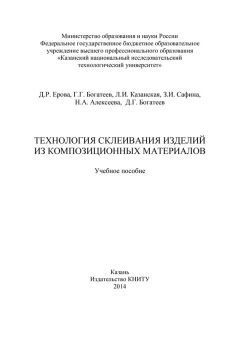
Автор книги: Людмила Казанская
Жанр: Учебная литература, Детские книги
сообщить о неприемлемом содержимом
Текущая страница: 4 (всего у книги 9 страниц)
Качество клееных изделий, а также технология приготовления и нанесения клея зависит от подбора растворителя и пластификатора. Растворителями называют химические соединения, способные растворять полимеры и отвердители клея. Применяют растворители для того, чтобы привести клеевую композицию в состояние, удобное для нанесения ее на склеиваемые поверхности.
Основным свойством растворителя, определяющим его качество, является растворяющая способность. Чем выше скорость растворения, меньше вязкость растворенной композиции при одинаковой концентрации полимера, ниже температура, обеспечивающая растворение с заданной скоростью, тем активнее растворитель. Другим важным свойством растворителей является их способность быстро смачивать поверхность и обеспечивать диффундирование молекул полимера к ее активным центрам.
Растворители оказывают значительное влияние на физикомеханические свойства клеевых прослоек, в частности на величину усадочных напряжений, водо– и теплостойкость.
Различают собственно растворители (активные) и разбавители. Если растворитель самостоятельно растворяет полимеры и смолы до весьма низкой концентрации, то разбавитель может растворять смолы только в смеси с активным растворителем или разбавлять уже растворенные продукты. Для разбавления применяют нефтепродукты, отходы химической переработки древесины и каменного угля.
Одни и те же жидкости могут быть растворителем для одних и разбавителем для других составов.
В качестве растворителей наиболее часто применяют ацетон, этиловый спирт, метиленхлорид, дихлорэтан, этилацетат, метилэтилкетон, циклогексанон. В технологии каучуковых клеев получили распространение бензин «галоша», уайт–спирит, петролейный эфир, дихлорэтан и др. [10].
Присутствие растворителя в клее замедляет процесс отверждения, снижает прочность и герметичность клеевой прослойки, так как испарение растворителя сопровождается порообразованием.
Поэтому содержание растворителя в клее должно быть ограничено минимумом, необходимым для выполнения технологических операций. Для удаления растворителя непосредственно после нанесения клея на склеиваемые поверхности применяют так называемую открытую выдержку покрытых клеем деталей. Продолжительность открытой выдержки зависит от плотности (или пористости) материала и испаряемости растворителя.
Некоторые клеевые композиции содержат в своем составе мономеры, временно являющиеся разбавителями, которые затем вступают в реакцию с основным компонентом клея (например, стирол взаимодействует с ненасыщенными полиэфирмалеинатами в полиэфирном клее). Такие реакционно-способные разбавители способствуют получению плотных и почти безусадочных клеевых пленок, что значительно улучшает физико-механические свойства клеевых соединений, в частности повышается эластичность и ударопрочность.
В результате взаимодействия между активными группами растворителей и свободными радикалами полимеров клеевая прослойка после отверждения может содержать некоторое количество остаточного растворителя, который временно играет роль пластификатора.
Пластификаторы, как самостоятельный компонент клеевой композиции с точки зрения физического взаимодействия с полимерами, близки к растворителям. В реакцию с другими компонентами клея пластификаторы не вступают, но придают полимерам пластичность. Роль и значение пластификаторов совершенно иные, чем растворителей, применение которых ограничено этапами приготовления и нанесения клея. Пластификаторы должны долго сохраняться в клеевой прослойке для того, чтобы придать ей эластичность, снизить усадочные напряжения, повысить сопротивление ударным нагрузкам. Жидкие пластификаторы снижают начальную вязкость и повышают жизнеспособность клея, облегчают введение в него наполнителя, но и снижают теплостойкость клеевой прослойки, увеличивают ее влагопроницаемость и склонность к старению.
Совместимость пластификатора с определенным полимером зависит от его химического состава и структуры полимера. При совмещении частицы пластификатора распределяются между макромолекулами или группами макромолекул соединения. В результате этого энергия межмолекулярного взаимодействия ослабляется и цепи полимера становятся более подвижными.
В качестве пластификаторов обычно используют высококипящие малолетучие жидкости, представляющие собой сложные эфиры, например: фталаты – дибутилфталат, диоктилфталат; фосфаты – трикрезилфосфат, трифенилфосфат; себацинаты – дибутилсебацинат [11].
Пластификатор должен иметь такие свойства, как незначительная летучесть, совместимость с полимером и растворителем, устойчивость к атмосферным воздействиям, химическая стабильность, морозостойкость, негигроскопичность и, кроме того, высокую температуру вспышки.
Выбирая пластификатор и определяя его количество, необходимо в каждом конкретном случае внимательно проверять влияние его на наиболее важные характеристики клеевого соединения. Иногда для обеспечения заданных свойств клея или мастики берут смесь двух или трех различных пластификаторов.
Пластифицирующими свойствами обладают и некоторые модифицирующие добавки, способные не только совмещаться, но и химически взаимодействовать с основным компонентом в клее в процессе его отверждения, в частности некоторые полиэфиры, применяемые в технологии эпоксидных клеев, низкомолекулярные каучуки и полиамиды. В результате введения модифицирующих добавок получают более стойкие к старению и более эластичные клеевые соединения.
В технологии каучуковых и битумных мастик пластификаторы часто называют мягчителями. Это различные минеральные масла, неочищенные нефтепродукты и т. п., повышающие эластичность композиций.
Переход клея из жидкого состояния в твердое происходит в результате испарения растворителей, охлаждения расплавов и, главное, реакций поликонденсации или полимеризации. При нормальной температуре процессы поликонденсации и полимеризации жидких смол обычно протекают медленно – в течение нескольких недель или месяцев, с повышением температуры они значительно ускоряются.
Чтобы осуществить реакцию отверждения клея (как при нормальной, так и при повышенной температуре) в состав клея часто вводят отвердители – катализаторы и инициаторы. Различие между ними в том, что катализаторы (кислоты, соли, основания) участвуют только в промежуточных этапах полимеризации (поликонденсации) и не входят в состав образующихся полимеров, в то время как инициаторы (органические и неорганические перекиси) остаются в их составе. Действие инициаторов заключается в их распаде с образованием частей молекул (свободных радикалов), которые, соединяясь мономером, повышают его способность к полимеризации. Активность инициаторов усиливают, вводя так называемые ускорители – вещества, не участвующие в реакции. Инициаторами могут быть перекись бензоила или гидроперекись изопропилбензола, ускорителями – соли металлов, например нафтенат кобальта.
В процессе отверждения клеев и мастик выделяется тепло, которое при большом объеме состава может привести к его перегреву, к нарушению структуры клея и значительной усадке клеевого слоя. Поэтому для обеспечения необходимой жизнеспособности клея при введении отвердителя в клеевую композицию предпринимают некоторые меры для отвода выделяющегося при реакции тепла (водяное охлаждение, ограничение объема реагирующих веществ). Скорость отверждения имеет большое значение для склеивания. Она зависит не только от температуры, но и от содержания в композиции растворителей, пластификаторов, наполнителей. При медленном испарении растворителя действие отвердителей несколько ограничивается. Если наполнитель обладает кислотными или щелочными свойствами, то он может усиливать или ослаблять (нейтрализовать) действие отвердителей, также имеющих кислую или щелочную реакцию.
При механизации и автоматизации процессов склеивания, когда ускоренное отверждение необходимо, применяют интенсивное нагревание или сильнодействующие отвердители. Однако использовать эти способы можно не всегда: некоторые склеиваемые материалы не допускают нагревания до высокой температуры, а введение сильнодействующего отвердителя иногда очень сокращает жизнеспособность клея.
В настоящее время во многих странах пытаются получить клеи ускоренного отверждения, содержащие микрокапсулы диаметром 20 – 150 мк из тончайших пленок, заполненные быстродействующими отвердителями Пленочные оболочки разрушаются при склеивании под влиянием тепла или давления. Такие клеи транспортабельны, длительно жизнеспособны (практически неограниченно). В составе сухих клеев микрокапсулы могут содержать и растворители, способствующие быстрому переводу клея в жидкое состояние.
В некоторых случаях отверждение клеев может происходить под влиянием влаги, адсорбированной на склеиваемых поверхностях. Так отверждаются, например, цианакрилатные клеи. В других случаях (при склеивании металлов) катализатором служит сам металл. При нанесении клея на поверхность очищенной детали сразу же начинается процесс отверждения. Необходимым условием этого является отсутствие кислорода воздуха на поверхности склеивания (анаэробные клеи) [5].
Переход каучуковых клеев и мастик в неплавкое и нерастворимое состояние происходит в результате вулканизации – процесса, схожего с отверждением. Под вулканизацией понимают такой процесс образования химических связей между макромолекулами, в результате которого получается полимер пространственного строения, обладающий весьма высокой эластичностью. Таким образом вулканизацию можно рассматривать как один из видов структурирования полимеров.
Для вулканизации каучуковых мастик и клеев используют органические и неорганические перекиси, окислы металлов. Вулканизацию ускоряют, добавляя небольшое количество органических соединений (дифенилгаунидин, меркаптобензотиазол и др.), называемых ускорителями вулканизации. Вулканизация иногда возможна и без применения вулканизующих агентов – при действии только нагревания [10].
Для того чтобы продлить срок сохранности исходных продуктов для клеев, в них вводят вещества, тормозящие или полностью прекращающие процессы полимеризации. Такие вещества называют ингибиторами. Как правило, ингибиторы добавляют в весьма малых количествах.
В качестве ингибиторов стирола, метилметакрилата, акрилонитрила применяют гидрохинон, ароматические амины и некоторые нитросоединения. Реакция поликонденсации ряда смол (феноло-формальдегидных, резорцино-формальдегидных) замедляется в присутствии растворителей – ацетона, этилового спирта. Избыток этих растворителей способствует длительной сохранности смол. Стабильность карбамидных смол обеспечивают добавки многоатомных спиртов.
На свойства клеевых соединений может влиять старение полимеров – процесс, при котором под влиянием различных факторов изменяется состав и структура молекул. При старении различают деструкцию – расщепление макромолекул и дополнительное структурирование (сверх необходимого для нормального отверждения). В том и другом случаях необходимы меры по предотвращению отрицательных последствий старения.
Для замедления процессов старения, развивающихся в полимерах под влиянием тепла, кислорода воздуха, солнечного облучения, в состав некоторых синтетических клеев и мастик вводят небольшие добавки противостарителя, или стабилизатора.
Различают блокирующие и экранирующие стабилизаторы. Блокирующие стабилизаторы легко распадаются на отдельные группировки, блокируют, т. е. насыщают свободные связи макромолекул, возникшие в процессе деструкции. Например, блокирование концевых групп сонолимеров стирола может осуществляться эпихлоргидрином или этиленимином. Экранирующие стабилизаторы поглощают источники старения, препятствуя их влиянию на полимер. Такими стабилизаторами могут быть вещества, окисляющиеся с более высокой скоростью, чем полимер (многоатомные фенолы, амины и соединения, содержащие сульфгидрильные группы).
Большое значение имеют стабилизаторы в технологии каучуковых мастик и клеев, особенно при длительном воздействии высокой температуры и кислорода воздуха на клеевые соединения.
6.3.2 Синтетические термореактивные клеиСинтетические термореактивные клеи отверждаются в результате реакций поликонденсации или полимеризации в условиях относительно высокой температуры (в пределах до +100 °C) в большинстве случаев.
Феноло-формальдегидные смолы, являющиеся основным компонентом одноименных клеев, представляют собой продукт реакции поликонденсации фенола и его гомологов (крезолов, ксиленолов) с формальдегидом в присутствии кислых или щелочных катализаторов.
Для клеев используют, как правило, резольные смолы. Отверждение их происходит в несколько стадий. На 1 стадии смола называется резолом. Она хорошо растворяется в щелочах, ацетоне, спиртах, этилацетате. Нагревание резола переводит его во 2 стадию – резитол, который не растворяется, а лишь набухает в некоторых органических растворителях и слабых растворах щелочей.
Дальнейшее нагревание резитола переводит его в 3 стадию – резит, неплавкий и нерастворимый продукт. Переход в стадию 3 сопровождается значительной усадкой полимера.
Резиты – это твердые, хрупкие вещества, подверженные усадке, с хорошими диэлектрическими свойствами и химической стойкостью.
Отверждение феноло-формальдегидных клеев возможно при повышенной температуре без введения отвердителей (горячий способ) и при нормальной температуре (15–17 °C) с отвердителями (холодный способ).
Скорость отверждения в первом случае существенно зависит от температуры в клеевом шве. Так, при 130 °C фенолоформальдегидный клей отверждается за 13 мин, а при 155 °C – за 3 мин.
При склеивании холодным способом клей отверждается в течение 24–48 ч. В качестве отвердителей используют бензол– и толуолсульфокислоты. Промышленное применение получил отвердитель – смесь сульфонафтеновых кислот, так называемый контакт Петрова, представляющий собой побочный продукт переработки нефти.
Для растворения феноло-формальдегидных клеев применяют ацетон, спирт, воду. В промышленности используют преимущественно водорастворимые и спирторастворимые смолы. Первые предпочтительны для склеивания древесины как более дешевые и менее дефицитные.
Пластификаторы для феноло-формальдегидных клеев не применяют ввиду плохой совместимости их с полимером. Для наполнения клеев используют древесную муку, хлопковые очесы, асбест, молотую скорлупу орехов и фруктовых косточек. Наполненные клеи применяют, в основном, для склеивания древесины.
Свойства соединений на феноло-формальдегидных клеях зависят от способа отверждения и содержания низкомолекулярных компонентов. Клеи холодного отверждения образуют хрупкие прослойки, обладающие значительной (6–8 %) усадкой. Такие прослойки растрескиваются из-за появления в них внутренних напряжений.
Соединения на клеях горячего отверждения более стойки к колебаниям температуры и долговечны.
Феноло-формальдегидные клеи и соединения на них водо– и теплостойки. Отливки клея КБ-3, например, лишь незначительно изменяют прочность при длительном вымачивании в воде. Набухание при этом за 3–5 месяцев составляет всего 8–10 %. Одновременное увлажнение и нагревание (до кипячения) в воде снижает прочность отливок на 30–40 %.
Водо– и теплостойкость соединения зависят от состава полимера и его концентрации в клее. Менее стойки соединения на клеях, изготовленных на основе так называемых суммарных фенолов (смесь фенола и его гомологов) и на клеях с малой концентрацией полимера (20–30 %). Термическое разложение фенолоформальдегидных полимеров начинается при температуре около 200 °C.
В процессе приготовления клея и склеивания выделяется свободный фенол. Это весьма токсичное вещество, которое необходимо немедленно удалять. Однако наряду с вредным в технологическом отношении действием повышенное содержание фенола улучшает некоторые физические свойства клеевых соединений. Проведенными в последнее время исследованиями установлено, что увеличение содержания свободного фенола в феноло-формальдегидных смолах до 10–15 % повышает прочность, долговечность, термостабильность резитов.
Как уже говорилось, феноло-формальдегидные смолы применяют в основном для склеивания древесины, древесных пластиков и плит. Отверждаются они холодным и горячим способами.
Для склеивания металлов и пластмасс применяют фенолоформальдегидные смолы, модифицированные поливинилбутиралем (клеи БФ). Отдельные марки клеев БФ различаются соотношением этих двух основных компонентов, феноло-формальдегидная смола придает соединениям прочность и термостойкость, а поливинилбутираль – эластичность и вибрационную стойкость. Так, в составе широко известного клея БФ-2 на 1 вес. ч. фенолоформальдегидной смолы приходится 1 вес. ч. поливинилбутираля, а в составе клея БФ-4 на 1 вес. ч. смолы – 5,67 вес. ч. поливинилбутираля.
Клей БФ-2 применяют для склеивания изделий из фарфора, фаянса, стекла, дерева, многих металлов и пластмасс. Изделия из целлулоида, поливинилхлорида, органического стекла, полистирола клеем БФ-2 не склеиваются.
Перед склеиванием поверхность изделий тщательно очищают от грязи, пыли, ржавчины, следов жира и просушивают. На обе склеиваемые поверхности наносят тонкий слой клея и высушивают на воздухе. Затем наносят второй слой клея и слегка подсушивают. После этого склеиваемые части соединяют так, чтобы было обеспечено плотное соединение. Склеивание производят при температуре 100–150 °C в течение 1,5–2 ч. После прогревания изделие охлаждают в скрепленном состоянии до комнатной температуры.
Можно склеивать изделия и при комнатной температуре, но в этом случае изделие должно быть выдержано в скрепленном состоянии в течение 3–4 суток.
Соединения металлов на клеях типа БФ обладают высокой прочностью: сопротивление, сдвигу стальных пластинок составляет 200–350 кг/см², чугунных и дюралюминиевых – 150–300 кг/см². При склеивании пластмасс прочность соединения часто превышает прочность самих склеиваемых материалов. Недостатком клеев БФ является относительно невысокая термостойкость.
Для повышения теплостойкости и эластичности фенолоформальдегидные смолы модифицируют синтетическими каучуками, полиамидами и кремнийорганическими соединениями. Кроме того, феноло-формальдегидные смолы модифицируют полихлоропреном в сочетании с полиамидом. Однако такие клеевые композиции менее теплостойки, чем, например, широко известный фенолонитрильный клей ВК-32-200. Этот клей состоит из двух компонентов: фенолоформальдегидной смолы (лака ИФ) и раствора резиновой смеси (бутадиенакрилонитрильного каучука СКН-40), взятых в соотношении 7:180. Рабочая вязкость его 200–700 спз. Клей приготовляют не ранее чем за 24 ч до применения. Наносят клей двумя слоями.
Первый слой выдерживают 30 мин при нормальной температуре, второй – 90 мин при 60 °C. Отверждается клей при 180 °C в течение 1–2 ч. Требуемое давление при склейке 6–20 кг/см², расход клея 150–200 г/м² на каждый слой. Клей ВК-32-200 может быть получен и в виде пленки, применение которой в отдельных случаях значительно упрощает процесс склеивания. Клеем ВК-32-200 можно склеивать сталь, алюминий, титановые сплавы, стеклотекстолит, пенопласты. Прочность склеивания, стали и алюминия (сопротивление сдвигу) достигает 200 кг/см², а стеклотекстолита 100 кг/см². При длительном (400 ч) нагревании склеенных металлических изделий прочность соединения остается выше 100 кг/см², что можно считать удовлетворительным. Соединения на клее ВК-32-200 устойчивы и к переменным температурам в интервале от –60 до +200 °C [10].
Аналогичными технологическими характеристиками обладают феноло-каучуковые клеи ВК-3 и ВК-4 отличающиеся повышенной эластичностью и улучшенными физико-механическими свойствами. Клеем ВК-3 склеивают металлы и неметаллические материалы, работающие в интервале температур от –60 до +200 °C. Клей готовят смешением спиртового раствора феноло-формальдегидной смолы с раствором резиновой смеси на основе акрилонитрильного каучука. В отличие от клея ВК-32-200 он содержит добавки, повышающие эластичность, применять его можно в жидком виде и в виде пленки. Соединения на клее ВК-3 устойчивы к воздействию воды, растворов солей, бензина, масел, спирта. Клей не вызывает коррозии цветных и черных металлов.
Клей ВК-4 более теплостоек, чем клей ВК-32-200, соединения металлов на нем можно эксплуатировать при 275–300 °C. Применяется в жидком виде и в виде пленки, а также в сочетании подслоя из жидкого клея с пленкой.
С помощью клея ВК-4 можно склеивать различные стали, титановые и другие сплавы. Отверждение клея происходит при 200 °C в течение 2 ч при удельном давлении 10–20 кг/см².
Повышенной теплостойкостью отличаются клеи, модифицированные кремнийорганическими соединениями.
Совмещением феноло-формальдегидных смол с поливинилацеталями и алкоксисиланом получают клеи ВС-ЮТ и ВС350, предназначенные для склеивания металлов, стеклотекстолитов различных марок, а также теплостойких пенопластов. Основой этих клеев, служит композиция ВС-10, состоящая из поливинилацеталя и алкоксисилана, которые при нагревании вступают в реакцию и образуют полимер пространственного строения. Фенолоформальдегидная смола также реагирует с алкоксисиланом, в результате образуется блоксополимер с высокой теплостойкостью. Соединения на клеях ВС-ЮТ и ВС-350 обладают хорошей водостойкостью и характеризуются высокими показателями длительной прочности. Масло, керосин и бензин практически не влияют на свойства клеевых соединений.
Клей ВС-ЮТ и ВС-350 применяют для крепления фрикционных накладок при ремонте строительных машин, а также для вклеивания втулок и наклеивания лент при выводе износа трущихся частей машин, нагревающихся в эксплуатации.
Клей ВС-10Т представляет собой раствор поливинилацеталя, феноло-формальдегидной смолы и алкоксисилана в смеси органических растворителей. Концентрация сухого вещества составляет 15–30 %, вязкость клея колеблется в пределах 50–120 сек по вискозиметру ВЗ-1.
Клей наносят на очищенные и обезжиренные поверхности двумя слоями из расчета 70 г сухого вещества на 1 м² склеиваемой поверхности. Склеивание производят при 180–200 °C в течение 2 ч под давлением 0,5–2 кг/см².
Прочность клеевого соединения стали достигает 180 кг/см² и после длительного нагревания при 200 °C остается выше 60 кг/см². Клей ВС-ЮТ устойчив к воздействию масел и жидких топлив, не токсичен, не вызывает коррозии металлов. Хранят клей в закрытой таре в течение 6 месяцев и более, при загустевании разбавляют до необходимой консистенции.
Клей ВС-350 отличается от клея ВС-ЮТ тем, что содержит феноло-формальдегиднофурфурольную смолу и обладает более высокой (до 350 °C) теплостойкостью. Технология склеивания такая же, как и для клея ВС-ЮТ.
За рубежом для соединения металлов применяют фенолоформальдегидные клеи в комбинации с полиамидной пленкой. Основой пленки часто служит стеклоткань, пропитанная смолой.
На поверхность металла наносят сначала слой фенолоформальдегидной смолы и подсушивают его в течение 30 мин, затем накладывают полиамидную пленку, соединяют детали и выдерживают соединения под давлением 0,7-7 кг/см² в течение 2 мин при температуре 220 °C. Прочность соединения при нормальной температуре до 350 кг/см², в результате длительного воздействия нагрузки предел прочности снижается более чем в 3 раза. Длительное нагревание (до 150 °C) снижает кратковременное сопротивление сдвигу до 200-230 кг/см².
Несмотря на давность применения феноло-формальдегидных клеев свойства их изучены еще недостаточно полно. Остается предметом дискуссий механизм образования пространственной сетки и адгезионных связей в резитах. Ведутся поиски новых способов модифицирования клеев [2].
В строительстве феноло-формальдегидные клеи применяют для изготовления столярных изделий, деревянных конструкций, деталей сборных домов, для склеивания трехслойных панелей, ремонта машин, крепления теплоизоляции, при отделке зданий (устройстве пола, перегородок и т. п.).
Правообладателям!
Это произведение, предположительно, находится в статусе 'public domain'. Если это не так и размещение материала нарушает чьи-либо права, то сообщите нам об этом.