Текст книги "Сварка, пайка и виды соединений"
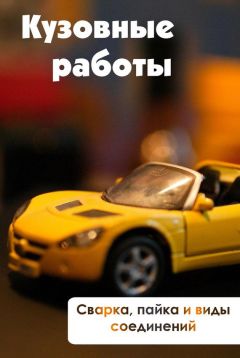
Автор книги: Илья Мельников
Жанр: Хобби и Ремесла, Дом и Семья
Возрастные ограничения: +12
сообщить о неприемлемом содержимом
Текущая страница: 1 (всего у книги 5 страниц) [доступный отрывок для чтения: 1 страниц]
Илья Мельников
Сварка, пайка и виды соединений
Виды соединений
Ремонт соединений – это важная часть кузовного ремонта. Соединения – это способы крепления металлических деталей кузова автомобиля и других элементов, изготовленных большей частью из листового металла.
Способы соединения деталей кузова:
● жесткие временные механические соединения (их называют разъемными);
● жесткие постоянные соединения (неразъемные);
● соединения с нагревом (жесткие неразъемные).
Жесткие разъемные соединения позволяют соединять и затем разбирать детали, составляющие узел.
Способы жесткого неразъемного соединения не позволяют произвести разборку деталей после их соединения.
При любом способе сварного соединения металлов используют тепловой источник, обеспечивающий местное увеличение температуры и вызывающий плавление металла или сцепление расплавленного металла с твердым металлом. Эти соединения называют сварными. Различают два типа сварки: сварку разнородных металлов и сварку однородных металлов.
Сварка разнородных металлов обеспечивает жесткое неразъемное соединение двух одинаковых или различных металлов. Два металла, соединяемые между собой, не доводятся до плавления, а лишь до температуры, при которой они становятся одинаковыми с присадочным металлом. Этот материал, будучи расплавленным, соединяет детали только в определенном диапазоне температур. Такие процессы получили название от вида применяемого присадочного металла: пайка на оловянном припое и твердая пайка.
Сварка однородных металлов (автогенная) обеспечивает жесткое неразъемное соединение двух однородных металлов. Соединяемые кромки нагревают до плавления, что обеспечивает их соединение после охлаждения. Если при этом требуется присадочный металл, он должен быть таким же, как и свариваемые детали, что создает однородную внутреннюю структуру.
О сварочных работах и условиях, необходимых для их осуществления, а также о технике безопасности мы писали в предыдущих главах, а теперь остановимся на видах сварки подробнее.
Существует множество процессов сварки. При ремонте кузовов автомобилей примененяются следующие:
● кислородно-ацетиленовая сварка;
● дуговая сварка;
● дуговая сварка в среде защитного газа;
● сварка сопротивлением.
Кислородно-ацетиленовая сварка
Кислородно-ацетиленовая сварка называется автогенной, так как соединеняет детали из одинакового металла путем их плавления. Жесткое неразъемное соединение получается путем местного плавления кромок соединяемых деталей при нагреве пламенем кислородно-ацетиленовой горелки. Жидкий металл, получаемый при этом, образует неразрывный расплав, в который при необходимости вводится присадочный металл.
Пламя кислородно-ацетиленовой горелки создается горением ацетилена в другом газе – кислороде.
Ацетилен получают в ацетиленовых генераторах и тут же его используют. Как и кислород, ацетилен может быть в баллоне. Из баллона газ проходит через редуктор, затем смешивается в сварочной горелке, на выходе которой его поджигают, создавая кислородно-ацетиленовое пламя.
Сырьем для получения ацетилена являются карбид кальция и вода. Карбид кальция представляет собой твердое вещество, по внешнему виду и твердости напоминающее камень. Его получают путем соединения углерода с известью в электрической печи при температуре 3000°С. Затем дробят и укладывают в бочки, на которых указывается размер камней, что является важной характеристикой для использования карбида в генераторах. Бочку необходимо закрывать герметично, так как карбид кальция сильно поглощает пары воды, содержащиеся в воздухе. При этом скорость реакции намного медленнее, чем в генераторе, тем не менее, в результате ее также получается ацетилен, который может смешиваться с воздухом, находящимся в бочке, и образовывать взрывчатую смесь.
Ацетилен получается в результате реакции карбида кальция с водой. Этот газ обладает особым запахом, возникающим особенно в генераторах, в которых не происходит очистка ацетилена от сероводорода. При сварке кузова обычно используют контактные генераторы высокого давления. Генераторы выполнены с жестким газометром и имеют камеру для заполнения водой. По мере увеличения давления ацетилена он выжимает воду в камеру нагнетания и отделяет воду от контакта с карбидом кальция. При понижении давления в газометре зеркало воды поднимается и реакция возобновляется. Образующаяся известь выпадает в осадок на дно бачка и должна удаляться при каждой новой зарядке генератора. Сухие клапаны и водяные затворы предназначены для предотвращения возврата кислорода в газометр. В баллонах ацетилен растворен в ацетоне, которым пропитана пористая ткань. Максимальная емкость баллона составляет 1000 л/ч.
На станциях автосервиса в зависимости от их мощности применяют ацетиленовые генераторы – стационарные или передвижные. Наибольшее применение из передвижных нашли однопостовые ацетиленовые генераторы марок АСМ– 1,25-3; АСВ-1,25; АНВ-1,25 производительностью 1,25 м3/ч. Из стационарных применяют генераторы марок ГРК-10-68 производительностью 10 м3/ч. В этом случае сварочные посты снабжаются ацетиленом по трубопроводам централизованной раздачи.
Широко применяются для обеспечения работы газосварочных постов находят баллоны со сжиженным газом, в том числе и с ацетиленом. Ацетилен поставляют в баллонах типа 100 или БАС-158, кислород – в баллонах типа 150 и 150Л. Углекислый газ хранят и транспортируют в баллонах типа 150.
Редукторы для понижения давления газа, отбираемого из баллона, выпускают 18 типоразмеров (на различные давления и производительность). При газопламенной сварке кузовных деталей применяют редукторы марок ДКП-1-65 – для кислорода, ДАП-1-65 – для ацетилена, ДЗД-1-59М – для углекислого газа. Для централизованного питания постов кислородом от распределительных рамп применяют рамповые редукторы марки КРР 61.
Шланги изготовляют из вулканизированной резины с тканевой прослойкой или нитяной оплеткой, снаружи oтделанной резиновым слоем. Шланги выпускают трех типов: тип I – для ацетилена с рабочим давлением не более 0,608 МПа; тип II – для бензина и керосина с рабочим давлением не более 0,608 МПа; тип III – для кислорода с рабочим давлением не более 1,520 МПа.
Для горелок малой мощности применяют облегченные шланги с внутренним диаметром 6 мм, для горелок большой мощности с внутренним диаметром 16 и 18 мм.
Наружный слой ацетиленовых шлангов имеет красный цвет, шлангов для жидкого топлива – желтый, для кислорода – синий. Длина шланга при работе от баллона должна быть не менее 8 м, а при работе от генератора – не менее 10 м.
Сварочные горелки – основной инструмент при ручной газовой сварке. Они позволяют регулировать тепловую мощность пламени путем изменения расхода горючего газа и кислорода.
Для сварки тонколистовых металлов (0,2-4 мм) применяют горелки малой мощности (Г2; ГС-2; «Звездочка»; «Малютка») с комплектом наконечников № 0; 1; 2; 3. Малые горелки имеют массу 360-400 г и рассчитаны на работу со шлангами внутренним диаметром 6 мм.
К недостаткам газопламенной сварки следует отнести повышенную возможность пожаро– и взрывоопасности, повышенную загазованность рабочих мест. Кроме того, при сварке тонколистовых кузовных деталей наблюдаются их значительные коробления, перегрев и пережог. Трудоемкость доводки такой поверхности до требований товарного вида высока, а срок службы сварочного соединения низок из-за слабой коррозионной стойкости.
Ацетилен в горелке засасывается кислородом, который выходит из инжектора с большой скоростью. В расширяющемся канале газы смешиваются. Набор различных сопел обеспечивает получение пламени различной тепловой интенсивности. Зоной, осуществляющей сварку, является остроконечное пламя.
Подготовка кромок для сварки осуществляется с учетом толщины свариваемого металла и способа применяемой сварки. На практике при кузовных автомобильных работах газовая сварка выполняется на тонких листах. Чтобы после сварки можно было произвести рихтовку, свариваемые листы необходимо выставить в одной плоскости. Способ сварки, применяемый в этом случае, называют левой сваркой.
По возможности и в особенности для выполнения сварки с высокой надежностью, например, сварки лонжеронов, применяют вертикальную сварку с двойным швом.
Сварка внутренних или наружных углов не позволяет производить рихтовку сварных швов тонких листов, однако она может быть очень полезной при соединении труб.
В настоящее время листы толщиной, равной или более 2 мм, обычно сваривают дуговой сваркой.
Подготовка тонких листов под сварку очень простая. Кромки листов обрезаются ножницами или пилой, обеспечивающими прямой рез. Листы плотно состыковывают друг с другом. Если листы подогнаны не точно, их разъединяют и подгоняют, а затем снова состыковывают для выполнения сварки. Если сварочный шов должен быть расположен в углу, то в зависимости от формы детали предпочтительнее применить такой метод, при котором сварку можно выполнять встык отогнутой кромки одного листа с прямой кромкой другого листа, предвидя выполнение в последующем рихтовки.
Сварщик, работающий правой рукой, держит горелку в правой руке, при этом горелку располагает вдоль оси сварного шва, наклоняя ее так, чтобы пламя было направлено налево. Конец пламени удерживают на расстоянии около 1 мм от зеркала расплавленного металла. Горелку перемещают справа налево. В этом случае сопло наклонено в сторону выполненного сварного шва, а струя пламени прогревает линию сварки.
На практике иногда бывает невозможно производить поперечную сварку. Независимо от направления перемещения сопла горелки, оно всегда наклоняется в сторону выполненного сварного шва.
Если сварка производится с присадочным металлом, то его удерживают симметрично соплу, погружая конец присадочного металла короткими быстрыми движениями в расплавленный металл шва.
Сварку без присадочного металла применяют, в частности, в кузовных жестяных работах. Способ левой продольной сварки часто называют кузовной.
Сварка точками. Это предварительная прихватка, заключающаяся в скреплении двух соединяемых деталей короткими сварными строчками, которые называют сварными точками. Эти точки удерживают кромки в необходимом положении в процессе сварки. Сварные точки должны быть достаточно прочными, чтобы под действием расширения при сварке не происходило их разрыва. Однако сварные точки не должны быть и длинными, чтобы их можно было легко разрушить при необходимости подгонки деталей. Сварные точки не должны сильно превышать толщину свариваемой детали, чтобы не являться помехой в процессе выполнения окончательной сварки. Первую точку желательно выполнить посередине линии сварки.
Если сварной шов формирует угол, то первую точку следует выполнить в вершине угла. Если сварка предназначена для ремонта излома, то первую сварную точку выполняют в месте начала излома на листе. Далее сварные точки располагают с интервалом 30 толщин свариваемого листа, однако в большинстве случаев их следует сближать больше (сжатая точечная сварка).
Сварные точки выполняют, начиная от первой, направляя горелку в направлении не схваченных точками участков. При нагреве кромок происходит их расхождение, однако при охлаждении, следующем после плавления, происходит усадка, вызывающая сближение кромок.
Не следует вначале соединять точками два конца сварного шва, а затем выполнять промежуточные точки, так как при этом будет возникать расширение в противоположных направлениях, которое приведет к деформации кромок, вызывающей либо их перекрещивание, либо изменение уровня расположения.
При сварке точками замкнутого шва прямоугольной формы вначале выполняют точки на двух наиболее плоских сторонах, расположенных противоположно друг другу, а затем на двух других более выпуклых сторонах, так как в результате неизбежного защемления деформация, вызванная удлинением будет временно акцентироваться в центре.
При сварке точками без присадочного металла острие пламени приближают к кромкам и расплавляют.
Если расплав металла каждой кромки с трудом соединяется друг с другом, нужно немного поднять горелку, что обычно приводит к образованию единого расплава металла. Следует дать сварной точке затвердеть до ее почернения.
Если нарушился уровень расположения кромок или кромки, не прихваченные точками, налезают друг на друга, нужно подрихтовать последнюю точку. Если несоединенные точками кромки слишком толстые, необходимо полностью охладить последнюю точку, что приведет к максимальной усадке металла. Если этого окажется недостаточным, следует произвести сварку более близко расположенными точками, расплавляя небольшие капли присадочного металла.
Сварка намного облегчается, если подгонка кромок и соединение точками выполнены очень тщательно. В равной степени можно производить сварку кузовных деталей без прихвата точками. Один из свариваемых листов при этом является неподвижным, а другой приваривают сразу, держа горелку в одной руке и направляя второй рукой привариваемый лист так, чтобы кромка листа была установлена для сварки точно.
Выполнение сварки на горизонтально располагаемых деталях кузова. Для выполнения такой сварки, так же как и для прихватки точками, на горелку необходимо установить сопло, соответствующее толщине сварки. Нормальный расход газа 100 л/ч на 1 мм толщины сварки. На практике стандартный расход составляет 50-70 л. Для меньшей горелки принимают и меньший расход. В действительности листовая обшивка кузовов легковых автомобилей имеет толщину менее 1 мм.
После точечного прихвата следует произвести подрихтовку всей линии стыка, соединенного сварочными точками. Нельзя начинать сварку с края листа, так как кромки расходятся. Начинают сварку с внутренней части шва и направляются к краю листа, т.е. выполняют закраину. Затем производят сварку, начиная от закраины, и ведут ее к другому краю.
Если вырез, который подлежит сварке, имеет форму угла, то сварку начинают с вершины угла и ведут ее в направлении одного края, а затем другого. Если производят сварку детали, образующий отверстие посередине панели, то сваривают попарно две противоположные стороны. Перед сваркой производят тщательную регулировку пламени, а затем подводят его на расстояние около 1 мм до поверхности металла. Сопло наклоняют под углом приблизительно равным 45° к оси сварного шва. Как только металл расплавится, горелку равномерно перемещают без смещения в боковом направлении. Поддерживают нормальное плавление металла путем изменения скорости подачи и корректировки угла наклона горелки.
При увеличении наклона сопла проникновение зоны расплавленного металла уменьшается. Поэтому при сварке угол наклона сопла изменяется в пределах 15-45°. Во всех случаях надо иметь наготове пруток присадочного металла, чтобы заполнить случайно образовавшееся при сварке отверстие.
С внутренней стороны сварочный шов должен представлять собой тонкую линию непрерывно расплавленного металла. Сварочный шов должен иметь небольшую ширину – ширина шва должна быть ориентировочно в пределах 3-4 толщин свариваемого листа. После сварки металлу дают охладиться, не смачивая его. Сварочные швы и их закраины необходимо затем отрихтовать, следя за тем, чтобы металл сильно не вытягивался.
Немного иначе выглядит левая сварка.
Она применяется на несъемных деталях автомобиля, особенно в том случае, когда деталь невозможно расположить так, чтобы произвести горизонтальную сварку.
Иными словами, сварочный шов может располагаться в наклонной или вертикальной плоскости. Для выполнения такой сварки, которая еще называется сваркой по месту, устанавливают сопло, производительность которого приблизительно на 30 % меньше той, которая необходима для горизонтальной сварки листов такой же толщины.
Вертикальная сварка двойным швом. Этот тип сварки с высокой надежностью подходит лишь для сварки внутренних деталей, например лонжеронов. Применяют сопло с расходом 60 л/ч. Для прихватывания сварными точками зазор между листами принимают равным двум толщинам. Горелку удерживают под углом около 30° к горизонтали, а присадочный металл – под углом 20° к горизонтали.
В противоположность тому, что было определено для других способов, сварку начинают с создания отверстия. Затем начинают подачу горелки и присадочного металла. Отверстие необходимо сохранять в течение всего процесса сварки. Таким образом, расплавленный металл удерживается отверстием в процессе затвердевания, проникновение расплавленного металла в шов уверенное.
Сварка по внутреннему углу. Горелку перемещают в том же направлении, что и при левой сварке. Устанавливают сопло с расходом 125 л/ч. Сопло наклоняют под углом 45° и удерживают его в плоскости, проходящей через биссектрису внутреннего угла. Присадочный металл располагают симметрично под тем же углом и перемещают по небольшому участку круговой дуги, чтобы заполнить сварочный шов вдоль вертикального листа, а затем остальную часть шва. Это делается для компенсации стекания жидкого металла на горизонтальный лист, в результате чего на вертикальном листе могут образовываться желобки, а иногда и отверстия.
При необходимости для обеспечения равномерного плавки двух соединяемых кромок, производят корректировку расположения сопла горелки. Каждый раз, если это только возможно, свариваемые детали располагают таким образом, чтобы поверхность жидкого металла сварного шва располагалась горизонтально. В этом случае легче выполнять сварку.
Сварка по наружному углу. Перемещение горелки при данном способе производится так же, как и при левой сварке. Используют сопло с расходом 75 л/ч. Свариваемые листы располагают так, чтобы их края образовывали фаску. При возможности следует размещать свариваемые детали так, чтобы фаска располагалась плашмя. В противном случае необходимо удерживать сопло горелки почти горизонтально, что задерживает расплавленный металл.
Эту способ сварки можно практиковать с присадочным металлом или без него. Сварной шов трудно подвергается рихтовке, следовательно, кромка шва остается деформированной.
Влияние температуры сварки на свариваемые детали. Нагрев, позволяющий довести металл до местного плавления, вызывает местное значительное удлинение, пока происходит изменение состояния металла, который из твердого состояния переходит в пластичное, затем в пастообразное и, наконец, в жидкое. За зоной жидкого металла начинается охлаждение металла, которое приводит к уменьшению объема – усадке, пока металл из жидкого состояния переходит в пастообразное, затем в пластическое и твердое.
Экспериментально влияние удлинения и усадки можно наблюдать с использованием оснастки, имеющейся в любой мастерской. Берут С-образный корпус небольшой струбцины, с расстоянием между плечами корпуса, например, 70 мм. Вырезают два образца из листа толщиной 1,5 или 2 мм. Один образец А имеет ширину 15 мм, другой В шириной 60 мм. Длина образцов выбирается равной расстоянию между плечами струбцины. Образец подгоняют так, чтобы он вошел в струбцину без усилия и без зазора.
Теперь можно экспериментировать. Более узкий образец А располагают между плечами корпуса струбцины. Подводят пламя горелки так, чтобы нагревалась центральная часть образца. Под действием теплоты образец расширяется и удлиняется, однако перемещение концов образца блокировано, так они упираются в корпус струбцины. В результате этого образец выгибается. Однако как только температура небольшого участка достигнет значения 550 °С и он станет красным, пластичность этого участка приводит к тому, что деформация, вызванная продольным изгибом, концентрируется на этом участке и становится постоянной. После охлаждения образец сохраняет свою форму. По сравнению с исходной формой стрела прогиба образца составляет 3 мм, а длина становится короче приблизительно на 0,5 мм.
Затем устанавливаем образец В так, чтобы один из его концов встал в одной плоскости с торцами струбцины. Нагревают, как и в предыдущем случае, центральную часть ленточного участка, соединяющего два плеча струбцины. Возникает небольшой продольный прогиб образца, однако гораздо меньший, чем в предыдущем случае, так как остальная часть образца нагревается медленнее и блокирует нагретую зону.
Как только металл нагреется докрасна, образец получает незначительный продольный прогиб. Длина металла между плечами струбцины остается постоянной, а удлинение сопровождается увеличением толщины.
При охлаждении утолщение остается, хотя величина его не настолько большая, чтобы его можно было увидеть, однако путем ощупывания листа большим и указательным пальцами можно ощутить небольшое утолщение. Соседний с нагреваемым участком металл стягивается к его центру. Чтобы восстановить первоначальную форму образца достаточно отбить молотком утолщенный участок и привести его к первоначальной толщине.
Попробуем применить этот опыт на практике. При выполнении соединения сварными точками, мы наблюдаем, что как только металл нагревается, происходит удлинение двух состыкованных кромок, которые давят друг на друга, их длина возрастает, а свободные края временно расходятся. Таким образом, происходит частичное смещение металла соединенных кромок в зоне сварных точек. При охлаждении сварные точки стягивают два листа и могут привести к перехлестыванию несваренных кромок. Это явление можно устранить легким выстукиванием последней сварной точки навесными ударами. Если схваченные сварными точками детали сваривают, то установленные встык кромки при нагреве расширяются. Пока металл не достиг температуры 500° С удлинение небольшой нагретой поверхности вызывает деформацию всего листа при условии, что он тонкий (листовая обшивка кузовов автомобилей) и легко деформируется в направлении предварительно выполненной формы. Если форма листовой детали выпуклая, то лист поднимается. Если форма вогнутая, то лист прогибается. После того, как температура нагрева достигнет 500°С, металл становится пластичным и деформируется на всем протяжении. Повышение температуры сопровождается выдавливанием, т.е. утолщением металла, которое затем поглощается сварочным швом. За жидким расплавом металла ранее расплавленный металл начинает охлаждаться и проходит непрерывно пастообразное состояние, затем пластическое и твердое с уменьшением в объеме (усадкой).
В пастообразном состоянии металл не обладает никакой прочностью. Поэтому необходимо создать очень прочную зону за пастообразным металлом, чтобы удлинение зоны жидкого расплава, расположенного в непосредственной близости с ним, не вызывало расхождения металла. Вот причина, по которой закраину выполняют сплошным швом в направлении края листов. Затем производят сварку от начала закраины в направлении второго конца свариваемых листов. Если требуется заварить трещину, то конец трещины играет роль закраины.
В процессе охлаждения сварочного шва его металл уменьшается в объеме и стягивает окружающий металл. Пока металл сварного шва обладает пластичностью, он может вытягиваться, однако при температуре ниже 500° он сжимается (усаживается) и вызывает растяжение и деформацию соседнего со швом металла. Именно поэтому необходимо производить рихтовку сварного шва, что позволяет восстановить внутреннее равновесие металла.
После медленного охлаждения (для мягкой стали) жестянщик берет наковаленку, прижимает ее с усилием к одной из сторон шва и простукивает шов молотком короткими навесными ударами для уменьшения толщины зоны сварки, что приводит к увеличению поверхности при постоянном объеме. Поверхность сварного шва выравнивается, а металл нагартовывается, что в значительной степени повышает его механическую прочность.
Обращаем внимание: если обработка молотком будет слишком грубая, то почти определенно удлинение металла будет слишком большое, что приведет к образованию пузыря – дефекта, хорошо известного жестянщикам. Этот дефект придется устранять путем выполнения усадочных точек.
Деформации будут значительно меньше, если листы могут свободно удлиняться. Поэтому во всех возможных случаях практикуют сварку без предварительного прихватывания сварными точками. По той же причине нельзя закреплять некоторые детали в процессе сварки, например при замене поврежденной части кузова, закрепленной на стенде. После прихвата детали сварными точками ее необходимо освободить для выполнения сварки, а затем снова закрепить для окончательной рихтовки, что позволяет металлу восстановить свою форму и внутреннее равновесие.
Обработка сварного шва молотком выполняется только на листах, сваренных встык. Она может выполняться на плоских или изогнутых участках, но нельзя обрабатывать молотком кромочные швы, соединения в угол или внахлестку.
Вообще говоря, влияние процесса расширения и усадки является более сложным, чем показано в данном разделе. Тем не менее, рассказанного для специалистов по кузовным работам достаточно.
Дефекты кислородно-ацетиленовой сварки. Основным дефектом при этом является непровар, возникающий вследствие большой скорости перемещения, при котором металл расплавляется не на всю толщину. При осмотре изнаночной стороны сварного шва будет отсутствовать след провара металла.
При сварке плашмя или под наклоном хороший провар определяется по внешнему виду зоны расправленного металла. Поверхность расплава должна быть слегка вогнутой. Если поверхность расплава плоская и очень узкая, то провара не произошло. Если расплав металла шва оседает и становится широким, необходимо на короткое время поднять горелку, чтобы избежать прожигания металла.
Другим основным дефектом при сварке с присадочным металлом является налипание расплавленного металла на металл свариваемых деталей, нагретых до красного цвета, но не доведенных до плавления. Этот дефект виден при небольшом разъединении краев сварного шва. В этом случае разошедшиеся стыки следует снова проварить. Этот дефект можно заметить и во время сварки, если пруток присадочного металла слишком наклонен к поверхности свариваемых деталей. Желобки или бороздки вдоль сварного шва возникают при очень сильном пламени и недостаточной наплавке. Искажение свойств металла заключается в том, что в результате разрегулировки пламени может происходить насыщение его углеродом или окисление, тогда сварка является некачественной и не подлежит восстановлению.
Внимание! Это не конец книги.
Если начало книги вам понравилось, то полную версию можно приобрести у нашего партнёра - распространителя легального контента. Поддержите автора!Правообладателям!
Данное произведение размещено по согласованию с ООО "ЛитРес" (20% исходного текста). Если размещение книги нарушает чьи-либо права, то сообщите об этом.Читателям!
Оплатили, но не знаете что делать дальше?