Текст книги "Умножая эффективность. Метод внедрения бережливого производства с умной IT-интеграцией: в кондитерке, пищёвке, FMCG в целом"
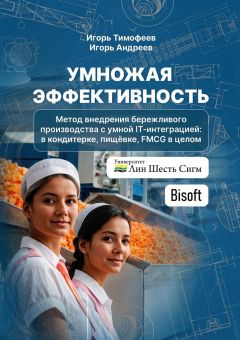
Автор книги: Игорь Тимофеев
Жанр: Техническая литература, Наука и Образование
Возрастные ограничения: +12
сообщить о неприемлемом содержимом
Текущая страница: 3 (всего у книги 5 страниц)
Логика и последовательность внедрений для устранения (предотвращения) потерь
Вероятно, всем нам хотелось бы простых инструкций для внедрения бережливого производства. Простых, как для сборки тумбочки из «Икеи». Типа, сначала возьми вот эту деталь и к ней присоедини вон ту, затем добавь деталь №3 и так далее.
Однако это несколько сложнее, чем собрать тумбочку.
Скорее, так. Начинаем с первого этапа и, ещё не закончив его, берёмся за второй, а потом параллельно с ним за третий и так далее. Работа на разных фронтах идёт одновременно, успехи в одном служат предпосылкой для успехов в другом, а те усиливают эффект на первом и открывают возможности для третьего.
Итак, вот предстоящий путь.
Сначала мы организуем сбор данных о потерях. Ведь нам нужно понимать, над чем работать в плане улучшений. Благодаря этому мы наконец-то начнём видеть «болезни» производства, всё как на ладони.
Потом мы научим людей выполнять проекты повышения эффективности с помощью методов DMAIC, «Кайдзен-мероприятие», «Сфокусированные улучшения». Здесь же сбор «низковисящих плодов», известный в народе как рацпредложения. Благодаря этому ваши сотрудники научатся побеждать любые, простые и сложные, проблемы на линии и втянутся в процесс непрерывных улучшений.
Третье, что мы сделаем, – наведём порядок на рабочих местах по методу «5S». Больше не будет бардака в рабочем пространстве. Некоторые думают, что это «всего лишь» вопрос удобства. Но эксперты подтвердят: из-за неупорядоченности на рабочем месте тратится колоссальный объём времени, что выливается в простои. А так работать станет удобно: всё под рукой, ничего лишнего, всё чистенькое, красота.
Четвёртое: упорядочим и приведём к почти идеальному состоянию трафик людей и предметов – это линфлоу. Потоки сырья, материалов и готовой продукции в рабочем пространстве оптимизируются. Никто и ничто не будет мешать друг другу. Больше не будет «дорожных пробок» на линии и нагромождения всяких коробок и поддонов тут и там. Да, заодно наладим не только внутренние потоки, но и «связи с внешним миром»: потоки входящего сырья и исходящей продукции.
Затем – сразу несколько глав – ура: началась предметная работа по TPM!
Прежде всего мы приведём оборудование в базовое состояние, и теперь оно будет работать как должно, а не как попало. Дальше нужно будет только поддерживать его в базовом состоянии.
Для этого мы внедрим процедуры, известные как CIL: очистки, инспекции, смазки. Начнут осуществляться регулярно и должным образом. Ваше оборудование будет вам благодарно, обещаю. Впрочем, главное, что вы сами будете довольны.
Следующая после CIL практика для поддержания оборудования в базовом состоянии – плановое обслуживание по компонентам. Внедрим, и больше ничто и почти никогда не будет ломаться в самый разгар работы, когда останавливаться нельзя. С облегчением вздохнут не только инженеры и механики: пожалуй, больше других радость жизни ощутит начальник производства.
Дальше: анализ поломок. Раньше было: сломалось – исправили, сломалось – исправили, и так бесконечно. Теперь будет так: ваши люди почти на лету разбирают причины поломок, находят корневую причину, а потом её устраняют – и поломка не повторяется. Хорошо!
Четвёртая из четырёх практика для поддержания оборудования в базовом состоянии – журнал красных бирок. Дефекты больше не будут копиться, операторы с механиками сами всё улаживают. А вы ими любуетесь и раздаёте премии и почётные грамоты за хорошую работу. Всем очень приятно.
Условно десятый этап внедрений – система аудитов. Всё, что должно быть под контролем, будет под контролем: от поддержания оборудования в базовом состоянии и порядка на рабочих местах до соблюдения рецептуры и техники безопасности. Люди не смогут делать что-то неправильно, и не только потому, что ваш добрый, но строгий взгляд им обо всём напоминает, но и потому, что они скоро привыкнут к контролю и самоконтролю – и, самое прекрасное, им самим всё это будет нравиться.
Дополнительный этап внедрений – опциональный – изменения в оргструктуре. Для обслуживания оборудования в одних случаях удобнее, чтобы техслужба подчинялась начальнику производства, в других – чтоб была отдельной, в подчинении у директора фабрики. С этим нужно определиться – вот вы и решите, как лучше для вас.
Когда вы всё это сделаете, предприятие под вашим руководством станет практически эталонным образцом для подражания завистливых конкурентов. Можно экскурсии вдоль линий водить.
Судите сами.
Потерь нет… Ну, не совсем нет, а почти нет, ибо производство с нулевыми потерями бывает только в сказках. (Но стремиться к этому нужно!)
Прибыльность на высоте. Нет потерь – выпуск максимальный, себестоимость минимальная – доходы взлетают до потолка. Хватит и на дивиденды акционерам, и на бонусы руководству, и на технические модернизации, и (тоже важно!) чтобы платить хорошим сотрудникам зарплату выше средней по отрасли.
Текучесть кадров минимальная, сотрудники держатся за свои рабочие места. Мест, где так хорошо работать, слаженный коллектив и достойная зарплата, не так уж много, и ваша фабрика одна из таких.
И ещё важный момент: есть чем гордиться. Преобразить производство из «как у всех» в вот такое упорядоченное, удобное, производительное и высокодоходное – это, знаете ли, достижение. Все хотят, чтобы на предприятии всё работало как часы, легко, понятно, предсказуемо, управляемо и с максимальной прибылью. Но собраться и довести затею до победного финала способны не все. А вы сможете.
Ну а потом, вероятно, вы захотите нечто большее. Высокий уровень культуры и отличные показатели станут для вас мечтой, которая уже сбылась, и захочется сделать своё очень хорошее производство совершенным. Тогда вы сделаете то, что написано в главе «Продвинутый уровень управления». То, что в России – по крайней мере, в пищёвке и FMCG – пока ещё мало кому удалось, хотя это не так сложно. Скоро сами увидите.
Да, и ещё два аспекта, на первый взгляд не связанных с бережливым производством, но чрезвычайно важных.
Не обойтись без внедрения правильной IT-интеграции. Очень важно автоматизировать, синхронизировать все процессы, чтобы, с одной стороны, упростить и ускорить рабочие процедуры, с другой – иметь нужные данные для эффективного управления. Обязательно раскроем связь между MES, ТОиР и процессами.
И ещё – снова о людях. Вам нужно, чтобы ваш персонал был грамотным и мотивированным, и желательно, чтобы, даже несмотря на текучесть кадров, знания сохранялись внутри предприятия, передавались от человека к человеку. Для этого есть технология наставничества, о ней будет отдельно.
Вы готовы? Начинаем?
Дисклеймер о терминах
Прежде чем перейдём к предметному разговору об этапах внедрений, должен сделать оговорку о допустимой «вольности» в употреблении терминов в этой книге.
У методик повышения эффективности своя история. Когда-то они развивались в разных странах параллельно. Хорошо работающее одни перенимали у других.
Не секрет, что СССР в начале XX века многое перенял из лучших практик США и Германии. Но также создал и много своего. К примеру, у нас разработали НОТ – научную организацию труда, которая потом всплыла в Японии: система «5S», известная как один из столпов корпорации «Toyota», содержит много черт НОТ, чего никто и не скрывает. Да-да, известные эффективностью своей промышленности японцы кое-что перенимали и у нас.
Сейчас на слуху методология Лин Шесть Сигм, в основе которой лежат две концепции: американская Шесть Сигм (Six Sigma) и японская Лин (Lean). При этом Лин – не что иное, как «бережливое производство».
В Лин основной акцент – на устранение потерь. Исключение любой деятельности, потребляющей ресурсы, но не создающей ценности, пользы.
К инструментам и подходам Лин (читай – бережливого производства) относятся, в частности: быстрая переналадка оборудования, рациональная организация рабочих мест («5S»), всеобщее производственное обслуживание (TPM), карта потока создания ценности (value stream map, или линфлоу) и др. Сюда же относится Кайдзен – практика, направленная на непрерывное совершенствование процессов, и не только в производстве, любых процессов.
В методологии Шесть Сигм основной акцент – на системность и организованность. То есть деятельность «упакована» в проекты, где у каждого чёткие цели и сроки, ясное распределение ролей и обязанностей, единообразие в описании стандартов (например, служебных инструкций), а также очень строгое правило о принятии решений на основе фактических данных, измерений, но ни в коем случае не догадок и предположений.
Особое внимание Сигмы уделяют статистическому контролю процессов, который позволяет предсказывать их поведение, что, в свою очередь, даёт возможность заблаговременно внести корректировки в процесс и избежать потенциальных проблем.
К инструментам и подходам Шести Сигм относятся: планирование эксперимента (design of experiment: метод определения оптимальных параметров процесса), DMAIC (метод разрешения сложных многосоставных проблем), статистическое управление процессами (SPC), развёртывание функции качества (quality function deployment: определение наиболее важных, с точки зрения удовлетворенности клиента, характеристик продукта) и др.
В конце 1990-х оба подхода, Сигмы и бережливое производство, перестали сравнивать и начали применять совместно. Так и возник термин «Лин Шесть Сигм».
При этом профессионалы в сфере эффективности, особенно в российском деловом обороте, часто говорят «бережливое производство», подразумевая всё это вместе, то есть, по сути, под бережливым производством имея в виду весь набор инструментов и методов Лин Шесть Сигм.
Так же и я: не буду строго разграничивать смежные понятия, чтобы не затруднять восприятие книги. Профессионалы поймут, а буквоеды пусть меня простят. Ну а читателю-новичку не так уж важна буквоедская точность: мы же хотим повысить эффективность для максимальной прибыли, а не вызубрить правильный словарь. Хорошо?
Итак, начнём…
Сбор данных: всё под контролем
Доказательства лучше рассуждений.
Японская поговорка
Если рассмотреть проблему достаточно внимательно, то вы увидите себя как часть этой проблемы.
Аксиома Дучарма
Реальный случай, коллега рассказывала.
Приехала в командировку в Индию, спрашивает местного на фабрике: «Какая у вас величина OEE на линии?»
OEE – от англ. Overall equipment effectiveness, общая эффективность оборудования: показатель, по которому ясны потери из-за простоев, сбоев, замедлений и пр.
Тот отвечает: «По ощущениям, 83%».
Она: «Что?! По ощущениям – это как?»
«Мы не считали, но я вот так ощущаю», – говорит…
Это всё равно что на вопрос, какая у вас зарплата, сказать: «По ощущениям, сто тысяч». Или на вопрос, сколько у вас детей, сказать: «У меня приблизительно трое».
Я видел индийские фильмы, они там всё время танцуют и поют, так что не исключаю, что у них и на производстве всё иначе, по-своему. Спел, потанцевал в цехе – и сразу ощущаешь: эффективность такая-то.
Если серьёзно, так нельзя, но у нас в России многие тоже «контролируют» своё производство «по ощущениям».
Хватит ощущений, нужны точные данные!
Вы можете управлять только той ситуацией, параметры которой измеряете и знаете. Поднять эффективность – значит минимизировать потери, а для этого надо знать, сколько теряем и где, на чём.
Основные потери на производстве – простои, брак и перевесы. Давайте разберёмся с ними?
Перевес
Перевес – когда фактическая масса продукта выше заявленной. Скажем, продали 100 грамм, а передали 120.
В разных отраслях по-разному, где-то и вовсе без перевесов. Например, когда-то я работал на предприятии, которое занимается добычей и огранкой алмазов, так вот: в бриллиантах перевеса не бывает. Используют сверхточные весы, вплоть до десятитысячной грамма.
Ну а в FMCG продукты дешёвые, поэтому перевес обычное дело. А уж в пищёвке повсеместно.
Мол, чего нам биться за копейки, настроим оборудование на какой-то разумный процент перевеса, да и чёрт с ним. По-своему это разумно, если добиваться стабильного целевого показателя по весу обойдётся дороже, чем отгружать немножко лишнего.
Производители пищевой продукции всегда предпочитают перевесить, чем недовесить. Недовес – обман потребителя, можно налететь на судебный иск. Лучше не рисковать, все перестраховываются, отпускают «с горкой».
Тем не менее, если слишком много перевешивать, набегают существенные суммы. А потери нам ни к чему.
Каковы масштабы перевеса? По-разному.
Например, по вкусной жевательной конфете, которую выпускает компания, которую я консультирую сейчас, перевес составляет всего 4%. Довольно неплохой показатель, обычно в пищёвке перевешивают намного больше.
А вот история, которую мне на днях рассказал друг.
Он решил похудеть, увлёкся правильным питанием и теперь взвешивает всё, что ест. Говорит, взвесил французский багет из «Ашана» (у них своя пекарня в ТЦ «Авиапарк»), оказалось, фактический вес выше номинального: 140 грамм против 125. То есть перевес 12%.
Не берусь критиковать пекарей. Может быть, они могут себе позволить такой перевес, в конце концов, мука стоит куда дешевле, чем ингредиенты карамели, и, возможно, для финансов «Ашана» это приемлемо. Это просто пример: масштаб перевесов у всех разный.
Прежде чем взяться за попытку добиться стабильной и точной развесовки, вам следует понять масштаб потерь. Насколько вы, собственно, перевешиваете?
То есть прежде чем начать борьбу с перевесом, надо убедиться, что он ваш главный на данный момент враг. Обычно предприятия теряют куда больше от брака и простоя – этих врагов и надо победить в первую очередь.
Если вы поймёте, что потери от перевеса – далеко не самая большая дыра, куда выливаются ваши деньги, надо браться сначала за более важную проблему.
Напомню, в этой главе мы говорим не о том, как побороть потери, а о том, как получить данные, на основе которых вы будете принимать решения о борьбе с потерями.
Теперь кратко о «лечении» перевеса.
Его причина – нестабильность производственного процесса, оттого и вес продукта то больше, то меньше.
Производитель избегает недовеса, чтоб рассерженный потребитель не подал в суд, и держит средний вес продукта выше номинального.
Принимают решение так.
Допустим, у нас стандартное отклонение 5 грамм, и мы говорим: давайте настроим оборудование так, чтоб держать средний вес на 5 грамм больше, тогда гарантированно избежим недовеса. Когда-нибудь дойдут руки и до наладки стабильного процесса, а сейчас пока так.
Как измерить перевес на вашем производстве?
Мне знакомы два варианта: хороший и плохой.
Плохой: на линию сажают девочку, которая будет выборочно взвешивать в течение смены вес упаковок продукта на конце конвейера.
Вроде логично: полученный средний вес затем умножить на количество выпуска – это приблизительный вес партии, его можно сравнить с нормативным.
Но ведь у нашей девочки получится очень грубая выборка, точность результатов никудышная. Ну скажите, сколько конфет она успеет взвесить из выпуска?
На одной известной мне фабрике линия карамели выдаёт примерно тысячу штук в минуту – сколько успеешь взвесить? Если вес продукта от единицы к единице «пляшет», а это и есть нестабильный выпуск, то и цифра итоговая получится почти «по ощущениям».
В общем, это не наш метод.
Правильный, надёжный метод – грамотное техническое решение: используем чеквейер (конвейерные весы) и систему IT-интеграции (о ней подробнее в главе 21).
Ставим в конце линии, взвешивает каждую единицу, а система IT-интеграции данные о массе собирает, анализирует и визуализирует. Если девочка могла взвесить лишь выборочно и получались сомнительные цифры, неверные выводы, то чеквейер взвешивает всё, у вас точные данные по всей совокупности единиц продукта.
Кстати, по продукции вроде той же карамели мы не взвешиваем каждую штучку. Они упаковываются в шоу-боксы, такие коробочки, их-то и взвешивает чеквейер, и мы понимаем вес коробки. Зная, сколько в ней конфет, легко посчитать средний вес конфетки в коробке. Ну а дальше просто: фактический вес минус номинальный (как должно быть) – вот и величина нашего перевеса.
На предприятиях, выпускающих другие продукты – например, на вашем предприятии, – решения чуть другие, но суть та же самая, вы поняли.
Организуйте сбор данных по перевесу, чтобы принять решение, бороться ли в первую очередь именно с ним.
А то, может быть, вы теряете намного больше на чём-то другом. Например, на браке…
Брак
Измерить потери от брака несложно. Не надо изобретать велосипед – просто взвешиваем на весах.
Брак сортируем по видам, кладём в лотки разного цвета и взвешиваем по отдельности.
Санитарный брак – что упало на пол: с конвейера, ещё откуда-то. На фабрике, где я сейчас помогаю с внедрением бережливого производства, санитарный брак собирают в лотки чёрного цвета. В конце смены взвешивают – ага, вот сколько «насанитарили», ясно.
Другой вид брака – процессный. Например, дефектные конфеты: расплющенные, помятые, шарик сплюснутый, или из него палочка вывалилась. С гигиеной всё нормально, на пол не падало, но тоже не продашь.
Чтобы не путать с санитарным браком, процессный кладут в лотки другого цвета, взвешивают отдельно.
Работа по взвешиванию ложится на оператора. Он собирает брак в разные лотки и фиксирует, сколько брака произвели и какого именно по видам.
Как фиксировать данные – три варианта.
По старинке: там, где пока ещё не ушли от бумаги, у оператора лежит листочек, чек-лист брака. Вписывает: сегодня санитарного брака 15 кг, а процессного 30 кг.
Если от бумаги перешли хотя бы на электронную табличку (обычно Excel), оператор вносит цифры туда. По сути, электронная версия чек-листа, где прописаны виды брака. Оператор вводит цифры в ячейки, потом файл сгружается сотруднику, который всё будет анализировать.
Третий, самый эффективный вариант фиксации, – с помощью MES-системы. Весы, на которых оператор взвешивает брак, подключены к ней, и сведения о браке автоматически идут в базу данных в разрезе видов и категорий.
Напомню, сейчас речь о том, как наладить сбор данных о потерях, чтобы понять, где теряешь, и, соответственно, устранить причины тех потерь. Именно поэтому очень важно классифицировать брак по видам, категориям. Ведь причины у разных видов брака разные.
Взять тот же процессный брак: он делится на подкатегории. Например, за смену 30 кг, в том числе: карамель колотая – 10 кг, без палочки – 8 кг, деформированная – 12 кг. У карамели без палочки причина, вероятно, не та же, что у колотой, а значит, и способы решений будут разными.
Чтобы понимать, какого брака сколько, нужно измерять отдельно по видам и категориям.
Ах да, кроме санитарного и процессного, есть ещё интересная категория брака – инцидентный: когда случается из ряда вон выходящее событие. Помню, на одном производстве был случай: оператор при засыпке сахара в тестомес уронил вместе с сахаром полиэтиленовый пакет. Тестомес разорвал полиэтилен на кусочки, которые затем оказались в готовом продукте; вся партия печенья пошла в утиль.
Бывает инцидент по качеству из-за ошибки человека: например, оператор в клубничную конфету залил апельсиновый сироп. А бывает из-за ошибки технической системы: например, клапан дозатора сломался и залил в замес 50 литров сиропа вместо 30.
Как видите, виды брака, в зависимости от причин, бывают самые разные. Их нужно классифицировать, хорошенько продумать список видов и категорий брака, характерный для вашего производства, – чтобы фиксация брака давала вам нужную информацию.
Благодаря этому операторы смогут корректно и легко фиксировать данные, а вы – получать достоверные сведения о том, сколько теряете на браке и на каких именно его видах. А там уже рукой подать до избавления от причин, из-за которых тот брак возникает.
Простои
Думаю, что не ошибусь, если скажу: в большинстве случаев главный враг эффективности – простои. Их нужно фиксировать: когда, сколько, продолжительность, тип. Так вы сложите полную картину и увидите, какие из них влекут наибольшие потери.
В наше время фиксировать простои должна MES-система, но нельзя слепо уповать на неё. Объясню.
Давным-давно я работал на заводе, принадлежащем холдингу «Procter & Gamble». Там стояло оборудование, привезённое с его же зарубежных заводов. Весьма неплохое, но б/у, производства 80-х годов – никакой MES там не было. Нам с коллегами поставили задачу: обеспечить данные о простоях. Вот как мы это сделали.
Установили в конце линии концевик, такой датчик, он считал коробки со стиральным порошком, выходящие с конвейера. Коробка, проезжая мимо, задевает концевик – счётчик срабатывает.
Чтобы каждый час фиксировать, сколько коробок доехало до финиша, мы поставили оператору компьютер с табличкой Excel, он ежечасно вписывал в соответствующую ячейку цифру со счётчика.
Далее. Допустим, за час вышло 80 коробок, а по норме должно быть 100 в час. То есть фактический выход меньше нормы на 20%, а значит, и простой составил 20%. Ну а 20% от 60 минут – 12 минут.
Так мы наладили сбор данных о длительности простоев внутри часа. Но это ещё не всё, надо фиксировать причины простоев, чтобы потом с ними расправиться.
Оператор, введя количество выпущенных коробок, вспоминал, какие остановки на его линии были за минувший час. Например, что за остановки были в те 12 минут.
Мог быть один 12-минутный простой, оператор линию останавливал, чтобы почистить от загрязнений. Или могло быть пять простоев по 2—3 минуты: заминало пачку со стиральным порошком, он останавливал, вынимал смятую пачку, вновь запускал.
Вспомнил – вписал в табличку. Каждый час.
Затем эти цифры мы превращали в статистику: день, месяц, квартал, год. Получается целостная картина: где болит, что лечить. Так мы и решили задачу со сбором данных о простоях. Создали ясность, причём в разрезе всех причин, и на этой основе далее успешно устраняли, шаг за шагом, все причины всех простоев.
Помните, три страницы назад я говорил, что надо фиксировать не весь объём брака скопом, а в разрезе видов, категорий? То же с простоями: нужно фиксировать в разрезе видов. Ведь у разных остановок разные причины.
Сегодня фиксировать данные технически намного проще, чем было двадцать лет назад в «Procter & Gamble», ибо есть IT-интеграция, MES-система.
Однако я неспроста рассказал вам ту историю. Мораль басни такова: нужно хорошо понимать ваш процесс.
Многие наивно уповают на IT-решения вроде MES, как на волшебника, с которым порядок сам себя наведёт. Но чтобы наладить IT-интеграцию, кто-то должен сначала описать процессы на производстве, выделить ключевые показатели, установить порядок их фиксации.
В том числе, конечно, выделить причины простоев.
Их, как и другие аналитические маркеры, вы сначала осмыслите, встроите в логическую цепочку своих рассуждений о процессах, а потом внесёте в MES в качестве категорий. Чтобы потом оператор не ломал голову, а просто, ткнув пальцем в экран, выбрал нужный пункт.
А у вас в итоге будут все данные, полная картина…
Правообладателям!
Данное произведение размещено по согласованию с ООО "ЛитРес" (20% исходного текста). Если размещение книги нарушает чьи-либо права, то сообщите об этом.Читателям!
Оплатили, но не знаете что делать дальше?