Текст книги "Современные отделочные и облицовочные материалы. Практический справочник для строительства и ремонта домов и квартир"
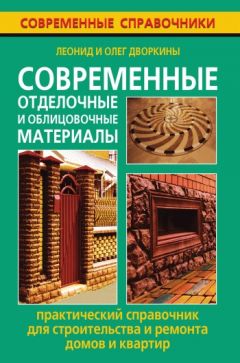
Автор книги: Леонид Дворкин
Жанр: Справочники
Возрастные ограничения: +12
сообщить о неприемлемом содержимом
Текущая страница: 5 (всего у книги 20 страниц) [доступный отрывок для чтения: 7 страниц]
Глава 4
Растворы и бетоны
4.1. Общие сведения
Отделочные растворы и бетоны применяют для архитектурного оформления элементов зданий и сооружений, штукатурных покрытий стен, устройства полов, крепления облицовочных материалов.
В зависимости от состава применяемых растворов штукатурки бывают обычными, специальными и декоративными.
Обычной штукатуркой отделывают внутренние помещения домов и фасады. Она бывает трех видов: простая, улучшенная и высококачественная.
Простая штукатурка состоит из одного слоя набрызга и одного слоя грунта. Ее применяют для оштукатуривания вспомогательных и складских помещений, временных и некоторых производственных сооружений.
Улучшенная штукатурка, кроме слоев набрызга и грунта, включает покровный слой. Ее применяют для оштукатуривания жилых, производственных и общественных зданий и сооружений.
Высококачественная штукатурка состоит из одного слоя набрызга, нескольких слоев грунта и покровного слоя. Ее применяют в случае повышенных требований к отделке жилых и общественных зданий.
Основные свойства растворных смесей – удобоукладываемость и водоудерживающая способность, а затвердевших растворов – прочность при сжатии и морозостойкость.
К штукатурным растворам специального назначения относят гидроизоляционные, акустические, теплоизоляционные, рентгенозащитные и другие растворы.
Декоративные бетоны и растворы изготавливают, применяя белые и цветные вяжущие и заполнители, а также пигментированные смеси. Вяжущими для декоративных бетонов и растворов могут быть обычные, белые и цветные цементы, известь, гипс, магнезиальные вяжущие, жидкое стекло, а также синтетические полимеры.
Для получения заполнителей применяют щебень и песок, добываемые путем измельчением мрамора, гранита, кварцита, туфа и других декоративных горных пород, природных и искусственных пористых материалов с коэффициентом размягчения не менее 0,8. В качестве наполнителей применяют тонкомолотые кварцевые пески, маршаллит, каменную муку и т. п.
Для светлых облицовочных покрытий в декоративные бетоны и растворы как заполнители вводят известняк и доломиты. Они значительно дешевле щебня и песка из мрамора и других декоративных пород, имеют хорошее сцепление с цементным камнем. Зерновой состав смеси декоративных мелких и крупных заполнителей зависит от желаемой фактуры обработки. Максимальную крупность заполнителей для декоративных бетонов и растворов выбирают в зависимости от толщины конструкций или лицевого слоя; она может колебаться от 5 до 40 мм.
Прочность крупного заполнителя для декоративных бетонов не должна быть менее 40 МПа, водопоглощение – не более 4 % по массе, а его морозостойкость должна обеспечивать морозостойкость бетона не ниже проектной.
Цветные декоративные растворы разделяют на известково-песчаные, терразитовые, камневидные. Терразитовые растворы отличаются тем, что изготовляются из сухой цветной смеси вяжущих, пигментов, заполнителей и мелких чешуек слюды. Камневидными растворами имитируют в штукатурных покрытиях разнообразные горные породы. Они состоят преимущественно из белого или цветного цемента (иногда добавляется до 5 % известкового теста), крошки из различных горных пород, пигментов.
Разновидностью декоративной обработки посредством цементно– или известково-песчаных растворов является обработка сграффито, получаемая нанесением двух или более различных по цвету слоев с последующим процарапыванием их по рисунку; последний наносят с помощью трафарета.
В настоящее время широкое распространение получили тонкослойные декоративные штукатурки с применением акриловых и других полимеров.
Для изготовления искусственного мрамора, имитирующего природный, гипсовые вяжущие окрашивают и насыщают уплотняющими добавками (животным клеем, квасцами и т. п.), после затвердения шлифуют и полируют, подбирая цвета основного фона и прожилок.
К разновидностям цветных бетонов и растворов относят мозаичные бетоны и растворы, в которых заполнителями являются крошка и песок из декоративных горных пород. Их чаще всего используют для устройства полов в зданиях гражданского и промышленного назначения. Каменную крошку для мозаичных бетонов и растворов изготовляют из полируемых пород камня с прочностью при сжатии, как правило, не менее 60 МПа. Преимущественно используют крошку мрамора или мраморовидного известняка.
Мозаичные покрытия из бетонов и растворов с мраморной крошкой во время эксплуатации истираются более равномерно, чем покрытия с крошкой из более твердых пород камня, например гранита. Мозаичные полы при обеспечении необходимой прочности, зернового состава заполнителей и контрастности долговечны, мало истираются, имеют хорошие декоративные свойства, гигиеничны, не нуждаются в сложном уходе.
Для устройства теплого покрытия пола в помещениях, испытывающих систематическое увлажнение, действие агрессивных реагентов (кислот, сахара, веществ брожения и т. п.), значительные удары и нагревание до температуры свыше 35 °C, применяют ксилолитовые растворы – смеси каустического магнезита или доломита с опилками на водном растворе хлорида магния. Ксилолит можно использовать и в виде растворной смеси, и в виде готовых плит.
Улучшенные декоративные свойства, низкую истираемость, высокую прочность при растяжении и изгибе, повышенную адгезию к различным основаниям имеют полимерцементные мастики, растворы и бетоны. Их изготовляют из смеси полимерцементного вяжущего (портландцемента и пластифицированной поливинилацетатной дисперсии или латекса), наполнителей, заполнителей, пигментов и воды.
Полимерцементные смеси применяют для устройства полов в помещениях с интенсивным движением людей (вестибюли зрелищных сооружений, магазины), а также транспортных средств на резиновых шинах.
Полимерцементные растворы используют также для наклеивания различных облицовочных материалов, штукатурных покрытий, отделки фасадной поверхности элементов сооружений после их термообработки.
Декоративной выразительности конструкций, в особенности при заводском изготовлении, можно достичь фактурной обработкой. Для этого применяют полусухую набивку-укладку на поддон формы лицевого слоя декоративного бетона или раствора полусухой консистенции; обнажение зерен декоративного заполнителя различными способами (табл. 4.1); присыпку крошки с накатыванием ее на поверхность изделий с мелкозернистым заполнителем.
Таблица 4.1. Способы обнажения крупного заполнителя при фактурной обработке конструкций

К распространенным способам обнажения заполнителя принадлежит химический, применяемый при формовании изделий прежде всего «лицом вниз». Суть способа состоит в удалении с поверхности отделочного слоя, прошедшего обработку горячим паром, а также незатвердевшего или ослабленного цементного раствора. Чтобы замедлить твердение и уменьшить прочность поверхностного отделочного слоя, используют специальные смеси (табл. 4.2), которые наносят или на поддон формы, или на свежеуложенный бетон.
Таблица 4.2. Составы смазок, %, замедляющих твердение цементных бетонов и растворов

Чаще всего заполнитель обнажают на глубину 1/3… 1/2 его максимального диаметра. Наилучшего эффекта достигают, используя бумагу или ткань, насыщенные замедлителями твердения (сульфитным щелоком, смесью декстрина и технического сахара и т. п.). Необходимый рисунок поверхности бетона получают накатыванием валиком, рельефными матрицами и т. п. В затвердевшем состоянии бетонные поверхности обрабатывают электромеханическим инструментом, газовыми горелками и т. д.
4.2. Растворы для обычных штукатурок
Растворы для обычных штукатурок подразделяют на цементные, известковые, цементно-известковые, цементно-глиняные, гипсовые, известково-гипсовые, глиняные, глино-известковые.
Цементные растворы применяют для внешних штукатурок с систематическим увлажнением и внутренних штукатурок в помещениях с относительной влажностью воздуха свыше 60 %. Для повышения водостойкости цементных растворов желательно применять гидрофобизирующие добавки, например кремнийорганические жидкости (ГКЖ-10, ГКЖ-11 в количестве 0,05… 0,2 % массы цемента). Ориентировочные соотношения цемента и песка по объему: для набрызга– 1:2,5:4; грунта– 1:2:3; покровного слоя – 1:1:1,5.
Цементно-известковые растворы применяют для оштукатуривания как фасадов зданий, так и внутренних помещений с любой относительной влажностью воздуха. Введение извести резко повышает пластичность растворов. Расход известкового теста зависит от назначения слоя. Для набрызга вводят обычно 0,5… 0,7, для грунта – 0,7… 1, покровного слоя 1… 1,5 объемных частей извести. Изготавливают цементно-известковые растворы двумя способами: 1) сухую песчано-цементную смесь увлажняют известковым молоком до необходимой подвижности; 2) добавляют цемент в известково-песчаный раствор.
Для внешней штукатурки стен сооружений, которые систематически не увлажняются, а также для внутренней штукатурки стен, перегородок и перекрытий с относительной влажностью воздуха помещений до 60 % вместо цементно-известковых можно применять цементно-глиняные растворы. При этом дозировка глины в виде теста должна соответствовать глубине погружения стандартного конуса 13… 14 см. Отношение объема глиняного теста к объему цемента не должно превышать 1,5… 1.
Растворы на основе воздушной извести (известковыерастворы) применяют для оштукатуривания поверхности внутри помещений с относительной влажностью воздуха до 60 %. Их можно использовать также для внешних штукатурок, которые не увлажняются систематически. В этих растворах на одну объемную часть известкового теста плотностью 1400 кг/м3 приходится разное количество объемных частей песка: для набрызга – 2,5… 4, для грунта – 2… 3 и для покровного слоя – 1… 2 части. Известь лучше вводить в раствор в виде известкового молока. Главный недостаток известковых растворов – медленное твердение. Процесс твердения ускоряют, добавляя строительный гипс. Обычно рекомендуют следующий состав известково-гипсовых растворов, частей по объему: для набрызга – 1:(0,3… 1):(2… 3), грунта – 1:(0,5… 1,5):(1,5… 3) и покровного слоя – 1:(1… 1,5).
Известково-гипсовые растворы удобнее всего использовать для оштукатуривания деревянных поверхностей внутри помещений. Для повышения их водостойкости в раствор вводят гидравлические добавки – трепел, диатомит, шлаки, золы ТЭС и т. п.
Гипсовые растворы применяют для внутренних отделочных работ в помещениях с относительной влажностью до 60 %. Применение гипсовых штукатурок позволяет поддерживать в зданиях необходимый микроклимат, исключает или минимизирует шпатлевочные работы. Гипсовые штукатурки обеспечивают высокую адгезию с декоративными материалами, имеют повышенную трещиностойкость. Для замедления схватывания в гипсовые растворы вводят добавки-замедлители (мездровый и костный клей, известь, квасцы, буру, лимонную кислоту и др.), увеличивающие жизнеспособность растворов до 1,5 ч.
Глиняные и глино-известковые растворы используют для внешней и внутренней штукатурки деревянных и каменных стен, а также перегородок при эксплуатации сооружений в сухом климате с относительной влажностью воздуха внутри помещений до 60 %. Соотношение глиняного теста и песка по объему колеблется от 2,5 до 5 и зависит от жирности глины. К жирным принадлежат глины с содержанием песка до 5 % и плотностью теста 1300… 1400 кг/м3, нормальным – соответственно 15 % и 1400… 1500 кг/м3, тощим (суглинкам) – до 30 % и 1500… 1600 кг/м3.
Рекомендации по выбору вяжущих материалов для обычных штукатурных растворов приведены в табл. 4.3, а технические требования к основным вяжущим, используемым для изготовления растворов, приведены в табл. 4.4… 4.6.
Таблица 4.3. Рекомендации по выбору вяжущих материалов для штукатурных растворов

Как заполнители для штукатурных растворов применяют кварцевые или полевошпатные пески, а также измельченные пески из плотных и пористых пород и искусственных материалов (пемзовые, керамзитовые, перлитовые и т. п.).
В растворных смесях для обычных штукатурок используют песок с наибольшим размером зерен 2,5 мм для подготовительных слоев (набрызга и грунта) и 1,2 мм для отделочного слоя (покрывки).
Как добавки в растворах применяют неорганические и органические пластификаторы, микронаполнители, ускорители твердения, замедлители схватывания и др.
Таблица 4.4. Требования к прочности портландцементов общестроительного назначения

Примечание. «Р» – быстротвердеющий цемент.
Таблица 4.5. Марки гипсовых вяжущих

Таблица 4.6. Технические требования к строительной воздушной извести

Примечание. В скобках приведено содержание MgO для доломитовой извести.
Цементы общестроительного назначения изготавливают 5 типов:
• тип I – портландцемент (от 0 до 5 % минеральных добавок) марок 300, 400, 500, 550, 600;
• тип II – портландцемент с добавками (от 6 до 35 % минеральных добавок) марок 300, 400, 500;
• тип III – шлакопортландцемент (от 36 до 80 % доменного гранулированного шлака) марок 300, 400, 500;
• тип IV – пуццолановый цемент (от 21 до 55 % минеральных добавок) марок 300, 400, 500;
• тип V – композиционный цемент (от 36 до 80 % минеральных добавок) марок 300, 400, 500.
При нормировании прочности в двухсуточном возрасте цементы относятся к быстротвердеющим.
При условном обозначении указывают тип цемента и его марку. Вводят дополнительные обозначения для быстротвердеющего (Р), пластифицированного (Пл), гидрофобизированного цемента (Гф), а также цемента, полученного из клинкера с нормированным минералогическим составом (Н).
Портландцемент I типа содержит 95… 100 % клинкера без учета добавки гипса, вводимого для регулирования сроков схватывания. В него, как и в цементы других типов, можно вводить до 5 % дополнительных добавок для интенсификации помола (ускорители твердения, пластификаторы, другие регуляторы свойств цемента). Цемент I типа используется в основном для бетонов с высокой морозостойкостью (при строительстве цементобетонных покрытий дорог, изготовлении железобетонных труб, шпал, опор, линий электропередач и др.).
Наиболее распространенными в строительстве являются портландцементы II типа. Их различают по виду добавки, указываемой при условном обозначении цемента: с добавкой шлака (Ш), пуццоланы (П), золы-уноса (3), известняка (И) и композиций добавок (К). Добавка известняка в отличие от активных минеральных добавок не взаимодействует с Са(ОН)2, но образует комплексные соединения – гидрокарбоалюминаты и способствует кристаллизации гидратных новообразований. Добавки пуццоланы, золы-уноса, а также известняка вводятся в портландцемент в количестве не более 20 %. При этом содержание пуццолановых добавок осадочного происхождения не может превышать 10 %.
Цементы II типа со шлаковой или композиционной добавкой дополнительно подразделяют на группы А и Б. Портландцемент группы А содержит 6… 20 % добавок, группы Б – 21… 35 %. При введении в композицию добавок пуццоланы или известняка их количество не может превышать 20 %.
Шлакопортландцементы (ШПЦ) и пуццолановые цементы (ППЦ) также изготавливают двух групп. В ШПЦ группы А вводят 35… 65 % доменного гранулированного шлака, группы Б – 65… 80 %. Пуццолановые цементы группы А содержат 21… 35 % пуццолановой добавки, включая и золу-унос, группы Б – 35… 55 %.
В композиционные цементы (тип V) наряду с другими возможными минеральными добавками обязательно вводится доменный гранулированный шлак. Цементы этого типа группы А содержат 36… 60 % композиции добавок, группы Б – 61… 80 %.
Добавка шлака в цементах группы А составляет 18… 40 %, группы Б – 41… 60 %.
При необходимости в цементы всех типов могут быть введены пластифицирующие и гидрофобизирующие поверхностно-активные вещества (ПАВ) в количестве не более 0,3 % от массы цемента в пересчете на сухое вещество добавки.
Все виды штукатурных растворов должны иметь необходимую подвижность, не отслаиваться во время оштукатуривания, соответствовать требованиям механизированного производства работ, обеспечивать хорошее сцепление с основанием.
Для изготовления штукатурных растворов, подачи их к рабочему месту и нанесения на поверхность используют комплекты машин, штукатурные агрегаты и штукатурные станции.
Подвижность растворной смеси выбирают в зависимости от размещения слоя в штукатурном покрытии и способа нанесения (табл. 4.7). Для набрызга используют наиболее подвижный раствор, хорошо заполняющий все неровности поверхности и содержащий в себе избыточное количество воды, поглощаемой основанием.
Таблица 4.7. Подвижность штукатурных растворов

Слои грунта наносят из относительно вязкого раствора для образования необходимой толщины штукатурки. Раствор для отделочного, или покровного, слоя имеет консистенцию, дающую возможность хорошо выравнивать грунт и заглаживать его поверхность. От вида штукатурного слоя зависит также предельная крупность песка. Для набрызга и грунта она составляет 2,5 мм, для покровного слоя – 1,2 мм. Штукатурные растворы для нижних слоев процеживают сквозь сетку 3×3 мм, для отделочного слоя – 1,5×1,5 мм.
Ориентировочные составы растворов различных видов приведены в табл. 4.8–4.11.
Указанные составы цементно-известковых и известковых растворов рассчитаны на плотность известкового теста 1400 кг/м3. Если используют известь с другой плотностью, количество ее определяют путем умножения расчетного объема теста с ρ0 = 1400 кг/г3 на коэффициент Кизв. (табл. 4.12).
Глину применяют в виде теста или порошка грубого помола. Подвижность теста может составлять 13… 14 см. При использовании глиняного порошка из «тощей» глины его количество соответствует количеству глиняного теста, количество порошка из средней глины уменьшается на 15 %, а из жирной – на 25 % по сравнению с расчетным объемом теста.
Изготовить легкоукладываемые растворы можно, если частично или полностью заменить известковое тесто органическими пластификаторами.
Таблица 4.8. Составы штукатурных растворов в объемных частях

Примечание. Деревянные и гипсовые поверхности оштукатуривают преимущественно известково-гипсовыми растворами.
Таблица 4.9. Составы глиняных и глино-известковых растворов в объемных частях

Таблица 4.10. Составы цементно-известковых растворов в объемных частях

Таблица 4.11. Составы цементно-глиняных растворов в объемных частях

Таблица 4.12. Коэффициент Кизв. для известкового теста различной плотности

Органические пластификаторы вводят в растворные смеси в количестве 0,03… 0,3 % массы цемента. Нужное количество органических пластификаторов определяют экспериментально; при этом плотность раствора не должна уменьшаться больше чем на 6 % по сравнению с раствором без органического пластификатора. Зола-унос, используемая в строительных растворах, должна отвечать требованиям ГОСТ 25818-91.
Золу-унос рекомендуется использовать в цементных, цементно-известковых и известковых растворах. Зола в растворах играет роль активной минеральной добавки, пластификатора и микронаполнителя, улучшая структуру и качество растворов (пластичность, водоудерживающую способность и прочность).
С применением золы-уноса можно получить растворы марок (по прочности при сжатии) 4, 10, 25, 50, 75, 100, 150.
Содержание золы в цементных и цементно-известковых растворах на портландцементе и шлакопортландцементе рекомендуется в пределах 100… 200 кг/м3, в тощих растворах возможен и больший расход.
С увеличением расхода цемента количество золы уменьшается до 40… 50 % массы цемента. При расходе цемента свыше 400 кг/м3 введение золы в состав раствора малоэффективно.
Золу желательно вводить вместо части цемента, извести и песка. При этом достигают экономии 30… 50 кг цемента и 40… 70 кг известкового теста на 1 м3 раствора без ухудшения удобоукладываемости и прочности. Добавка золы практически не изменяет водосодержание цементно-известковых растворных смесей и эффективна при применении портландцемента и шлакопортландцемента.
Крупнодисперсную золу используют как добавку вместо части извести и песка без уменьшения расхода цемента.
Применение мелкозернистой золы улучшает удобоукладываемость растворной смеси.
В известковых растворах с заменой извести золой расход известкового теста уменьшается на 50 % без уменьшения прочности и других свойств известковых растворов. При замене 50 % извести и части песка удвоенным по массе количеством золы, достигают экономии извести и повышения марки раствора. Таким способом можно получить известково-зольный раствор марки 25 без использования цемента.
В табл. 4.13 приведены ориентировочные составы растворов, содержащих золу-унос при применении мелкозернистого песка. Подвижность растворной смеси по погружению стандартного конуса для приведенных составов – 6… 7 см.
При изготовлении смешанных растворов с неорганическими пластификаторами (глиной, известью и т. п.), а также цементных, известковых и глиняных растворов в растворосмеситель сначала подают воду, потом загружают заполнитель, вяжущее и пластификатор.
Продолжительность сухого перемешивания материалов с момента окончания загрузки материалов в растворосмеситель не должна составлять более 1 мин., а после добавления воды все виды растворов перемешивают до достижения однородности смеси, но не менее 1 мин.
Таблица 4.13. Составы растворов, содержащих золу-унос

В зависимости от вида растворов изменяются сроки выдерживания слоев штукатурки и сроки полного высыхания к началу малярных работ (табл. 4.14).
На рост прочности растворов значительно влияют температурные условия (табл. 4.15). Зимой вид и количество противоморозных добавок определяют в соответствии с табл. 4.16.
Добавки желательно применять в виде водных растворов 10… 12 %-ной концентрации. Не допускается применение противоморозних добавок в растворах для конструкций, на поверхности которых не допустимы высолы, в банях, прачечных и других помещениях с влажным режимом эксплуатации, для конструкций, работающих при температуре более 40 °C, и в химических цехах, где возможен контакт с агрессивными реагентами.
Таблица 4.14. Технологические перерывы при выполнении штукатурных работ

Таблица 4.15. Относительная прочность цементных и смешанных растворов при положительных температурах твердения

Примечания: 1. В случае использования шлакопортландцемента и пуццоланового цемента значения прочности умножают на 0,3 при t = 1 °C, на 0,7 – при t = 5 °C и на 0,9 – при t = 20 °C. 2. Значения прочности приведены для относительной влажности воздуха 50… 60 % в период схватывания.
Таблица 4.16. Относительная прочность цементных и смешанных растворов с добавками при отрицательных температурах твердения

Средняя температура раствора с химическими добавками в момент его укладки должна составлять: при температуре воздуха -10 °C – 4… 6 °С, -11… -20 °C – 9… 11 °С, менее -20 °C – 14… 16 °C.
Правообладателям!
Данное произведение размещено по согласованию с ООО "ЛитРес" (20% исходного текста). Если размещение книги нарушает чьи-либо права, то сообщите об этом.Читателям!
Оплатили, но не знаете что делать дальше?