Текст книги "Дом на колесах. О чем не расскажут в автосалоне"
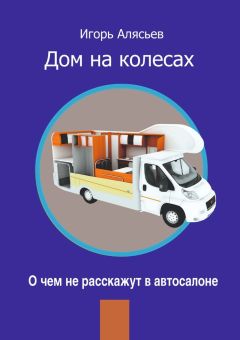
Автор книги: Игорь Алясьев
Жанр: Книги о Путешествиях, Приключения
Возрастные ограничения: +12
сообщить о неприемлемом содержимом
Текущая страница: 4 (всего у книги 14 страниц) [доступный отрывок для чтения: 5 страниц]
Когда этапы установки стен закончены, то начинается монтаж крыши. Соединение боковых стен и крыши различное. В одном варианте стена может крепиться саморезами через клеевую основу, также, как и пол. В другом же, крыша может загибаться в сторону стены и склеиваться. Все зависит от конкретного производителя автодома. Декоративный профиль из пластика закрывает образовавшийся шов и проклеивается водонепроницаемой мастикой. А для более плотного прилегания стены к крыше используют промышленные клеи. Кроме того, в отдельных случаях, дополнительно, она может фиксироваться к крыше на саморезы.

Рисунок 3.19. Установка крыши. Слева: крыша загибается в стороны стены и имеет сточную канавку для слива дождевой воды, которая может попасть под декоративный пластик. Пластиковая накладка будет приклеен позже. Справа: монтаж крыши на автодом «Hymer».
«Corado», «RolIer Team», Sunlight» и некоторые другие бренды могут использовать иную технологию монтажа крыши жилого фургона. Делается это следующим образом: сначала на несущие стены, задней части автодома, там, где они ровные т.е. до подъема алькова, монтируется прямая панель крыши. Далее на автодоме собирается и монтируется альков, собранный из двух кусков сэндвич-панелей сложной формы, которые стыкуют с ровной поверхностью крыши. Образовавшиеся в таком варианте стыки закрывают алюминиевыми порожками. Все стыки декорируются пластиковыми накладками.

Рисунок 3.19. Слева: наклеивание пластика на альков. Справа: крыша, готовая к наклейке пластика.
Завершающая стадия производства автодома включает в себя оклейку в фирменные цвета бренда – производителя, проверку всего оборудования жизнеобеспечения, а также приемку готового изделия специальной комиссией.

Рисунок 3.20. Последние, заключительные работы. Слева: готовый дом на колесах бренда «Capron». Справа: автодом «Corado».
Производство интегрированных автодомов «класса А».
У многих Европейских производителей, в производственной линейке, есть автодома «класса А». Высочайший уровень комфорта как для водителя, так и для пассажиров, дорогая отделка салона, отличная теплоизоляция и максимальный комфорт в путешествии присущ только этим автодомам. Над внешним видом и внутренним наполнением жилого пространства работают лучшие авто дизайнеры. В итоге интерьеры таких домов на колесах, да и сам внешний вид у каждой модели становится индивидуальным и уникальным. Такие дома на колесах легко отличить в автомобильном потоке.

Рисунок 3.22. Автодом «Hymer» «класса А» Европейского производства.
С каждым годом автодома «класса А» набирают популярность. По сути – это гибрид жилого прицепа и автомобиля. Поэтому изготовление такого дома на колесах во всех стадиях очень похоже на производство жилых прицепов.1818
Более подробно о производстве жилых прицепов можно прочитать в «Жилой прицеп от А до Ы» И. В. Алясьева.
[Закрыть]
В самом начале для «класса А» выбирается шасси, на котором в дальнейшем будет построен автодом.1919
Шасси для таких автодомов могут быть как передне, так и заднеприводными.
[Закрыть] Колесная база представляет собой готовое изделие, предназначенное только для домов на колесах и отвечающее предъявляемыми к ним требованиям. А именно: она очень напоминают раму грузовика, поскольку есть лонжероны, и необходимые элементы для обеспечения жесткости всей конструкции. Поперечные усилители рамы для монтажа жилого фургона устанавливают по конкретному запросу со стороны производителя автодома. Кроме того, такие шасси поставляются без кабины и сидений водителя и пассажира.

Рисунок 3.23. Стандартное шасси для постройки интегрированного автодома: слева переднеприводное «Fiat – Ducato», справа – рама заднеприводного «Iveco-Deily».
Управляемость автодома на таком шасси, а также крены при повороте – очень важный момент, который учитывается при постройке интегрированного дома на колесах. Ведь наклоны кузова часто обусловлены фургоном, который либо высокий, либо слишком широкий, по сравнению с основанием, на котором он установлен.2020
Если автодом строится на готовой раме грузового шасси.
[Закрыть] Чтобы убрать эти недостатки, рама занижается и облегчается. При этом заднюю колею расширяют до 1980 мм, при колесной базе 3 800 мм.
В технологическом плане, производство полностью интегрированных автодомов «класса А», отличаются от построения полу интегрированных домов на колесах «класса В». Для этого на заводе-производителе предусмотрена отдельная сборочная линия.

Рисунок 3.24. Слева: установка и подключение оборудования снизу рамы шасси. Справа: монтаж мебели.
Все основные операции проходят в том же порядке, что и в производстве полу интегрированных домов: установка мебельных модулей, душевой кабины, прокладка всех необходимых коммуникаций: отопления, газо-водоснабжения. Поэтому мы не будем подробно останавливаться на этих этапах производства Особенность заключается в самих боковых сэндвич-панелях, которые представляет собой единое целое с кабиной водителя.

Рисунок 3.25. Слева – монтаж мебельных модулей. Справа – монтаж системы воздушного отопления и установка холодильника

Рисунок 3.26. Слева – установка и монтаж боковой панели. Справа – задняя стенка, установленная на место.
Отдельно изготавливается передняя часть автодома, где бампер объединен с решеткой радиатора. Так как кабина интегрирована с жилой зоной, то и комплектующие этой части автодома индивидуальны. Например, огромное лобовое стекло, специальные большие габаритные зеркала, и индивидуальные наружные декоративные накладки: такие как решетка радиатора. Она производится из ABS-пластика, предавая внешности автодома яркую индивидуальность. Такой дом, как уже говорилось, становится ярким, уникальным и отличным от других брендов.

Рисунок 3.27. Слева – накладка на шасси кабины. Справа – начала монтажа накладки.

Рисунок 3.28. Слева – монтаж опускающейся кровати. Справа – почти готовый автодом.

Рисунок 3.29. Слева – установка фаркопа. Справа – готовый автодом «Dethleffs».
Производство автодомов «класса В+ и В++»
Цельнометаллический фургон.

Рисунок 3.30. Автодом «класс В+»
Перед началом переоборудования цельнометаллического грузового фургона в автодом, производитель выбирает шасси, которое он будет модернизировать. Почти 80% домов на колесах этого класса изготавливают на базе «Fiat-Ducato» и его «одноклассниках»: «Citroën Jumper» и «Peugeot Boxer». В меньшей степени на шасси «Mercedes-Benz Sprinter», и еще менее на «Iveco-Deily» и фургонах других фирм. И дело тут не в переднем или заднеприводном шасси автофургона, хотя это тоже влияет на престиж и конечную цену автодома, а в геометрических размерах кузова. Если посмотреть на «Fiat-Ducato» сзади, со стороны распашных дверей, то кузов представляет собой форму квадрата, т.е. сужение кузова к крыше практически нет. У других марок цельнометаллических фургонов происходит заметное сужение в верхней части грузового фургона, т.е. ширина пола больше, чем крыши. Поэтому только в цельнометаллическом фургоне «Fiat-Ducato» можно расположить спальные места поперек, от стенки к стенке, не производя дополнительных изменений в металлическом кузове. А ведь это очень важно в готовом ограниченном пространстве. Впрочем, и на других шасси цельнометаллических фургонах тоже можно оборудовать спальное место в задней части, поперек кузова. Но он будет слишком коротким, чтобы поместиться там взрослому человеку и подойдет разве лишь для ребенка. Для сравнения приводим таблицу внутренней верхней ширины у популярных моделей цельнометаллических фургонов. Из нее видно, что самый широкий кузов у фургона «Fiat-Ducato». Но надо иметь ввиду, что это только «чистый размер» от борта до борта.

Рисунок 3.31. Ширина кузова у разных марок цельнометаллических фургонов.

Рисунок 3.32. Слева спальное место у «Fiat-Ducato». (Слева на фото видно углубление для увеличения поперечных размеров спального места. Справа – «Mercedes-Benz Sprinter». (Видно, что спальное место узкое. Двухместная кровать с продольным расположением спальных мест).
Любому дому на колесах необходимо утепление, а уж в металлическом фургоне и подавно, ведь металл сильно нагревается на солнце, и так же быстро остывает на морозе. При утеплении кузова толщиной на 50 мм, по периметру, общая ширина жилой зоны уменьшится на 100 мм, и полезное пространство сузится до 1770 мм у «Fiat-Ducato». А на других моделях и того меньше! На такой кровати спать будет крайне неудобно. Именно поэтому в «Fiat-Ducato», в месте, где организованы поперечные спальные места, утепление уменьшено до 10 мм. И в этих местах вклеиваются специальные вставки с углублениями. Но некоторые производители, для установки поперечного спального места и увеличения полезного жилого пространства, сами расширяют заднюю верхнюю часть в цельнометаллических фургонах. Например, в «Mercedes-Benz Sprinter», в боковых стенах железного кузова, где обычно предусмотрена врезка окон, делаются вырезы и в них вклеиваются стеклопластиковые муляжи окошек, которые выпирают наружу, но не выходят за внешние габариты автофургона. Тем самым увеличивается поперечный размер спального места.

Рисунок 3.31. Слева – планировка на базе фургона «Fiat-Ducato». Справа – «Mercedes-Benz Sprinter», с увеличенной шириной фургона. (Представлен модельный ряд фирмы «LaStrada» моделей «AVANTI» и «REGENT»).
Итак, на завод поступает цельнометаллический фургон, который будет переоборудован в «Kastenwagen». В работу берутся автомобили разной длины, и, по возможности, с максимально высокой крышей, если речь идет о серийном производстве. Переоборудование начинается с утепления кабины водителя. А для этого: демонтируется весь внутренний пластик, обивки дверей и перегородок. Снимаются накладки с потолка, вынимаются сиденья водителя и пассажира.

Рисунок 3.32. На заводе «Dethleffs»: слева – автомобили, подготавливаемые к переоборудованию; справа – производство различных модификаций бренда «Possl».
Дальше начинается очень ответственный этап, который состоит из внесения изменений в кузов: резка крыши (если это предусмотрено моделью), окон, вентиляционных люков и отверстий. На данном этапе нельзя допускать никаких ошибок. Ведь любая неточность может быть непоправимой.
Наиболее аккуратным вырезом следует считать крышу, если в будущем планируется установка пластиковой надстройки, например, как в автодомах фирмы «Westphalia», или подъемную крышу «VW Transporter» («Camper-Van»). После того, как резка сделана, необходимо по периметру установить каркас, который служит элементом жёсткости.

Рисунок 3.33. Слева – разметка до начала выреза. Справа вырезанная крыша будущего «Camper-Van» «Класс В++».

Рисунок 3.34. Слева – фургон без крыши. Справа – каркас, усиливающий жесткость крыши.
После этого, происходит монтаж крыши. Это относится как подъемным, так и к пластиковым конструкциям. Подъемная крыша крепится к установленному каркасу. А пластиковая приклеивается непосредственно к самому фургону теми же промышленными клеями-герметиками, которые применяются при производстве фургонов из сэндвич-панелей.

Рисунок 3.35. Слева – установка пластиковой крыши. Справа – вид изнутри: крыша приклеена и зажата струбцинами до полного высыхания.
После того, как крыша установлена на место, пришло время вырезать отверстия под окна.2121
Если модельным рядом фирмы-производителем не предусмотрена разка крыши, например на «Fiat-Ducato», размером кузова L3H4, или «Mercedes-Benz Sprinter» с максимальными габаритами кузова, то после поступления в производство машина сразу же переходит на этап врезки окон.
[Закрыть] Для предотвращения деформации стены, ведь лист железа кузова фургона довольно тонкий, необходимо, чтобы резка была быстрой и точной. После выполнения этой операции, и чтобы избежать в дальнейшем ржавления металла, срез защищается антикоррозийным покрытием. В каждое отверстие, внутри фургона, вставляется и приклеивается деревянный каркас, который придает не только жесткость металлу стены, но и является посадочным местом для окна.

Рисунок 3.36. Слева – разметка стены для резки. Справа – вырезанное окно. Внутри приклеенный каркас для окна.
Именно для того, чтобы набрать толщину стены в 50 мм и делаются деревянные оконные вставки. В будущем на эту толщину будет сделано утепление всего фургона. Деревянные рамы должны соответствовать форме кузова, ведь кузов имеет изогнутую поверхность. И внутри, в будущей жилой зоне, желательно, чтобы изгибы кузова были минимальны.2222
Акриловые стеклопакеты, которые будут установлены в кастенваген точно такие же, что устанавливают в сэндвич-панель на производстве фургонов панельных автодомов.
[Закрыть] Далее вырезается отверстие под дверку туалетной кассеты, выхода дымохода отопителя, внешней водяной заливной горловиной.

Рисунок 3.37. Слева – вклеенные рамки. Справа – установленное окно (верхняя часть рамы находится на вровень с ребром жесткости, и нижняя имеет подоконник).
По той же технологии прорезаются отверстия под крышные люки. Но, так как поверхность крыши ребристая, для каждой модели цельнометаллического фургона имеются свои переходные рамки для люка, предназначенные только для этой марки автомобиля, повторяющие профиль крыши. Она вклеивается между металлической поверхностью крыши и основанием наружной части люка.
После того, как все окна установлены, пришло время утепления всего фургона. Предварительно устанавливаются деревянные бруски, которые будут являться ребрами жесткостями для крепления облицовочных панелей, а также мебели, полка, столов и т. д. В утеплении фургона применяются два вида утеплителя: первый – уже знакомый листовой пенополистирол EPS, и второй – утеплитель «изодом ПЛ», который выпускается в виде рулона. Между ребер жесткости, на металл наклеивается пенополистирол или «изодом ПЛ», и, после этого, на большие поверхности стен и потолка. Далее устанавливаются и монтируются вертикальные стеновые панели и декоративная панель крыши. И после этого производится монтаж и вклейка окон и крышных нужных люков.

Рисунок 3.38. Слева: монтаж душевой кабины навесной полки. Справа: задняя часть жилого фургона.
Прежде чем положить основной пол, монтируется металлический каркас для дивана пассажиров с ремнями безопасности, который крепится к полу кузова фургона, в места, специальные предназначенные для этого. Раскладывается утеплитель и устанавливается большая половая панель, оклеенная виниловым покрытием высокого класса износостойкости. Далее на место монтируется душевая кабина. Это самый громоздкий модуль во всем цельнометаллическом фургоне. После его установки начинается монтаж всей мебели. Но предварительно прокладывают водо и газопроводы, электрические жгуты, устанавливается котел обогрева фургона с системой раздува воздуха и прочие инженерные работы. Производится монтаж мебели.

Рисунок 3.39. Слева – монтаж коммуникаций. Справа – почти готовый фургон на базе «Mercedes-Benz Sprinter».
Для того, чтобы соответствовать форме переоборудуемого транспортного средства, каждая мебельная панель изготовлена по шаблону на станке с ЧПУ. Все элементы собраны в готовые модули, которые монтируются внутри фургона. Так как размеры и планировка заранее известны, мебельные блоки подвозят к каждому фургону на специальных тележках. Далее происходит монтаж основных модулей: кухни, шкафа для одежды, холодильника, ящика для газовых баллонов. Закрепляются полочки и устанавливается спальное место.

Рисунок 3.40. Слева – сборка навесных полок, которые будут смонтированы над распашными задними дверями. Справа – готовые модули.
После монтажа всей мебели на место, декоративными накладками закрываются утепленные задние распашные двери, а также большая сдвижная дверь салона. Устанавливаются поворотные механизмы для водителя и пассажира, под полом автодома крепится бак для грязной воды и проводятся последние отделочные работы внутри.

Рисунок 3.41. Слева – установлены поворотные кресла с дополнительными подлокотниками. Справа – готовые жилые фургоны.
Пройдя проверку всех систем жизнеобеспечения готовый кастенваген покидает фабрику и проходит последнее испытание на вибростенде, а также герметичность окон и крышных люков. После всех этих процедур автодом готов к эксплуатации.
Производство автодомов с кузовом монокок
В линейке «класса В+» есть автодома, которые выделяются методами строительства. Фургоны производятся полностью из стеклопластика и такие кузова можно объединить под названием «монокок». Это итальянский бренд «Wingamm» и «La Strada» в топ-модели «Nova». Кроме того, на рынке 2012 году появился «Monos Reimo» на базе «Volkswagen Transporter». Несмотря на серийное производство, многочисленные этапы постройки таких автодомов выполняются вручную. Качество каждого отдельного автомобиля соответствует самым высоким стандартам.
В монококе весь кузов автодома: боковые и задняя стенка, крыша изготавливается как целая деталь, в одной пресс-форме, из стеклопластика. Слой за слоем происходит напыление пенополиуретана, используемого в качестве изоляционного материала, который позже образует внешнюю оболочку всего кузова.

Рисунок 3.42. Слева – внутренняя деталь. Справа – наружная деталь. (Монокок «Wingamm»).
После этого производится утепление всего монокока. Далее, в подготовленные места, вставляются окна, двери багажника, прокладываются кабели электро и газопроводки. После этого, без монтажа мебели, корпус монокока крепиться на шасси, через пол, на сквозь. При этом соблюдаются все Европейские стандарты по изготовлению автодомов. Как говорилось ранее: вся мебель – модульная, как и на любом производстве автодомов, для таких домов на колесах, производится на отдельной производственной линии. Этапы наполнения мебелью в основном такие же, как при постройке цельнометаллического фургона: сначала душевая кабина, затем вся остальная мебель.

Рисунок 3.43. Слева – монокок, готовы под сборку автодома. Справа – утепление и установка окон. «La Strada».

Рисунок 3.44. Изготовление мебели: слева – кухонный блок, справа – готовые шкафы. «La Strada».

Рисунок 3.45. Шасси «Mercedes-Benz Sprinter» для «La Strada», справа – установка монокока на шасси «Fiat Ducato» («Wingamm»).
Производство соответственно дорогое, результатом которого является очень прочный кузов автодома, который гарантирует длительный срок эксплуатации.

Рисунок 3.46. Слева – на право: «La Strada», «Wingamm», «Monos Reimo».
Жилой модуль на пикап

3.47. Жилой модуль на пикап.
Промышленное производство жилых модулей серийно освоено в Америке и Европе.2323
Мы не будем рассматривать производство американских изделий, так как они рассчитаны на пикапы с длиной кузова от 2-х метров и грузоподъемностью от 1000 кг.
[Закрыть] В Евросоюзе и Китае производятся пикапы с маленьким кузовом и небольшой грузоподъемностью, в сравнении с американскими стандартами. Для таких автомобилей строятся облегченные жилые модули. Лидерами рынка считаются компании «Тischer» и «Bimobil». Есть и другие фирмы, которые строят такие модули, но производят их небольшими партиями. В России промышленно выпускает жилые модули компания «Автокемпер – Пром», которые отличаются оригинальной конструкцией складывающейся крыши. В производстве, используются, в основном, российские комплектующие. Из-за низкой конкурентной цены, такие модули поставляются и за границу. В подмосковном Щелкове, «на заказ», так же можно изготовить и приобрести такой модуль. Все перечисленные компании производят свои модули по разным технологиям.

Рисунок 3.48. Слева – жилой модуль на пикап «Bimobil», справа – «Тischer».
Компания «Bimobil» изготавливает корпус из сэндвич-панелей. Технология та же, что и при производстве полу интегрированных домов на колесах: на стадии изготовления панели, вклеиваются деревянные закладные, к которым в будущем будет крепиться мебель. После изготовления панелей происходит сборка модуля. Жилое внутреннее пространство наполняется стандартным оборудованием. При этом полная масса в снаряженном состоянии не превышает грузоподъемность пикапа.
«Тischer» выклеивает фургон жилого модуля из стеклопластика, достигая при этом аэродинамическую обтекаемость и минимальный вес всей конструкции. После этого происходит наполнение мебелью, которая изготавливается так же из облегченной фанеры и всей необходимой техникой для проживания. Монтируются электропроводка и системы отопления. При этом инженеры «Тischer» строго следят, чтобы вес жилого модуля не превышал грузоподъемность пикапа, на котором он будет эксплуатироваться.
Компания «Автокемпер» производит свои модули из фанеры. Крыша и корпус изготавливаются отдельно. Всё изделие покрывается снаружи специальным консервирующим и водоотталкивающим составом. Затем они стыкуются вместе, устанавливаются автоматические подъёмные механизмы, монтируется электропроводка, водопровод и система отопления. Инженеры фирмы строго следят за весом всей конструкции, потому что перерасход, например только саморезов, несет за собой увеличение веса на 1—2 кг. Тоже самое может происходить и с электропроводкой. Даже небольшой перерасход провода увеличивает массу модуля в целом. Поэтому каждое готовое изделие взвешивается при прохождении ОТК.

Рисунок 3.49. Жилой модуль компании «Автокемпер» в разложенном и транспортном состоянии.
Правообладателям!
Данное произведение размещено по согласованию с ООО "ЛитРес" (20% исходного текста). Если размещение книги нарушает чьи-либо права, то сообщите об этом.Читателям!
Оплатили, но не знаете что делать дальше?