Текст книги "Сегодня и завтра"
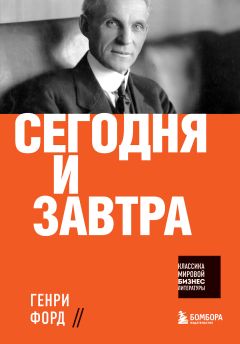
Автор книги: Генри Форд
Жанр: Зарубежная деловая литература, Бизнес-Книги
Возрастные ограничения: +12
сообщить о неприемлемом содержимом
Текущая страница: 4 (всего у книги 16 страниц) [доступный отрывок для чтения: 5 страниц]
Глава 6
Потребность в научных исследованиях
В сфере научных изысканий мы сосредоточены только на том, что имеет отношение к нашему главному делу. Мы уверены, что не располагаем достаточным потенциалом для более глубоких научных экспериментов и, скорее всего, это отрицательно сказалось бы на нашей основной деятельности, суть которой – выпуск моторов и создание автомобилей. Наша механическая лаборатория в Дирборне оснащена всем необходимым для проведения самых разных исследований. Вообще говоря, в основном мы применяем метод наглядного опыта Эдисона.
Тем не менее в таких обстоятельствах мы решаем довольно широкий круг вопросов, поскольку обязаны учитывать множество факторов, как то: уменьшение поставок по причине исчерпанности их источников, экономия ресурсов и создание современных материалов и топливных средств, которые пришли бы на смену тем, что используются сейчас. Зачастую мы не сразу воплощаем в жизнь наши открытия, а ждем удобного момента, когда условия рынка станут более подходящими. К примеру, в случае выхода стоимости газолина за допустимые рамки, его дальнейшее использование стало бы невыгодным, и мы заменили бы его новым веществом. Однако наш главный принцип – создавать один продукт наилучшим способом и не отвлекаться на другие идеи. Работа над этим единственным изделием вынудила нас заняться исследованиями во многих иных сферах.
Мы бережно расходуем материал и труд. Практически еженедельно вводится какое-либо усовершенствование в работе. Одни новшества не слишком значительны, другие чрезвычайно важны, однако наш метод производства не меняется. Примечателен факт, что самая существенная экономия порой выходит при производстве деталей, создание которых нам казалось едва ли не идеальным.
Однажды выяснилось, что, расходуя на два цента больше сырья при производстве определенной детали, можно уменьшить ее общую стоимость на 40 %. В этом случае затраты на материал для детали возрастали на два цента, но производилась деталь настолько быстрее, что общая ее стоимость, ранее исчислявшаяся 0,2852 доллара, теперь составляла лишь 0,1663 доллара (наши расходы всегда рассчитываются до десятитысячных долей). При внедрении данного подхода понадобилось десять дополнительных механизмов, но мы выиграли около двенадцати центов на изделии, так что затраты сократились приблизительно в два раза. И поскольку ежедневно выпускалось по десять тысяч деталей, то экономия в целом составила 1200 долларов в день.
В самом начале нашего дела и довольно долго после для производства рулей мы использовали дерево, что было очень невыгодно, так как приходилось брать исключительно наилучшие сорта древесины, а идеальной точности никакие операции с этим сырьем не гарантируют. В то же время на Дирборнском сельхозпредприятии у нас скопилось большое количество соломы, которая не использовалась или отпускалась по бросовой цене. Из нее мы начали вырабатывать уникальное вещество, названное фордитом, которое внешне напоминает плотную резину. В настоящее время из этой соломы делаются оправа руля и примерно сорок пять деталей авто, имеющих отношение к работе электрических приборов. Теперь нам нужно так много соломы, что производственные мощности фермы покроют лишь десятимесячную потребность. Так что мы вынуждены приобретать этот материал у других.
Переработка соломы происходит так. Солома, резина, сера, силикат и другие компоненты смешиваются и расфасовываются по 150-фунтовым дозам. Эта смесь направляется в специальные машины, где она вымешивается горячими валиками на протяжении сорока пяти минут. Образовавшаяся масса движется по трубам и выходит через отверстие диска, как сосиски из мясорубки. Далее массу нарезают на ленты длиной 52 дюйма, после чего раскатывают на полосы, которые весьма напоминают резину и используются для покрышек авто. Полосы укладывают в форму и поддают гидравлического давления в 2000 фунтов на квадратный дюйм, прогревая паром в течение примерно одного часа. Готовые рулевые колеса еще мягкими достают из формы, однако очень скоро они приобретают твердость кремня, и качество это со временем не меняется. Потом они доставляются в другие цеха, где их обтачивают и полируют. По окончании на руль накладывают прессованный стальной «паук», или перекладину, и надежно фиксируют специальным автоматом, который сперва сверлит маленькое отверстие, а потом вкручивает винт. Теперь рулевое колесо готово и может устанавливаться на автомобиль.
Таким образом мы выручаем около половины стоимости древесины и сберегаем природу.
Автомашине для верха, гардин и обивки необходимо примерно 15 ярдов искусственной кожи пяти разных видов. Применение натуральной кожи было бы абсолютно неосуществимо, поскольку, во‐первых, стоило бы чересчур дорого, а во‐вторых, не нашлось бы должного количества животных. Наши специалисты приложили массу усилий для создания искусственной кожи, которая нас устроила. Эксперименты заняли от пяти до шести лет. Сперва надо было придумать смесь для лакирования ткани, которая выступала основой кожи, а потом сделать непрерывным процесс создания материала. Своя выработка кожи дает нам свободу от рынка (наша основная цель), но и экономит больше двенадцати тысяч долларов в день.
Сейчас процесс создания искусственной кожи таков. Ткань доставляется в особые печи, представляющие собой ряд башенок. Внизу каждой башенки установлена цистерна с лакировочным составом. Его выливают и ровным слоем распределяют на ткани при помощи ножа, удаляющего излишек. Полностью покрытая смесью ткань подается на башенку на высоту тридцати футов при температуре до 200° по Фаренгейту. Вниз она опускается абсолютно сухой. Во второй печи она заливается следующим слоем, высушивается на башенке, направляется в цистерну третьей печи и так далее до того момента, пока ткань-основу не покроют семь слоев специального состава.
Потом полученный материал взвешивают, чтобы оценить количество лака, необходимого на один ярд, и переводят под пресс, где давлением в 700 тонн делается оттиск рисунка. В последней печи основу покрывают верхним слоем, который придает ей блеск и эластичность.
Лак представляет собой смесь касторового масла и черного пигмента, в который добавлен хлопок, обработанный серной кислотой и растворенный в смеси этила и бензола. Вещество весьма быстро улетучивается, что и способствует легкости высушивания. В печах этил, алкоголь и бензол превращаются в пары, которые накапливаются в специально сконструированных агрегатах. Испарения пропускают через уголь кокосовых орехов до полного насыщения угля. Потом последний обрабатывают паром, который вместе с испарениями попадает в конденсатор, где они и разделяются. Вот так мы смогли добиться сохранения 90 % паров. Производственный процесс протекает без перерывов. Едва рулон ткани заканчивается, его край пришивают к следующему рулону, и покрытие смесью идет без пауз. Безостановочность процесса – чрезвычайно важное условие, потому что даже маленькая задержка позволила бы составу затвердеть.
В помещении нет ламп, искусственный свет попадает в него снаружи. Это сделано во имя пожарной безопасности. Каждый механизм прочно закреплен, и нами приняты такие же противопожарные меры, как и на производстве взрывчатых веществ. На нашем предприятии не произошло ни одного несчастного случая.
Первостепенное значение приобретает подготовка стали, потому что при увеличении прочности можно снизить вес деталей. Однако обработка стали весьма непростое дело: если изделие будет излишне мягким, оно быстро сотрется, а если чересчур твердым – разрушится. Уровень требуемой твердости зависит от предназначения того или иного элемента. Это представляется само собой разумеющимся. Однако производство значительного числа деталей, каждая из которых имеет свою степень твердости, – отнюдь не простая задача.
Раньше необходимую степень твердости пытались угадать. Это не наш путь, мы не будем гадать и не оставим ни один этап производства на усмотрение человека. Мы считали наши способы прокалки достаточно хорошими. Они и были вполне хороши – для своего времени, так как операции выполнялись работниками с минимальной подготовкой, а механическое регулирование позволяло выпускать однородную продукцию. К сожалению, в помещениях, где сталь закалялась, труд был невероятно тяжел, а мы не любим ничего подобного в наших цехах. Тяжелый труд – удел машин, а не человека. А кроме того, прямые детали, например оси, охлаждались неравномерно, и по окончании закаливания их следовало выпрямлять, что вело к росту затрат.
Одному молодому человеку мы предложили исследовать и улучшить все, что имеет отношение к закалке стали. Он проводил опыты на протяжении года-двух и таки добился успеха. Ему удалось сократить количество работников, участвующих в процессе, а также создать центробежную закалочную машину, что позволило достичь равномерного остывания прямых деталей. Теперь они не искривляются, их не надо выпрямлять. Крупнейшей инновацией оказалась замена газовой печи на электрическую. У старых газовых печей трудились шесть работников и мастер, они производили в час тысячу соединительных прутьев, при этом происходило только вытягивание. Теперь их сменили две электрические печи, которые вытягивают и закаливают тысячу триста прутьев в час и обслуживаются лишь двумя работниками: один подает сырье, а другой убирает его.
Чрезвычайно важные условия производства – безостановочность процесса и соблюдение противопожарных мер.
Оси прокаливают в большой двухкамерной печи. Особый цилиндр медленно продвигает оси в нижнюю камеру печи с временным интервалом в одну минуту. Прохождение осью камеры занимает 28 минут. На протяжении этого времени ось выдерживается при 1480° по Фаренгейту. Контроль температуры осуществляется при помощи автоматического устройства.
В тот момент, когда оси медленно появляются из дальнего проема печи, работник выхватывает их щипцами и по одной перемещает в другой агрегат. Там они опускаются в едкий раствор. Машина вращает их, и благодаря этому вся поверхность оси практически тут же остывает. Такая процедура гарантирует одинаковую твердость и исключает повреждения, которые могут возникнуть из-за неравномерного остывания.
Покинувшие раствор оси при помощи конвейера доставляются в верхнюю камеру печи и перемещаются обратно к входу при температуре 680° по Фаренгейту. Этот этап длится 45 минут. После извлечения оси верхним конвейером доставляются к другим станкам для завершающей обработки.
Нововведения поначалу представляются не слишком значительными, но, поскольку теперь мы не выпрямляем оси после закалки, нам удалось за четыре года сэкономить примерно тридцать шесть миллионов долларов.
Также мы разобрались в технологии производства электрических батарей и вскоре смогли обеспечить себя ощутимо более дешевыми батареями, чем те, что мы приобретали у других.
Производство автомашины включает 162 операции ковки. Поэтому мы сформировали специальное отделение для ковки, в котором каждый день проходят обработку больше двух миллионов фунтов стали и где путем постоянных усовершенствований и экспериментов мы сумели сэкономить много миллионов долларов. Несколько сложных операций мы собрали в одну и, вместо того чтобы ковать сталь при помощи молотов, возложили этот труд на механизмы, которые попросту вдавливают ее в специальные формы. Мы всегда стараемся свести к минимуму все последующие мероприятия.
В одном из таких станков есть массивные, расположенные вертикально пуансоны, которые опускаются на горячий стальной брус. Чтобы придать последнему требуемую форму, необходимо выполнить три или более манипуляций. Сперва брус оказывается между верхними пуансонами, которые, собственно, и производят формовку, другими словами, делают короче и толще фрагмент стального бруса – до нужных размеров. Изредка требуется два действия. Прочие пуансоны сообщают брусу определенную форму, просверливают его, обтачивают и обрезают. Существуют огромные станки, в которых работают девяносто шесть паровых молотов. Самый маленький из них снабжен тараном и пистоном, которые весят 800 фунтов, а самый большой оснащен такими же устройствами весом 5600 фунтов.
Пуансоны находятся в наковальнях и обделочных молотах. Всякий молот оснащен пуансоном, который выполняет полную фазу некоего этапа производства – как в штамповальных станках. Работа между молотами не распределяется. При выработке коленчатого вала раскаленный брусок стали располагается поперек наклонного пуансона на левой стороне наковальни. Удар определенного пуансона на обделочном молоте изгибает брус. Затем уже изогнутый брус перемещается направо. Несколько ударов второго пуансона завершают процесс, в результате которого выходит коленчатый вал. Задача молотов этим ограничивается. А производимая деталь поступает к формовочному прессу, и коленчатый вал обретает законченный вид в штамповальном станке.
Для выработки ряда деталей весь брус не нужен. Тогда к молотам обрабатывающего станка крепятся специальные резаки, и ударом молота сформированная деталь отсекается от остального бруса. Другую, более мелкую ковку проделывают при помощи молотов, чьи формующие матрицы абсолютно идентичны, и так получают сразу несколько экземпляров.
Последовательность, в которой выполняются этапы ковки, меняется в соответствии со свойствами той или иной детали. К примеру, оси направляют сперва в штамповальный станок, который сообщает им основную форму, удлиняет и разрезает концы. Потом их доставляют к молотам. Поскольку оси очень длинные и не помещаются под молотом полностью, то сперва куют одну их половину, а затем другую.
Восемьдесят отделочных прессов очищают изделия от шероховатостей, возникающих при ковке. Большая часть прессов соединяется с конвейерами, и таким образом устранение неровностей происходит безостановочно. Маленькие детали также оказываются на конвейере. На выходе из здания выкованные изделия с конвейера перемещаются в коробки. Другой конвейер доставляет обрезанные куски металла в специальный вагон, который тоже размещается снаружи.
Пуансонам отделочного пресса придают форму изделия, а в матрице делается отверстие, в точности совпадающее с его очертаниями. Заготовка под давлением пропускается через отверстие матрицы, и всякие шероховатости ею просто отсекаются.
Для производства изделий разной величины применяют особое оборудование. Так, для выработки осей сконструирован особый автомат.
Создание колонки управления на специально предназначенном для этого штамповальном станке происходит с точностью до 1/32 дюйма.
При выпуске зубчатки тройного зацепления теперь задействованы тринадцать штамповальных устройств. Прежде для создания детали нужно было выполнить три отдельные поковки. Ныне она производится из одного стального бруска.
Самым сложным в процессе штамповки является производство гнезда для подшипника карданного вала. Оно делается при помощи двойного штампования с обоих концов. Операцию невозможно выполнить простым механизмом.
Вращающаяся шарошка для обработки стали также представляет собой достаточно любопытный прибор.
Литье алюминия в матрицах должно было обеспечить нам существенную экономию. Много лет ушло на создание подходящего нам способа. Очень долго полагали, что литье в матрицах – задача нерешаемая. Прежний способ литья в земляных формах допускал проникновение воздуха сквозь толщу земли, из-за чего раскаленный металл растекался, и отлитый продукт имел множество дефектов. Позднее изобрели метод нагнетания снизу в матрицы жидкого металла. Матрицу укрепляют прямо над емкостью, в которой находится металл в расплавленном состоянии. По сути, она представляет собой крышку. В момент литья жидкий металл под давлением воздуха через фидер попадает в матрицу и заполняет ее. Из заполненной металлом матрицы через крошечные отверстия вытекает воздух. В полных матрицах начинает происходить поверхностное затвердевание литья. Таким образом, воздух вытесняется первым же потоком расплавленного металла, а поскольку он может попасть в матрицы исключительно через фидер, риск появления воздушных пузырей сведен к нулю, и отлитое изделие не имеет раковин и прочих недостатков.
Мы в чрезвычайно больших количествах потребляем изолированную медную проволоку, а она весьма дорога. Вот почему мы сами начали ее выпуск и сегодня вырабатываем приблизительно сто миль проволоки в день. Для этого мы применяем обычную проволочно-тянульную машину, но с рядом новшеств и упрощений, которые дают возможность производить нужное нам изделие. Создание изолированной проволоки берет свое начало с медного прутка диаметром 5/16 дюйма и завершается обмоточной проволокой. Пруток протягивают сквозь девять постепенно сужающихся проемов железных матриц. Получившаяся проволока выходит из последней матрицы и со скоростью 725 футов в минуту наматывается на катушки. Ее диаметр составляет примерно 3/32 дюйма.
При протягивании прутка выделяется достаточно большое количество тепла, его приходится компенсировать водой, циркулирующей вокруг матриц. Данный прием также способствует сохранению твердости продукта. А для того чтобы вновь размягчить проволоку, что требуется для последующей протяжки, ее отжигают в специальной электрической печи.
Для соединения отдельных фрагментов предпочтительнее использовать заклепки, потому что они обеспечивают большую крепость по сравнению с винтами.
Проволоку помещают в емкость с водой на столе, который вращается до того момента, пока она не будет доставлена к топке. Потом проволоку загружают в воздухонепроницаемый цилиндр и оставляют там на час при температуре 1045° по Фаренгейту. Воздух откачивают, чтобы не произошло окисление.
Станки для изготовления проволоки оборудованы восемью алмазными матрицами с отверстиями, сквозь них она и протягивается, при этом каждый алмаз сокращает диаметр производящейся проволоки на несколько тысячных дюйма. Алмазы, стоимостью триста долларов каждый, практически не стираясь, используются в течение шести месяцев. Финальная матрица с отверстием в 0,044 дюйма выдает 12 gauge (мера измерения проволоки, которая укладывается в особые клетки (gauge), принятая на заводах Форда. – Прим. ред. 1-го изд.) чистой проволоки, предназначенной для изолирования.
Изоляционный материал представляет собой пять слоев диэлектрической эмали и хлопчатобумажного покрытия. Процесс эмалирования является последовательным и автоматизированным. Над 80 катушками проволоки размеренно трудятся четверо рабочих. Они их разматывают и сматывают, нанося слои эмали при температуре 845° по Фаренгейту. При этом каждый дюйм готовой проволоки проверяется на разрыв эмали и дефекты, а потом изделие направляется к обматывальным агрегатам.
Отрезки недостаточно хорошо прокатанной проволоки удаляют, спаивают оставшиеся концы и снова эмалируют.
На прядильных станках для изолировочных машин производят 18 кусков пряжи, которые наматываются на катушки. Когда между катушками проходит эмалированная проволока, они разматываются, и пряжа, будучи натянутой очень туго, обматывает ее. Всего функционирует 72 веретена, их контролируют четыре работника. Станки абсолютно автоматические.
Нельзя не признать, что отвертка – старинный и важный инструмент, однако один рабочий с единственной отверткой не соответствует современным способам производства. Он едва ли сможет оправдать свой труд. Впрочем, мы не отказываемся от отвертки. Сегодня мы задействуем шестнадцатишпиндельный станок для отверток, и он в ходе выполнения одной процедуры вставляет 16 винтов в зубчатку стартера.
При подходе передачи конвейер присоединяет болты и прокладки ко всем 16 магнитным выступам, болты стягиваются, и деталь изделия оказывается скреплена с маховиком, который поддерживает магниты в требуемом положении. У каждого конца магнита размещается катушка из белого металла и магнитный хомутик. Полоса меди пропускается через проем магнитного хомутика, продвигается между концами магнита, через катушку из белого металла и сквозь крошечное отверстие в маховике и попадает в зубчатку стартера. Вот теперь все можно стягивать винтами и болтами.
Передача плавно перемещается под шпиндельным станком для отверток, и при помощи рычага сцепочного механизма собирается производимая деталь.
Существует особое оборудование, позволяющее подвести винты прямо к шпиндельному станку для того, чтобы ввинтить их в маховое колесо. Отвертки вращаются благодаря шпиндельному механизму, высота которого регулируется. Каждая из них помещена в пробку, которая вставляется через головку винта. В момент, когда стойка рычага собрана, она нацеливает отвертку в паз. Когда введен винт, возрастает фрикция. Для дальнейшего вращения винта требуется большее усилие, чем было достаточно для начальных оборотов. Когда винт оказывается на месте, фрикционное сцепление, находящееся в «конусе», скользит, действие останавливается, и пазам для винтов поломка не грозит. От шпиндельного станка для отверток передача идет к восьмишпиндельному станку для сбалчивания, действующему по тому же принципу, что и первый. Он стягивает болты, которые проходят через магнитные выступы в маховик. До того как был запущен шестнадцатишпиндельный станок для отверток, шесть рабочих занимались стягиванием винтов – сейчас операция выполняется одним работником и продолжается считаные секунды.
Также следует упомянуть об использовании заклепок вместо винтов для соединения отдельных фрагментов. Заклепки предпочтительнее винтов, потому что они обеспечивают большую крепость. Мы начали широкое применение заклепок, когда сами освоили их выпуск. В настоящее время мы ежедневно используем 3 млн заклепок.
Способы отливки бронзовых втулок все время изменялись и совершенствовались – люди стремились избежать тяжелого ручного труда. Длилось это до момента открытия литейной.
Обычно плавление металла происходит в 12 электрических печах. В каждую из них помещают примерно одну тонну сырья, и процесс нагревания продолжается приблизительно 70 минут. Печь стоит неподвижно, пока металл не станет жидким. Затем происходит небольшое колебание вперед-назад – для того чтобы смесь стала однородной.
По достижении расплавленным металлом температуры в 2200° по Фаренгейту берут на анализ лабораторную пробу, чтобы исключить погрешности литья.
Применяемые для литья маленьких втулок модели соединяются по четыре или по пять штук в одну для облегчения процесса. В этом случае для получения значительного числа втулок требуются лишь одно плавление металла и только одно отливание. Шипы, скрепляющие формы, сконструированы так, чтобы литье происходило быстрее.
На смену ручному просеиванию земли пришли электрические сита, и теперь формы уплотняются при помощи пресса. Чтобы получить нужную форму, земля должна быть тщательно просеяна и хорошо утрамбована. С заданием механизм справляется намного лучше, чем вся бригада работников. Форму высушивают на металлическом столе с использованием электричества – в процессе выделяется большое количество тепла, что вредно для здоровья людей. Для защиты от жары проведена целая система воздуходувов, обеспечивающая поступление свежего воздуха непосредственно к рабочим местам.
Для того чтобы можно было легко доставать литье из формы, последнюю делают из двух соединяемых фрагментов. Формы всегда покрывались особым веществом из ликоподиума, в состав которого входят споры этих цветов, встречающихся только в России. Стоило все чрезвычайно дорого, и мы заменили его сравнительно дешевым средством, которое дает подобный эффект. Воздушным вибратором и с помощью элементарного зубчатого устройства форма разъединяется без малейшего повреждения.
Готовая форма посредством конвейера доставляется к месту литья и заполняется расплавленным металлом. Прежде требовалось устанавливать на формы весьма тяжелые грузы, чем и были заняты наименее квалифицированные работники. Ныне процедура легко выполняется благодаря обычному хомуту, который вращается на шпинделе, поддерживающем платформу с формой. Потом формы разъединяют, достают застывшее литье, а прочие детали, которые применялись для соединения форм, этим же конвейером направляются в формовочную.
Втулками загружается большая цилиндрическая мельница, и они вращаются там, пока абсолютно не очистятся от налипшей формовочной земли. Потом литье оказывается на снабженной волнистыми каналами платформе, которая доставляет его к шлифующему диску – для устранения наплавов металла. Далее можно начинать окончательную обработку литья, но к ней приступают, только получив от лаборатории результаты исследования излома детали. Литье, произведенное при разных температурах металла, не перемешивается между собой до получения результатов лабораторного анализа. Затраты на транспорт и перебои в работе сведены к минимуму из-за расположения трех отделочных цехов прямо рядом с литейной.
Все обрабатывающие станки функционируют в автоматическом режиме и совершенно точно. Двойной автоматический резец настолько тщательно в течение восьми часов отделывает шесть тысяч втулок, что лишь 1,3 % изделий требуется корректировка. Автоматические развертки завершают отверстие непосредственно в грубом литье – проверка происходит автоматически. Резец-автомат характеризуется определенными скоростью и измерениями оправы. Посредством зубчатки каждые несколько секунд изменяется направление вращения, что предпочтительнее, чем если бы станок работал впустую, потому что в этот момент готовая втулка заменяется следующей, необработанной. В дальнейшем действуют еще два механизма, между которыми, словно челнок, двигается резец.
Сверлильные станки обладают своими опасными особенностями – мелкие осколки металла могут травмировать руки работника. На наших предприятиях подобные ранения невозможны. Для защиты сотрудников понадобилось разместить под сверлящим патроном специальную емкость, в которой скапливалась бы металлическая стружка. Вставленное сверло толчком фиксируется на месте. Высверливаемую втулку окружает воронка, а следующая поступает через канал намного быстрее, чем происходило бы при подаче вручную. Автоматический сверлильный инструмент имеет два резца, поскольку выполняются две процедуры – высверливание и резка. Для сортировки или инспекции измерений втулок используется машина с тремя парами дисков, сконструированными так, что первая пара отбирает чересчур длинные втулки, вторая – выбирает втулки нормальных размеров, а третья пара дисков собирает «коротышек». Процесс обеспечивается промежутком между дисками, причем с точностью до десятитысячных дюйма.
Затем втулки перемещаются на большое шероховатое колесо, направляющее их к выходным дискам. Проверка их наружного диаметра делается очень просто. Два полированных точеных барабана располагаются наклонно и параллельно друг другу. Они имеют коническую форму, поэтому расстояние между ними постепенно растет. Под действием силы тяжести втулки падают на барабаны и начинают вращаться. Двигаясь под уклон, они смещаются в промежуток между барабанами. Годные втулки попадают в одну воронку, а слишком короткие – в другую. Что это дает?
В 1918 году в цехе за восемь часов рабочего дня выпускали в среднем 350 готовых втулок на одного работника, брак составлял примерно 3 %. Сегодня в среднем изготавливается 830 втулок на одного сотрудника при браке лишь в 1,3 %.
В процессе выпуска рессор достигнуты значительные успехи как в плане точности производства, так и в экономии труда. Рессорные болты делаются настолько качественно и точно, что они подходят для всех соответствующих рессор, причем создаются и закаляются в масле в ходе всего одной операции. Потом их подвергают воздействию азотнокислой соли при температуре 875° по Фаренгейту, а затем они термически обрабатываются и используются. В 1915 году четверо рабочих ежедневно производили 50 рессор. Ныне 600 работников изготавливают 18 тысяч рессор в день.
Правообладателям!
Данное произведение размещено по согласованию с ООО "ЛитРес" (20% исходного текста). Если размещение книги нарушает чьи-либо права, то сообщите об этом.Читателям!
Оплатили, но не знаете что делать дальше?