Текст книги "Сегодня и завтра"
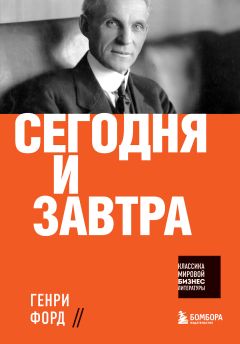
Автор книги: Генри Форд
Жанр: Зарубежная деловая литература, Бизнес-Книги
Возрастные ограничения: +12
сообщить о неприемлемом содержимом
Текущая страница: 3 (всего у книги 16 страниц) [доступный отрывок для чтения: 5 страниц]
Полируют стекло на специальных круглых подставках, на которых стеклянные листы закрепляются при помощи алебастра. Подставки плотно закрываются стеклом и подводятся к шлифовальной машине. Для шлифовки используются семь разных жерновов – от сделанных из грубого песка и до изготовленных из измельченного цемента. По окончании шлифовки подставку отмывают от мелких фрагментов жерновов и перемещают к полировальному станку, где вращающиеся войлочные цилиндры придают стеклу блеск. На следующем этапе его переворачивают на другую сторону и отправляют снова к шлифовальным машинам, где процесс начинается сначала. Метод требует очень много времени и приводит к чрезмерному расходованию ресурсов.
Изготовление из глины емкостей для плавки стекла является единственным старинным методом на фордовских заводах. Чаны производятся вручную. Сначала рабочие месят глину голыми ногами до тех пор, пока масса не станет однородной, а все лишнее не будет удалено. Потом руками слой за слоем тщательно лепят емкости в форме горшков, дабы закрыть все, даже самые маленькие щелочки, сквозь которые сможет поступать воздух, потому что хватит и микроскопической трещинки, чтобы чан, помещенный в печь, раскололся. Пока еще не придумали механизмов, чьи изделия не уступали бы ручной работе. Внедрив новую технологию, мы перестали нуждаться в ручной лепке горшков, поскольку больше их не применяем.
Для того чтобы создать сырьевые резервы на Гласмирском заводе, мы были вынуждены приобрести силикатные разработки в Кавоте, на расстоянии 18 миль от предприятия. На этой точке трудятся сорок человек: они добывают, дробят и отгружают не менее 10 вагонов силикатного песка в день. Мы наняли тех же людей, которые и раньше были заняты на тех же работах, но, начав получать по 6 долларов зарплаты в день и имея постоянную работу, они совершенно преобразились. Практически все они являются низкоквалифицированными работниками, поскольку при нашем способе производства почти ни на каком этапе не нужно особое мастерство. Однако люди отнюдь не бесталанны. Они не увольняются с завода, добросовестно трудятся, откладывают средства, и значительная часть рабочих уже перебрались из своих хлипких полуразвалившихся лачуг в комфортабельные собственные дома. При новых методах и приемах работы производительность каждого трудящегося, по нашей информации, увеличилась не менее чем в два раза по сравнению с работой традиционными способами. Затраты производства в таком случае существенно уменьшаются, потому что практически все технологические процессы совершаются при помощи машин.
Так, бурение скважин выполняется посредством горных буров. Затем скважины начиняют динамитом, который, взрываясь, разламывает песчаник на крупные куски. Расколотый песчаник собирают, специальными паровыми лопатами складывают в небольшие вагонетки из стали и тракторами, оснащенными стальными же колесами, доставляют на предприятие, где его измельчают. Там камень крошат, просеивают и многократно промывают для того, чтобы получить материал, достаточно чистый для применения при выработке стекла. На заключительном этапе обработанный песчаник по трубам перемещается в вагоны и отправляется на Гласмирский завод.
Отметим также, что и силикатные разработки, и дробильное предприятие достаточно чисты. Еще одно наше правило – всякий процесс должен проходить в чистой обстановке. Некоторые машины неизбежно загрязняют воздух, как, скажем, дробильный агрегат, но их укрепляют и снабжают специальным устройством для устранения пыли. Недопустимо вынуждать работников дышать грязным воздухом, как и негоже засыпать пылью окружающее пространство и губить живую природу.
Для того чтобы создать собственный резерв железной руды и уменьшить транспортные расходы, мы приобрели шахту «Императорская» в Мичигане, в 80 милях к северу от Железной горы – центра наших лесных разработок. Десятилетие она простояла без дела, но мы решили, что она богата рудой и в плане транспортировки тоже выгодна. Мы не сомневались, что при ее разработке получим прибыль, и впервые попытались заняться добычей железной руды. Руководствуясь нашей кадровой политикой, управлять компанией мы пригласили человека, который был согласен с нашими методами и принципами.
Для начала шахту требовалось расчистить: с этого всегда надо начинать, чтобы оценить объем дальнейших усилий. Шахта, стоявшая заброшенной так долго, заросла травой и была засыпана землей. Сложилась нелепая традиция, что на шахтах обязательно должно быть грязно. Но мы не выносим никакой нечистоты – она стоит чересчур дорого. А потом мы приступили к работе и одновременно начали учиться.
Главная идея состояла в том, чтобы рабочие получали достойную зарплату, трудились и жили в безопасных и удобных условиях и чтобы шахта давала значимое количество дешевой руды. Мы добились цели.
Выстроенные около шахты сооружения можно принять за домики пригорода. Все они выкрашены в светлые оттенки – так будет видно малейшее пятнышко. Наши постройки окрашиваются не для того, чтобы замаскировать грязь, – мы предпочитаем белый или светло-серый оттенки, чтобы чистота стала абсолютным правилом. Старые дома пришли в негодность, и несмотря на то что мы не планировали ничего строить, все-таки были вынуждены этим заняться. Мы возвели здания и около угольных шахт, и на лесных разработках. Выстроили общежитие для холостых работников, для каждого с отдельной спальней, а потом для семей доставили переносные домики. Позже их заменили коттеджи. Они сдавались во временное пользование по 12 долларов за месяц, включая электричество. Следует отметить, что и шахта, и лесной поселок освещены электрическими лампочками. Когда-то школа была устроена в амбаре. Наша компания открыла современную школу и отличный магазин, где все можно купить по себестоимости.
Само собой, была установлена обычная наша оплата труда. К нам потянулись лучшие шахтеры со всех шахт в округе. Хотя в одну смену бывают заняты не более 225 человек, число заявлений о приеме на работу многократно превышает количество свободных мест. Рудокопы работают 8 часов без сверхурочных, простои при этом минимальны. На наших заводах идет непрерывная работа, и люди трудятся не покладая рук.
Пока что мы не имеем существенного опыта добычи железной руды, поскольку занимаемся этим слишком непродолжительное время, чтобы спланировать какие-то улучшения. Но, судя по всему, машины найдут здесь гораздо большее применение, чем бывает обычно. Мы шли вперед медленно еще и потому, что старались сделать труд шахтеров как можно более безопасным. Руда добывается под землей, и работа даже при самых хороших условиях сопряжена с риском, поэтому прежде всего мы стремились каждый этап как можно более обезопасить. Мы этого добились, и число несчастных случаев у нас минимально. Все подразделения шахты и лесного поселка поддерживаются в полном порядке. Подземные коридоры выстроены в три слоя, на расстоянии 200 футов друг от друга. Руду взрывают по окончании каждой из двух восьмичасовых смен. Потом при помощи электрической железной дороги ее вывозят. Из штреков, находящихся на разных уровнях, руда сжатым воздухом выдувается в специальные проводы, направленные к яме на дне шахты, оттуда вагонетками на канатах руда поднимается на поверхность. Если руда залегает более глубоко, ее поднимают при помощи особого механизма.
Стены и потолки коридоров регулярно проверяются главным инспектором. Также мы создали отдельный комитет по вопросам безопасности, который пользуется поддержкой всех шахтеров. При манипуляциях со взрывчаткой принимаются предельно строгие меры предосторожности. Фонарики, которые крепятся к головным уборам шахтеров, отключаются за 25 футов от того места, где находятся взрывчатые вещества, освещается оно электрическими лампами.
Разветвленная система насосов откачивает воду из впадин, а затем коридоры осушаются при помощи парового отопления. Шахтеры трудятся в специальной одежде и резиновой обуви. По окончании смены рабочие моются в душевых, которые тоже принадлежат предприятию, и переодеваются. В течение того времени, пока шахтеры отдыхают, их рабочая одежда как следует прогревается и высушивается.
Шахты функционируют весь год, и добытая руда по железной дороге доставляется в Маркет, а там отгружается на пароходы для поставки на Фордзоновский завод. Зимой, когда нет навигации, руда складируется возле входа в шахту посредством специальных машин. Компания не использует труд животных.
Добыча руды сейчас составляет около 200 тыс. тонн в год. Расходы предприятия при этом существенно меньше, чем затраты любой другой шахты, которая платит маленькую зарплату. После приобретения шахты мы выкупили все прочие рудные залежи в округе.
Вот так мы обращаемся со средствами, которые получаем от народа. Более подробный рассказ ждет вас в следующих главах. Все накопленные нами капиталы были получены из дохода.
Глава 5
«Это неосуществимо!»
Одним из самых поразительных фактов в сфере индустрии является то упрямство, с которым многие держатся за устаревшие способы работы, применявшиеся задолго до возникновения механической силы и механизмов, тогда как для нас единственной ценной традицией в производстве выступает неизменно хороший результат. Все прочее, что называется традицией, полагалось бы называть экспериментом.
В первую очередь следует отбросить идею, что механическая сила не требуется, если в наличии человеческая сила и она дешева. Работа людей не является товаром. Мы уже не раз отмечали, что трудящиеся должны быть для компании лучшими клиентами и что пока это не стало реальностью, абсолютно нет смысла увеличивать заработную плату. Несомненно ошибочным является утверждение, что стоимость работника определяется той заработной платой, за которую он согласен трудиться, и что владелец предприятия должен назначать зарплату и цены в целях полного использования рынка, иначе говоря, имеет право выплачивать работнику минимум и получать от своих клиентов все, что только они способны дать. Дело не может вестись случайным образом – необходимо следовать четкому и конкретному плану.
Многим людям это нелегко осознать. Проще всего быть как все, принять обстоятельства такими, какими они являются, использовать любой подходящий момент, чтобы урвать побольше, а потом хвалиться своей оборотистостью. Но все это противоречит принципу обслуживания и не имеет ничего общего с грамотным управлением предприятием. Даже больше – мешает накоплению финансов. Разумеется, действуя по старым нормам, предприниматель способен удачно провернуть операцию-другую и разбогатеть на парочку миллионов – порой и игроку везет выиграть крупные деньги. Однако в настоящем деле азартная игра неуместна. Достойная компания сама «выращивает» своих клиентов.
Мы считаем, что обязательно должны изыскивать самые лучшие методы и приемы для создания наших продуктов и что каждый производственный этап надо рассматривать как эксперимент. Когда мы добиваемся результатов, которые представляются нам превосходными сравнительно с тем, что получалось ранее, значит, выработка продукта пребывает на определенном этапе, и ничего больше. Это и не может быть ничем иным. Внедренные нами новшества утвердили нас в мысли, что в будущем произойдут еще большие изменения и что, таким образом, ни одна отдельно взятая операция не осуществляется настолько хорошо, как должна бы. Мы не стремимся к переменам ради перемен, но мы всегда вносим изменения в процесс, как только получаем доказательства того, что новый метод лучше прежнего. Также мы полагаем своим долгом устранять все, что мешает развитию, и оказывать общественности все более качественные услуги, руководствуясь нашими принципами формирования цен и заработка сотрудников.
Отвязаться от традиционных методов непросто. Вот почему все наши новые проекты возглавляются людьми, которые прежде определенным видом деятельности не занимались и, следовательно, не привыкли что-либо называть «неосуществимым». Технические эксперты приходят нам на помощь всякий раз, когда потребуется. Но никакое дело не управляется именно техником, потому что такому служащему, как правило, известно чересчур много «нереальных» вещей. Если нам заявляют: «Это сделать невозможно», мы всегда говорим: «Ступайте и сделайте».
К примеру, рассмотрим процесс выработки стекла. В предыдущей главе мы описали способы, которые применяются на Гласмирском заводе. Принципиально приемы не отличаются от бывших в ходу сто лет назад. Искусство изготовления стекла имеет многовековую историю. Живы и традиции, в основном касательно той глиняной емкости, в которой стекло варится. Мы уже рассказали, что чан лепится вручную. Понятно, что механизмы помогают людям перемещать котлы от печи к станку и обратно. Построены конвейеры для транспортировки сырья, шлифовальные и полировальные механизмы, отменившие тяжелый ручной труд. Однако сама процедура, по сути, осталась прежней. Механика по мере возможности делает все то, что раньше выполнялось руками.
Однако следует отметить, что сам процесс выработки никогда как следует не исследовался, не были определены и его базовые элементы. Ручной труд всегда можно заменить машинным, но механическая сила не будет использована на 100 процентов. Самое трудное – начать все сначала и создать технологию, которая не просто передаст какую-то одну ручную операцию машине, а сделает так, что абсолютно все виды работ будут производиться машиной, а человек станет лишь наблюдать за ними. Вот это и есть «машинное» понимание индустрии – в противоположность «ручному».
Мы предположили, что возможно создавать зеркальное стекло в виде сплошной широкой ленты и совсем не применять ручной труд. Специалисты по производству стекла заверяли нас, что такие попытки совершались, но были неудачными. А мы доверили решение вопроса служащим, которые никогда раньше не имели дела со стеклом. Они стали экспериментировать в Хайленд-Парке и… столкнулись именно с теми трудностями, о которых нас предупреждали, и еще с целым набором других, о которых никто не знал, но в итоге они задачу решили. Небольшая компания в Хайленд-Парке выдает сейчас 2,5 млн кв. футов в год, а крупное предприятие на реке Руж, которое мы открыли, как только уверились, что способны выпускать первосортное зеркальное стекло, производит в год 12 млн кв. футов. Предприятие занимает около половины площади Гласмирского завода, а вырабатывает в два раза больше. Работников там лишь на треть больше, чем в Гласмире. Несмотря на то что мы не смогли укрупнить наши предприятия настолько, чтобы покрыть наши нужды, производимое самостоятельно стекло позволяет нам сэкономить не менее 3 млн долларов в год.
Идея нового метода в следующем. Сырье для изготовления стекла расплавляется в больших печах, причем каждая вмещает 408 т жидкой субстанции. При плавке сохраняется температура в 2500° по Фаренгейту, а при очистке – в 2300°. Печи заполняются песком, содой и другими химическими составляющими каждые 15 минут. Жидкое стекло потоком льется на плавно крутящийся железный барабан и потом идет под валом, который сообщает ему необходимую толщину и раскатывает в лист. Из барабана стекло попадает в так называемый лер, который двигается со скоростью 50 вершков в минуту. Он имеет 442 фута в длину и закаляет стекло при постепенно снижающейся температуре.
Именно конструкция лера являлась одной из самых нерешаемых задач, в которую упирались все остальные попытки улучшения процесса. Нам не удалось бы соорудить его, если бы мы не имели настолько богатый опыт создания конвейеров и точных механизмов. Действительно, не так просто сконструировать станок, который сможет поддерживать перемещающийся лист стекла в 442 фута длиной, который при этом охлаждается от температуры в 1400° по Фаренгейту (температура под валом) до такой температуры, когда изделие можно взять в руки. Перемещение конвейерной ленты должно быть совершенно плавным, и валы, по которым направляется стекло, должны быть настолько тщательно выровнены и столь точно рассчитаны, чтобы при прохождении всех 442 футов стеклянный лист не претерпел ни малейшего перекоса. Задача постепенного снижения температуры решается при помощи установки термостатических контролируемых газовых горелок на определенных участках конвейера.
В конце лера стекло режется на листы длиной 113 вершков. Это точно соответствует шести автомобильным окнам. Отрезанный лист стекла при помощи конвейера переносится к полировальным устройствам.
Стекла помещают в фиксирующие алебастровые рамки и затем подают к специальным столам, где начинают свою работу шлифовальные и полировальные диски. Через отверстие в центре чугунного шлифовального диска просачиваются песок и вода и направляются к краю диска. По мере движения стекла используется все более мелкий песок. В процессе шлифовки и полирования задействованы восемь сортов песка и шесть – полировального порошка.
Простота выработки и отказ от ручного труда обеспечивают высокий уровень безопасности.
По окончании шлифовки стекло омывается и перемещается к полировальным дискам. Их оборачивают войлоком и промокают смесью полировального порошка и воды. Будучи обработанным такими инструментами, стекло автоматически переворачивается на другую сторону и доставляется назад к другим шлифовальным и полировальным машинам. После всех процедур оно считается законченным и отполированным. Таким образом, в процессе создания стекла до него ни разу не дотронулась рука человека.
Люди также не касаются ни песка, ни всяческих видов полировального порошка. Точно так же не заняты они и при изготовлении пасты из песка и прочих ингредиентов. В вагон с доставленным сырьем из всасывающего агрегата вставляется тяжелый резиновый шланг. По этому шлангу смесь перемещается и попадает в приемник. Особый элеватор поднимает ее наверх и сыплет на другой конвейер, сконструированный специально для того, чтобы перемещать сырье в соответствующую приемную емкость.
Песок для шлифовки необходимо сортировать прямо в ходе применения. Процесс называется левигацией.
Поступивший на предприятие песок рассыпается по огромным емкостям, установленным поблизости от железнодорожных путей. По мере необходимости он омывается водой и ею же доставляется в колодец. Оттуда при помощи насоса песок передвигается по всему заводскому помещению к распределительным цистернам, укрепленным над печами, и поближе к шлифовальным и полировальным машинам. Из первых распределительных цистерн песчаная смесь по трубам, установленным под наклоном, стекает в первые шлифовальные машины. В процессе грубой полировки отработанный песок автоматически сбрасывается в специальные каналы под шлифовальными станками и оттуда посредством насосов подается в левигационную систему.
Очутившись в огромной емкости, полной воды, песок естественным образом сортируется. Крупные и тяжелые песчинки оседают на дно второй цистерны. Прочие зависают на различных уровнях, в зависимости от размеров. Вода, которая выливается через край второй цистерны, вымывает мелкие и легкие частички, перенося их в третью цистерну, где водно-песчаная смесь опять отстаивается. Вода, перелившаяся через край третьей цистерны, наполняет четвертую… Так продолжается до тех пор, пока вода не поступит в восьмую и последнюю цистерну, в которой уже будет находиться самый мелкий песок.
Песок, который поставляется шлифовальным станкам всеми цистернами, кроме второй, посредством насоса переносится из каналов назад во вторую цистерну, откуда он таким же путем распространяется дальше. От начала и до завершения шлифовки вода, переливающаяся через край, доставляет в каждую цистерну песок, который точно соответствует конкретным шлифовальным устройствам. Раздробленный гранитный камень, который используется последними шлифовальными станками, разделяется на виды точно таким же образом.
Операция представляется элементарной, и она в действительности довольно проста. Всякое тщательно просчитанное дело всегда незамысловато. Простота выработки и отказ от ручного труда обеспечили высокий уровень безопасности. Ранее выпуск стекла был делом рискованным. На наших заводах все иначе. На протяжении двух последних лет по причине несчастных случаев мы утратили менее одного часа на работника. В будущем показатель мы уменьшим.
Волокно и ткачество появились в незапамятные времена и потому оказались отягощены большим количеством норм и правил, которые стали уже, по сути, священными традициями. Текстильная индустрия первой применила механическую силу, но она также первой стала использовать труд детей. Многие владельцы текстильных фабрик твердо уверены в том, что дешевой выработки не бывает без низкооплачиваемого труда. Технический переворот в этой сфере индустрии поражал воображение, однако неизвестно, смог ли кто-либо из работающих в ней производителей рассмотреть вопросы текстильной промышленности без лишних предрассудков и устаревших норм.
Каждый день мы используем более 200 тыс. ярдов хлопчатобумажной материи и больше 25 тыс. ярдов шерстяной, и потому даже крошечная экономия на ярде за год дала бы нам приличные деньги. И вот мы несколько лет назад начали ряд экспериментов в сфере текстильной промышленности. Мы вовсе не собирались производить какие бы то ни было ткани, а искали возможность нивелировать колебания хлопкового рынка и заполучить относительно недорогую ткань необходимого качества.
Поначалу мы полагали, что хлопчатобумажные ткани совершенно незаменимы, поскольку для производства покрытия из искусственной кожи мы использовали только их. Мы открыли собственное текстильное предприятие и стали проводить эксперименты, но нас не ограничивали старые предубеждения, и вскоре мы задумались: «А в самом ли деле хлопчатые ткани – лучшее сырье для нас?»
Выяснилось, что мы использовали этот материал не потому, что он лучше всего соответствовал нашим целям, а потому, что его проще было найти. Лен, конечно, прочнее, так как крепость ткани прямо пропорциональна длине фибры, а льняная фибра – самая длинная. Хлопковые поля находились от Детройта в тысячах миль. Если бы мы стали производить хлопчатобумажные ткани, то пришлось бы оплачивать доставку хлопка-сырца, а также перевозку хлопка, обработанного под нужды автомобильной индустрии. В то же время лен хорошо растет в Мичигане и Висконсине – неподалеку от нас. К сожалению, выработка льняного полотна еще больше перегружена традициями, чем хлопчатобумажного, и в Соединенных Штатах эта отрасль почти не развивалась, в основном потому, что для производства льняной ткани полагалось абсолютно обязательным значительное количество ручной работы.
До того момента, как Эли Уитни открыл свой метод очистки, хлопчатобумажные изделия почитались предметами роскоши, и, собственно, хлопок был мало распространен. Ранее, как всем известно, семена из коробочек доставали вручную – работа не только тяжелая и дорогостоящая, но и весьма расточительная.
Волокна льна обычно трепались руками в Ирландии, Бельгии и России – везде, где используется материал. Способы его обработки сохранились практически неизменными со времен египетских фараонов. Именно поэтому льняные ткани так высоко ценятся, и поэтому же в Америке льном засевается так мало площадей. К счастью, в стране больше нет низкооплачиваемого труда в количестве, достаточном для того, чтобы культуру, которая требует ручной работы, превратить в прибыльную.
Мы провели ряд экспериментов в Дирборне, и наш опыт показал, что существует возможность обрабатывать лен при помощи механизмов. Наконец, этап экспериментов остался позади – коммерческая выгода от машинной переработки была доказана.
Мы все начали с самого начала и засеяли льном примерно 600 акров. Все делалось при помощи машин: мы ими пахали и обрабатывали почву, сеяли, жали, сушили и молотили и, в конце концов, очищать волокно тоже стали машинами. До этого никто ничего подобного не делал.
Мы не собирались на наших заводах брать в работу сырье, требующее ручного труда, а льняное волокно – всегда огромное количество дешевой работы, выполняющейся вручную.
Лен отлично выращивается в Мичигане и Висконсине, хотя в последнем лен культивировался преимущественно не ради волокна, а из-за семян – источника льняного масла. Лен, дающий прекрасное волокно, мало распространен в Соединенных Штатах, поскольку практически единственным рынком для него выступают зарубежные страны, где достаточно дешевого труда. Лен является крестьянской культурой, поэтому до войны основным его поставщиком была Россия, где люди привыкли жить на невообразимо маленькие деньги. Америка не проявляла интереса к этой культуре и потому не имела представления, какие площадки для нее наиболее пригодны. Судя по всему, лен нуждается в сыром климате. Однако в том случае, если в США производство льна начнет развиваться, мы, конечно, выведем разные виды растения – для всех климатических зон, так что всякий регион страны получит свой сорт льна, который ему будет выгодно выращивать.
Собственно, требуемое волокно льна находится на внешней стороне стебля, которая окружает плотную сердцевину. Поэтому бытовало мнение, что лен недопустимо жать, как пшеницу, поскольку стебли всегда надо укладывать параллельно друг другу, иначе перерабатывать его вручную станет еще труднее. Более того, уборка льна старым способом оставляла на земле большое количество волокна около корня. За рубежом, как правило, лен вырывают руками, а потом обмолачивают, добывая семена. При этом значительное количество ценных семян утрачивается. Итак, уже в самом начале процесса мы обратили внимание на два расточительных и затратных вида ручной работы – уборку льна и его очистку. Мы попытались использовать весьма сложный механизм для вырывания льна, но он вышел чересчур дорогим, и стало понятно, что более выгодно просто скашивать лен пониже. Учитывая механическую обработку сырья, больше нет необходимости выкладывать стебли параллельно, а неизбежная при этом потеря некоторой части семян в любом случае будет стоить нам меньше, чем ручная работа. Вот почему мы жали лен при помощи машин, а семена оставляли на растениях.
Еще одна традиционная процедура – вымачивание льна. Стебли вяжут в снопы и помещают в воду. Сверху кладут гнет, чтобы течение их не смыло. Когда растения подгниют, снопы достают из реки и высушивают под солнцем. Все манипуляции совершаются руками и являются крайне тяжелой и грязной работой, потому что запах гниющего льна вынести практически невозможно. А еще требуется большой опыт, чтобы понимать, в какой воде следует замочить лен и когда его пора доставать.
Самым же скучным, расходным и дорогостоящим из всех является следующий этап, так называемая трепка – процесс отделения волокна от сердцевины стебля.
Наш подход исключает эти затратные ручные работы. Сжатый лен мы выдерживаем на поле в течение нескольких недель, потом собираем его в стога, как сено. Мы не сушим растения на солнце, а при помощи конвейера пропускаем через печь. Конвейер же доставляет сухой лен в очистительный агрегат, который и представляет собой суть нашего метода, потому что полностью устраняет трепку вручную. Очистительный комбайн состоит из шести отделов, которые двигаются с разными скоростями. В итоге чудо-машина автоматически отделяет семена и сердцевину стебля и выдает волокно, часть которого будет использована для производства льняных тканей, а часть пойдет на пеньку.
Наш метод обеспечивает экономию труда и сырья. Очистительным механизмам все равно, в каком виде поступают в них растения, и больше не надо класть стебли в определенном порядке. По нашей информации, один очистительный комбайн, функционирующий восемь часов под контролем двух работников, обрабатывает столько же льна, сколько треплют руками десять тружеников в течение двенадцати часов.
Выпуск льняной материи позволяет производить более качественную продукцию и предоставляет фермерам доходную сельскохозяйственную культуру.
Произведенное волокно прядут. Пряжа выходит двух видов – для тонких и для плотных тканей. Выполняется это машинами, приобретенными за рубежом. Однако наши специалисты уже кое-что в них усовершенствовали, а как только мы полнее разберемся с работой, непременно будут внедрены и другие улучшения. В итоге мы добьемся того, что с одной стороны цеха будет загружаться лен-сырец, а с другой – выпускаться готовая к употреблению окрашенная льняная ткань. Одновременно станем производить искусственную кожу, так что весь технологический процесс окажется непрерывным.
Выпуск льняной материи мы расцениваем как важнейший эксперимент по той причине, что он не только позволяет нам производить более качественную продукцию, чем раньше, но и представляет фермерам доходную сельскохозяйственную культуру. Только наше производство нуждается почти в 50 тыс. акров в год, а лен отлично впишется в многопольный севооборот. Следовательно, фермеры возьмут на вооружение прибыльную культуру, и в стране, возможно, появится новая сфера индустрии. Причем мы еще не учли побочные продукты этого производства – льняное масло и пеньку, из которой получается замечательная мебельная набивка. Сейчас наши эксперты-химики работают с льняными отходами, пытаясь отыскать возможность превратить их в целлюлозу. Разновидности целлюлозных смесей могли бы применяться при создании лака для верха автомобилей, в качестве материала для ручек и для тех или иных деталей электрических приспособлений.
Обработка льна, а именно возделывание, прядение и производство ткани, способна и должна быть децентрализована, чтобы она могла стать дополнением к четко организованному сельскому хозяйству. В этом случае мы, само собой, подразумеваем зерновое хозяйство, в отличие от молочного или скотоводческого. Очищающие, прядильные и ткацкие фабрики следует размещать неподалеку от тех участков, где выращивается лен. Такая сфера индустрии может поддерживаться фермерами, которым настолько интересно промышленное производство, что они некоторую часть своего времени тратят на него.
Также мы стремимся изучить способы изготовления тканей из шерсти, которые нужны нашим предприятиям. Причем мы поступаем в соответствии с нашим принципом, добиваясь непрерывности производственного процесса. Так, мы выбрали одного молодого служащего и на три месяца отправили его на ткацкую фабрику, чтобы он научился всему необходимому, кроме ограничивающих правил. Пока что мы смогли внедрить лишь незначительные изменения и улучшения в уже имеющиеся машины. И хотя наше экспериментальное ткацкое предприятие выдает продукцию в катастрофически малых объемах по сравнению с потребностями, мы решили, что на шерстяных тканях сможем сэкономить почти тридцать процентов, а за год получим много миллионов долларов. Вообще если техника конструируется для производства лишь одного конкретного изделия и для этого изучается все необходимое, то экономия превосходит самые смелые ожидания.
Правообладателям!
Данное произведение размещено по согласованию с ООО "ЛитРес" (20% исходного текста). Если размещение книги нарушает чьи-либо права, то сообщите об этом.Читателям!
Оплатили, но не знаете что делать дальше?