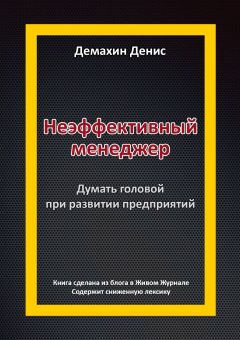
Автор книги: Денис Демахин
Жанр: Руководства, Справочники
Возрастные ограничения: +18
сообщить о неприемлемом содержимом
Текущая страница: 5 (всего у книги 17 страниц) [доступный отрывок для чтения: 6 страниц]
Нельзя отклоняться от намеченного курса: после принятия решения и утверждения плана действий любые обсуждения должны быть прекращены. Высказывать мнение допустимо исключительно о том, как именно реализовать принятое решение. Умри, но сделай.
Если ваш подчинённый не верит в какое-то дело и говорит об этом, то переубедите его, а не затыкайте.
Но легче заткнуть сотрудника, ведь в противном случае руководителю предстоит обосновать перемены вышестоящему начальству. А там спросят «Как же вы так планировали, что потом передумали? Для вас это шутки?»
Проблема в том, что львиная доля информации о задаче возникает в процессе ее выполнения, а вовсе не на этапе постановки. Новые вводные могут прямо указывать на то, что нужно отказаться от утвержденного плана действий или вообще от выполнения задачи.
4. Ставить несколько ответственных на одну задачу«Один не справится, второй подстрахует», – думает начальник
Нет, это так не работает.
Много ответственных на одну задачу – это рай для подчиненных. Каждый из них может ничего не сделать, задача будет провалена, и никто из них не будет виноват. Так уходили от ответственности под конец правления Сталина. Каждый нарком под каждым своим решением собирал визы еще двадцати. Если случался провал, всех наркомов разом не расстреляешь – поэтому к стенке не ставили ни одного из них.
5. Не назначать ни одного ответственного на задачуНа совещании изрекать задачи «в толпу». Сделать это, сделать это, сделать это. Не называть ни фамилий, ни должностей тех, кто именно это должен делать. На следующем совещании орать в ту же самую толпу: «Почему ничего не сделано?» Снова не называть фамилий и должностей, не обращаться ни к кому конкретно. Так по кругу до бесконечности. Классика.
6. Мыслить штампамиНапример, вбить себе в голову, что каждый сотрудник должен всё успевать в течение рабочего дня и что если он остается дольше, то это его явный недостаток.
Для рабочего с четко рассчитанной трудоемкостью и нормой на количество изготовленных деталей – это было бы справедливо. Но кто когда вообще нормировал работу инженерно-технического сотрудника? Вот и не надо путать кислое с длинным. То, что какой-то сотрудник трудится дольше, чем длится его рабочий день, может означать все, что угодно. Например, что объема работы изначально больше, чем на 8 часов в день. Так это или нет – надо изучать дополнительно. Делать поспешные выводы и с упрямством их отстаивать – плохая парадигма.
7. Иметь дежурную жопуНайти человека, который всегда во всем виноват. Причем, он просто «виноват» и всё. Без каких-либо дальнейших действий со стороны руководства в виде увольнения, изменения порядка работы, переопределения зон ответственности или любых других последствий.
Дежурная жопа появляется на производстве не потому, что у носителя этого звания нет яиц, а из-за их отсутствия у руководителя. Когда он боится высказать виноватому и предъявляет претензии тому, кому может.
Жопа может занимать какую-нибудь должность и нести формальную ответственность за коллектив или участок, но фактически не иметь полномочий. Но зачем руководитель вообще обвиняет в чем-либо дежурную жопу, если сам прекрасно знает, что это бесполезно? Ситуация не меняется и не изменится никогда?
Потому что когда возник какой-то косяк, надо же что-то сделать! Предпринять корректирующие действия! Ведь если вообще ничего не сделать, то остается дискомфортное ощущение незавершенности. А так хоть жопу поругает. И если вышестоящее начальство спросит у этого руководителя: «Вы предприняли меры, чтобы этого косяка больше не повторялось?», то он с чистым сердцем ответит: «Да, провел работу с персоналом».
Дежурную жопу не повысят, но ее и никогда не уволят. Ведь если бы хотели, то сделали бы это уже давно. Но кто тогда будет во всем виноват?
Глава 19. Раздельный сбор мусора как правильный и сильный принцип
Планету изрядно завалили пластиком – это вызывает тоску. Но вы можете кое-что сделать с этим.
Организуйте раздельный сбор отходов в масштабах своего предприятия. С необходимыми вещами вы справитесь без проблем: договоритесь с компанией по переработке отходов, поставьте контейнеры, проведите собрание. Это просто.
Но есть один решительный ход, на который осмелится не каждый, он не для слабаков:
Пусть все ваши сотрудники отдадут мусорное ведро из-под своего стола и ходят выбрасывать мусор до контейнеров в пределах каждой комнаты на самом видном месте и в коридорах.
Это напряжно: придется каждый раз вставать. Но в этом и смысл. Когда ведро рядом, лень вставать и нести бумагу в контейнер для бумаги, а пластик – в такой же для пластика. Всё идёт в бытовые отходы.
И чем мне это поможет?Ничем! На ходьбу будет тратиться время. Но это поможет планете.
Чтобы не внедрять доброе и вечное насильно, проведите в коллективе голосование и сделайте так, как проголосует большинство.
Если большинство за раздельный сбор мусора и отказ от урн, это подействует долговечнее любого тимбилдинга. Сотрудники будут ощущать, что они все объединены некой идеей.
Тогда они с большей готовностью поверят в «миссию компании», которая висит в рамочке на стене. Чтобы сотрудники поверили, что у вас на самом деле есть какая-то миссия, у вас должно быть что-то святое.
Ощущение причастности к этой идее может целиком поменять мировоззрение сотрудников. Как вариант: они начнут более осознанно приобретать пластик. Перестанут брать в магазинах пакеты, например. Или начнут более рачительно использовать бумагу на работе.
Часть 3. Методы совершенствования
Обычного описания каждого инструмента бережливки тут не будет. Это можно прочитать у других авторов, повторяться нет смысла. Исключение – система 5S, т.к. там я говорю то, чего не говорили другие.
Здесь будет только общий костяк, а потом только мой взгляд на методы совершенствования.
Вы не можете выучить один набор приёмов и везде его использовать. В одном месте подошло, в другом не подойдет. Контекст будет другой. Но вы можете повышать насмотренность, чтобы импровизировать успешнее, переосмыслять.
Глава 20. Бережливое производство (Lean)
Бережливое производство – это система управления, при которой продукция изготавливается в точном соответствии с запросами потребителей, как по качеству так и по количеству.
Для чего именно нужно БП:– Увеличение отдачи от капитала за счет сокращения запасов и сокращения времени с момента размещения заказа до момента выдачи клиенту.
– Обеспечение роста бизнеса посредством делегирования ответственности и высвобождения собственника или руководителя от текущих проблем.
– Снижение зависимости от ключевых специалистов и обеспечение быстрого процесса обучения.
– Использование внутреннего потенциала сотрудников и предприятия за счет вовлечения каждого в процесс совершенствования.
Принципы БП1. Ориентация на потребителя
В массовом производстве мы пытаемся угадать, что нужно рынку, производим этого как можно больше, и надеемся распродать. В бережливом производстве мы имеем на складах минимальный запас готовой продукции. И когда их раскупают, тогда и производим продукцию, чтобы восполнить этот запас. Ну или вообще работаем под заказ. То есть, сначала получаем заказы, и производим под них. Закупаем столько сырья, сколько нужно (под конкретные заказы). Кроме того, очень внимательно относимся к обратной связи от клиентов.
Сейчас удастся встретить мало предприятий, загружающих склады, а не работающих под заказ. Но так работали General Motors, Chrysler и Ford.
2. Поток вытягиванияБережливое производство – это вытягивающее производство. В массовом выталкивающем производстве стараются максимально загрузить оборудование, чтобы оно не простаивало, а производило как можно больше (пока есть из чего делать – делаем). Это создает огромные запасы как незавершенного производства, так и готовой продукции. Все эти запасы лежат без движения, ржавеют, теряются, устаревают морально и аккумулируют в себе деньги.
В вытягивающем производстве оборудование делает детали только тогда, когда с последующего производственного этапа приходит информация, что они там нужны (истощился минимальный запас). Система оповещения о том, что и на каком участке нужно производить, называется «канбан».
Через вытягивание сокращаются запасы сырья, незавершенного производства и готовой продукции.
В бережливом производстве всё совершенствование выстраивается от потока создания ценности (производственного потока), который перестраивается и балансируется. Делается всё возможное, чтобы он стал как можно более быстрым и оптимальным. Все остальные инструменты совершенствования вертятся вокруг потока и нужны для того, чтобы сделать совершенным именно поток создания ценности.
Фокусирование процесса совершенствования потока направляется расположением «узкого места». Концентрируется на нем. «Узкое место» – это некое ограничивающее общую производительность линии звено. После того, как узкое место улучшено, какое-то другое место теперь самое узкое.
«Lean» – это переводится не «бережливый». Это тощий, поджарый, стройный. Бережливо относиться можно к какой угодно системе производства. Но «Lean» – это именно тощий, лишенный жировых запасов.
3. Сокращение длительности выпуска заказаВсе, чем мы занимаемся, – это следим за временем между размещением заказа потребителем и получением денег за выполненную работу. Мы сокращаем этот промежуток времени, устраняя потери, которые не добавляют ценности (Тайити Оно, 1988).
Нужно добиваться того, чтобы с того момента, как клиент подал заявку до момента, когда он получил свой заказ, проходило как можно меньше времени.
В этом процессе нужно ориентироваться на три понятия: время цикла, время такта и время выполнения заказа.
Время такта – это расчетная величина, зависящая от величины спроса. Это частота, с которой готовые изделия ДОЛЖНЫ выходить с линии. То есть это цель, целевой значение. Также, это время, за которое конвейер должен делать одно перемещение (с одной рабочей станции до следующей).
Время цикла – это фактическое время выполнения операции одной (каждой в отдельности) рабочей станцией. Задача состоит в том, чтобы синхронизировать время цикла под время такта.
Время выполнения заказа – это длительность прохождения изделия по всему потоку от самого начала и до конца, через все рабочие станции. Через все времена цикла.
Массовое производство имеет очень короткое время цикла (выпускает как из пулемета), но очень длительное время выполнения заказа (каждая из единиц производится долго). помимо замораживания материальных средств в виде незавершенного производства это также очень снижает скорость производства редких марок продукции.
4. ГибкостьВ массовом производстве переналадка оборудования делается крайне редко – оборудование производит детали гигантскими партиями. В бережливом производстве следует изготавливать детали небольшими партиями (чтобы покупатели редких марок продукции не ждали долго), поэтому требуется часто переналаживать оборудование. Именно поэтому в БП очень развит инструмент SMED «Быстрая переналадка».
5. Устранение потерьДля того, чтобы сократить время цикла, а также снизить себестоимость, устраняют потери. Потери – это всё, без чего можно обойтись при производстве продукции. Или всё, что не добавляет продукту ценности. Прибыль повышается за счет устранения потерь на производстве.
Виды потерь– Перепроизводство – вся непроданная продукция, загромождающая склад готовой продукции;
– Излишние запасы – на них потрачены деньги, но они лежат без дела. Портятся, теряются. Требуют инвентаризации. Всё это лишние затраты;
– Ожидание – людей, деталей, продукции. Всё, что находится без дела, стоит без движения в очереди куда-то;
– Транспортировка – лишняя по времени и расстоянию;
– Лишние движения во время рабочих операций – не оптимизированная работа людей руками. Лишняя работа из-за несовершенства инструмента.
– Излишняя обработка – когда мы делаем то, что не нужно клиенту;
– Дефекты, брак;
– Нереализованный потенциал сотрудников – рацухи, которые они могут написать, но не пишут.
6. Внутрицеховая логистикаПоток создания ценности, а также потоки снабжения по возможности должны двигаться в едином направлении, исключая возвратные и пересекающиеся потоки. Длина путей перемещения также должна быть максимально сокращена. Для этого используется инструмент «диаграмма спагетти» (рисовать маршруты перемещений сотрудника по планировке цеха), с помощью которой анализируем все перемещения, после чего решаем, как их оптимизировать. Спагетти – это потому что внешне похоже на длинные макароны.
7. Всеобщее вовлечение в процесс совершенствования33Подробнее в книге «Кайдзен. Ключ к успеху японских компаний», Масааки Имаи
[Закрыть]
Для того, чтобы устранять 8 видов потерь, этим постоянно должны заниматься все сотрудники компании во главе с первым лицом. Вовлечение в этот процесс первого лица – это ключевое условие успеха. Для этого потребуется отказ от культуры порицания в пользу открытого признания проблем. Отказ решать проблемы методом «найти и наказать виновных».
Иначе ваш процесс совершенствования поломается о то, что ваши сотрудники будут совершенствовать только свою незаменимость. Чтобы их не уволили.
Ключевая особенность совершенствования – непрерывность. Нельзя перестроить предприятие, а потом к этому вопросу не возвращаться. Проект – это что-то имеющее начало и конец. А процесс совершенствования должен быть вектором. Вектор имеет начало, но не имеет окончания.
Как часто нужно тренироваться, чтобы быть спортсменом? Постоянно. Как часто нужно повышать свою квалификацию чтобы быть профессионалом? Постоянно. Также и с производством. Японцы в этом плане впереди всей планеты, и у них краеугольный камень это постоянное совершенствование процессов. Нон-стопом десятилетиями.
Как японцы считают порочно: повседневная работа + совершенствование.
Как японцы считают правильно: повседневная работа = совершенствование.
Совершенствование должно быть неуклонным. Нельзя 1 раз сделать что-то здоровое и жить до 100 лет. Правильный образ жизни нужно поддерживать на протяжении всей жизни непрерывно.
8. Иди в гембу (иди и смотри)Важнейший принцип совершенствования и вовлечения. Он заключается в том, что начальники не должны заниматься развитием предприятия из кабинетов. Они должны идти в цех и смотреть, как выполняется работа. Или идти и смотреть по месту, где происходит брак. Искать причину его возникновения. Японский начальник всегда идет на передовую. Туда, где идет сама работа.
Придя на место создания ценности, нужно искать корневые причины появления проблем. Не дергать верхушки, а копать до самого корня. Для этого есть метод «5 почему». 5 раз или больше подряд задав вопрос «почему?» рабочему на участке, можно выяснить, «откуда ноги растут». И принять действенные меры.
Это что касается потока создания ценности. А вообще, проблемы нужно искать не только в гемба, но и в администрации.
9. Ориентированность на процесс, а не на результатУ нас могут похвалить, если как-то обманул систему и выкрутился из сиюминутной проблемы. Потырил детали из какого-то другого заказа (который отгружать через 2 дня, а не сегодня), или руками влез в приоритет работы участка изготовления металлических деталей для повторного изготовления каких-то деталей, потерянных на своем заказе, который сегодня отгружать.
Заказ с грехом пополам отгрузили, и все такие «фух!» – выдохнули. Сейчас нужно разобраться, почему так произошло на этом заказе. Как потеряли изготовленные детали, и почему вовремя не приехали покупные. Но подождите-ка! Мы только что забрали детали из заказа, который отгружать послезавтра! Теперь нужно срочно думать, как его отгружать. Кроме того, мы вмешались в приоритет участка металлообработки, и он теперь работает с запозданием, и с этим тоже нужно что-то срочно делать! Некогда сейчас заниматься выяснениями, почему так произошло. Да и потом: всё же получилось. Результат же есть. А это – самое главное! (нет).
В бережливом производстве нужно именно постоянно совершенствовать процесс, и тогда уже он будет давать стабильный результат.
10. Отказ от массового контроляОтказ ставить сотрудника ОТК после каждого станка. Вместо этого возложение обязанностей с проверкой на самих рабочих на последующих стадиях выполнения работы. Такое возможно только в культуре совершенствования, где виновников не наказывают и не штрафуют, а просто пытаются выяснить, что вызвало брак и устранить возможность появление брака в будущем. Например, при помощи внедрения способов защиты от непреднамеренных ошибок (Пока-ёке).
Тогда рабочие не будут бояться сообщать о бракованных деталях друг друга, и сотрудники ОТК не будут нужны в таком количестве.
Это лучше, чем проверять всю продукцию в самом конце, т.к. в конце на нее затрачено уже гораздо больше ресурсов, чем если бы брак был обнаружен на самых ранних этапах. Поэтому при возникновении брака на одном из участков конвейер останавливают, пока не выяснят, в чем дело. Чтобы не гнать брак дальше.
11. ВизуализацияЧтобы вовлеченные сотрудники могли улучшать процессы, процессы должны быть визуальны, прозрачны, понятны и стандартизированы. В мутной воде совершенно непонятно, что происходит и как всё устроено, поэтому нет идей, как это улучшить. Не видно потерь. Цель в том, чтобы любой человек, придя на участок, не задавая вопросов понял, как тут всё устроено, как должно работать, и не происходит ли нарушений.
12. Статистическое управлениеБережливое производство в своих решениях опирается на анализ и факты, а не эмоции и слухи. А факты – это статистика. Руководство должно принимать решения на основании статистических данных о производстве.44
Начать можно с книги «Статистические методы повышения качества», Хитоси Кумэ
[Закрыть]
Метод составления описан в книге «Учитесь видеть бизнес-процессы», Майк Ротер, Джон Шук
[Закрыть]
Основной инструмент по выявлению потерь. Можно сказать, что это огромная фотография рабочего дня всего процесса. Мы зарисовываем всё, что делается. Фиксируем время, информационные потоки, количество персонала на операциях, простои, дефекты и другую важную информацию. На основании всего этого мы делаем одну большую карту, созерцая которую ищем возможности для улучшений.
Глава 21. Мой подход к преподаванию бережливого производства в университете
Все читают лекцию по презентациям на проекторе, но их слайды очень перегружены и похожи на страницу газеты.

Моя презентация состоит из серии таких слайдов
Минимализм. Только тема. Лицо автора для лучшего запоминания. Фраза-триггер для интереса. И дальше моя лекция на тему и диалог со студентами. Можно ничего не записывать, т.к. в левом нижнем углу каждого слайда есть ссылка, скрытая за QR-кодом, по которой можно прочитать все рассказываемые мной на этом слайде материалы. Зачем писанина, когда там уже всё написано? Гораздо лучше обратить всё внимание на преподавателя, а не на тетрадь.
Самым последним слайдом идет перечисление всех предыдущих слайдов. Это на случай если останется время, и можно будет вернуться к одной из предыдущих тем и рассказать про нее поподробнее.

Таким образом вся подготовка приобретает вот такую структуру
Горизонтальная линия – это то, что происходит на лекции. Легкая прогулка по лужайке. А то, что под землей – это самостоятельное изучение. Благо, все ссылки мной предоставлены. Причем, за каждой статьей стоит ещё какая-то книга, но книги идут еще глубже под землю. Информацию нужно рыть, знаете ли.
В итоге можно заметить, что самое мощное растение черпает силы из наиболее глубоких слоев почвы.
Мой подход нацелен на то, чтобы пробудить у студентов интерес к самообразованию, пробудить любопытство. На лекциях ведь всему не научат. Конечно, есть слой почвы еще глубже, чем книги. Это практический опыт.
Как обучать бережливому производствуФормат, который я часто видел у других. Создают презентацию и стремятся отчитать ее от корки до корки. Возникающие в процессе вопросы принимают очень нехотя, а иногда даже сопровождают фразой «давайте все вопросы в конце, а то мы так ничего не успеем».
Специфика Лина в том, что когда вы набираете аудиторию для проведения обучения, вы никогда не можете знать заранее, кто из присутствующих ничего не слышал о Лин, а кто знает больше вас.
В связи с этим стандартная вводная презентация кому-то покажется скучной, а кому-то слишком оторванной от реалий этого предприятия.
Поэтому в самом начале я всех предупреждаю, что меня можно перебивать вопросами, дополнениями или примерами. Такое можно сказать, когда совершенно не боишься того, что знаешь в Лин всего одну тропинку, и по ней и хочешь провести презентацию, а неожиданным вопросом могут заставить свернуть куда-то в сторону, а там «тёмный лес».
Я составляю презентацию так, что в самом начале идет самое важное в Lean, а к концу остаются слайды со все менее и менее важными темами. И что если в ходе длительных обсуждений мы выйдем за временной лимит, мы сможем совершенно безболезненно обрубить концовку, и ничего от этого не потеряем. Соберем все сливки.
Так все присутствующие будут вовлечены, а опытные в Лине коллеги не только не будут скучать, но и смогут взять и подхватить какую-то тему и дорассказать за меня то, что им показалось важным.
Этот подход позволяет наиболее близко подвести тему lean к конкретным примерам, и позволяет рассказать слушателям именно то, что они больше всего хотят узнать. Тема Лин очень объемна, и какие именно аспекты осветить – вопрос для обучения и вовлечения первостепенный.
Данный подход вызвал очень положительный отклик и живые дискуссии, а также предложения по улучшению, которые рождались прямо по ходу. После этого слушатели писали на почту с просьбой выслать материалы. Из-за этого подхода тема Лин начинает восприниматься слушателями актуальной, применимой, и интересной.
Правообладателям!
Данное произведение размещено по согласованию с ООО "ЛитРес" (20% исходного текста). Если размещение книги нарушает чьи-либо права, то сообщите об этом.Читателям!
Оплатили, но не знаете что делать дальше?