Текст книги "Котлы тепловых электростанций и защита атмосферы"
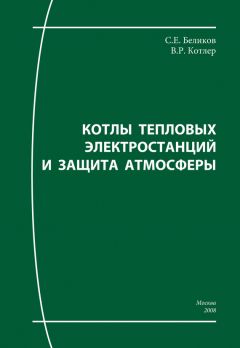
Автор книги: Сергей Беликов
Жанр: Техническая литература, Наука и Образование
Возрастные ограничения: +12
сообщить о неприемлемом содержимом
Текущая страница: 4 (всего у книги 17 страниц) [доступный отрывок для чтения: 6 страниц]
В последние десятилетия при использовании высоковлажных и низкокалорийных твердых топлив на тракте между мельницей и горелкой стали устанавливать пылеконцентраторы (рис. 3.15). Необходимость их установки объясняется следующим образом.

Рис. 3.15. Схема пылеконцентратора: 1 – корпус; 2 – завихритель; 3 – рассекатель; 4 – основной отвод; 5 – сбросной отвод
При сжигании, например, болгарского лигнита с Qir = 5,46 МДж/кг и Wr = 56 % теоретическая (адиабатическая) температура горения составляет всего 1373 К (1100 °С). Столь низкое значение ϑa объясняется не только большой влажностью, но и сушкой топлива газами рециркуляции для получения достаточно подсушенной пыли. Подача в ядро горения вместе с топливом большого количества инертных газов приводит к дополнительному снижению теоретической температуры горения топлива. Расчеты показывают, что, например, для получения достаточно сухой пыли (Wpf <20 %) при размоле болгарских бурых углей доля газа, идущего на сушку, а затем вдуваемого вместе с пылью в ядро факела в виде сравнительно холодного агента (140–200 °С), составляет 40–60 % всех топочных газов. Кроме того, наличие в первичной аэросмеси такого большого количества инертного продукта и водяного пара уменьшает концентрацию кислорода, что также затрудняет нормальное развитие топочного процесса.
Для надежного сжигания высоковлажных углей типа болгарского бурого, путем повышения температуры и концентрации кислорода в ядре факела при сохранении всех преимуществ системы с прямым вдуванием, был использован пылеконцентратор, позволяющий отделить часть слабозапыленного влажного сушильного агента и сбросить его в верхнюю часть топки.
Принцип действия пылеконцентратора заключается в разделении исходной пылегазовой смеси на сильно– и слабозапыленные потоки за счет различных гидродинамических свойств твердой и газовой фазы. В центробежном пылеконцентраторе, схема которого приведена на рис. 3.15, поток аэросмеси проходит через лопаточный завихритель и приобретает вращательное движение. За счет действия центробежной силы пылевые частицы отжимаются к внутренней поверхности корпуса, увеличивая концентрацию несущего газового потока. Рабочий процесс в пылеконцентраторе заканчивается выделением в самостоятельные отводы части несущего газового потока, имеющего большую, по сравнению с исходным потоком, концентрацию пыли и другой части с соответственно меньшей, чем у исходного, концентрацией пыли.
Основными режимными параметрами пылеконцентратора являются gc и l, где gc – это доля пыли, поступающей в основной отвод, то есть
gc = Gосн /Gо, (3.2)
а l – доля газа (несущего агента), также поступающего в основной отвод:
l = Qосн/Q0. (3.3)
Слабозапыленный поток, включающий в себя остаток пыли Gсбр = G0−Gосн, выносится газовым агентом Qсбр = Qо−Qосн в сбросной пылепровод и далее в сбросную горелку.
Глубина разделения пылегазового потока выражается как отношение:
gc/l = (Gocн · Q0)/(G0 · Qосн). (3.4)
Следовательно,
gc/l = μосн/μ0
где μ0, μосн – концентрации пыли на входе в пылеконцентратор (то есть за мельницей) и в основном отводе (перед основной горелкой).
Меньшая часть угольной пыли (l – gc) вместе с определенной частью сушильного агента (1 – l) поступает, как упоминалось ранее, в сбросные горелки, расположенные выше основных. Поэтому время для горения сбросной пыли в топочной камере несколько уменьшается. Это обстоятельство накладывает определенные требования на фракционный состав сбросной пыли: она не должна содержать крупные частицы, особенно размером более 1000 мкм. И в этом плане центробежные пылеконцентраторы с регулируемой степенью крутки потока оказываются наиболее подходящими.
При проведении испытаний центробежного пылеконцентратора, изображенного на рис. 3.15, оказалось, что при α = 20° доля топлива, поступающая в основные горелки (gc), была равна 0,85, а l = 0,5, то есть l/gc = 0,59. В опытах с большей круткой потока (α = 45°) оказалось: gc = 0,9; l = 0,6 и l/gc = 0,67. Гидравлическое сопротивление пылеконцентратора составляло 60–65 кгс/м2.
На рис. 3.16 показана конструкция двухступенчатого пылеконцентратора, позволяющая слабозапыленный поток аэросмеси дополнительно разделить на два потока. Один из них содержит чрезвычайно мало частиц угольной пыли, причем наиболее тонких, которые могут выгореть, поступая даже в верхнюю часть топочной камеры.

Рис. 3.16. Двухступенчатый пылеконцентратор: 1 – внешний корпус; 2 – завихритель; 3 – рассекатель; 4 – внутренний корпус; 5,6 – внешний и внутренний основные отводы; 7,8 – внешний и внутренний сбросные отводы; 9 – обтекатель
3.2. Мазут: прием, хранение и подача в котельный цех
Жидкое топливо на тепловых электростанциях – это, главным образом, мазуты марок 40 (40 В) и 100 (100 В), поставляемые нефтеперерабатывающими заводами (НПЗ). Символ «В» сохранился с тех времен, когда лучшие сорта топочного мазута удостаивали государственного Знака качества.
Сравнительно редко на ТЭС можно встретить высококачественные флотские мазуты (Ф5 и Ф12), еще реже – остатки перегонки смол, получаемых при термической переработке углей и горючих сланцев. Низкокачественный мазут для мартеновских печей марки 200 вообще не должен поставляться на тепловые электростанции. Технические требования и нормы качества мазутов в соответствии с ГОСТ 10585-75 приведены в табл. 3.3.
Таблица 3.3 Характеристики качества мазутов, поставляемых российскими НПЗ

В состав мазутов входят те же основные элементы, что и в состав нефти, из которой получены эти мазуты: горючие вещества – углерод, водород и сера, а также негорючие – кислород и азот. Содержание водорода и углерода несколько ниже у высокосернистых мазутов, что и приводит к некоторому уменьшению их теплоты сгорания.
Кроме углеводородных соединений – основного компонента мазута – в их состав входят асфальтосмолистые вещества (асфальтены, карбены и карбоиды), а также минеральные примеси (в основном – растворенные в воде соли щелочных металлов) и влага. Содержание воды в мазутах колеблется от 0,3–1,0 до 3–5 %. При разогреве мазута паром (например, при сливе мазута из цистерн) обводненность мазута может увеличиться до 5–10 % в летнее время и 15–20 % – в зимнее (для высоковязких мазутов).
Содержание серы в мазуте определяется сернистостью исходной нефти, а также технологией ее переработки. Присутствует сера в мазуте, главным образом, в виде сероорганических соединений, и в меньшей степени – в виде сероводорода и серы элементарной.
Важнейшая характеристика мазута – вязкость, так как именно она определяет условия транспортировки, слива и хранения жидкого топлива. Вязкость определяет также требуемый подогрев мазута и эффективность работы мазутных форсунок при её сжигании в котельных установках.
Вязкость обычно измеряется вискозиметром Энглера (рис. 3.17) в градусах условной вязкости (ВУ) при определенной температуре. Условной вязкостью называют отношение времени непрерывного истечения 200 мл мазута при определенной температуре ко времени истечения дистиллированной воды при 20 °С.

Рис. 3.17. Вискозимер Энглера: 1 – металлический сосуд; 2 – жидкость; 3 – ванна; 4,5 – термометры; 6 – калиброванный сосуд
Из табл. 3.3 следует, что для флотских мазутов стандартной является температура 50 °С, а для мазутов марок 40 и 100 – уже 80 °С. Хотя марки 40 и 100 получили свое обозначение именно по максимальному значению условной вязкости (градусов ВУ) при температуре 50 °С.
Еще один параметр имеет чрезвычайно важное значение при использовании мазута на тепловых электростанциях. Речь идет о температурах вспышки и воспламенения мазута. Температурой вспышки называют ту температуру, до которой нужно нагреть мазут в определенных условиях, чтобы количество выделившихся при этом паров (в смеси с воздухом) могло вспыхнуть при поднесении к этой смеси запала. Если вслед за вспышкой паров в течение не менее 5 с начинается горение самого топлива, то соответствующая температура называется температурой воспламенения, или верхним пределом температуры вспышки.
В условиях ТЭС температура вспышки определяется для установления максимально допустимой температуры подогрева мазута в емкостях, не изолированных от окружающего воздуха. По условиям пожарной безопасности фактическая температура должна быть на 10 °С ниже температуры вспышки.
Топочный мазут, как правило, поступает на тепловые электростанции с использованием железнодорожного, водного или автомобильного транспорта. При удалении ТЭС от НПЗ на расстояние не более 20 км мазут подается по трубопроводам. В этом случае отпадает необходимость в приемносливных устройствах и не происходит обводнения мазута, неизбежного при его разогреве для полного слива из цистерн.
Для разгрузки и слива мазута из железнодорожных цистерн электростанция должна иметь разгрузочную эстакаду, оборудованную устройствами для разогрева мазута, обслуживания цистерн и слива мазута в приемные резервуары. Обычно сливные лотки обогреваются паровыми спутниками для подогрева мазута и ускорения его движения по лоткам. Емкость и количество приемных резервуаров должны быть рассчитаны на бесперебойный слив мазута из всех прибывших железнодорожных цистерн.
Хранение мазута на ТЭС осуществляется, как правило, в железобетонных резервуарах сборной конструкции, но в районах с повышенной сейсмичностью требуется установка металлических резервуаров. Последние требуют тщательной тепловой изоляции. Поддержание необходимой температуры при хранении мазута в обвалованных железобетонных резервуарах (60–70 °С) обеспечивается циркуляционным подогревом мазута с использованием внешнего подогревателя.
На линии подачи мазута из хранилища в котельный цех осуществляется дополнительный подогрев мазута с целью лучшего его распыливания в топочной камере. Оптимальная вязкость мазута перед форсунками (1,5–2 °ВУ) обеспечивается при повышении температуры мазутов марки 40 и 100 до 130 и 140 °С соответственно. Требуемый подогрев мазута на линии подачи к форсункам можно получить, используя специальные трубчатые теплообменники, в которые подается пар с температурой около 200 °С.
Кроме подогрева, необходимо проводить и очистку мазута от механических примесей. Фильтрационная очистка уменьшает износ и загрязнение форсунок, а также предотвращает отложения в мазутопроводах. Первая ступень очистки осуществляется в отводных лотках сливных устройств (фильтры-сетки с ячейками 10–12 мм). Вторая ступень (фильтр тонкой очистки с сеткой, имеющей 32 или 64 отверстия на 1 см2) устанавливается в мазутонасосной после насосов II подъема.
Особого внимания требует подготовка к сжиганию высокосернистого мазута. Дело в том, что в процессе хранения, подогрева и перекачки мазута сернистые соединения могут вызвать коррозию металла. Кроме того, сернистые соединения приводят к опасному загрязнению вод мазутохранилищ, что требует их очистки или утилизации перед сбросом в водоемы.
В некоторых случаях для устранения трудностей, связанных с использованием серосодержащих мазутов, приходится применять присадки. Количество вводимых в мазут присадок находится в пределах от 0,01 до 0,1 %, но всё же обработка мазута увеличивает его стоимость. В 1970–1980-е гг. при длительной работе многих электростанций на сернистых мазутах широко использовались отечественные присадки ВНИИНП-112 и ВТИ-4ст, которые существенно снижали загрязнение поверхностей нагрева и предотвращали их коррозионное разрушение.
Следует отметить, что процессы подогрева, перемешивания мазута в резервуарах и его фильтрация осуществляются, как правило, при низком (около 1 МПа) давлении, создаваемом насосами первого подъема. Но затем насосы второго подъема (3,5–4,5 МПа) перекачивают мазут в главный корпус, к котельным установкам. От общей мазутной магистрали жидкое топливо, после запорных задвижек и регулирующих клапанов, направляется к котлам и далее – к отдельным форсункам. Часть мазута, неизрасходованного в котле, возвращается в основной резервуар по линии рециркуляции мазута. Это позволяет сохранять температуру жидкого топлива на требуемом уровне, независимо от потребления его котлом.
3.3. Газоснабжение котлов на тепловых электростанциях
Природный газ поступает на тепловые электростанции от мест добычи по магистральным газопроводам, давление в которых может составлять 5–7 МПа. Непосредственно к ТЭС газ подается от газораспределительных станций (ГРС) с давлением 0,7–1,3 МПа. После ввода на ТЭС газ попадает в местный газорегулировочный пункт (ГРП), в котором его давление снижается до необходимого уровня и поддерживается постоянным в пределах от 0,05 до 0,12 МПа. Кроме регуляторов давления, в ГРП имеются фильтры, необходимые для очистки газа от механических примесей. Здесь установлены также предохранительные клапаны, срабатывающие при аварийном повышении давления газа, расходомер, манометр и продувочная свеча. На крупных электростанциях ГРП располагается в отдельном помещении. Прокладка всех газопроводов на территории ТЭС выполняется наземной, на железобетонных или металлических эстакадах.
В последние годы для снижения избыточного давления газа всё чаще стали применять турбодетандеры – газотурбинные генераторы, работающие на перепаде давления газа. На тепловых электростанциях турбодетандеры врезают параллельно газораспределительным станциям, понижающим давление природного газа из магистрального трубопровода.
При пропуске газа через турбину детандера сброс давления осуществляется за счет передачи энергии турбине, которая вращает генератор электрического тока. Незначительное количество газа при этом используется для подогрева рабочего тела на выходе из турбины.
В зависимости от перепада давления и объема применяемого на ТЭС природного газа турбодетандеры могут иметь мощность от 1 до 36 МВт. Поскольку при работе турбодетандера практически не происходит расходование топлива, получаемая энергия является «экологически чистой», то есть не приводит к выбросам в атмосферу как токсичных, так и тепличных газов. Кроме того, выработка электроэнергии турбодетандерами экономит расход природного газа, а значит, еще больше снижает выбросы загрязняющих веществ в атмосферу.
После ГРП газ подается в котельный цех и через индивидуальные расходомеры поступает к каждому котлу. На этих линиях обязательно устанавливают автоматический регулятор расхода газа (АРР) и отсекающий быстродействующий клапан (БК). Последний срабатывает при возникновении аварийной ситуации, а регулятор АРР обеспечивает необходимую тепловую мощность при работе котла на газе.
Газопроводы к котлам прокладывают в виде тупиковых ответвлений от общестанционной магистрали. Все газопроводы, как и положено по технике безопасности [3], снабжаются свечой, отводящей газ при продувке газопроводов в атмосферу. Свечи обычно выводят в места, недоступные для пребывания людей. Через свечи вытесняется также газовоздушная смесь, появляющаяся в газопроводе перед растопкой котла. Схема газопроводов с необходимой арматурой в помещении котельного цеха приведена на рис. 3.18. Для газопроводов используются стальные бесшовные трубы, диаметр которых выбирается по расходу газа и принятой скорости его движения. Рекомендуемые значения скорости составляют 60–80 м/с для магистральных газопроводов и 40–60 м/с для отводов к котлам.

Рис. 3.18. Схема газопроводов в помещении котельной
На электростанциях, расположенных по соседству с предприятиями металлургического профиля, часто сжигают доменный или коксовый газ. В этих случаях система газоснабжения принципиально не отличается от схемы подачи природного газа. Но в любом случае для котлов, получающих из общей магистрали технологический газ, должен быть предусмотрен индивидуальный ГРП, в котором осуществляются дросселирование и поддержание постоянного давления газа.
Глава 4. Тепловой и материальный баланс котельной установки
Котельная установка сконструирована и работает в строгом соответствии с законом сохранения энергии. Это значит, что тепловая энергия, полученная в топке в результате сгорания органического топлива, расходуется на нагревание и превращение воды в пар, а также на перегрев этого пара до заданной температуры. Некоторая часть тепловой энергии при этом теряется в окружающую среду, с уходящими газами, с физическим теплом золы и шлака. Присутствует среди потерь и несгоревшая часть топлива – химический и механический недожог (рис. 4.1).

Рис. 4.1. Схема основных тепловых потоков котла
4.1. Газовоздушный тракт
Для превращения химической энергии органического топлива в тепловую, в топочную камеру котла подаются топливо и окислитель, а из котла удаляются продукты сгорания. Конструкторы котла и эксплуатационный персонал (каждый – в зоне своей компетенции) стараются обеспечить максимально полное сгорание топлива, минимальные потери в окружающую среду и максимальную степень охлаждения продуктов сгорания, покидающих котельную установку. Всё это вместе приводит к повышению коэффициента полезного действия – КПД (брутто).
Приходная часть материального баланса котла — это топливо (В, кг/с) и окислитель (LB, кг/с), в качестве которого используется организованно подаваемый в топку горячий воздух. Кроме того, в негазоплотных котлах, работающих под разрежением, в топку и конвективные газоходы подсасывается некоторое количество воздуха (ΔLт и ΔLк, кг/с). При этом подсосанный в конвективный газоход воздух в процессе горения не участвует, то есть является полностью балластным.
Расходная часть материального баланса — газообразные продукты сгорания, покидающие котел, и твердые очаговые остатки – золошлаки (последние – только при сжигании твердого топлива). При этом шлак удаляется через холодную воронку или через летку (в топках с жидким шлакоудалением), а зола уноса улавливается в электрофильтрах или других золоуловителях (за исключением небольшой части, уносимой газообразными продуктами сгорания через дымовую трубу).
Таким образом, уравнение материального баланса по газовоздушному тракту можно записать в таком виде:
B + LB + ΔL = Lr + ΣGз/ш. (4.1)
В случае сжигания жидкого или газообразного топлива в этом уравнении последний член отсутствует.
Расход топлива В определяется мощностью (паропроизводительностью) котельного агрегата, а необходимый расход окислителя (кислорода) можно подсчитать по содержанию в топливе горючих компонентов – углерода С, водорода Н и серы S.
Так, например, количество кислорода, необходимое для полного сгорания углерода, легко определить, зная молекулярные массы углерода (12), кислорода (32) и плотность кислорода при 20 °С и 101,3 кПа (1,428 кг/м3):
(4.2)
Точно так же можно подсчитать количество необходимого кислорода для полного сгорания водорода (5,56 м3/кг) и серы (0,7 м3/кг). После этого легко определить теоретически необходимый расход кислорода для полного сгорания твердого и жидкого топлива (с учетом кислорода Оr, который имеется в сжигаемом топливе):
. (4.3)
Если учесть, что содержание кислорода в воздухе (по объему) составляет приблизительно 21 %, то для определения теоретического количества сухого воздуха VBO (м3/кг), необходимого для полного сгорания твердого и жидкого топлива (то есть при α = 1,0), можно записать:
VBO = 0,0889 (Сr + 0,375SrO+K) + 0,265Нr − 0,ЗЗЗОr. (4.4)
Аналогичный расчет для случая, когда в котле сжигается газообразное топливо, позволяет определить теоретически необходимое количество воздуха для полного сгорания 1 м3 газа (VBOм3/м3) с известным химическим составом:
VBO = 0,0476 [0,5СО + 0,5Н2 + 1,5H2S + 2(m + n/4)СmНn−O2]. (4.5)
Скорость горения, как и скорость других химических реакций, зависит, в частности, от концентрации реагирующих веществ. Поэтому теоретически необходимого количества воздуха оказывается недостаточно для полного сгорания топлива: на последней стадии горения скорость реакций станет недопустимо малой – топливо не успеет сгореть в зоне высоких температур. Именно поэтому в топку подают количество воздуха, превышающее теоретически необходимое. Отношение первого ко второму называют коэффициентом избытка воздуха и традиционно обозначают первой буквой греческого алфавита – α. Следовательно,
α = VB / VBO, (4.6)
где VB и VBO – фактический и теоретически необходимый расходы воздуха (м3/кг или м3/м3).
В некоторых странах используют не «коэффициент» (отношение), а «избыток» воздуха в процентах, то есть 100 (VB − VBO) / VBO. Понятно, что α = 1,15, например, соответствует избытку воздуха 15 %, α = 1,2–20 %, и т. д.
После завершения топочного процесса в котле образуются продукты сгорания, состав и количество которых имеют большое значение как для процессов теплообмена и аэродинамики в конвективных поверхностях нагрева, так и для анализа проблемы загрязнения атмосферного воздуха.
Если пренебречь ничтожно малым объемом монооксида углерода Vco, то можно считать, что газообразные продукты сгорания – это трехатомные газы: (Vco2+ Vso2), азот VN2 и водяные пары VH2O. Объем трехатомных газов VRO2 (м3/кг) удобно выразить в виде одного члена:
. (4.7)
Объем азота при сжигании топлива с теоретически необходимым количеством воздуха будет равен сумме азота воздуха и молекулярного азота, образовавшегося из азотсодержащих компонентов топлива:
. (4.8)
Объем водяных паров в продуктах сгорания складывается из нескольких составляющих: водяного пара, образовавшегося при сгорании водорода топлива, испарившейся влаги топлива и, наконец, влаги, внесенной в топку вместе с теоретически необходимым количеством воздуха:
. (4.9)
В этом уравнении принято, что влагосодержание воздуха αв = 10 г/кг. В тех случаях, когда в котле сжигается мазут с использованием форсунок парового распыливания, необходимо добавить еще один член – 1,24 GФ, где GФ – расход пара, кг/кг.
Объем водяных паров при фактическом расходе воздуха (α>1) будет несколько больше за счет водяных паров, содержащихся в дополнительном воздухе (α−1):
. (4.10)
Таким образом, окончательное выражение для подсчета объема продуктов сгорания 1 кг твердого или жидкого топлива К (м3/кг) имеет вид:
. (4.11)
При сжигании газообразного топлива теоретический объем азота, как и в случае с углем, состоит из азота воздуха и молекулярного азота, присутствующего в топливе:
. (4.12)
Объем трехатомных газов VRO2 (м3/м3) при сжигании газа равен:
. (4.13)
Теоретический объем водяных паров также рассчитывается по формуле, отличающейся от аналогичной зависимости для угля:
. (4.14)
Здесь dг.тл – влагосодержание газообразного топлива, отнесенное к 1 м3 сухого газа, г/м3. Теперь, для определения объема водяных паров и общего объема дымовых газов при сжигании газообразного топлива с α>1,0 можно воспользоваться уравнениями (4.10) и (4.11).
В некоторых случаях требуется определить плотность сухого газа ρdг.тл (кг/м3). Зная состав газа, легко рассчитать ρdг.тл при нормальных условиях:
ρdг.тл = 0,01[1,96CO2 + 1,52H2S + 1,25N2 + 1,43О2+ 1,25СО + 0,0899Н2 + Σ(0,536m + 0,045n)СmНn]. (4.15)
После этого можно определить массу дымовых газов (кг/м3) при сжигании природного газа:
. (4.16)
При сжигании твердого топлива масса продуктов сгорания (кг/кг) рассчитывается по другой формуле:
. (4.17)
Правообладателям!
Данное произведение размещено по согласованию с ООО "ЛитРес" (20% исходного текста). Если размещение книги нарушает чьи-либо права, то сообщите об этом.Читателям!
Оплатили, но не знаете что делать дальше?