность изделия охлаждается до 120 °C. По мере дальнейшего перемещения закаленная область изделия входит в отпускной виток индуктора, который осуществляет ее подогрев до заданной температуры отпуска.
Несмотря на сложную конфигурацию детали, включающей в себя шпоночный паз, рейку в виде зубчатой поверхности, концентрично оси детали выступающий упорный бурт подшипника и шлицевую поверхность, закалочных дефектов на поверхности детали после многократной закалки обнаружено не было. Надежность процесса проверялась десятикратной закалкой детали, изготовленной из стали 38ХГС, с завышенным содержанием углерода до 0,47 %, после которой трещин обнаружено не было.

Рис. 3. Схема спрейера для циклической закалки: 1, 2, 3 – спрейеры с углами охвата изделия 270°, 180° и 90° соответственно; 4 – закаливаемое изделие; 5 – штуцер для подачи воды
Стендовые испытания полуоси, изготовленной из стали 40Х и термообработанной по новой технологии, показали 7-кратное увеличение усталостной прочности и ни разу не были доведены до поломки детали ввиду недостаточной прочности испытательного стенда. Лабораторией была спроектирована универсальная нагревательная станция, впоследствии нашедшая широкое применение не только на предприятиях и в институтах республики, но и на других предприятиях бывшего СССР.
И вновь поисковая работа. Казалось, все получилось. Перед закалкой ТВЧ головка блока объемно нагревалась до 200 °C. Требуемая скорость охлаждения после нагрева обеспечила высокую твердость без образования трещин (рис. 4). Получено авторское свидетельство на изобретение. Но при производственных испытаниях на Минском моторном заводе трещинки все же пошли. И работа не была внедрена.

Рис. 4. Устройство для закалки гнезд клапанов головки блоков цилиндров трактора МТЗ: а – общий вид; б – схема: 1 – привод для вращения индуктора; 2 – подшипник; 3, 4, 5 – элементы индуктора-трансформатора; 6 – вращающийся виток индуктора; 7 – вал крепления
Теперь современная работа – термическая обработка балки плуга на филиале МТЗ в г. Сморгони (рис. 5). Очень оригинальное решение. Перемещаемая по роликам со скоростью до 20 мм/с деталь длиной от 4 до 7,6 м растягивается двумя стальными тросами. Это и обеспечивает передвижение детали, и снижает степень ее коробления. При этом сечение балки – от 40×60 мм до 200×200 мм, а толщина стенки – 8 мм. Использован тиристорный преобразователь мощностью 500 кВт с частотой тока 2400 Гц. Температура нагрева – 950 °C. Это оборудование уже сделано умом и руками нового поколения тэвэчистов. Руководитель работ – в прошлом главный металлург МТЗ, а теперь – начальник управления Минпрома Олег Евгеньевич Лашкевич.
Мы привели лишь некоторые примеры разработок тракторостроителей и только несколько публикаций. Всего специалистами технологий ТВЧ получено 40 авторских свидетельств на изобретения и патенты, опубликовано несколько десятков статей, сделано много докладов на научно-технических конференциях.

Рис. 5. Общий вид установки (а) и индуктора (б) для закалки балки плуга
Важно отметить, что за весь период существования службы ТВЧ Минского тракторного завода ее специалисты оказывали помощь по наладке, запуску оборудования ТВЧ, созданию технологий индукционного нагрева более чем 50 предприятиям республики и всего бывшего Советского Союза, среди которых Бобруйский завод автотракторных деталей, БелАЗ (Белорусский автомобильный завод, г. Жодино), Минский авторемонтный завод, МЗАЛ (Минский завод автоматических линий), Слуцкий авторемонтный завод, Кулебакский металлургический завод, Минский ГПЗ 11 (Государственный подшипниковый завод 11), Челябинский тракторный завод, Ташкентский тракторный завод и др.
Расскажем о замечательных людях – тракторозаводчанах – первопроходцах индукционного нагрева на Минском тракторном заводе (рис. 6, 7).

Рис. 6. Лев Степанович Космович
Лев Степанович Космович – бессменный руководитель всех работ по развитию технологий нагрева ТВЧ на МТЗ с 1950 по 1991 г. Кандидат технических наук. О преданности делу развития технологий ТВЧ говорит справка кадровой службы МТЗ: за период трудовой деятельности Космовича в области технологий ТВЧ на заводе сменилось: начальников Центральной заводской лаборатории – 5, главных металлургов – 6, директоров – 6, главных инженеров – 10, главных технологов – 12.

Рис. 7. Владимир Степанович Баранов
Владимир Степанович Баранов – прошел путь от рабочего-термиста на участке ТВЧ до начальника отдела электронагрева, автор более 20 авторских свидетельств (патентов) на изобретения. Работал на МТЗ с 1948 по 1996 г. Инициатор и участник проведения практически всех основных разработок установок и технологий индукционного нагрева на МТЗ. С 1991 по 1996 г. – начальник ОТВЧ МТЗ.
В своих воспоминаниях Лев Степанович и Владимир Степанович написали: «За 45 лет через службу ТВЧ МТЗ прошли человек 150–200, а может быть и больше. Часть из них проработали до пенсии, часть уволились по объективным причинам, а часть – «не пришлись ко двору». О последних сказать нечего, а вот первая и, отчасти, вторая группа – это люди, определившие успехи и создавшие доброе имя БЛЭН – ПЛЭН – ОТВЧ (базовой лаборатории электронагрева – проблемной лаборатории электронагрева – отдела токов высокой частоты), – B. C. Баранов, А. Н. Басалыго, В. И. Дмитриев, Я. И. Добис, М. А. Довнар, Н. Ф. Ладутько, В. И. Прицев, М. Р. Слепян, В. И. Сорокин, Я. Т. Федорович, М. Л. Этин, К. Н. Кошеленков». Добавить здесь что-то трудно.

Рис. 8. Ветераны – энтузиасты развития индукционного нагрева на Минском тракторном заводе. На переднем плане Н. А. Космович. Во втором ряду: Н. В. Кошеленкова, Б. Н. Хоцкевич, В. И. Прицев, М. Л. Этин. В третьем ряду: В. А. Гуринович, К. Н. Кошеленков, В. Ф. Волчек, Л. С. Космович, В. С. Баранов (г. Минск, 1993 г.)
В 1990 г. началось омоложение руководства отдела. В. И. Прицева сменил В. Ф. Волчок, а в 1991 г. заместителем начальника по производству стал В. А. Гуринович.
В 1993 г. состоялась встреча ветеранов – энтузиастов скоростного индукционного нагрева Минского тракторного завода (рис. 8).
Индукционные технологии и оборудование Минского автомобильного завода
Первые установки индукционного нагрева на Минском автозаводе появились в 1949 г. Однако если на тракторном заводе практически уже с 1950 г. быстро росло число деталей, обрабатываемых с использованием закалки ТВЧ, то на МАЗе системные работы начались только с 1957 г., когда была создана лаборатория электронагрева.
Первым руководителем лаборатории был Николай Федорович Андрющенко (рис. 9). Мастер спорта СССР, золотой медалист VI Всемирного фестиваля молодежи и студентов в Москве по прыжкам в длину. В его спортивной биографии – и XV олимпийские игры в Хельсинки, и III Всемирный фестиваль молодежи и студентов в Берлине. Спортивная закалка помогала. При внедрении новых технологий также приходилось преодолевать непонимание и опасение осторожных руководителей цехов и отделов завода. Это по инициативе и под руководством Николая Федоровича был начат перевод на индукционный нагрев заготовок под ковку и штамповку. К 1975 г. уже сотни заготовок на МАЗе нагревали индукционно под обработку давлением.
За этот период времени была освоена также поверхностная индукционная закалка таких сложных и тяжелонагруженных деталей автомобиля, как поворотные кулаки и шкворни поворотного устройства передней оси автомобиля, сложнопрофильные головки и цилиндрические шейки разжимных кулаков тормозного устройства, полуоси и кожухи полуосей ведущего моста, кулаки шарниров коробки отбора мощности, наружная сферическая поверхность шаровых пальцев и внутренняя сферическая поверхность головок тяг рулевого управления и многие другие детали автомобиля МАЗ. При этом быстро развивалась технология поверхностной индукционной закалки с применением одновременного локального нагрева упрочняемых зон небольших размеров и непрерывно-последовательная закалка длин номерных деталей (например, полуосей длиной 1120 мм). Для закалки этих деталей конструкторами лаборатории разработаны и совместно с технологами, слесарями, наладчиками и другими специалистами внедрены в производство многочисленные индукторы и универсальные индукционные установки для одновременной и непрерывно-последовательной закалки типовых деталей простой цилиндрической формы, а также специализированные установки для закалки длинномерных деталей и деталей сложной конфигурации.
С 1966 по 1979 г. начальником лаборатории была Мария Александровна Попова (рис. 10). В эти годы масштабы применения индукционных технологий на заводе были серьезно расширены. 14 кузнечных индукционных нагревателей типа КИН-100 и КИН-200 с механизированной загрузкой заготовок в индуктор и автоматизированной подачей их в рабочую зону прессов и молотов были изготовлены и внедрены в кузнечном производстве МАЗа при активном участии специалистов лаборатории: В. П. Князькова, Ф. Г. Майсюка, Н. Б. Кондратовича.
В 1969 г. уже 250 наименований деталей подвергались индукционному нагреву. В этот период времени разработаны и внедрены процессы и оборудование установок поверхностной закалки с применением индукционного нагрева: объемно-поверхностной закалки шестерен ведущего моста автомобилей МАЗ из стали НИПРА (1967 г.) и шкворней поворотного устройства из стали 45 (1973 г.), непрерывно-последовательной закалки пальцев рессоры и полуосей автомобилей МАЗ (1975 г.), одновременной закалки шаровых пальцев рулевого управления, поворотных кулаков передней оси (1976 г.) и др. Было освоено горячее выдавливание с индукционного нагрева головок крепежных изделий, тройников и угольников для гидросистем, шаровых головок пальцев рулевого управления и других деталей.

Рис. 9. Николай Федорович Андрющенко

Рис. 10. Мария Александровна Попова
С 1979 по 1983 г. начальником лаборатории электронагрева был Виктор Максимович Быков (рис. 11). Им разработан и внедрен в производство ряд уникальных автоматизированных установок поверхностной закалки: объемно-поверхностной закалки шестерен ведущего моста (1967 г.) и шкворней поворотного устройства автомобилей (1973 г.), непрерывно-последовательной закалки пальцев рессоры и полу осей (1975 г.), одновременной закалки шаровых пальцев рулевого управления, поворотных кулаков передней оси (1976 г.).
Создана конструкция универсальных одно– и двухпозиционных станков для одновременной и непрерывно-последовательной закалки осевых деталей (1964 г.), впоследствии использованная АЗЛК (Автомобильным заводом им. Ленинского комсомола) в качестве базовой конструкции для серийного производства таких станков для предприятий автомобильной промышленности СССР. В. М. Быков принимал непосредственное участие и осуществлял техническое руководство при разработке установок индукционного нагрева заготовок под изготовление чизельных зубьев на Кобринском автоагрегатном заводе (1984 г.), малолистовых рессор на Минском рессорном заводе (1985 г.), электроконтактного нагрева пружин на КЗТШ (Кузнечном заводе тяжелых штамповок, г. Жодино) (1982 г.), пластин и плоских заготовок на БелАЗе (1990 г.). В соавторстве им разработана и внедрена установка контурной малодеформационной закалки бортовых шестерен колесной передачи автомобилей МАЗ (1994 г.), универсальная установка для регулируемой закалки деталей ШРУС (шарнира равных угловых скоростей) на Минском подшипниковом заводе (1993 г.) и многие другие технологические устройства индукционного нагрева.

Рис. 11. Виктор Максимович Быков
Уже в 1982 г. на МАЗе количество деталей, подвергаемых индукционному нагреву, составило 400 наименований; при этом мощность оборудования – 10 000 кВт (около 700 типовых индукторов).
Большие заслуги в переоснащении кузнечного производства на индукционный нагрев вместо печного принадлежат инженеру-электрику В. П. Князькову. Совместно с энергетиком кузнечного цеха С. И. Головней и электриком П. А. Каменко выполнял отладку и внедрение кузнечных индукционных нагревателей и их обслуживание в эксплуатации. За внедрение автоматизированных комплексов в составе индукционных нагревателей и устройств автоматизированной загрузки заготовок в индуктор, выгрузки заготовок из индуктора и подачу на рабочее место кузнеца в штамп В. П. Князьков, С. И. Головня и П. А. Каменко были удостоены премии Минского автомобильного завода. В этих линиях полностью устранен тяжелый ручной труд кузнеца-нагревальщика. Заготовки без участия кузнеца из накопительного бункера попадают во вращающееся ориентирующее устройство, где выстраиваются в непрерывную «колбасу», проходящую индуктор, а далее, нагретые до ковочной температуры, по одной цепным транспортером подаются в штамп. И сегодня такой тип загрузочного устройства является одним из самых перспективных в кузнечном производстве отечественных и зарубежных предприятий.
Большая роль в создании оснастки и оборудования индукционного нагрева на Минском автомобильном заводе принадлежит конструктору Валентине Фроловне Волчек, проработавшей инженером-конструктором лаборатории электронагрева с 1958 по 1988 г. Она спроектировала большую часть набора типовых индукторов на все виды подлежащих обработке с индукционным нагревом заготовок и деталей автомобилей МАЗ. Достойной ученицей и преемницей В. Ф. Волчек стала инженер-конструктор Татьяна Андреевна Воеводина, прибывшая на работу на МАЗ по распределению ЛЭТИ (Ленинградского электротехнического института) и проработавшая на заводе всю свою трудовую жизнь – с 1975 по 2010 г. Она продолжила разработку технологической оснастки для деталей новой осваиваемой автотехники, завершила систематизацию и составление каталогов индукторов и технологических центров для индукционной закалки деталей, разработала ряд сложных технологических приспособлений. Сей час на МАЗе более 700 наименований только типовых индукторов.
Заметный след в разработке устройств индукционного нагрева на ОАО «МАЗ» оставил Николай Сергеевич Карпушкин, проработавший в лаборатории электронагрева с 1995 по 2009 г. в должности инженера-конструктора, а затем начальника КБ. Его «карандашу» принадлежат проекты полуавтоматических станков для контурной закалки ведомых шестерен автомобилей МЗКТ и контурной закалки наружных зубьев шестерен конечной передачи трактора «Беларусь». С его участием созданы проекты индукционных установок для термообработки стальной литой дроби, объемно-поверхностной закалки шестерен и сателлитов колесной передачи, термообработки круглого проката и др.
Особая роль принадлежала инженеру-конструктору Федору Григорьевичу Майсюку, проработавшему в лаборатории электронагрева с 1965 по 2010 г. Он был компетентным не только во всех вопросах производства, методах обработки и конструирования технологической оснастки, но и в разработке целого ряда кузнечных индукционных нагревателей кузнечного и агрегатного цехов МАЗа, индукционных нагревателей Минского рессорного завода, оборудования для электроконтактного нагрева под навивку и закалку пружин на КЗТШ, установок для закалки поворотных кулаков, типовых универсальных установок индукционного нагрева, работающих на всех заводах объединения «БелавтоМАЗ» и за его пределами, и многих других видов оснастки.
Организацией производственной, научной и учебной деятельности в ЦЗЛ (Центральной заводской лаборатории), УЛИР (Управлении лабораторных и исследовательских работ) и УГМет (Управлении главного металлурга) c 1996 г. по настоящее время занимается ведущий инженер-технолог МАЗа Ирина Владимировна Коленко. Наряду с технологическими обязанностями она ведет всю организационную и «бумажную» работу по планированию и отчетности выполнения научно-исследовательских работ, согласованию расчетов их экономической эффективности, расчета стоимости выполняемых работ для сторонних организаций, организации документооборота, организации и функционированию системы качества, аудитов, организации научных конференций, созданию и функционированию учебно-научно-производственной лаборатории и филиала кафедры, организации учебного процесса студентов, повышения квалификации и переаттестации персонала, а также выполняет много других функций, без выполнения которых деятельность крупного структурного подразделения предприятия сегодня не представляется возможной.
Говоря о конструкторских работах, нельзя не отметить кропотливый труд по копированию тушью на кальку конструкторской документации при помощи пера, линейки и рейсфедера. Последний инструмент помнят только ветераны. Но 20 или даже 10 лет назад без ручного копирования чертежей тушью на кальке не могло обойтись ни одно конструкторское бюро. Выполняли эту нелегкую и к тому же низкооплачиваемую работу, как правило, женщины, обладающие не только красивым почерком, но и большим терпением и усидчивостью. Кто хоть раз пробовал копировать на кальку порой неразборчивые и еле различимые карандашные чертежи, тот знает, какого терпения и внимания эта работа требует. Поэтому сомневаемся, что кто-то может назвать хоть одного копировщика-мужчину. В разное время в лаборатории электронагрева МАЗа эту работу выполняли
Краснянская Светлана, Яковчук Лариса и Париш Нина. И хотя их нелегкая работа по созданию калек чертежей была выполнена десятки лет назад, этой документацией пользуются и сегодня как производственники, так и студенты.
Сегодня в лаборатории электронагрева работает грамотный инженер-конструктор Александр Игоревич Губашин, приходят на работу и молодые специалисты. Незаменимые ранее в конструкторской деятельности чертежные приборы типа «Кульман» сегодня уже остались в лаборатории только в качестве музейных экспонатов. Вся разработка и тиражирование конструкторской документации выполняются на современном вычислительном оборудовании.
Трудно преувеличить роль талантливого инженера-электрика лаборатории электронагрева МАЗа Николая Брониславовича Кондратовича в развитии технологии и оборудования индукционной обработки в период с 1972 г. по настоящее время не только на Минском автомобильном заводе, но и на многих предприятиях Республики Беларусь. Им разработаны, собраны, отлажены, внедрены и на протяжении многих лет поддерживаются в рабочем состоянии многочисленные системы автоматизированного управления технологическими процессами и индукционными установками на Минском автомобильном заводе, всех заводах объединения БелавтоМАЗ и многих предприятиях республики. К этому скромному, всегда старающемуся оставаться в тени людского внимания выдающемуся специалисту часто обращались и обращаются за помощью со многих предприятий республики, когда трудно установить причину остановки оборудования и (или) отладить режимы технологического процесса индукционного нагрева.
С 1972 по 2011 г. верным помощником Н. Б. Кондратовича в части монтажа, отладки и эксплуатации технологического оборудования и технологических процессов индукционного нагрева был слесарь-электрик Виктор Павлович Аношко, который на экспериментальном участке ТВЧ был аккуратным и незаменимым хозяином запчастей и комплектующих деталей.
С 2011 г. все работы по внедрению, отладке, ремонту и обслуживанию высокочастотных индукционных установок на Минском автомобильном заводе выполняет опытный инженер-электроник Святослав Станиславович Прасмыцкий.
Внимание! Это не конец книги.
Если начало книги вам понравилось, то полную версию можно приобрести у нашего партнёра - распространителя легального контента. Поддержите автора!Правообладателям!
Данное произведение размещено по согласованию с ООО "ЛитРес" (20% исходного текста). Если размещение книги нарушает чьи-либо права, то сообщите об этом.Читателям!
Оплатили, но не знаете что делать дальше?