Текст книги "Профессия инженер"
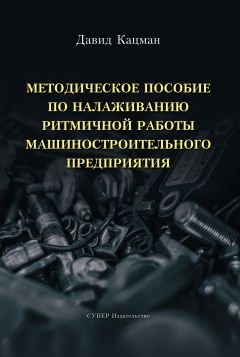
Автор книги: Давид Кацман
Жанр: Техническая литература, Наука и Образование
Возрастные ограничения: +12
сообщить о неприемлемом содержимом
Текущая страница: 3 (всего у книги 10 страниц) [доступный отрывок для чтения: 3 страниц]
Производительность труда и ритмичность
1. Технический уровень нормирования труда на производстве.
Обеспечив проведение в жизнь указанных в предыдущих главах технических и организационных мероприятий, нам удастся наладить ритмичную работу отдельной операции (предшествующих и последующих операций), связанных между собой соответствующим ритмом.
Достаточно ли это, чтобы сказать, что данная операция (линия мехобработки) на какой – то опреде– ленный период времени соответствует современному уровню производства и не подлежит изменению.
Нет, не можем, если учесть, что существуют еще ряд неуказанных раннее факторов, которые постоянно подлежат изменению и оказывают свое влияние на ход производственного процесса.
Это, во-первых, накапливаемый в процессе работы опыт и навыки рабочего и, во-вторых, трудоемкость операции (линии), изменение которой в сторону уменьшения с целью повышения производительности труда – является постоянно планируемым фактором.
Опыт и постоянно повышающиеся знания рабочего являются положительным фактором, способствующим повышению надежности выполняемой операции, а также повышению производительности труда без дополнительных капитальных затрат и модернизации действующего технологического процесса.
Однако, при этом, не должна нарушаться стабильность уже отлаженного процесса, вмешательство в его ход допустимо только под контролем специалиста (технолога, мастера), нельзя бездумно повышать режимы резания т. к. это приводит к преждевременному износу инструмента, выходу из строя оборудования, ухудшению качества выпускаемой продукции
Кроме того, повышение производительности только одной или нескольких операций в поточной механизированной линии, практически не приводит к увеличению производительности труда всей линии (участка).
Следовательно, при необдуманном, технически и экономически не обоснованном, подходе к увеличению производительности на отдельных операциях, мы вносим отрицательный фактор в ритмичную работу линий, это необходимо очень хорошо представлять всем, кто непосредственно связан с производством, особенно это касается работы БРИЗа, (бюро рационализации и изобретательства), где всегда учитывают только техническую сторону вопроса и игнорируют организацию, хотя техника и организация, как уже было показано выше, связаны неразрывно.
Еще более серьезно нужно подходить к планированию и выполнению работ, связанных со снижением трудоемкости выполняемых операций.
Здесь на первое место также выходит организационная сторона вопроса, хотя и техническая сторона нормирования имеет серьезное принципиальное значение.
Трудоемкость, при существовавшем раннее методе планирования, на любом этапе (от начала внедрения до конца производства изделия, иногда в течении десятка лет) была величина переменная и подлежала обязательному изменению в сторону уменьшения.
Факторами способствующими снижению трудоемкости являются: постоянное совершенствование действующего технологического процесса на базе новой техники и передовой технологии, внедрение прогрессивного оборудования и инструментов, повышение навыка работы и квалификации исполнителей, о чем уже говорилось выше.
Большое значение в снижении трудоемкости имеет организационная работа.
Грамотное нормирование должно способствовать четкой напряженной работе, а не создавать дыр (операций с различной напряженностью труда).
Необходимо внедрять, в этом случае, многостаночное обслуживание, расчетно – обоснованные нормы.
Их выполнение в процессе производства является одним из основных путей повышения производительности труда.
2. Рекомендации по разработке методов контроля и определению трудоемкости контрольных операций.
Анализ контрольных операций технологических процессов изготовления изделий основного производства, показывает, что процент контроля технологами назначается произвольно.
При этом, например, процент контроля отверстий в корпусных и алюминиевых деталях, обрабатываемых на алмазно – расточных станках, задается в широких пределах от 10 % до 100 %; то же касается и других контролируемых параметров деталей.
Имеется возможность установить единый на заводе порядок назначения трудоемкости контроля при заполнении контрольных карт технологических процессов и назначении ответственных исполнителей контрольных переходов. (комплекс контроля).
При этом необходимо исходить из 2-х факторов:
1. Важность контролируемых параметров для работы детали, узла.
2. Технологичность выбранных методов обеспечения контролируемых параметров (стабильность технологических процессов, типаж оборудования).
Анализ исполнительных размеров детали и привязочных размеров узла показывает, что всегда необходимо выделить 3 – 5 параметров, которые нужно прямым или косвенным путем контролировать 100 %.
Это те исполнительные размеры, отклонения от которых приводят к прямому выходу из строя узла или невозможности его эксплуатации (например, сборки с двигателем), а также, если нет полной технической гарантии в стабильности обеспечения указанных параметров.
Отнесем эти исполнительные размеры к 1 группе.
Ко 2 группе – отнесем исполнительные размеры и ТУ, отклонения от исполнения которых приводит к нарушению собираемости узла и не обеспечению его основных характеристик.
К 3 группе – исполнительные размеры черновые, технологического назначения, габаритные, линейные и др.
4-группа – прочие исполнительные размеры (канавки, выточки для выхода инструмента и т. д.)
5 – группа – исполнительные размеры заготовок, ТУ и требования технологии входного контроля.
Необходимо учесть, что разбивка на группы по типажу оборудования условна.
В каждом отдельном случае в зависимости от типа оборудования, стабильности наладки (стойкости инструмента), важности контролируемого параметра возможно одни размеры относить к 1-2 группе, другие к 3 группе, хотя все они обеспечиваются обработкой на одном станке.
Необходимо обратить внимание на 2 принципиальных положения, вытекающие из рекомендаций:
а) усиление роли и ответственности исполнителей (финишные операции, личные клейма).
в) необходимость проектирования и внедрения комплексных приборов – совмещение в одном приборе 100 % контроля 3-х, 4-х и более параметров.
г) применение обработки деталей по копирам, использование активного контроля, что гарантирует качество обрабатываемых поверхностей деталей.
1.7 К вопросу установления и сокращения трудозатрат при изготовления продукции.
Работа, направленная на снижение трудоемкости выпускаемой продукции, всегда рассматривалась, как один из основных факторов снижения cебестоимости выпускаемых изделий и, следовательно, экономической эффективности работы предприятия.
В условиях рынка, жесткой конкурентной борьбы, этот вопрос приобретает особую остроту, – выигрывает тот, кто ищет и находит новые нетрадиционные пути снижения трудозатрат, устанавливает более низкие цены, чем конкурент.
Правда, успех может иметь продукция и с более высокими ценами, если технико – эксплуационные характеристики ее значительно превосходят подобную продукцию и потребитель получает более высокие гарантии качества и комфорта. (скажем, автомобили немецких. америк. фирм).
Вопрос первичного установления и динамики снижения трудовых затрат (трудоемкости) изготовления продукции следует расматривать, исходя из следующих основных критериев:
1. Проектная трудоемкость
А. Оригинальность конструкции, её приемственность (стандартизация, унификация).
Б. Отработка на технологичность.
В. Проектный технологический процесс (оборудование, оснастка, исходя из заданного объема производства).
Г. Организация производства (пространственное расположение линий, транспорт, утилизация отходов и т. д).
2. Расчетная трудоемкость
Отличается от проектной – рассчитывается исходя из реального техпроцесса, сложившегося на момент внедрения, действующей организации производства и труда на каждом рабочем месте.
3. Действующая трудоемкость
Отражает фактическое состояние производства (простои в связи с доводкой конструкции и технологии, недостатки организации производства и труда, принципиальное значение имеет квалификация исполнителей, – наличие у них практического опыта или первичное обучение с приобретением навыков работы (выработка динамического стериотипа), преодоление «психологического барьера» при внедрении нового (переучивание, материальная заинтересованность и т. д).
Задача руководителя участка, мастера, технолога устранить огрехи, возникшие при внедрении, освоить в сжатые сроки расчетную трудоемкость, соответствующую действующей технологии (техническим возможностям оборудования и организации труда), – достичь в заданные сроки проектной трудоемкости при наличии всех необходимых условий
В дальнейшем трудоемкость держится на заданном уровне, наступает период стабильности. Чтобы и дальше повышать производительность труда необходимо внесение существенных изменений в конструкцию и технологию производства, улучшение организации и условий труда.
Частичные изменения, не меняющие общую картину, могут иметь место, если хорошо налажена рационализаторская работа.
Таким образом, процесс снижения трудоемкости характеризуется не плавным течением во времени, а скачками, поэтому планирование постоянного снижения трудоемкости без наличия на то соответствующей базы приводит к разрушению качественных характеристик производства.
Период стабильности должен быть рассчитан и задан заранее.
Другими словами, – речь идет о прогнозировании экономической целесообразности выпуска продукции в соответствующем ассортименте, количестве и качестве на определенный период.
Подробное обоснование данного тезиса будет приведено в главе «Новая техника и ритмичность»
Таким образом, жизненный цикл выпуска продукции складывается из 3-х частей:
1. Освоение и доведение до запланированных показателей (проектной трудоемкости).
2. Стабильная работа с обеспечением проектных показателей.
3. Переход на новую или модернизированную продукцию (при этом, часто возникает еобходимость сохранить часть старого производства в виде запчастей).
Длительность по времени 2 этапа определяется коньюктурой рынка и вложенными затратами в уже действующее производство, его технико-экономическими характеристиками.
В полностью автоматизированном производстве время освоения проектной трудоемкости приближается к 0, в механизированном, где человеческий фактор играет существенную роль, оно колеблется в зависимости от состава оборудования и квалификации рабочих.
Фактически (принимая квалификацию рабочих, как обязательное условие) время освоения операции в полной мере зависит от главного фактора– используемого оборудования.
По паспортным и статистическим данным устанавливается время работы оборудования до морального и физического износа, здесь учет фактора экономической целесообразности обязателен.
Это очень важно для своевременного воспроизводства (недопущения срывов в процессе производства)
Новая техника и ритмичность
Рассмотрим вопрос – каковы причины того, что производство постоянно совершенствуется; можно ли затормозить этот процесс, регулировать его в определенных, разумно допустимых пределах, или, наоборот, форсировать внедрение всяческих изменений в уже отлаженный и действующий технологический процесс?
Чтобы этот вопрос решить, необходимо в начале разобраться – каковы пути попадания на производство новых идей.
Это внесение изменений в действующую конструкторскую документацию с целью модерназации, повышения качественных характеристик выпускаемых изделий; внедрение стандартов (например, на инструмент); распоряжения руководства предприятий, в части освоения новой техники и передовой технологии; модернизация действующего оборудования; рационализаторская и изобретательская работа, оргтехмероприятия, планы снижения трудоемкости, повышения качества продукции, наконец, личные творческие планы ИТР и планы повышения производительности труда рабочих.
В начале необходимо определить понятие – «новое».
«Новое» – это не обязательно передовое, прогрессивное, под понятием нового будем рассматривать любое вторжение в уже отлаженный действующий процесс (операцию), что приводит к изменению какого – либо его элемента.
Изменение или замена действующего процесса, в связи с внедрением более совершенного оборудова– ния или прогрессивной технологии, будем именовать в дальнейшем – техническим новшеством.
Не всегда высказанные идеи, предложения удается реализовать в действующем производстве.
Путь этот непростой и сложный, требующий время и терпения.
В качестве примера приведу одну из проблем, с которой пришлось мне. молодому технологу. столкнуться. как только я начал работать цеховым технологом на участке коленвала цеха 100 Челябинского тракторного завода.
Первая операция, – проточка коренных и шатунных шеек коленвала, осуществлялась на токарном станке.
Раскаленная. сливная стружка вилась вокруг суппорта станка и отводилась в сторону оператором с помощью крючка.
Были попытки решить вопрос стружколомания привычными методами, (конструкция резца. порожек на передней грани). но результаты были отрицательные.
С точки зрения техники безопасности, операция вызывала опасение и я начал ломать себе голову. как решить эту проблему.
Возникла идея осуществлять точение методом ступенчатой подачи, то-есть прерывистое точение, – на один оборот детали с подачей следует следующий оборот без подачи.
Нужно было исследовать режим смены подачи, – решение вопроса – оригинальная конструкция профилирующего кулачка или изменение конструкции вала подач.
Занятый текущим производством и не имея соответствующей базы я отложил осуществление этой идеи на потом. а жаль. спустя три года я прочитал в журнале «Станки и инструменты» статью, в которой говорилось. что метод ступенчатой подачи. с целью стружколомания был внедрен одной из зарубежных фирм при проектировании новой автоматической линии.
Была также мною высказана идея более широко использовать групповой метод Митрофанова.
На основании технологических процессов обработки деталей в мелкосерийном и единичном производствах вывести типовые варианты получения базовых поверхностей (1-этап техпроцесса), и далее разработать теоретические и практические предпосылки комплектования обрабатываемых деталей в группы.
Но вернемся от идей к реальному производству.
Необходимо сразу различить те изменения, внедрение которых неизбежно и которые существенно не влияют на ход процесса: (например, изменение Госта на инструмент или материал, уточнение техдокументации и существенные изменения, внедрение которых связано с остановкой процесса, переучиванием исполнителя, что не может не отразиться на ритмичном ходе производственного процесса в целом.
Поэтому, разрабатывая и внедряя производственный процесс (понятие значительно шире, чем понятие – технологический процесс), необходимо ставить задачу создания экономических условий на определенное заранее указанное время (период), когда вмешательство в данный процесс, даже с самыми благими намерениями, является не только не желательным, а даже вредным.
Другими словами, создание и поддержание четкой системы воспроизводства всех элементов процесса (операции), совершенствование выходных данных за счет роста квалификации исполнителя, замены отдельных элементов на более прогрессивные, в то же время не должно сопровождаться коренной ломкой процесса на определенном, заранее заданном временном интервале (период стабилизации процесса), в противном случае невозможно создать стабильный технологический процесс, обеспечивающий ритмичную работу.
Нужно отказываться от порочной практики вести непрерывное внедрение (замену или модернизацию выпускаемых изделий) без остановки действующего производства, так как в этих условиях невозможно решить все организационно – технические вопросы, о которых говорилось выше; сиюминутно получаемая при этом эффективность в дальнейшем приносит отрицательный результат.
Постоянное вмешательство в действующее производство с целью рационализации (чем больше, тем лучше), к сожалению, также получило широкое распространение. Связано это с тем, что заводу раннее планировались такие показатели, как количество рационализаторов на 1000 работающих, количество внедренных предложений и т. д.
Поэтому, ради красивого отчета, закрывались глаза на те отрицательные явления, которые при этом имели место.
Забывалась мудрая народная пословица: «Семь раз отмерь, один раз отрежь».
Естественно, что создать стабильно действую– щее, эффективное производство, не требующее постоянного вмешательства, можно лишь в том случае, если технологический процесс соответствует современному уровню техники и решает не только технические, но и организационные вопросы, обеспечивает надежное функционирование производства с учетом количественных и качественных показателей.
Такие условия имеют место, когда разрабатывается типовой технологический процесс с учетом перспективы не менее, чем на 3..7 лет. (имеется ввиду крупносерийное, массовое производство).
Именно срок 7 лет принят как оптимальный при эксплуатации специального и специализированного оборудования, хотя срок физического износа иногда достигает 20 лет.
Отдельно хочу остановиться на идее разработки типового перспективного технологического процесса, который характеризуется единством содержания и последовательности большинства операций и переходов для группы изделий с общими конструктивными признаками и соответствует современным достижениям науки и техники, методы и средства осуществления которого полностью или частично предстоит освоить на предприятии.
Разработка типовых перспективных технологических процессов может осуществляться в такой последовательности:
1. Определение номенклатуры узлов и деталей, подлежащих освоению в ближайшие годы (3. 5 лет).
Наличие отработанной документации годной для подготовки серийного производства указанных изделий.
2. Разработка каталога типовых узлов и деталей, вплоть до метизов, находящихся в производстве и подлежащих освоению в перспективе на данном предприятии.
3. Отработка единых технологических решений по геометрии и исполнительным параметрам каждой группы деталей с учетом технологичности их изготовления в заданных условиях.
4. Определение необходимых технических, экономических, социологических предпосылок постановки на производство типовых групп деталей: выбор вида производств, оборудования. необходимость спец. условий (термоконстантные помещения для финишных и контрольных операций, стендовое хозяйство для испытаний работоспособности изделий в северном и тропическом исполнении и т. д.), решение кадровых вопросов.
Закладывание указанных данных в проект реконструкции завода.
5. Разработка на указанной выше в п.1..4 базе типовых перспективных технологических процессов.
В качестве примера можно привести типовые перспективные технологические маршруты на обработку деталей типа валов и корпусов.
Данные технологические процессы вобрали в себя передовой опыт отечественного и мирового машиностроительного производства (на момент их разработки).
Ряд идей, заложенных автором в типовой перспективный технологический процесс обработки деталей типа валов, нашли свое реальное воплощение на производстве:
а) получение заготовок на стане поперечно-клиновой прокатки и их последующая обработка на 6-ти шпиндельных токарных полуавтоматах.
С целью осуществления обработки заготовок валиков на указанном оборудовании разработаны и внедрены спец. патроны оригинальной конструкции (авторы Ворона А.Ф., Ю.И. Меркотан, Петровская).
б) получение канавок на валах методом пластической деформации на прессах, с полной автоматизацией процесса, взамен фрезерования на шлицефрезерных станках;
в) обработка 2-х…3-х шеек одновременно на круглошлифовальных автоматах модели 3М 1 5 1Е и 3 Т 1 6 1 (автоматическая правка шлиф. камня по копиру, активный контроль, многостаночное обслуживание).
Данный опыт говорит о перспективности и правильности выбора указанного выше направления совершенствования производства на предприятии.
Начинать надо с осуществления ряда организационных мер, без увеличения штата ИТР и служащих, создать условия для работы на перспективу.
Как определить, что разработанный и внедренный производственный процесс соответствует современному уровню техники и организации?
Кто может дать такую оценку?
Надо иметь такой квалификационный орган в пределах отрасли, куда должны войти лучшие представители науки и практики и куда может обратиться за консультацией руководитель предприятия.
Их оценка должна исходить из принципа: соответствует ли рецензируемый проект условиям обеспечения высокой производительности и экономичности на базе НОТ, гарантирует ли стабильную работу и качество выпускаемой продукции или нет.
Прошедший экспертизу проект внедряется в производство и получает право гражданства на определенный и заранее оговоренный срок.
В течении указанного времени вмешательство в действующее производство без достаточных и веских оснований нужно свести к минимуму.
ВЫВОДЫ
Таким образом, анализируя все сказанное, нужно отметить, что для обеспечения ритмичности производственного процесса необходимо выполнение по крайней мере 2-х важных условий, с одной стороны, постоянное, плановое, технически грамотное обслуживание действующего производства (воспроизводство качественных характеристик процесса), и с другой стороны – невмешательство, в течении определенного времени, с целью его совершенствования и модернизации (внедрение технических новшеств нужно строго реглаиентировать).
Сразу возникает вопрос? Что же, надо перестать заниматься совершенствованием действующего производства, приостановить все работы по новой технике, рационализации и т. д.
Нет, конечно.
Наоборот, эта работа должна быть усилена и проводиться на более высоком техническом и организационном уровне.
Необходимо, уже настало такое время, перенести эту работу в хорошо оснащенные технологические лаборатории, каждое новшество должно пройти тщательную проверку, быть полностью подготовленным для переноса в действующее производство.
Сейчас, во время научно – технической революции, если поставленное выше условие не будет выполнено, вся деятельность ИТР, производственного персонала цехов и участков будет направлена на постоянные изменения действующего техпроцесса, что негативно скажется на ритмичности работы, выполнении плановых заданий с обеспечением качества продукции.
Прогрессивный метод освоения новых изделий (без остановки действующего производства), о чем уже говорилось выше, должен иметь четко оговоренный временной предел, иначе он может превратиться в свою противоположность, если время освоения равно бесконечности.
Указанный порядок разработки и внедрения прогрессивной технологии и новой техники приводит к разделению труда ИТР, прежде всего, технологов.
Определенная категория исполнителей должна заниматься вопросами технического обеспечения действующего производства, другая категория, – вопросами разработки новых прогрессивных процессов, как с технической, экономической, так и организационной точки зрения.
Причем, службы технического обеспечения должны быть централизованы в целом по заводу, – положительный опыт такой централизации имеется на ВАЗе, этот опыт необходимо изучить и широко распространить на другие машиностроительные предприятия России.
Известно, что опыт ВАЗа дает возможность определить наиболее перспективные для освоения и внедрения на предприятиях машиностроения производственные методы. технологические процессы, средства механизации и автоматизации, которые дают значительный экономический эффект.

Почему в данной книге так много внимания уделяется опыту ВАЗа.?
Потому, что хотя в печати писали о достижениях флагмана отечественного автомобилестроения. фактически изучению и пропаганде его опыта уделялось очень мало внимания.
Даже разработанные по указанию вышестоящих инстанций мероприятия по совершенствованию организации производства, труда, управления и заработной платы по опыту ВАЗа – тут же были похоронены.
В чем тут причина?
Характеризуя производственно -хозяйственную деятельность предприятий Союза и сравнивая с родственными зарубежными фирмами, приходишь к однозначному выводу, что административно-командная система и создание современного экономически эффективного управления. комфортных условий производства и труда – вещи несовместимые.
Пропаганда. демонстрация опыта ВАЗа открывала глаза рабочим на реальное положение дел в сфере управления производством. организации труда на каждом рабочем месте, показывало нашу дремучую отсталость и косность.
Что скрывалось за плотным занавесом от рабочего класса оказалось вдруг на виду у всех в Тольятти, объяснить это было невозможно, один выход – запретить.
ВАЗ фактически постигла та же судьба, что и Щекинский эксперимент, который выбивал у госчиновников их власть над предприятиями, так как в дело вступали экономические законы, здравый смысл, не подвластный диктату.
Таким образом, всякая попытка в условиях административно – командной системы построить производственные отношения, техническую политику на основе экономических законов (экономика должна быть экономной) была заранее обречена на провал.
Должно было пройти много лет для того, чтобы были созданы условия реальной хозрасчетной деятельности предприятий, экономической их самостоятельности.
Выживание в жестких условиях рынка, конкуренции невозможно, если отставать от достигнутого сегодня передового уровня организации производства и труда.
Вот почему данные рекомендации очень актуальны и злободневны, и, надеюсь, найдут применение на многих предприятиях, и не только машиностроения.
Несколько слов о задачах службы подготовки производства (из истории вопроса)
Вопросы, касающиеся подготовки производства новых изделий и обеспечения инструментом и оснасткой действующего производства, – самые острые и злободневные на заводе.
Основной упор обычно делается на то, что существующие мощности инструментального цеха недостаточны и решение вопроса заключается в укреплении цеха квалифицированными кадрами и выделении дополнительного оборудования.
Естественно, что в связи с ростом номенклатуры и обьемов выпуска продукции, необходимо наращивать мощности обеспечивающего и обслуживающего производств, однако, основной недостаток кроится совсем в ином, – в отсутствии централизованного планирования в цехах и по заводу в целом всего комплекса работ, связанного с подготовкой производства; планирование работ инструментальному цеху производится без учета возможностей цехов самих себя обеспечивать оснасткой и ее ремонтом (исключая координатные работы, прессформы, специнструмент и крупные наладки).
Имеет место заказ оснастки цехами в больших количествах, про запас, при этом бывают случаи заказа оснастки снятой с производства.
План инструментальному цеху верстается из двух источников: заявки цехов и заявки ОГТ по новой технике (включая и графики подготовки).
В ОГТ заявки соcтавляются на вновь спроектированную оснастку, причем в количествах необходимых для внедрения новшества в производство и создания минимального задела, обычно месяц– два до перезаказа цехом.
Так как, часто заявки ОГТ зависают, а сроки подпирают, оснастка, срочно, в одном, двух экземплярах изготавливается в лаборатории резания ОГТ и внедряется в производство.
При этом возникает любопытная ситуация, – заявка ОГТ остается не выполненной и повторяется снова, цех также заказывает эту оснастку (уже внедрена в производство), заказы суммируются в инструментальном цехе (выгодно набирать объемы, изготавливая большие партии), в конце концов оснастка изготавливается в таком количестве, которое цеху просто не нужно, – и это, заметим, при отсутствии производственных мощностей инструментального цеха.
Оснастка накапливается в инструментальной кладовой одного цеха и хранится годами, другой цех, не имея информации об этом, снова в срочном порядке заказывает ее и усугубляет ситуацию, драгоценное время и деньги летят на ветер.
Как навести порядок в указанном вопросе, – необходимо иметь централизованную службу подготовки производства, ввести систему ЧТЗ
Отделом АСУП завода «Гидросила» совместно с НИПИАСУ г. Волгоград разработаны две задачи, цель которых, – автоматизировать решение вопросов, указанных выше.
1-я задача: «Информационно – поисковая система сопровождения изготовления технологической оснастки с выводом запросной информации на видеотерминальное устройство». АС 280.01.10.03В
2-я задача: «Учет наличия и использования технологической оснастки по инструментальным кладовым цехов» АС 280.01.11.000 ЗВ.
Указанные постановки задач могут быть использованы при разработке задач на ПЭВМ.
Внимание! Это не конец книги.
Если начало книги вам понравилось, то полную версию можно приобрести у нашего партнёра - распространителя легального контента. Поддержите автора!Правообладателям!
Данное произведение размещено по согласованию с ООО "ЛитРес" (20% исходного текста). Если размещение книги нарушает чьи-либо права, то сообщите об этом.Читателям!
Оплатили, но не знаете что делать дальше?