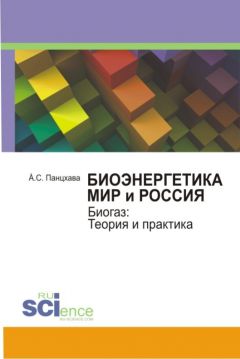
Автор книги: Евгений Панцхава
Жанр: Прочая образовательная литература, Наука и Образование
сообщить о неприемлемом содержимом
Текущая страница: 9 (всего у книги 68 страниц) [доступный отрывок для чтения: 22 страниц]
Вторым сырьевым источником крахмала для производства этанола в России является картофель. Из 1 тонны картофеля можно получать до 60 л этанола. При урожае картофеля в России в 2012 году в объеме 29.3 млн. тонн потенциальный объем этанола может составить 1.76 млн. куб. м на сумму 1.16 млрд.$ US.
Картофель – культура широко распространенная в России в регионах рискованного земледелия. Производство его для технических целей, например для производства этанола, может оказать существенное влияние на подъем экономики в этих регионах.
Для того чтобы выйти по производству этанола в объемах современного его производства в США в России нужно засевать картофелем до 15 млн. га.
Третьим потенциальным сырьем для производства этанола в России может стать сладкое сорго, культивируемое на Северном Кавказе, Дальнем Востоке и в Поволжье.
Урожай сладкого сорго – 20–30 т/га. Из 1 тонны массы сорго получают 800–850 литров сока с содержанием 20 % углеводов, или можно получить до 80 литров этанола, или с 1 га – 2 куб. м на сумму 1320 $ US.
Таким образом, перспектива развития производства транспортного этанола в России с последующим его экспортом достаточно оптимистичны. Но, совершенно очевидно, что основным сырьем для его производства в России должна стать древесина, что требует создания современных технологий ее разложения на лигнин и целлюлозу.
3.16. Получение биоводородаОдин из методов получения биоводорода из биомассы – это бутиловое или ацетоно-бутиловое брожение сахарозы или крахмала.
3.6.1. Ацетоно-бутиловое брожение (Cl. Acetobutylicim)
2 М Глюкозы = 1 М Бутанола + 1 М ацетона + 4 М Водорода + 5 М СО2
На 1 тонну мелассы образуется 80 куб. м водорода, или на все произведенную мелассу в 2013 году– 124.8 млн. куб. м
С 1 гектара плантаций сахарной свеклы (мелассы) можно получить до 140 куб. м водорода.
Дополнительно к водороду с 1 тонны мелассы получают до 114 кг бутанола до 36 кг ацетона, или со всего годичного объема мелассы – Бутанола 177840 тонн, Ацетона -56160 тонн.
4.2 Бутиловое брожение (Cl. Butylicum)
3 М Глюкозы = 1 М Бутирата + 1 М Ацетата + 6 М СО2 + 9 М Водорода + 4 М Воды
На 1 тонну мелассы можно получить до 140 куб. м Водорода, или на всю произведенную мелассу в 2013 году можно получить 218 млн. куб. м Водорода, а с 1 гектара плантаций сахарной свеклы(меласса) – 315 куб. м.
В СССР до конца 70-х годов ХХ столетия в эксплуатации находилось 4 ацетоно-бутиловых завода: в г. Грозном, в г. Нальчике, в г. Талица (Свердловской области) и в г. Ефремов (Тульской области). К концу 90-х годов остались Грозненский и Ефремовский заводы.
Ефремовский завод производил в сутки до 50 тонн растворителей (бутанол: ацетон: этанол = 13:4:1) и до 29 тысяч куб. м водорода, или в год: 15000 тонн растворителей и до 8.7 млн. куб. м водорода.
Грозненский завод– в сутки: 74 тонны растворителей и 43 тысячи куб. м водорода, в год: 12.9 млн. куб. м водорода и до 22 тысяч тонн растворителей.
К сожалению, весь образующийся водород в то время выпускался в атмосферу (углекислота шла на производство жидкой и твердой углекислоты).
Ефремовский ацетоно-бутиловый завод можно восстановить.
В конце 60-х годов ХХ столетия на Ефремовском ацетонобутиловом заводе (1967) и Грозненском АБЗ (1969) были введены в эксплуатацию два цеха по производству кормового витамина В-12 методом термофильного метанового брожения жидких отходов этих производств – барды (3000 куб. м/сутки) Кроме витамина В-12 каждый цех производил в сутки до 30 тысяч куб. м биогаза, который целиком использовался для производства тепловой энергии для всего производственного цикла.
Таким образом, в конце 60-х годов в СССР впервые в мире были созданы крупномасштабные промышленные производства биотоплив из биомассы (биовородород, биометан, биобутанол, биоацетон и биоэтанол).
Картофель.
При ацетонобутиловом брожении с 1 тонны картофеля можно получить 25 куб. м водода, 340 кг Бутанола и 110 кг Ацетона.
С 1 гектара картофельных плантаций – 875 куб. м Водорода + 12 тонн Бутанола + 4 тонны Ацетона. При бутиловом брожении с 1 тонны картофеля – 42 куб. м Водорода, или с 1 гектара плантаций – 1500 куб. м водорода.
Сладкое сорго.
С 1 тонны стеблей сорго при ацетонобутиловом брожении можно получить до 30 куб. м Водорода + 114 кг Бутанола + 40 кг Ацетона.
При бутиловом брожении – 50 куб. м Водорода.
С 1 гектара плантаций сахарного сорго при ацетонобутиловом брожении: 900 куб. м Водорода + 3.4 тонны Бутанола + 1.2 тонны Ацетона, при бутиловом брожении – 1500 куб. м Водорода.
3.17. Биодизельное топливо – перспективы производства в РоссииРоссия имеет все возможности для производства растительных масел с целью производства и экспорта биодизельного топлива. В России основными продуцентами растительных масел являются: подсолнечник, лен, горчица, небольшой объем занимают: кукуруза, соя и рапс.
Ведущее место занимает подсолнечник. В 2000 году Россия произвела более 4 млн. тонн растительных масел.
Очень перспективным для России является расширение посевов льна в Средней полосе (традиционное российское производство льна) с производством льняного волокна и семян для отжима масла, а также в Южных регионах: подсолнечника, сои, рапса.
В Мурманской области работают две крупных биогазовых установки с реакторами объемом в 50 м3.
Литература3-1..Биотопливо – Википедия ru.wikipedia.org.
3-2. Панцхава Е.С., Березин И.В., Техническая биоэнергетика, // Биотехнология, 1986, № 3, с. 8–15.
3-3.O., Rosillo-Calle I7., 10 Biomass (Other then Wood)// Survey of Energy Resources., 1998, 18th Edition, p. 227–257.
3-4. Велихов Е., интервью, газета «Поиск», № 3, 13 марта 2001 г.
3-5. Zervos A., Lius Ch., Schrafer O., Tomorrow’s world// REW., 2004, v. 7, n 4, p. 238–245.
3-6. Bhattacharya S.C., Fuel for thought // REW, 2004, v. 7, n 6, p. 122–130. th
3-7. Raldow W., Research in the 6th FP-future, calls. Bioenergy enlarged perspectives. Budapest., 2003.
3-8. Sims R., Richard K., REW, 2004, n 2, p. 128–133.
3-9. FAO. Forestry, Fuels and the Future // Forestry Topics Report, 1996, n. 5, FAO Forestry Department Rome.
3-10. Rosillo-Calle F., Cortez L.A., Forward ProAlcochol 11: Re-viero of Brazilian National Bioethanol Program // Biomass and Bioenergy, 1996.
3-11. NUTEC, Federal Energy Research and Development for the challenges of the 21st Century // Report of the Energy Research and Devel-opment Panel, 1997. The President’s Committee of Advisors on Science and Technology., Washington DC.
3-12. Lourin A., Biodisel: Tomorrow’s Liquid Gö1d // Biologist 1998, 445. 11. p. 17
3-13. European Commission., 2004, Refined Biofuels Pellets and Briquettes (LAMNET).
3-14. Rakes Ch., Hotting up, REW, 2004, v. 7, n 4.
3-15. Kaizer W., Shimizu M., High– temperature gasification, Waste management world, 2004, n. 6.
3-16. Tonsing R., The new block gold, REW, 2004, v. 7, n 3.
3-17. Fulton L., Driving ahead, REW, 2004, v/ 7, n 4.
3-18. Экспресс-информ. Интернет– www.einform.com., ua.
3-19. Производство биоэтанола в США стремительно растет – Abercade abercade.ru.
3-20. Недельное производство биоэтанола в США побило… – ПроАгро www.proagro.com.ua/news/sng/4082037.htm.
3-21. Fulton L., Driving ahead, REW, 2004, v/ 7, n 4.
3-22. Экспресс-информ. Интернет– www.einform.com., ua.181/ 09.htmk.
3-23. Raavindranath N. H., Hall D.O., Estimates of feasible productivities of short rotation tropical forestry plantation // Energy for Sustainable Development, 1996, n 2, p. 14–20.
3-24. Natarajan I., Biogas for All // Wood Energy News, 1997, 12(2), p. 22., FAO, Bangkok.
3-25. Biomass for Energy – Danish Solutions // Danosh Energy Agency, 1996, Ministry of Environmental and Energy, Copenhagen.
3-26. Панцхава Е.С. и др., Биогазовые технологии, М., 2002.
3-27. Панцхава Е.С., Пожарнов в.а., Российские биогазовые технологии и их коммерциализация. // Сб. трудов Международной конференции «Энергоэффективность крупного промышленного региона», 79 июня 2004 г., Донецт, Украина.
3-28. Willumsen H., Landfill gas recovery plants., Waste management world, 2004.
3-29. Самая крупная в Дании установка по производству биогаза …www.lemvigbiogas.com/RU.htm
3-30. Denmark's largest biogas plant receives large amounts of fish waste…www.lemvigbiogas.com/GB.htm
3-31. Good practice examples on heat use of biogas plants in Denmark., www.e-sieben.at.
3-32. Биогаз в США, www.rosbiogas.ru.
3-33. Панцхава Е.С., Кошкин Н.Л., Использование энергии биомассы в России: Проблемы и перспективы. Тезисы германо – российской конференции, 1994, 24–26 октября, г. Фрайбург, ФРГ
3-34. Бензин и этанол – мировые перспективы – рынок топлива www.samoupravlenie.ru
3-35. Новости о конце света» Ресурсы планеты неисчерпаемы 2012over.ru
3-36. Биотопливо, Материал из Википедии – свободной энциклопедии ru.wikipedia.org/wiki.
3-37. 05 февр. 2007 г. – Биомасса ползет в бак, Галина Костина, expert.ru /expert/2007/05/biomassa.
3-38. Ольга Ракитова, Ресурсы, www.rg.ru.
3-39. «Новости о конце света» Ресурсы планеты неисчерпаемы 2012over.ru.
3-40. Иван Карташев, Зачем нужны биотоплива,
2007,www.computerra.ru.
3-41. Виды биотоплива 3-42. Отчет РЭА, 2011.
3-43. Биомасса(энергия биомассы) http://www.ecomuseum.kz) 3-44. Новости о конце света» Ресурсы планеты неисчерпаемы 2012over.ru/resursi-planeti-neischerpaemi.html.
3-45. Виды биотоплива
3-46. Биотопливо – альтернативный вид топлива 3-47. Альтернативное биотопливо – биодизель alternativenergy.ru.
3-48. Вместо бензина автомобили будут заправлять биотопливом, изготовленным из водорослей, biointernational.ru.
3-49. Я. М. Паушкин, Г. С. Головин, А. Л. Лапидус, А. Ю. Крылова, Е. Г. Горлов, В. С. Ковач, Получение моторных топлив из газов газификации растительной биомассы, www.promeco.h1.ru.
3-50. Биотопливо – плюсы и минусы, e-ypok.ru.
3-51. Наша позиция в отношении биотоплива 3-52. Автомобили: использование биотоплива, http://europa.eu. 3-53. Перспективы производства электрической энергии из биомассы …www.uabio.org
3-54. Поколения биотоплива., www.bionovosti.ru.
3-55. Third generation biofuels from microalgae – Formatex Research. www.formatex.info.…
3-56. Historical Overview – Biogas-china.org., www.biogas-china.org.
3-57. Бензин и этанол – мировые перспективы – рынок топлива., www.samoupravlenie.ru.
Глава 4. Технологии, используемые для производства исходного сырья из биомассы для синтеза моторных топлив разного класса
Ниже представлены короткие описания различных способов переработки биомассы: термохимические методы переработки, физикохимические методы переработки биомассы, а также биохимические методы.

Рис. 4–1. Технологии переработки биомассы. Переработка биомассы [4–1]
4.1. Термохимические технологии
Древнейший, но наименее выгодный процесс с КПД получения тепловой энергии 15… 18 %. Однако существуют такие виды биомассы, которые выгоднее сжигать при условии создания тепловых агрегатов с более высоким КПД. К таким видам – биомассы относятся:
• солома злаковых и крупяных культур, стебли подсолнечника и кукурузы, из которых готовят топливные гранулы – пеллеты;
• некоторые виды древесины, древесные отходы;
• твердые отходы сельскохозяйственного производства;
• городские твердые отходы [4–2];
• отходы производства сахара из сахарного тростника – багасса, которая при прямом сжигании используется для производства пара, электричества, пульпы, бумаги, картона, корма для животных [4–3]. В 1995 г. во всем мире было получено около 200 млн. т багассы, из которых 95 % использовалось как топливо для производства сахара, заменив 40 млн т нефти.
Существует множество типов и размеров систем прямого сжигания биомассы, в которых можно сжигать различные виды топлива: птичий помет, соломенные тюки, дрова, муниципальные отходы.
Тепло, получаемое при сжигании биомассы, может использоваться для отопления и горячего водоснабжения, для производства электроэнергии и в промышленных процессах. Одной из проблем, связанных с непосредственным сжиганием, является его низкая эффективность.
Сжигание древесины может быть разбито на 4 фазы: – Кипение воды, содержащейся в древесине. Даже древесина, высушенная в течение нескольких лет, содержит от 15 до 20 % воды в клеточной структуре. – Выделение газовой (летучей) составляющей. Очень важно, чтобы эти газы сгорали, а не "вылетали в трубу". – Выделяющиеся газы смешиваются с атмосферным воздухом и сгорают под воздействием высокой температуры. – Сгорание остатков древесины (преимущественно углерод). При хорошем сжигании энергия используется полностью. Единственным остатком является небольшое количество золы.
Для эффективного сжигания необходимы три условия: 1. Достаточно высокая температура. 2. Достаточное количество воздуха. 3. Достаточное время для полного сгорания. [4–4].
Один кубический метр сухой древесины содержит 10 ГДж энергии (десять миллионов кДж). Для нагревания 1 литра воды на 1 градус требуется 4,2 кДж тепловой энергии. Для того, чтобы довести до кипения литр воды, потребуется менее 400 кДж, содержащиеся в 40 кубических сантиметрах древесины – то есть небольшая деревянная палочка. На практике на открытом огне потребуется, по крайней мере, в 50 раз большее количество древесины. Эффективность преобразования не превышает 2 %.[4–4] Разработка печей или котлов, способных эффективно использовать энергию топлива, требует понимания процессов сгорания твердого топлива. Первым процессом, потребляющим энергию, является испарение содержащейся в древесине воды. Для относительно сухого топлива на испарение используется лишь несколько процентов от общего количества выделяемой энергии. В самом процессе сгорания всегда имеются две стадии, потому что любое твердое топливо содержит две сгораемые составляющие. Летучие компоненты выделяются из топлива при повышении температуры в виде смеси паров и испаренных смол и масел. При сжигании этих продуктов образуются небольшие пиролизные струи. [4–4]. Современные устройства для сжигания (котлы) обычно производят тепло, пар, используемый в промышленных процессах, или электроэнергию. Устройство систем прямого сжигания варьируется в зависимости от варианта использования. Выбор топлива также влияет на дизайн и эффективность систем сжигания. Системы прямого сжигания биомассы подобны аналогичным устройствам, сжигающим уголь. На практике биомасса может сжигаться совместно с углем в небольшой пропорции в существующих угольных котлах. Биомасса, сжигаемая совместно с углем, представляет собой дешевое сырье, например отходы лесного или сельского хозяйства. Это помогает уменьшить выбросы в атмосферу, обычно связанные с использованием угля. [4–4]
Термохимическая конверсия сырья без доступа воздуха при температуре 450…550 °C позволяет из 1 м3 абсолютно сухой древесины получать: 140… 180 кг древесного угля, не содержащего ни серы, ни фосфора и используемого для получения лучших сортов стали, 280.. 400 кг жидких продуктов – метанола, уксусной кислоты, ацетона, фенолов; 80 кг горючих газов – метана, монооксида углерода, водорода [4–2].
Разные виды высокоэнергетического топлива могут быть получены с помощью нагрева сухой древесины и даже соломы. Процесс использовался в течение столетий для получения древесного угля. [4–4].
Традиционный пиролиз заключается в нагреве исходного материала (который часто превращается в порошок или измельчается перед помещением в реактор) в условиях почти полного отсутствия воздуха, обычно до температуры 300 – 500 °C до полного удаления летучей фракции. Остаток, известный под названием древесный уголь, имеет двойную энергетическую плотность по сравнению с исходным материалом и сгорает при значительно более высоких температурах. В зависимости от влажности и эффективности процесса, 4-10 тонн древесины требуется для производства 1 тонны древесного угля. В случае если летучие вещества не собираются, древесный уголь содержит две трети энергии исходного сырья.[4–4].
Пиролиз может проводиться в присутствии малого количества кислорода (газификация), воды (паровая газификация) и водорода (гидрогенизация). Одним из наиболее полезных продуктов в этом случае является метан, представляющий собой топливо для производства электроэнергии с помощью высокоэффективных газовых турбин.
Более сложная техника пиролиза позволяет собрать летучие вещества. Кроме того, контроль температуры позволяет контролировать их состав. Жидкие продукты могут использоваться в качестве жидкого топлива. Однако они содержат кислоты и должны очищаться перед использованием.[4–4]. Получение древесного угля.
Производство древесного угля охватывает широкий диапазон технологий от простых и рудиментарных земляных устройств до сложных, обладающих большой мощностью реторт. Использование различных технологий приводит к получению древесного угля разного качества.
Типичные параметры качественного древесного угля: – Содержание золы – 5 %. -Содержание углерода – 75 %. -Содержание летучих компонентов – 20 %. -Плотность – 250–300 кг/м3. Физические параметры – Умеренно рыхлый.
Усилия по оптимизации производства древесного угля направлены на оптимизацию приведенных выше параметров при минимальных инвестициях и затратах на обслуживающий персонал и максимальном выходе угля по отношению к количеству древесины на входе. [4–4] Производство древесного угля состоит из шести главных этапов:
• Подготовка древесины.
• Сушка или уменьшение влажности.
• Предварительная карбонизация – уменьшение количества летучих компонентов.
• Карбонизация – дальнейшее уменьшение количества летучих компонентов.
• Завершение карбонизации – увеличение содержания углерода.
• Охлаждение и стабилизация древесного угля.
Первый этап состоит из сбора и подготовки основного сырья – древесины. [4].
Второй этап получения древесного угля выполняется при температурах от 110 до 220 °C, заключающийся в уменьшении количества воды в древесных порах, воды, содержащейся в клетках и химически связанной воды.
Третий этап проводится при температурах от 170 до 300 °C и называется этапом предварительной карбонизации. На этом этапе выделяются пиролизные жидкости в форме метанола и уксусной кислоты, а также малое количество окиси и двуокиси углерода.
Четвертый этап выполняется при температурах от 200 до 300 °C, когда образуется основная часть легких смол и пиролизных кислот. В конце этого этапа образуется древесный уголь, являющийся результатом карбонизации древесных остатков.
На пятом этапе при температурах от 300 до максимальной 500 °C завершается выделение летучих компонентов и увеличивается содержание углерода в угле. [4] На шестом этапе полученный уголь охлаждают в течение, по крайней мере 24 часов, чтобы увеличить его устойчивость и снизить риск самопроизвольного возгорания.
Наконец, финальный этап заключается в извлечении угля, упаковке, транспортировке, оптовой и розничной продаже потребителям. [4–4]
Сжигание биомассы при температуре 900… 1 500 °C в присутствии воздуха или кислорода и воды с получением синтез-газа, состоящего из смеси монооксида углерода, водорода и стеклообразной массы (7… 10 % массы исходного материала), применяемой как наполнитель для дорожных покрытий. Газификация – более прогрессивный и экономичный способ использования биомассы для получения тепловой энергии, чем пиролиз. Синтез-газ имеет высокий КПД тепловой конверсии. Он может употребляться для получения метанола, этанола и углеводородов. [4–2].
Интерес к газификации вновь возрос во время энергетического кризиса 70-х годов, а затем упал вместе с снижением цен на нефть в 80х годах. По оценкам Мирового Банка (1989) всего лишь 1000–3000 газификаторов установлено в мире, преимущественно в Южной Америке для производства древесного угля. [4].
Газификация древесины.
Газификация древесины называется также газогенерацией или сухой перегонкой. Монооксид углерода, метиловый газ, метан, водород, газообразные углеводороды и другие компоненты в различных пропорциях могут быть получены с помощью нагрева или сжигания древесины в условиях отсутствия или недостатка кислорода. В разных процессах получаются разные продукты. Если при сжигании древесины обеспечить необходимое количество кислорода, то в процессе такого сжигания образуются двуокись углерода, вода, небольшое количество золы (соответствующее содержанию неорганических веществ) и тепло. Этот тип сжигания реализуется в обычных древесносжигающих печах. После начала процесса горения можно ограничить поступление воздуха. При этом горение будет продолжаться, но с частичным сгоранием. В случае полного сгорания углеводорода (древесина в основном состоит из углеводородов) кислород объединяется с углеродом, а также с водородом. В результате чего получаются CO2 (двуокись углерода) и H2O (вода). Ограниченное количество воздуха и тепло обеспечивают продолжение неполного сгорания. В этих условиях один атом кислорода объединяется с одним атомом углерода, в то время как водород взаимодействует с кислородом лишь частично. В результате получается монооксид углерода, вода и газообразный водород. Кроме того, образуются и другие компоненты, например, углерод в виде дыма. Под воздействием тепла разрываются химические связи в молекулах сложных углеводородов, содержащихся в древесине (а также в любом другом углеводородном топливе). Одновременно в процессе объединения атомов углерода и водорода с кислородом выделяется тепло. Таким образом, процесс поддерживает сам себя. Если количество воздуха недостаточно, то в результате такого процесса образуется достаточно тепла для разложения молекул древесины, но продуктами этого процесса будут монооксид углерода и водород – горючие газы. Другие продукты неполного сгорания – это преимущественно диоксид углерода и вода.[4–4].
В процессе возгонки древесины образуются метан, метиловый газ, водород, углекислый и угарный газы, древесный спирт, углерод, вода, а также многие малые добавки. Количество метана может достигать 75 %.[4–4].
При воздушной газификации производится генераторный газ (ГГ) с высшей тепотворной способностью 4…6 МДж/м3 (низкокалорийный газ). Этот газ можно сжигать в котлах, после очистки – в газовых двигателях или турбинах, но он не пригоден для транспортировки по рыбоводу, ввиду низкой энергетической плотности. Газификация с использованием кислорода дает средне-калорийный газ (10… 12 МДж/м3), пригодный для ограниченной транспортировки по трубопроводу и для использования в качестве синтез-газ с целью получения метанола и газолина. Среднекалорийный газ (15…20 МДж/м3) может быть получен также путем паровой (пиролитической) газификации. Это двухстадийный процесс, реализуемый в двух реакторах кипящего слоя. [5–5].
Основные технологии могут быть разделены на газификацию в плотном (неподвижном) слое с восходящим/ нисходящим/ поперечным движением газа, газификацию в кипящем слое (стационарный КС, ЦКС, два реактора КС) и газификацию в потоке. [5–5].
Особенностью реактора с НДГ – это движение газа вниз через опускающийся плотный слой сырья. Такая технология обеспечивает получение почти чистого генераторного газа с содержанием смол 50…500 мг/нм3. ГГ может использоваться в газодизельных электростанциях небольшой мощности. В гафикаторах плотного слоя с ВДГ биомасса, поступающая сверху вниз, сначала просушивается ГГ, который движется вверх. Затем твердое сырье пиролизируется с образованием углистого вещества, которое продолжает двигаться вниз и проходит стадию газификации. Парообразные продукты пиролиза уносятся вверх горячим ГГ. Смолы, содержащиеся в этих продуктах, конденсируются на холодном опускающемся сырье или уносятся из реактора произведенным газом. Таким образом, концентрация смол в генераторном газе увеличивается и может достигать 10…100 г/нм3. Ввиду значительного содержания смол, без дополнительной очистки газ может только сжигаться в котле, расположенном в непосредственной близости от установки. Газификаторы с ПДГ в работе во многом сходны с газификаторами с НДГ. Воздух или смесь воздуха с паром подводятся в реактор через боковую стенку в нижней части корпуса реактора. ГГ отводится из реактора с противоположной стороны. Широкого распространения газификаторы данной конструкции не получили. Отличительными особенностями газификаторов с КС по сравнению с реакторами плотного слоя являются высокие скорости тепло– и массопереноса и хорошее перемешивание твердой фазы, что обеспечивает высокие скорости реакции и близкую к постоянной температуру слоя. Частицы сырья должны быть более мелкими, чем при газификации в плотном слое, то есть необходимо дополнительное измельчение. Реакторы с КС – единственный вид газификаторов, работающих с изотермическим слоем сырья. Производится ГГ с содержанием смол 5…10 г/нм3, что является средним показателем между газификацией с ВДГ и НДГ. При газификации в ЦКС частицы, унесенные из реактора потоком газа, отделяются от ГГ в циклоне и возвращаются обратно в слой для увеличения степени конверсии углерода. Произведенный ГГ в большинстве коммерческих приложений используется для сжигания в котлах. Технология газификации биомассы в КС и ЦКС может быть реализована как при атмосферном, так и при высоком давлении. Преимущества этой технологии проявляются при использовании в крупных парогазотурбинных установках с внутрицикловой газификацией БМ. В этом случае не требуется дополнительного сжатия ГГ перед подачей в камеру сгорания газовой турбины. Установка с двумя реакторами КС позволяет получить ГГ с более высокой теплотворной способностью, чем в случае одного КС с воздушным дутьем. Первый реактор по своей функции близок к пиролизу. Теплота привносится в него горячим песком, циркулирующим между двумя ректорами. Смесь генераторного газа, густого вещества, золы и песка из газификатора поступает в циклон, где твердая фракция отделяется и попадает во второй реактор с КС (камеру сгорания). Углистое вещество сгорает, а нагретый песок возвращается в первый реактор. Произведенный генераторный газ имеет высокую теплотворную способность, однако содержит много смол, поскольку процесс конверсии сырья близок к пиролитическому. До настоящего времени имеется небольшой опыт работы с БМ в таких установках. Среди других видов реакторов можно выделить [4–5]:
• Реактор с движущимся слоем (горизонтальный слой, наклонный слой, многокамерная печь, печь со шнеком): механическое перемещение слоя сырья. Газификация в таком реакторе обычно является низкотемпературной.
• Вращающаяся печь: в основном используются для переработки отходов ввиду хорошего контакта газа и твердых частиц и хорошего перемешивания сырья. Необходима тщательно продуманная конструкция для избежания уноса твердых частиц.
• Циклонные и вихревые реакторы: высокие скорости движения частиц обеспечивают высокие скорости протекания реакций. Циклонные газификаторы отличаются простотой конструкции. Однако они лишь недавно стали применяться для конверсии биомассы, и технология еще не до конца отработана.
Правообладателям!
Данное произведение размещено по согласованию с ООО "ЛитРес" (20% исходного текста). Если размещение книги нарушает чьи-либо права, то сообщите об этом.Читателям!
Оплатили, но не знаете что делать дальше?