Текст книги "100 знаменитых изобретений"
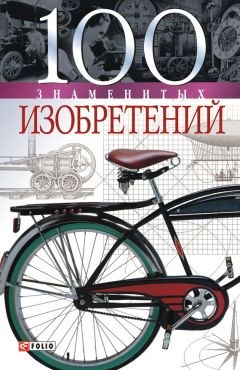
Автор книги: Владислав Пристинский
Жанр: Публицистика: прочее, Публицистика
сообщить о неприемлемом содержимом
Текущая страница: 45 (всего у книги 47 страниц)
Электрическая сварка
Сварка представляет собой процесс создания неразъемного соединения твердых материалов. Она происходит при местном сплавлении или совместном пластическом деформировании свариваемых частей.
Простейшие приемы сварки применялись, по оценкам историков, еще в VIII–VII тысячелетии до н. э. Медные изделия предварительно подогревались, а затем сдавливались. Позже изделия из меди, бронзы, свинца, золота и серебра соединялись при помощи литейной сварки. При этом соединяемые детали заформовывали, подогревали и в месте соединения заливали расплавленным металлом. Для изделий из железа и его сплавов применялась так называемая кузнечная или горновая сварка. Их нагревали до «сварочного жара», а затем проковывали. Вплоть до конца XIX в. применялись только эти способы сварки.
Развитие электротехники вызвало к жизни новый способ соединения металлов – электрическую сварку, предложенную в 1867 г. американским электротехником Томсоном.
Томсон пропускал электрический ток большой силы и небольшого напряжения через два куска металла, предназначенных для сварки и расположенных так, чтобы они соприкасались в месте сварки. Сопротивление прохождению тока в месте стыка кусков металла вызывало выделение тепла, достаточное для сварки металлических частей. Однако этот способ сварки металлов, названный позже контактным, не получил в это время широкого распространения.
Русские изобретатели электрической сварки H. Н. Бенардос и Н. Г. Славянов пошли по другому пути.
Для электросварки они применили электрическую дугу, т. е. использовали явление, при котором между сближенными угольным и металлическим электродами возникает яркое пламя огромной температуры, которое и расплавляет металл. Ее открыл в 1802 г. русский ученый В. В. Петров. Он рекомендовал использовать свое открытие как источник тепла.
В 1882 г. H. Н. Бенардос предложил способ сварки, названный им «электрогефест». Бенардос соединил один полюс сильной электрической батареи с угольным электродом, а другой – со свариваемым металлом. Как только он подносил электрод к металлу, вспыхивала яркая дуга, расплавлявшая края свариваемых швов. В месте соединения образовывался шов, представляющий собой полоску сплавленного металла. Для заполнения зазора между свариваемыми листами, усиления шва или наплавления другого металла в зону сварки вводился присадочный пруток.
Способ Бенардоса получил широкое применение на железных дорогах при ремонте рельсов и подвижного состава. Совершенствуя его, изобретатель в дальнейшем разработал не только сварку при помощи угольного электрода, но и изобрел, по существу, основные способы дуговой электрической сварки, применяемые и поныне.
Вначале электросварку использовали для исправления не вполне удавшихся металлических отливок, заварки трещин и пустот в металлических изделиях, восстановления изношенных поверхностей.
Затем она стала применяться не только для вспомогательных ремонтных работ, но и как основной технологический процесс производства новых изделий.
Так, в Великобритании на заводах компании «Ллойд – Ллойд» при помощи сварки приваривали стальные фланцы к железным трубам, проделывали отверстия во фланцах, сваривали железные трубы.
В Германии фирма «К. Мюллер» поставила товариществу братьев Нобель трубы для буровых скважин диаметром 2,1 м, сваренные по способу Бенардоса. Они выдерживали давление до 7 МПа.
Развивая и совершенствуя способ электросварки, созданный H. Н. Бенардосом, Н. Г. Славянов в 1888 г. разработал свой способ использования электрической дуги для сварки металлов. В отличие от Бенардоса, Славянов применял при сварке только металлические электроды. Металлический электрод у него служил как для поддержания электрической дуги, так и для получения из него расплавленного металла, необходимого для создания шва или заливки. Сварочная ванна в аппарате Славянова была защищена слоем шлака – расплавленного металлического флюса. Швы накладывали отдельными участками, а для того, чтобы шлак и расплавленный металл не растекались, зону сварки ограничивали барьером из формовочной земли.
Для поддержания достаточной электрической дуги Славянов разработал и применил на практике электрифицированный сварочный полуавтомат, или, как он его назвал, «плавильник». «Плавильник» подвешивали над местом сварки. Постоянство длины дуги в пределах оплавления электрода поддерживалось двумя соленоидами, втягивающими железный сердечник и обеспечивающими автоматическую подачу электрода. По мере оплавления электрод подавали в зону сварки вручную через маховичок, вращавший направляющие ролики.
Будучи замечательным технологом, Славянов добился исключительно высокого качества работ, подвергая сварке не только железо и сталь, но и чугун, бронзу, латунь. Свое изобретение Н. Г. Славянов назвал «электрической отливкой металлов».
Изобретение Славянова применялось для исправления дефектов литья, ремонта деталей паровозов, паровых машин, артиллерийских орудий.
В 1889 г. будущий основатель фирмы «Дженерал электрик» Ч. Коффин применил двухэлектродный держатель для сварки дугой косвенного действия, в которой объект сварки не включен в цепь сварочного тока.
В конце XIX в., несмотря на успехи способов Бенардоса и Славянова, часто применяли электрический ток для нагрева до размягчения отдельных участков кромок изделия, после чего окончательное изделие формировали ручной или механической проковкой. Обычно это были изделия с короткими швами, поскольку необходимо было проковать весь шов до его остывания.
Одновременно с «электрогефестом» появился еще один метод электросварки – контактная сварка. При контактной сварке через место соприкосновения соединяемых частей пропускают электрический ток, который нагревает металл в этом месте до размягчения, затем сдавливают части, получая прочное соединение. Количество теплоты, выделяющейся при прохождении тока, по закону Джоуля – Ленца пропорционально электрическому сопротивлению. В 60-е гг. XIX в. патент на такое соединение получил ангиличанин Ф. Уальд. Но он не разработал его до промышленного применения. Слава изобретателя стыковой контактной сварки закрепилась за американцем Э. Томсоном. В 1884 г. он сконструировал мощный трансформатор и специальные клещи-тиски для зажима свариваемых брусков, а в 1886 г. получил два первых патента на стыковую контактную сварку сопротивлением.
За короткое время Томсон и его сотрудники – Коффин, Девейн, Лемп, Расмуссен – получили 150 патентов по контактной сварке. В 1889 г. фирмой «Джонсон» впервые были сварены железнодорожные рельсы. Кроме этого применения стыковой контактной сваркой в первое десятилетие после изобретения сваривали только неответственные детали.
Одновременно со способом Томсона другой способ контактной сварки – точечную контактную сварку изобрел и H. Н. Бенардос. Немецкий патент свидетельствует, что это произошло до 1887 года. Бенардос подвел ток к двум наложенным друг на друга стальным пластинам с помощью клещей, в которые вставил угольные электроды. Проходя через электроды, зажимавшие пластины, нагревал их. Выделившейся теплоты было достаточно для образования сварной точки.
В конце XIX – начале XX в. электросварка не получила широкого распространения: электроэнергия была малораспространенной, известные способы сварки не были универсальными и мобильными, а удовлетворительное качество переплавленного металла обеспечивалось ценой высокой трудоемкости.
Но без сварки в то время уже нельзя было обойтись, и в начале XX в. родился еще один способ не только быстрого соединения металлов, но и их разъединения, основанный на использовании теплоты, выделяемой при сгорании газов. Попытки использовать горючие газы для резки металлов делались многократно, но необходимые для этого температуры достигаются только при сжигании газов или паров жидкости в смеси с чистым кислородом. Поэтому применение газовой сварки появилось с возможностью получения технически чистого кислорода в промышленных масштабах.
В 1840 г. немецкий химик Д. Рихман разработал аппарат для получения кислорода путем взаимодействия азотной кислоты и цинка. Водородным пламенем, образующимся на выходе из горелки, можно было паять и сваривать легкоплавкие металлы. Кислородное пламя имело температуру 2600 °C и могло расплавить платину, золото и серебро. Появление в 1880-х гг. электролиза облегчило получение водорода и кислорода.
Сам термин «газовая сварка металлов» впервые употребил француз Д. де Рисимен в 1840 г., описывая в статье способ сварки свинца при помощи воздушно-водородной горелки. Одновременно велась работа по созданию надежной аппаратуры. Одной из первых таких конструкций была горелка американца Р. Хейра для получения водородно-кислородного пламени. Для предотвращения обратного удара (потока горящего газа внутрь системы) в 1847 г. он создал диафрагму в водородном канале, через которую газ выдавливался в наконечник горелки и выходил наружу. В 1850 г. француз Девиль создал горелку, в которой, как и в современных горелках, водород и кислород смешивались до выхода наружу.
Позже химики стали использовать в горелках ацетилен С2Н2, теплота сгорания которого более чем в 5 раз выше теплоты сгорания водорода, температура пламени в смеси с кислородом достигает 3200 °C. Еще Г. Дэви получил ацетилен, разлагая водой карбид кальция. Но карбид кальция был дорог, и потребовалось несколько десятков лет, чтобы найти дешевый способ его производства. Для его промышленного производства было применено электричество. В 1892 г. основатели фирмы «Вильсон алюминиум» Дж. Морехед и Т. Вильсон выпустили первую промышленную плавку карбида. В это же время электроплавку карбида проводит во Франции А. Муассан.
В 1895 г. А. ле Шателье в сообщении Парижской академии наук отметил, что в пламени ацетилена не окисляется расплавленное железо. Именно такое пламя было необходимо для сварки.
Французски инженер Ш. Пикар смешал ацетилен и кислород прямо в горелке, до выхода из мундштука. Это требовало подачи ацетилена под давлением, и горелки работали тогда, когда газ подавался из баллонов. Внедрение газовой сварки тормозили частые взрывы сжиженного ацетилена в баллонах при транспортировке. Для предотвращения этого А. ле Шателье предложил помещать растворы газа в ацетоне в пористое тело. Баллоны наполняли губкой, затем заливали ацетон и накачивали ацетилен. Это сделало транспортировку относительно безопасной, и ацетилен стал широко распространяться в промышленности. Но газ из генераторов выходил под нормальным давлением, поэтому применять их в горелках Пикара было опасно.
Этот недостаток устранил Э. Фуше. В 1901 г. он впервые использовал в горелках сжатый ацетилен (в ацетоне) и сжатый кислород, а в 1901 г. подал в горелку ацетилен прямо из генератора при нормальном давлении, а кислород – под избыточным давлением. Позже такие горелки применяли не только для сварки, но и для резки, увеличив давление кислорода на выходе из дополнительных каналов.
Широкое применение газовой сварки началось, когда в 1902 г. немецкий ученый К. Линде создал ректификационный аппарат для разделения воздуха на компоненты.
Преимуществом ацетиленовой сварки и резки было отсутствие потребности в электричестве, автономность, подвижность и простота эксплуатации. При газовой сварке улучшалось качество шва, поскольку зона сварки была защищена от воздействия воздуха.
Электро– и газосварка могли заменить клепку при производстве металлических конструкций, применялись в ремонте этих изделий. Но при сваривании изделий с большими площадями сечений возникали серьезные проблемы. Применение аппарата Славянова ограничивали стационарный аппарат и тяжелый генератор, а способом Бенардоса и газовой сваркой можно было выполнять швы высотой не более 3–5 мм за один проход, а при многослойной сварке снижались производительность и качество.
Эта задача была решена при помощи алюминотермии. Процесс получения металлов и сплавов восстановлением оксидов металлов алюминием открыл в 1859–1865 гг. русский ученый H. Н. Бекетов. Суть процесса состоит в том, что шихта из смеси порошков алюминия и оксида железа засыпается в тигель и поджигается. Температура горения при этом достигает нескольких тысяч градусов. В результате шихта превращается в железо и шлак. Вместо алюминия можно применять магний. Позже это было использовано при создании нового способа сварки, в котором для нагрева применяется энергия горения термитной смеси, состоящей из алюминия или магния и оксидов металлов (главным образом железа). В 1898 г. немецкий химик Г. Гольдшмидт соединил два железных бруска, заполнив место стыка термитной смесью, после чего поджег ее. Перегретое жидкое железо подплавило кромки и, остыв, превратилось в шов.
Такие преимущества термитной сварки, как портативность оборудования, возможность соединения крупных заготовок на месте и быстрого последующего использования оценили железнодорожники. Термитом сваривали рельсы, сломанные детали и т. п. Термитная сварка оказалась наиболее выгодной при соединении деталей с площадью сечения более 5 см2. Ее применяли в судостроении для сварки валов, гребных винтов, якорей, в машиностроении и других отраслях. В течение нескольких лет способ термитной сварки оставался практически неизменным.
В начале XX в. различные способы сварки получили широкое применение. С 1908 г. на заводах Форда вместо кузнечной стала применяться газовая сварка. В 1911 г. фирмой «Дэвис – Борнонвиль» был разработан пантограф, приводившийся в движение электродвигателем и перемещавший резак.
В это время газовая сварка преобладала над дуговой. Но основным недостатком ацетиленовой горелки была невозможность увеличить скорость сварки, что в дуговой решалось увеличением силы тока дуги.
Шведский морской инженер Кьелберг создал плавящийся электрод в виде отрезка проволоки, покрытого порошком силикатов для защиты металла от окисления. Это улучшило качество шва, но не решило проблемы полностью. В дальнейшем состав покрытия изменялся, в него добавляли алюминий, соединения калия, натрия, кальция. Это позволяло легче возбуждать дугу и поддерживать ее горение.
Постепенно сварочные генераторы перешли на переменный ток. В качестве источников тока наряду со сварочными преобразователями стали применять специальные трансформаторы и выпрямители.
Для облегчения труда электросварщиков в середине 20-х годов прошлого века были разработаны полуавтоматы. Сварочные держатели с электродом перемещались вдоль шва на раме с роликами.
Существовавшие методы сварки не позволяли качественно сваривать легированные стали и цветные металлы и сплавы: было трудно подобрать материалы покрытия и электродов, а также режим дуги. В этих условиях пригодился метод газоэлектрической сварки. В 1911 г. американский физикохимик И. Ленгмюр открыл атомарный водород и разработал процесс сварки металлов в его среде. Он получил название атомно-водородной сварки. При подаче водорода в зону горения дуги он из молекулярного превращался в атомарный, а попав на сравнительно холодный металл, вновь становился молекулярным. При этом выделялась дополнительная теплота. Позже кроме водорода стали применяться смеси других газов: инертных (аргон, гелий), а также азот, хлор.
Это упростило процесс сварки и обеспечило высокую прочность металла.
В 1930-е годы возникла потребность в научном обосновании сварочных технологий. Это было связано со слухами о ненадежности сварных соединений, возникших в связи с обрушениями сварных мостов в Германии, Бельгии, Канаде и других странах. Многие инженеры и конструкторские организации выступали против применения сварки в ответственных конструкциях.
В Советском Союзе первым занялся сваркой В. П. Вологдин. Исследования, проведенные под его руководством, доказали возможность применения и научного изучения сварки. В 1929 г. исследованиями сварных соединений занялся 59-летний инженер – мостостроитель Е. О. Патон. Под его руководством в Киеве была создана электросварочная лаборатория. В 1935 г. в Киеве был создан Институт электросварки, позже получивший имя Е. О. Патона. В нем разрабатывали и осваивали механизированную и автоматическую сварку угольным электродом. При этом электрод перемещался на тележке, и были применены специальные средства защиты зоны сварки.
Е. О. Патон стал решать проблему автоматизации комплексно, уделив особое внимание аппаратам и защите зоны сварки. Еще в 1923 г. в Советском Союзе Д. А. Дульчевский применил при сварке меди угольный порошок и другие горючие вещества, оттеснявшие воздух от жидкого металла. Позже тоже пытались вносить защитные средства в зону сварки отдельно от электрода. В 1930 г. в США Б. С. Робинов, С. Е. Пейк и В. Е. Квиллен получили патент на способ сварки, при котором дуга засыпана флюсом, непрерывно высыпавшимся из бункера впереди электрода. Расплавляясь он образовывал надежную шлаковую и газовую защиту.
Способы автоматической сварки под флюсом совершенствовались: изменялся состав флюса, способы его подачи в зону сварки. Е. О. Патон поставил перед сотрудниками своего института задачу разработать гранулированный флюс для сварки сталей угольным и металлическим электродами. Он должен был прикрыть жидкий металл от воздуха, ввести дополнительные легирующие элементы в металл шва и связать вредные примеси. В 1939 г. был разработан флюс и изготовлен специальный аппарат.
Разработки Патона и его коллег внесли неоценимый вклад в победу над Германией. Дуговая и газовая сварка применялась при производстве танков. Особенно важную роль автоматическая сварка сыграла при сварке танковых корпусов. Она позволила резко увеличить производительность и качество изделий по сравнению с ручной сваркой. Ни в США, ни в Германии такой технологии не было, танковую броню сваривали вручную.
Во II половине XX в. появились новые способы сварки: плазменная, электронная, фотонная, лазерная, сварка взрывом, ультразвуком. Они расширили сферу применения сварочных технологий.
Электрическая турбина
Развитие электротехники потребовало перехода к более мощным двигателям, поскольку паровые машины не могли обеспечить увеличение мощности генераторов электрического тока. Перейти на качественно новый уровень можно было лишь за счет применения турбин.
Появление гидравлических турбин явилось следствием того, что водяные колеса не могли обеспечить энергией места, удаленные отводных источников. Они могли работать лишь при малом напоре воды (до 8 м), который был на равнинных реках. Это не позволяло использовать огромные запасы энергии, сосредоточенные в реках с большими напорами. Возможность их освоения заключалась в создании гидравлического двигателя, принципиально отличающегося от водяного колеса. Им стала водяная турбина, использовавшая силу реакции, создаваемой потоком воды на лопастях рабочего колеса.
Толчком к ее появлению стали труды Д. Бернулли. В своей работе «Гидродинамика», опубликованной в 1738 г., Бернулли обобщил ряд своих исследований по вопросам гидравлики и гидродинамики и вывел уравнение, устанавливающее на основании закона «живых сил» связь между давлением и скоростью в каждой точке потока несжимаемой капельной жидкости.
Уравнение Бернулли не только отражало закон сохранения и превращения энергии для частного случая гидравлической энергии, но и отчетливо указывало на принципиальную возможность построения гидравлических двигателей двух разных классов: использующих либо кинетическую, либо потенциальную составляющую полной энергии водного потока. Кроме того, Бернулли создал теорию реактивного действия, происходящего от вытекания струи через отверстие, сделанное в стенке сосуда.
Практически это явление было использовано впервые в 1745 г. английским механиком Баркером, построившим реактивное колесо, а в 1747 г. – венгерским физиком Я. Сегнером. Сегнер, работавший в Геттингенском университете, создал прибор, названный сегнеровым колесом, явившийся прототипом реактивного гидравлического двигателя. Позднее Сегнер совершенствовал конструкцию для практического использования своего колеса. Первоначально он построил цилиндр с двумя трубками для выпуска воды, а затем – с четырьмя трубками и даже шестью. Последнюю из этих конструкций Сегнер пытался применить для вращения жернова. Однако недостаточное знание сущности физических процессов, происходящих в таком двигателе, не дало Сегнеру возможности его усовершенствовать.
Л. Эйлер увидел в реактивном двигателе Сегнера большие практические возможности и занялся его изучением. В своих докладах, сделанных Берлинской академии наук, Эйлер дал анализ процессов в сегнеровом колесе и указал, что его низкий КПД связан с потерями энергии, которые можно значительно снизить. Потери при входе воды в колесо, происходящие от резкого изменения скорости и направления течения воды (потери на удар), могут быть уменьшены, если подводить воду к колесу в направлении вращения сосуда и со скоростью этого вращения. Чтобы уменьшить потери на выходе из турбины, Эйлер заменил горизонтальные водовыпускные трубки в двигателе Сегнера трубками криволинейной формы, идущими сверху вниз. В них не требовалось делать сбоку отверстие для выпуска воды, а можно было оставлять открытым нижний конец загнутой трубки. Эйлер подчеркнул, что в сегнеровом колесе может быть использована и превращена в механическую энергию почти вся энергия воды, пропускаемой через колесо.
Эйлер предложил разделить новую гидравлическую машину на две части: неподвижный направляющий аппарат, через который вода поступала в нижнее вращающееся колесо, насаженное на вал и являющееся рабочим органом машины. Рабочее колесо он снабдил 20 короткими изогнутыми трубами для выхода воды. Гидравлический двигатель Эйлера представлял собой переходную конструкцию от сегнерова колеса к гидравлической турбине.
К началу XIX в. в связи с успехами в области паровых двигателей применение водяных колес сократилось.
Исследования ученых, в частности Ж. В. Понселе, показали, что изогнутые лопатки водяных колес более эффективны, чем плоские, так как позволяют осуществить безударный вход воды на лопатки, что повышало КПД. Из металла можно было изготовлять изогнутые лопатки любого вида. Поэтому в этот период металлические водяные колеса стали преобладать над водяными колесами с плоскими лопатками.
Понселе предложил особый род подливных колес, в которых благодаря специальной форме лопаток можно было получить высокий КПД (до 0,7). Лопаткам в них придавалась такая кривизна, что подводимая вода поступала на лопатки в направлении их кривизны, проходила на некоторое расстояние вверх по лопатке и затем, опускаясь, выводилась наружу. Это совершенно устраняло удар воды о лопатки при входе и сопутствующие ему потери энергии. При металлических водяных колесах устраивались особые щитки для рационального направления воды к лопаткам колеса. Наиболее распространенными типами водяных колес, изготовлявшихся в XIX в., были применявшиеся при малых напорах (не более 1,5 м). Такими являлись, например, среднебойные водяные колеса Сажбьена и водяные колеса Цуппингера. У них была небольшая окружная скорость и малое число оборотов, что требовало большого диаметра, значительной ширины обода колеса и большого числа лопаток. В водяном колесе Сажбьена ширина обода была еще больше, лопатки имели криволинейную форму по всей поверхности так, что лопатки выходили из нижнего канала нормально к поверхности воды.
В 1832 г. на конкурсе, который проводило французское «Общество для поощрения национальной промышленности», свой гидравлический двигатель представил Б. Фурнейрон.
Турбина Фурнейрона являлась реактивным гидравлическим двигателем радиального типа с движением воды через направляющий аппарат от центра к периферии. Представленный на конкурс образец имел мощность 50–70 л. с., число оборотов более 60 в минуту, КПД – 0,7–0,8. В отчете Парижской академии наук о работе этой установки указывалось, что, применив особые внутренние ободья при лопатках рабочего колеса и соответствующие опускные затворы, удалось добиться такой регулировки турбины, что она работала с одинаковым КПД как в половодье, так и при низком уровне воды. В последнем случае понижалась лишь мощность.
Существенное отличие турбины от водяного колеса состоит в том, что в турбине вода входит на одну кромку лопатки турбины, проходит по лопатке и сходит с другой кромки, не меняя направления движения по лопатке. В водяном колесе вода входит и выходит в одном и том же месте, совершая перемещение по лопатке в обратную сторону. Вследствие этого скорость и направление движения воды в лопатке колеса изменяются по времени. В турбине вода не останавливается, не меняет направления течения на обратное, а течет непрерывно. Поэтому турбина может применяться в широком диапазоне напоров и развивать большее число оборотов, чем водяное колесо. В турбине вода проходит одновременно по всем лопаткам рабочего колеса, а в водяном колесе – лишь по небольшой их части, что приводит к уменьшению размеров турбины по сравнению с водяным колесом. При одинаковой окружной скорости на ободе двигателя, пропорциональной скорости подводимой воды, число оборотов турбины больше, чем водяного колеса, так как диаметр ее меньше. Это обстоятельство упрощает передаточные механизмы или даже делает их ненужными.
Водяные турбины разных конструкций можно классифицировать по отдельным признакам. Прежде всего, они делятся на два основных класса: реактивные и активные.
В реактивных турбинах вода заполняет все каналы между лопатками направляющего аппарата и рабочего колеса. Это так называемые полные или напорные турбины. Энергетический процесс в них протекает в основном за счет изменения суммы энергии давления и частично кинетической энергии.
В активных турбинах вода проходит через турбину свободно, не заполняя всего рабочего колеса или действуя на часть его, причем давление среды, окружающей воду в турбине, всюду одинаково. В них передача энергии потока воды в рабочее колесо осуществляется в основном за счет изменения кинетической энергии воды. Эти турбины получили также название свободноструйных. Активные турбины пригодны в условиях переменного или малого количества воды, но при больших напорах. Активные турбины могут действовать при одновременной работе не всех, а только части рабочих лопаток. Такие турбины носят название парциальных.
Водяные турбины могут быть либо с горизонтальным валом, на который насажено рабочее колесо, либо с валом вертикальным. В соответствии с этим различают турбины горизонтальные и вертикальные.
Наиболее естественным представляется размещение направляющего аппарата турбины над рабочим колесом. В таких турбинах движение воды будет происходить по цилиндрическим поверхностям, ось которых параллельна оси рабочего колеса; подвод воды также происходит в направлении, параллельном этой оси. Такие турбины получили название осевых, или аксиальных, реактивных турбин.
В турбине Фурнейрона осуществлялся подвод воды к рабочему колесу из направляющего аппарата в радиальном направлении, причем рабочее колесо охватывало направляющий аппарат. Такие реактивные турбины называют радиальными или центробежными. Если относительное расположение направляющего аппарата и рабочего колеса обратно предыдущему, т. е. приток воды происходит в радиальном направлении от периферии к центру, то двигатель называется турбиной с наружным радиальным подводом воды (иногда их называли центростремительными). Этот тип оказался более удобным, так как размеры вращающегося рабочего колеса при этом получаются меньшими, можно видоизменять конструкцию рабочего колеса в зависимости от числа оборотов.
Реактивные турбины строились как горизонтальными, так и вертикальными. В них лопатки направляющего колеса и рабочего колеса имели форму винтообразно искривленных поверхностей, причем направление кривизны лопаток направляющего колеса противоположно направлению кривизны лопаток рабочего колеса. Турбины Геншеля – Жонваля стали строиться с новым основным рабочим органом – отсасывающей трубой, позволявшей использовать весь располагаемый перепад, размещая турбину настолько выше нижнего уровня воды, насколько это удобно при компоновке всей установки (в пределах Юм). Турбина Геншеля – Жонваля быстро вытеснила турбины Фурнейрона и использовалась в течение всего XIX в. После начала передачи электроэнергии на расстояние были построены быстроходные турбины Геншеля – Жонваля для непосредственного соединения с электрическим генератором.
Наибольший успех в XIX в. выпал на долю радиально-осевых реактивных турбин. Американский конструктор Хауд в 1838 г. получил патент на радиальную турбину с внешним подводом воды с центростремительным движением. Ее подробно изучил и испытал в 1849 г. американский инженер Д. Б. Френсис, улучшивший ее, после чего она стала называться турбиной Френсиса. В 1855 г. американский инженер Свейт сделал эту турбину радиально-осевой, заставив поток менять направление в рабочих лопатках с радиального на осевое, что позволило объединить турбину со всасывающей трубой.
В 1877 г. Финк предложил конструкцию поворотных лопаток в направляющем колесе радиально-осевых турбин, при которой их вращение осуществлялось поворотом общего соединительного кольца, связанного с регулятором турбины. Эта схема регулирования расхода воды и мощности обеспечила лучшую маневренность двигателя.
Уменьшение габаритов рабочего колеса в радиально-осевых турбинах позволило обеспечить рациональный отвод отработавшей воды от рабочего колеса. Этому способствовало применение отсасывающей трубы, которой стали снабжаться все реактивные водяные турбины с наружным подводом воды. Ее назначение – отвести от рабочего колеса воду с наименьшими потерями. Действие трубы основано на том, что протекающая по ней вода создает под рабочим колесом разрежение и тем компенсирует уменьшение напора от расположения рабочего колеса турбины выше нижнего уровня.
Для подвода воды к турбине была применена камера, имевшая в плане форму спирали. Она обеспечивала равномерность питания турбины, подводя воду во всех точках по окружности колеса с одинаковой скоростью и по одинаковому направлению. Применение спиральной камеры улучшило работу направляющего аппарата и повысило КПД турбины.
Для использования энергии воды при больших напорах были разработаны активные водяные турбины. Среди них были парциальная турбина Швамкруга и тангенциальное колесо А. Пельтона.
В турбине Швамкруга рабочее колесо большого диаметра (5 м и более) имело направляющие лопатки, расположенные внутри обода. Подводящая труба входила внутрь рабочего колеса и имела несколько сопел, отверстия которых регулировались задвижками. Движение воды в этих турбинах происходило по касательной к рабочему колесу, лопатки которого расширялись снаружи.
Правообладателям!
Это произведение, предположительно, находится в статусе 'public domain'. Если это не так и размещение материала нарушает чьи-либо права, то сообщите нам об этом.