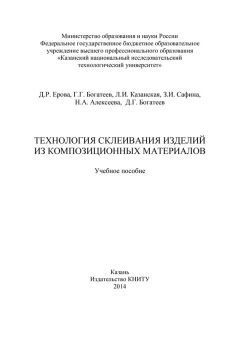
Автор книги: Людмила Казанская
Жанр: Учебная литература, Детские книги
сообщить о неприемлемом содержимом
Текущая страница: 9 (всего у книги 9 страниц)
8.2 Приготовление клея
Процесс требует особого внимания, так как ошибки на этом этапе сделают бессмысленной всю последующую работу. Если клей хранился при пониженной температуре, то перед тем, как им воспользоваться, ему следует дать согреться до температуры применения, чаще всего – до комнатной, но для некоторых, например клеев-расплавов, эта температура будет значительно выше. Приготовление клея заключается в смешение его отдельных компонентов в соотношение и последовательности, определяемых рецептурой. Для получения максимальной прочности клеевого соединения необходимо выдержать точное соотношение этих компонентов. Особенно это относится к случаям каталитических реакций (отверждение эпоксидных смол отвердителями). Недостаток отвердителя приведет к неполному отверждению смолы, что проявится повышенной хладотекучестью и низкой адгезией, избыток же даст хрупкий отвержденный материал и также низкую адгезию. Помимо всего, непрореагировавший со смолой отвердитель вызывает коррозию склеиваемых металлов.
Основное правило при смешении – введение отвердителя или ускорителя непосредственно перед применением клея. В ряде случаев потребитель получает уже готовый клей, так что необходимость в этой операции отпадает.
8.3 Подготовка склеиваемых поверхностей
Подготовка соединяемых поверхностей является одной из важнейшим операций в технологии склеивания. Она заключается в подготовке их друг к другу к специальной обработке или очистки. Ровные, хорошо подогнанные поверхности склеиваемых материалов необходимы для получения тонкой равномерной по толщине клеевой прослойки. Особенно тщательная подгонка поверхности должна быть при склеивании клеями, в момент запрессовки обладают как малые, так и слишком большой текучестью. Способ обработки поверхности зависит от типа пластмассы и природы клея. Композиционные пластики и пластмассы на основе отвержденных реактопластов перед склеиванием обрабатывают преимущественно механическим способом. При этом не только увеличивается истинная площадь склеивания и на поверхности материала обнажаются частицы, более легко склеивающиеся наполнители, но и удаляются различные загрязнения, смазки и т.д.
Перед нанесением слоя обработанные поверхности промывают растворителем (кетоны, бензин) или протирают тампоном, смоченным в растворителе и сушат при 293–238 К в течении нескольких минут.
Наряду с механической обработкой для некоторых типов отвержденных реактопластов применяют химическую обработку. Например, фенопласты обрабатывают ацетоновым раствором оксипроизводных бензола и других ароматических соединений.
Эффективный способ повышения прочности склеивания – нанесение подслоев (грунтов) из разбавленных растворов полимеров. Одним из современных способов подготовки поверхности пластиков, упрочненных волокнистым наполнителем, служит нанесение перед формованием детали на участки, подлежащие склеиванию, слоя ткани из термопластов или стеклянной ткани, покрытой фторопластом или кремнийорганическим полимером, и удаление этого слоя непосредственно перед нанесением клея. Эти защитные слои, называемые иногда «жертвенными», защищают пластик на стадиях переработки, предшествующих склеиванию, и способствуют созданию шероховатого рельефа поверхности.
Применение клеев, которые адсорбируют жировые и масляные загрязнения, исключает из технологического процесса операции очистки.
Обработку поверхностей термопластов также производят механическим, химическим, физическим или комбинированными способами.
К физическим методам обработки поверхностей через склеивание относятся: электрическая обработка, в том числе наиболее эффективная ее разновидность – обработка электронно-возбужденным инертным газом ультрафиолетовое и радиоактивное облучение.
8.4 Склеивание
На обе склеиваемые поверхности с помощью кисти или шпателя наносят клей в один или два слоя.
Приложенное давление (запрессовка) во время приведения соединяемых поверхностей в контакт обеспечивает фиксирование деталей, достижение более полного контакта между клеем и склеиваемым материалом и созданием клеевой прослойки оптимальной толщины. Чем меньше толщина клеевой прослойки, тем выше прочность соединения при равномерном отрыве или сдвиге.
Давление при склеивании создают различными способами, зависящими от конструкции изделия, формы и размеров шва, типа клея, серийности производства: с помощью груза, а пневматических или гидравлических прессах, с помощью вакуумного мешка, в прессах с винтовыми или экстрентиловыми зажимами, стягивающими лентами, в сборочных стапелях, дополнительно оборудованных различными зажимами, устройствами [13].
Отверждение клеев на основе реактопластов является наряду с подготовкой поверхности важнейшей операцией в технологии склеивании. Выбор режимов (температуры, продолжительности, давления) отверждения клея зависти не только от его природы, но и от типа соединяемого материала и условий эксплуатаций изделий.
Нагрев склеиваемых участков производят в термошкафу, контактными нагревателями высокочастотным способом или с помощью ультразвука. Давление во время отверждения необходимо увеличить по сравнению с давлением в момент запрессовки, если повышается противодавление летучих продуктов в клеевом шве.
При склеивании термопластичными клеями, содержащими растворители, существенное значение имеет удаление растворителя (особенно при склеивании газонепроницаемых материалов), так как остаточный растворитель значительно снижает прочность клеевого соединения. Поэтому на склеиваемые поверхности термопластичный клей низкой вязкости наносят не менее двух слоев с сушкой каждого клеевого слоя до контактирования склеиваемых деталей. Клеевой слой можно считать высохшим, когда он становится прозрачным. Только после этого можно прижать детали друг к другу. В зависимости от природы клея прижатие может осуществляться приглаживанием или зажатием струбцинами. Затвердевание термопластичных клеев происходит в результате испарения растворителя или охлаждения зоны шва.
Склеивание листовых материалов встык трудноосуществимо и нерационально, так как при воздействии незначительного изгибающего напряжения оно разрушается. Надежно ведут себя подвергающиеся сдвигу при растяжении соединения внахлестку. Нахлестка может быть одинарной, одинарной с накладкой, двойной или с подсечкой. Соединения на ус и ступенчатой нахлесткой позволяют сохранить толщину материала по месту стыковки деталей. Они более прочны на сдвиг и изгиб, чем простая нахлестка, однако требуют очень тщательной подгонки склеиваемых стыков.
8.4.1 Технология выполнения комбинированных клееклепаных соединенийТехнология получения комбинированных клеевых соединений заключается в следующем: на обе склеиваемые поверхности наносят жидкий подслой эластичного клея (ВК-3 или ВК-32-200), который просушивают в течение времени 1800 с при комнатной температуре и затем в течение 5400 с при температуре 65 °C, после этого на обе поверхности наносят по одному слою клея ВС-10Т, который просушивают в течение 5400 с при комнатной температуре, после чего поверхности соединяют и осуществляют отверждение клеевого соединения в течение 6000 с при температуре 180…185 °C и давлении 0,08 МПа.
Соединения, выполненные на комбинации клеев, незначительно уступают в прочности при сдвиге и приближаются по прочности при неравномерном отрыве к клеевым соединениям на клее ВК-3 и превосходят клеевые соединения на клее ВС-10Т. Такие соединения обладают хорошей водостойкостью. Воздействие воды в течение 30 сут. практически не влияет на прочность и эластичность клеевых соединений.
В качестве эластичного подслоя в комбинированных соединениях высокой теплостойкости и термостабильности можно использовать клей ВК-32-200.
Удельное давление формования можно определить, используя следующую формулу:

где N – количество заклепок на заданной площади; Fп. с – площадь соединений; Т – усилие прессования; α – коэффициент, учитывающий неравномерность распределения давления.
8.4.2 Технология выполнения клеесшивных и клееигольчатых соединенийСуществует ряд прогрессивных способов выполнения сшивных и игольчатых соединений.
Сшивные соединения стеклопластика на основе ткани ТСУ8/3-ВМ – 78 выполняют нитками из органоволокон от одного до пяти рядов. После сшивки проводят отверждение связующего ЭДТ-10.
Игольчатые соединения осуществляют двумя способами: запрессовкой игл в стыковой шпангоут и механической обработкой предварительно выдавленных ребер на многошпиндельном полуавтомате. Последующее соединение выполняют в процессе намотки оболочки и одновременной замотки стыковых и игольчатых элементов.
Сравнительная характеристика прочности сшивных соединений представлена на рис. 14. Анализируя результаты испытаний соединений на прочность, выяснили, что с уменьшением диаметра отверстий под КЭ увеличивается не только прочность шва, но и долговечность. Поэтому дальнейшая отработка технологии изготовления сшивных и игольчатых соединений и создание специализированного полуавтома-тического оборудования для их выполнения являются насущной задачей, решение которой позволит резко расширить объем применения КМ в силовых конструкциях.

Рис. 14. Сравнительная характеристика прочности сшивных и и гольчатых соединений: а – коэффициент увеличения прочности; б – коэффициент увеличения долговечности; в – сравнительная характеристика соединений; 1 – клеевые; 2 – клепаные; 3 – резьбовые; 4 – игольчатые (запрессовка); 5 – игольчатые (механическая обработка); г – тип образца
8.5 Испытания клеевых соединений
На результаты испытания оказывают влияние многие факторы, важнейшими из которых являются:
– шероховатость склеенных поверхностей: если она превышает нескольких мкм, то в этом случае не удастся получить достоверные значения модуля сдвига;
– толщина шва оказывает большое влияние на прочность клеевого соединения. При малой толщине клея возможно образование «голодного» клеевого шва, и прочность такого соединения будет невысокой. Неравномерность толщины клеевого шва по площади склеивания также приводит к уменьшению прочности склеивания.
Регулировать толщину клеевого шва достаточго сложно. Для обеспечения заданных толщин применяют калибровочные прокладки или стеклянные шарики, которые равномерно распределяют в клеевом шве. Более простым способом обеспечения равнотолщинности является применение прессов (для плоских деталей) или вакуумных мешков (для изделий сложной геометрической формы).
8.5.1 Испытания на сдвигИзвестно, что клеевые материалы хорошо работают в условиях сдвиговых нагрузок, и поэтому существует большое количество разнообразных методов испытаний клеевых соединений при сдвиге.
Схема испытаний при сдвиге приведена на рис. 15. Два образца в форме прямоугольных пластинок склеиваются между собой (площадь склеивания S = b 10). В зависимости от деформационных характеристик клеевого шва [F=f{Al)] могут быть определены следующие параметры:
– разрушающая нагрузка F и средние разрушающие напряжения;
– модуль упругости при сдвиге G определяют через тангенс угла наклона касательной F=f{kl) при условии, что разрушение носит коге-зионный характер;
– предел упругости при напряжении т и деформация е^: (для жестких клеев). Для клеевых материалов с высокими деформационными характеристиками целесообразнее определять данные показатели традиционным способом;
– энергия диссипации Gcis, которая также определяется графически и характеризует способность клеевого материала рассеивать энергию. Этот показатель позволяет прогнозировать долговечность и работоспособность клеевого соединения.

Рис. 15. Способы испытания на сдвиг
8.5.2 Испытания на изгиб
Чаще всего используется трехточечный метод испытания прочности при изгибе. Схема нагружения показана на рис. 16. Данный метод не применяется для жестких подложек, т.к. результаты аналогичны простому сжатию. Но если одна из деталей, подлежащих склеиванию, является гибкой, то испытания позволяют имитировать реально встречаемые условия нагружения. Например: при креплении листовых материалов (пластиковые панели, имеющие декоративные функции); расслоение многослойных конструкций, слоистые панели, лыжи и пр.
Схема четырехточечного изгиба испытания прочности используется в том случае, если одна из склеиваемых деталей является жесткой и хрупкой, например стекло. В этом случае, для того чтобы избежать ее повреждения в процессе испытаний, в клеевом шве делают надрез. Это позволяет задать нужное исследователю направление развития трещины.

Рис. 16. Схема испытаний на изгиб
8.5.3 Испытания на отдир
Испытание предела прочности при отдире (отслаивании) состоит в отделении гибкого элемента соединения, приклеенного к другому гибкому или более жесткому элементу. Образец нагружают под углом 90 или 180°. Прочность на уголковый отдир (отслаивание под углом 90°) для соединений металлов определяют на образцах, склеенных из двух полос толщиной 0,5 мм, размером 30X130 мм и участком склеивания длиной 100 мм. Несклеенные концы полос (30 мм) отгибают вручную под углом 90°, закрепляют в зажимы испытательной машины и испытывают при растяжении со скоростью 20–25 мм/мин. При этом определяют среднее погонное отдирающее усилие в Ньютонах на 1 см ширины образца. Для клеевых соединений многих неметаллических материалов испытание на отслаивание является основным, а иногда и единственно возможным (ткани, пленки, теплоизоляционные материалы и т. д.). Отечественными методиками предусматривается отслаивание только под углом 180°. Такое испытание регламентировано для клеевых соединений резины с металлом, резины с резиной, тканей с фанерой, рыхловолокнистой теплоизоляции с металлом и др. Ширина образцов должна составлять 25 мм при склеивании резин и ткани, 50 мм для склеивания ткани и фанеры, а также теплоизоляции с металлом. Скорость отслаивания склейки резины с металлом 100 – ПО мм/мин, резины с резиной 200 мм/мин. Среднее усилие отслаивания (в Ньютонах на 1 см ширины образца) рекомендуется определять по диаграмме, вычерчиваемой установленным на испытательной машине самописцем.
Длительная прочность в настоящее время определяется только для клеевых соединений металлов. Испытания проводят при длительном статическом нагружении растягивающим усилием образцов с односторонней нахлесткой (ГОСТ 14759–69). Обычно для установления длительной прочности при сдвиге применяют машины рычажного типа. Условный предел длительной прочности определяют, проводя последовательные испытания при различных постоянных нагрузках вплоть до разрушения образца и вычисляя среднее по площади склеивания напряжение сдвига, вызывающее разрушение за определенное время (обычно 500 ч).
ЗАКЛЮЧЕНИЕ
Склеивание – один из эффективных способов соединения современных конструкционных материалов. Преимущество склеивания по сравнению с заклепочными и болтовыми соединениями в том, что оно не ослабляет рабочее сечение элементов отверстиями, врезками и поэтому обеспечивает более равномерное распределение напряжений в узлах под воздействием нагрузок. Склеивание в отличие от пайки и сварки также позволяет избежать термического ослабления материалов в месте соединения. Клеи вводят иногда в заклепочные, сварные и винтовые соединения для того, чтобы повысить их прочность и несущую способность, особенно при повторностатических, ударных и знакопеременных нагрузках. Синтетическими клеями соединяют разнородные материалы, для которых другие виды скреплений почти неосуществимы. В некоторых случаях склеивание используют, чтобы обеспечить герметичность и уменьшить возможность коррозии материалов в месте соединения.
Практическая ценность клеев определяется совокупностью таких данных, как прочность, долговечность, стойкость к температурным, химическим и влажностным воздействиям, простота технологии. Выбор клея производится только после всестороннего анализа всех этих данных.
Появление новых синтетических полимеров, обладающих улучшенными характеристиками, несколько затрудняет систематизацию клеев и разработку общих правил обращения с ними. Для работы с клеями и мастиками необходимо приобрести определенные навыки и знания, которые нужны для освоения физических, химических и технологических основ процессов склеивания.
КОНТРОЛЬНЫЕ ВОПРОСЫ
1. Области применения технологии склеивания в современном производстве.
2. Физический смысл склеивания.
3. Процесс образования адгезионного соединения при склеивании материалов.
4. Принципы выбора клея.
5. Преимущества и недостатки склеивания по сравнению с другими видами соединения материалов.
6. Требования, предъявляемые к клеям.
7. Классификация, типы и назначение клеев.
8. Свойства и применение клеев животного происхождения.
9. Общая характеристика клеев растительного происхождения.
10. Виды синтетических клеев.
11. Компоненты синтетических клеев.
12. Основные свойства и области применения синтетических термореактивных клеев.
13. Клеи на основе феноло-формальдегидных смол.
14. Эпоксидные клеи холодного и горячего отверждения.
15. Основные свойства и области применения синтетических термопластичных клеев.
16. Типы клеевых соединений.
17. Технология процесса склеивания.
18. Испытания клеевых соединений.
СПИСОК ИСПОЛЬЗУЕМЫХ ИСТОЧНИКОВ
1. Г.В. Мотовилин. Склеивание: параллельный словарь-справочник.: англ. – нем. – рус., ISBN 5-02-027408-9, 2000 г.
2. А.П. Петрова. Клеящие материалы. Справочник. – М.: ЗАО «Редакция журнала «Каучук и резина», 2002. – 196 с.
3. Э. Кинлок. Адгезия и адгезивы. Наука и технология. – М.: Мир, 1991. – 484 с.
4. В.А. Белый, Н.И. Егоренков, И.М. Плескачевский. Адгезия полимеров к металлам. – Минск, Наука и техника, 1971.
5. Д.И. Бокарев. Сварка пластмасс и склеивание металлов: учебн. пособие. – Воронеж, Ворон. гос. техн. ун-т, 2004. – 172 с.
6. http://www.znaytovar.ru/s/Klassifikaciya-kleev.html
7. В.Н. Волынский. Технология клееных материалов: учебн. пособие по спец. "Технология деревообработки". – Архангельск, 1998. – 298 с.
8. С.М. Кудрявцев, С.В. Логинов, В.И. Крылов и др. Прогрессивные технологические процессы сборки с применением адгезивов (клеев и герметиков) в машиностроении. – Минск, 1990. – 49 c.
9. Б.А. Степанов. Материаловедение для профессий, связанных с обработкой дерева: учебник. – М.: ПрофОбрИздат, 2001. – 328 с.
10. Л.Х. Айрапетян, В.Д. Заика, Л.Д. Елецкая, Л.А. Яншина. Справочник по клеям. – Л.: Химия, 1980. – 304 с.
11. Г.В. Мовсисян. Справочник по клеям. – Издательство Химия, Ленинградское отделение, 1980. – 304 с.
12. Х. Ли, К. Невилл. Справочное руководство по эпоксидным смолам. Пер. с англ. / Под ред. Н.В. Александрова. – М.: Энергия, 1973. – 416 с.
13. Ж.Ж. Вильнав. Мир материалов и технологий. Клеевые соединения. – М.: Техносфера, 2007. – 384 с.
Правообладателям!
Это произведение, предположительно, находится в статусе 'public domain'. Если это не так и размещение материала нарушает чьи-либо права, то сообщите нам об этом.