Текст книги "Безопасность газораспределительных систем. Часть 1"
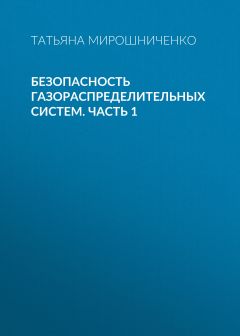
Автор книги: Татьяна Мирошниченко
Жанр: Учебная литература, Детские книги
сообщить о неприемлемом содержимом
Текущая страница: 3 (всего у книги 10 страниц) [доступный отрывок для чтения: 3 страниц]
– разработка и оптимизация алгоритмов управления, включающих в себя полный комплекс информационных, вычислительных, управляющих и диагностических задач;
– выбор из многообразия предлагаемых аппаратно-технических средств оптимального варианта, с учетом сложности решаемых задач и материальных возможностей;
– подбор надежных исполнительных устройств и механизмов, с возможностью управления от запроектированного контроллера или управляющего комплекса;
– разработка программного обеспечения, реализующего все отраженные алгоритмом управления задачи;
– обеспечение возможности интегрирования в системы верхнего уровня и реализация информационного обмена этими системами по стандартному протоколу или по специальным, заранее оговоренным протоколам обмена.
В результате решения указанных задач появляется специализированная система автоматического управления технологическим оборудованием заданного объекта.
Емкость двухстенная для хранения одоранта. Разработка специалистами ОАО «НИИПТхиммаш» (г. Пенза) двухстенных емкостей для хранения одоранта в значительной мере способствует решению задачи правильного хранения одоранта и контролирования его расхода. Конструкция такой емкости обеспечивает постоянный контроль межстенного пространства и предотвращает возможность загрязнения почвы, а также атмосферного воздуха, в случае нарушения герметичности корпуса. Основная (внутренняя) емкость изготавливается из нержавеющей стали, что значительно снижает степень загрязнения хранящегося в ней одоранта продуктами коррозии. Сигнализатор уровня позволяет выдавать предупредительный сигнал о необходимости пополнения запасов одоранта.
Насосы для перекачки одоранта. В большинстве случаев заправка расходной емкости одоризационной установки производится методом передавливания. Автоматизировать этот процесс иногда удобнее с использованием насоса. Такие насосы способны перекачивать одоранты в сосуды под давлением.
Интеллектуальный датчик уровня. В основу работы датчика заложен гидростатический метод, позволяющий, непосредственно в микропроцессорном блоке управления, с высокой точностью рассчитать уровень, объем и массу жидкости. В настоящее время идет доводка конструкции и отработка программно-математического обеспечения интеллектуального датчика для реальных условий газораспределительной станции.
Контрольные вопросы
1. Что называется одоризацией газа?
2. Какие требования к одорантам предъявляются?
3. Какие основные свойства одорантов?
4. Какие способы одоризации газа вам известны?
5. В чем особенность капельного способа одоризации природного газа? Зарисуйте схему капельного способа одоризации газа и опишите её работу.
6. В чем особенность фитильного ввода одоранта в поток газа? Зарисуйте схему фитильного способа одоризации газа и опишите её работу.
7. В чем особенность барботажного способа ввода одоризации в поток газа? Зарисуйте схему барботажного способа одоризации газа и опишите её работу.
8. Как работают автоматизированные системы одоризации газа?
9. Какие условия необходимо соблюдать для хранения одоранта?
10. Является ли одорант ядовитым веществом? Почему?
11. Какая концентрация одоранта необходима для придания характерного запаха природному газу объемом 1000 м3?
12. Какие вещества в газовом хозяйстве принято использовать в качестве одорантов газа?
13. Какие меры предосторожности необходимо соблюдать обслуживающему персоналу при работе с одорантами?
4. Утилизация попутного газа
Специфика добычи попутного газа заключается в том, что он является побочным продуктом нефтедобычи. По геологическим характеристикам различают газы газовых шапок и газы, растворенные в нефти. Для эффективного использования природных ресурсов при добычи нефти необходимо не допустить потери газа, связанной с неподготовленностью инфраструктуры для его сбора, подготовки, транспортировки и переработки, отсутствием потребителей. В этом случае попутный газ просто сжигается на факелах.
В зависимости от района добычи с 1 т нефти получают от 25 до 800 м3 попутного нефтяного газа.
Учитывая высокую энергоёмкость нефтедобычи, во всём мире существует практика его использования для выработки электроэнергии для промысловых нужд. Использование попутного газа позволяет обеспечить электроэнергией и теплом самые отдаленные месторождения.
Примерный компонентный состав попутного газа приведен в следующем соотношении: СН4 – 64 %; С2Н6 – 11 %; С3Н8 – 11 %; С4Н10 – 3 %; С5Н12 – 2 %; N2 – 9 %;.
Наиболее оптимальным и перспективным решением утилизации попутного нефтяного газа признается использование его в качестве топлива для газопоршневых электростанций, газотурбинных электростанций и теплостанций для нужд добывающий предприятий. Одной из наиболее серьезных проблем при подготовке попутного нефтяного газа является его очистка от газоконденсата, нефти, капельной, мелкодисперсной, аэрозольной влаги и механических шламовых примесей. Газ, содержащий капельную жидкость (нефть, влагу) и механические вкрапления, можно применять на газопоршневых электростанциях и газотурбинных электростанциях после его очистки.
Наиболее перспективным направлением по подготовке топливного газа является создание компактных малогабаритных технологических комплексов – установка подготовки газа, позволяющая производить глубокую очистку газовой примеси непосредственно на отдельных скважинах или на локальной группе скважин.
Разработанные конструкции блока подготовки топливного газа (БПТГ) обеспечивают компактность, простоту обслуживания, высокую надежность работы, гарантированное качество глубокой очистки нефтяного газа. Установка подготовки газа позволяет проводить подготовку попутного газа к утилизации непосредственно на нефтяных месторождениях, тем самым избежать потери попутного нефтяного газа и решить связанные с «газовыми факелами» вопросы экологии.
Современные технологии утилизации попутного газа предоставляют возможность полностью использовать попутный нефтяной газ на месторождениях, получить дополнительную электроэнергию и тепло.
Комплекс оборудования имеет широкий диапазон характеристик, получаемых за счет блочно-модульной компоновки. Установки оснащаются системой автоматического управления АСУ. Простота конструкции и автоматическое управление процессом – преимущество такой установки. Оборудование легко транспортируется и устанавливается на месте эксплуатации, сводя к минимуму затраты на монтаж и пусконаладку.
Основным преимуществом блочно-модульной компоновки оборудования является возможность утилизации попутного нефтяного газа небольших скважин. Установки утилизации попутного нефтяного газа представляют собой блочно-модульный комплекс и могут рассматриваться как временный способ утилизации попутного нефтяного газа. После выработки определенного месторождения оборудование может быть перемещено. Установка подготовки газа имеет низкие показатели энергозатрат и является самым эффективным в настоящее время.
Масса, габаритные размеры, потребление электрической мощности, стоимость и время, необходимое на изготовление и монтаж установки подготовки газа, зависят от параметров газа конкретного месторождения.
Блок подготовки топливного газа осуществляет подготовку попутного нефтяного газа для питания газопоршневых и газотурбинных электростанций.
Подготовка заключается в очистке топливного газа от механических примесей, капельной жидкости, осушке, редуцировании и поддержке давления газа на заданном уровне на выходе БПТГ. В блок подготовки топливного газа смонтировано всё технологическое оборудование, включая системы очистки, обессеривания, автоматики, освещения, отопления, приточно-вытяжной вентиляции.
Система контроля АСУ позволяет полностью в автоматическом режиме контролировать весь процесс (от сбора газа до выработки электро– и теплоэнергии). По желанию заказчика можно осуществлять контроль не только локально, но и централизованно контролировать несколько станций.
Контрольные вопросы
1. Что называется попутным газом?
2. Как называются данные вещества СН4, С2Н6, С3Н8, С4Н10, С5Н12, N2?
3. Как полезно используется попутный газ на нефтепромысловых месторождениях?
4. Чем отличается попутный газ от топливного?
5. Какой обработке подвергается попутный газ для дальнейшего использования?
6. Какие современные технологии утилизации попутного газа вам известны? Опишите основные особенности каждой технологии.
7. Какую роль выполняет в подготовке топливного газа АСУ?
5. Подготовка газа к транспорту. Требования к составу и качеству транспортируемого газа
Для оценки качества газа, перекачиваемого по магистральным газопроводам и подаваемого потребителям, используют следующие показатели:
1. Содержание влаги в газе. Влага способствует коррозии газопроводов и оборудования компрессорных станций, а также образованию кристаллогидратов. Для предотвращения этого явления необходимо, чтобы точка росы газа по влаге была на 5–7 °C ниже наиболее низкой температуры газа при его транспортировке по магистральным газопроводам. Поэтому требуется осушка газа на промыслах, головных компрессорных станциях (ГКС) и промысловых газораспределительных станциях (ПГРС).
2. Точка росы по углеводородам. Наличие в газе конденсирующихся углеводородов приводит (при определенных термодинамических условиях) к выделению конденсата, что снижает пропускную способность магистральных газопроводов и увеличивает требуемую мощность ГПА. Использование сорбционных методов, когда определенные фракции из газа поглощаются, дает возможность выделить тяжелые углеводороды при температуре выше точки росы (примерно 313 К или 40 °C). Далее эти углеводороды используются для получения газовых бензинов.
3. Содержание сероводорода. Наличие сероводорода HS способствует коррозии внутренней поверхности труб, ГПА, арматуры, образованию пирофорных соединений, загрязнению атмосферы и помещений токсичным продуктом (яд вызывает паралич органов дыхания и сердца, поэтому ПДК этих веществ в рабочей зоне допускается не более 0,01 мг/л). По ГОСТ 5542–78, в 1 м3 газа допускается содержание H2S не более 0,02 г.
4. Содержание механических примесей. Механические примеси способствуют развитию эрозии, износу газопровода и ГПА, засоряют контрольно-измерительные приборы (КИП), увеличивают вероятность аварийных ситуаций на компрессорных станциях, магистральных газопроводах и ГРС, снижают теплоту сгорания. Допустимое содержание твердых взвесей – не более 0,05 мг/м3.
5. Содержание O. В природных газах О отсутствует. Кислород в трубы попадает при строительстве или ремонте магистральных газопроводов при недостаточной продувке трубы. Наличие О приводит к образованию взрывоопасных смесей или выделению элементарной серы S при наличии сероводорода HS.
6. Содержание СО. В сухом газе СО образует балластную смесь, снижающую калорийность газа. Токсичное вещество оказывает также наркотическое действие и удушье из-за недостатка кислорода О в помещении. Содержание СО в газе не должно превышать 2 %.
7. Содержание меркаптановой и общей органической серы. Меркаптановую серу в качестве одоранта вводят в газ. Необходимый уровень запаха – 16 г/1000 м3 газа. Наличие в газе органической серы более 30–50 г требует его доочистки для химических процессов.
8. Число Воббе (W). Этот показатель используется в бытовых горелочных устройствах. Определяет режим горения в бытовых приборах. W учитывает взаимосвязь теплоты сгорания (q) и плотности газа по отношению к воздуху. Установлено номинальное значение W (11000–12000 кДж/м3), на которое регулируют газовые приборы. Номинальное значение W достигается очисткой и осушкой газа.
Очистка газа. Транспортируемые по магистральному газопроводу газы содержат различные твердые (песок, окалину, сварочный грат) и жидкие (конденсат, воду, масло) примеси. Одни примеси попадают в магистральный газопровод непосредственно из скважин, другие – после строительства (магистрального газопровода, компрессорной станции, ГРС) и в процессе эксплуатации.
Наличие различных примесей приводит к преждевременному износу самого газопровода, запорной и регулирующей арматуры, а также к нарушению работы КИП и регулирующих приборов. Вода и конденсат, скапливаясь в пониженных местах, сужают сечение газопровода и способствуют образованию в нем кристаллогидратов. Поэтому транспортируемый газ подвергается очистке в специальных аппаратах. От механических примесей природный газ очищают в призабойной зоне, на промысле, на компрессорной станции и ГРС. Призабойную зону скважины оборудуют фильтрами, представляющими собой стальные трубы с перфорацией. Гравийные фильтры более качественно предохраняют колонну скважины от выноса песка, известняка и других пород.
На промысле газ очищают от воды, конденсата, частиц породы и пыли в наземных сепараторах (непосредственно у скважины или на сборных пунктах при групповом сборе газа гравитационными сепараторами, циклонными сепараторами).
На линейной части газопроводы очищают продувкой или пропуском очистных устройств. На компрессорной станции предусматривают очистку газа от механических примесей (твердых и жидких частиц). Для этого используются пылеуловители (ПУ) вертикальной конструкции – циклонные и масляные, сухого и мокрого отделения пыли.
На ГРС осуществляют окончательную очистку газа перед потребителем. В зависимости от производительности ГРС применяются для очистки газа различные аппараты: циклонные и мультициклонные сепараторы, висциновые фильтры, масляные или циклонные пылеуловители.
Аппараты для очистки газа от механических примесей. Сепараторы для очистки газа (рис. 5.1) – это аппараты, в которых отделение примесей от газа происходит за счет использования сил тяжести и сил инерции при изменении направления движения и скорости газа. На ГРС применяются гравитационные и циклонные сепараторы. В гравитационных сепараторах отделение примесей происходит путем оседания их за счет резкого изменения направления потока газа при одновременном уменьшении скорости его движения. В циклонных сепараторах отделение примесей происходит за счет инерции, возникающей в цилиндрической части сосудов, при входе газа по тангенциальному вводу. Поступающий на очистку газ подводится к циклону по трубопроводу, направленному по касательной к цилиндрической части аппарата.
В результате этого газ совершает внутри аппарата вращательное движение вокруг внутренней трубы. Под действием центробежной силы, развиваемой при вращательном движении газа, обладающие большой массой твердые частицы отбрасываются от центра к периферии, осаждаются на стенке, а затем через коническую часть удаляются из аппарата. Очищенный газ через внутреннюю трубу циклона поступает в газопровод. Циклонные сепараторы отличаются относительно небольшим гидравлическим сопротивлением, они хорошо очищают газы.
Мультициклонные пылеуловители. Пылеуловители мультициклонные предназначены для очистки газа от механических примесей и конденсата с тонкостью очистки от 60 мкм. Пылеуловитель представляет собой вертикальный аппарат, в верхней части которого расположен пылеулавливающий элемент мультициклонного типа. Принцип действия пылеуловителя основан на извлечении механических и жидких примесей из потока газа под действием центробежных сил. На основании этого принципа созданы конструкции батарейных циклонов – мультициклонов, в которых частицы осаждаются лучше, чем в обычных циклонах.
Газ с примесями жидких и твердых частиц подается через входной патрубок в среднюю часть мультициклона. Далее через вихревые устройства циклонов поступает в нижнюю часть мультициклона, где происходит оседание всех примесей. Освобожденный от частиц пыли и жидкости газ идет по внутренним патрубкам циклонов, попадает в верхнюю часть и по выходной трубе направляется в газопровод. Осевшая на дне аппарата загрязненная жидкость удаляется через дренажную трубу в перевозную емкость. Сброс конденсата может быть автоматизирован.
Висциновые фильтры устанавливаются на ГРС малой производительности. Газ в висциновом фильтре проходит через слой насадки из колец Рашига, которая размещается в корпусе между двумя металлическими сетками. Кольца Рашига смазываются висциновым маслом. Газ, проходя через фильтр, многократно изменяет свое направление, ударяясь о кольца, а частички пыли, имеющиеся в потоке газа, прилипают к поверхности колец. По мере увеличения перепада давления газа на фильтре, что свидетельствует о загрязненности насадок фильтра, кольца очищают. Очистка колец Рашига – трудоемкий процесс. Для извлечения колец из фильтра его отключают запорными органами, стравливают газ и, открыв верхний и нижний люки, высыпают кольца в ванну с жидким растворителем (керосином или горячим содовым раствором). После промывки кольца опускают в висциновое масло. Когда излишнее количество масла стекло, кольца засыпают в фильтр (нижний люк при этом должен быть закрыт). Затем закрывают верхний люк, производят продувку и включают фильтр в работу.
Очистка газа от H2S и CO2. Природные газы очищают от HS и СО сорбционными методами с использованием жидких (абсорбентов) и твердых (адсорбентов) веществ – сорбентов. При низких парциальных давлениях извлекаемых компонентов и при необходимости глубокой очистки используют адсорбционный способ очистки. Абсорбционные методы применяют как наиболее экономичные и позволяющие полностью автоматизировать замкнутый цикл.
В качестве жидких поглотителей применяют водные растворы этаноламинов: моноэтаноламин (МЭА), диэтаноламин (ДЭА), триэтаноламин (ТЭА). Эти вещества тяжелее воды при Р = 0,1 МПа. Они имеют следующие температуры кипения: МЭА-455К – 182 °C; ДЭА-541К – 268 °C; ТЭА-550К – 277 °C.

Рис. 5.1. Схемы очистки газа в циклонных, мультициклонных и гравитационных сепараторах, висциновых фильтрах
Предпочтительность МЭА объясняется высокой реакционной способностью, стабильностью, легкостью регенерации от загрязненных растворов, низкой стоимостью. Очистка газа от HS и СО происходит по следующей схеме (рис. 5.2).
Газ с содержанием HS и СО под давлением 1,39 МПа поступает в нижнюю часть абсорбера, где происходит предварительная сепарация его от жидкости. Отсепарированный газ проходит 16 тарелок абсорбера (2), на которые сверху противотоком подается регенерированный МЭА. МЭА, поглощая HS и СО, перетекает в низ абсорбера, а очищенный газ через верхний патрубок поступает в газопровод. МЭА, насыщенный HS и СО2, из нижней части абсорбера поступает в теплообменник (6), где предварительно нагревается горячим регенерированным МЭА. Затем насыщенный МЭА поступает в пароподогреватель (8), откуда с t = 125 °C разливается на тарелки десорбера (9), в котором поддерживается нормальное давление. Избытки воды и растворенных в МЭА H2S и СО2 при этой температуре на тарелках в десорбере быстро испаряются и выходят через верхнюю часть в холодильник (5). Здесь происходит конденсация паров МЭА, а газы HS и СО сбрасываются на факел или поступают на спецустановки для получения из сероводорода элементарной серы. Сконденсированный МЭА из сепаратора (11) забирается насосом (7) и вновь нагнетается в десорбер (9), что предотвращает его потери. Регенерированный МЭА забирается насосом из нижней части десорбера и через теплообменник (6) и холодильник (5) вновь подается на тарелки абсорбера (2).
Недостатки применения этаноламинов: вместе с H2S почти полностью извлекается СО2; повышенный расход абсорбента и снижение эффективности производства серы и кислых газов (СО).
Ряд месторождений содержат примеси в виде HS и меркаптанов и требуют тонкой очистки от соединений серы. К природным цеолитам относятся: шабазит, морденит и др. Они обладают следующими преимуществами: глубокой степенью осушки, высокой влагоёмкостью при низкой относительной влажности и повышенной температуре газа, прочностью при наличии капельной влаги, избирательной адсорбционной способностью.

Рис. 5.2. Схема очистки газа от сероводорода:
1 – вход газа; 2 – абсорбер; 3 – тарелка; 4 – капелеотбойник; 5 – холодильник; 6 – теплообменник; 7 – насос; 8 – пароподогреватель; 9 – выпарная колонна; 10 – хладоагент; 11 – сепаратор; 12 – котельная
На основании исследований ВНИИГаза предложен метод очистки от меркаптанов физической абсорбцией с использованием трибутилфосфата (ТБФ). Очистка обеспечивается до остаточного содержания меркаптановой серы 50–80 мг/м3. Применяется также новый процесс очистки от H2S «Кэмсвит» по наименованию реагента – неорганическое соединение цинка. Эти установки обеспечивают очистку газа от H2S до концентрации 0,008 мг/м3.
Осушка природного газа. Осушкой называется процесс удаления из газа паров воды. Влагосодержанием влажного газа называется количество влаги (в кг), приходящейся на 1 кг сухого газа. Применяется также понятие «абсолютная влажность газа», выражаемая в граммах влаги на 1 м3 влажного газа. Осушка природного газа производится с целью извлечения паров воды и предупреждения образования и отложения гидратов на стенках газопроводов. При осушке газа стремятся уменьшить содержание влаги в газе до такой степени, чтобы пары воды в газопроводе не достигали состояния насыщения (точки росы) и, следовательно, не могли конденсироваться.
Осушка газа осуществляется на специальных установках твердыми веществами (хлористый кальций СаСl, силикагель, алюмогель, молекулярные сита и др.) или спиртовыми вязкими жидкостями (диэтиленгликоль ДЭГ и триэтиленгликоль ТЭГ), а также с использованием холода, вырабатываемого специальными холодильными машинами или получаемого путем снижения высокого давления газа в штуцерах. Чаще всего для осушки газа используют жидкие сорбенты ДЭГ и ТЭГ, имеющие целый ряд преимуществ перед другими сорбентами, и холод, получаемый путем дросселирования газа в штуцерах.
Преимущества жидких сорбентов следующие: ДЭГ и ТЭГ обладают высокой взаимной растворимостью с водой, они легко регенерируются (восстанавливаются) и обладают высокой стабильностью после регенерации, имеют низкую упругость паров при контакте с газом и поэтому потери их незначительны, не образуют пен и эмульсий с углеводородным конденсатом и довольно легко разделяются с последним в отстойниках в результате значительной разницы в плотностях.
Установки осушки природного газа с указанными сорбентами строятся в местах скопления большого количества газа, чаще всего на территориях отдельных компрессорных станций (КС), промысловых газораспределительных станциях (ПГРС) и подземных хранилищ газа (ПХГ), откуда газ направляется по магистральным газопроводам к различным потребителям.
Принципиальная схема осушки газа изображена на рис. 5.3. Поступающий со сборных коллекторов газ сначала проходит сепаратор 2, а затем направляется под нижнюю тарелку абсорбера 6. Поднимаясь через тарелки, газ контактирует с регенерированным раствором гликоля, подаваемым насосом на верхнюю тарелку абсорбера.

Рис. 5.3. Схема осушки природного газа
Концентрированный раствор гликоля, двигаясь с верхней тарелки навстречу газу вниз, постепенно насыщается парами воды и опускается в нижнюю часть абсорбера. Газ, двигаясь навстречу гликолю, отдает ему пары воды и осушенный через жалюзийную кассету 5 поступает в магистральный газопровод. Насыщенный водой гликоль через теплообменник 9 поступает в выветриватель 11, фильтр 12, а затем в десорбер (выпарную колонну) 19. В кипятильнике выпарной колонны гликоль нагревается от 150 °C (ДЭГ) до 180 °C (ТЭГ), в результате чего вода, испаряясь, вместе с небольшим количеством паров гликоля проходит через холодильник 20 и попадает в сепаратор 22. Сконденсированные пары воды и гликоль скапливаются в сепараторе, а затем сбрасываются в специальную емкость или снова в кипятильник 16. В верхней части выпарной колонны температура поддерживается в пределах 105–107 °C. Регенерированный раствор гликоля забирается насосом 13 и через теплообменник 9 и холодильник 10 с температурой около 30 °C снова поступает на верхнюю тарелку абсорбера 6. Затем цикл повторяется.
Если необходимо получить высокую концентрацию гликолей (98–99 %) с целью достижения низких точек росы газа (–10… –15 °C), регенерацию гликолей производят под вакуумом. Практикой установлено, что для успешной осушки газа должно циркулировать не менее 25 % гликоля на 1 кг абсорбируемой воды и применяться возможно большее число тарелок в абсорбере (10 штук). На линейных КС в блоках топливного и пускового газа – БТПГ для осушки газа используют чаще всего силикагель в адсорберных установках.
Контрольные вопросы
1. Какие показатели качества газа учитываются при его транспортировке?
2. Как содержание влаги влияет на качество газа?
3. Опасно ли чрезмерное содержание сероводорода в природном газе? Каким способом газ очищают от сероводорода?
4. Как природный газ очищают от агрессивных газов, таких как О2, СО2?
5. Какие механические примеси могут содержаться в природном газе?
6. Какие современные методы очистки газа от механических примесей вам известны? Дайте им подробное описание.
7. В чем отличие очистки газа в циклонных аппаратах от мультициклонных пылеуловителей? Выполните анализ эффективности данных методов.
8. Для чего производят осушку газа и какими способами?
Внимание! Это не конец книги.
Если начало книги вам понравилось, то полную версию можно приобрести у нашего партнёра - распространителя легального контента. Поддержите автора!Правообладателям!
Данное произведение размещено по согласованию с ООО "ЛитРес" (20% исходного текста). Если размещение книги нарушает чьи-либо права, то сообщите об этом.Читателям!
Оплатили, но не знаете что делать дальше?