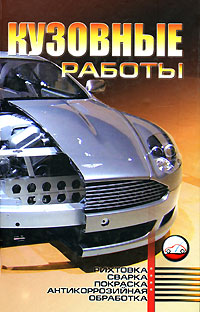
Автор книги: М. Ильин
Жанр: Хобби и Ремесла, Дом и Семья
Возрастные ограничения: +12
сообщить о неприемлемом содержимом
Текущая страница: 8 (всего у книги 32 страниц) [доступный отрывок для чтения: 11 страниц]
Кроме профильных резиновых уплотнений, предназначенных для герметизации ветровых и задних стекол, на автомобиле применяются и другие резиновые профильные уплотнения.
Они устанавливаются между подвижной деталью и остовом кузова. Если подвижная деталь автомобиля находится в закрытом положении, резиновое уплотнение сжимается и обеспечивает тем самым герметизацию. Кроме того, резиновые уплотнения устраняют стук металлических поверхностей, находящихся в контакте. Уплотнения приклеивают специальным клеем на обвод подвижной детали автомобиля или на неподвижную часть кузова напротив подвижной.
Со временем резиновые уплотнения разрушаются. Причины разрушения резиновых уплотнений следующие:
– в результате старения резина теряет эластичность;
– в летнее время уплотнения прилипают к нагретому металлу кузова;
– в зимнее время уплотнения примерзают и отрываются при открывании подвижной детали.
Технология ремонта этих деталей проста. Поврежденное уплотнение отклеивают и соскабливают частички резины, оставшиеся на металле. Затем специально предназначенным для этой цели клеем смазывают поверхности металла и нового уплотнения. Дают выдержку, пока уплотнение размягчится под действием клея, и приклеивают уплотнение сначала одним концом, а затем равномерно укладывают, не допуская лишнего натяжения.
На многих отечественных легковых автомобилях («Москвич», «Волга») уплотнение дверей осуществляется с помощью губчатых резиновых профилей, которые приклеивают на двери автомобилей и в проем клеем 78–БЦСП. Этот клей обеспечивает работоспособность клеевого соединения при температурах от 90 до –50 °C. Для надежного приклеивания используют клей, как правило, с вязкостью в стадии поставки 40–60 с (по ВЗ-4). Если вязкость выше, клей разбавляют смесью бензина с этилацетатом в соотношении 1:2 по массе. Губчатый уплотнитель, предназначенный для приклеивания, обезжиривают бензином БР-1. Наносят клей и склеивают при 18–25 °C и относительной влажности не более 75 %. Порядок такой: на склеиваемую поверхность губчатого уплотнителя кистью наносят равномерный слой клея и сушат его на воздухе 10–15 минут. (Допускается хранение уплотнителя с нанесенным клеем до 6–8 часов). На окрашенную поверхность металла кистью наносят первый равномерный слой клея и сушат его 3–5 минут, затем наносят второй слой клея, который сушат 0,5–1,5 минут. Уплотнитель плотно прижимают руками, а затем прикатывают его роликом.
Выдержав указанные режимы, можно обеспечить надежное приклеивание с высокими показателями на отрыв и отслаивание.
Для приклеивания уплотнителя можно использовать также клей 88-НП, но он обладает более низкой термостойкостью (до 60 °C).
Ремонт радиаторов и топливных баковДля отвода теплоты от жидкости, которая циркулирует по радиатору, радиатор должен иметь большую поверхность теплоизлучения. Необходимый теплоотвод обеспечивается за счет ряда трубок, проходящих сквозь металлические пластины, повышающие способность к теплоизлучению. Трубки и пластинки, соединенные между собой, образуют корпус радиатора и обеспечивают хорошую проводимость теплоты. Активной частью радиатора является система трубок.
При одинаковом первоначальном объеме плотность горячей воды меньше плотности холодной воды, горячая вода легче холодной за счет расширения при нагревании. Ряды трубок радиатора расположены вертикально, что способствует опусканию в радиаторе охлажденной воды из-за ее большей плотности. Для увеличения теплоотдачи необходимо приблизить центральные слои воды, циркулирующие в трубках, к их стенкам. С этой целью трубки выполняются сплюснутыми по сечению и имеют прямоугольное сечение со скругленными кромками. Трубки проходят через уже установленные пластинки и своими концами входят в бачки радиатора, где пропаиваются.
Бачки представляют собой металлическую коробку в форме прямоугольного параллелепипеда с закругленными углами. У радиатора два бачка – верхний и нижний. Нижний с помощью патрубка соединяется с водяной рубашкой блока двигателя и сливным краном. Верхний бачок соединяется с насосом охлаждения, запорным краном для наполнения системы охлаждения и переливной трубкой.
Радиаторы изготовляют из меди, латуни, оцинкованной стали или алюминиевого сплава.
Причины выхода из строя радиатора бывают внешние и внутренние.
Одна из причин выхода из строя радиатора объясняется его расположением. Радиаторы чаще всего устанавливаются в передней части автомобиля, где наиболее благоприятные условия для обдува охлаждающим воздухом. Но при повреждении передка автомобиля, даже не очень серьезном, радиатор оказывается заклиненным между двигателем и облицовкой радиатора, которая продавливается деталью, подвергшейся деформации в результате удара. При этом происходит сплющивание трубок (большее или меньшее) и радиатор деформируется.
Другая причина выхода из строя радиатора связана с температурным режимом его работы. С течением времени охлаждающая жидкость испаряется, восстановление уровня производится много раз небольшими порциями. В добавляемой воде содержатся мельчайшие инородные частички. Размер внутренней полости сечения трубки находится в пределах 1–2 мм, трубки частично засоряются мелкими инородными частицами.
Даже если вода абсолютно чистая, в ней все равно содержатся растворимые соли, преимущественно известковые. Под действием теплоты эти соли выпадают в осадок и осаждаются на стенках трубок в зонах малых скоростей перемещения воды – так образуется накипь. Образование на стенках накипи приводит к полному закупориванию трубок. Частицы накипи могут отрываться от стенок и, в свою очередь, забивать трубки, как и инородные частицы.
Антифриз способствует отрыву частиц накипи и частично выводит их из трубок радиатора, однако он не в состоянии полностью очистить трубчатую систему радиатора, и она засоряется, что из-за снижения интенсивности циркуляции воды приводит к перегреву двигателя.
Третья причина ремонта – растрескивание радиатора. Под действием вибраций в радиаторе возникают мелкие трещины, преимущественно в месте сварки с недостаточным проваром. В результате возникают небольшие утечки, которые приводят к понижению уровня охлаждающей жидкости. Если утечка незначительная, ее не всегда можно заметить, так как нагретая вода быстро испаряется.
Рассмотрим ремонт радиаторов. При аварии в результате удара часто происходит деформация только верхнего или нижнего бачка радиатора. Если деформация позволяет, бачки разъединяют распайкой, восстанавливают их форму и затем спаивают. Однако очень часто повреждается и трубчатая система, тогда непригодным к ремонту становится весь радиатор. Есть два варианта, из которых можно выбрать один:
– заменить поврежденный радиатор новым;
– заменить систему трубок новой, сохранив верхний и нижний бачки старого радиатора вместе с патрубками и элементами крепежа. Системы трубок поставляются специализированными предприятиями по ремонту автомобилей. Распайка верхнего и нижнего бачков радиатора осуществляется путем прогрева на большой длине шва до расплавления олова. Затем бачки оттягивают и разъединяют.
Для проведения этой технологической операции обычно используют пламя кислородно-ацетиленовой горелки.
При необходимости верхний и нижний бачки подвергаются правке, рихтовке и травлению. Затем бачки одевают на законцовочную пластину новой системы трубок сверху и снизу и припаивают оловом с помощью паяльника л(ибо пламени кислородно-ацетиленовой горелки). Горелка должна обеспечивать быстрый нагрев, что сокращает время работы. Однако горелка может вызвать перегрев небольшого участка, что приведет к возникновению на нем дефектов.
Ремонт, о котором рассказано, с экономической точки зрения менее дорогой, чем полная замена радиатора. В зависимости от модели автомобиля стоимость ремонта радиатора на 40–70 % дешевле замены его новым.
Понятно, что засорение радиатора случается на автомобилях, эксплуатируемых в течение длительного времени. В таких случаях радиаторы очищают. Очистку радиатора можно произвести двумя способами: химическим (без снятия радиатора) и механическим (со снятием радиатора).
Химическую очистку радиатора нельзя производить любым травящим реактивом, поскольку среди них есть такие, которые взаимодействуют с металлом и разрушают его. В системе охлаждения двигателя применяются различные по своим свойствам металлы. Так, радиатор выполняется из латуни или оцинкованной стали, головка блока двигателя из алюминиевого сплава, а блок цилиндров из чугуна или алюминиевого сплава. При очистке реакция должна происходить между накипью и химическим реактивом без воздействия на металл. Промышленные реактивы для удаления накипи представляют собой химические вещества, применяемые для этой цели. Их добавляют в воду радиатора и включают двигатель. Время работы двигателя определяется инструкцией изготовителя реактива. После остановки двигателя из системы охлаждения спускают жидкость и тщательно ее промывают.
В качестве реактива для снятия накипи применяется каустическая сода. Она применяется в том случае, если в системе охлаждения не содержится алюминиевых деталей или деталей из алюминиевых сплавов. Латунь и чугун не взаимодействуют с содой, однако алюминий и его сплавы реагируют тем интенсивнее, чем выше температура содового раствора в воде. Чтобы убедиться в этом, достаточно приготовить ванну с каустической содой, разогреть ее до 80 °C и бросить в нее кусочек алюминия. Непрерывное выделение пузырьков газа укажет на реакцию металла с каустической содой. При этом глубина травления алюминия зависит от времени его погружения в раствор соды. Следовательно, соду нельзя применять, если в системе охлаждения имеются детали из алюминия и его сплавов.
Раствор соляной кислоты в системе охлаждения вызывает умеренное коррозирующее действие, при этом быстрого разрушения металлов, покрытых медью, и легких сплавов не наблюдается. Однако при высокой концентрации кислоты последние реагируют очень бурно. В данном случае время работы двигателя для промывки системы ограничивается пятнадцатью минутами, после чего система тщательно промывается.
Азотная кислота является более предпочтительной, если в радиаторе не содержится никакого другого вещества для удаления накипи. Она не действует на алюминий и его сплавы. В то же время она вступает в реакцию с медью и латунью. Ход очистки можно контролировать визуально, наблюдая за состоянием видимой внутренней поверхности радиатора, частично сливая жидкость по мере необходимости. После полного удаления жидкости из системы производят обильную промывку при полностью открытых сливных отверстиях.
Во всех случаях надо иметь в виду, что химическое травление является эффективным лишь тогда, когда трубки радиатора закупорены не полностью и травящий раствор может циркулировать.
Применяется и механическая очистка радиатора. При этом из системы охлаждения сливают жидкость и снимают радиатор. Для снятия радиатора выполняют следующие работы: снимают соединительные шланги и болты крепления верхнего и нижнего бачков к кузову. Далее работу выполняют на верстаке. Снимают переливную трубу и заливную пробку.
Для доступа к трубкам необходимо распаять по меньшей мере один из бачков. Чтобы удалить олово из места пайки, каждый шов, подвергаемый распайке, устанавливают так, чтобы олово стекало со шва в момент его плавления. В зависимости от удобства работы линия распайки может быть установлена вертикально или горизонтально, а открытый конец желобка направлен вниз. Расплавление припоя обычно производится пламенем горелки. В процессе распайки следует размягчить олово, чтобы произвести несколько растяжений и сдавливаний бачка радиатора, что вызывает разрушение оставшегося паяного шва.
При работе с горелкой надо следить за тем, чтобы не возникало перегрева, вызывающего деформацию и разрушение пайки около трубок. После снятия бачка законцовочная планка полностью освобождена.
Работа по механической очистке трубок заключается в том, что в каждую трубку вставляют стальной прут соответствующего сечения и длины и перемещают его возвратно-поступательно, чтобы он проходил по всей длине трубки и удалял внутренние отложения. При невозможности прочистить трубки с одной стороны отпаивают второй бачок, чтобы иметь возможность прочищать трубки и с другой стороны.
После очистки трубки промывают и протравливают кислотой для удаления оставшихся осадков, которые не удалось прочистить прутом. И снова промывают трубки.
Перед установкой бачков на место всю поверхность законцовочной пластинки вокруг трубок необходимо залудить для предотвращения возможных утечек, которые могут быть вызваны расшатыванием пайки в момент распайки и прочистки. Затем устанавливают на место каждый бачок и закрепляют точечной сваркой, после этого пропаивают с помощью паяльника либо пламени газовой горелки, снабженной соплом малой производительности.
По окончании работы трубки заглушают посредством пробок или герметичных заглушек. Заливают радиатор водой и производят испытание герметичности сварки. При проверке желательно приложить небольшое усилие на растяжение и сдавливание радиатора.
Для испытания не обязательно применять насос, достаточно расположить радиатор горизонтально и установить вертикально трубу, соединенную с переливным патрубком шлангом. Труба длиной 1 м создаст вполне достаточное давление для контроля. Испытание радиатора с помощью сжатого воздуха при опускании радиатора в воду может привести к повышению давления, если не установлен предохранительный клапан, что чревато, разрывом радиатора.
Есть и такой метод контроля. Он заключается в том, что из радиатора сливают воду и закупоривают патрубки пробками. Пробками могут служить наборы резиновых цилиндрических колец, которые сжимаются болтом через две металлические шайбы, установленные с двух сторон резинового блока. В результате сжатия блок шайб раздувается и создает герметичность. Переливная трубка радиатора соединяется гибким шлангом с источником сжатого воздуха, находящимся в мастерской. Радиатор погружается в бак с водой. При подаче в радиатор воздуха под небольшим давлением, в случае утечки пузырьки воздуха поднимаются вверх, указывая на негерметичность радиатора.
Часто приходится иметь дело с трещинами радиатора. Ремонт в основном производят посредством пайки оловянным припоем. В большинстве случаев для выполнения пайки следует снимать радиатор. Перед работой необходимо отметить места утечек.
Есть тенденция применения радиаторов, состоящих из системы алюминиевых трубок и пластмассовых водяных бачков. Такие радиаторы ремонту не подлежат.
В большинстве случаев топливные баки состоят из двух деталей, получаемых вытяжкой и сваренных роликовой сваркой по отогнутым бортам. Металлом для топливных баков служит мягкий стальной лист, покрытый свинцом (либо луженый). В новых моделях автомобилей прослеживается тенденция использования композиционных материалов для изготовления баков. Применение композиционных материалов способствует снижению массы автомобилей, а также уменьшению стоимости топливных баков.
Причин повреждения топливных баков несколько. Так как бак устанавливается под автомобилем, его верхняя часть оказывается на уровне пола. На некоторых моделях автомобилей топливный бак установлен вертикально в багажном отсеке сбоку. Баки, находящиеся под автомобилем, могут повреждаться от ударов камней. Баки, установленные в багажном отсеке, повреждаются коррозией, возникающей от конденсации влаги.
Для ремонта стального топливного бака сначала необходимо слить горючее, а затем снять бак. Если ремонт сводится к выправке вмятины и никаких утечек топлива не наблюдается, то операция заключается в подаче сжатого воздуха в бак через заправочную горловину или через отверстие, соединяющее бак с топливным насосом. Для этого необходимо выполнить следующее:
– заглушить одно из двух отверстий в баке;
– вставить в открытое отверстие бака конический резиновый наконечник, просверленный насквозь для обеспечения герметичности соединения бака с трубопроводом сжатого воздуха;
– подать сжатый воздух в бак и произвести восстановление его размеров и формы.
В случае повреждения бака нельзя тотчас производить его сварку.
Внутри бака всегда остаются пары топлива (бензина или дизельного топлива), которые смешиваются с воздухом и образуют взрывчатую смесь. Пламя может вызвать взрыв содержащейся в баке смеси, что, в свою очередь, приведет к разрыву бака и ранению находящихся поблизости людей.
Чтобы вести паяльные работы, необходимо промыть бак, затем наполнитьт его водой или инертным газом. Промывку можно произвести раствором моющего средства в горячей воде, при этом бак энергично встряхивают и затем выливают содержимое. Последующую промывку бака производят посредством полного его заполнения и сливания.
Если пайка бака производится оловянным припоем при помощи паяльника, паять можно без заполнения бака. Если при ремонте требуется нагрев бака пламенем, например, для выполнения горячей пайки, то предварительно необходимо наполнить бак водой, а затем установить его так, чтобы внутри, под местом пайки, оставался небольшой воздушный промежуток.
При проведении этой работы нельзя герметически закрывать бак, образующийся при пайке газ должен свободно выходить наружу или выдавливать воду из бака. Для этого предварительно подсоединяют гибкий шланг к заливной горловине, которая после переворота бака оказывается внизу. При этом для поддержания нужного уровня шланг изгибают.
Бензобаки можно ремонтировать жидкими полиэфирными смолами. Этот способ ремонта обладает тем преимуществом, что устраняется возможность взрыва, присущая пайке с применением газовой горелки. Работа выполняется в следующей последовательности: в чистый сосуд наливают полиэфирную смолу и отвердитель (в пропорции в зависимости от марки), затем смолу и отвердитель тщательно перемешивают до получения однородной массы. Клей готов. Подготовленной смесью с помощью кисти покрывают ремонтируемое место бака накрест лежащими слоями. Потом следует подождать, пока произойдет полимеризация смолы, и тогда нанести второй и, возможно, третий слой.
Если пробоина в баке большая, необходимо выполнить следующее:
– покрыть края отверстия смолой, затем наложить на отверстие стеклоткань и покрыть ее смолой;
– в том же порядке наложить еще 2–3 слоя стеклоткани, промазывая каждый слой смолой.
Отметим, что соединенные вместе слои стеклоткани и смолы обладают прочностными характеристиками, сравнимыми с характеристиками металла бензобака.
Во всех случаях ремонта перед установкой топливного бака необходимо убедиться в отсутствии в нем утечек.
Детали кузова из пластических материаловПластические материалы находят очень широкое применение в машиностроении. Кузова автомобилей из пластика производятся редко, но некоторые широко распространенные модели имеют наружные детали из пластика.
Если говорить о кузовах, полностью изготовленных из слоистых пластиков, они состоят из элементов, собранных между собой, так как форма кузова очень сложная, чтобы ее можно было сформовать целиком. Кузова из слоистого пластика не являются несущими, они устанавливаются посредством разъемного соединения на стальную раму, несущую механические узлы. Изготовление деталей осуществляется формовкой.
Чтобы изготовить деталь, нужна по меньшей мере одна форма, которая может быть охватываемой или охватывающей. Форма должна иметь уклон для извлечения из нее готового изделия. Качество поверхности формуемой детали будет тем выше, чем лучше отполирована форма.
При формовке выполняют следующие подготовительные работы. Внутреннюю поверхность формы покрывают веществом, способствующим выемке готовой детали из формы.
Исходя из сопротивления действующим нагрузкам и внешнего вида, выбирают соответствующую стеклоткань для армирования изготовляемой детали. Готовят шаблон из плотной бумаги, размечают и вырезают по шаблону стеклоткань.
Далее выбирают полиэфирную смолу соответствующего качества и характеристиками, необходимыми для последующей эксплуатации детали. В смолу вводят красители. Существует множество разновидностей смол, отличающихся различным химическим составом. Каждая из них соответствует определенному назначению. Смола, предназначенная для нанесения первого слоя на форму, получила название ледяного покрытия. Стеклоткань применяется в виде плотного материала – войлока, состоящего из коротких нитей длиной приблизительно 50 мм, расположенных хаотически и связанных друг с другом тонким слоем смолы. Толщина стеклоткани находится в пределах 1–2 мм, однако чаще всего ее измеряют по массе 1 м2. Наиболее часто встречаются значения 300, 450, 600, 900 г/м2. Это ткани различного типа, отличающиеся способом изготовления, массой и природой стекловолокна. Наибольшее распространение получила «тафта», имеющая клеточную текстуру. Стекловойлоки обладают меньшей механической прочностью, чем ткани, однако они более удобны для изготовления сложных форм.
В серийном производстве применяют другой вид стекловолокна: резаные волокна, которые имеют длину волокон, аналогичную стекловойлоку или несколько меньшую. Их применяют для изготовления основы.
Формовать детали кузова можно различными способами, но в любом случае они должны обеспечивать следующее:
– правильное размещение ткани в форме;
– полную пропитку ткани полиэфирной смолой без малейшего пузырька воздуха;
– достаточно высокую производительность, необходимую для серийного производства.
Для ознакомления с технологией производства рассмотрим формование на одной форме, или контактное формование. Это самый простой способ. При этой технологии уменьшается количество используемого материала, но требуется большее количество рабочей силы. Качество готовых деталей зависит от умения и от аккуратности исполнителей. Способ применим для изготовления одной детали, нескольких идентичных деталей или малой серии. Формы могут быть самыми различными, в том числе и очень больших размеров. Как уже говорилось, форма может быть охватываемой или охватывающей – в зависимости от желания получить хороший внешний вид внутренней или наружной поверхности детали.
Форма должна быть очень жесткой. Уклоны формы должны составлять не менее 3–5°. Если деталь, подвергаемая формовке, имеет обратный уклон, то форму выполняют из нескольких точно подогнанных частей.
Материал формы зависит от типа производства, который она должна обеспечить. Так, например:
– гипсовая форма удовлетворяет производству одной детали;
– стальная форма обеспечивает ее максимальное использование при формовании нескольких тысяч деталей;
– при изготовлении деталей мелкими сериями наиболее простым является изготовление модели, с которой затем снимают слепок формы. В этом случае форма получается из слоистого пластика (стекловолокно + полиэфирная смола). Усиление формы осуществляется посредством погружения в слоистый пластик профилированного картона или деревянных пластинок, что создает образование нервюр. Такого типа форма обеспечит изготовление многих сотен деталей.
При подготовительной работе обращается особое внимание на следующее. После вырезки полотен их помещают во влажное помещение и так, чтобы их можно было взять в порядке нанесения слоев. Среди различных по составу веществ, способствующих разделению изделия и формы, необходимо выбрать то, которое соответствует материалу формы. После сушки разделительного покрытия надо, по возможности, нанести первый закрывающий слой специальной окрашенной смолы (в некоторых случаях с наполнителем), который скрывает волокна стеклоткани, делая их незаметными на поверхности детали. Толщина слоя должна быть в пределах 0,3–0,4 мм. Если слой очень толстый, то впоследствии возникнут трещины.
Если наличие видимых волокон стеклоткани на поверхности детали не имеет значения, тогда нет необходимости накладывать закрывающий слой. В этом случае можно сразу нанести достаточно толстый слой смолы.
Чтобы избежать подтеков на вертикальных стенках, в смолу добавляют наполнитель. После нанесения первого слоя его высушивают до студнеобразного состояния перед наложением последующих слоев.
Студнеобразное состояние слоя определяют по легкому прилипанию при касании. В течение перерыва следует приготовить смолу, которая будет использоваться при формовке. Приготовление смолы осуществляют в два этапа: добавляют ускоритель полимеризации и смешивают его со всей предназначенной для использования смолой, а в случае необходимости подкрашивают. Дозирование и смешивание катализатора полимеризации является следующим этапом и производится по мере необходимости, т. е. в расчете на количество смолы, которая может быть использована в течение последующих 15 минут. Разделяют смолу, предназначенную на половину рабочего дня, на две равные порции. В одну емкость помещают полное количество ускорителя, в другую – полное количество катализатора. По мере необходимости готовят смесь равными порциями в третьей емкости. Такой способ позволяет избежать повторяющегося приготовления небольших количеств смолы и катализатора.
Дозировать смолу можно либо взвешиванием на весах, либо применением емкости, в которую помещается определенная масса смолы. Дозирование ускорителя и катализатора полимеризации производится с помощью мензурок очень маленькими дозами.
Как только покрывающий слой или первый слой смолы стал студенистым, накладывают первый слой стекловолокна. При этом можно применить легкий стекловойлок (300 г/м2). При наложении первого слоя стекловолокна, как, впрочем, и при наложении последующих слоев, необходимо следить, чтобы стекловолокно ложилось в форму постепенно и ровно, особенно в местах закруглений, без образования воздушных карманов. (Карманы образуются в результате либо очень поспешного прижатия, либо неплотного сопряжения острого угла). Затем уложенное стекловолокно пропитывается. Для этого каждый рабочий снабжается банкой, содержащей количество смолы, рассчитанное на 12 мин применения, и инструментом для нанесения смолы. В качестве инструмента используют кисточки или валики. Если применяют кисточку, то лучше похлопывать концом кисти по поверхности стеклоткани, как это делается при крашении, чем растягивать слой.
После окончания пропитки не следует пытаться отделить стекловолокно, так как при этом волокна приподнимаются и вырываются. Затем, не дожидаясь загустения, укладывают слой стеклоткани. Для обеспечения высокой механической прочности можно укладывать поочередно слой стекловойлока и слой стеклоткани. Последним укладывают стекловойлок или отделочную стеклоткань (300 г/м2).
При выполнении этой работы необходимо соблюдать следующие правила:
– использовать только чистые полиэтиленовые или металлические банки;
– полностью использовать смолу, содержащуюся в банке, перед заполнением ее новой порцией;
– не поддающиеся устранению воздушные пузыри нужно убрать, надрезая их лезвием бритвы;
– сразу же после применения промыть кисти, валики ацетоном или трихлорэтиленом. Промывку нужно производить до того, как произойдет полная полимеризация оставшейся и подлежащей удалению смолы;
– чтобы избежать прямого контакта смолы с кожей, работать необходимо в резиновых перчатках;
– работать можно только в вентилируемом помещении, так как пары полистирола вызывают раздражение глаз и слизистой оболочки;
– нельзя тереть глаза, так как случайно попавшие на кожу стеклянные волокна проникают в нее и могут травмировать глаза;
– помещение, в котором производится работа, должно быть защищено от холода, влажности и прямого солнечного света. Температура должна быть не ниже 20 °C;
– нельзя курить и перемещать смолы перед пламенем, так как смолы являются огнеопасными;
– выемку изделия следует производить через 12 часов. Это время можно сократить, если применить сушку в сушильной камере (температура не выше 60 °C) или нагрев инфракрасными лучами;
– после выемки изделия необходимо обрезать и загладить края;
– при желании окрасить деталь, ее зачищают шлифовальной шкуркой, а затем наносят полиуретановую краску;
– если большое количество деталей подвергается сборке склеиванием, необходимо сделать шероховатыми контактные поверхности, промыть их ацетоном, а затем склеить либо специальным клеем, либо тесьмой, пропитанной полиэфирной смолой.
Описанная технология – это практически единственный способ, с помощью которого кузовщик может по заказу клиента изготовить из слоистого пластика какие-либо детали кузова.
Познакомимся также с формовкой деталей в мешке. Работа выполняется так же, как описано выше, после чего на изделие в форме оказывают давление либо с помощью раздувающегося эластичного пузыря, помещенного в закрытую форму, либо посредством создания разрежения между гибкой мембраной и слоистым покрытием, нанесенным на форму. Полученные таким образом детали имеют наилучшее качество, так как обеспечивается более равномерная концентрация смолы. Этот способ применим для среднесерийного производства.
Чтобы обеспечить хороший внешний вид и высокое качество готового изделия, формовка во входящих друг в друга формах может производиться либо со слабым сжатием, либо без него. Способ применим в среднесерийном производстве.
Формовка под давлением во входящих друг в друга формах может производиться укладкой стекловолокна, а затем отмеренного количества смолы на форму. Сжатие позволяет обеспечить равномерное распределение смолы в детали. Обычно формы подогревают, что дает возможность применить этот способ в крупносерийном производстве, а также при производстве с первоначальным изготовлением основы будущей детали.
Обрезанные стеклянные волокна за счет разрежения прижимаются к поверхности формы, выполненной из перфорированного листа. В этом состоянии волокна пропитывают смолой из краскопульта. Форму с нанесенной на нее основой детали помещают на несколько минут в камеру для сушки. Затем полуфабрикат отделяют от формы, помещают в окончательную форму, покрывают отмеренным количеством смолы и сжимают с одновременным подогревом весь комплект в течение нескольких минут. Деталь готова. Этот способ применяют в серийном производстве кузовных деталей.
Ремонт кузова из слоистого пластика осуществляют только с наружной поверхности детали. Порядок таков. Если повреждение незначительное, поврежденную зону зашлифовывают, затем зачищенное место заполняют полиэфирной шпатлевкой. После затвердевания шпатлевку зашлифовывают, а затем красят.
Если поврежденная часть расколота со значительным количеством более или менее измельченных осколков, пилой вырезают поврежденную зону. По краям отверстия снимают фаски. Фаски должны быть очень пологими и шириной, равной как минимум трем толщинам. Ремонт можно производить как снаружи, так и изнутри детали. Фаску снимают с той стороны, откуда будет производиться ремонт. По форме ремонтируемого участка детали готовят металлический лист. Он предназначен для частичной замены исходной формы. Если ремонт производится снаружи, то лист помещают с внутренней поверхности детали. При проведении ремонта с внутренней стороны детали лист-форма должен быть расположен с наружной стороны, поверхность которой имеет лучшую отделку.
Правообладателям!
Данное произведение размещено по согласованию с ООО "ЛитРес" (20% исходного текста). Если размещение книги нарушает чьи-либо права, то сообщите об этом.Читателям!
Оплатили, но не знаете что делать дальше?