Текст книги "100 великих изобретений"
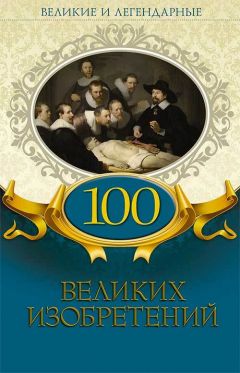
Автор книги: Коллектив авторов
Жанр: Прочая образовательная литература, Наука и Образование
Возрастные ограничения: +12
сообщить о неприемлемом содержимом
Текущая страница: 5 (всего у книги 25 страниц) [доступный отрывок для чтения: 8 страниц]
Ножницы. Булавки. Наперстки
Ножницы
В наше время ножницы являются одним из самых привычных и необходимых предметов быта. Но когда они появились впервые, неизвестно.
Очевидно, примерно в VIII в. какому-то ремесленнику пришла в голову идея соединить два режущих полотна с помощью стержня-заклепки. Так получились ножницы, практически не отличающиеся от современных. А в XV в. Леонардо да Винчи заново «изобрел» ножницы. Правда, гораздо раньше, еще в Древнем Риме, существовали так называемые «овечьи ножницы» (ими стригли овец, отсюда и название). Два лезвия соединялись подобно пинцету дугообразной пружинящей пластиной и сжимались рукой.
Ножницы изготавливали из стали, железа (стальные лезвия наваривали на железную основу), серебра, покрывали позолотой и богато украшали.
В наши дни существует множество видов ножниц: секаторы, с помощью которых стригут кусты на газонах, ножницы, с помощью которых разделывают птицу, режут торт, стригут шерсть овец, раскраивают ткани, прорезают петли и многие другие.
Булавки
Если вспомнить, насколько обширна сфера применения булавок, можно только удивиться тому, как раньше человек мог обходиться без них. Скорее всего, булавки той или иной формы, изготовленные из разных материалов, использовались человеком с древнейших времен.
Самым древним способом скрепления мягких деталей, по-видимому, были шипы растений. Неслучайно в некоторых языках слово «булавка» происходит от латинского слова, которое обозначает «шип» или «колючка». Затем человек начал мастерить подобные предметы из костей животных или рыб. Во времена неолита булавки делали из бронзы.
Неожиданным может показаться то, что так называемая английская булавка (как мы ее называем сейчас) была в ходу на территории нынешней Европы уже к концу Бронзового века, примерно за 1000 лет до н. э. Этот небольшой предмет изготавливали из бронзы и сгибали так, что кончик фиксировался головкой.
В Средние века булавки использовались как декоративный элемент богатой одежды, а уже позже, в эпоху их массового распространения, ими стали фиксировать детали одежды.
Первые булавки с одним концом, загнутым в колечко, появились во Франции примерно в конце XV в. Французы возили их на продажу в Англию, но вскоре и англичане научились делать булавки высокого качества. В то время они были такой ценностью, что набор булавок считался дорогим и важным подарком. В английском языке даже появилось выражение «деньги на булавки» ― карманные деньги на расходы.
Наперсток
История человечества – это история открытий, изобретений и находок, но имена подавляющего большинства изобретателей канули в Лету.
Наперсток – один из самых привычных портняжных предметов. Скорее всего, он появился, когда неизвестному портному надоело постоянно колоть пальцы булавками, и он задался целью придумать способ, как защитить руки.
В Средние века уже были известны мастера, занятые исключительно изготовлением наперстков, ― очевидно, этот предмет широко использовался. До нашего времени дошли настоящие шедевры – изящные наперстки, украшенные эмалью, инкрустацией и гравировкой. Многие старинные наперстки были сделаны из золота. Позже их стали делать из позолоченного серебра или бронзы, но цвет по традиции оставался желтым, поскольку на таком фоне было проще разглядеть движение острой серебристо-белой иглы.
В 1824 г. был изобретен универсальный станок для производства наперстков любого вида и размера. Открытие было запатентовано, и вскоре началось массовое производство этой чрезвычайно нужной вещицы.
В конце XIX в. наперстки стали такими популярными, что их продавали даже в качестве сувениров. Более того, их стали использовать в коммерческих целях: граверы наносили на них рекламные названия фирм и отдельных изделий.
Медь. Бронза. Латунь. Железо
Медь
Медь, скорее всего, была первым металлом, который обнаружили наши далекие предки. До III века до н. э. люди использовали в основном инструменты из камня. Их было тяжело делать, но служили они долго.
В поисках подходящих камней человек столкнулся с самородными медными рудами – медным колчеданом, медным блеском (халькозином) и купритом (красной медной рудой). Попробовав что-то сделать с рудой, мастера заметили, что, если обработать медь ударами каменного молота, она становится тверже. Так появился метод холодной обработки металла, или холодной ковки.
Позже было обнаружено другое интересное свойство руды. Если кусок руды случайно попадал в огонь, он расплавлялся и, остыв, приобретал другую форму. Сначала таким способом изготавливали украшения, а позже стали применять и для производства орудий труда. Со временем для обработки меди придумали специальные печи, которые напоминали гончарные.
Медь намного мягче камня, зато ее легче затачивать. Инструменты проще создавать из меди, чем из камня, который нужно долго оббивать и шлифовать. Поэтому спрос на металлические орудия все время возрастал.
В местах залежей медной руды возникло рудное и шахтное дело, которое развивалось очень быстро. Шахты укреплялись деревянными подпорками, создавалась система вентиляции, освещения, поднятия наверх добытой руды. Медь плавилась в небольших глиняных печах с толстыми стенками. Следующим этапом истории развития металлов стало открытие бронзы.
Бронза
Переход от каменных орудий труда к металлическим изменил и значительно ускорил технический прогресс человечества. Первым металлом, который получил широкое распространение, была медь. В условиях быстрого роста спроса на металлические инструменты человек начал «охотиться» за медной рудой, к тому же оказалось, что она встречается далеко не везде.
К открытию бронзы людей подтолкнул случай, который связан с особенностями обработки меди и производством из нее инструментов. Некоторые медные руды содержат небольшую примесь олова, буквально 2 %. Люди заметили, что медь, полученная из такой руды, намного тверже обычной. Тогда они принялись более пристально изучать характеристики олова и стали специально добавлять его к меди. Так получился первый искусственный сплав – бронза.
При нагревании медь, соединенная с оловом, лучше плавилась, из нее было проще отливать изделия, поскольку расплав был более текучим. Бронзовые инструменты оказались тверже медных, а кроме того, они хорошо и легко затачивались.
Использование бронзы повысило в несколько раз продуктивность труда во всех отраслях деятельности человека. Производить инструменты стало значительно проще. Мастерам не надо было ковать и затачивать, они просто наполняли специальные формы жидким металлом и получали качественный готовый продукт.
Техника литья совершенствовалась. Сначала отливку производили в открытых формах – глиняных или песчаных – это были просто углубления разной формы. Их сменили открытые формы, вырезанные из камня, которые можно было использовать многократно. Однако у открытых форм имелся существенный недостаток: при литье можно было получить только плоское изделие. Для отливки изделий сложной формы нужно было что-то придумывать.
Как мы уже неоднократно повторяли, человек не изобретал ненужного. Когда возникает необходимость – появляется новое изобретение. Таким изобретением в металлургии стали закрытые разъемные формы. Перед процессом литья половинки формы прочно соединялись между собой. Затем через специальное отверстие заливалась расплавленная бронза. Когда металл затвердевал и остывал, форму разбирали и получали готовое изделие. Такой способ позволял отливать изделия сложной формы, но для фигурного литья этого было недостаточно. Вскоре и эта проблема была решена.
Сначала стали изготавливать из воска точную модель будущего изделия, ее обмазывали глиной и обжигали в печи. Воск плавился и испарялся, а мастер получал точный слепок модели из глины. В полученную форму заливали бронзу. Когда бронза остывала, глиняную форму разбивали, чтобы извлечь готовое изделие. Этот способ называется литье по выплавляемым моделям.
Со временем были открыты новые приемы работы с металлами – волочение, клепка, пайка и сварка, дополнявшие ковку и литье.
С развитием металлургии бронзовые изделия начали вытеснять каменные. Конечно, это происходило постепенно. Руды цветных металлов имелись далеко не везде, а олово встречалось куда реже меди. Металлы приходилось перевозить на далекие расстояния, поэтому стоимость изготовленных из них инструментов была высокой. Следующим, вернее параллельным, этапом развития металлургии стало появление латуни.
Латунь
Латунь – это сплав меди с цинком, к которому иногда добавляют алюминий, олово, никель, свинец, марганец или железо. Температура плавления латуни колеблется от 880 до 950 °C в зависимости от состава. С увеличением содержания цинка температура плавления сплава снижается. За свой желтый цвет латунь получила название «поддельное золото».
Известно, что латунь издавна применяли в Индии, Китае, Греции и Риме. Этот металл, как считают ученые, впервые был получен римлянами в начале нашей эры. Для производства латуни цинк завозили из Индии и Китая, где его добывали. Уже самые первые образцы сплава показали его высокие технологические качества – он хорошо поддавался прокатке, сварке, полировке. По сравнению с медью, латунь более устойчива к атмосферному воздействию. Правда, на воздухе поверхность латуни чернеет, но чтобы этого не происходило, ее покрывают лаком.
Латунь – прекрасный материал, который в Средние века использовали для изготовления преимущественно мелких бытовых предметов, а позже стали широко применять в машиностроении.
В ювелирном деле используются четыре вида латунного сплава. Например, томпак – разновидность латуни с содержанием цинка не более 10 %. Этот сплав пластичен и слабо подвержен коррозии. Благодаря золотистому цвету он широко применяется для создания изысканных художественных изделий, знаков отличия, красивых сосудов и ювелирной галантереи.
Железо
Все медные сплавы были невероятным шагом вперед в развитии инструментов труда. Однако только с появлением железа произошла настоящая промышленная революция, превратившая кустарное ремесло в производство.
Свободное самородное железо в земной коре, в отличие от меди, почти не встречается, однако оно входит в состав многих минералов и распространено достаточно широко. В древности его добывали из озерных, болотистых, луговых и других руд. Металлургия железа является сложным процессом, более трудным, чем добыча меди. Однако не будь у человечества опыта в медной металлургии, железо и его сплавы так и не появились бы.
Температура плавления железа – 1539 °C. Древним мастерам такая высокая температура была совершенно недоступна. Поэтому железо вошло в обиход значительно позже меди. Широкое применение железа как материала для изготовления оружия и инструментов началось только в I тыс. до н. э., когда стал известен сыродутный способ восстановления железа.
Самые распространенные железные руды – это магнитный железняк, красный железняк и бурый железняк. Это все соединения железа с кислородом или гидраты окиси железа. Чтобы получить из них металлическое железо, нужно извлечь кислород из соли железа.
Древние мастера не были знакомы со сложными химическими процессами, происходящими при восстановлении железа, но, наблюдая за плавлением железной руды, они заметили важные закономерности, которые легли в основу простейших методов изготовления железа.
Первой закономерностью было то, что необязательно доводить руду до температуры плавления железа, чтобы получить нужный металл. Его можно получать и при низких температурах, но при этом необходимо использовать больше топлива, чем при выплавке меди, и оно должно быть лучшего качества. Нужно также, чтобы огонь был как можно более «горячим». Эти наблюдения потребовали создания печи с особым строением и со специальными условиями плавки.
Приступая к плавке железа, древние мастера выкапывали круглую яму, стенки которой обмазывали толстым слоем глины. С наружной стороны к яме подводили «тоннели», через которые нагнетался воздух. Затем сооружали верхнюю конусообразную часть печи. В качестве топлива использовали древесный уголь, который засыпали в яму. На уголь слоями укладывали шихту – измельченную руду и уголь. Затем сверху насыпали толстый слой угля.
Уголь внизу поджигали, и руда сильно нагревалась. Во время нагревания углерод в угле окислялся, и железо восстанавливалось. Тестообразное железо в виде мелких лепестков опускалось вниз, поскольку оно в три раза тяжелее шлака, и оседало в нижней части печи. На дне ямы собирался ком мягкого сварного железа – крица ― смесь мягкого металла с пустотами, заполненными твердыми шлаками. Когда «плавка» заканчивалась, печь разламывали и извлекали крицу.
Дальнейшая обработка крицы происходила в кузнице. Крицу снова разогревали в горне и обрабатывали ударами молота, чтобы удалить шлаки. После ковки железо приобретало качества, необходимые человеку.
В чистом виде железо использовать нельзя, поскольку оно слишком мягкое. Для производства необходим исключительно сплав железа с углеродом.
Если в металле содержится от 0,3 до 1,7 % углерода, то такой сплав называется сталью. Отличительной и важной особенностью этого сплава является его способность к закалке. Чтобы закалить, то есть придать дополнительную твердость, изготовленный инструмент нагревали докрасна, а затем охлаждали. Температура в печи при естественном притоке воздуха не поднималась выше 1000 °C. После закалки сталь становилась твердой, поэтому из нее производили качественные режущие инструменты.
Древние мастера заметили, что из руды можно получить большее количество железа отличного качества, если в печь с помощью мехов нагнетать воздух. Меха изготавливали из шкур и приводились в движение вручную. С помощью сопел и мехов в печь нагнетали сырой (не подогретый) воздух, поэтому процесс называли сыродутным. Однако и при этом способе температура в печи поднималась только до 1200 °C, и из руды добывалась в лучшем случае половина железа, содержащегося в ней.
Став дешевым материалом, железо достаточно быстро стало востребованным во многих отраслях производства. С появлением железного топора и сохи с железным лемехом появилась возможность расчистить и подготовить почву, ранее малопригодную для земледелия. Именно после возникновения железных инструментов земледелие превратилось в важнейшую отрасль производства у большинства народов.
Благодаря железу ремесленники обзавелись инструментами такой твердости и остроты, которым не могли противостоять ни камень, ни бронза. Качественные инструменты повлияли, в свою очередь, на развитие ремесел.
Металлургия. Получение литой стали, электролиз алюминия
Литье железа
На протяжении многих веков железо добывалось в сыродутных печах способом, открытым в глубокой древности, который описан выше. Пока не было недостатка в легкоплавких рудах, этот способ вполне удовлетворял потребности производства. Но в Средние века спрос на железо увеличился, поэтому приходилось использовать тугоплавкие руды. Чтобы извлечь железо из тугоплавкой руды, требовалась более высокая температура. В то время было известно только два способа повысить температуру: увеличить высоту печи или усилить дутье.
К XIII в. сыродутная печь трансформировалась в более высокую и усовершенствованную плавильную печь, которая называлась штукофеном («печь, изготавливающая крицу»). Штукофены были первым шагом на пути к созданию доменной печи.
Первые штукофены появились в Штирии, богатой железом, затем в Чехии и других горнопромышленных районах. В таких печах уже можно было достигать более высокой температуры и обрабатывать тугоплавкие руды. Шахта штукофена имела форму двойного усеченного конуса, сужающегося к колошнику (верхней открытой части печи, через которую порциями ― колошами ― загружали руду и уголь) и ко дну.
В стенке было сделано одно отверстие – для фурмы (трубы, через которую в печь с помощью мехов нагнетался воздух) и для последующего извлечения крицы. В штукофенах процесс образования железа проходил так же, как в сыродутных печах, но был и заметный прогресс: закрытая шахта хорошо сохраняла тепло, а благодаря высоте (до 3,5 м) плавка шла равномернее, медленнее и полнее, добывалось больше железа. В штукофенах производилось сразу три вида железного сырья: чугун, стекавший вместе со шлаком, ковкое железо в крицах и сталь, тонким слоем покрывавшая крицу.
Количество углерода в сплавах железа варьируется незначительно, но железо, сталь и чугун по своим свойствам заметно отличаются друг от друга. Железо – это мягкий металл, хорошо поддающийся ковке. Сталь – очень твердый материал, прекрасно подходящий для изготовления режущих инструментов. Чугун твердый и хрупкий, совершенно не поддается ковке. Количество углерода заметно влияет и на другие свойства сплавов ― чем больше его в сплаве, тем металл более легкоплавкий. Чистое железо – тугоплавкий металл, а чугун плавится при гораздо более низких температурах.
Однако штукофен подходил не для всех видов тугоплавких руд. Требовалось более сильное дутье. Для приведения в действие мехов стали использовать водяное колесо. На вал водяного колеса вразбивку сажали кулачки, которые оттягивали крышки клинчатых кожаных мехов. В каждой плавильной печи имелось два меха, работавших попеременно.
К концу XIV в. появились гидравлические двигатели и меха. Известно, что уже в XV в. многие плавильни перемещались с гор и холмов в долины и на берега рек. Это было крупнейшим сдвигом в технике металлургии, который привел к открытию литейных и переделочных свойств чугуна.
Увеличение силы дутья повлияло на весь процесс. Теперь в печи развивалась настолько высокая температура, что восстановление металла из руды происходило до того, как образовывался шлак. Железо сплавлялось с углеродом и превращалось в полностью расплавленную массу ― чугун – материал с более низкой температурой плавления. Поначалу качества чугуна не были оценены по достоинству. Застывший чугун был лишен природных свойств железа – он не ковался, не сваривался, из него нельзя было сделать прочных инструментов, гибкого и острого оружия. Поэтому чугун долгое время считали отходом производства. Но избавляться от него не спешили – при восстановлении железа из тугоплавких руд немалая его часть оставалась в чугуне.
Со временем «негодный» чугун стали выбирать из остывшего шлака и пускать во вторую переплавку, добавляя его к руде или самостоятельно. Во время переплавки чугуна оказалось, что этот материал легко плавится в горне и после усиленного дутья легко превращается в кричное железо, которое по своему качеству превосходит то железо, получаемое из руды.
Поскольку чугун плавится при более низкой температуре, чем железо, процесс требовал меньше топлива и занимал мало времени. Так в XV в. было сделано величайшее открытие металлургии – переделочный процесс. Широкое распространение он получил уже в XVI в., когда повсеместно стали применять доменные печи.
У чугуна оказались и другие положительные свойства. Твердую крицу нелегко было достать из печи. На это уходило немало времени, печь при этом остывала, а для ее разогрева требовались дополнительное топливо и время. Оказалось, что проще выпускать из печи расплавленный чугун. Печь не остывала, и ее можно было сразу загружать новой порцией руды и угля. Так металлургический процесс стал непрерывным.
Чугун обладает прекрасными литейными качествами. Особенно широко он применялся в артиллерии: из него сначала отливали ядра, а затем и отдельные детали пушек. Правда, до конца XV в. чугун был неоднородным, недостаточно жидким и со следами шлака, поэтому из него производили грубые и незатейливые изделия: печные котлы, молоты, надгробия.
Литье чугуна требовало изменений в устройстве печи, поэтому были созданы так называемые блауофены (поддувные печи). Это явилось еще одним шагом к созданию доменной печи. Блауофены были выше, чем штукофены, ― 5―6 м, а процесс плавки в них мог быть непрерывным при очень высокой температуре. Чуть позже появилась идея разделить процесс восстановления железа на два этапа: в одной печи непрерывно выплавляли чугун, а в другой – этот чугун переплавляли в железо.
Когда плавка железа заканчивалась, шлак выпускали через отверстие ниже фурмы. После охлаждения его измельчали и отделяли чугун. Крицу извлекали клещами и ломом, а затем обрабатывали молотом. Наиболее крупные крицы весили до 40 пудов (около 650 кг). Кроме того, из печи вынимали до 20 пудов (330 кг) чугуна. Одна плавка длилась 15 часов. На извлечение крицы требовалось 3 часа, на подготовку печи к плавке – до 5 часов.
Наконец, был организован двухступенчатый процесс плавки. Блауофены после усовершенствования превратились в печи нового типа – доменные, которые предназначалась только для получения чугуна. Вместе с ними было окончательно признано преимущество переделочного процесса. Сыродутный процесс остался в прошлом.
Принцип действия доменной печи подобен тому, который применяли в блауофенах. Первый шаг: из руды выплавляли чугун. Второй шаг: при вторичной переплавке чугуна получали железо. Первая стадия получила название доменного процесса, вторая – кричного передела.
Первые домны появились в Зигерланде (Вестфалия) во второй половине XV в. От блауофенов они отличались большей высотой шахты, более сильным воздуходувным аппаратом и увеличенным объемом верхней части шахты.
В домнах достигалась значительно более высокая температура, что гарантировало более длительную, ровную плавку руды. Сначала строили домны с «закрытой грудью», но вскоре открыли переднюю стенку и расширили горн. Доменная печь высотой 4,5 м могла давать до 1600 кг чугуна в день.
Перерабатывали чугун в железо в кричном горне – устройстве, сходном с сыродутной печью. Передел начинался с загрузки древесного угля и подачи дутья. После того как древесный уголь вблизи сопла разгорался, добавляли чугунные чушки. Чугун плавился под действием высокой температуры, стекал вниз и терял часть углерода. Далее металл загустевал и переходил из расплавленного состояния в тестообразную массу малоуглеродистого железа. Эту массу ломами поднимали к соплу. Здесь происходило дальнейшее выгорание углерода, осевший на дно горна металл был мягким, легко сваривающимся. Постепенно на дне образовывался ком крицы, который извлекали из горна и ковали под молотом для уплотнения и выдавливания жидкого шлака. Весь процесс занимал 1–2 часа. В кричном горне можно было получить около 1 т металла в сутки, выход готового кричного железа составлял 90–92 % веса чугуна. При этом качество кричного железа было гораздо выше сыродутного.
Переход к двухступенчатому (доменному и кричному) процессу позволил значительно повысить производительность труда. Но вскоре металлургия столкнулась с новыми затруднениями: для выплавка железа требовалось огромное количество топлива.
За несколько веков в Европе было уничтожено тысячи гектаров леса. Некоторые государства приняли законы, запрещавшие бесконтрольную рубку. Особенно остро этот вопрос стоял в Англии. Из-за нехватки древесного угля англичане вынуждены были ввозить часть железа из-за границы.
В 1619 г. для плавки железа впервые был применен каменный уголь. Правда, широкое применение каменного угля тормозилось присутствием в нем серы. Очищать каменный уголь от серы научились только в 1681 г. В 1735 г. инженер-металлург Авраам Дерби впервые использовал для доменной печи кокс. Новый период в коксовой металлургии начался, когда в 1785 г. англичанин Джон Вилкинс установил на своем заводе первую паровую машину двойного действия, которая работала на коксовом угле. После этого в металлургии коксовый уголь полностью вытеснил каменный.
Литая сталь
О двух первых этапах в истории процесса получения железа мы только что рассказали. Последний и революционный этап приходится на вторую половину XIX в. – зарождение производства литой стали.
Сталь во все времена оставалась самым необходимым и желанным материалом в металлургии, потому что она обладает той твердостью и крепостью, которая требуется для изготовления инструментов, оружия и деталей машин.
Производство мягкого железа и ковка долгое время тормозили развитие процесса обработки железа, поскольку на это уходило слишком много сил и времени. Проблема возникла в XIX в., когда резко возросли потребности в дешевой стали.
Английский изобретатель Генри Бессемер высказал идею о том, что необходимо придумать способ получения жидкого металла со свойствами железа и стали. Многие ученые начали работать над реализацией этой мысли. На решение поставленной задачи ушло нескольких десятилетий упорного труда многих металлургов. Было сделано несколько важных открытий и изобретений, каждое из которых сыграло свою роль в истории обработки железа.
До конца XVIII в. передел чугуна в мягкое ковкое железо выполняли в кричных горнах. Однако этот способ был недостаточно выгодным и эффективным. Во-первых, металл, который добывали в кричных горнах, был неоднородным, по своим качественным характеристикам он занимал промежуточное положение между ковким железом и сталью. Во-вторых, к углю, который использовался в процессе переработки, предъявлялись очень высокие требования, так как любые примеси в его составе влияли на качество конечного продукта. В-третьих, расход угля был очень велик: на восстановление 1 кг железа уходило приблизительно 4 кг угля. В крупных горнах за сутки можно было получить не более 400 кг железа. Между тем рынок требовал все больше железа и стали.
Значительным шагом на пути к созданию более совершенного способа переделки чугуна стал процесс пудлингования в специально созданной печи, который изобрел Генри Корт в 1784 г.
Принципиальное отличие пудлинговой печи от кричного горна состояло в следующем. Продукты горения через каменный порог попадали в рабочее пространство печи, где на поду находился загруженный чугун с железистыми шлаками. Шлаки под действием пламени переходили в тестообразное состояние и частично расплавлялись. С повышением температуры начинал плавиться чугун, а его примеси выгорали за счет кислорода, заключенного в шлаках. Таким образом чугун освобождался от углерода, то есть превращался в крицу губчатого железа.
В качестве горючего для пудлинговой печи можно было использовать любое топливо, даже дешевый неочищенный каменный уголь. Это обстоятельство было значительным преимуществом по сравнению с кричным горном. Также пудлинговая печь отличалась гораздо большим объемом. Кроме того, конструкция Корта не требовала принудительного вдувания: доступ воздуха и хорошая тяга достигались благодаря высокой трубе.
Однако у пудлинговой печи был и существенный недостаток. В этом устройстве воздух обдувал только верхнюю часть чугуна. Чтобы восстановление железа шло равномерно и охватывало весь объем обрабатываемой массы, приходилось периодически открывать печь и перемешивать чугун, а это уже тяжелый ручной труд. Это обстоятельство не позволяло увеличить размер печи – ведь сила человека ограниченна.
Благодаря изобретению Генри Корта процесс производства железа стал значительно дешевле. Пудлинговые печи широко использовались на металлургических заводах того времени. Но к середине XIX в. они перестали удовлетворять потребности промышленности. Чтобы увеличить производительность, приходилось на каждую большую домну строить несколько печей: в среднем одну домну обслуживало десять пудлинговых печей. Это усложняло производство и делало его более дорогим.
Первым эту задачу удалось разрешить инженеру Генри Бессемеру. Он искал способ производства высококачественной литой стали, из которой можно было бы отливать пушки. В 1856 г. Бессемер продемонстрировал новое изобретение – неподвижный конвертер для переработки жидкого чугуна в сталь. Это была невысокая вертикальная печь, сверху закрытая сводом с отверстием для выхода газов. Сбоку в печи располагалось второе отверстие ― для заливки чугуна. Готовую сталь выпускали через отверстие в нижней части печи. Во время работы конвертера отверстие забивали глиной. Воздуходувные трубки (фурмы) располагались возле самого пода печи. Конвертер был неподвижным, поэтому продувку начинали до того, как вливали чугун, и продолжали до тех пор, пока весь металл не был выпущен, чтобы металл не залил фурмы. Процесс переработки чугуна в неподвижном контейнере длился не более 20 минут, малейшая задержка приводила к получению бракованного металла.
Недостатки неподвижного конвертера заставили Бессемера изобрести вращающуюся печь. В 1860 г. он оформил патент на новую конструкцию – поворотный конвертер, который остался практически без изменений до нашего времени.
Способ Бессемера был настоящей революцией в металлургии. За 8—10 минут конвертер превращал 10–15 т чугуна в ковкое железо или сталь. Прежде на это требовалось несколько дней работы пудлинговой печи или несколько месяцев работы кричного горна.
Бессемеровский метод попробовали применить в промышленности, но его результаты оказались хуже, чем в лаборатории, сталь получалась очень низкого качества. Через два года Бессемер выяснил причину плохих результатов. Оказалось, что он проводил свои опыты с чугуном, который содержал мало фосфора, а в Англии использовали чугун, выплавленный из железных руд с высоким содержанием фосфора. Фосфор и сера не успевали выгореть вместе с другими примесями – из чугуна они попадали в сталь и существенно снижали ее качество. Куда шире поворотные конвертеры распространились в Германии и США, где использовались другие руды.
Наряду с бессемеровским способом огромную роль вскоре приобрел мартеновский метод, согласно которому в специальной регенеративной печи чугун сплавляли с железным ломом.
Регенеративная печь была придумана и построена в 1861 г. немецкими инженерами Фридрихом и Вильямом Сименсами для стекольной промышленности, но быстро нашла применение и в металлургии. В регенеративной печи в результате правильно организованного теплообмена температура поднималась до 1600 °C, превышая температуру плавки безуглеродистого железа.
Создание высокотемпературных печей открыло новые горизонты перед металлургией, ведь уже в середине XIX в. во многих промышленных странах накопились немалые запасы железного лома. Его не могли использовать в производстве из-за высокой тугоплавкости. Французские инженеры, отец и сын Эмиль и Пьер Мартены, предложили сплавлять этот лом с чугуном в регенеративной печи Сименсов и таким образом получать сталь. В 1864 г. прошла первая успешная плавка.
Мартеновские печи были дешевле конвертеров, но ни бессемеровский, ни мартеновский способ не позволяли получать высококачественную сталь из руд, содержащих серу и фосфор. Эта проблема оставалась неразрешенной до 1878 г., когда английский металлург Сидней Томас добавил в конвертер известь. Шлаки, которые образовывались при этом, удерживали фосфор, и он выгорал вместе с другими примесями, а чугун превращался в высококачественную сталь. Теперь можно было производить сталь и из фосфоросодержащих европейских руд.
Правообладателям!
Данное произведение размещено по согласованию с ООО "ЛитРес" (20% исходного текста). Если размещение книги нарушает чьи-либо права, то сообщите об этом.Читателям!
Оплатили, но не знаете что делать дальше?