Текст книги "Современные отделочные и облицовочные материалы. Практический справочник для строительства и ремонта домов и квартир"
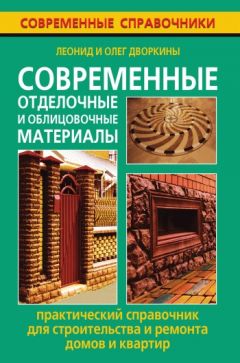
Автор книги: Леонид Дворкин
Жанр: Справочники
Возрастные ограничения: +12
сообщить о неприемлемом содержимом
Текущая страница: 7 (всего у книги 20 страниц) [доступный отрывок для чтения: 7 страниц]
4.5. Тонкослойные декоративные штукатурки
В современном строительстве для отделки зданий и сооружений широко используют тонкослойные декоративные фасадные штукатурки. Они выполняются обычно из готовых порошкообразных и мастичных (ластовых) смесей. Тонкослойные штукатурки обладают как декоративной, так и защитной функцией, образуют слой, стойкий к атмосферному, в том числе ультрафиолетовому воздействию, а также механическим повреждениям (см. рис. 8 на цветной вклейке). Легкие штукатурки улучшают теплоизоляционные свойства стен, сохраняют нужный микроклимат внутри помещений, обеспечивают выполнение специальных требований: экранирование радиоволн, защиту от рентгеновского излучения, шума и т. д. Отдельную группу составляют штукатурки, применяемые в реставрационных работах. Одним из основных требований к декоративным штукатуркам при выполнении реставрационных работ является достаточная скорость диффузии водяного пара.
Основной группой тонкослойных штукатурок являются декоративные фасадные штукатурки толщиной 1… 3 мм, укладываемые в виде отделочного слоя как традиционных цементно-известковых штукатурок, так и систем теплоизоляции зданий. Общая качественная характеристика основных видов тонкослойных декоративных штукатурок приведена в табл. 4.26.
Тонкослойные штукатурки позволяют получать как разнообразную цветовую гамму, так и различные виды фактур после затирки гладкой нержавеющей теркой. Распространены рустикальная («короед») и шероховатая («барашек») фактуры. Первую получают вертикальными и круговыми движениями, вторую – круговыми.
Таблица 4.26. Общая характеристика тонкослойных штукатурок

Минеральные штукатурки изготавливаются в виде сухих смесей на основе портландцемента и кварцевой или мраморной крошки с размером зерна до 1,5; 2 или 3 мм. Акриловые штукатурки имеют консистенцию пасты и изготавливаются на основе водной дисперсии акриловых смол.
Акриловые штукатурки образуют гидрофобное покрытие с большой стойкостью к механическим повреждениям, однако они стареют под влиянием ультрафиолетовых лучей. Разновидностью акриловых штукатурок является мозаичная штукатурка. Она изготавливается на основе акриловой смолы с добавлением мрамора и цветной кварцевой крошки, имеет высокую прочность, стойкость к мытью, очистке, рекомендуется для отделки лестничных площадок, цоколей, стен.
Силикатные и силиконовые штукатурки применяют в виде готовых к применению масс, изготовленных соответственно на основе жидкого стекла и кремнийорганической смолы, мраморной, доломитовой и т. п. крошки. Они образуют прочные поверхности с большой эластичностью, пропускающие водяной пар, стойкие к мытью и биологической коррозии. Силиконовые штукатурки способны к самоочищению под влиянием атмосферных осадков.
Важный этап при использовании тонкослойных штукатурок – подготовка поверхности основания, которое должно быть чистым, прочным и ровным.
В табл. 4.27—4.29 приведены технические характеристики акриловых, силикатных и силиконовых штукатурок «Ceresit».
Таблица 4.27. Основные технические характеристики акриловых штукатурок «Ceresit»

Таблица 4.28. Основные технические характеристики силикатных штукатурок «Ceresit»

Таблица 4.29. Основные технические характеристики силиконовых штукатурок «Ceresit»

Тонкослойные декоративные штукатурки позволяют получать покрытия, известные как венецианские штукатурки. Впервые такие покрытия были получены в эпоху Ренессанса в Венеции на основе мраморной пыли, извести, растительных красителей и воды. В настоящее время подобные штукатурные составы обязательно содержат акриловые связующие. Как правило, венецианские штукатурки с повышенным содержанием полимера образуют более эластичные и трещиностойкие покрытия.
Полимерные штукатурки стойки к атмосферным влияниям, ударостойки, гидрофобны, паропроницаемы, легко наносятся на поверхности конструкций, не вредны для здоровья людей. Покрытия могут выполняться как в одном цвете, так и многоцветными. Венецианская штукатурка предусматривает «подпрессовку» нескольких тонких полупрозрачных слоев материала. Благодаря игре отраженных лучей света, проходящих через толщу покрытия, венецианская штукатурка напоминает полированный мрамор. Технология получения покрытия включает операции заглаживания, «железнения» и полирования шпателем каждого слоя. Готовое покрытие имеет толщину 3… 5 мм, характеризуется высокой паропроницаемостью, что создает в помещении хороший микроклимат. Венецианская штукатурка позволяет художникам создавать на ее поверхности декоративные панно, роспись делается по влажному последнему слою специальными пигментами.
Декоративную штукатурку на основе натурального целлюлозного волокна и клеевого связующего с добавлением пигментов называют жидкими обоями. Жидкие обои напоминают бумажные с небольшим рельефом или ворсистую ткань. Они позволяют получать сплошное бесшовное покрытие, скрывают небольшие трещины и дефекты. Преимущество этой штукатурки заключается в том, что она легко наносится, не требует значительных трудовых затрат для приготовления смеси. Поверхность, покрытая жидкими обоями, может иметь различную структуру, она хорошо чистится и реставрируется. На нее легко наносится краска, клеятся рулонные обои.
4.6. Декоративные (архитектурные) бетоны
Декоративные бетоны применяют для архитектурной отделки конструктивных элементов зданий и сооружений – стен, полов, лестниц, разделительных полос дорожных покрытий и др. Декоративность бетона достигается как цветом, так и фактурой лицевой поверхности.
Для изготовления цветных бетонов используют обычный портландцемент, шлакопортландцемент, пуццолановый портландцемент, а также белый и цветной портландцементы.
Белый и цветной портландцементы изготовляют из маложелезистого клинкера, отличающегося от обычного повышенным содержанием SiO2 (23,5… 25,5 %) и Аl2O3 (5,5… 7 %) и незначительным количеством Fe2O3 (0,25… 0,5 %) и МnО (0,05… 0,15 %). Минеральный состав клинкера для белого цемента, %: C3S – 35… 50; С3А – 14… 17; C4AF – 0,9… 1,4. Количество MgO не должно превышать 4 %.
По составу различают белый портландцемент и белый портландцемент с минеральными добавками; последние не должны превышать 20 % массы. По согласованию с потребителем можно добавлять в белый цемент специальные добавки, не превышающие 2 % массы цемента, и пластифицирующие добавки, не превышающие 0,5 % массы цемента. Выпускаемые марки белого цемента – М400 и М500.
Степень белизны, определяемая коэффициентом отражения (в % абсолютной шкалы), должна быть не ниже: для портландцемента 1-го сорта – 80; 2-го сорта – 75; 3-го сорта – 70; для инертных минеральных добавок – 80; активных минеральных добавок – 75; гипса – 70.
Степень белизны цемента и добавок определяют фотометром, а также используя матовое стекло.
Цветной портландцемент изготовляют методом совместного тонкого измельчения белого или цветного клинкера, активной минеральной добавки, пигмента и гипса. Цветные клинкеры получают при введении в сырьевые смеси небольшого количества соединений кобальта, хрома, марганца и т. п.
Цветной портландцемент должен содержать (в % от массы цемента): клинкера – не менее 80, активной минеральной добавки – не более 6, минерального искусственного или природного пигмента – не более 15, органического пигмента – не более 0,5.
Содержание гипса – не более 3,5 % в расчете на SO3. Белизна активной минеральной добавки – не менее 68 %.
Цветной цемент подразделяют по прочности на марки М300, М400 и М500.
Основные виды пигментов, используемых для получения цветного цемента на основе белого, приведены в табл. 4.30.
Таблица 4.30. Пигменты для цветного цемента на основе белого

Пигменты для цветного цемента должны иметь достаточную красящую способность, высокую стойкость к щелочам, солнечному свету и атмосферному влиянию. Они не должны содержать вредных примесей и растворимых солей. Изменение интенсивности цвета цемента в зависимости от количества добавленного пигмента приведено в табл. 4.31.
Таблица 4.31. Изменение интенсивности цвета цемента в зависимости от количества добавленного пигмента

С увеличением содержания пигментов активность цемента уменьшается. Обычно на цементных заводах в цветной цемент добавляют не более 10 % пигмента.
Белый и цветной цемент характеризуются повышенной усадкой при твердении, пониженной морозостойкостью (табл. 4.32).
Таблица 4.32. Морозостойкость образцов (циклы) цементного камня в зависимости от вида и количества добавленных пигментов

Усадочные деформации возрастают с увеличением в составе цемента содержания белита и трехкальциевого алюмината, активных минеральных добавок и некоторых пигментов.
Активные минеральные добавки, связывающие гидроксид кальция в малорастворимые гидросиликаты кальция, в значительной мере уменьшают образование выцветов на декоративных облицовках. Этому способствует также введение в белый и цветной цемент гидрофобизирующих добавок.
Белый и цветной цемент хранят и транспортируют в специальных контейнерах или мешках.
Введением пигментов окрашивают также обычный цемент (табл. 4.33). Цемент светлых тонов изготавливают смешиванием обычного портландцемента с разбеливающими минеральными добавками (мелом, молотым известняком, мрамором и т. п.), а также с белилами. Содержание разбеливающих минеральных добавок достигает 25 %. Пигменты средней интенсивности типа охры, мумии, сиены добавляют в количестве свыше 10 %, более интенсивные – до 10 %.
Таблица 4.33. Пигменты для получения цветного цемента на основе серого

Для расширения палитры цветной цемент подкрашивают органическими красителями.
Введение повышенного количества пигментов в бетонную смесь часто приводит к снижению прочности. Количество пигментов, разбеливающих цемент (молотый мрамор, мел, титановые белила), может достигать не более 25 % по массе; природных пигментов, имеющих невысокую цветовую насыщенность (охра, мумия, сиена, глауконит), – чуть более 10 %; интенсивных минеральных (окись хрома, редоксайд, ультрамарин) – до 10 %; пигментов на основе оксидов железа – до 5 %. Органические фталоцианиновые пигменты голубого и зеленого цветов вводятся в количестве 0,15… 0,35 % массы цементно-песчаной смеси.
Рекомендуется изготовление цветных вяжущих путем совместного помола цементов с пигментами в шаровых или вибрационных мельницах. Допускается также перемешивание сухих пигментов и компонентов бетонной смеси в процессе ее изготовления, однако таким способом трудно осуществить точное дозирование и получить бетон равномерной окраски. Для повышения точности механического дозирования применяют пигменты в виде водной суспензии, а также гранулированные пигменты. Водная суспензия пигмента чаще всего изготавливается непосредственно на бетонном заводе путем смешивания пигмента и воды в соотношении 1:2 в пропеллерных мешалках непосредственно перед подачей в бетоносмеситель. Для улучшения диспергации пигмента могут использоваться добавки ПАВ. Транспортировка суспензии производится диафрагменными насосами.
Декоративные щебень и песок изготовляют измельчением горных пород, окрашенных в различные цвета (гранита, диорита, диабаза, андезита, кварцита, мрамора и др.). В зависимости от крупности зерен песок разделяют на фракции до 2,5 и 2,5… 5 мм. Для щебня установлены фракции 5… 10, 10… 20, 20… 40 мм. Возможна при согласии сторон поставка песка фракций 0,14… 3, щебня – 10… 15, 15… 20 мм. Песок высшей категории качества крупностью до 2,5 мм поставляют фракциями 0,3… 0,6; 0,6… 1,2; 1,2… 2,5 мм.
Для заполнителей крупностью свыше 2,5 мм зерновой состав должен находиться в следующих пределах:

К зерновому составу песка фракций до 2,5 мм выдвигают такие требования: полный остаток на сите 2,5 мм – не более 10 %; 0,14 мм – не менее 90 % массы. Марки по прочности щебня и песка должны быть не ниже М800 для щебня и песка из изверженных пород, М400 – из метаморфических и М300 – из осадочных.
Для щебня устанавливают марки по морозостойкости: F15, F25, F50, F100, F200 и F300. Для песка их определяют испытанием исходной горной породы. Щебень и песок, применяемые для бетонов, предназначенных для устройства полов, должны соответствовать требованиям к истираемости исходных горных пород (не выше 2,2 г/см2 при интенсивности движения менее 100 чел./ч и не выше 0,5 г/см2 при большей интенсивности движения).
Предельное содержание пылевидных и глинистых частиц в декоративных заполнителях нормируется в зависимости от вида и марок горных пород по прочности (табл. 4.34). Нельзя допускать наличие в заполнителях глины в комках, зерен с пределом прочности менее 20 МПа свыше 5 % массы, пластинчатых и игловидных зерен свыше 35 % массы декоративного заполнителя.
Таблица 4.34. Содержание пылевидных частиц в декоративных заполнителях из природного камня, % массы

Цвет отделочных слоев декоративных бетонов обеспечивается за счет цвета заполнителей непрерывной гранулометрии. Цвет подбирают при условии наиболее плотной упаковки заполнителя, обеспечивающей его максимальный выход на поверхность отделочного слоя. Если состав бетона с наименьшим расходом цемента подобран правильно, крупный заполнитель занимает не менее 55 % объема. Его зерна выходят на поверхность до 65 % площади бетона.
Беспесчаные декоративные бетоны состоят из цемента и каменной крошки в соотношении по массе 1:4 и 1:5, составы корректируются в зависимости от марки цемента и гранулометрического состава заполнителя.
Мелкий заполнитель для цветных декоративных бетонов по цвету обычно соответствует применяемому цементу, а крупный контрастирует с основным фоном.
Состав цветных бетонов должен удовлетворять проектным характеристикам бетона. Изготовляют бетонную смесь в смесителях принудительного действия. В процессе перемешивания смеси вначале подают заполнители, потом цемент, в который при необходимости предварительно вводят пигменты. После кратковременного сухого перемешивания в бетонную смесь добавляют воду. Цветные бетоны можно изготавливать, используя цветное цементное тесто, являющееся продуктом совместной обработки вяжущих и пигментов в акустическом или аэрогидродинамическом активаторе. Вместо воды для замешивания можно использовать также цветные стабилизированные суспензии, получаемые тщательным перемешиванием воды и пигментов с добавлением поверхностно-активных веществ.
При изготовлении цветных бетонов существует опасность появления на поверхности высолов в результате выщелачивания цементного камня или использования добавок-электролитов. Для предупреждения высолообразования эффективно использование гидрофобизирующих добавок (ГКЖ-10, ГКЖ-11, СНВ, мылонафт и др.).
При формовании декоративных бетонных изделий следует избегать загрязнения поверхностей смазкой для форм путем использования полимерных пленок и форм, а также немедленной распалубки (при применении сверхжестких смесей и интенсивных методов уплотнения).
Для придания декоративной фактуры бетону обнажают поверхность заполнителя шлифовальными, колочными машинами, фрезами, бучардами, пневмомолотками, пескоструйными аппаратами, а также путем использования замедлителей твердения, позволяющих снизить прочность поверхностного слоя (см. рис. 9 на цветной вклейке).
Для получения штампованного (печатного) декоративного бетона на бетонную смесь в пластичном состоянии наносят рельефный оттиск, повторяющий текстуру и форму натурального камня, кирпича, древесины и др.
4.7. Бетоны и растворы для полов
Полы с бетонными покрытиями применяют в производственных зданиях, где они подвергаются механическим воздействиям, нагреванию до температуры не более 100 °C, воздействию минеральных масел, органических растворителей. Бетонные покрытия выполняют по грунтовым основаниям, подстилающим бетонным слоям, железобетонным плитам перекрытий и по цементно-песчаным стяжкам. Для безыскровых (взрывобезопасных) бетонных покрытий используют щебень и песок из известняка, мрамора и других каменных материалов, не образующих искр при ударах. Крупность щебня и гравия для бетонных покрытий не должна превышать 0,6 толщины покрытия. Расход крупных заполнителей составляет не менее 0,8 м3 на 1 м3 бетона, а песка – 10… 30 % объема пустот в щебне или гравии. Класс бетона принимается не менее В15 (М200). Для снижения трудозатрат эффективно применение литых бетонов с добавкой суперпластификаторов. Высокое качество бетонных полов достигается также вакуумированием, которое позволяет обеспечивать высокие физико-механические характеристики поверхностного слоя. При вакуумировании бетонная смесь уплотняется вибрированием, а затем излишек воды удаляется с помощью вакуумного агрегата и отсасывающих матов. При этом бетон приобретает достаточную прочность для немедленной обработки поверхностного слоя заглаживающими машинами. Ориентировочные составы бетонных полов, получаемых методом вакуумирования, приведены в табл. 4.35.
Таблица 4.35. Ориентировочные составы бетонов при устройстве бетонных полов методом вакуумирования


Для повышения стойкости и эстетических свойств бетонные покрытия подвергают фрезерованию и шлифованию, пропитке флюатами и уплотняющими составами, лакированию. Глубина фрезерования выбирается исходя из условия максимального обнажения зерен заполнителя при исключении возможности его выкрашивания. В качестве флюатов применяют водные растворы кремнефтористоводородной кислоты и ее солей. Для пропитки применяют также жидкое стекло, раствор хлористого кальция. Для лакирования бетона применяют полиуретановые, эпоксидные и другие полимерные лаки и эмали.
Наряду с цементными бетонами для устройства полов общего назначения применяют цементно-песчаные растворы. Их укладывают на железобетонные плиты перекрытий и цементно-песчаные стяжки. Ориентировочные составы цементно-песчаных растворов приведены в табл. 4.36.
Таблица 4.36. Составы цементно-песчаных растворов для полов (цемент марки М400)

Подвижность растворных смесей для покрытия полов – 2,5… 3,5 см, для стяжек – 11… 13 см. Цементно-песчаные растворы должны твердеть во влажных условиях в течение 7… 10 суток.
В производственных зданиях устраивают также полы с металлоцементным покрытием. Покрытие состоит из нижнего слоя – цементно-песчаного раствора марки М400 толщиной 20 мм, и верхнего – раствора марки М500 из смеси стальной стружки, цемента и воды не менее 20 мм толщиной. Стальную стружку измельчают на бегунах или в шаровых мельницах, затем обезжиривают прокаливанием и просеивают на сите с размером отверстий 1,2 мм. Насыпная плотность стальной стружки должна быть не менее 2000 кг/м3. При изготовлении металлоцементных смесей цемент и стальную стружку дозируют в соотношении по объему 1:1. Количество воды подбирают так, чтобы подвижность смеси соответствовала погружению конуса 1… 2 см.
Полы из мозаичных смесей устраивают прежде всего в вестибюлях, на лестничных площадках, в коридорах, санитарных узлах, а из ксилолитовых – в помещениях, где люди находятся долго и мало передвигаются (административных, учебных, зрелищных и т. п.). Мозаичные и ксилолитовые смеси используют для покрытия как монолитных, так и сборных (из готовых плит) полов.
Мозаичные смеси изготовляют с применением белого, цветного или обычного разбеленного портландцемента и крошки из твердых пород (чаще всего мрамора), которые поддаются шлифованию, имеют предел прочности при сжатии не менее 60, 80 и 100 МПа соответственно для покрытий марок М200, М300, М400. Размер каменной крошки должен быть 2,5… 15 мм: крупной (МК) – 10… 15 мм, средней (МС) – 5… 10 мм, мелкой (ММ) – 2,5… 5 мм. Крошка не должна содержать пылеватых и глинистых примесей и легко разрушаемых зерен. Твердость крошки должна соответствовать твердости покрытия, иначе его качество будет снижаться вследствие неравномерного истирания.
Рекомендуется использовать крошку с водопоглощением в пределах 12… 16 %; при более низком водопоглощении ухудшается ее сцепление с цементным камнем, при более высоком – способность к шлифованию.
Помимо каменной крошки для некоторых мозаичных смесей применяют кварцевый песок. Для разбеливания обычного серого цемента вводят порошок (крупность зерен менее 1,5 мм) из белых горных пород, предел прочности которых при сжатии не менее 20 МПа, в количестве 20… 40 % массы цемента. Выбирая состав мозаичной смеси, исходят из условия создания после обработки поверхности, содержащей 75… 80 % каменных заполнителей и 20… 25 % цементного камня. Количество крупной крошки обычно не менее 0,8 м3 на 1 м3 мозаичного раствора, а объем мелкой крошки или добавляемого песка должен на 10… 30 % превышать объем пустот крупного заполнителя.
Состав мозаичных смесей зависит от марки бетона; ориентировочно он может быть следующим, масс, ч.:

Подвижность мозаичной смеси соответствует осадке конуса 2… 4 см.
Цвет каменной крошки, соотношение ее мелкой и крупной фракций, необходимые количество и вид пигментов выбирают в зависимости от заданного цвета и тона покрытия (табл. 4.37).
Изготовление мозаичного монолитного покрытия включает укладку сначала жесткого цементно-песчаного раствора толщиной 20… 25 мм, затем лицевого мозаичного слоя, который после отвердевания шлифуют мозаично-шлифовальными машинами. Во время твердения должны быть обеспечены благоприятные условия для предотвращения быстрого удаления влаги из бетона. Для этого обычно через двое суток после укладки поверхность мозаичного пола засыпают слоем опилок не менее 30 мм и на протяжении 4… 7 суток периодически увлажняют. К отделке поверхности мозаичного покрытия приступают после достижения им такой прочности, при которой каменная крошка не выкрашивается. Отделка включает операции обдирки (для удаления верхнего слоя цементного камня и обнажения заполнителя), шлифования и полирования.
Помимо обычных устраивают наборно-мозаичные облицовки, имитирующие декоративные горные породы. Облицовки набирают из отдельных кусков и крошки природного камня различных пород заданного цвета и формы и укладывают по рисунку на цементно-песчаном растворе. Затвердевшее покрытие шлифуют. При устройстве такого пола заполнитель из декоративного камня и связывающий его цементно-песчаный раствор должны быть равнопрочными. Иначе пол при эксплуатации будет неравномерно истираться.
Художественно-монументальная мозаика набирается из отдельных кусочков смальты, боя керамических плиток, декоративного камня. Она выполняется по специальным рисункам методами прямого и обратного набора. При прямом наборе элементы мозаики закрепляют цементным раствором или специальными мастиками на облицовываемой поверхности, на которую предварительно нанесен рисунок. Обратный набор отличается тем, что элементы мозаики набирают по рисунку и укладывают лицевой поверхностью вниз, приклеивая их к бумаге или картону клейстером. Полученную мозаичную карту переворачивают и закрепляют цементным раствором на отделываемой поверхности, шлифуют и полируют.
Таблица 4.37. Составы мозаичных растворов, объемн. ч.


Ксилолитовые покрытия (рис. 4.2) бывают эластичными и жесткими, однослойными и двухслойными. Эластичные ксилолитовые покрытия изготавливают из смеси магнезиального вяжущего и опилок, а в жесткие покрытия добавляют каменные заполнители. Последние применяют в помещениях с интенсивным передвижением людей и безрельсового транспорта.

Рис. 4.2. Ксилолитовые и поливинилацетатно-цементно-опилочные полы: а – однослойные; б – двухслойные; I – на грунте; II – на плите перекрытия; III – то же, на стяжке, уложенной на тепло– или звукоизоляционный слой; 1 – однослойное покрытие; 2 – двухслойное покрытие; 3 – стяжка; 4 – тепло– или звукоизоляционный слой; 5 – плита перекрытия; 6 – грунт основания; 7 – бетонный подстилающий слой
Вяжущими в ксилолитовых растворах являются каустический магнезит и каустический доломит. Каустический магнезит – порошок, состоящий преимущественно из оксида магния, его получают помолом магнезита, обоженного при 700… 800 °C. Каустический доломит – порошок из оксида магния и карбоната кальция; его получают помолом доломита, обожженного при 650… 750 °C.
Для затворения каустических магнезита и доломита применяют растворы хлорида и сульфата магния, сульфата железа. Наибольшей прочности достигают, используя раствор хлорида магния с содержанием MgCl2 не менее 45 % и плотностью 1,15… 1,20 г/см3. Раствор хлорида магния можно приготовить, нейтрализуя соляную кислоту каустическим магнезитом. С этой же целью применяют карналлит.
Каустический магнезит является сравнительно высокопрочным быстротвердеющим вяжущим веществом. При перемешивании с водным раствором хлорида магния плотностью 1,2 г/см3 через 1 сутки твердения его прочность при растяжении составляет не менее 1,5 МПа, а через 28 суток – 3,5… 4,5 МПа, прочность при сжатии – 40… 50 МПа и более. Начало схватывания магнезитового теста должно наступать не ранее 20 мин., конец – не позже 6 ч. после замеса.
Каустический доломит имеет меньшую прочность (10… 30 МПа). Вместо 1 кг магнезита расходуется 1,7 кг доломита.
Основным заполнителем ксилолитовой смеси являются древесные опилки. Как добавки вводят тальк, асбест, кварцевый песок, каменную муку и т. п.
Чаще используют опилки хвойных пород, получаемые при продольной распиловке леса. Крупность опилок для верхнего слоя покрытия должна быть до 2,5 мм, для нижнего—до 15 мм. Не рекомендуется использовать опилки твердых пород деревьев, опилки влажностью более 20 % и зараженные грибами.
Для получения цветных покрытий в ксилолитовые смеси добавляют щелочестойкие минеральные пигменты в количестве 3… 5 % массы сухих составляющих.
Составы ксилолитовых смесей приведены в табл. 4.38. При повышенных требованиях к чистоте помещения и внешнему виду полов в ксилолитовую смесь для отделки верхнего слоя покрытия добавляют тальк (около 6 % объема магнезита и опилок). Прочность покрытия при ударе может быть существенно повышена при введении в ксилолитовую смесь до 25 % объема магнезита асбеста 5-го или 6-го сорта с волокнами 1,5… 2 мм длиной.
Таблица 4.38. Составы ксилолитовых смесей

Примечание. Для окрашивания в ксилолитовую смесь лицевого слоя покрытия добавляют пигмент в количестве 3… 4 % объема магнезита и опилок.
Ксилолитовую смесь изготавливают в растворосмесителях, производительность которых выбирают такой, чтобы смесь была израсходована в течение не более 40 мин. после ее затворения.
Раствор хлорида магния добавляется к смеси до тех пор, пока ее подвижность не станет равной 2… 3 см по погружению стандартного конуса. Изготавливая ксилолитовую смесь и укладывая ее, следует учитывать коррозионное действие раствора хлорида магния на металлическое оборудование и детали. Необходимого сцепления ксилолитового покрытия с основанием достигают грунтовкой смесью каустического магнезита и раствора хлорида магния плотностью 1,06… 1,07 г/см3 в соотношении 1:4 по массе. Ксилолитовую смесь укладывают до начала схватывания раствора, примененного для грунтовки основания. Ксилолитовые покрытия обрабатывают циклевкой и шлифованием. Чтобы получить глянцевую поверхность, ксилолитовые покрытия протирают масляными веществами.
Внимание! Это не конец книги.
Если начало книги вам понравилось, то полную версию можно приобрести у нашего партнёра - распространителя легального контента. Поддержите автора!Правообладателям!
Данное произведение размещено по согласованию с ООО "ЛитРес" (20% исходного текста). Если размещение книги нарушает чьи-либо права, то сообщите об этом.Читателям!
Оплатили, но не знаете что делать дальше?