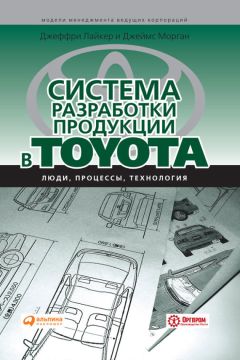
Автор книги: Джеффри Лайкер
Жанр: Зарубежная деловая литература, Бизнес-Книги
Возрастные ограничения: +12
сообщить о неприемлемом содержимом
Текущая страница: 9 (всего у книги 36 страниц) [доступный отрывок для чтения: 12 страниц]
Нередко цель бережливого производства определяют как устранение потерь. Но борьба с муда – это еще не все. Подлинно бережливое мышление не ограничивается устранением муда, оно нацелено на ликвидацию трех взаимосвязанных типов потерь: муда, мура и мури (3M).
1. Муда – отсутствие добавления ценности. В муда входят все семь видов потерь в производственной системе Toyota и аналогичные потери при разработке продукции, о которых рассказывалось выше. К муда относятся любые действия, которые увеличивают время выполнения заказа и неоправданно повышают производственные затраты.
2. Мури – перегрузка. В определенном смысле представляет собой противоположность муда. Мури заставляет машину, процесс или человека работать на пределе возможностей. Перегрузка людей угрожает их безопасности и вызывает проблемы с качеством. Перегрузка оборудования ведет к авариям и дефектам. Перегрузка процесса порождает длинные очереди, что увеличивает время выполнения заказа при разработке продукции, или заставляет «срезать углы», что ведет к появлению ошибок на более поздних этапах и приводит к переделкам и доработкам.
3. Мура – неравномерность. В традиционных производственных системах поток работ неравномерен. Временами работы больше, чем могут выполнить люди и оборудование, а порой ее недостаточно. Инженерам хорошо знакома спешка при завершении отдельных этапов проекта (например, сдаче опытного образца или запуске нового изделия в производство). Такие авралы чередуются с относительно спокойными периодами. Причина неравномерности – неправильно составленный график или колебание объема работ, вызванное внутренними проблемами, например отказами компьютерных систем или недостатком информации. Муда – следствие мура. При неравномерных объемах производства необходимо, чтобы количество наличных ресурсов (оборудования, материалов, людей) соответствовало максимальному объему производства – даже если его средний уровень значительно ниже.
Начиная применять методы бережливого производства, в большинстве компаний выбирают какой-нибудь процесс с неравномерным графиком работы и бросают все силы на войну с потерями, устраняя муда. Почти всегда эта работа начинается с сокращения объема запасов и связывания отдельных операций. Далее следует перераспределение объема работ и высвобождение людей. Затем осуществляется реорганизация рабочего места для устранения лишних движений. После этого представители компании запускают систему вновь. Однако, к их смятению, «усовершенствованная» система страдает от чудовищных перегрузок. Люди оказываются загруженными работой сверх меры, количество отпусков по болезни резко возрастает, оборудование выходит из строя чаще, чем прежде, и вскоре менеджмент приходит к выводу, что, бережливое производство не работает. В этих компаниях не понимают, что прежде чем браться за внедрение бережливого производства, нужно стабилизировать систему и обеспечить равномерность, которая позволит инструментам бережливого производства работать должным образом.
Бережливое мышление помогает относительно легко выявлять и устранять потери в системе. Но чтобы создать выровненный поток работы, требуется куда больше усилий. Многие компании зацикливаются на ликвидации муда, поскольку это обеспечивает краткосрочное снижение затрат. Порой дело доходит до крайностей – например, объем инженерно-технических работ сокращается на 10–15 %. Затраты снижены – значит, компания устранила «потери». Но так ли это? С точки зрения бережливого мышления более сложная задача – это неуклонное, кропотливое устранение мури и мура, то есть управление и совершенствование перегруженных, неравномерно работающих систем. Сокращение объема инженерно-технических работ не решит ни той ни другой задачи. Напротив, оно неизбежно приведет к перегрузкам и неравномерности на других этапах процесса.
Большинство людей считают, что непрерывный поток – это выровненный поток. На основе такой посылки принимаются ошибочные решения, которые помогают устранить «потери» в одном виде деятельности, но уходят из виду потери на других этапах процесса. Так, создав поток единичных изделий и избавившись от запасов на нескольких рабочих местах, вы не устраните резкие колебания темпа работы и нестабильность номенклатуры продукции. Этого недостаточно, чтобы создать непрерывный поток. Таким образом мы только получим неравномерный поток единичных изделий в режиме «старт-стоп» с чередованием перегрузки и недогрузки и риском сбоев. В таких условиях вряд ли удастся производить качественную продукцию, обеспечить высокую производительность или заниматься непрерывным совершенствованием. Непрерывный поток означает, что в потоке создания ценности устраняются все виды деятельности, не добавляющие ценности, и продукт беспрепятственно проходит путь от разработки концепции до поставки потребителю.
Факторы, способствующие и препятствующие потоку: подход теории очередейНа данном этапе важно понять, почему семь видов потерь, перечисленные выше, распространены так широко. Ни одна компания не поймет, как избавиться от потерь, пока не выявит их коренные причины. Если рассматривать процесс разработки продукции как предприятие, выполняющее заказы по обработке знания, можно сделать ряд важных выводов о первопричинах потерь, опираясь на широко известные представления теории очередей. Теория очередей помогает увидеть, как традиционные подходы к разработке продукции усиливают вариабельность, присущую данному процессу, и порождают огромное количество потерь. Наибольшее число проблем порождают следующие методы работы.
• Центры разработки продукции комплектуют крупные партии материалов по завершении отдельных этапов разработки.
• Уровень производительности центров разработки продукции постоянно колеблется, а представление об их реальных возможностях отсутствует. Это порождает постоянные перегрузки в системе.
• Объем проектировочных работ непредсказуем и постоянно растет, в результате работа занимает все рабочее время всех инженеров, участвующих в реализации проекта.
• Цикличность объема работ – чередование затишья и авралов, которое сопровождается чудовищной перегрузкой системы, – значительно увеличивает время выполнения заказов и мешает уложиться в намеченные сроки.
• Низкий уровень качества работы и несоблюдение графика порождает высокую вариацию сроков завершения работ и поступления новых заданий.
Чтобы понять, какие причины ведут к появлению такого рода потерь, рассмотрим процесс разработки продукции как систему, где новые поступления (заказы на работу) формируют требования на ограниченные ресурсы, которые описываются терминами пребывания в системе, ожидания и обслуживания. Мы проанализируем традиционные методы разработки продукции в свете основных понятий теории очередей, которые хорошо разработаны применительно к производству и прекрасно освещены в книге «Природа предприятия» (Factory Physics, Spears and Hopp, 1996).
• Правило комплектования партий: «Продолжительность цикла на маршруте примерно пропорциональна размеру партии, обрабатываемой на данном маршруте».
• Правило нарастания вариабельности: «Вариабельность на более ранних этапах маршрута порождает большие объемы незавершенного производства и сильнее влияет на время цикла, чем равноценная вариабельность на более поздних этапах маршрута».
• Правило загрузки: «Если загрузка системы повышается в отсутствие иных изменений, наблюдается резкий нелинейный рост средней продолжительности цикла».
• Правило вариабельности: «При неизменном состоянии повышение вариабельности всегда ведет к увеличению среднего времени цикла и объемов незавершенного производства».
Эти принципы помогают понять первопричины основных видов потерь в системе разработки продукции. Правило комплектования партий говорит о том, что если процесс разработки продукции организован как цепочка передаточных пунктов, в которых процесс приостанавливается, а разработка продукции осуществляется при помощи множества отдельных подразделений (например, функциональных), которые пропускают через себя крупные партии информации, – объемы незавершенного производства и время выполнения заказов резко возрастают. Возьмем, к примеру, централизованный отдел технического анализа, который, получая множество запросов на проведение расчетов, выдает результаты крупными партиями. Естественно, это ведет к увеличению времени выполнения заказа. Замените технический анализ проверками высшего руководства, работой дизайнерской студии, разработкой кузова, изготовлением опытных образцов, испытаниями, автоматизированным проектированием или разработкой инструментальной оснастки, и вы увидите, что правило комплектования партий применимо к выполнению любых заказов.
Хорошо известно, что превышение производительности системы негативно сказывается на ее эффективности. Тем не менее при планировании разработки продукции производительность системы учитывается крайне редко. Кривая показывает, что при увеличении загрузки системы время выполнения заказа растет (рис. 5–3), при этом когда коэффициент загрузки достигает 80 %, оно начинает расти почти по экспоненте, то есть дальнейшее увеличение нагрузки вызывает непропорционально большее увеличение длительности всего процесса. К сожалению, обычно уровень загрузки систем разработки продукции нередко намного превышает показатель 80 %.

На рис. 5–4 показано, что негативные последствия этой взаимосвязи усугубляет высокая вариабельность, изначально присущая процессу разработки продукции.

Вариабельность – определяющий фактор низкой эффективности системы. К сожалению, вариабельность характерна для большинства традиционных систем разработки продукции. Нас интересуют два вида вариабельности.
1. Вариабельность выполнения задач. Имеются в виду различия в методах и продолжительности выполнения конкретных задач при разработке продукции.
2. Вариабельность поступления задач – временной интервал между фактическим и запланированным поступлением работы. Эту вариацию часто порождают вариабельность выполнения задач и ресурсные ограничения.
Если в системе присутствуют оба вида вариации, это приводит к стремительному росту общей вариации, что наносит огромный ущерб эффективности системы. Более того, вариация, существующая на ранних этапах процесса, существенно увеличится на дальнейших этапах. Любые усилия, направленные на устранение вариабельности в начале процесса (стадия разработки концепции, в LPDS опирается на принцип 2), окупаются с лихвой. Поэтому управление вариацией и постоянный контроль производительности системы чрезвычайно важны для повышения эффективности разработки продукции.
Пожалуй, проще всего понять эти феномены с помощью следующей аналогии. Всем нам случалось попадать в дорожные пробки. Движение сначала останавливается, а затем машины трогаются с места, но едут с черепашьей скоростью. Проехав так не одну милю, мы, наконец, узнаем, почему возник затор. Оказывается, произошла пустяковая авария, из-за которой две машины и автомобиль полиции заняли одну полосу трехполосной автострады (см. рис. 5–5). Но почему это полностью блокировало движение? Если бы условия были иными (например, на дороге было бы меньше машин, то есть ее загрузка была бы ниже), помехи движению на одной полосе не вызвали бы пробки. Избыточная пропускная способность автострады помогла бы нейтрализовать вариацию. Однако, если автострада загружена на 80 % и более, «изъятие из оборота» одной полосы порождает чудовищные пробки. В этом случае вариабельность (неожиданные столкновения машин и интенсивное движение в часы пик) приводит к перегрузке системы в целом и длительному времени выполнения заказа (машины движутся очень медленно).

Убедительные доказательства эффективности применения принципов теории очередей к разработке продукции приводит Пол Адлер (Adler et al., 1996). Вместе с другими исследователями он изучил несколько проектов по разработке продукции и подтвердил общий вывод: реализация проекта идет без помех в периоды, когда объем работ невелик и люди не слишком загружены. Однако, когда коэффициент загрузки возрастает и достигает 70–80 % производительности системы, даже небольшой рост объема работ резко увеличивает время выполнения заказа. Любая вариация в процессе (например, отсутствие или запаздывание важных данных и неправильная информация) в сочетании с увеличением объема работ вызывает сбой в системе. Чрезмерная загрузка ресурсов при разработке продукции в сочетании с высокой вариабельностью процесса – главная причина длительного времени выполнения заказов, задержек при реализации проекта и даже проблем с качеством. Регулируя загрузку системы и используя базовые инструменты снижения вариабельности времени выполнения задач и вариабельности поступления задач, компаниям удается постепенно сократить время выполнения заказа и повысить производительность системы в целом (Adler et al., 1996).
Принципы теории очередей почти всегда помогают выявить первопричины семи видов потерь при бережливой разработке продукции. На рис. 5–6 показана взаимосвязь потерь и порождающих их факторов. Разумеется, здесь перечислены далеко не все причины потерь и обозначены далеко не все взаимосвязи между потерями и их причинами. Однако данный рисунок дает наглядное представление о системных причинах, которые можно устранить, реорганизовав систему разработки продукции.

Компаниям, которые продолжают рассматривать процесс разработки продукции с традиционной точки зрения, то есть как неконтролируемую цепь разрозненных, неожиданных событий, придется и впредь занимать оборонительную позицию и бороться с вариабельностью и проблемами загрузки мощностей в режиме тушения пожаров. В Toyota никогда не считали, что проблемы вариабельности неизбежны или не поддаются контролю. Далее мы расскажем о действенных средствах, которые позволяют Toyota устранять первопричины потерь в процессе разработки продукции и обеспечивать поток процесса. Подробный анализ показывает, что многие методы, применяемые Toyota с самого начала процесса, прекрасно согласуются с основными положениями теории очередей.
Выровненный поток вместо неразберихи: кенто и потокToyota атакует потери с самого начала процесса бережливой разработки продукции. Третий принцип LPDS гласит: обеспечить правильный старт процесса разработки, чтобы на ранних стадиях проектирования досконально изучить альтернативные варианты. В предыдущей главе подчеркивалось, что правильный старт чрезвычайно важен для выравнивания объема работ. Управление портфелем, планирование цикла и жесткий график использования общих ресурсов на входе процесса – вот предварительные условия выравнивания объема работ в системе бережливой разработки, которая имеет дело со множеством продуктов. Решающее значение для создания потока на этапе выполнения работ в Toyota имеет период кенто, когда межфункциональные команды работают над предупреждением возможных сбоев, вырабатывают базовую стратегию проектирования и выстраивают иерархию целей и задач, ориентированную на концепцию главного инженера. Как отмечалось выше, этап кенто позволяет взять под контроль или изолировать значительную часть вариации при разработке продукции, что позволяет Toyota сосредоточиться на результате.
Согласуя цели и задачи функциональных подразделений и заблаговременно разрабатывая контрмеры, Toyota обеспечивает поток процесса и синхронизирует работу функциональных подразделений. Такой подход помогает компании сокрушить смертельного врага потока при разработке продукции – незапланированные запоздалые технические изменения. Такие изменения дезорганизуют процесс, повышают затраты и снижают качество. Разумеется, хотя в Toyota стараются избегать технических изменений после выпуска комплекта итоговой документации, отдельные исправления и доработки при создании столь сложного продукта, как автомобиль, неизбежны. Чтобы минимизировать негативный эффект этих изменений, Toyota подчиняет их общей логике процесса.
Роль логики процессаВ первом приближении логика процесса определяет последовательность задач, которые нужно выполнить, чтобы создать новый продукт и сами задачи. Она отражается в пошаговом описании процесса, на основе которого составляется график работ. Логика процесса диктует, кем и когда выполняются конкретные виды работ, какие решения нужно принять проектной команде на каждом этапе процесса разработки продукции. Речь идет не о детальном описании предстоящей работы, а об общей схеме на макроуровне, которая координирует действия всех участников процесса. Подробные инструкции по выполнению работ создаются и корректируются функциональными подразделениями, которые досконально знают тот или иной процесс. Централизованное управление сводится к незначительному количеству необходимых необременительных проверок. Чтобы изложить требования к процессу разработки продукции на макроуровне, достаточно менее 200 одностраничных карт, которые покажут общее состояние проекта и послужат ранним предупредительным сигналом в случае возникновения проблем. Все участники знают эти требования и подчиняются им. Сама по себе логика процесса не может обеспечить поток, но ее несостоятельность вызывает необходимость переделок и доработок, порождает потери и тем самым препятствует потоку.
Распространенное упущение при непродуманной логике процесса – плохая синхронизация последовательно выполняемых задач. Так, если технологи начинают работать с проектными данными до окончательного утверждения конструкции, неизбежные технические изменения сведут плоды их трудов на нет. Другой пример: в ряде испытаний и проектно-конструкторских работ не предусматривается достаточно времени на анализ результатов испытаний и разработку контрмер. Последний пример нарушения логики процесса: команду принуждают принимать решения или брать на себя обязательства в отсутствие достаточного количества достоверной информации (Ward et al., 1995). Инженеры, удрученные нарушением логики процесса, часто пытаются решить проблемы обходным путем, что увеличивает вариацию в системе разработки продукции и создает дополнительные помехи потоку.
При разработке продукции в Toyota составление графиков начинается с изучения логики процесса и поэтапных требований, что позволяет сбалансировать потребности всех проектов. Во-первых, графики составляются таким образом, чтобы поддерживать равномерную загрузку ресурсов. Во-вторых, разрабатываются общие графики проектирования всех подсистем автомобиля, где учитывается содержание и продолжительность работ. Компания составляет отдельные графики для трансмиссии, шасси и корпуса кузова, которые позднее сводятся воедино. Toyota оценивает каждый новый продукт и потребности производства с учетом объема работ по каждой из этих подсистем. Объем работ определяет сроки завершения этапов для каждой подсистемы, а высокоуровневый график обусловлен изменениями в отдельных подсистемах.
Макроуровневая логика процесса Toyota отличается изящной простотой. Она обеспечивает централизованное управление и разумное распределение ответственности, позволяя избежать потерь, связанных с громоздкими сводными планами работ в традиционных системах разработки продукции, где чудовищная сложность графиков часто мешает их соблюдению.
Выравнивание объема работ, планирование цикла и распределение ресурсовВ большинстве компаний разработка продукции – это циклический процесс, и попытки выровнять объем работ могут свести с ума. Однако без этого нельзя добиться эффективного использования ресурсов и ускорить поставку товара на рынок. Выравнивание объема работ должно предшествовать выполнению работы; в процессе бережливой разработки продукции оно предшествует определению облика. На самом деле оно начинается одновременно с планированием ассортимента портфеля продуктов и ресурсов, которое предваряет выполнение работы.
Планирование нового продукта начинается с анализа эффективности существующего портфеля продуктов. Задача такого анализа – выявить потенциальные возможности и упущения и решить, какие продукты следует начать разрабатывать. План цикла – документ, в котором указаны сроки разработки конкретных продуктов. Поскольку этот план определяет потребности системы разработки продукции в ресурсах, важно, чтобы он был относительно стабилен. Однако экономические факторы и острая конкуренция могут сделать поддержание стабильности очень непростой задачей. Расстановка сил на рынке стремительно меняется, и чтобы выжить, компания должна уметь быстро реагировать на изменение условий. Циклические всплески и спады спроса на ресурсы наносят ощутимый ущерб системе разработки продукции. Острота этой проблемы напрямую связана с масштабами деятельности организации. Чем шире ассортимент продукции компании, тем серьезнее проблема. Toyota решает эту проблему несколькими способами.
Правообладателям!
Данное произведение размещено по согласованию с ООО "ЛитРес" (20% исходного текста). Если размещение книги нарушает чьи-либо права, то сообщите об этом.Читателям!
Оплатили, но не знаете что делать дальше?