Текст книги "Toyota. Путь к совершенству"
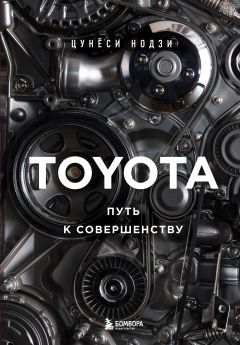
Автор книги: Цунёси Нодзи
Жанр: О бизнесе популярно, Бизнес-Книги
Возрастные ограничения: +12
сообщить о неприемлемом содержимом
Текущая страница: 5 (всего у книги 19 страниц) [доступный отрывок для чтения: 6 страниц]
Тайити Оно после войны
После войны, когда Киитиро снова вернулся к разработке легкового автомобиля, Тайити Оно стал начальником сборочного цеха на заводе в Коромо. Сборочный цех представлял собой целое предприятие, где собирают автомобиль из деталей, произведённых моторным цехом, механическим цехом, а также различными поставщиками запчастей с окрестных территорий. Сборочный цех – самый важный и сложноорганизованный на автомобилестроительном заводе. Однако детали в сборочных цехах не производят. Их дефицит особенно чувствовался во время войны. Самое большее, что смог сделать Оно в то время – это стандартизировать операционные процессы.
В обязанности Оно входило обучение людей стандартным операционным процессам и ознакомление с названиями деталей и инструментов, дабы не допустить путаницы в цеху.
Даже по окончании войны к полноценному производству ещё не перешли. Вначале нужно было привезти и установить станки, эвакуированные в различные части страны. Когда станки были проверены, линии запущены, а детали доставлены, приходило распоряжение на сборку грузовиков.
Оно предпочитал работать рядом с линией, хотя в его собственном кабинете тоже был стол. Его рост составлял 180 см. Это довольно много для человека тех времён, так что стоило ему появиться в цеху или других помещениях завода, люди сразу его замечали.
Его прическа всегда была волосок к волоску, на чистой отглаженной спецовке ни одной морщинки. Это был аккуратист по натуре. Единственное, что бросалось в глаза – это усы. С маленькими усиками прямо под носом, он широким шагом пересекал пространство цеха. Рабочие, которые его боялись, завистливые коллеги и враждебно настроенное начальство за глаза называли его «усы» или «старик с усами».
Однажды, когда Оно был на линии, работа остановилась. Он обратился к рабочему и услышал ответ: «У нас нет акселератора и рулевого колеса».
– Это в третьем цеху[7]7
Третий цех – это третий механический цех. На заводе в Коромо в первом цеху собирали двигатели, во втором шестерни, а третий отвечал за работы, связанные с шасси, изготавливая передние и задние мосты.
[Закрыть], – подумал Оно.
Оно взял с собой только подмастерьев и отправился в цех № 3. Игнорируя начальника этого цеха, Оно сам начал делать акселераторы и рулевые колёса, попутно обучая этому подмастерьев.
Изготовив необходимое количество деталей, Оно с подмастерьями вернулся в сборочный цех и установил их на кузов автомобиля.
С точки зрения рабочих в третьем цеху, это было превышением полномочий, они наверняка сочли Оно наглым и дерзким. Тем не менее, как только у Оно кончались детали, он шёл в механический цех и изготавливал их. Он никогда не переступал порог первого цеха, где производились двигатели, но во второй и третий цеха заходил с невозмутимым лицом, как будто к себе на работу.
В производственной модели Toyota есть принцип – вторая линия забирает детали у первой, но изначально это просто было удобнее, потому что детали не поступали вовремя. Эта ситуация так повлияла на Оно, что привела к закреплению процесса в будущей системе.
Оно брал своих людей и отправлялся работать на первую линию.
– Оно, ты опять пришёл? – спрашивал бригадир третьего цеха.
– Без этой детали мы не можем собрать машину, – отвечал ему Оно и проводил утро за изготовлением запчастей, а во второй половине дня шёл собирать грузовик к себе в цех.
В 1947 году Оно назначили начальником второго и третьего машинных цехов (название должности изменили с заведующего). Его начальство наверняка слышало, как Оно жаловался на медлительность машинных цехов и подумало: «Если поставить Оно главным, может, он немного успокоится?»
Сборочный цех – это место, где различные детали соединяются и результат по форме начинает напоминать автомобиль. Рабочие стоят у конвейерной ленты. Они крепят электропроводку, рулевое колесо, сиденья, двери. С помощью отвёртки прикручивают гайки и затягивают болты. Всё это, разумеется, делается стоя.
С другой стороны, машинные цеха, где режут и гнут металл. Поскольку в этих цехах выполнялось много мелкой работы, рядом с линией стояли стулья для рабочих. Поэтому были и сидячие рабочие места. Когда Оно поставили во главе машинных цехов, первым делом он заставил всех работать стоя.
– Послушайте меня, если вы работаете сидя, то в пояснице возникает зажим. Если вы каждый день будете работать в таком положении, у вас обязательно заболят поясница и шея. Работать нужно стоя. Крестьянин, зеленщик, рыботорговец – все работают стоя. Так лучше для вашего организма.
Но те, кто работал сидя, вставать совсем не хотели.
– Заставлять работать стоя – усложнять нам задачу.
– Мы и сидя прекрасно справлялись. Почему теперь мы должны стоять?
Среди недовольных были и члены профсоюза. Пришлось Оно жёстко их осадить.
– Во время войны я работал на прядильно-ткацком производстве. Там женщины-ткачихи каждый день стоя обслуживали в одиночку 20 станков. Так почему здоровые мужики отказываются подняться для работы? Я повторюсь, сидячая работа вредит пояснице и шее. Естественное для выполнения работы положение тела – стоя.
В этом вопросе Оно не отступил ни на шаг. Это был кайдзен, направленный не на эффективность труда, а на здоровье рабочих. Лишь одно из многих улучшений, которыми Оно занимался всю свою жизнь. После того, как работники освоились, Оно продолжил потихоньку внедрять нововведения. Сразу после войны он потратил на это несколько лет. В то же время Toyota переживала управленческий кризис, из-за трудовых споров компания оказалась на грани банкротства. Однако даже в разгар забастовок Оно повторял своим сотрудникам: «Давайте работать вдумчиво». Порой протестующие блокировали цех и выставляли всех на улицу. Даже в этом случае он ловил собравшихся под красным флагом рабочих и пытался убедить: «Если компания рухнет, всему конец».
Воспитание многостаночников
Следующим шагом стало внедрение многостаночного управления. По сути, именно с этого улучшения и началась производственная модель Toyota.
Оно так объяснил идею своему начальству:
– Представьте, что токарь работает не только на токарном, а ещё и на фрезеровочном станке. А когда появляется возможность, то можно попросить его также поработать на сверлильном станке. На это уйдёт время, но я непременно смогу их убедить.
Сверлильные станки состоят из диска и сверла. Металлическая пластина устанавливается на диск и фиксируется на месте. Вращающийся бур спускается сверху и сверлит отверстия.
Токарный станок похож на повёрнутый на бок сверлильный. Обрабатываемая металлическая деталь зажимается с обеих сторон и фиксируется, а затем начинает вращаться. Резец выходит сбоку и соскабливает вращающийся металл.
Фрезерный станок удаляет обломки с металла и выравнивает поверхность. Все три типа станков издают высокочастотный скрип, когда шлифуют металл о металл. Шум в машинном цехе негромкий, но раздражающий.
До прихода Оно мастера в механическом цехе относились к каждому станку как к своему собственному. Они так гордились своим умением, что не желали, чтобы кто-либо ещё прикасался к их машинам. Токарь работал только на токарном станке, фрезеровщик – только на фрезерном.
– Надо что-то делать, – подумал Оно.
Войдя в цех, он нахмурился. Сразу было видно, кто из мастеров работает, а кто страдает от избытка свободного времени. Рядом с увлечённым работой специалистом стоит мужчина с сигаретой в зубах, неспешно натачивающий резец. Вместо командной работы каждый был занят чем-то своим.
Обратим внимание на обстоятельства. Если бы не задержки с поставками сырья, все специалисты были бы загружены работой. Но нередко случалось так, что заготовки для токарного станка поступили, а стальных листов для сверлильного нет. Если работы нет, ничего не остаётся, как смазывать станки маслом и полировать их тряпкой.
– Эй, не окажешь услугу?
Оно подошёл к мужчине, стоявшему с сигаретой в зубах у токарного станка. Это был опытный и искусный мастер, и Оно подумал, что если убедит его, то другие тоже согласятся работать на нескольких станках. В то время на заводе были люди, пришедшие ещё до войны. Они не планировали трудиться на Toyota всю жизнь, это были специалисты, привыкшие менять место работы. Оно ничего не оставалось, как говорить с ним мягко.
– Что бы ты сказал, если бы тебе предложили научиться работать не только на токарном, но ещё и на сверлильном и фрезерном станках?
Мужчина ответил:
– На сверлильном? С этой машиной для сверления дырок и девчонка управится. Токарная работа – это работа для мастера, требующая ремесла. Однажды поработав на токарном станке, человек уже не встанет за сверлильный.
– Так ли это? Не знаю, не знаю… Вот ты упомянул девчонок. В прядильном деле одна девчонка отвечает за 20 станков. Даже жаль, что ты, мужчина и такой опытный мастер, прилип к одному единственному.
На это мятежному мастеру было нечего ответить. Оно специально выбирал слова, которые заденут гордость собеседника.
– Ещё чего, я тоже могу! – но к сверлильному станку шага не сделал.
– Что, сложная машина? – спросил Оно, глядя мужчине в глаза.
– Разберёмся, – сказал мастер, надувшись, и нехотя начал разбираться в станке. На уговоры ушло полдня.
Оно был начальником. У него было право распоряжаться в цеху. Если он скажет «надо», то рано или поздно рабочие освоят несколько станков. Однако есть разница между работой, которую делают неохотно, и работой, которая горит у мастера в руках. Исходя из этого принципа, сначала нужно было убедить авторитетных мастеров, а затем потихоньку увеличивать число тех, кто управляется с двумя и более станками. Не просто бездумно сказать людям: «Делай!», а собственными руками вырастить нужных специалистов.
Приходит время, когда одним из самых важных навыков станет умение выполнять разнообразную работу.
Позднее Оно назвал это воспитанием многопрофильных работников.
– Возьмём, к примеру, сварку. У человека есть лицензия, есть навык. Но если он будет заниматься только сваркой, стране придётся туго. Сейчас, если человек в состоянии получить лицензию сварщика, он также может выполнять другую работу, если немного подучится. Но он думает: «Я сварщик, значит, буду заниматься только сваркой». Вскоре люди, которые умеют только что-то одно и только этим и занимаются, не смогут работать на малых и средних предприятиях страны. Приходит время, когда одним из самых важных навыков станет умение выполнять разнообразную работу.
Работая над систематизацией производственной системы Toyota, он скажет, что суть работы состоит не в разделении труда на ручной и машинный, а в умении объединить их в одну систему.
– Возьмём подачу деталей на станок. Обработка занимает 20 или 30 секунд. Человек, закончив подачу, мог бы вернуться к сварке детали, если до этого он занимался сваркой и поработать эти 20–30 секунд. Когда станок закончит обработку, человек поставит следующую деталь. Пока работает машина, человек тоже выполняет свою работу. Мы должны подумать, как уложить человеческий труд в 8-часовой рабочий день.
Если конца всё равно не миновать, надо хотя бы попробовать.
Однако такая предупредительность снова встретила критику у части рабочих. Но недовольные голоса звучали не только в цехах – некоторые руководители тоже осуждали подход Оно: «Он только и делает, что провоцирует разногласия в цеху».
Единственным, с кем Оно мог посоветоваться, был Эйдзи, ведь Киитиро – президент компании, просто так к нему не обратиться. Только под покровительством Эйдзи, тоже проводившего преобразования, Оно смог провести свои реформы.
С тех пор как Оно перевели в механический цех, он занимался кайдзеном. Ему удавалось проводить одно улучшение за другим, поскольку в то время производственные объёмы Toyota были небольшими и в цеху было время подумать. Это было ещё до моторизации, и, так как запчасти не поступали, делать было нечего – сотрудникам приходилось выполнять приказы Оно.
Оно было слегка за тридцать, его окружали опытные мастера, старше по возрасту. В таком обществе оставалось держать спину прямо и давать очевидные указания. Только дома становилось ясно, как он устает.
Своей жене Ёсихисе он всегда говорил одно и то же: «Нужно ещё немного времени».
Перед сном он занимался тем, что приводил в порядок домашние дела.
– Я хочу реализовать то, о чём говорил Киитиро, – «точно в срок». Но для начала надо добиться он производителей комплектующих их своевременной поставки, а это невозможно. Если бы мы решили перейти на эту модель, мы могли бы это сделать немедленно. Конечно, транспортные расходы возрастут. А рост расходов мы себе позволить не можем, значит, не сейчас. Но что мы можем сделать? Каков следующий шаг для «точно в срок»?
Оно не общался с Киитиро напрямую и не мог слышать его слов, но переданное Эйдзи породило в нём бурю, он разделил это ощущение приближающегося кризиса и сразу же предложил меры по реформированию. В этой погружённости была и доля зацикленности.
– Стоит только появиться американскому автопроизводителю, и нам конец.
Не только Киитиро и Оно так думали. После капитуляции большинство японцев разделяли пораженческие настроения. Это была общая тенденция.
– Если конца всё равно не миновать, надо хотя бы попробовать.
Оно с самого начала работал в состоянии отчаяния.
Не смей убегать
Оно любил свою работу, при этом он был человеком, который инициировал и систематизировал свою работу, но она не была всей его жизнью. У него был восьмой дан по стрельбе из японского лука, а вскоре после того, как занялся гольфом, получил сингл-гандикап. Также нередко просиживал ночь за маджонгом[8]8
Маджоˊнг, или мацзян, – китайская азартная игра с использованием игральных костей для четырёх игроков. – Прим. ред.
[Закрыть].
Он был немногословным человеком.
Когда Оно видел, что что-то идёт не так, то сначала наблюдал. И приглашал инспектора и бригадира понаблюдать вместе. Не давал прямых указаний: «Делайте так, а не так». Он ждал, пока инспектор или бригадир сами предложат способ решения проблемы.
Один подчинённый рассказал, что никогда не забудет громовой возглас «Не смей убегать» из уст Оно.
– Это было очень страшно. Я собирался сходить за инструментом, чтобы исправить неполадку на линии, когда Папаша рявкнул: «Не смей убегать». Мои ноги буквально вросли в землю. Он имел в виду, что проблему надо устранить, но не лёгким способом, который я выбрал. Поэтому он меня отругал. Он учил думать и воспитывал из нас думающих людей.
Глава 4
Первые реформы
Превзойти Форда
Автомобили, произведённые Toyota сразу после войны, были грузовиками типа SB, а не Toyopets (легковой автомобиль) типа SA. Хотя на заводе в Коромо была конвейерная линия, использовалась она не очень активно.
С запчастями тоже было не всё гладко, и, самое главное, не было налаженной системы производства. На каждом заводе руководитель предприятия брал за образец систему Форда и добивался эффективности только в рамках своего участка.
Однако из-за того что производство в цехах не было органически связано между собой, например, машинный цех мог произвести больше акселераторов, чем планировалось, а сборочный цех в результате не справлялся с этим перепроизводством, возникала потребность в пространстве для хранения между цехами. А для управления этим пространством нужны были люди.
Оно чувствовал опасность постоянного увеличения запасов хранения. Он сильно сомневался, что Toyota следует продолжать следовать этой системе в её неизменном виде.
– Интересно, как они в США решают проблему постоянно растущих промежуточных запасов?
Если в начале месяца установить целевое количество и производить в соответствии с ним, деталей всё равно будет больше, чем нужно.
Оно постоянно думал о том, как добиться производства «точно в срок». Для этого, прежде всего, необходимо было ликвидировать саму систему промежуточных запасов. Он решил ещё раз досконально изучить систему Ford.
Система Ford – это метод массового производства, но малой серийности. Чем меньше разнообразие, тем лучше. Один цвет, одна форма кузова – и поточное производство с помощью ленточного конвейера. Заводы по сборке автомобилей не только в США, но и в других развитых странах считали следование этой системе само собой разумеющимся.
В системе Ford выполняемая работа разбивается на ключевые этапы. Затем для каждого отдельного этапа определяется норма времени выполнения.
При определении стандарта времени Генри Форд сам с секундомером в руках замерял, за какой отрезок квалифицированный рабочий сможет выполнить задание.
Оно был не согласен с Фордом в использовании «квалифицированных рабочих» в качестве стандарта для замера времени, а производственная система Toyota вообще не использовала такое понятие, как «квалифицированный рабочий».
– Если брать за стандарт время квалифицированного рабочего, придётся ускорять конвейер, – говорил он. – Это нехорошо. Стандартизированная операция должна выполняться в том темпе, который может поддерживать каждый.
Согласно производственной системе Toyota стандарт времени выполнения операции определяется общим объёмом производства, но со скоростью, которую могут поддерживать даже рабочие-стажёры.
Однако Форд планировал выпускать всего одну модель автомобиля – Ford T.
Прикреплённые к линии рабочие должны были выполнять простые повторяющиеся операции со скоростью конвейера. Для этого не требовалась высокая квалификация. Неквалифицированные рабочие тоже могли собирать автомобили.
Настало время поточного производства. Если раньше на сборку одного автомобиля уходило 14 часов, то после перехода на систему Ford сборка стала занимать 1 час 33 минуты.
– Если производить товар в большом количестве, он становится дешевле.
Такова основная идея системы Ford. Чем выше скорость конвейерной ленты, тем ниже стоимость единицы продукции. Руководителям производства она казалась очень привлекательной.
Разница между подходом Генри Форда и подходом Киитиро и Оно заключалась в наличии или отсутствии у них опыта работы на производстве. Форд был простым управленцем. Тем временем Киитиро и Оно всё время находились в цеху.
Система Ford способствовала повышению эффективности производственных предприятий, но Киитиро и Оно сомневались.
Киитиро считал, что система массового производства всего одной модели не подходит японскому авторынку, а Оно считал, что существуют иные способы снизить затраты в массовом производстве.
Изучив систему Ford, Оно выдвинул свою гипотезу:
– В США можно производить большие объёмы односерийной продукции. Но в Японии производят в принципе небольшие объёмы. Если переносить систему Ford в неизменном виде, она не будет работать.
И Киитиро, и Оно выступали за введение конвейерных лент. Это было намного эффективнее, чем толкать шасси на тележках по заводскому цеху. Они также в целом не возражали против разделения работы на этапы, но были не согласны с упрощением всех операций до уровня примитивного физического труда. Оба понимали, что для повышения производительности нужны другие идеи.
Разница между подходом Генри Форда и подходом Киитиро и Оно заключалась в наличии или отсутствии у них опыта работы на производстве. Форд был простым управленцем. Тем временем Киитиро и Оно всё время находились в цеху. Производственная система Toyota была разработана на основе реального положения дел в цеху и использовала это знание.
В США и Японии действует разная система оплаты труда. Американская обычно основана на почасовой ставке, работник получает фиксированный размер оплаты за час своей работы. Предположим, что есть задача по установке шин на автомобили. Если рабочим приходится ставить большое количество шин, то стоимость установки одной шины будет ниже.
С другой стороны, если линия останавливается на 30 минут, работник всё равно получит зарплату за это время. Тогда стоимость установки одной шины вырастет в два раза. Поэтому в США разгоняют конвейер и не допускают его остановок.
В Японии иначе: зарплата привязана к конкретному человеку. Если человек с высокой зарплатой будет ставить шины, стоимость монтажа окажется выше, чем если той же работой займётся человек с низкой зарплатой.
Оно говорил:
– В США только что собранная машина сразу продаётся, однако в Японии, пережившей военное поражение, автомобили не покупают направо и налево.
Если мы продолжим производить автомобили исходя из утверждения, что чем больше мы их делаем, тем дешевле они становятся, скоро придётся строить склад для хранения этих автомобилей. Складское хранение стоит денег, а долго стоящая на хранении продукция неизменно превращается в неликвид.
Американские производители машин в целом обладают в сотни раз большей капитализацией, чем мы, и располагают большими производственными мощностями. Также у них новейшее оборудование. Toyota, которая летит только при попутном ветре, никак не может использовать те же методы производства, что и «большая тройка». Производственную систему надо адаптировать для малых и средних предприятий.
Когда Оно внедрял производственную систему Toyota на заводах и в компаниях-партнёрах, он решил, что объяснять должны только люди, непосредственно знакомые с системой. Если выпускать только письменное руководство, то люди будут неправильно интерпретировать текст.
Оглядываясь назад, можно сказать, что и Генри Форд, и Киитиро давали советы по повышению эффективности и проверяли опасные участки. В грохоте цехов их посещали новые идеи. Вероятно, визг металла и шум конвейерных лент стимулировали их ум лучше, чем сидение над чертежами в кабинете.
Правообладателям!
Данное произведение размещено по согласованию с ООО "ЛитРес" (20% исходного текста). Если размещение книги нарушает чьи-либо права, то сообщите об этом.Читателям!
Оплатили, но не знаете что делать дальше?