Текст книги "Управление операционной логистической деятельностью"
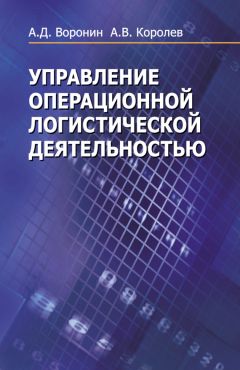
Автор книги: Андрей Королев
Жанр: Учебная литература, Детские книги
сообщить о неприемлемом содержимом
Текущая страница: 6 (всего у книги 18 страниц) [доступный отрывок для чтения: 6 страниц]
6.6. Планирование, связывающее средний и текущий временные периоды
Данный вид планирования должен обеспечить:
• оптимальное распределение ресурсов по производственным участкам и рабочим местам (центрам);
• определение оптимального размера партий;
• установление приоритетности работ (существует 10 правил формирования приоритетов, о которых речь пойдет ниже);
• текущее перераспределение приоритетов и централизованное управление движением (диспетчирование, характерное для выталкивающего управления);
• периодическая актуализация информационных панелей о состоянии потоков (диспетчирование, характерное для вытягивающего управления);
• цеховое управление производственной деятельностью, заключающееся в ежедневном планировании рабочих мест и распределении ресурсов, контроле прохождения заказов и предупреждении остановок;
• проталкивание срочных заказов – процедура, характерная только для выталкивающего управления, не обеспечивающего участия в анализе контрактов производственников и закупщиков.
Собственно производственная часть операционного планирования, находящаяся исключительно в компетенции цеховых работников, начинается именно с этапа текущего планирования.
Порядок планирования для каждого предприятия имеет свою специфику. Текущее планирование отражает показатели стратегического планирования и одновременно является декомпозицией маркетинговых планов (продаж). Очевидно встраивание в потоки текущей деятельности бюджетирования, которое осуществляется на основе потоков и покрытия затрат внутренних поставщиков внутренними потребителями и связывает все эти планы.
6.7. Организация текущего планирования
Перед лицами, отвечающими за планирование, должны быть поставлены определенные цели, которые необходимо достигнуть в результате планирования и выполнения планов. Цели могут быть следующие:
• безусловное (или обусловленное) выполнение сроков изготовления и поставок;
• достижение специальных качественных характеристик с ослаблением требований к срокам;
• жесткие сроки и уровень соответствия требованиям;
• минимизация длительности всех процессов для соблюдения установленного такта;
• минимизация оборотных ресурсов, в том числе незавершенного производства;
• исключение простоев и очередей;
• минимизация процессов, не добавляющих ценности. Могут быть и другие целевые установки, связанные, например, с минимизацией издержек или повышением скорости реагирования на изменения требований рынка.
Рассмотрим варианты организации и техники планирования.
Существует, по крайней мере, два варианта организации планирования: с использованием техники «планирование вперед» и техники «планирование назад».
Техника «планирование вперед». Применяется при работе на неустойчивом, слабо предсказуемом рынке, когда цеховое планирование осуществляется в «горящих» условиях. Тогда ведут отсчет «вперед» от текущей даты, пытаясь уменьшением длительности процессов и цикла в целом приблизиться к сроку выполнения заказа, установленному потребителем. В этом случае чаще всего востребована функция проталкивания срочных заказов.
Техника «планирование назад». Применяется при работе на рынках с регулярным устойчивым планированием. В этом случае рассчитывают сроки запуска изделий в производство, отсчитывая эту дату от срока поставки, установленного заказчиком, «назад», к поставщикам.
Ситуация в бизнесе складывается так, что успешные предприятия благодаря плотным партнерским отношениям с потребителями все большую часть планирования переводят на второй вариант.
Рассмотрим методы текущего планирования, основанные на его функциях. Их применение позволяет на практике для каждого предприятия устанавливать порядок планирования, наилучший с точки зрения сочетания и последовательности выполнения этих функций.
Оптимальное распределение ресурсов по производственным участкам и рабочим местам (центрам). Для реализации этой функции в каждом цехе по каждому рабочему месту должны быть разработаны оптимальные схемы работы в режиме поддержания установленных параметров и в режиме с переналадкой. Кроме того, должно быть предварительно спланировано оптимальное размещение рабочих мест, обеспечивающее минимальное применение процессов и операций, не добавляющих ценности.
Должны быть также предварительно определены оптимальные правила взаимодействия между рабочими местами по поводу передачи изготовленных изделий, обеспечения их ресурсами и управляющей информацией. Для каждого рабочего места необходимо установить перечень выполняемых работ, правила замены, совмещения профессий и подтверждения квалификации и компетентности.
Документирование этих требований может быть осуществлено с помощью стандарт-планов для рабочих мест, в которых устанавливаются:
1) требования к производственной среде;
2) параметры подготовительных работ для рабочих мест;
3) параметры настроечных работ для рабочих мест;
4) параметры прочих работ для рабочих мест.
Соединение рабочих мест в поток целесообразно проектировать в виде циклограмм, которые объединяют в себе логистику потоков и технологические циклы в привязке к ритмам, устанавливаемым в зависимости либо от параметров продаж, либо от «барабана» узких мест. Если все это имеется, для дальнейшей реализации данной функции необходимо управлять приоритетами.
Определение оптимального размера партий. Необходимо иметь возможность оптимизировать размеры партий, увязывая их с экономическими показателями. В качестве параметров, на основе которых устанавливается оптимальный размер партии, чаще всего берутся следующие:
1) ритм поставки изделий потребителю, обеспечивающий конкурентоспособность;
2) количество изделий в загрузке для групповой обработки;
3) время переналадки и его сравнение с временем переработки партии;
4) минимальный объем и дискретность закупок;
5) расходы на заказ и на хранение;
6) потери от очередей и ожиданий.
Вывод формулы возможен, но лучше всего для каждого предприятия ранжировать перечисленные параметры и строить графики их взаимной зависимости для нахождения оптимума. Такую работу необходимо делать для отдельных цехов или их групп исходя из характера производства.
Установление приоритетности работ. Существует 10 правил, определяющих варианты формирования приоритетов:
1) по принципу «Первым вошел – первым обработан и поставлен»;
2) по самому короткому совокупному циклу изготовления;
3) по установленным срокам выполнения заказа и поставки;
4) по дате заключения контракта;
5) по минимальному оставшемуся времени на выполнение заказа;
6) по расчетному минимальному времени, остающемуся на конкретные критические операции;
7) по критическому отношению, величина которого рассчитывается как отношение периода времени, оставшегося до выполнения заказа, к технологически необходимому. Чем меньше коэффициент, тем раньше необходимо изготовить партию (изделие);
8) по отношению времени, остающегося до срока выполнения заказа, к нормативу пребывания в очереди, если на предприятии существуют эти нормативы;
9) по принципу «Последним вошел – первым обработан и поставлен»;
10) в порядке, устанавливаемом руководителями, плановиками или самими исполнителями.
Применение этих правил обусловлено тем, какие циклограммы реально установлены для различных вариантов изготовления изделий и исполнения заказов. Результаты такого планирования должны отражаться на оперативных графиках движения товарно-материальных ценностей, например в виде графиков Гантта, имеющих очень простую и удобную форму (табл. 6.6).
Таблица 6.6
Оперативный график движения товарно-материальных ценностей

График Гантта напрямую связан с циклограммами, а также с реальными сроками планово-предупредительного ремонта, подготовительных, транспортных и прочих операций.
Диспетчирование (текущее перераспределение приоритетов или периодическая актуализация информационных панелей о состоянии потоков). Главная задача диспетчирования – обеспечить актуальность графиков Гантта в режиме реального времени. Для его нормального соблюдения необходимо создать систему привязки вспомогательных процессов к основному потоку. В графиках Гантта для этого могут быть предусмотрены столбцы «Вспомогательные входы», позволяющие управлять связями с ответственными лицами, которые должны планировать свою деятельность в зависимости от реальной ситуации с планом и фактом на входах и выходах основного процесса.
Для исключения невыполнения заданий при централизованном планировании полезным является создание ежедневных списков очередей, формируемых по иерархии, начиная от центральной диспетчерской службы.
Цеховое управление производственной деятельностью. Включает следующие функции:
1) организация выполнения тактических календарных планов и заданных уровней качества;
2) оперативное планирование производства на каждом участке;
3) планирование и поддержание инфраструктуры в состоянии, обеспечивающем вовлечение персонала в выполнение планов и позволяющее постоянно повышать результативность и эффективность;
4) обеспечение рабочих мест материалами, полуфабрикатами, сервисом механиков и энергетиков;
5) обеспечение настройки, идентификации и прослеживаемости;
6) обеспечение сбора данных и обработки текущей информации;
7) управление незавершенным производством;
8) поддержка текущего календарного планирования;
9) цеховое диспетчирование;
10) мониторинг и оптимизация выполнения заказов;
11) управление входами и выходами;
12) сбор информации и обеспечение отчетности.
Проталкивание срочных заказов. Эта процедура характерна только для такого варианта выталкивающего управления, в котором не обеспечивается участие в анализе контрактов производственников и закупщиков. Реальная жизнь заставляет поручать такую роль группам специальных представителей заказчика, выполняющего только эту функцию.
6.8. Организация планирования деятельности участков и вспомогательных служб
Данный этап планирования зависит от размеров участков и их роли в производственных процессах. Если участок по своим размерам, функциям и роли соответствует уровню цеха, планирование в нем должно быть организовано по цеховому принципу. Если же участок не находится на уровне цеха, он должен быть включен в общую логистику планирования как рабочий центр (производственная ячейка) или как набор этих центров. Это касается как основного, так и вспомогательного производства.
Удобно осуществлять планирование производства на уровне участков, мастеров и рабочих по производственным ячейкам, или рабочим центрам, или бригадам.
Планирование на уровне участков, мастеров и рабочих эффективно с применением рабочих центров, но с ними или без них необходимо отталкиваться от планирования трудовых процессов. Это планирование направлено на поддержание высокой эффективности деятельности и рабочих, и производственных участков, и цехов. Поддержание высокого уровня эффективности подразумевает возможность работать, не отвлекаясь, что обеспечивается вовлечением всех производственных процессов.
Планирование производственных процессов в свете изложенного подразумевает такое распределение работ, которое обеспечивает максимальную отдачу от каждого работника. Для этого служит элементарная единица планирования – сменное задание (табл. 6.7).
Таблица 6.7
Сменное задание

Приведенная форма включает систему экономической оценки степени соответствия выполненных заданий требованиям, осуществляемой внутренним потребителем, что подразумевает планирование трудовых процессов на уровне мастера. В операционном менеджменте для этого разработаны пять принципов:
1) оптимальное разнообразие рабочих заданий в пределах компетенций рабочих;
2) концентрация заданий на применение рабочими наиболее эффективных умений и творческих подходов;
3) организация постоянной обратной связи от конечных внутренних потребителей;
4) оптимальное сочетание индивидуальной и групповой ответственности с полномочиями;
5) автономность рабочих, т. е. постоянное подчеркивание в процессе планирования самостоятельности рабочих и их права собирать данные, анализировать их и принимать решения в пределах своей компетенции.
Для поддержки системы экономически контролируемых сменных заданий желательно введение горизонтального сквозного планирования, основанного, например, на графиках Гантта. Эти графики и сменные задания обеспечивают не только ежедневную установку внутренним поставщикам и потребителям количественных и качественных показателей, но и привязку к ним согласно их ответственности и полномочиям.
Если операционные менеджеры планируют деятельность вспомогательных подразделений локально, без привязки к конкретным текущим задачам и проблемам производственного подразделения, это чисто декларативное мероприятие. Поэтому главная задача при организации такого планирования – обеспечить возможность горизонтального взаимодействия в режиме реального времени соответствующих уровней производственных и вспомогательных подразделений на основе:
• понятной ответственности вспомогательных подразделений перед производственными;
• отражения деятельности вспомогательных подразделений в графиках Гантта конкретных подразделений;
• возможности применения механизма сквозного покрытия издержек внутренних поставщиков внутренними потребителями.
По отношению к производственным потокам главная задача вспомогательных служб – поддержание высокой эффективности их функционирования. Вспомогательные службы должны планировать свою работу по ремонту и техническому обслуживанию таким образом, чтобы основные производящие потоки не меняли своей производительности. Особенности планирования, характерные для предприятий сферы услуг, обусловлены непосредственным взаимодействием представителя продавца и покупателя услуги, а также нематериальным характером продаваемого продукта. Несмотря на то что в процессе оказания услуги покупатель может вместе с нематериальным компонентом получать и некоторое материальное сопровождение (можно привести примеры из химчистки, продажи билетов и т. д.), главным здесь остается организация процесса в точке продажи услуги. Это объясняется тем, что продукты материального производства можно перемещать, хранить, накапливать, а услуги должны оказываться там и тогда, где и когда они актуальны. Поэтому если при планировании материального производства это графики отгрузки, то в сервисе – это параметры потока обслуживаемых потребителей.
Таким образом, главные параметры для планирования в сфере услуг – это актуальное время и актуальное место. К данным параметрам должны быть привязаны соответствующие мощности обслуживания, обеспечивающие ожидаемые потребителями качество и скорость обслуживания, что требует планирования такого параметра, как пропускная способность данной точки оказания услуги, в зависимости от контингента потребителей, их психологических и других особенностей, привычек и настроения.
6.9. Организация контрольных процессов по обеспечению требуемого качества продукции
Чтобы понять необходимость организации контрольных процессов на предприятии, рассмотрим несколько подходов к этому вопросу. Советский подход (кстати, весьма эффективный в своей основе) прослеживается в ГОСТ 16504–81 «Испытания и контроль качества продукции», который и по сей день действует на территории России и большей части стран СНГ. Этот стандарт определяет технический контроль как проверку соответствия объекта установленным техническим требованиям. В машиностроении он представляет собой совокупность контрольных операций, выполняемых на всех стадиях производства: от контроля качества поступающих на предприятие материалов, полуфабрикатов, комплектующих приборов и изделий до выпуска готовой продукции. Как известно из истории развития технического контроля, по мере усложнения продукции и технологии ее изготовления требования специальных компетенций для этого вида функций на предприятии становятся все более жесткими и специфичными.
Зарубежная практика подтверждает это. Разделяя технический контроль на верификацию, мониторинг и измерение продукции и процессов, соответствующие профессиональные организации (например, бюро «Веритас») предлагают услугу по верификации продукции и процессов на всех этапах жизненного цикла продукции на условиях аутсорсинга. При этом внутренние проверки предполагается оставлять за самой организацией, постоянно повышая их качество и концентрируя все большее внимание на предупреждении появления несоответствий, а не на их простой фиксации.
Собственно говоря, последние версии международных стандартов ISO серии 9000 основаны на таком же подходе. Смысл этого подхода заключается в профессионализации технического контроля (в зарубежной интерпретации – Product quality inspection – инспекции) и сосредоточении его функций на предупреждении возможностей появления несоответствий. Наличие и эффективное функционирование специальной службы – отдела технического контроля (ОТК) направлено на поддержание имиджа фирмы (как компонента бренда) и создание у потребителей уверенности в качестве и надежности продукции фирмы, что является базисом для устойчивого успеха и развития.
Вначале рассмотрим, что ОТК не должен делать. Очевидно, что ОТК не имеет права отвечать за качество продукции и процессов. Точно так же ОТК не должен отвечать за объем выпускаемой продукции и сроки ее изготовления, за длительность циклов и обеспечение рабочих мест материалами и полуфабрикатами.
Основной задачей отдела технического контроля на предприятии является обеспечение всех заинтересованных лиц достоверной, своевременной и объективной информацией о качестве продукции, состоянии оборудования и технологического процесса с целью предупреждения несоответствий и отклонений, которые могут привести к нарушениям требований конкретных потребителей, технических условий и стандартов.
Это означает, что суть организации работы ОТК по обеспечению требуемого качества продукции заключается в создании систем:
• сбора данных о состоянии процессов (и их компонентов) и продукции;
• переработки данных в информацию, простую и понятную для принятия решений;
• быстрой доставки информации соответствующим лицам для принятия решений;
• воздействия на соответствующие службы для предупреждения возможности появления несоответствий;
• совершенствования контроля и повышения его эффективности с точки зрения потребителей и бизнеса.
Каждая из систем – отдельная функциональная область, требующая расшифровки и соответствующего наполнения. Одна из главных проблем при этом – правильное определение зон ответственности и получение необходимых полномочий.
Исходя из основной задачи ОТК, можно выделить следующие производные (составляющие или частные) задачи.
1. В каждом новом изделии и новом технологическом процессе осуществлять разработку системы расположения точек контроля, методик технических измерений и мониторинга параметров процессов и изделий с внесением их в соответствующую документацию
2. В каждой точке контроля обеспечивать установленный документами объем контрольных операций с формированием на их основе непрерывного потока данных о качестве продукции, состоянии оборудования и технологического процесса.
3. Поддерживать непрерывную обработку данных о мониторинге и измерении процессов и продукции в установленных точках с целью предупреждения несоответствий и отклонений, которые могут привести к нарушениям требований конкретных потребителей, технических условий и стандартов.
4. В системе эффективного управления потоками создания ценностей организовывать мониторинг общего уровня изменчивости и уровня качества и выступать инициатором разработки программ повышения стабильности и управляемости процессами.
5. В системе постоянных улучшений отвечать за вопросы, связанные с улучшением систем технического контроля и снижением стоимости, не добавляющей ценности в общей ценовой структуре изделий.
Каждая из этих задач требует формирования определенных функций и компетенций в службе технического контроля и очень глубокой проработки с соответствующими службами факторов, влияющих на техническую составляющую качества продукции и услуг. Чтобы функции не пересекались и ответственность не размывалась, необходимо разделить зоны ответственности ОТК с другими подразделениями.
Так же, как и во всех подразделениях любого предприятия, в ОТК обязательно присутствует иерархия компетенций и ответственности. Нижний уровень непосредственно контактирует с материальными потоками, верхние – только с информационными, связанными с принятием решений.
Чтобы выделить зоны ответственности на нижнем иерархическом уровне ОТК, рассмотрим, что является объектом технического контроля. Исходя из предыдущей логики, это может быть продукция, являющаяся результатом процесса, или сам этот процесс.
При контроле продукции общепринятым подходом всегда был такой, при котором после обработки изделие подвергается межоперационному или окончательному контролю специально обученным работником службы ОТК. При таком подходе изделие изымается из производственного потока и возвращается в него только при подтверждении соответствия его параметров (тех, которые должны проверяться согласно технической документации). В этом случае зона ответственности ОТК ограничена точкой изъятия изделий из производственного потока и точкой возврата их в поток. При этом суть ответственности состоит в том, что контролер отвечает перед производством:
• за правильность применения утвержденной методики контроля;
• достоверность полученных данных;
• своевременность их оформления и передачи лицам, принимающим решение;
• сроки проведения контроля;
• правильность изолирования выявленной несоответствующей продукции;
• точность соблюдения процедур, связанных с коррекцией и корректирующими действиями.
При контроле процессов объектами для ОТК становятся технологические процессы, логистические процессы (транспортирования, хранения), процессы технического обслуживания и ремонта. Суть ответственности ОТК при работе с процессами заключается в контроле правильности их настройки исходя из требований, заложенных в документацию на них. Очень важной зоной ответственности ОТК по отношению к процессам является мониторинг изменчивости процессов, контроль статистики отклонений и их тенденций, статистический анализ процессов и инициирование предупреждающих действий в соответствии с п. 6.4.1 стандарта ISO 9001: 2008.
Контроль качества документации при ее разработке и использовании не является предметом ответственности ОТК, за исключением тех случаев, когда определенное требование, например о комплектности или актуальности, присутствует в документации на соответствующий процесс.
Как видно из изложенного, сфера ответственности ОТК всегда ограничивается именно технологией и процедурами контроля и ни в коем случае не распространяется на качество проверяемых объектов. Ответственность за качество проверяемых объектов несут лица, обрабатывающие изделие или выполняющие процесс, но не лицо, контролирующее их технические характеристики. Более того, наличие на объекте операционных средств мониторинга и измерения текущего состояния объектов является обязательным и предусмотрено требованиями п. 7.5.1 стандарта ISO 9001: 2008.
Внимание! Это не конец книги.
Если начало книги вам понравилось, то полную версию можно приобрести у нашего партнёра - распространителя легального контента. Поддержите автора!Правообладателям!
Данное произведение размещено по согласованию с ООО "ЛитРес" (20% исходного текста). Если размещение книги нарушает чьи-либо права, то сообщите об этом.Читателям!
Оплатили, но не знаете что делать дальше?