Текст книги "Справочник автолюбителя"
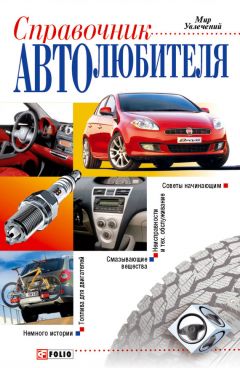
Автор книги: Владимир Ярошенко
Жанр: Автомобили и ПДД, Дом и Семья
сообщить о неприемлемом содержимом
Текущая страница: 5 (всего у книги 26 страниц) [доступный отрывок для чтения: 9 страниц]
На современных автомобилях, сходящих с конвейера завода, установлены аккумуляторные батареи нового типа – необслуживаемые, готовые к использованию, т. е. залитые электролитом и заряженные. В таком же виде эти батареи поступают в запасные части.
Корпус (моноблок) батареи изготовлен из белой или цветной термопластичной пластмассы с общей крышей и межэлементными соединениями сквозь перегородку моноблока.
В связи с тем, что на батарее блоки электродов (пластины) опущены до самого дна, над пластинами более чем в 2 раза увеличился объем электролита, что позволило уменьшить периодичность доливки дистиллированной воды. При нормальном зарядном токе батарея нуждается в доливке дистиллированной воды не более 1 раза за четыре месяца эксплуатации. Батареи имеют меньший саморазряд и могут храниться залитыми электролитом и заряженными в течение 12 месяцев без подзарядки.
Готовность батареи к эксплуатации при установке на автомобиль проверяется путем измерения статического напряжения и плотности электролита. При напряжении менее 12,5 В батарею необходимо подзарядить.
Не реже 1 раза в месяц следует:
– проверить надежность крепления батареи в гнезде и контактов наконечников проводов с выводами батареи;
– при необходимости очистить батарею от грязи и пыли;
– проверить, нет ли видимых повреждений, таких как трещины и разрушения моноблока, крышки, вызывающие утечку электролита; при обнаружении течи снять батарею с автомобиля и устранить повреждение.
Периодически через каждые четыре месяца следует проверить уровень электролита. При значительном снижении уровня электролита необходимо проверить исправность электрооборудования. Регулируемое (зарядное) напряжение реле-регулятора должно быть в пределах 14,1+0,2 В.
Для доливки дистиллированной воды нужно снять планку и вывернуть пробку. Не допускается эксплуатация батарей с уровнем электролита ниже нижней линии на моноблоке. Доливать в аккумуляторы электролит воспрещается, за исключением тех случаев, когда точно известно, что понижение уровня электролита произошло за счет его выплескивания. При этом плотность доливаемого электролита должна быть такой же, какую имел электролит в аккумуляторе до выплескивания.
Батарею, не установленную на автомобиль или снятую с автомобиля после небольшого периода работы, необходимо полностью зарядить и довести плотность электролита до нормативных значений, а затем плотно ввернуть пробки и вставить планку. Такую батарею по возможности нужно хранить в неотапливаемом сухом помещении, защитив ее от прямого попадания солнечных лучей.
При отказе батареи в процессе эксплуатации, а также периодически через каждые 4 месяца необходимо проверять ее заряженность измерением плотности электролита аккумуляторным ареометром.
После определения плотности электролита в аккумуляторах следует установить степень заряженности батареи. Батарею, разряженную более чем на 25 % зимой и более чем на 50 % летом, необходимо снять с автомобиля и подзарядить с помощью зарядного устройства.
Срок хранения новой батареи без подзарядки составляет
12 месяцев. После 12 месяцев бездействия аккумуляторную батарею следует подзарядить и установить на автомобиль или на следующий период хранения (таких периодов может быть не более трех). Для подзарядки аккумуляторной батареи необходимо снять ее с автомобиля, присоединить положительный вывод батареи к положительному полюсу источника постоянного тока, а отрицательный – к отрицательному, снять с батареи планку и отвернуть пробки, установить зарядный ток 2,2 А. В процессе заряда необходимо следить за температурой электролита. Она должна быть в пределах 15–45 °C. Заряд следует проводить до постоянства напряжения и плотности электролита в течение трех часов.
Если уровень электролита окажется ниже нормы, нужно в аккумуляторную батарею долить электролит либо дистиллированную воду до уровня, соответствующего метке.
Свеча зажигания искровая служит для образования искрового разряда и зажигания рабочей смеси в камере сгорания двигателя. Искровая свеча (рис. 3.2.16, а) состоит из изолятора 1, корпуса 4, центрального 7 и бокового 8 электродов.
Для герметизации свечи по центральному электроду применен токопроводящий стеклогерметик 3. Герметичность между изолятором и корпусом свечи осуществляется прокладкой 5 и термоосадкой корпуса свечи по верхнему бортику изолятора.
В процессе работы на двигателе на части свечи, расположенные в камере сгорания, попадает масло, которое, сгорая, образует нагар, шунтирующий искровой зазор в свече. Это приводит к утечке энергии и снижению вторичного напряжения. Энергия может также утекать по наружной поверхности изолятора, если она загрязнена или покрыта влагой.
Нагар на тепловом конусе 9 изолятора исчезает при нагреве его до температуры 400–500 °C. Эта температура называется температурой самоочищения свечи. Если температура теплового конуса изолятора превышала 850–900 °C, может возникнуть калильное зажигание.



Рис. 3.2.16. «Горячая» (а), «холодная» (б) свечи зажигания искровые, тепловой баланс и температура различных мест изолятора (в) свечи:
1 — изолятор, 2 – контактная головка, 3 — токопроводящий стекло-герметик, 4 – корпус, 5, 6 — уплотнительные прокладки, 7 – центральный электрод, 8 — боковой электрод, 9 – тепловой конус (юбочка)
Температура теплового конуса изолятора 400–900 °C называется тепловым пределом работоспособности свечи. Так как тепловой предел для всех свечей практически одинаков, а тепловые условия работы свечи на различных двигателях существенно отличаются, то свечи изготовляют с различной тепловой характеристикой (калильным числом). Калильное число характеризует способность свечи работать на двигателе без калильного зажигания. Чем выше это число, тем надежнее свеча будет работать на двигателе с высокой степенью сжатия. Калильные числа могут иметь следующие значения: 8, 11, 14, 17, 20, 23 и 26.
В условном обозначении свечей зажигания (например, А17ДВР) цифры и буквы обозначают: первая А – резьба на корпусе М14х1,25 или М – резьба на корпусе М18х1,65; вторые одна или две цифры – калильное число; далее буквы Н (длина резьбовой части корпуса 11 мм) или Д (длина резьбовой части корпуса 19 мм); В – выступание теплового конуса изолятора за торец корпуса; Р – герметизация по соединению изолятор – центральный электрод термоцементом.
3.2.1 °Cистема смазкиБесперебойный подвод масла к трущимся поверхностям в ДВС обеспечивает система смазки.
Система смазки автомобильного двигателя должна обеспечивать подачу достаточного количества масла к трущимся деталям при работе на различных скоростных и нагрузочных режимах, при подъемах и спусках до 35 %, кренах до 25 %, при отрицательных и положительных температурах окружающего воздуха, положительных и отрицательных горизонтальных и вертикальных ускорениях. Кроме того, она должна обеспечивать возможность длительной работы двигателя без перегрева масла с минимальным его расходом, а также обеспечивать достаточную очистку масла от механических примесей, не требовать больших трудозатрат на обслуживание.
Подвод масла к трущимся поверхностям осуществляется с помощью циркуляционных систем смазки или путем добавления масла в состав топлива (3–6 % по объему).
Последний вариант смазки используется в маломощных двухтактных двигателях с кривошипно-камерной продувкой. В остальных двигателях применяются циркуляционные системы смазки, в которых масло, подводимое к трущимся поверхностям, собирается, очищается от продуктов износа и повторно подается для смазки деталей.
В зависимости от способа подвода масла в циркуляционных системах различают подачу смазки под давлением и путем разбрызгивания. В современных системах смазки двигателей используются оба варианта подвода масла, поэтому их называют комбинированными. Под давлением смазываются коренные и шатунные подшипники коленчатого вала, подшипники распределительного вала, вала турбокомпрессора, оси коромысел привода клапанов, сопряжения шатунов с поршневыми пальцами и др. В некоторых конструкциях для улучшения смазки организуется принудительный впрыск масла на зеркало цилиндра, а также на внутреннюю поверхность днища поршня с целью его охлаждения. Подвод масла под давлением организуется также в охлаждаемых циркулирующим маслом поршнях, к поршням с изменяемой степенью сжатия, гидравлическим толкателям клапанов, механизмам изменения фаз газораспределения и к другим исполнительным механизмам. Остальные подвижные детали двигателя смазываются путем разбрызгивания – каплями, образующимися при вытекании масла из подшипников коленчатого вала и других сопряжений. При этом распределение разбрызгиваемого масла в значительной степени связано с компоновкой двигателя.
В зависимости от места размещения основного запаса масла различают системы смазки с мокрым (рис. 3.2.17, а) и сухим (рис. 3.2.17, б) картером.
В автомобильных двигателях наиболее распространены системы смазки с мокрым картером, которые имеют более простую конструкцию. В этом случае основной запас масла находится в поддоне картера и при работе двигателя масло подается к трущимся деталям масляным насосом.
В системах с сухим картером основной запас масла содержится в автономном масляном баке и масло подается к трущимся деталям нагнетающим масляным насосом. Стекающее в поддон масло полностью удаляется из него откачивающим насосом и вновь подается в масляный бак.
Система смазки с сухим картером обеспечивает длительную работу на крутых подъемах, спусках и при кренах без утечки масла через сальники коленчатого вала, а также дает возможность снизить высоту двигателя. Отсутствие запаса масла в зоне вращения коленчатого вала исключает возможность его забрасывания на стенки цилиндров, что положительно влияет на снижение эксплуатационного расхода смазки.
Кроме того, при сухом картере масло в меньшей степени нагревается от горячих деталей и подвергается воздействию картерных газов, благодаря чему сохраняет свои физико-химические свойства в течение более длительного времени, чем в системах с мокрым картером.
В основу большинства систем смазки положен один и тот же принцип. Масло из картера 11 (или бака 14) нагнетающим насосом 2 через полнопоточный фильтр 3 подается в масляную магистраль. Давление в ней контролируется манометром 5. Из масляной магистрали масло подается к шейкам коленчатого вала 16 (в некоторых вариантах к одной шейке, а к остальным по внутренним каналам коленвала), распределительного вала 8 и к другим парам трения. Слив избытка масла из магистрали осуществляется через фильтр 9. Контроль температуры масла осуществляется термометром 12, охлаждение – с помощью радиатора 13. Уровень масла контролируется мерным щупом 10. Для откачки масла в системах с сухим картером используются насосы 75. В качестве насосов в системах смазки, как правило, используются шестеренчатые насосы (прямозубые или косозубые) с шестернями внешнего или внутреннего зацепления.


Рис. 3.2.17. Схемы систем смазки:
а – с мокрым картером; б – с сухим картером; 1 — маслоприемник,
2 – нагнетающий насос, 3, 9 — фильтры, 4 — редукционный клапан, 5 – манометр, 6 — подвод масла к коленчатому валу, 7 – поршень, 8 – распределительный вал, 10 – щуп, 11 – картер, 12 — указатель температуры, 13 — радиатор, 14 – бак, 15 — откачивающий насос, 16 – коленчатый вал
Производительность масляного насоса и создаваемое давление в значительной мере зависят от вязкости масла и частоты вращения вала двигателя, которая изменяется в широких пределах. Кроме того, в процессе эксплуатации сопряженные детали двигателя изнашиваются, что приводит к увеличению зазоров между ними и к повышению количества прокачиваемого масла. Чтобы обеспечить бесперебойную подачу масла ко всем трущимся деталям при неблагоприятном сочетании указанных факторов, расчетную производительность масляного насоса увеличивают, а для поддержания требуемого давления в магистрали вводят регулятор, называемый редукционным клапаном.
Редукционные клапаны могут устанавливаться в корпусе насоса на входе в главную масляную магистраль или в конце масляной магистрали. Установка редукционного клапана в корпусе насоса исключает возможность резкого повышения давления на входе в магистраль. Однако в этом случае давление в конце магистрали, под которым смазываются подшипники, может значительно колебаться при изменении гидравлического сопротивления системы и расхода масла. В связи с этим в некоторых системах устанавливают два редукционных клапана – в начале и в конце магистрали. Кроме редукционных в системах смазки могут устанавливаться нагнетательные, впускные, обратные и перепускные клапаны.
Давление масла в системах смазки ДВС различных типов и назначения находится в пределах от 0,2 до 1,5 мПа. Большие значения относятся к быстроходным форсированным двигателям.
Производительность используемого в системе смазки насоса должна обеспечивать расход масла 13–68 л/кВт-ч. Наибольшие значения используются для форсированных быстроходных двигателей с масляным охлаждением поршней.
Объем масла в системах смазки с мокрым картером для двигателей различных типов составляет 0,03—0,48 л/кВт.
Очистка масла от механических примесей в системах смазки осуществляется фильтрами. Наибольшее распространение в двигателях современных автомобилей получили бумажные полнопоточные поглощающие фильтры, улавливающие частицы размером до 0,5 мкм.
Для исключения перегрева масла и сохранения нормального теплового режима трущихся пар масло в системе смазки двигателя, особенно в летний период, нуждается в охлаждении. Чаще всего для этого используются воздушно-масляные радиаторы, устанавливаемые перед радиатором системы охлаждения двигателя.
С целью снижения вредного воздействия на масло прорывающихся из камеры сгорания газов (картерных газов), а также снижения давления в картере для предотвращения утечек масла из двигателя картер снабжают системой вентиляции. В настоящее время для минимизации вредных выбросов автомобильными двигателями в атмосферу используют закрытые системы вентиляции картера. Для отвода картерных газов в этих системах картер соединяется с впускным трубопроводом и (или) с воздушным фильтром.
3.3. Трансмиссия
Группа агрегатов, входящих в трансмиссию автомобиля, предназначена для передачи крутящего момента от двигателя к ведущим колесам, изменения его по величине и направлению и распределения между ведущими мостами и колесами.
В нашей стране, а также в ряде других государств предельная нагрузка на ось автомобиля ограничена, что необходимо для сохранности автомобильных дорог. В связи с этим автомобили большой грузоподъемности выпускаются многоосными.
Увеличение числа осей, а следовательно, и числа колес, уменьшает давление на полотно дороги и обусловливает меньший его износ. Увеличение числа ведущих осей улучшает проходимость автомобиля, для характеристики которой большое значение имеет так называемая колесная формула, состоящая из двух цифр: первая из них обозначает общее число колес, вторая – число ведущих колес, например 6x4 для трехосного автомобиля, имеющего всего 6 колес и из них 4 ведущих. Каждая пара ведущих колес имеет свой ведущий мост.
Схема трансмиссии определяется числом и расположением ведущих мостов автомобиля. В двухосном автомобиле с одним задним ведущим мостом в трансмиссию входят сцепление, коробка передач, карданная передача, главная передача с дифференциалом и полуоси. Если ведущими являются передний и задний мосты автомобиля («Нива»), то в его трансмиссию входит еще раздаточная коробка. Раздаточная коробка позволяет распределить крутящий момент между ведущими мостами автомобиля.
3.3.1. СцеплениеСцепление представляет собой фрикционную муфту, в которой передача крутящего момента происходит за счет силы трения. Оно позволяет отключить двигатель от коробки передач в момент переключения передач и для получения свободного хода.
По конструкции автомобильные сцепления делятся на одно– и двухдисковые. На большинстве автомобилей применяется однодисковое сухое сцепление.
Размеры сцепления определяются наружным диаметром ведомого диска, который выбирают, исходя из требований передачи максимального крутящего момента, развиваемого двигателем, и рассеивания тепла, появляющегося при буксовании сцепления в момент переключения передач.
На рис. 3.3.1 показано устройство однодискового сцепления с периферийными пружинами.

Рис. 3.3.1. Однодисковое сцепление с периферийными нажимными пружинами:
1 — картер маховика, 2 – кожух сцепления, 3 – нажимные пружины, 4 — маховик, 5 – ведущий вал коробки передач, 6 — пружина гасителя, 7 – ведомый диск, 8 – рычаги выключения сцепления, 9 — нажимный диск, 10 — диски гасителя с маслоотражателем, 11 – муфта выключения сцепления
К маховику 4 привернут кожух 2 с гнездами для нажимных пружин 3. Когда сцепление включено, нажимный диск 9 под действием пружин прижимает к торцовой поверхности маховика ведомый диск 7, сидящий на шлицах ведущего вала 5 коробки передач. Выключают сцепление отводом муфты 11, действующей на нажимный диск посредством рычагов 8. Рычаги отводят нажимный диск вправо, и давление на ведомый диск 7 прекращается.
К ведомому диску приклепаны фрикционные накладки из материала, обладающего большим коэффициентом трения.
Для быстрого гашения крутильных колебаний, передаваемых сцеплением от коленчатого вала двигателя, в ведомом диске сцепления устанавливают гаситель крутильных колебаний (демпфер), который устроен следующим образом. К ступице ведомого диска приклепаны с двух сторон диски 10 гасителя с маслоотражателями. Между дисками гасителя установлена опорная пластина. В ведомом диске и в опорной пластине выполнены окна с отбортовками, в которых расположены цилиндрические пружины 6.
При резком изменении крутящего момента, вызываемом крутильными колебаниями, ведомый диск поворачивается на некоторый угол относительно ступицы и пружины 6 сжимаются. При этом происходит трение между ведомым диском и фрикционными накладками гасителя, поглощающее энергию крутильных колебаний и приводящее к их затуханию.
На некоторых моделях отечественных автомобилей («Москвич», «Жигули») устанавливалось сцепление с одной центральной диафрагменной нажимной пружиной (рис. 3.3.2). Пружине придана форма усеченного конуса. Она отштампована из листовой пружинной стали толщиной 0,9 мм. Радиально расположенные 18 лепестков пружины служат не только упругими элементами, но одновременно являются выжимными рычагами.
Существенным преимуществом диафрагменной пружины является ее нелинейная характеристика. При изменении нажатия на такую пружину усилие сначала возрастает, а затем, дойдя до определенного значения, начинает падать, в то время как у цилиндрических пружин усилие всегда пропорционально их сжатию.
В случае износа фрикционных накладок сцепления предварительное сжатие цилиндрических нажимных пружин уменьшается, давление на диски уменьшается и сцепление начинает пробуксовывать. При установке же диафрагменной пружины износ накладок практически не отражается на давлении, создаваемом пружиной, и опасность пробуксовки сцепления в этом случае исключена. Применение диафрагменной нажимной пружины позволяет уменьшить габаритные размеры, массу и значительно упростить конструкцию сцепления.


Рис. 3.3.2. Диафрагменное сцепление автомобиля ВАЗ:
а — в сборе, б — детали; 1 – пластина крепления нажимного диска к кожуху сцепления, 2 — болт крепления кожуха к маховику, 3 – соединительная пластина крепления упорного фланца к кожуху, 4 – пружина крепления муфты подшипника к вилке, 5 – вилка включения сцепления, 6 – муфта подшипника выключения сцепления, 7 – картер сцепления, 8 – зубчатый венец маховика, 9 – пружинная шайба, 10 – кожух сцепления, 11 – нажимный диск, 12 – ведомый диск в сборе, 13 – пружина гасителя колебаний ведомого диска, 14 — фрикционное кольцо гасителя колебаний ведомого диска, 15 – пружина фрикционного элемента гасителя колебаний, 16 — ступица ведомого диска, 77– ведущий вал коробки передач, 18 — крышка подшипника ведущего вала коробки передач, 19 – болт, 20 – фиксатор нажимной пружины, 21 – маховик, 22 – подшипник выключения сцепления, 23, 24 – фрикционная накладка, 25 – заклепка крепления фрикционных накладок к ведомому диску
Отсутствие отдельных деталей, расположенных на периферии сцепления, облегчает его балансировку и исключает появление центробежных сил, которые могли бы уменьшить давление на диски при работе с большим числом оборотов. Таким образом, на ведомый диск сцепления передается равномерная нагрузка при всех режимах работы.
Особенности устройства сцепления с диафрагменной пружиной заключаются в наличии двух неразборных сборочных единиц (узлов). В один из них входит нажимный диск 11 в сборе с диафрагменной пружиной и кожухом 10. Другой сборочной единицей (узлом) является ведомый диск 12 с гасителем крутильных колебаний. Сцепление заключено в картер 7, отлитый из алюминиевого сплава, крепящийся к картеру маховика.
Для выключения сцепления служит скользящая муфта с шариковым подшипником 22, усилие на которую передается от педали управления через гидравлический привод.
Сцепление с диафрагменной пружиной требует минимального технического обслуживания. Для его нормальной работы необходимо лишь обеспечить правильный свободный ход педали сцепления и поддержание в заполненном состоянии системы гидравлического привода.
Сцепление выключается с помощью механического или гидравлического привода. Устройство его показано на рис. 3.3.3. Педаль 1 выключения сцепления установлена на оси, вращающейся в пластмассовых сферических подшипниках. При нажатии на педаль ось поворачивается и приводит в движение систему 5 тяг и рычагов, действующих на вилку выключения сцепления 8. Поворачивание вилки 8 вызывает перемещение муфты 3 выключения сцепления, которая посредством выжимного подшипника действует на рычаг сцепления, оттягивающий нажимный диск от ведомого, и тем самым выключает сцепление.
При отпускании педали сцепления оттяжные пружины 2 и 7 возвращают все части привода в исходное положение, и сцепление включается.
На многих отечественных легковых автомобилях применяется гидравлический привод выключения сцепления, состоящий из главного и рабочего цилиндров, соединенных между собой трубопроводом. Полости цилиндров и трубопровод заполнены тормозной жидкостью.

Рис. 3.3.3. Механический привод выключения сцепления:
1 — педаль сцепления, 2, 7 — оттяжные пружины, 3 – муфта,
4 — подшипник выключения сцепления, 5 — тяги, 6 — валик выключения сцепления, 8 – вилка выключения сцепления


Рис. 3.3.4. Гидравлический привод выключения сцепления:
1 — бачок, 2 – главный цилиндр, 3 – плунжер, 4 — толкатель главного цилиндра, 5 – шаровая опора вилки, 6 – вилка выключения сцепления, 7 – оттяжная пружина, 8 — педаль, 9 – толкатель рабочего цилиндра, 10 – рабочий цилиндр
Устройство такого привода показано на рис. 3.3.4. Педаль 8 выключения сцепления соединена с толкателем главного цилиндра, действующим на его плунжер 3. Перемещение плунжера оказывает давление на жидкость, передаваемое по трубопроводу в рабочий цилиндр 10. Под давлением жидкости плунжер рабочего цилиндра перемещается вправо и через толкатель 9 действует на вилку 6, которая отводит выжимной подшипник и выключает сцепление.
Нарушение работы гидравлического привода может быть вызвано попаданием в него воздуха. Для удаления воздуха (путем прокачки системы) на корпусе рабочего цилиндра установлен перепускной клапан.
Правообладателям!
Данное произведение размещено по согласованию с ООО "ЛитРес" (20% исходного текста). Если размещение книги нарушает чьи-либо права, то сообщите об этом.Читателям!
Оплатили, но не знаете что делать дальше?