Текст книги "Профессия инженер"
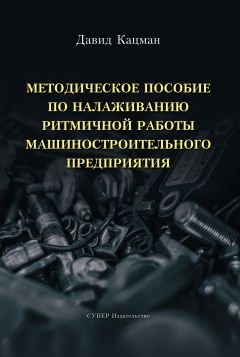
Автор книги: Давид Кацман
Жанр: Техническая литература, Наука и Образование
Возрастные ограничения: +12
сообщить о неприемлемом содержимом
Текущая страница: 2 (всего у книги 10 страниц) [доступный отрывок для чтения: 3 страниц]
Моральный кодекс ремонтника
(опыт ВАЗа)
– Каждый ремонтник обязан руководствоваться принципами изложенными ниже:
– Трудиться в полную меру своих способностей, искать, дерзать. внедрять все новое, передовое в свой труд.
– Приобретать знания и опыт систематически, не стыдиться обращаться за советом к товарищам, работоспособность оборудования выше всего. предупреждение аварий – долг каждого ремонтника, настоящее и будущее принадлежит профилактике;
– Знания, которые не пополняются, убывают с каждым днем, научился сам, научи товарища;
– Анализировать каждую поломку агрегата, точное определение неисправности – половина качества ремонта;
– Бороться за жизнь оборудования не щадя своих сил и времени (сломанный станок – мертвый металл, работающий, – гимн труду ремонтника).
– Критика – первое лекарство, а не яд; если не будем боятся говорить друг другу гневную и тяжелую правду напрямик, то мы научимся побеждать все и всякие трудности.
– Ничто так не научит ремонтника, как признание собственной ошибки, – это одно из главных средств самовоспитания и самоусовершенствования;
– Долголетие оборудования – в руках ремонтника. беречь его – честь ремонтника.
1.3. Организация надежной работы оснастки, режущего, мерительного и вспомогательного инструментов.
а) Приспособления.
Обрабатываемая деталь устанавливается в приспособление и крепится в нем; при этом, каждая последующая деталь должна устанавливаться строго в определенное положение, надежно базироваться.
Неправильная установка и базирование детали, ненадежное крепление, неправильное положение приспособления относительно режущего инструмента приводит к забракованию детали, нарушению нормальной работы режущего инструмента, его поломке.
Следовательно, для нормального протекания процесса резания, обеспечения качественной обработки детали необходимо соблюдать следующие условия:
1. точную установку и выставку приспособления на станке относительно инструментального шпинделя.
2. надежное крепление приспособления на столе станка;
3. качественное состояние опорных базовых поверхностей приспособления, обеспечивающих правильную установку детали;
4. надежное крепление детали в приспособлении (при этом не должна наблюдаться деформация детали от усилий зажима, – так как при отжиме будет нарушена геометрия обработанной поверхности).
Современные приспособления, оснащенные пневматическими, гидравлическими, электромеханическими, электрическими (магнитными) приводами представляют собой сложные устройства.
Работа их в соответствии с заданными требованиями ограничена по времени в определенных пределах.
Рассмотрим основные элементы приспособлений, которые подвергаются изменениям в процессе эксплуатации, приводящим к разрегулированию процесса в качественном отношении.
Опорная поверхность приспособления обычно выдерживает весь срок работы без существенных нарушений геометрии, влияющих на точность обработки детали; надежность крепления приспособления к столу станка, особенно в серийном или массовом производстве, обычно также гарантируется.
Наиболее уязвимыми местами приспособлений являются базовые поверхности (опорные планки, призмы, направляющие втулки и т. д.) и детали привода, в том числе поверхности зажимных элементов.
Указанные поверхности подвержены износу и требуют тщательного внимания и ухода.
В конструкции приспособлений предусмотрена возможность восстановления или замены базовых деталей и деталей привода, однако, нет четко разработанных рекомендаций (нормативов), указывающих срок эксплуатации данных деталей, без нарушения геометрии рабочих поверхностей от износа, здесь просматривается 2 пути: один, – теоретические исследования и подготовка рекомендаций на базе интенсивно развивающейся науки – триботехники, второй, – практический опыт, определение норм расхода всех видов оснастки на 1000 выпускаемых изделий, введение централизованной системы планово-предупредительного ремонта, которая разработана не на всех предприятиях и очень медленно внедряется в жизнь.
Поэтому еще очень часты остановки производства, забракование деталей по вине вышедших из строя отдельных элементов приспособлений.
Очевидно, что уже при проектировании приспособления, в его паспорте, конструктор обязан указать детали и элементы подлежащие периодической замене.
При этом срок службы приспособления должен устанавливаться с учетом проведения планово – предупредительных ремонтов.
К сожалению, еще часты случаи, когда выход из строя того или иного элемента приспособления приводит к заказу его дублера (налицо явно неоправданное расточительство, необоснованная загрузка мощностей инструментального цеха).
Для того, чтобы производить ППР приспособлений в цехах основного производства, необходимо иметь хорошо организованную техническую службу, которая создается на базе цехового технологического бюро и механического участка по ремонту оснастки.
В последнее время интерес вызывает служба ОАЭСП (отдел анализа эффективности средств производства) централизованная в целом по заводу (опыт ВАЗа).
Бюро технического обеспечения производства (БТО), будем так называть цеховое технологическое бюро, организовывает и проводит работу по ППР оснастки (указанная работа является основной функциональной обязанностью БТО, о других обязанностях будет сказано ниже).
Порядок проведения ППР следующий: за каждым технологом закрепляется производственный участок цеха, он выполняет работу по паспортизации оснастки, выявляет ее наличие в цехе и кладовой оснастки, техническое состояние.
Далее разрабатывается график ППР оснастки, подбирается или разрабатывается техдокументация на изготовление запчастей, быстроизнашиваемых элементов на механическом участке цеха (инструментальный цех привлекается для координатных работ).
Строго контролируется выполнение графика ремонта оснастки и отладки последней на станках с целью обеспечения качества выпускаемой продукции.
При напряженном производственном ритме в массовом и крупно– серийном производствах, ремонт и отладку приспособлений необходимо проводить в субботние и воскресные дни, что дает возможность полностью исключить простои оборудования.
С этой целью в штаты бригады по ремонту остнастки вводят квалифицированных наладчиков, способных наладить оборудование в указанные нерабочие дни.
Сложная оснастка (например. прессформы), контрольный инструмент ремонтируется централизованно, технологи БТО разрабатывают задание инструментальному цеху, которое по согласованию с инструментальным отделом вносится в план производства на соответствующий месяц или квартал.
Итак, из сказанного выше вытекает, что организационная структура БТО цеха состоит из технологического бюро, мех. участка, бригады слесарей и наладчиков по ремонту и отладке приспособлений, а также кладовой оснастки.
В штатах БТО должен быть работник ОТК, для осуществления контроля, как вновь прибывшей в цех, так и отремонтированной оснастки.
Такая структура позволяет, кроме профилактики, оперативно проводить работу по устранению аварийных ситуаций, непредвиденных выходах из строя оснастки и инструмента.
В этих случаях технолог срочно оформляет эскизы, чертежи на детали, подлежащие замене; в указанный нач. БТО срок производится изготовление запчастей и ремонт вышедшей из строя оснастки.
В таких ситуациях велика роль механического участка, поэтому он должен быть оснащен всем необходимым набором оборудования, включая, если это возможно и координатно – расточной станок.
Таким образом, на базе БТО в производственных цехах предприятий создается техническая служба, способная оперативно и грамотно решать вопросы технической эксплуатации оснастки, что является одним из главных факторов ритмичной работы и обеспечения высокого качества выпускаемой продукции.
Однако, ППР оснастки только одна из функций БТО, их обязанности и права значительно шире.
Это, прежде всего, работа по внедрению новых технологических процессов, мероприятий оргтехплана и новой техники, проведение работ по контролю соблюдения технологических процессов на базе разработанных на заводе СТП, выявление и устранение причин брака, контроль и обеспечение качественной работы режущего инструмента.
Подробно о работе цеховых технологических бюро, о богатом, но забытом опыте, будет подробно рассказано в главе «Поклонимся и поучимся»
б) Режущий инструмент.
На последнем надо остановиться подробнее; но прежде, чем говорить о режущем инструменте, поговорим о вспомогательном.
Вспомогательный инструмент (оправки, переходные втулки, державки, подкладки и т. д.) служат для правильной установки, направления и крепления режущего инструмента.
Все, что говорилось раннее о приспособлениях, имеет прямое отношение и к вспомогательному инструменту, только вспомогательный инструмент чаще подлежит контролю и замене.
От качества изготовления вспомогательного инструмента, его конструкции зависит нормальная работоспособность режущего инструмента.
Например, плавающие патроны для инструмента типа зенкеров и разверток или патроны с ограничением крутящего момента для нарезания резьбы метчиком, – в первом случае патроны обеспечивают направление инструмента и качество обработки, во – втором – сохранность метчика при возникновении усилий выше допустимого.
Из всего сказанного ясно, что значение вспомогательного инструмента в работе режущего огромно, следовательно, нельзя недооценивать всей важности и необходимости организации работ в цехе по его технически грамотной эксплуатации.
Как известно, режущий инструмент состоит из 3-х основных частей: режущей, переходной и крепежной.
При этом погрешности установки и крепления инструмента относительно обрабатываемых поверхностей, биение режущих кромок такого инструмента, как червячные фрезы, долбяки, торцевые фрезы и т. д. приводит к их повышенному износу и понижает стойкость работы инструмента.
Если учесть, что стоимость указанного инструмента довольно высока, то станет ясно, что экономически обоснованное использование режущего инструмента находится в прямой зависимости от конструкции, правильной наладки и качества работы вспомогательного инструмента.
Пример, – характер притупления червячной фрезы таков: зубья имеющие наименьший износ лежат с противоположной стороны зубьев имеющих максимальный износ.
Если оправка имеет второй шпоночный паз и фрезу можно переустановить не меняя положения оправки, то практически стойкость фрезы от переточки до переточки увеличивается в 2 раза. (по данным работ к.т. н М. Подгаецкого).
Отсюда вывод: изготовление вспомогательного инструмента, контроль его качества, своевременная замена, – важная задача БТО и прямо направлена на поддержание должного уровня качества выпускаемой продукции, а также экономически оправданную эксплуатацию режущего инструмента
Далее, остановимся подробно на режущем инструменте.
1, Режущий инструмент устанавливается и крепится на инструментальном шпинделе непосредственно или с помощью вспомогательного инструмента, о котором говорилось раннее.
От состояния инструмента (имеется ввиду правильный выбор конструкции, качество изготовления, заточки режущих кромок, правильность установки и выставки инструмента относительно обрабатываемых поверхностей) зависит его работоспособность и нормативная стойкость.
Два слова о переходной части режущего инструмента.
Конструктивно переходная часть должна задаваться таким образом, чтобы не уменьшать жесткости инструмента и обеспечивать оптимальные условия его эксплуатации в заданной наладке.
Рабочая часть режущего инструмента имеет режущее лезвие, конструктивно оно оформляется различно в зависимости от вида инструмента.
Условия рациональной эксплуатации режущего инструмента:
1. Выборочный входной контроль режущего инструмента поступающего в инструментальную кладовую; проверка стойкостных качеств согласно требований чертежа.
2. Налаженная система учета режущего инструмента, выдачи его на рабочие места (штука за штуку, талоны), весьма эффективен активный способ питания рабочих мест инструментальными средствами.
3. Обеспечение 100 % централизованной заточки и принудительной замены определенной категории сложного режущего инструмента, а также инструмента на финишных операциях.
Контроль качества перетачиваемого инструмента
4. Выбор оптимальных режимов резания, применение наиболее эффективных, с точки зрения стойкости инструмента, смазочно-охлаждающих жидкостей, спец. очистка их от стружки и грязи (фильтрация), отвод отходов резания и др.
5. Постоянная работа по поддержанию оптимальной стойкости режущего инструмента, исходя из изменяющихся условий действующего производства. Совершенствование конструкции инструментов, повышение их долговечности и стойкости на базе проведения научно-исследовательских работ, использования передового опыта.
Режущий инструмент – это орудие производства и поэтому невозможно добиться качественной, отлаженной во всех сферах, экономически целесообразной производственной деятельности, без создания эффективной системы эксплуатации и постоянного совершенствования режущего инструмента.
Для проведения этой работы необходимо иметь централизованные, в пределах завода, инструментальные службы, опирающиеся на квалифицированные кадры и оснащенные современным оборудованием технические лаборатории и инструментальные цеха.
Характерен в этом плане опыт ЧТЗ по организации цеха эксплуатации и восстановления инструмента, куда вошли заточные отделения цехов (в пределах корпусов).
в) Мерительный инструмент и контрольные приспособления обеспечивают контроль качественной стороны производства.
От простоты конструкции, удобства в эксплуатации, надежности и долговечности мерительного инструмента зависит объективный контроль качества выполняемой операции.
Большое распространение получили в настоящее время контрольные приборы, дающие возможность контролировать ход производства без остановки последнего (активный контроль), комплексные электронные приборы и контрольные сортировочные автоматы.
С повышением требований к объекту производства, значительно вырастает роль метрологической службы, в цехах организовываются контрольные, изолированные от основного производства посты (термоконстантные помещения), где созданы все условия для объективного контроля истинных геометрических параметров изготавливаемых деталей.
Вся работа, связанная с организацией разработки, внедрением в производство, контролем за правильной эксплуатацией всего комплекса измерительных средств, а также связь с проектными организациями, заказ приборов на стороне, – должна вестись метрологической службой предприятия.
В целях обеспечения бездефектной работы приборов должна быть реализована система мер по их своевременному ремонту, анализу надежности в процессе эксплуатации.
Метрологическая служба тесно связана с технологической службой предприятия и согласовывает применяемые технологами методы и конструкции мерительных инструментов и приборов при разработке новых и модернизации действующих технологических процессов.
Большое значение имеет паспортизация контрольных приборов с учетом определения точностных характеристик, предельных погрешностей замера.
Все сказанное создает объективную техническую базу для организации бесперебойной работы мерительного инструмента, обеспечения качественных параметров изготавливаемых изделий.
1.4 Основные требования предъявляемые к заготовкам, деталям в серийном и массовом производствах.
Мы рассмотрели оборудование, приспособления, режущий и мерительный инструмент; обратимся теперь непосредственно к обрабатываемой детали.
Деталь поступает на операцию предварительно подготовленная под обработку; уже в стадии получения заготовки предусматриваются черновые базовые поверхности, на которые происходит установка детали на первой операции.
Качеству базовых поверхностей и соответствию припусков под последующую обработку, термической обработке уделяется самое серьезное внимание с целью улучшения обрабатываемости, обеспечения нормальных условий механической обработки.
Заготовки (отливки, поковки) проходят операции удаления литников, прибылей, очистку поверхностей.
Зачистку линий разъема и даже механическую обработку базовых поверхностей часто производят в литейном или заготовительном цехах, особенно это имеет место, если заготовки в последующем обрабатываются на автоматическом или полуавтоматическом оборудовании.
На каждой операции механической обработки деталь необходимо установить в приспособление; обычно эта операция выполняется вручную, реже механическим путем на станках и автоматических линиях, оснащенных загрузочными устройствами.
Базовые поверхности приспособления перед установкой детали подлежат очистке от стружки; производится очистка смыванием интенсивной струей эмульсии (опыт ВАЗа), вручную с помощью щетки (обдувка воздухом не рекомендуется, исходя из условий техники безопасности и, обеспечения гарантийного срока работы оборудования).
Выполнение первых операций представляет особую, подчас наиболее сложную часть технологического процесса. Связано это с тем, что обработка производится от черных баз со снятием значительных припусков, которые имеют место ввиду того, что, как правило, в настоящее время мы еще не располагаем точными заготовками (за отдельными исключениями).
Часто и технологи завышают припуска на заготовках во избежание возможного брака, чернот, хотя это и не всегда оправдано, так как обрабатываемые на первых операциях поверхности часто обрабатываются повторно и все первоначальные погрешности снимаются.
Вопрос получения баз, обработки деталей на первых операциях технологического процесса, еще недостаточно изучен, поэтому мы имеем тут наибольший процент брака и именно здесь заложен резерв экономии металла и трудоемкости.
Опыт расчета размерных цепей по всему ходу технологического процесса обработки детали, применяемый на «Гидросиле» (по методике ЧТЗ) позволил практически исключить такой вид брака как черноты, уменьшить припуски на черновые операции.
Пример расчета размерной цепи смотри приложение.
Отдельно необходимо рассматривать вопросы рационального раскроя и использования отходов при холодной прессовой обработке заготовок.
Хорошо было бы иметь каталог выштамповок (отхода металла) на предприятиях города и области (в том числе и проката), рассмотреть возможность использования отходов на базе межзаводской кооперации.
Необходимо отметить, что технологи не располагают необходимым оборудованием для выполнения черновых операций (исключение составляют фрезерно – центровальные и карусельно – фрезерные станки, которые дают возможность подготовить надежную базу для последующей обработки корпусных деталей и деталей типа валов, однако и они не всегда имеют достаточную мощность и жесткость.
Токарного оборудования для указанных работ практически нет, плохо обстоит дело и с фрезерным оборудованием, особенно для черновой обработки зубчатых колес (кроме нескольких моделей станков ES для обработки конических шестерен).
Рассмотрим вопрос подачи заготовок на рабочие места. Первичная подача осуществляется завозом заготовок электро или дизельными погрузчиками в унифицированной таре (это наиболее рациональный и распространенный метод транспортировки заготовок: отливок, поковок).
К началу рабочей смены тара с заготовками должна находиться на рабочем месте. К сожалению, несвоевременный завоз заготовок, полуфабрикатов в связи с организационными неурядицами является одной из причин простоя рабочих и оборудования.
Речь идет о внутренних недостатках, когда заготовки имеются на заводе; часто имеют место случаи срыва производства и по причине неудовлетворительно налаженной кооперации.
С целью своевременного снабжения цехов заготовками и вывоза готовой продукции, а также организации внутрицехового перемещения заготовок должны быть разработана карта централизованного обслуживания участка (линии) заготовками и технологическими материалами; к а р т а межоперационной и внутрицеховой транспортировки заготовок, деталей, отходов производства. (см. карты оргпроцесса 4.1 и другие в приложении)..
Передача деталей с операции на операцию технологической линии осуществляется с помощью межоперационного транспорта.
Схемы межоперационной транспортировки могут быть различными
В качестве межоперационного транспорта используются подвесной транспортер (опыт ВАЗа), спец. скаты, склизы, тележки и т. д.
Важно соблюсти принцип удобства транспортировки для исполнителей – рабочих, сохранности поверхностей деталей, экономии производственных площадей.
Существенное влияние на ритмичную работу оказывает качество поступающих на обработку заготовок; имеется в виду отклонения в составе металла, твердости (отбел у чугунных отливок), геометрические погрешности: увеличение или занижение припуска на механическую обработку, литейные поддутости, неочищенный облой у поковок, литники и т. д.
Поэтому важно больше внимания уделять внешнему контролю.
На предприятиях создают специальные лаборатории, которые проверяют не только поступающие в производство заготовки и комплектующие изделия, но и технологические материалы (масла, смазки, охлаждающие жидкости и т. д). Необходимо быть уверенным, что на операцию поступают заготовки, обработка которых не вызовет аварийной ситуации или интенсивного износа оборудования и инструмента.
Большое значение для качественного выполнения операций механической обработки и сборки имеет, так называемая, санитарная обработка заготовок: моечные и слесарные работы.
Часто с целью мнимой экономии трудозатрат стараются указанные работы не выполнять, тем самым вводят дополнительные погрешности в производство, резко отрицательно сказывающиеся, как на надежной ритмичной работе оборудования, так и на качестве выпускаемой продукции
И, конечно, основным, главным фактором ритмичной работы является строгое выполнение запроектированного технологического процесса, всякая самодеятельность, даже с самыми лучшими побуждениями, приносит только вред, рационализация только тогда может иметь место, когда она рассмотрена технологом и внесена в технологический процесс.
1.5 Обеспечение ритмичной работы производственной операции в функции времени.
Для эффективного осуществления технологической операции необходимо рассматривать выполнение рабочим функций, оговоренных технологическим процессом и функций ей сопутствующих, вспомогательных.
Как известно, всякий производственный процесс представляет собой взаимодействие орудий труда, предметов труда и самого труда.
Поэтому, изучая вопрос ритмичной работы каждой конкретной операции, необходимо рассматривать ее неразрывную связь с производством в целом, а также многообразие физиологических. психологических, социологических закономерностей трудовой деятельности человека, воздействие на неё в неразрывном единстве всех элементов системы человек – машина – среда.
Итак, первичное звено производственного процесса – производственная операция (понятие производственной операции шире, чем технологической, сюда включаются и функции обслуживания).
Каковы условия ее функционирования в функции времени.
Хорошо отлаженная операция, с учетом выполнения требований оговоренных в § 1,2, дает возможность работать ритмично, без брака, но только определенное, ограниченное время.
Если мы рассмотрим элементы производственного процесса на данной операции в функции времени, то увидим следующее:
Тц. – время равное циклу обработки >
происходит замена обрабатываемой детали;
Тст. – время равное min. стойкости >
централизованная замена инструмента
(многоинстр. наладки) режущего инструмента,
рабочих жидкостей.
Тсти. – время стойкости измерительного
инструмента >
централизованная замена контрольной
аппаратуры, мерительного инструмента;
Тост. – время стойкости оснастки >
ремонт, замена базовых деталей
(кондукт. втулки, базовые, зажимные призмы).
Тобр. – время обеспечения технологической точности оборудования >
ППР оборудования, централиз. система смазки;
Тэобр. – время безаварийной работы электро-
оборудования >
ППР электрооборудования;
Тотх. – время уборки отходов производства >
график уборки, утилизации отходов;
Тсм. – время равное рабочей смене >
замена исполнителя операции,
предусмотреть дублирование рабочего
(естеств. надобности, срочный вызов,
заболевание).
С определенной долей условности можно отнести к постоянным составляющим операции следующие элементы: созданные условия работ (планировка рабочих мест, типаж установленного оборудования, сантехнические и электрические сети, состояние воздушной среды и др.)
Однако и эти элементы подлежат постоянному воспроизводству (восстановление, ремонт, модернизация, замена на более прогрессивные, соответствующие духу времени).
О цикличности отдельных элементов операции в функции времени уже сказано выше, цикличность воспроизводства постоянных составляющих зависит от вида производства и в каждом отдельном случае изучается на месте.
Вопрос стабильной ритмичной работы – это обеспечение неизменного (в качественном и временном отношении) строго последовательного воспроизводства указанных выше составных элементов операции.
Необходимо определить оптимальный цикл каждого элемента операции, после которого необходимо активное вмешательство с целью воспроизводства первичных рабочих параметров данного элемента. (например, норма расхода оснастки на тысячу выпускаемых машин, цикл замены рабочих жидкостей и т. д.).
Реальное производство соответствует определенному техническому уровню, скажем уровень I.
Если происходит усовершенствование процесса, то мы переходим на уровень II.
При этом необходимо проследить четкую взаимосвязь всех элементов операции, указанных выше (если изменились режимы, то соответственно меняется стойкость и время работы инструмента, износ оборудования и оснастки и т. д.), т. е. необходимо в этом случае проанализировать всю функцию.
Если один из рассматриваемых элементов операции переходит на более высокий уровень, а другие нет, то происходит разладка процесса по времени, что чревато аварийными ситуациями, которые, к сожалению, имеют место на производстве.
Чтобы избежать последнего, необходимо разработать систему мер, гарантирующих синхронную работу по обеспечению воспроизводства всех составляющих операции, определить службы, конкретных исполнителей.
От операции перейти к линии (участку), цеху, определить те факторы, которые сказываются на ритмичной работе этих подразделений.
Указанные вопросы детально разработаны в оргпроцессе – организационной части производственного процесса изготовления детали, изделия, – системе документов, разработанных автором.
Подробно об оргпроцессе в следующих главах.
Правообладателям!
Данное произведение размещено по согласованию с ООО "ЛитРес" (20% исходного текста). Если размещение книги нарушает чьи-либо права, то сообщите об этом.Читателям!
Оплатили, но не знаете что делать дальше?