Текст книги "Современные отделочные и облицовочные материалы. Практический справочник для строительства и ремонта домов и квартир"
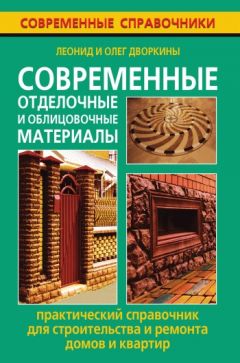
Автор книги: Леонид Дворкин
Жанр: Справочники
Возрастные ограничения: +12
сообщить о неприемлемом содержимом
Текущая страница: 6 (всего у книги 20 страниц) [доступный отрывок для чтения: 7 страниц]
4.3. Специальные штукатурные растворы, растворы для полов
Специальные растворы применяют для водонепроницаемых, кислотоупорных, теплоизоляционных, акустических, рентгенозащитных и других штукатурок.
Водонепроницаемые растворы используют для гидроизоляции строительных конструкций. Их наносят на изолируемую поверхность также, как и другие штукатурные растворы, или способом торкретирования. Водонепроницаемые цементно-песчаные растворы (состав 1:2… 1:3, В/Ц < 0,4) имеют повышенную плотность, содержат уплотняющие добавки: нитрат кальция, алюминат натрия, хлорид железа (III), жидкое стекло и т. п. Для получения водонепроницаемых растворов кроме портландцемента, пуццоланового и шлакопортландцемента эффективны гидравлические быстротвердеющие вяжущие: водонепроницаемый расширяющийся цемент (ВРЦ), водонепроницаемый безусадочный цемент (ВВЦ), гипсоглиноземистый расширяющийся цемент (ГГРЦ).
Водонепроницаемый расширяющийся цемент (ВРЦ) изготовляют путем тщательного перемешивания глиноземистого цемента, строительного гипса и высокоосновного алюмината кальция в следующем соотношении (%): глиноземистый цемент – 70; гипс – 20; четырехкальциевый алюминат – 10.
Прочность ВРЦ через 6 ч. после замешивания – не менее 7,5 МПа; через 3 сут. – 30 МПа; через 28 сут. – 50 МПа.
Водонепроницаемый безусадочный цемент (ВВЦ) является продуктом тщательного перемешивания или совместного помола глиноземистого цемента (не менее 85 %), гипса и извести в соотношении 0,5: 1 (до 15 %). Прочность ВВЦ через 2 ч. после замешивания – не менее 5 МПа; через 6 ч. – 12,5 МПа; через 3 сут. – 25 МПа; через 28 сут. – 30 МПа.
Гипсоглиноземистый расширяющийся цемент (ГГРЦ) изготовляют совместным помолом высокоглиноземистого шлака с двуводным гипсом. Количество гипса в ГГРЦ не должно превышать 30 %. Начало схватывания ГГРЦ – не ранее 20 мин., конец – не позднее 4 ч. с начала замешивания. Этот цемент выпускается в марках М400 и М500. Марку цемента определяют через 3 сут. Прочность цемента марки М400 при сжатии через 24 ч. должна быть не менее 35 МПа, М500 – 45 МПа.
Уплотняющие добавки к цементно-песчаным растворам вводят в количестве, % массы цемента: нитрат кальция – 1… 2, хлорид железа (III) – 1… 2, алюминат натрия – 2… 3.
Водонепроницаемость растворов с уплотняющими добавками возрастает втрое по сравнению с водонепроницаемостью растворов без добавок. Гидроизоляционные работы с использованием уплотняющих добавок выполняют при температуре воздуха не ниже 5 °C. Повышенное содержание хлорида железа (III) может интенсифицировать коррозию арматурной стали.
Порошкообразные добавки до введения в растворную смесь предварительно растворяют в воде. Необходимое количество добавок на замес или 1 м3 раствора определяют в зависимости от плотности их растворов. Для раствора хлорида железа (III) соотношения плотности и концентрации следующие:

Раствор хлорида железа (III) можно приготовить из технической соляной кислоты (плотностью 1,15… 1,19 г/см3) и пиритных огарков (отходов суперфосфатного производства, которые содержат 70… 80 % оксида железа). Пиритные огарки из отвалов предварительно подсушивают, чтобы их влажность не превышала 2 %. Для ускорения реакции применяют стальную стружку.
Соотношения исходных материалов для приготовления хлорида железа (III) (в частях по массе): техническая соляная кислота (плотность 1,15… 1,11 г/см3) – 100; пиритные огарки – 50; стальная стружка или опилки – 5… 10.
Добавка хлорида железа (III) ускоряет темпы роста прочности растворов как в ранние, так и в поздние сроки. В возрасте 28 суток прочность образцов с этой добавкой на 20… 25 % превышает прочность контрольных образцов без добавки.
Добавка алюмината натрия сокращает сроки схватывания раствора; время от его изготовления до применения – 15… 25 мин. Для увеличения сроков схватывания добавляют технические лигносульфонаты в количестве до 0,1 % массы цемента. Предел прочности цементно-песчаного раствора с добавкой алюмината натрия в суточном возрасте приблизительно вдвое превышает прочность раствора без добавки. В последующие сроки замедляется рост прочности раствора с добавкой алюмината натрия.
Для изготовления водонепроницаемых расширяющихся растворов рекомендуют комплексную добавку, содержащую, в массовых частях: алюминиевую пудру – 0,01, хлорид кальция – 2, сульфат алюминия – 2, лигносульфонаты технические – 0,1. Технология изготовления растворов состоит в раздельном растворении в воде сульфата алюминия и других добавок, а потом введения их вместе с водой затворения в растворосмеситель с сухой смесью цемента и песка.
Для изготовления водонепроницаемых растворов повышенной кислотостойкости применяют калиевое жидкое стекло. Цемент с песком замешивают жидким стеклом плотностью 1,4… 1,42 г/см3, разбавленным водой, в соотношении 1:5… 1:10. Растворы на жидком стекле быстро схватываются (через 2… 5 мин.), поэтому их следует приготовлять в небольшом количестве. Учитывая, что жидкое стекло неустойчиво по отношению к содержащемуся в воздухе углекислому газу, покрывочный слой растворов на жидком стекле выполняют из цементного раствора.
К распространенным водонепроницаемым растворам относятся растворы с добавкой церезита, получаемого из олеиновой кислоты, извести, аммиака, водного раствора сернокислого аммония.
В растворы церезит вводят в виде церезитового молока, содержащего на 1 часть добавки 10 частей воды. Применяют водонепроницаемые растворы с добавкой церезита следующих составов (объемн. ч.): цемент– 1, глина – 0,1… 0,2, церезит – 0,12, песок – 2… 3. Церезитовые растворы используют не позднее чем через час после их приготовления.
Водонепроницаемость цементных растворов обеспечивают, кроме указанных, добавки битумных эмульсий, латексов, других полимеров, а также гидрофобизирующих и пластифицирующих поверхностно-активных веществ.
Надежно служат гидроизоляционные растворы, нанесенные методом торкретирования.
Для гидрофобизации штукатурных покрытий их пропитывают растворами кремнийорганических гидрофобизаторов 3… 5 %-ной концентрации. Применение растворов более высокой концентрации может вызвать появление на защищаемой поверхности белого налета.
Кислотостойкие растворы изготавливают из смеси кислотостойких заполнителей и дисперсных наполнителей с кремнефторидом натрия, замешенной на жидком стекле.
Жидкое стекло – воздушное вяжущее вещество, представляющее собой водный раствор щелочных силикатов (силикат-глыбы или гранулята) состава R2O·nSO2, где R2O – Na2O или K2O, n – модуль стекла.
Натриевое жидкое стекло в зависимости от вида исходного полуфабриката разделяют на содовое с п = 2,31… 3,5 и плотностью 1,36… 1,5 г/см3 и содово-сульфатное с п = 2,31… 3 и плотностью 1,43… 1,45 г/см3. Калиевое жидкое стекло имеет n = 3… 4, плотность 1,4… 1,42 г/см3.
Заполнителями кислотостойких растворов являются кварцевый песок, а также пески из измельченного гранита, андезита, базальта и других пород. Наполнители – тонкомолотый кварцевый песок, маршаллит и прочие кремнеземистые порошковидные материалы. Содержание кремнефторида натрия, являющегося отвердителем жидкого стекла, составляет около 15 % массы жидкого стекла.
Для повышения водостойкости кислотостойких растворов к ним добавляют активные минеральные добавки – трепел, опоку, диатомит и т. п.
Полимерные добавки в составе кислотостойких растворов повышают их плотность и непроницаемость.
Распространенные составы кислотостойких растворов приведены в табл. 4.17. Кислотостойкие растворные смеси сохраняют способность к укладке и уплотнению на протяжении не более 40 мин. Схватываются они в воздушно-сухих условиях при температуре не ниже +10 °C. Предел прочности растворов при сжатии в 28-суточном возрасте не менее 15… 20 МПа.
Теплоизоляционные и акустические растворы содержат легкие пористые заполнители: перлит, пемзу, шлак и т. п.
Составы растворов для теплоизоляционных штукатурок на основе перлитового вспученного песка приведены в табл. 4.18.
Для изготовления перлитовых растворов в растворосмеситель сначала загружают перлитовый песок, потом 75 % необходимого количества воды с добавками, цемент и в конце – оставшуюся воду. В целом время перемешивания составляет 3… 5 мин. С увеличением времени перемешивания происходит дробление перлитового песка и увеличение плотности и теплопроводности затвердевшего раствора.
Таблица 4.17. Составы кислотостойких растворов

Примечание. Кислотоупорные составы 1 и 6 рекомендуются при действии кислот средних и высоких концентраций. Состав 6 рекомендуется при постоянном действии серной, фосфорной, уксусной, хромовой кислот, натриевые соли которых образуют кристаллогидраты с большим содержанием воды. Составы 2–5 можно применять при действии кислот любых концентраций, а также при переменном действии кислоты и воды.
В растворах для акустических штукатурок заполнителями могут быть пемза, керамзит, легкие шлаки, туф и т. п. При средней плотности пемзы или шлака 400 кг/м3 объемное соотношение между портландцементом (или строительным гипсом), заполнителем и водой – 1:4:1,25 (для пемзы) и 1:4:0,7 (для шлака). Заполнитель до использования в акустических растворах просеивают сквозь сита с отверстиями 5 и 3 мм. Плотность акустических растворов – 600… 1200 кг/м3, коэффициент звукопоглощения – 0,5 в интервале 800… 1600 Гц.
Огнестойкие растворы обеспечивают защиту металлических железобетонных конструкций от действия высоких температур в случае возникновения пожара. Огнестойкие штукатурки не должны плавиться и отслаиваться под воздействием температуры до 1200 °C. Защитное действие растворов этого типа должно сохраняться в течение 0,5… 4 ч. В табл. 4.19 приведены составы огнестойких растворов с использованием перлита и гранулированной минеральной ваты как заполнителей.
Биоцидныерастворы предназначены для использования в конструкциях, на поверхности которых в результате попадания органических веществ возможно развитие процессов гниения, брожения и т. п. Такие нежелательные коррозионные процессы могут развиваться в конструкциях зданий и сооружений пивоваренной, мясной, молочной, рыбной, сахарной, биологической, кондитерской промышленности, сооружений технического водоснабжения.
Для придания биоцидных свойств растворам в их состав вводят катапин-бактерицид в количестве 1… 10 % массы цемента. Катапин-бактерицид не повреждает кожные покровы и органы дыхания человека.
Добавка не должна уменьшать прочность раствора более чем на 15 %.
Таблица 4.18. Составы теплоизоляционных штукатурок и физико-механические свойства растворов

Примечание. Составы приведены в пересчете на сухую смесь с влажностью не более 0,5 %.
Таблица 4.19. Составы огнестойких растворов

Растворы для защиты от ионизирующего излучения применяют для устройства защитных штукатурок в рентгеновских кабинетах, на АЭС, предприятиях, производящих изотопы, и т. п.
Плотность рентгенозащитных растворов должна быть быть более 2200 кг/м3, для этого применяют баритовый песок с зернами крупностью до 1,25 мм и баритовый тонкомолотый наполнитель.
Составы растворов для рентгенозащитных штукатурок, части объема: 1) портландцемент М400 – 1; известковое тесто – 0,5; баритовый песок – 4; вода – до необходимой консистенции; 2) портландцемент М400 – 1, баритовый песок – 2, баритовая пыль – 1, вода – до необходимой консистенции.
Водоцементное отношение растворов не должно превышать 1,5. Защитные свойства штукатурок улучшают путем введения веществ, содержащих бор, и добавок, в которых имеются такие элементы, как водород, литий, кадмий.
4.4. Декоративные растворы
Декоративные растворы применяют для внешней и внутренней отделки зданий, а также для отделки лицевых поверхностей стеновых панелей и блоков. Выбирая вяжущие для приготовления декоративных растворов, следует учитывать вид отделываемых поверхностей.

Подвижность растворных смесей для подготовительного слоя декоративных штукатурок при механизированном нанесении – 6… 10 см, покровного слоя – 7… 10 см (по погружению стандартного конуса). При ручном нанесении подвижность растворной смеси для подготовительного слоя увеличивают до 8… 12 см, а для покровного – до 9… 12 см при введении в растворную смесь гипса. Ориентировочные составы цветных известково-песчаных, терразитовых и камневидных штукатурок приведены в табл. 4.20—4.22.
Таблица 4.20. Составы цветных известково-песчаных штукатурок


При изготовлении цветных известково-песчаных растворов в растворосмесителе сначала перемешивают большую часть известкового теста с добавкой цемента в течение 1… 2 мин., затем засыпают песок и перемешивают смесь еще в течение 3 мин. На последней стадии в смесь добавляют пигмент, перетертый с оставшейся известью. Цветными известково-песчаными смесями оштукатуривают фасадные части зданий. Для оштукатуривания интенсивно увлажняемых поверхностей из плотного бетона, цоколей, пилястров используют смеси с добавкой цемента.
Фактура затвердевшей штукатурки зависит от метода нанесения покровного слоя и способа его отделки. В основном цветными известково-песчаными штукатурками имитируют песчаник и травертин.
Штукатурки типа сграффито изготовляют из известково-песчаных смесей, составы которых приведены в табл. 4.20. Для тонкослойного одноцветного сграффито на первый покровный цветной слой кистью наносят второй толщиной 0,3… 0,5 мм, который процарапывают по рисунку, нанесенному при помощи трафарета. При двухцветном сграффито грунт покрывают цветным слоем, а после его затвердевания – вторым слоем другого цвета. На второй слой по трафарету наносят рисунок и процарапывают по нему до обнажения нижнего слоя.
Составы растворов для двухцветного сграффито, % массы

Таблица 4.21. Составы терразитовых штукатурных смесей, объемные части


Примечание. М, С, К – мелкозернистый, среднезернистый и крупнозернистый песок.
Таблица 4.22. Составы камневидных штукатурных смесей, %



Примечание. В приведенных составах принят портландцемент марок М400 и М500.
Первые слои многоцветного сграффито выполняют из цветных растворов, а дополнительную расцветку создают методом фресковой живописи.
Терразитовые растворы (табл. 4.21) изготавливают обычно из сухих цветных смесей. В процессе изготовления терразитовой растворной смеси из отдельных компонентов в растворосмеситель сначала загружают заполнитель и смесь цемента с пигментами и тщательно перемешивают. Воду, известковое молоко и пластификаторы вводят на последнем этапе перемешивания. Для определения подвижности терразитовых смесей непосредственно на объекте имеется несколько способов. Подвижность считают достаточной, если смесь не осыпается при нанесении на вертикальную загрунтованную поверхность слоем 6… 8 мм для мелкозернистого, 8… 10 мм – для среднезернистого и 10… 12 мм – для крупнозернистого терразита.
Фактура терразита зависит от предельной крупности зерен заполнителя. Мелкозернистые заполнители в терразитовых смесях имеют зерна 0,15… 2 мм, среднезернистые – 2… 4 мм, крупнозернистые – 4… 6 мм. Крупнозернистый терразит (терразит К) при обработке фасадов используют для оштукатуривания цоколей и нижних этажей, среднезернистый (терразит С) – для поверхностей стен, мелкозернистый (терразит М) – для устройства карнизов. При формовании железобетонных панелей на заводе для их отделки используют терразитовые смеси из белого цемента и цветной каменной крошки в соотношении от 1:4 до 1:5. Зерновой состав каменной крошки: фракция 1,2… 2,5 мм – 35… 40 %; 2,5… 5 мм – 60… 65 %. Количество воды подбирают так, чтобы подвижность смеси характеризовалась погружением конуса на 2… 3 см. После нанесения и уплотнения отделочного слоя поверхность изделия обрабатывают распыленной водой; вследствие этого цементное тесто вымывается с внешней стороны зерен цветного заполнителя и заполняет пустоты между его зернами.
После двух-трехчасовой выдержки при нормальной температуре изделия обрабатывают горячим паром. Для повышения водонепроницаемости и морозостойкости декоративного слоя, уменьшения его загрязнения во время эксплуатации эффективна обработка растворами кремнийорганических соединений.
Камневидными штукатурками (табл. 4.22) отделывают в основном фасады и цоколи монументальных сооружений. Основным вяжущим является цемент; известковое тесто вводят в количестве 10… 20 % для придания растворным смесям пластичности и разбеливания цемента. Как заполнитель используют обычно крошку имитируемой горной породы (см. рис. 7 на цветной вклейке). Важное значение при этом придается зерновому составу каменной крошки, который должен соответствовать способу обработки поверхности затвердевшего раствора и нужной фактуре. При пескоструйной обработке поверхности желательно, чтобы смесь содержала не менее 50 % зерен крупностью 2,5… 5 мм. Для мелкозернистой фактуры, изготавливаемой циклеванием, размер зерен заполнителя не должен превышать 1,2 мм, для рельефных фактур применяют крупнозернистые смеси.
Затвердевший декоративный слой камневидной штукатурки обрабатывают камнетесными инструментами, бучардой, пескоструйными аппаратами. Применяют также обработку циклеванием, набрызгом и др. (см. рис. 8 на цветной вклейке). Для лучшего обнажения каменной крошки отделочный слой протравливают 10… 15 %-ным раствором соляной кислоты.
При заводском изготовлении стеновых панелей для получения камневидного покрытия фасадную поверхность панелей отделывают несколькими способами: посыпкой и углублением измельченного материала в свежесформованный слой цементно-песчаного раствора, нанесенного на поверхность изделий; применением фиксирующих слоев из песка, мелкозернистой крошки или саморазрушающихся паст, укладываемых на поддон формы, и т. п.

Рис. 4.2. Примеры обработки растворных покрытий: а – бучардой, б – скарпелем, в – циклеванием, г – набрызгом
Камневидное покрытие из раствора с углубленной крошкой декоративных горных пород изготовливают, формуя панели лицевой поверхностью вверх. На выровненную поверхность свежесформованных изделий укладывают цементно-песчаный раствор состава 1:3… 1:4 с погружением конуса до 4 см, по которому равномерно распределяют декоративный материал, который притрамбовывается или накатывается до погружения на глубину 0,5… 0,6 поперечного сечения зерен с последующей кратковременной вибрацией. Необходимый цвет покрытия создают введением пигментов или обработкой слоя раствора пигментированным цементным молоком, изготовляемым в механических смесителях или гидродинамических диспергаторах. После обработки горячим паром фасадную поверхность панелей моют водой, очищают металлической щеткой и обрабатывают гидрофобными веществами.
Для изготовления камневидного покрытия при формовании панелей лицевой поверхностью вниз используют подстилающий слой из песка, на который насыпают и вдавливают на 0,3… 0,5 диаметра декоративный материал, потом укладывают цветной раствор и формуют панели.
Применяют также способ нанесения на смазанный поддон формы фиксирующей пасты слоем 3… 10 мм, которую посыпают измельченным декоративным материалом. После достижения пастой прочности при сжатии 0,4… 0,5 МПа укладывают раствор и формуют изделия. Состав фиксирующей пасты, %: строительный гипс – 65, гидратная известь – 22, сернокислый глинозем – 13. Замешивая пасту, добавляют 1 % замедлителя схватывания гипса. При обработке панелей горячим паром паста испытывает деструктивные изменения в результате образования гидросульфоалюминатов кальция, превращается в бессвязную массу и смывается водой.
Для изготовления камневидного покрытия при формовании изделий применяют также бумажные коврики, на которые с помощью жидкого стекла наклеивают каменную крошку. Коврики укладывают на поддоны очищенных и смазанных форм, наносят слой декоративного цементно-песчаного раствора и формуют изделия. После обработки горячим паром поверхность изделий очищают от бумаги.
Растворы на основе коллоидного цементного клея (КЦК) имеют повышенную прочность и адгезию к бетонам, сравнительно низкое водопоглощение. КЦК – это продукт совместного вибропомола цемента и кварцевого песка в соотношении 7:3 по массе. Удельная поверхность смеси должна быть не менее 500 м2/кг. Для изготовления окрашенного КЦК используют цветные портландцементы или добавление к белому цементу при помоле щелочестойких пигментов. Сухую смесь клея, приготовленную на заводе и централизованно доставленную на объект в полиэтиленовых мешках, сохраняют не более 15 суток. Штукатурные растворы на основе КЦК можно изготовить смешиванием клея с песком и водой. Если нужна штукатурка с повышенной водостойкостью, в раствор добавляют гидрофобизаторы типа ГКЖ. Используют кварцевые пески с крупностью зерен до 1 мм, а также пески, являющиеся продуктом измельчения горных пород (мрамор, гранит, известняк) с пределом прочности при сжатии не ниже 40 МПа.
КЦК изготовляют непосредственно перед использованием. С этой целью порошок с водой при водовяжущем отношении 0,35… 0,5 перемешивают в течение 5… 6 мин. в вибросмесителе или ультразвуковом активаторе. При отсутствии вибросмесителя и активатора изготовление растворных смесей допускается в смесителях других конструкций. После 3… 4 мин. перемешивания смесь подвергают пятиминутной виброактивации с помощью любого высокочастотного вибратора, обеспечивающего 10 000… 14 000 кол./мин.
Подвижность рабочей смеси составляет: для беспесчаных растворов (клеев) – 7… 8 см, для растворов на основе КЦК-10… 12 см.
Применяют три способа отделки панелей растворами на основе КЦК:
1) нанесение отделочного раствора на поддон формы с последующим бетонированием панели (при формовании «лицом вниз»);
2) нанесение отделочного раствора на свежесформованную и выровненную поверхность панели (при формовании «лицом вверх»);
3) нанесение отделочного раствора на поверхность готовой панели после обработки ее горячим паром (при любом методе формования).
Как разновидность декоративно-отделочных растворов можно рассматривать искусственный мрамор на гипсовых и цементных вяжущих. Изготовление искусственного мрамора состоит из следующих операций: очистка и промывание водой облицовываемой поверхности; нанесение грунта; наложение на высохший грунт лицевого слоя; зачистка, циклевка, шлифование, лощение и полирование. Искусственным мрамором облицовывают каменные, бетонные и деревянные конструкции.
Составы растворов для грунта под искусственный мрамор приведены в табл. 4.23.
Таблица 4.23. Составы растворов для грунта под искусственный мрамор

Для изготовления искусственного мрамора на основе гипсовых вяжущих гипсопесчаную смесь замешивают на 2… 2,5 %-ном клеевом растворе.
На поверхности грунта для лучшего сцепления лицевого слоя искусственного мрамора нарезывают сетку с царапинами глубиной 3… 4 см.
Составы гипсового теста для искусственного брускового мрамора приведены в табл. 4.24.
Искусственный мрамор на основе цемента изготовляют из сухой смеси следующего состава, масс, ч.:

Гипсовые и цементные смеси применяют для изготовления бесшовного или брускового искусственного мрамора, литых плит на стекле, мраморовидного лицевого слоя при заводской отделке бетонных и железобетонных изделий.
Таблица 4.24. Составы растворов для искусственного брускового мрамора

При изготовлении на заводе изделий с мраморовидной поверхностью для образования прожилок на поддон формы, покрытый маслом, пистолетом-краскораспылителем наносят пигментирующее вещество; после этого из вибробункера или бетоноукладчика набрасывают растворную смесь. Рецептуры некоторых распространенных пигментирующих составов приведены в табл. 4.25.
Таблица 4.25. Пигментирующие составы для искусственного мрамора с цветными прожилками

Правообладателям!
Данное произведение размещено по согласованию с ООО "ЛитРес" (20% исходного текста). Если размещение книги нарушает чьи-либо права, то сообщите об этом.Читателям!
Оплатили, но не знаете что делать дальше?