Текст книги "Асбестоцементные строительные материалы и изделия"
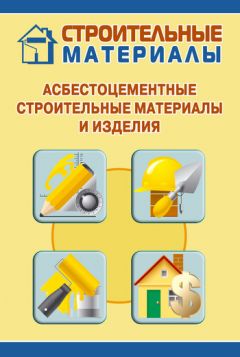
Автор книги: Илья Мельников
Жанр: Хобби и Ремесла, Дом и Семья
Возрастные ограничения: +12
сообщить о неприемлемом содержимом
Текущая страница: 5 (всего у книги 6 страниц)
Изготовление бетонных изделий и конструкции состоит из следующих технологических этапов.
1 этап. Входной контроль качества всех используемых материалов – минерального вяжущего вещества, заполнителей, добавок, арматуры, воды и др.
2 этап. Расчет состава бетонной смеси и его лабораторная проверка.
3 этап. Приготовление заданной бетонной смеси.
4 этап. Транспортировка смеси к месту изготовления конструкции.
5 этап. Укладка в форму (опалубку) и уплотнение смеси.
6 этап. Твердение бетона.
7 этап. Раскрытие формы (снятие опалубки).
8 этап. Отправка готового изделия на строительную площадку или склад готовой продукции.
Расчет состава бетонной смеси. Расчет состава бетонной смеси производят с использованием графиков и таблиц, в которых учитываются следующие данные:
– условия эксплуатации будущей конструкции или изделия, с учетом которых подбирают исходные материалы;
– показатели качества материалов;
– проектируемая марка бетона;
– пластичность бетонной смеси, выбираемую в зависимости от размеров бетонируемой конструкции;
– густота армирования;
– способ уплотнения бетонной смеси.
Расчеты проверяют в лабораторных условиях путем изготовления опытных образцов из рассчитанного состава и контроля их прочности.
Бетонная смесь. Бетонную смесь приготовляют на централизованных бетоносмесительных узлах предприятия в виде пластичного материала. Данный материал должен обладать связанностью и однородностью. Если бетонную смесь приготовляют из сухой смеси компонентов, в нее вводят воду, затем компоненты тщательно перемешивают непосредственно на строительной площадке. Этот способ приготовления бетонной смеси применяют в случае, если стройка находится далеко от предприятия.
Для приготовления бетонной смеси материалы сначала подготавливают, затем дозируют и перемешивают. Такие операции по подготовке заполнителей, как дробление, удаление загрязняющих примесей и разделение по фракциям, производят на предприятиях по производству нерудных материалов.
Если бетонирование выполняют зимой, заполнители подогревают на складах или в бункерах на предприятии-изготовителе при помощи паровых труб, путем пропусканием пара или горячего воздуха через заполнитель.
Водяной раствор добавок нужной консистенции готовят в специальной емкости, снабженной системой трубопроводов для подачи сжатого воздуха и пара для улучшения перемешивания.
На специальном оборудовании (дозаторах) подготовленные материалы (цемент, воду и добавки) взвешивают с точностью до 1% , заполнители взвешивают с точностью до 2%, затем все подготовленные материалы подают в бетоносмеситель, режим работы которого зависит от свойств бетонной смеси. Так, чтобы получить пластичные смеси на плотных заполнителях, применяют смесители свободного падения. В таких смесителях перемешивание происходит за счет вращения барабана и многократного подъема и сбрасывания материалов с некоторой высоты. В смесителях принудительного действия получают жесткие смеси и смеси на пористых заполнителях. Энергичное перемешивание в течение 3 – 5 минут достигается путем использования вращающихся лопастей.
Качество бетонной смеси оценивают по ее связности, однородности и удобоукладываемости – формуемости. Эти свойства зависят от вязкости и количества цементного теста, которое обволакивает заполнитель и заполняет пустоты между ним.
Количество цементного теста должно быть достаточным для того, чтобы эта система, состоящая из многих компонентов, приобрела связность, то есть превратилась в структурированную однородную систему с определенными физическими и механическими свойствами.
Если содержание цементного теста более оптимально в бетонной смеси, то это приводит к снижению многих эксплуатационных свойств. Повышаются усадка и ползучесть бетона, избыточное тепловыделение при гидратации приводит к появлению трещин и снижению прочности, морозостойкости и водонепроницаемости.
Для того, чтобы бетонная смесь стала подвижной и легко заполняла определенный объем, нужно не только заполнить пустоты, но и раздвинуть зерна заполнителя прослойками из цементного теста. Чем раздвижка будет больше, тем легче будут скользить зерна заполнителя относительно друг друга и тем выше будет пластичность смеси.
В зависимости от того, плотный или пористый заполнитель, а также от соотношения между количеством зерен мелкого и крупного заполнителя минимальное содержание цементного теста в бетонной смеси, обеспечивающее ее нерасслаиваемость и качественное уплотнение, составляет от 170 до 200 л в жесткой смеси и до 220…270 л в подвижной и литой на 1 м куб. бетонной смеси.
При неизменном расходе воды свойства компонентов существенно влияют на подвижность бетонной смеси. Например, чем тоньше помол цемента и чем больше он содержит молотых добавок – трепела, диатомита, опоки (пуццолановый портландцемент), тем более жесткой будет бетонная смесь. Это связано с увеличением суммарной площади поверхности частиц, которая для получения пластичной смеси должна быть покрыта тонким слоем воды. Подвижность бетонной смеси зависит также от формы, размера и чистоты поверхности зерен заполнителя. Пылевидные примеси, адсорбируя на своей поверхности часть воды затворения, повышают водопотребность бетонной смеси, снижая ее подвижность.
Большое влияние на подвижность бетонной смеси оказывает соотношение между песком и щебнем. При увеличении доли крупного заполнителя и использовании гравия окатанной формы подвижность увеличивается.
Каждая бетонная смесь обладает определенной водоудерживающей способностью, которая определяется опытным путем. С увеличением содержания воды пластичность смеси повышается. При большом содержании воды вязкость цементного теста становится недостаточной, чтобы удержать заполнитель во взвешенном состоянии и равномерно распределить его по всему объему.
Под действием собственной тяжести плотный заполнитель оседает, при этом бетонная смесь расслаивается. Расслоение нарушает однородность бетонной смеси и бетона в конструкциях при его твердении.
Избыточная вода при уплотнении бетона, обтекая зерна заполнителя, отжимается вверх. Образуются капиллярные ходы, снижающие морозостойкость и водонепроницаемость бетона, которые в результате последующей гидратации повышаются. Вода скапливается также под зернами крупного заполнителя, образуя полости, ухудшающие строение и свойства бетона, поэтому водоотделение строго ограничено.
Исключить расслоение бетонной смеси можно несколькими путями:
– снизить расход воды;
– увеличить расход цемента;
– ввести добавки пластификаторов и суперпластификаторов;
– увеличить содержание мелкого заполнителя;
– применить специальные добавки, повышающие вязкость цементного теста, например, высокогидрофильной бентонитовой глины.
Удобоукладываемость бетонной смеси является одной из ее важнейших характеристик. Удобоукладываемость представляет собой способность равномерно занимать определенный объем под действием собственной силы тяжести или под действием приложения нагрузки (вибрации) при жесткой бетонной смеси.
Чтобы оценить удобоукладываемость, в зависимости от ее пластичности используют показатели подвижности и жесткости. Подвижность определяют для пластичных бетонных смесей, замеряя осадку в сантиметрах отформованного из бетонной смеси усеченного стандартного конуса. Данный показатель является статической характеристикой структурной прочности бетонной смеси, так как ее осадка происходит под действием собственной массы.
Показатель жесткости применяют при наличии жестких смесей с ОК менее 1 см. Жесткость является динамической характеристикой вязкости бетонной смеси, так как ее определяют с применением вибрации. Оценивают жесткость, применяя специальную методику, по времени вибрации в секундах, достаточном для заполнения отформованным усеченным бетонным конусом формы – куба определенного размера, либо применяя специальный прибор. К жестким смесям относят смеси при времени вибрации от 40 секунд до 5 секунд, к сверхжестким – от 100 до 41 секунды.
Для повышения пластичности бетонной смеси необходимо:
– увеличить водоцементное соотношение;
– ввести пластификатор и суперпластификатор;
– снизить расход мелкого заполнителя;
– увеличить расход цемента.
Приготовленную бетонную смесь транспортируют к месту укладки, используя ленточные конвейеры, бетононасосы, пневматические приспособления, а также самосвалы, автобетоносмесители, автобетоновозы и трубопроводный транспорт.
Форму перед подачей бетонной смеси очищают, смазывают, укладывают в нее, согласно проекту, арматуру и закладные детали. При формовке бетонных и железобетонных изделий и конструкций используют такое важное свойство бетонной смеси, как тиксотропность.
Важной особенностью является способность многокомпонентного пластичного состава понижать вязкость под действием вибрации в результате нарушения сцепления между частицами и восстанавливать структурную целостность и прочность при снятии механического воздействия. Таким образом, бетонная смесь, с одной стороны, обладает свойствами жидкости, способной занимать определенный объем, с другой – твердого тела, обладающего структурной прочностью.
Обычно бетонные изделия формуют на специальных виброплощадках. Для уплотнения сверхжестких смесей применяют вибрирование с пригрузом: вибропрессование, виброштампование. Применяемое вибровакуумирование основано на частичном удалении воды за счет создаваемой разности давления на верхней и нижней поверхностях бетонируемой конструкции.
Ударный и безвибрационный способы уплотнения
В настоящее время наиболее часто применяют ударный и безвибрационные способы уплотнения. При помощи этих способов экономится электроэнергия, уменьшается опасность вибрационного воздействия на рабочих.
При ударном способе изготовления изделий формы с пластичной бетонной смесью многократно поднимают и опускают с небольшой высоты. При этом происходит постепенное уплотнение и равномерное распределение бетонной смеси по всему объему.
Из безвибрационных способов применяют:
– наливной способ,
– набивной способ,
– способ центрифугирования.
Наливной способ. При наливном способе используют высокоподвижные литые бетонные смеси, которые равномерно распределяются при заливке их в форму. Чтобы смесь не расслаивалась при сохранении водоцементного отношения, вводят тонкомолотые минеральные добавки или добавки пластификаторов и суперпластификаторов.
Набивной способ. Набивным способом в зависимости от последовательности приготовления смеси получают шприц-бетон и торкрет-бетон. И тот, и другой подают в форму или на защищаемую поверхность под давлением сжатого воздуха. Отличие состоит в том, что в первом случае сухую смесь из песка и цемента смешивают с водой непосредственно при выходе из сопла, во втором – относительно пластичный состав готовят заранее и подают под давлением в форму.
Центробежный способ формовки. Центробежный способ формовки применяют для изготовления труб, колонн и других полых изделий. Способ основан на равномерном распределении по поверхности формы и уплотнении подаваемой бетонной смеси под действием центробежной силы, возникающей при вращении.
Монолитные бетонные конструкции. Чтобы изготовить монолитную конструкцию, вначале устанавливают опалубку и арматуру.
Опалубку обычно изготовляют из досок, фанеры или металлических листов. Для повышения стойкости деревянную опалубку защищают слоем из полиэтилена или армированного стекловолокном пластика. В некоторых случаях в качестве опалубки можно использовать железобетонные плиты, которые являются частью будущей сборно-монолитной конструкции.
В соответствии с проектом в виде арматурных стержней или каркасов устанавливают арматуру. Для ответственных конструкций используют жесткую арматуру в виде двутавров, швеллеров и проката специальных профилей. Бетонирование больших монолитных сооружений или конструкций выполненяют отдельными блоками, устраивая между ними рабочие швы. Блок бетонируют непрерывно. В этом случае каждая последующая порция бетонной смеси должна быть уложена и уплотнена глубинными и поверхностными вибраторами до схватывания предыдущей.
В случае возведения монолитных конструкций на строительной площадке бетон твердеет в условиях, которые зависят от времени года и климата. Температурно-влажностные условия твердения оказывают большое влияние на набор прочности бетоном.
Снижение влажности воздуха вызывает испарение воды с поверхности отформованного бетонного изделия, что приводит к появлению усадочных трещин, обезвоживанию бетона, прекращению набора прочности в условиях дефицита воды и формированию дефектной, водопроницаемой структуры. Поэтому бетон необходимо выдержать во влажном состоянии при нормальных условиях – температуре 20 – 23 градуса и влажности 95 % не менее семи суток после бетонирования. При высоких температурах твердения бетон выдерживают до достижения 50…70 % проектной прочности.
При производстве работ в осенне-весенний период температура твердения снижается, уменьшается химическая активность воды и затормаживается набор прочности, что особо характерно для пуццоланового портландцемента и шлакопортландцемента, содержащих большое количество минеральных добавок.
При понижении температуры до – 5 0С твердение бетона продолжается очень медленно, так как вода, которая содержится в мельчайших порах, не замерзает. Понижение температуры до -10 градусов и ниже прекращает процесс гидратации. Дальнейшее нарастание прочности при оттаивании бетона и набор марочной прочности зависят от происшедших структурных изменений в бетоне.
Если замораживание наступило сразу после укладки бетона в конструкцию, то дальнейшее повышение температуры приводит к оттаиванию бетона и набору им заданной марки. Если бетон замерз после набора той прочности, когда сформировавшаяся структура бетона уже способна к восприятию без разрушения давления замерзающей воды, то потери конечной прочности будут незначительны.
Существенный недобор прочности происходит только при замораживании бетона на стадии формирования структуры, когда напряжения, возникающие из-за давления льда, выше, чем прочность контактов между кристаллическими продуктами гидратации. При последующем твердении в условиях положительных температур происшедшие разрушения не восстанавливаются, что сказывается на прочности.
Для набора необходимой прочности бетона, составляющей от 25 до 50 % проектной, необходимо:
– применять высокоэффективные быстротвердеющие портландцементы;
– снизить расход воды затворения;
– ввести специальные противоморозные добавки, которые обеспечивают гидратацию вяжущего вещества за счет понижения температуры замерзания раствора;
– применить теплоизоляцию поверхности свежеуложенного бетона, приготовленного на подогретых заполнителях и воде или с применением противоморозных добавок;
– применить тепловую обработку с использованием энергии пара, нагретого воздуха или электрического тока.
Тепловую обработку применяют при изготовлении сборного железобетона на заводах, а также при нормальных условиях твердения, если необходимо получить заданную прочность бетона в более короткий срок. Как правило, применяют следующие виды тепловой обработки: термовлажностная обработка при нормальном и повышенном давлениях, электроподогрев и гелиообработка.
Термовлажностная обработка. При обычном давлении термовлажностную обработку проводят с использованием специальных герметических камер, режим работы которых предусматривает повышение температуры до 70…90 0С в условиях насыщенного пара.
Процесс термовлажностной обработки проходит в несколько этапов. Сначала следует предварительная выдержка бетона до начала схватывания, затем медленный подъем температуры до максимально заданной, далее следует выдержка при этой температуре с последующим медленным охлаждением бетонных смесей. Первые этап обычно занимает от 1,5 до 3,5 часов, что зависит от жесткости смеси, вида применяемого цемента и добавок. Удлиняет этот период применение пуццоланового портландцемента или шлакопортландцемента, пластичных смесей и добавок пластификаторов, которые несколько замедляют процесс гидратации цемента в первые часы контакта вяжущего материала с водой.
На втором этапе поднимается температура. Скорость подъема может достигать от 10 до 30 0С в час. Чем раньше бетон приобретает минимальную структурную прочность, способную противостоять давлению пара и газообразных продуктов, тем больше может быть скорость подъема температуры. Максимальная температура зависит от активности портландцемента и составляет для высокоактивного быстротвердеющего портландцемента 50…60 0С, рядового портландцемента – 70…80 градусов, пуццоланового и шлакопортландцемента – 85 …90 0С.
Время изотермии определяется заданной заказчиком прочностью бетона после термовлажностной обработки, которая обычно составляет от 50 до 70 % проектной. В случаях, когда предусматривается нагружение конструкции расчетной проектной нагрузкой, отпускная прочность соответствует заданной, гарантированной проектной прочности.
Качество пропаренного бетона в большой степени зависит от перепада температуры и влажности, который вызывает перемещение воды и пара в непрочном еще бетоне, так как перемещение приводит к разрыхлению структуры. Поэтому ускорение набора прочности бетоном с использованием термовлажностой обработки обусловливает формирование более дефектной структуры по сравнению с бетоном, твердевшим в нормальных температурно-влажностных условиях. Это ведет к снижению водонепроницаемости бетона, коррозионной стойкости и морозостойкости.
Чтобы при тепловлажностной обработке исключить влагопотери с поверхности бетонных изделий, необходимо использовать рулонные пароизоляционные материалы – полимерные пленки, рубероид, прорезиненную ткань, пленкообразующие составы, наносимые распылением на поверхность свежеотформованного бетона (латексные, водные эмульсии синтетических каучуков), или добавки – депрессоры испарения – высшие жировые спирты. Их применение позволяет проводить термообработку продуктами сгорания природного газа без ухудшения свойств бетона.
Чтобы уменьшить продолжительность термовлажностной обработки на 3…6 часов и снизить тем самым затраты энергии, необходимо совместить интенсивное механическое и тепловое воздействие на бетон. Механическое давление на твердеющую смесь может создаваться специальным пригрузом, жесткой крышкой форм, пакетированием изделий, а также избыточным давлением пара в камере.
Снижение энергозатрат достигается также и применением комплексных добавок, состоящих из ускорителей и суперпластификаторов. Таким образом, можно снизить расход воды более чем на 20%, сохранив при этом заданную пластичность бетонной смеси. Добавки позволяют уменьшить температуру изотермии, а также отказаться от использования бездобавочных энергоемких цементов при получении бетонов прочностью 60…70 МПа, уменьшить в несколько раз интенсивность и продолжительность виброуплотнения.
Процесс твердения бетона ускоряет повышение температуры термовлажностной обработки до 100 градусов и свыше. Так как гидратация минерального вяжущего вещества может протекать только в присутствии воды, то с целью предупреждения ее вскипания и испарения этот вид термообработки проводят при повышенном давлении.
Запаривание бетона производят в герметических камерах – автоклавах. Кроме ускорения твердения бетона, запаривание приводит к образованию дополнительных кристаллических соединений, повышающих прочность бетона до 50…100 МПа. По автоклавной технологии получают цементные изделия, а также силикатные кирпичи и бетоны, в которых в качестве вяжущего вещества используют тонкомолотую смесь из гашеной или негашеной извести и кремнезема. Автоклавная обработка состоит из нескольких этапов:
1 этап. Впуск пара и постепенный нагрев до 100 градусов.
2 этап. Повышение температуры и давления пара до максимальных значений (175…203 градуса и 0,8…1,6 МПа).
3 этап. Выдерживание изделий при заданной температуре и давлении.
4 этап. Снижение давления до нормального и температуры до 100 0С.
5 этап. Остывание изделий до температуры окружающей смеси.
Электроподогрев бетона может осуществляться за счет прохождения электрического тока либо по металлической форме и арматуре и перехода электрической энергии в тепловую вследствие высокого электросопротивления стали, либо через свежеуложенный бетон между двумя электродами.
Довольно часто применяют гелиотермообработку железобетонных изделий. При гелиобработке в качестве теплоносителя используют солнечную энергию. Для этого используют гелиоформы, фокусирующие энергию солнца или специальные пленочные покрытия черного цвета. Ускорить процесс можно, применив комплексное использование энергии солнца в сочетании с быстротвердеющим цементом и ускорителями твердения – специальными добавками.
Правообладателям!
Это произведение, предположительно, находится в статусе 'public domain'. Если это не так и размещение материала нарушает чьи-либо права, то сообщите нам об этом.