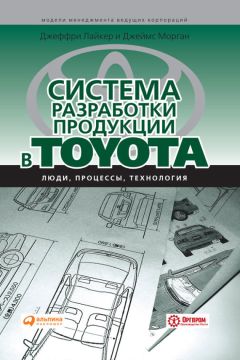
Автор книги: Джеффри Лайкер
Жанр: Зарубежная деловая литература, Бизнес-Книги
Возрастные ограничения: +12
сообщить о неприемлемом содержимом
Текущая страница: 12 (всего у книги 36 страниц) [доступный отрывок для чтения: 12 страниц]
Любопытно, что многие проектно-конструкторские стандарты Toyota не содержат конкретных указаний «делай то, не делай это». Чаще стандарты устанавливают соотношения и описывают физические процессы. Используя стандарты типа «если, то», инженеры Toyota могут свободно и самостоятельно творить, соблюдая требования бережливого производства. Не ограничивая инженеров жестко заданными «точечными» параметрами, проектно-конструкторские стандарты помогают выявлять оптимальный комплекс решений.
Проектно-конструкторские стандарты встроены в набор подробных контрольных листков по отдельным деталям и процессам, выражаются в использовании общих компонентов, стандартных подсистем и унификации конструкции автомобиля. Об эффективности стратегии унификации конструкции рассказывалось в главе 4. Далее мы остановимся на ключевом инструменте стандартизации разработок – инженерных контрольных листках. Глава 15 иллюстрирует эту концепцию конкретными примерами и рассказывает о кривых компромиссных характеристик и их использовании для выявления комплекса оптимальных решений.
Разумеется, инженерные контрольные листки – не изобретение Toyota. Скорее всего они появились в Toyota вместе с главными инженерами, которые пришли в компанию из авиационной промышленности, переживавшей упадок (см. главу 7). Контрольные листки предназначены для того, чтобы не забыть сделать определенные вещи. В зависимости от подхода к их применению они могут быть весьма эффективными или абсолютно бесполезными. Контрольный листок будет полезен, если строго соблюдать порядок его заполнения и регулярно обновлять информацию. В противном случае от него нет никакого толку. К сожалению, во многих компаниях не налажены ни дисциплина внесения корректив в контрольные листки, ни их эффективное использование.
В идеале в контрольном листке по проектно-конструкторским работам собраны представления о правильных и ошибочных методах работы, накопленные компанией за долгие годы. Они включают сведения о заданных рабочих характеристиках и критических зонах сопряжения деталей, параметры, определяющие качество, требования к технологичности и стандарты, позволяющие широко использовать единые компоненты. Контрольные листки Toyota наглядны и продуманы до мелочей. В них отражены все аспекты работы и особенности конкретных деталей. Тому, кто не знает, какой тщательности Toyota требует от своих инженеров, они могут показаться чересчур подробными. Контрольные листки для сложных деталей включают сотни параметров. Любопытно, что хотя контрольные листки весьма подробны и содержат массу узкоспециальной информации, большинство инженеров, с которыми мы беседовали, наизусть знали контрольные листки не только по собственным, но и по сопряженным деталям, и по соответствующим производственным процессам. Это свидетельствовало о том, что они пользуются данным инструментом давно и регулярно и чувствуют себя хозяевами происходящего.
Хотя практика проектно-конструкторских работ и имеет научную основу, по сути это искусство, которое опирается на неявное знание, приобретаемое опытом и размышлениями. Разработчик оценивает множество сложным образом взаимодействующих переменных и далеко не всегда может предсказать лучшее решение заранее. Этот навык нарабатывается, а его развитию способствует философия кайдзен, согласно которой обучение – это бесконечный процесс, поскольку всегда есть возможность узнать больше. Стимулом для кайдзен при выполнении проектно-конструкторских работ служит непреходящее стремление к совершенству. Именно оно заставляет систематически обращаться к контрольным листкам, проверять свою работу и совершенствоваться.
Отсутствие стандартизации мешает компании учиться на собственном опыте и осваивать бережливое мышление. Любая компания, которая пытается внедрить те или иные новшества, не занимаясь стандартизацией, просто блуждает по лабиринту. Опираясь на голословные утверждения, она повторяет одни и те же ошибки и выбирает из огромного количества вариантов тот, который, как выясняется позднее, уже использовался ранее. В Toyota разработка продукции базируется на систематическом научном подходе. Здесь проверяют, оценивают, стандартизируют, совершенствуют и вновь проверяют, строго придерживаясь цикла «планируй – делай – проверяй – воздействуй», с которым десятки лет назад компанию познакомил Деминг. Toyota неустанно стандартизирует передовые практики сегодняшнего дня. Стандарты корректируются по мере накопления новой информации и нового опыта, поэтому закрепленные в них методы остаются передовыми.
Стандарты встроены в контрольные листки, которые в Toyota применяются на всех этапах разработки, начиная с дизайна и заканчивая запуском в производство. Прорабатывая различные варианты решений совместно со старшими инженерами отдела разработки кузова и технологического отдела, дизайнеры постоянно обращаются к контрольным листкам по конструкции и процессу, обсуждая каждую деталь, пока не выявят самый подходящий вариант. Таким образом, Toyota удается создавать технологичные продукты с первого раза, тогда как инженеры NAC обычно анализируют почти готовые конструктивные решения с учетом сиюминутных требований, что неизбежно ведет к изменениям на более поздних этапах. Перед запуском автомобиля в производство контрольные листки помогают проверить точность штампов и инструмента и убедиться, что инструменты, штампы и производственное оборудование обеспечивают заданные характеристики узлов и деталей.
Все это означает, что в Toyota используется огромное количество контрольных листков. Они содержат информацию по каждой детали, каждому правилу, каждому стандартному способу обработки деталей и каждому диапазону приемлемых и недопустимых значений. Любой инженер Toyota имеет сборники стандартов, с которыми сверяется, оценивая каждую деталь каждого узла. Рассказывая о структурированной и систематической работе с контрольными листками на семинарах или в ходе аудиторных занятий, авторы слышали немало любопытных и неожиданных замечаний. В любой аудитории кто-нибудь обязательно задаст следующий вопрос:
Не пора ли сделать контрольные листки электронными? Мы слышали про этот метод Toyota и планируем усовершенствовать его, создав интерактивную базу данных с системой перекрестных ссылок. Эта база данных, включающая все стандарты, будет доступна пользователям корпоративной интрасети. У нас есть подразделение, которое готово разработать такую базу данных на самом современном уровне. Делается ли что-то подобное в Toyota?
На этот вопрос трудно ответить однозначно. Во-первых, нужно сказать, что Toyota уже сделала определенные шаги в этом направлении и перевела большую часть контрольных листков и стандартов в электронный формат. Во-вторых, создание электронной базы данных не гарантирует успеха и не решает главных проблем, а значит, такая база данных вполне может оказаться бесполезной.
На самом деле то, как создаются и обновляются контрольные листки – на бумажных носителях или в электронном виде, – вторично. Куда важнее решить, как распределять роли и обязанности. Кто заполняет контрольный листок? Кто его применяет? Каковы конкретные обязанности того, кто отвечает за использование контрольных листков и их обновление? В Toyota применение контрольных листков определяется основным принципом функционирования организационной структуры (она рассматривается в главе 8): «Работа в команде – важнейший фактор обеспечения высокого качества, однако за любое дело должен отвечать конкретный сотрудник». Ответственность за контрольные листки возлагается на функциональные группы, которые занимаются отдельными подсистемами.
Так, начальник группы проектирования дверей отвечает за обновление информации в контрольном листке по проектированию дверей и следит, чтобы этот контрольный листок использовался всеми разработчиками. За контрольные листки по дверям совместно отвечают отдел разработки кузова и отдел организации производства. Начальник группы из отдела организации производства отвечает за контрольные листки, в которых описана технология обработки деталей двери и конструктивные особенности, обеспечивающие их технологичность. В начале нового проекта инженер, отвечающий за разработку дверей, запрашивает последнюю версию контрольного листка в отделе организации производства и изучает его наряду с контрольным листком отдела разработки кузова. Занимаясь проектно-конструкторской работой, он обязан учитывать требования обоих листков.
Таким образом, за использование и обновление контрольных листков отвечают те, кто применяет их в работе. С точки зрения бережливого мышления эта обязанность не может возлагаться на подразделение информационных технологий. За контрольный листок отвечают не «инженеры вообще», а вполне определенный инженер, разрабатывающий конкретную деталь автомобиля. Именно он должен координировать усилия всех специалистов, работающих над данной деталью, и включить накопленные знания, информацию, опыт – назовите это, как хотите, – в соответствующий контрольный листок.
В главе 5 рассказывалось, как Toyota реализует стратегию гибкого регулирования производительности, привлекая дочерние компании, находящиеся под ее полным контролем, и используя резерв квалифицированных специалистов, которые в нужный момент подключаются к реализации проекта. Проектно-конструкторские стандарты и строго регламентированный процесс позволяют инженерам и чертежникам дочерних компаний не тратить времени на раскачку. Чертежники специализируются на отдельных деталях и отлично знают соответствующие стандарты. Они умеют применять контрольные листки, выполнять сечения и использовать стандартные компоненты с учетом пространства проектных параметров – оно определяется с помощью сканирования поверхности глиняной модели и чертежей кузова K4, – для окончательной проработки конструкции автомобиля с целевыми характеристиками. При необходимости они могут оставить неизменной апробированную геометрию детали, чтобы сохранить технологичность и эксплуатационные качества автомобиля, такие как устойчивость к столкновениям и уровень шума и вибрации. Это позволяет сократить число испытаний и, следовательно, изготавливать меньше опытных образцов. Кроме того, это уменьшает количество запоздалых технических изменений, а значит, помогает избавиться от потерь в процессе разработки продукции. Имея в своем распоряжении опытный инженерно-технический персонал, вооруженный инструментами стандартизации, Toyota быстро и качественно осуществляет проектно-конструкторские разработки, гибко регулируя производительность. Далее будет дано несколько примеров контрольных листков.
Стандартизация процессаЭтот вид стандартизации дает возможность заниматься параллельным проектированием, синхронизируя деятельность функциональных подразделений, и добиваться исключительных темпов разработки автомобилей. Речь идет о стандартизации типовых задач, а также последовательности и продолжительности их выполнения. Такая стандартизация – основа непрерывного совершенствования процесса разработки продукции. Стандартизация процесса предотвращает возникновение вариабельности поступления задач, о которой рассказывалось в предыдущей главе. Только с помощью такой стандартизации можно достоверно знать, чем и когда занимаются другие функциональные подразделения и в какой момент соответствующее подразделение должно обеспечить ввод необходимой информации. И наконец, строгая дисциплина процесса в сочетании со стандартными процессами разработки – это единственно возможный способ управлять «фабрикой разработок» и оценивать ход работ по отдельным проектам.
Как отмечалось в главе 5, где речь шла о логике процесса, процесс бережливой разработки продукции предполагает централизованный контроль базовых требований к стандартному процессу с целью обеспечить синхронизацию. В Toyota (см. главу 4) это означает, что во многих проектах используются общие (высокоуровневые) понятия об этапах и параметрах сроков, а выполнение отдельных операций контролируется на уровне каждого функционального подразделения. Подробные графики выполнения каждого проекта разрабатываются с использованием обеих стандартизированных структур.
В NAC, в отличие от Toyota, стандартизацией основных этапов занимается руководство, которое чрезвычайно подробно описывает результаты, которых должны добиться функциональные группы к концу каждого из этапов (так называемая модель постадийного контроля). Обязанность изыскать пути достижения этих результатов возлагается на проектные и функциональные группы. В то время как в Toyota проектно-конструкторские подразделения стандартизируют средства разработки продукта, исходя из требований к проекту в целом, администрация NAC пытается стандартизировать лишь результаты разработок.
В отсутствие жесткой стандартизации и единой компоновки NAC не располагает эффективной стратегией гибкого регулирования производительности, что вызывает периодический дефицит важнейших ресурсов в процессе разработки продукции. NAC тоже привлекает к работе инженеров поставщиков и поручает проектирование сторонним организациям, однако, поскольку профессиональные знания и навыки, конструкция и процесс не стандартизированы, результаты такой работы часто оставляют желать лучшего, а передачи материала из рук в руки резко повышает затраты, причем вина за это обычно возлагается на поставщиков.
Стандартизированные процессы, которые определяют порядок работы на уровне функциональных подразделений, помогают гибко регулировать производительность и выравнивать объем работ. Без стандартизации невозможно реализовать третий принцип LPDS – обеспечить выровненный поток процесса разработки продукции. Хорошо известно, что стабильность – необходимое условие создания потока при бережливом производстве. То же самое справедливо и в отношении разработки продукции. Стандартизация обеспечивает стабильность, последовательные и непротиворечивые требования и предсказуемые результаты. Без этого нельзя создать поток.
Стандартизированный процесс разработки продукции имеет еще одно преимущество – он способствует четкому обмену информацией и улучшает взаимопонимание между функциональными подразделениями, поскольку единые подходы помогают находить общий язык.
Благодаря стандартизации, когда инженеры отдела разработки кузова приступают к работе с оцифрованными данными поверхности глиняной модели, отдел организации производства может приниматься за детальную разработку технологического процесса. Группы, которые занимаются разработкой штампов, технологической оснастки, фиксаторов и технологии их обработки, начинают предварительную работу. Группы отдела организации производства отслеживают эволюцию конструкции деталей, стараясь извлекать максимум из пока еще неполной проектной информации и идти в ногу с разработчиками. Отдел организации производства приступает к параллельному проектированию лишь когда конструкторское решение приобретает определенность. При таком порядке эффективный поток процесса предотвращает необходимость разорительных переделок и доработок на дальнейших этапах. Параллельное проектирование в отсутствие синхронизации нередко приводит к слишком поспешному выполнению работы на основе неполных данных или непродуманных идей. Это неизбежно вызывает необходимость последующих доработок и порождает потери. Помимо вездесущих контрольных листков, о которых рассказывалось выше, отдел организации производства использует сендзу, подробные чертежи каждой детали. Сендзу, которые обновляются по завершении каждого проекта и направляются соответствующим функциональным группам, содержат исчерпывающую информацию об изготовлении конкретной детали и оптимальных методах работы, в том числе об изменении геометрических параметров при изготовлении, принципах крепления, местах сварных соединений и т. д.
В этот напряженный период группа разработки штампов применяет стратегию гибкого регулирования производительности, привлекая к работе стажеров. Процесс бережливой разработки продукции предполагает разбивку сложной задачи по разработке штампов на ряд стандартизированных действий, а САПР обеспечивает общий доступ к банку данных по стандартным компонентам. Поэтому над одной и той же конструкцией могут одновременно работать несколько специалистов разной квалификации. Это ускоряет разработку и помогает гибко распределять персонал, который по мере высвобождения переключается на проработку других деталей. При этом чрезвычайно важно учитывать готовность деталей кузова, так как отдел разработки кузова выпускает итоговую документацию в определенной последовательности. Данные об этих деталях доступны специалистам отдела организации производства благодаря единой базе данных, поэтому соответствующая информация вытягивается по мере необходимости.
Как отмечалось выше, межфункциональная синхронизация стандартных процессов позволяет разработчикам начинать работу над отдельными деталями, опираясь на неполные данные. По мере проработки конструкции деталей разработчики штампов вытягивают нужную информацию и доводят работу до конца. На этом этапе отдельные несложные задачи, не требующие высокой квалификации, могут выполняться стажерами, которые помогают разработчикам. Такой процесс возможен лишь благодаря стандартизации, которая одновременно поддерживает все три подсистемы бережливой разработки продукции – процесс, инструменты и технологию и людей. Весьма эффективным средством такой стандартизации служат сендзу. Сендзу по штампам включают подробные сведения о форме зажимных приспособлений, деформации и радиусах изгиба. Комплекты сендзу по конкретной модели автомобиля содержат важную информацию, чрезвычайно важную для эффективной разработки штампов.
Стандартные производственные процессы и унификация конструкции позволяют приступить к предварительной разработке фиксаторов на ранних стадиях процесса, после того как определился внешний облик автомобиля. Фиксатор – это элемент формообразующего штампа, который удерживает листовой металл в процессе штамповки. Фиксаторы очень важны для качественной штамповки, и их создание может быть непростой задачей из-за сложной геометрической формы. При их разработке нередко приходится оценивать деформируемость штампуемых деталей с помощью компьютерного моделирования и анализа методом конечных элементов (FEA, Finite Elements Analysis). NAC в отсутствие стандартизации конструкции и процесса вынуждена выполнять анализ методом конечных элементов для всех штампуемых деталей, что при ограниченных ресурсах порождает чудовищные задержки в процессе. Поскольку в Toyota геометрические параметры деталей и производственные процессы стандартизированы, при разработке продукции менее трети штампуемых деталей требуют анализа методом конечных элементов. Две трети деталей не нуждаются в таком анализе, что помогает избежать появления узких мест и очередей, а следовательно, снизить вариабельность процесса разработки продукции. Кроме того, это сокращает среднюю продолжительность производственного цикла и существенно снижает затраты, что дает компании конкурентные преимущества на следующем этапе процесса бережливой разработки продукции.
На этом этапе, который включает отливку, станочную обработку, испытания и апробирование инструмента и штампов, принципы бережливого производства Toyota непосредственно влияют на процесс разработки продукции, поскольку изготовление инструментов и штампов – тоже разновидность производства. Точные, подробные стандарты конструкций штампов позволяют Toyota на данном этапе применять принципы бережливого производства к процессу разработки продукции, что служит важным конкурентным преимуществом системы бережливой разработки продукции. В среднем на изготовление крупного комплекта штампов, например штампов для боковых панелей кузова, уходит менее четырех месяцев. За это время компания успевает осуществить отливку, станочную обработку, сборку и предварительную отладку штампов в заводских условиях. Конкуренты Toyota тратят на ту же самую работу 10–12 месяцев, поскольку им каждый раз приходится решать весь комплекс задач с нуля. Из цеха штампы отправляются на штамповочный участок для отладки в условиях производства. Одновременно производится отладка автоматики и фиксаторов, необходимых для работы с заготовками. На это уходит по шесть – восемь часов один-два раза в неделю, что в общей сложности составляет еще месяц-два. Используя стандартные конструкции и современные технологии, Toyota значительно сократила количество опытных образцов при создании инструментальной оснастки, что дает ощутимую экономию времени и денег. Ниже речь пойдет о стандартных сроках разработки штампов и инструментальной оснастки в Toyota. Специальные проекты выполняются гораздо быстрее.
Внимание! Это не конец книги.
Если начало книги вам понравилось, то полную версию можно приобрести у нашего партнёра - распространителя легального контента. Поддержите автора!Правообладателям!
Данное произведение размещено по согласованию с ООО "ЛитРес" (20% исходного текста). Если размещение книги нарушает чьи-либо права, то сообщите об этом.Читателям!
Оплатили, но не знаете что делать дальше?