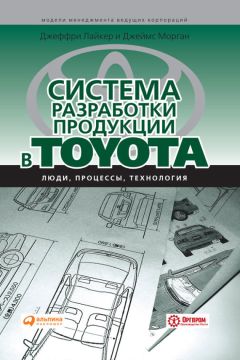
Автор книги: Джеффри Лайкер
Жанр: Зарубежная деловая литература, Бизнес-Книги
Возрастные ограничения: +12
сообщить о неприемлемом содержимом
Текущая страница: 11 (всего у книги 36 страниц) [доступный отрывок для чтения: 12 страниц]
При бережливом производстве время такта рассчитывается как отношение времени на изготовление продукции к потребительскому спросу. Оно определяет темп работы и ассортиментную структуру при выполнении производственных операций. Хотя в процессе бережливой разработки продукции нет точного эквивалента времени такта, чрезвычайно важно определить ритм проектно-конструкторских работ, чтобы обеспечить согласованность различных видов деятельности и стабильное и равномерное движение вперед. После того как вы устранили потери и создали выровненный поток в процессе разработки продукции, вам понадобится механизм, который поможет поддерживать единый, стабильный ритм функционирования системы. Toyota регулирует темпы разработок, используя несколько механизмов. Во-первых, компания согласует темпы разработки с мероприятиями на низовых уровнях, выполняемых для реализации базовых задач проекта. Единый ритм работы задает регулярность анализа состояния проекта. Инженеры и поставщики приходят на обсуждение результатов проекта с опытными образцами, результатами испытаний, нерешенными вопросами и т. д. Все это дает главному инженеру возможность определить (из первоисточника), выполняется ли план. Главный инженер беспощадно критикует представленную работу и задает вопросы, которые позволяют выявить потенциальные проблемы. Любой, кто посетил хотя бы одно из подобных мероприятий, знает, что скрыть недобросовестную работу практически невозможно. Ты либо готов, либо нет, и истинное положение дел выясняется очень быстро. Инженеры усердно готовятся к таким проверкам, поскольку они служат важными вехами в работе команды, ведь намеченное нужно выполнить точно в срок. Любые вопросы или проблемы сразу же обсуждаются.
На более поздних этапах процесса разработки продукции главный инженер с той же целью использует этапы сборки опытных образцов и проверки конструктивного соответствия компонентов. Эти действия имеют ту же направленность, что и анализ проекта. Они приурочены к определенным этапам процесса и позволяют главному инженеру внести важный вклад в разработку конструкции и создание инструментальной и технологической оснастки именно тогда, когда проектные команды нуждаются в его помощи. Это тоже способствует стабильному движению вперед. Как и перед анализом проекта, все участники напряженно трудятся, готовясь к этим мероприятиям по системной оценке. К примеру, задача проверки конструктивного соответствия компонентов – оценить качество стыковки штампованных панелей кузова и на основе этих данных принять решения, касающиеся штампов.
На низовом уровне ведущие специалисты проектно-конструкторских подразделений через день встречаются с главным инженером в обея, чтобы проанализировать состояние проекта, обсудить нерешенные вопросы и достижение намеченных показателей. Эти встречи непродолжительны и носят деловой характер, основное внимание в них уделяется ситуациям, которые представляют собой отклонение от нормы (подобно принципу дзидока на производстве). В инструментальном цехе группа руководителей каждое утро обходит все участки, сверяя текущее состояние деталей с почасовым графиком и при необходимости принимая экстренные контрмеры, и помогает участникам проекта подготовиться к таким важным событиям, как оценка опытного образца.
Такая интегрированная система методов, задающих ритм, имеет и еще одно преимущество. Она сокращает время управленческого цикла, а значит, дает возможность при необходимости быстро откорректировать курс и нацелить команду на решение определенной задачи. Время управленческого цикла – это период времени между проверками, которые выполняет менеджмент, или время, которым располагают инженеры для завершения определенного этапа работ. В системе бережливой разработки продукции управленческий цикл длится немногим более суток. Однако в тех компаниях, где управленческий цикл не имеет четкого значения, могут пройти месяцы, прежде чем кто-либо удосужится взглянуть на результаты работы и обнаружить проблемы. Именно так было у одного из поставщиков комплектующих. Поработав с авторами данной книги, он учредил четкий график еженедельных проверок, для визуального отображения хода работ использовал доски. Это значительно снизило время выполнения заказа.
В бережливом производстве дзидока (автономизация) нацелена на выявление отклонений и быстрое принятие мер. Реализовать этот принцип помогает использование инструментов визуального менеджмента, таких как андон (например, когда рабочий на линии дергает шнур, загорается лампочка). Эти инструменты очень важны для разработки продукции, ведь здесь необходимо быстро выявлять отклонения и устранять проблемы. В системе разработки продукции Toyota для этой цели применяется ряд инструментов, в том числе контрольные листки. Проектная группа вывешивает в обея перечень конкретных целей и отслеживает их достижение по ходу работы над проектом. Это пример применения дзидока и визуального менеджмента в системе разработки продукции Toyota.
Применяемая в Toyota система параметрического автоматизированного проектирования – пример использования технологии для выявления отклонений. При изменении конструкции отдельных компонентов система вносит необходимые изменения в конструкцию всех сопрягаемых деталей и соответствующих инструментов. В случае ошибки, например, если заданные условия вызывают разрушение детали, система уведомляет об этом всех разработчиков, участвующих в проекте. При этом любые проектно-конструкторские работы и инженерные расчеты в Toyota ведутся с пониманием всей системы (автомобиля) в целом. Это значит, что все инженеры и разработчики имеют доступ к документации по любым узлам и деталям и могут посмотреть, как планируемые ими изменения отразятся на других деталях.
Пока-ёкэ (предупреждение ошибок) – еще одна концепция, которая помогает обеспечить непрерывный поток в производственном процессе Toyota. Предупреждение ошибок сокращает продолжительность проверок и высвобождает время на встраивание качества. Родственная концепция – это контроль на рабочем месте. Вместо проверки третьими лицами в конце процесса ответственность за контроль качества возлагается на того, кто выполняет технологическую операцию. При разработке продукции философия пока-ёкэ выражается посредством:
• контрольных листков;
• подробных стандартных планов проведения испытаний;
• матриц качества компонентов;
• стандартной компоновки;
• использования одних и тех же компонентов в разных автомобилях;
• стандартизированных производственных процессов.
Контрольные листки направляют инженеров в процессе разработки продукции и позволяют избежать ошибок при проектировании. Планы проведения испытаний стандартизированы по видам деталей и содержат требования и сроки для каждой разрабатываемой детали. Кроме того, для каждой детали составляется подробная матрица качества, где описан стандартный производственный процесс, и влияние отдельных технологических операций на конструктивные характеристики. Матрица качества (см. главу 15) содержит рекомендации по разработке, ориентированные на процесс бережливого производства. Использование стандартной компоновки при создании новых продуктов позволяет Toyota поддерживать стабильный уровень параметров автомобиля – устойчивости к столкновениям, удобства управления и шумовых характеристик. То же самое относится к использованию одних и тех же комплектующих в разных моделях. И наконец, поскольку конструирование новых деталей ориентировано на стандартные производственные процессы, качество и производительность Toyota неизменно высоки. Система бережливой разработки продукции предупреждает сбои до их появления, что помогает добиваться предсказуемых результатов.
Вытягивание информации в системе разработки продукцииСистема вытягивания в бережливом производстве построена так, чтобы операции, расположенные ближе к концу потока создания ценности, сигнализировали предшествующим операциям о своих потребностях (спросе). Это помогает избежать перепроизводства. Средством такого оповещения обычно служат карточки канбан. При разработке продукции объектом потока становятся знания и информация. При разработке автомобилей современная технология обеспечивает головокружительную скорость передачи информации. Однако далеко не вся информация нужна каждому участнику процесса. Система бережливой разработки продукции использует вытягивание для сортировки огромного массива данных, чтобы соответствующие специалисты вовремя получали нужную информацию. Основной элемент (материал) в процессе разработки продукции – это знания.
В Toyota крайне редко прибегают к массовому оповещению персонала. Здесь считают, что каждый инженер должен вытягивать релевантную информацию оттуда, где она есть. Он должен уметь отыскивать и получать необходимую информацию, будь то расчетные данные, которые хранятся в системе сбора данных, сведения об эксплуатационных характеристиках выпускаемых автомобилей или мнение высшего руководства. Этому правилу подчиняются все – от новичка до главного инженера. Такой подход весьма эффективен, поскольку любой участник процесса имеет доступ к проектным данным и всегда может поговорить с главным инженером.
К примеру, на низовых уровнях проектной иерархии все инженеры несут ответственность за бенчмаркинг компонентов, которые они разрабатывают. Они должны собрать релевантную информацию, которая может повлиять на процесс разработки – ознакомиться с последними достижениями в развитии технологии, тенденциями развития отрасли и ассортиментом продукции поставщиков и конкурентов. Когда начинается этап выполнения работ, технологи, приступая к созданию штампов и технологической оснастки, вытягивают проектные данные из системы сбора данных. Все инженеры вытягивают информацию о соответствующих требованиях из контрольных листков, которые обновляются по завершении каждого проекта.
Опыт поставщика, упомянутого выше (компания со слишком длительным управленческим циклом), показывает, как система бережливой разработки продукции связывает отдельные процессы. Составив карту процесса создания ценности, этот изготовитель сидений увидел, что партии информации выталкиваются на очередную операцию. Конструкторское бюро отправляло сотни чертежей в отдел снабжения и заказывало сотни деталей, чтобы впоследствии изготовить сотни вариантов опытных образцов и т. д. Чтобы решить эту проблему, компания перешла к скользящему графику выпуска документации. При новой системе на следующую операцию в назначенный срок направлялась документация всего по нескольким видам сидений. При этом стали проводиться еженедельные проверки, для чего в каждом функциональном подразделении, включенном в цепочку добавления ценности, были установлены доски для визуального отслеживания хода работ. Такие доски (они называются «доски вытягивания») нужны главным образом для того, чтобы сигнализировать о том, какая информация нужна другим подразделениям. В результате стало значительно проще определить, когда понадобится та или иная информация. Задержки информации обнаруживались в течение недели, а не нескольких месяцев. Этот пример говорит о том, что для бесперебойного вытягивания данных в процессе бережливой разработки продукции нужно сократить время управленческого цикла.
Объединение операций в единый потокЧтобы создать поток и связать отдельные операции, на производстве часто используются ячейки. Для создания ячейки берется оборудование с разных участков и компонуется в соответствии с движением продуктового потока. Это позволяет быстро обрабатывать изделия, поступающие в ячейку, по одному. Там, где создание ячеек невозможно, предусматриваются небольшие буферные запасы, между процессами создаются системы вытягивания. Общий принцип бережливого производства – составить график работы одного из участков (процесса, задающего ритм) и обеспечить вытягивание материала к этому участку. График работы процесса, задающего ритм, не вполне соответствует порядку поступления заказов от потребителя, поскольку потребительский спрос редко бывает стабильным. Отдел управления производством выравнивает график процесса, задающего ритм, с учетом показателей потребительского спроса. Так обеспечивается выровненное вытягивание материала с предшествующих процессов и в конечном счете от поставщиков. Скорость выполнения процесса, задающего ритм, т. е. время такта, – это средний темп выровненного потребительского спроса за определенный период.
В процессе бережливой разработки продукции эквивалентом ячейки для обработки потока единичных изделий становится межфункциональная команда, которой поручена разработка изделия. Такая команда по мере надобности в нужной последовательности выполняет соответствующие операции. В определенном смысле именно этим занимается инженер по параллельному проектированию и межфункциональная команда разработки модулей. Эта виртуальная ячейка по мере необходимости вытягивает извне информацию и материалы. К сожалению, текущие операции на производстве регламентированы куда более жестко, чем процесс разработки продукции. Однако, как уже говорилось в этой главе, при разработке продукции Toyota применяет аналогичные принципы снижения вариабельности процесса и в значительной мере предупреждает переделки и доработки за счет жесткой дисциплины выполнения работ и соблюдения графика. Компания выравнивает объем работ путем детального планирования, гибко регулирует производительность, подключая резервные ресурсы в периоды всплеска объема работ, и создает поток с помощью скользящего графика выпуска документации и межфункциональной синхронизации, координируя работу системы за счет механизмов регулирования ритма.
Но хотя эти механизмы весьма важны и полезны, для построения бережливого процесса их недостаточно. На этом этапе читателю должно быть понятно, что бережливый процесс требует дисциплины и стандартизации. Речь об этом пойдет далее.
Резюме принципа 3
Обеспечить выровненный поток процесса разработки продукции
Чтобы сделать разработку продукции более эффективной, полезно рассматривать ее как процесс. Процесс бережливой разработки продукции имеет ряд отличительных черт.
• Используйте кенто, или этап изучения, при разработке концепции, чтобы выявить и решить как можно больше потенциальных технических проблем. Это позволит снизить вариацию в начале потока создания ценности.
• Четко определите логику процесса, выделив разумное количество управляемых этапов и видов деятельности.
• Синхронизируйте деятельность функциональных подразделений.
• Выровняйте объем работ, тщательно планируя цикл создания продукта. Это даст возможность регулировать производительность системы.
• Применяйте стратегию гибкого регулирования производительности, чтобы предотвратить сбои в периоды всплеска объема работ.
• Составляйте графики согласованной работы функциональных подразделений и детальные графики работ внутри подразделений, чтобы синхронизировать различные виды деятельности и устранить вариацию.
• Составьте скользящий график передачи информации из одного функционального подразделения в другое, определив приоритетность и очередность выполнения отдельных задач.
• Установите ритм выполнения проектно-конструкторских работ и непродолжительное время управленческого цикла, чтобы обеспечить согласованную работу системы и расчет реальных сроков завершения отдельных этапов.
• Строго придерживайтесь плана работ и следите за соблюдением графиков, чтобы устранить вариабельность поступления задач.
• Используйте контрольные листки и планы стандартизированной разработки деталей, чтобы устранить вариабельность выполнения задач.
• Встраивайте качество на каждом этапе процесса и не передавайте проблемы на следующий этап.
• Создайте систему и культуру, при которых инженеры вытягивают знания по мере надобности, а не захлебываются в море информации.
• Встройте в базовый процесс обучение и непрерывное совершенствование.
У нас получился достаточно длинный список, но именно совокупность всех этих методов позволяет наладить выровненный поток и создать управляемый процесс, который можно совершенствовать с помощью кайдзен.
Глава 6
Применять жесткую стандартизацию, чтобы снизить вариацию, повысить гибкость и обеспечить предсказуемость результатов
Стандартизация, которой мы достигли сегодня, – стартовая площадка для совершенствования, которое будет завтра. Если вы воспринимаете стандарт как лучшее из существующего сегодня и понимаете, что его предстоит совершенствовать завтра, – у вас есть перспективы. Но если вы считаете, что стандарт – это все, прогресс останавливается.
Генри Форд
Стандартизированная работа – одна из важнейших составляющих производственной системы Toyota, где любые операции расписаны по секундам и согласованы со временем такта – темпом потребительского спроса. Применим ли такой же подход к проектно-конструкторской работе? Стандартизация времени такта возможна для некоторых рутинных операций, например, простейшей работы в САПР, однако инженеры, которые переходят от решения одной крупной задачи к другой и сталкиваются с большим количеством факторов неопределенности, не могут точно определить начало и окончание той или иной работы.
Когда авторы посоветовали инженерам стандартизировать свою работу, ответы были вполне предсказуемы: «Мы люди творческие», «Мы не занимаемся однообразным ручным трудом», «Нам нужна возможность свободно планировать свое рабочее время, чтобы творить». Вполне естественно, что инженерам, которые разрабатывают продукцию, сложно понять, как можно сочетать творчество и стандартизацию. В то же время процесс разработки продукции в Toyota показывает, что различные виды стандартизации повышают гибкость и темпы работы проектных команд, точность, надежность, качество и предсказуемость результатов. Кроме того, стандартизация сокращает объем потерь, тем самым снижая затраты.
Стандартизация и дисциплина – самые мощные орудия организации, занимающейся разработкой продукции. Они помогают противостоять разрушительному воздействию вариации, которое отмечалось выше в контексте рассмотрения теории очередей. Именно стандартизация – один из основных факторов успеха Toyota в разработке продукции. Жесткая стандартизация конструкции дает возможность широко использовать общие платформы, включая в их состав важнейшие узлы и подсистемы и применяя единую технологию. Это снижает затраты и повышает качество. Унифицированная конструкция, ориентированная на предсказуемые процессы бережливого производства, обеспечивает стабильные эксплуатационные характеристики кузова, что значительно упрощает проведение испытаний. Стандартные процессы разработки продукции формируют атмосферу доверия и обеспечивают высокие темпы работы благодаря точной синхронизации. Все это помогает успешно управлять сложнейшим процессом разработки новых автомобилей. Стандартные процессы производства и испытаний гарантируют неизменно высокое качество и непревзойденный уровень бережливого производства, изначально накладывая вполне понятные ограничения на процесс разработки продукции. И наконец, стандарты знаний и навыков, необходимых для выполнения проектно-конструкторских работ, помогают Toyota взращивать блестящих инженеров и обеспечивать высокую эффективность процесса разработки продукции. Эти стандарты способствуют взаимному доверию совместно работающих специалистов. Стандартизация, которая никоим образом не умаляет значение самостоятельности и креативности инженеров, в сочетании со стремлением Toyota к совершенству, – основа высокого профессионализма и воодушевляющей атмосферы гордости, солидарности и взаимного уважения, равных которым нет в отрасли.
Три вида стандартизацииКак отмечалось ранее, в системе бережливой разработки продукции существует три вида стандартизации: стандартизация конструкции, стандартизация процесса и стандартизация знаний и навыков специалистов, которые занимаются проектно-конструкторской работой. Дав краткие определения трех видов стандартизации, мы рассмотрим каждый из них в контексте процесса разработки продукции в Toyota.
1. Стандартизация конструкции. Это стандартизация конструкции и компоновки изделия и его компонентов. Она включает использование стандартных, проверенных узлов и деталей в различных моделях автомобилей, создание новых моделей на базе существующих платформ, модульную структуру и проектирование с учетом стандартов бережливого производства. Все это позволяет создать надежную конструкцию, пригодную для многократного использования.
2. Стандартизация процесса предполагает стандартизацию задач, инструкций по выполнению работы и последовательности выполнения задач в процессе разработки продукции. Данный вид стандартизации распространяется на процессы производства и испытаний продукции.
3. Стандартизация профессиональных знаний и навыков. Это стандартизация навыков и умений инженерно-технического персонала. Принципы развития и обучения людей требуют практического применения освоенных навыков. Это весьма действенный подход, который нередко упускается из виду.
Правообладателям!
Данное произведение размещено по согласованию с ООО "ЛитРес" (20% исходного текста). Если размещение книги нарушает чьи-либо права, то сообщите об этом.Читателям!
Оплатили, но не знаете что делать дальше?