Текст книги "Умножая эффективность. Метод внедрения бережливого производства с умной IT-интеграцией: в кондитерке, пищёвке, FMCG в целом"
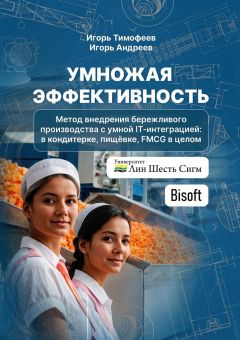
Автор книги: Игорь Тимофеев
Жанр: Техническая литература, Наука и Образование
Возрастные ограничения: +12
сообщить о неприемлемом содержимом
Текущая страница: 2 (всего у книги 5 страниц)
Когда эффективность не первое – и когда пора взяться за неё всерьёз
Эффективность – важная, но не всегда первая задача. Бывает, ко мне обращается руководитель и в ходе первичной диагностики я понимаю, что ему сейчас нужна помощь другого специалиста, а не моя.
Один из вариантов – проблемы с качеством. Оно бывает либо слишком низкое, либо слишком высокое.
Если качество ниже необходимого, товар не покупают. Тогда какой смысл улучшать процессы на линии? Будем стараться произвести побольше товара, который никто не купит, и его придётся списать в убыток? Зачем?!
Другой вариант – слишком высокое качество, обусловленное чрезмерно затратной рецептурой, раздувающей себестоимость продукта. Чем больше произведёшь, тем больше операционного убытка себе сделаешь. Нужно изменить рецептуру, чтобы себестоимость «поднырнула» под отпускную цену и появилась хорошая маржа.
Часто проблемы бизнеса лежат в маркетинге, в продажах. Если нет стабильного сбыта, значит что-то не так с востребованностью продукта, ценой, рекламой, логистикой, координацией с дистрибьюторами и пр. Это вопросы точно не к эффективности производства.
В подобных случаях предприятию нужно наладить сбыт, чтобы возник поток живых денег с рынка, а товар не залёживался на складе, – это вопросы к маркетологам и продажникам, не к производству.
Я специализируюсь на Лин Шесть Сигм и TPM (облуживание оборудования), и если в ходе диагностики понимаю, что это не то, в чём в первую очередь нуждается предприятие, так и говорю.
Мне нравится метафора про бочку с водой.
Представьте: у вас бочка, которую нужно наполнить, а в бочке несколько дырок на разных уровнях. Чтобы наполнить, надо сначала залатать самую нижнюю дырку, через которую вода сливается в данный момент. Залатаем нижнюю – вода поднимется выше, к следующей. Залатаем её – вода поднимется ещё выше, до третьей. И так последовательно одну за другой – вот бочка и наполнится.
Так вот: если дыра, связанная, например, с плохим обслуживанием оборудования, находится выше той, через которую ваша вода (в смысле – деньги) сливается сейчас, то сколько воды ни заливай, бочка не наполнится, а повышать эффективность – затыкать дыру более высокого уровня – преждевременно.
В подобных случаях я направляю к другому консультанту из числа проверенных коллег, по специализации.
(К слову, в последние годы ко мне обращаются в основном те, у кого с качеством и сбытом всё в порядке, им хочется больше прибыли именно за счёт роста эффективности. Поэтому у меня профдеформация: кажется, будто проблемы бизнеса сосредоточены в производстве, хотя это не всегда так. Просто ко мне приходят в основном с запросами по эффективности производства.)
А теперь давайте посмотрим, когда предприятию действительно пора всерьёз браться за эффективность.
Очевидно, когда период становления пройден, сбыт налажен, бизнес-процессы в целом отстроены и хочется увеличить выпуск на том же оборудовании, с теми же мощностями – в основном за счёт снижения потерь от простоев оборудования и снижения потерь от брака.
Когда бурный рост, связанный с выходом на рынок, в прошлом, уже сформировался круг покупателей, приучившихся кушать ваш продукт, вы начинаете понимать, что прирост объёма производства на какие-то 5—10% или даже на 1% даст вам много дополнительной прибыли.
Понимание вытекает из двух наблюдений.
Первое: всё, что производите, продаётся полностью – значит, рынок готов скушать вашего продукта больше, чем даёте сейчас. А сейчас вы недодаёте рынку продукции – и недополучаете с рынка денег.
Второе: проектная мощность оборудования больше, чем выпуск сейчас. То есть вы не выжимаете максимум из мощностей. Если линия рассчитана на 100 тонн в месяц, а выдаёт только 75 тонн, значит что-то не так в процессах – отсюда простои и брак. Вот вам и потеря выручки, эквивалентной 25 тоннам в месяц. Понимаете?
Неизбежно возникает вопрос: как из тех же ресурсов выжать больше продукта без потери качества и, таким образом, максимизировать выручку и минимизировать удельную себестоимость единицы продукта?
Тут-то мы и берёмся за эффективность производства!
Повышаем эффективность – прибыль растёт за счёт того, что себестоимость единицы продукта ниже, а объём выпуска больше. У вас появляются дополнительные деньги, жизнь становится веселее – появляются предпосылки для ускоренного роста.
Благодаря этому вы резко отрываетесь от конкурентов, которые вопрос эффективности упускают.
Какая связь между эффективностью и конкурентами?
Допустим, вы производите карамель «А», а ваш конкурент производит похожий продукт, карамель «Б». Произведёте «А» меньше, чем готов проглотить рынок, – люди вынуждены купить больше «Б», и деньги, которые могли бы прийти к вам, достанутся производителю «Б». Ничего личного, просто бизнес.
Это были рассуждения о природе эффективности с точки зрения бизнеса в целом. Для собственника слово «эффективность» значит прибыль: выше эффективность – больше прибыль. Но как представить, визуализировать эффективность «на земле»? Легко – например, вот так…
Понимание эффективности через «Формулу-1»
У нас в кругу консультантов в качестве примера для сравнения любят вспоминать работу механиков на пит-стопе в автогонках, например в «Формуле-1». Наверняка вы это видели по ТВ хотя бы раз.
Пит-стоп – техническая остановка машины во время гонки. Бригада механиков должна сменить шины, проверить техническое состояние и при необходимости что-то там подкрутить.
Когда гонщик заезжает на пит-стоп, каждый уже на своём месте в полной готовности. Один механик держит домкрат, другой резину для замены, третий что-то ещё. Быстро поднимают машину, один снимает колесо гайковёртом, другой его забирает, третий уже подаёт новое на замену. Двое прочищают воздухозаборники, третий протирает забрало шлема гонщика.
Раз – два – три – и снова погнал на трассу!
Почему они так торопятся?
Пока машина на обслуживании, а не на трассе, гонщик упускает драгоценные секунды, от которых зависит результат, его место в гонке. Зачастую время, потраченное на пит-стоп, оказывается решающим фактором для победы в соревновании.
Почему они работают так слаженно и быстро?
Кое-кто спланировал их работу, их проинструктировал, спроектировал им всю «логистику».
Плюс – надо ж внедрить – их всех натренировал.
Требуется высочайшая согласованность в работе всех членов обслуживающей команды, а показателем эффективности выступает время, затрачиваемое гонщиком на пит-стопе: чем меньше, тем лучше.
Слаженную работу механиков на пит-стопе часто приводят как пример того, как должны быть организованы переналадки технологического оборудования на производстве. Но не только переналадки: все процессы кто-то должен описать, спроектировать, стандартизировать, связать всех со всеми и ещё над всем этим добавить надстройку в виде процедур по сбору данных для постоянных улучшений и соответствующих внедрений.
Собственно, это то, чем мы занимаемся во время внедрений бережливого производства и TPM.
Другой хороший пример – как устроено обслуживание самолётов авиакомпаний-лоукостеров.
Смысл бизнеса в сфере авиаперевозок в том, чтобы самолет почти не стоял на земле, всё время летал – перевозил пассажиров. Летает – денежки капают в кассу. Стоит на земле – издержки копятся, а прибыль тает.
Соответственно, нужно организовать так, чтобы обслуживание на земле осуществлялось чуть ли не мгновенно, за считаные минуты. Процессы обслуживания быстрые и слаженные: пассажиры выходят из самолёта, стюардессы чистят салон и принимают новых пассажиров, а в это время самолёт уже заправлен, технические проверки сделаны, старый багаж выгружен, а новый загружен и т. д.
Любое замедление, сбой, остановка значат прерывание основного процесса – то есть авиакомпания начинает терять деньги, упускает прибыль.
(Кстати, говорят, что человек, придумавший бизнес-модель лоукостеров, подглядел идею в «Формуле-1». )
В вашем производстве должно быть так же!
Я не хочу сказать, что ваши работники должны носиться по цеху со скоростью механиков «Формулы-1». Но их работа должна быть столь же осмысленной, скоординированной и целесообразной. И тогда нет нужны в беготне, суете, авралах – всё как надо и вовремя, без простоев и накладок, синхронизировано и подконтрольно вам.
А то ведь как оно бывает. Остановили линию, и механик, к примеру, должен заменить форматные части – которые, если по уму, должны быть заранее подвезены, уже под рукой, и гаечные ключи тоже, всё наготове. А они остановили, и он такой: «О, гляди-ка, линию остановили» – и пошёл искать ключи и форматные части.
Почему часто бывает так – а не как в «Формуле-1»?
Первое: нет единого стандарта процедур.
Сотрудники работают по принципу «кто в лес, кто по дрова». На линии четыре разные смены, и в каждой своё представление о том, как надо, например, чистить оборудование. Каждый чистит, исходя из своего разумения (а также ответственности, рассеянности, лени и др.).
Второе: работники разобщены, каждый за себя.
Чуть что, валят ответственность друг на друга. Технический отдел говорит про производство: «Они не умеют нормально работать, поэтому всё ломается». Производство отвечает: «Мы-то в порядке, это они не могут нормально линию отремонтировать». Отдел качества жалуется на производство: «У них всё криво-косо, если мы перестанем их постоянно носом тыкать в брак, они только брак и будут гнать». Производство отвечает: «Нас этот отдел качества уже заколебал, из-за маленькой потёртости на упаковке заставляют линию останавливать, из-за них мы простаиваем, каждый раз из-за какой-то ерунды». Ну, вы поняли33
А кто-то и узнал себя – что неудивительно, ибо бывает повсеместно.
[Закрыть].
Третья причина: все озабочены операционной рутиной, делают план по валу, а над системой не работают – всё время варятся внутри рутинных задач.
В чём тут проблема? Чтобы управлять процессами, нужно видеть их сверху, а не находиться постоянно внутри них. Как говорится, трудно сварить борщ, если сам постоянно находишься в кастрюле с борщом.
Четвёртое, тесно связанное с третьим: самообман под девизом «нет времени».
По-моему, это самая большая беда и одновременно самое популярное самооправдание, потому что «нет времени» – поистине универсальная отмазка, на все случаи жизни. Только вот не помогает жить, а мешает.
Помните ту притчу про дровосека с тупой пилой?
Один человек шёл по лесу и увидел дровосека, который с большим трудом пилил дерево тупой пилой.
– Почему бы вам не наточить свою пилу? – спросил он дровосека.
– У меня нет времени точить пилу, пилить надо! – простонал дровосек, утирая пот со лба, и снова продолжил пилить тупой пилой.
Резюмируем. Нет стандартов, нет общего для всех понимания, что делать и как правильно. Нет согласованности, слаженности в единую команду. Постоянное застревание внутри рутинных дел – вопреки необходимости работать над системой, над бизнесом, над процессами. Ну и конечно, «нет времени» на работу по улучшениям – а ведь пока не поставишь её как приоритет №1, времени-то никогда и не будет.
Ну вот, собственно, поэтому эффективность хромает на многих предприятиях. Деньги сливаются, как вода в раковину, – в виде как лишних затрат, так и упущенной выручки. И вроде все работают, чем-то заняты, стараются, но итог стараний не похож на тот, что у победителей «Формулы-1», да и финансовые результаты не особо радуют…
Но мы не сдадимся. Мы наведём порядок.
Мы сделаем производство таким, где потерь минимум, а производительности максимум – и достойная прибыль как результат целенаправленных усилий.
У других получилось, получится и у вас.
Почему в отраслях FMCG легче внедрить бережливое производство – и почему иначе не выжить
В чём особенность производств FMCG?
Узкая номенклатура товаров, массовый выпуск – и стандартные процессы производства. В этом смысле все производства FMCG устроены примерно одинаково.
Кондитерская фабрика всё время делает одно и то же, например конфеты. Они, конечно, разные, но номенклатура маленькая – допустим, 15 видов. В пищёвке появление новых продуктов случается, наверное, один-два раза в год, а так фабрики производят одно и то же изо дня в день, из года в год.
Соответственно, технологические этапы тоже понятные, одни и те же. Есть само производство продукта. Есть его упаковка. Есть линии, которые это все делают. На линиях – люди, выполняющие повторяющуюся работу. Все процессы стандартизированные, одинаковые. Следовательно, наша задача предельно понятная: за счёт оптимизации процессов добиться выпуска как можно большего объёма одинаковых товаров в единицу времени.
Этим FMCG отличается от многих других производств.
Например, на огранке бриллиантов, где я тоже некоторое время работал, организация процессов очень сильно отличается. Каждый бриллиант – не стандартный товар, как ириска или коробка с макаронами, не похож на другие. Каждая единица требует индивидуального подхода, и там преимущественно ручной труд: огранку не может сделать машина, только человек. Иными словами, там много искусства, ремесленничества.
В давно минувшие эпохи нечто подобное касалось практически любых товаров, даже обуви. У сапожника каждая пара обуви была как снежинка: вроде по одним лекалам, но не похожа на остальные. Сегодня обувь практически штампуют роботы, оператор на линии только присматривает за процессом. А вот производство бриллиантов из алмазов так не устроишь, они, видимо, будут ручной работой всегда.
Не бриллианты, но схожая природа производства, например, на механическом заводе. Однажды я помогал разобраться с эффективностью на заводе, который входит в один металлургический холдинг и его же обслуживает. Они там делают тысячи полторы разных деталей для основного производства, по запросу. Плюс постоянно появляются какие-то новые детали: заказчик захотел что-то ещё, объяснил ТЗ, и под него делают вот эту новую деталь. Там тоже, конечно, можно и нужно кое-что оптимизировать, но сама природа производственных процессов иная: огромная номенклатура товаров, производство не поточное, а скорее штучное.
Получается, в таких производствах, как обработка алмазов или детали под заказ, вопросы эффективности лежат в совершенно других плоскостях, нежели в FMCG или, например, в фармацевтике.
На кондитерской фабрике на конвейерной ленте едут одинаковые конфетки. Поскольку процедура обработки сырья и его последующего превращения в готовую конфету у нас стандартная, шаблонная, появляется возможность этот поток разделить на этапы – так сказать, на микропеределы, на отдельные простые действия. Потом среди них выделить узкие места – и в них заметить, где случаются разнообразные затыки, сбои, накладки, из-за которых страдает скорость потока. А значит, можно и устранить причины тех затыков.
Чем мы и занимаемся в русле Лин Шесть Сигм.
Обработка у нас поточная, не ручная, работают не люди, а управляемые людьми машины. В этом есть особая прелесть для нас: мы можем повысить эффективность путём простых, понятных внедрений. Лично я люблю FMCG именно за это. Увидеть взаимосвязанные процессы как целостную картинку, выявить узкие места – и что-нибудь сразу улучшить, усилить, ускорить.
Невозможно не радоваться, когда видишь, как команда сотрудников при помощи здравого смысла и не таких уж сложных процедур превращает производство в мощный, высокопроизводительный механизм!
Другая важная характеристика FMCG: как правило, мы находимся в жёстко конкурентном рынке.
Нас кормят те самые люди, которые покупают в магазине наши леденцы, пастилки и жвачки, тратят на нашу продукцию свои кровные рубли. И тут одно из двух: либо им нравится наше качество и цена, и они платят, либо нет – и не платят, точка. Тем временем конкуренты на рынке не сидят сложа руки: стараются соблазнить своей продукцией «наших» потребителей.
Поэтому в отраслях FMCG всё честно и жёстко: либо ты умеешь давать конкурентоспособный продукт, при этом вмещая себестоимость и норму прибыли в цену, либо вылетаешь из игры. И снова на первый план выходит эффективность: без неё никак.
Хотя бывает, конечно, разное. Я как-то консультировал один молокозавод, который выпускает, в частности, адыгейский сыр. Когда они только вывели продукт на рынок, в той продуктовой нише практически не было конкуренции, и они об эффективности даже не думали. Ну и пусть много потерь: итоговая выручка всё покрывала и позволяла зарабатывать ощутимую прибыль.
Долгое время тот сыр, кроме них, никто не делал. Но потом появились конкуренты с предложением такого же качества, но дешевле. Они прикинули, что будет, если снизить отпускную цену, и озадачились: «Неужели кто-то продаёт то же самое дешевле – и с прибылью, не в минус? Неужели они такой ценой отбивают себестоимость?!» Тогда-то они и задумались о снижении издержек за счёт повышения эффективности.
И вот что было дальше.
Первичная диагностика. Я говорю: «Покажите мне Парето простоев, пожалуйста». Они говорят: «А что это такое?» Я говорю: «Ну, диаграмма, мы же должны посмотреть, какие факторы влияют на возникновение простоев, каков их вклад». Они говорят: «Да, мы понимаем, но… мы эту диаграмму никогда не строили».
Вот так. Оказывается, в XXI веке есть предприятия, причём там работают серьёзные люди, где ни разу не анализировали причины своих простоев.
Но рынок заставил их взяться за ум. И всех заставит.
Всех, кто хочет выжить и тем более преуспевать.
Мы с вами живём в рынке. Никаких дотаций: государство не содержит неудачников. Никаких оправданий: покупатель платит деньги тому, кто умеет конкурировать.
Многие в FMCG давно озаботились эффективностью. Другие активно включаются сейчас.
С одной стороны, иначе не удержишься на рынке. С другой, природа производств со стандартными повторяющимися процессами очень располагает к тому, чтобы навести порядок в процессах и тем самым «заткнуть дырки в бочке», увеличить выпуск и снизить себестоимость.
На следующей странице – об основных источниках потерь на производствах и об этапах внедрения практик Лин Шесть Сигм и производственной системы (TPM), которые предстоит пройти каждому предприятию.
Дальше в этой книге раскроем все эти этапы в такой же последовательности, глава за главой.
Общая природа потерь на производстве, их причины и способы устранения
Антипод эффективности – неэффективность, и это всегда подразумевает потери.
Потери в обывательском понимании – нечто, что потеряно буквально. Когда деньги потрачены (вложены) на какое-то дело, но не вернулись, это потери.
Бывает и на производстве. Например, сделали брак, потратив не него сырьё, энергию, оплаченный труд рабочих и т. д., – это потери. От причин, вызывающих такие потери, мы, конечно, избавляемся.
Однако в контексте повышения эффективности мы фокусируемся прежде всего не на деньгах, а на эффективном времени работы производства. Это время – деньги.
Здесь под потерями мы имеем в виду разницу между ценностью, которую могли и должны бы создавать за единицу времени, если бы работали максимально эффективно, и ценностью, которую создаём фактически. Потери – это «отрицательная дельта», сумма недополученного из-за низкой, по сравнению с целевой, эффективностью.
Давайте сделаем умственное упражнение с помощью образного сравнения: поездка на автомобиле.
Допустим, вам предписано проехать из точки А в точку Б, расстояние между которыми равно 1000 км, со средней скоростью 100 км/ч. Логично предположить, что на весь путь у вас должно уйти ровно 10 часов. (Время на плановые остановки для заправки, время на отдых водителя и др. сейчас игнорируем.)
Если за 10 часов вы вместо 1000 км сделали только 750 км, значит вы двигались со средней скоростью всего 75 км/ч. То есть потеря в скорости составила 25%.
Потеря в расстоянии тоже 25%: за 10 часов вы недобрали 250 из 1000 км. План не выполнен на 25%.
Чтобы «добить» 250 км, вам потребуется (с той же скоростью) потратить дополнительно ещё 3 часа 20 минут, которых у вас нет: на 1000 км было отведено 10 часов.
Причины потерь, из-за которых средняя скорость была 75 вместо 100 км/ч, могли быть какими угодно.
Может быть, вы ехали 100 км/ч, но по пути поломались и остановились на ремонт на 2,5 часа.
Может быть, где-то вы не туда свернули, пришлось возвращаться, делать крюк – потеряли те же 2,5 часа.
Может, где-то на пути вы наткнулись на строгого (но справедливого!) гаишника, который нашёл к чему придраться, и на улаживание инцидента ушло время. Это был внеплановый простой – на 2,5 часа.
Могла быть комбинация факторов: всё перечисленное понемножку плюс что-то ещё.
Как бы то ни было, фактический результат путешествия таков: за 10 часов вы «не доехали» 250 км, или, скажем иначе, на весь путь в 1000 км вам потребовалось 13 часов 20 минут вместо 10 часов.
Чтобы в следующий раз ту же дистанцию сделать за 10 часов, требуется устранить (упредить) факторы, из-за которых время терялось. В нашем примере с воображаемым путешествием это значит:
– не допустить поломок в поездке, т. е. обеспечить техническую исправность автомобиля;
– снабдить водителя навигатором и инструкцией о маршруте, чтобы чётко следовал маршрутному заданию;
– иметь в полном порядке документы, аптечку и пр., что обычно проверяют гаишники;
– и всё остальное, что зависит от вас, предусмотреть во избежание эксцессов, мешающих движению по плану.
Вот так всё просто, правда?
Перенесёмся на производственную линию.
Допустим, нормативный объём выпуска – 100 тысяч единиц стандартного продукта за 90 суток (2160 часов) при бесперебойной работе. Если за это время у вас получается только 75 тысяч единиц, значит потери составили 25% от целевого объёма, верно?
Если перевести штуки в минуты, получится, что ваша линия работала 75% времени: 1620 из 2160 часов. Потери времени – то есть суммарный простой – составили 540 часов. Верно?
Куда «пропали» 540 часов?
Причины, опять же, могли быть какими угодно.
Может быть, часть времени линия простаивает, потому что вы в это время просто не работаете: нерабочее время.
На часть времени производство могло быть не запланировано. Допустим, ваши продажники поняли, что не обеспечат 100% сбыта, нужно придержать коней, чтобы не работать тупо на склад, вот вы и сделали длительный «перекур». А может, приезжал президент корпорации, чтобы толкнуть речь перед сотрудниками, все собрались на одной площадке, слушали и вдохновлялись – и тоже не работали.
Часть времени ушла на плановые остановки. Регулярно останавливали линию для переналадки оборудования, скажем переключаясь с апельсиновой карамели на клубничную. Другой пример: остановились на планово-предупредительный ремонт оборудования или монтаж новых узлов.
Потери времени по любой из перечисленных выше причин означают потерю денег: в это время ваш станок, печатающий деньги, не работал, производство стояло.
Однако источником самой-самой острой боли обычно выступают другие потери времени.
Прежде всего это неплановые остановки – связанные, как правило, с поломками и сбоями оборудования. Их причины, конечно, кроются в неправильном обслуживании оборудования.
Но бывают неплановые остановки и по другим причинам. Например, со склада не вывозится вовремя готовая продукция, некуда складировать новую, вынуждены остановить линию – вот и простой, вот и потери. Аналогично – если не подвезли нужные ингредиенты для производства продукта: нет сырья, не из чего лепить конфетки – вот и простой, снова потери.
Отдельная песня – потери по качеству.
Операторы неверно выставили настройки оборудования или загрузили не те ингредиенты, из-за чего какое-то время шёл брак – считай, что линия работала впустую, то есть, по сути, не работала. Тоже простой.
Этот момент – потери из-за брака – хорошо понимают эксперты по эффективности, но обывателю такое непонятно. Кажется, что потери из-за брака состоят из стоимости сырья, потраченного на брак, вот и всё. Нет, не всё.
Если линия работала бесперебойно, но произвела то, что не будет продано, а пойдёт на помойку, это эквивалентно тому, что соответствующее количество времени производство простаивало. Линия должна была выпускать продукт на продажу, но не выпустила, а время ушло.
Исходя из понимания природы потерь, из понимания видов потерь, из анализа удельного веса разных видов потерь, в совокупности бьющих по эффективности вашего производства, можно (нужно) устранить соответствующие причины потерь.
Для этого мы и внедряем бережливое производство.
На следующей странице – в какой последовательности, глава за главой, – в книге изложены ключевые этапы внедрений и то, как они связаны с устранением соответствующих потерь.
Правообладателям!
Данное произведение размещено по согласованию с ООО "ЛитРес" (20% исходного текста). Если размещение книги нарушает чьи-либо права, то сообщите об этом.Читателям!
Оплатили, но не знаете что делать дальше?