Текст книги "Михаил Козловский: Өнегелі өмір. Вып. 30"
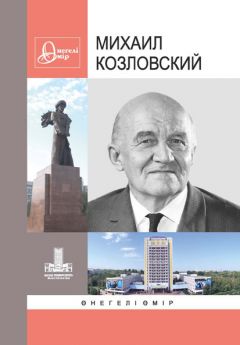
Автор книги: Коллектив авторов
Жанр: Зарубежная образовательная литература, Наука и Образование
сообщить о неприемлемом содержимом
Текущая страница: 5 (всего у книги 20 страниц) [доступный отрывок для чтения: 7 страниц]
ПОДНЯТЬ РОЛЬ ЗАВОДСКИХ И ПРОИЗВОДСТВЕННЫХ ЛАБОРАТОРИЙ
Технический прогресс – важнейшее условие развития социалистического производства. Большое значение для технического прогресса имеет укрепление содружества работников науки и производства. Практика ряда научно-исследовательских учреждений и вузов показывает весьма плодотворные результаты совместной с производственниками разработки вопросов новой техники и технологии. Очень важно поднять роль заводских лабораторий, укреплять их материальную и экспериментальную базу, состав научных работников.
Огромные задачи стоят перед заводскими и другими производственными лабораториями, в частности перед химическими, в связи с грандиозными перспективами развития народного хозяйства.
Ряд заводских лабораторий Казахстана успешно участвует в научно-исследовательской работе. Так, на Балхашском медеплавильном заводе в содружестве с Академией наук Казахской ССР была успешно проведена работа по извлечению редкого металла – рения, участники которой отмечены Государственными премиями. Лаборатория Карагандинского завода синтетического каучука осуществляет важные исследования по усовершенствованию процесса гидратации ацетилена, а лаборатория Гурьевского нефтеперерабатывающего завода – по использованию отходящих газов крекинг-процесса. Заметно оживляется научная работа, проводимая сотрудниками лаборатории Лениногорского полиметаллического комбината. Важные работы выполня– ются и лабораториями некоторых других предприятий. Од– нако общее состояние научно-исследовательской работы в большинстве лабораторий Казахстана еще нельзя считать удовлетворительным. Многие лаборатории проводят только рядовые анализы по стандартным методикам, не принимают активного участия ни в исследовательской работе по усовершенствованию технологического процесса, ни даже по аналитической химии.
Часто заводские лаборатории рассматриваются только как органы технического контроля, в обязанности которых входит установление качества сырья, поступающего на производство, и качества выпускаемой готовой продукции. Между тем их роль должна быть шире. Лаборатории призваны помогать совершенствовать процессы производства, вести научно-исследовательскую работу на предприятии. А наличие научно-исследовательских отделов на заводах ни в коей мере не исключает участия лабораторий в проведении исследовательской работы хотя бы потому, что их научные и практические выводы в области технологии целиком основываются, как правило, на данных анализа. Именно аналитическая роль работы в большинстве случаев является наиболее трудоемкой, от качества ее выполнения зависит успех проводимых исследований. Это, в свою очередь, требует от руководителей лабораторий не слепого выполнения заказов научно-исследовательских отделов, а творческого участия в их осуществлении.
Особенно большие задачи стоят перед лабораториями геологической службы. Не следует забывать, что все данные по подсчету запасов полезных ископаемых основываются на результатах химического анализа проб минерального сырья, отбираемых геологами-разведчиками, и что работа геолога неразрывно связана с работой химика-аналитика. В настоящее время эта область деятельности аналитических лабораторий значительно осложнилась. Если раньше от химика-аналитика обычно требовалось определение наиболее распространенных металлов (железо, медь, свинец, цинк, марганец и т.д.), то теперь необходимо определить почти все элементы периодической системы. При этом если раньше надо было определять лишь относительно большие содержания компонентов – обычно не меньше десятых и сотых долей процента, – то теперь речь идет об определении тысячных и даже десятитысячных долей процента. Изменились требования и к чистоте выпускаемых материалов, в частности металлов. Развитие атомной техники и полупроводниковой промышленности потребовало разработки методов определения примесей в чистом металле, присутствующих в стотысячных и миллионных долях процента. Высокие требования к чистоте материалов предъявляет и промышленность пластмасс.
Новые задачи ставятся перед аналитиками и в связи с развитием газовой промышленности. Прежде, когда газы нефтеперерабатывающих заводов, коксовых печей и природные использовались только как топливо, технолога интересовала их калорийность и общее содержание углеводородов. При использовании же таких газов в химической промышленности необходимо знать содержание каждого углеводорода в отдельности, а также характер присутствующих в газе посторонних примесей.
Вообще предстоящее развитие промышленности высокомолекулярных соединений, несомненно, поставит перед химиками-аналитиками такие вопросы, для решения которых потребуются совершенно новые методы.
Какие требования предъявляются к аналитикам в организации контроля самого технологического процесса? Чтобы на основании данных анализа управлять процессом производства, необходимо получать результаты этого анализа в кратчайший срок. При этом условии можно использовать данные анализа не только для регистрации неполадок в процессе, но и для своевременного устранения их. Отсюда вытекает потребность в так называемых экспрессных методах анализа. При автоматизации же производства необходима автоматизация и методов анализа.
Решение всех перечисленных выше задач нельзя осуществить, используя только старые «классические» методы химии – весовой и обычный объемный анализ. Самое широкое применение в современной аналитической химии получают различные физико-химические и физические методы анализа. Интересно отметить, что за последние годы число работ, посвященных физико-химическим методам анализа, составляет 52 % от общего числа работ по аналитической химии, опубликованных в мировой литературе, в то время как процент работ по весовому анализу – всего лишь 6,5 %, а по обычному объемному – 17,2 %. Около 9 % работ приходится на долю спектрального, рентгеновского и микрокристаллоскопического анализа и около 14 % – на долю газового анализа и биохимических методов.
Распространение новых методов анализа можно проиллюстрировать и на примере работ казахстанских лабораторий. Так, на первой конференции заводских лабораторий, проходившей в Алма-Ате в 1946 г., было прочитано всего 18 докладов, из которых лишь один был посвящен полярогра– фическому методу анализа и четыре – визуальной колориметрии, один – спектральному и один – рентгеноспектральному анализу, остальные – классическим методам аннализа и организационным вопросам. На пятой же конференции в октябре 1958 г. доклады по спектральному анализу пришлось выделить в специальную секцию, а из общего числа докладов по аналитической химии (51) на долю полярографии приходится уже 17 докладов. При этом ряд докладов посвящается уже не обычной полярографии, а новейшим ее видоизменениям.
Почти все доклады по колориметрии также посвящены новым ее видоизменениям. На конференции сообщалось о радиохимических методах анализа, о флуоресцентном анализе, о хроматографических и ионообменных методах разделения металлов. С докладами по амперометрическому титрованию, о котором вообще не говорилось на первой конференции, на последней же конференции выступили работники не научно-исследовательских институтов, а представители заводских лабораторий. Все это является показателем того Большого практического значения, которое приобретают физико-химические методы анализа.
Но при возрастающей роли физико-химических методов, классические нисколько не утрачивают своего значения. Необходимо дальнейшее усовершенствование этих методов, а также и методов разделения компонентов в анализируемом образце.
При оценке новых методов анализа большое значение придается их экспрессности. Однако, говоря об экспрессности того или иного метода, следует одновременно учитывать и его трудоемкость. Эти понятия не равноценны. Известен ряд методов весьма длительных, но малотрудоемких, и наоборот – экспрессных, но весьма трудоемких. Когда, например, при выполнении анализа проводится выпаривание на водяной бане, то на это затрачивается только время, а не труд аналитика. Равным образом фильтрование также требует много времени, но не труда. Электролиз же с контролем электродного потенциала, проводимый вручную, без автоматического прибора, – процесс хотя и быстрый, но трудоемкий, так как требует неотлучного присутствия аналитика. Это различие в экспрессности и трудоемкости особенно проявляется при массовых анализах, поскольку выпаривание, фильтрование или прокаливание, скажем, 50 проб зачастую потребует почти столько же времени, сколько проведение этих операций с одной пробой. Применение классических методов анализа при массовой работе иногда может обеспечшъ большую производительность лабораторий, нежели исполъзование так называемых «экспрессных».
Однако экспрессностъ совершенно необходима, как мы уже упоминали, в том случае, когда на основании резулътатов анализа осуществляется контролъ самого процесса производства. Высшая степенъ «экспрессности» проявляется при автоматическом анализе, который в ряде случаев сочетается с автоматическим управлением самим технологическим процессом. Наиболее пригодны для этой цели различные электрохимические методы, так как они легче всего позволяют передаватъ резулътаты анализа на расстояние и осуществлятъ дистанционное управление процессом. Наиболее легко автоматический анализ осуществляется при работе с растворами или газами, особенно если определяется всего один компонент. Между тем современная технология требует разработки автоматических методов анализа и других объектов (например, хвостов обогатителъных фабрик), причем одновременно на содержание несколъких компонентов. Это одна из важнейших задач современной аналитической химии.
Таким образом, задачи, стоящие перед современной аналитической химией, разнообразны и оченъ сложны. Их нелъзя разрешитъ силами одних научно-исследователъских учреждений, занимающихся подобными вопросами, тем более что таких учреждений, даже если включить в их число кафедры вузов, не так много. В этой работе должна участвовать многотысячная армия аналитиков всех отраслей народного хозяйства. Если академические учреждения в основном занимаются решением принципиалъных вопросов аналитической химии и разработкой новых методов анализа, то разработкой чистых методик применителъно к тем или другим промышленным объектам, к тому или иному виду сыръя должны заниматъся заводские и производственные лаборатории. Промежуточным звеном должны являться отраслевые исследовательские институты. Конечно, это не исключает того, что отдельные заводские лаборатории будут самостоятельно решать и крупные аналитические проблемы, а академические институты разрабатывать конкретные методики. Но в любом случае между академическими учреждениями и заводскими лабораториями обязательна тесная связь.
Исследовательскую работу заводским лабораториям необходимо развивать в двух направлениях: разработка и дальнейшее усовершенствование методов анализа и исследования, связанные с совершенствованием технологического процесса. О работах первого направления говорилось выше. Что же касается вопросов совершенствования технологических процессов, то здесь для химиков открывается необозримое поле деятельности.
В Казахстане, в частности, весьма актуальны работы по созданию химической промышленности «тяжелого» органического синтеза на базе переработки отходящих газов нефтеперерабатывающих предприятий, а также природных газов и твердого топлива. Именно на этой сырьевой базе в Казахстане должна быть создана мощная промышленность пластмасс и других синтетических продуктов.
Не менее важной для Казахстана с его неисчерпаемыми запасами черных, цветных и редких металлов является проблема рационального комплексного извлечения металлов из руд и усовершенствование процесса обогащения последних. Актуальными являются вопросы кооперирования металлургической и химической промышленности, в частности, на основе использования для производства серной кислоты от– ходящих газов металлургических заводов.
Большого внимания заслуживают проблемы переработки фосфоритов Каратау и природных солей Казахстана, химической переработки камыша и другого растительного сырья.
Решение этих проблем потребует самой напряженной исследовательской работы химиков Казахстана.
Реорганизация управления промышленностью создала более благоприятные условия для развития исследовательской работы на заводах. Чтобы лаборатории стали центрами научно-исследовательской работы на предприятиях, необходимо выполнение ряда условий. Прежде всего, лаборатория должна быть обеспечена высококвалифицированными кадрами с широкой общей химической подготовкой.
К сожалению, вопрос о подготовке химиков-аналитиков в настоящее время недооценивается: еще господствует взгляд на аналитическую химию как на какое-то мастерство, основанное не столько на научных предпосылках, сколько на практических навыках.
Наряду с подготовкой новых кадров работников заводских лабораторий необходимо организовать курсы повышения квалификации химиков вследствие быстрого внедрения в лабораторную практику различных электронных приборов, с которыми химики обычно очень мало знакомятся в вузах.
Вторым условием успешной работы лабораторий является обеспечение лабораторий современным оборудованием и реактивами. В практике лабораторий органические реактивы играют большую роль. Однако ассортимент реактивов, вырабатываемых химической промышленностью, крайне мал, и многие реактивы, предложенные нашими учеными, для рядовых лабораторий недоступны. Неудовлетворительно обстоит дело и с выпуском реактивов высшей степени чистоты, что чрезвычайно затрудняет проведение работы по анализу полупроводниковых материалов.
Одним из вяжных условий успешного развития заводских лабораторий является правильная организация их работы.
Устранение недостатков, создание лучших условий для работы позволят повысить роль заводских и производственных лабораторий в решении стоящих перед ними задач.
Народное хозяйство Казахстана, 1958. – № 10. – С.5.
М.Т. КОЗЛОВСКИЙ, П.И. ЗАБОТИН, В.М. ИЛЮЩЕНКО, С.П. БУХМАН, М.В. НОСЕК, В.Я. СЕРГИЕНКО, Я.3. МАЛКИН
Институт химических наук АН КазССР,Чимкентский свинцовый завод
ПРИМЕНЕНИЕ АМАЛЬГАМНОГО МЕТОДА К ИЗВЛЕЧЕНИЮ ТАЛЛИЯ ИЗ ПЫЛЕЙ ЧИМКЕНТСКОГО СВИНЦОВОГО ЗАВОДА
(В порядке обсуждения)
Основанием для проведения описываемой работы послужили результаты ряда исследований теоретического и прикладного характера в области амальгамных методов разделения и получения металлов, проведенных в Институте химических наук АН КазССР и Казахском государственном университете им. С.М. Кирова под руководством М.Т. Козловского [1-8].
Работа включает изучение отдельных стадий процесса (для обоснования принятой нами технологической схемы) и проверку его в полупромышленных условиях. Полупромышленные испытания амальгамного метода извлечения таллия из пылей агломерационного цеха Чимкентского свинцового завода проведены в тесном содружестве с Казахским государственным университетом и заводом. В работе принимали участие сотрудники кафедры аналитической химии Казахского государственного университета канд. хим. наук А. Зебрева, студ. В. Гладышев и работники Чимкентского свинцового завода М. Леванов, В. Прачев, Е. Рубанова, М. Шалагинова, Г. Носов, Ю. Столяров. Большую помощь в организации полузаводских опытов оказали б. директор Чимкентского завода К. Симаков и главный инженер Л. Ушков.
Анализы на таллий проводили сотрудники спектральной лаборатории завода под руководством И. Юделевича и Н. Карпенко. Химические и полярографические анализы проведены сотрудницей научно-исследовательского отдела завода Н. Поповой и лаборанткой Института химических наук АН КазССР О. Орса.
Лабораторные исследования
Характеристика сырья. Химический состав пыли рукавных фильтров агломерационногө цеха зависит от состава сырья, перерабатываемого заводом. В таблице 1 приведен состав агломерационной пыли, определенный в разное время.
Таблица 1
Анализ агломерационной пыли


О6жиг агломерационной пыли. Обжиг проводился в стальном противне в подовой электрической печи сопротивления с ручным перегребанием. Количество загружаемой пыли составляло 20-25 кг. Температура обжига поддерживалась в пределах 400-400-500о Характеристика огарка, полученного в процессе обжига, приведена в таблице 2 и на рисунке 1
Таблица 2
Изменение концентрации сульфидной серы и таллия в пыли в процессе обжига при 4000

Из анализов огарка видно, что уже за первый час обжига при 400о удаляется значительная часть сульфидной серы и таллия. Таким образом, если ставить цель сохранить в огарке весь таллий и выжечь только сульфидную серу, то использовать окислительный обжиг как предварительную операцию перед выщелачиванием нецелесообразно.
Выщелачивание пыли. Поскольку почти все соединения одновалентного таллия, которые могут содержаться в пылях агломерационного цеха, удовлетворительно растворимы в воде [9], нами для извлечения таллия было применено водное выщелачивание, проводившееся в фарфоровых смесителях при отношении ж: т = 4: 1. Во всех случаях пульпа перемешивалась механической мешалкой.

Рисунок 1. Изменение концен– трации сульфидной серы и таллия в пыли в процессе обжига при 400°
В таблице 3 приведены результаты выщелачивания водой двух образцов пыли (по 250 г) путем последовательной четырехкратной обработки одной и той же навески пыли при 80-90о и ж: т = 4: 1.
Как видно из табл. 3, четырехкратное водное выщелачивание обеспечивает извлечение таллия из пыли в раствор до 80 – 90 %. Были также проведены опыты по выщелачиванию при различных температурах, которые показали, что с по– вышением температуры извлечение таллия увеличивается. Последнее находится в соответствии с температурной зави– симостью растворимости его соединений.
Таблица 3
Результаты последовательного четырехкратного выщелачивания пыли

Продолжение таблицы 3

Проверкой скорости отстаивания пульпы (рисунок 2) 6ыло выяснено, что осаждение твердой фазы практически заканчивается через 30-40 мин.

Рисунок 2. Изменение высоты нижнего слоя пульпы со временем
Цементация таллия амальгамой цинка. Извлечение таллия из раствора в амальгаму проводилось цементацией амальгамой цинка. Раствор, полученный после водного выщелачивания, перед цементацией подкислялся серной кислотой до 5 г/л для уменьшения шламообразования ртути при цементации и для частичной очистки раствора от свинца. Для цементации использовался раствор, содержащий 0,36– 0,4 г/л2п, 0,127 г/лС6и 108 мг/л Т1.
Цементация проводилась при непрерывном прохождении раствора последовательно через две цементационные ячейки. Схема установки представлена на рис. 3. Раствор подавался на цементацию из напорного чана через фильтр в цементатор I, откуда он самотеком поступал в цементатор II, а затем направлялся в сборный чан через ванну для улавливания шлама. Скорость протекания раствора регулировалась и составляла примерно 1 л/мин. Скорость вращения мешалок в обоих цементаторах была ~1450 о6/мин. Объем ртути в цементаторе I составлял 1л, в цементаторе II – 1,5 л. В цементатор I загружался цинк в количестве, заведомо недостаточном для полной цементации таллия из всего объема раствора. В цементаторе II количество цинка было взято с некоторым избытком.

Рисунок 3. Схема цементационной установки: 1 – амальгама; 2 – раствор; 3 – шлам
Вцементаторе I для контроля содержания цинка во время цементации измерялся потенциал амальгамы. Он определялся обычным компенсационным методом. Во время цементации периодически отбирались пробы раствора после цементаторов I и II для определения содержания в нем цинка, таллия и, в некоторых случаях, кадмия. Результаты опыта представлены в таблице 4.
Таблица 4
Результаты цементации таллия амальгамой цинка в проточном растворе

Всего таким образом 6ыло переработано 195 л раствора. Продолжительность процесса составляла 185 мин.
После цементации в цементаторе I осталось 895 мл амальгамы, в цементаторе II – 1450 мл. Остальные 205 мл Нg были механически унесены с отработанным раствором в сборные чаны.
Как видно по результатам опытов, при цементации таллия в проточном растворе достигается значительное извлечение егө из раствора (около 98-990/о). При этом удалось трижды проследить полное удаление цинка из амальгамы цементатора I (см. значения потенциалов).
Разложение амальгамы анодным окислением. Амальгама, полученная при цементации, кроме таллия, содержала кадмий, свинец и остаток цинка. Для разделения металлов, содержащихся в амальгаме, применялись специальные электролиты: сульфатно-аммиачный (2-н. (NH4)2SO4 – 1-н. (NH4OH) для выявления цинка и кадмия, щелочной (1-н.NaOH) – для выделения свинца и сернокислый (1-н. H2SО4) – для выделения таллия.
Электролиз проводился с контролем анодного потенциала при анодной плотности тока от 100 до 50А/м2 при последующем постепенном снижении ее по мере извлечения выделяемого металла из амальгамы. В качестве катодов использовались алюминиевые пластины в первом и третьем электролитах и железные – во втором (щелочном).
Данные по распределению таллия в продуктах, получаемых при анодном разложении амальгамы, приведены в таблице 5.
Таблица 5
Распределение таллия по продуктам, получаемым при анодном разложении амальгамы

Полупромышленные испытания
Проведенные исследования позволили наметшъ технологическую схему извлечения таллия из пылей агломерационного цеха (рисунок 4), которая была осуществлена на полупромышленной установке Чимкентского завода. Аппа– ратурная схема представлена на рисунке 5.

Рисунок 4. Схема амальгамного способа производства таллия из пылей агломерационного цеха Чимкентского свинцового завода

1– смеситель емкостью 5 м3; 2 – промежуточный бак емкостью 5 м3; 3, 8, 9 – насосы; 4 – сборник промывных вод емкостью 25 м3; 5 – сборник готовых растворов емкостью 25 м3; 6, 7 – фильтр-прессы по 24 рамы; 10 – напорный чан емкостью 1,5 м3; 11– фильтр; 12 – цементатор I емкостью 35 л; 13-цементатор II емкостью 35 л; 14 – ванна для улавливания шлама емкостью 1 м3; 15 – электролизер емкостью 15 л; 16 – бачок для приготовления амальгамы цинка емкостью 5 л.
Примечание. Аппаратура позиций 1, 2, 5 изготовлена из железа и внутри покрыта кузбасс-лаком, 4 – из железа, 10 – из винипласта или дерева, 12-16 – из винипласт
Рисунок 5. Схема укрупненной установки для амальгамного извлечения таллия из пылей агломерационного цеха Чимкентского свинцового завода
Эта установка, хотя и не отвечала всем необходимым требованиям технологической схемы, так как для установки приспосабливалось, большей частью, уже имевшееся оборудование, все же обеспечила с апреля по октябрь 1956 г. переработку нескольких тонн пыли, а в октябре – проведение балансовых опытов.
Выщелачивание пыли. Аппаратура для выщелачивания состояла из двух железных баков емкостью по 5 м3, один из которых, оборудованный механической мешалкой, змеевиками для обогрева глухим паром и барботажными трубками для острого пара, использовался в качестве реактора, другой – для хранения промежуточных растворов; двух железных баков емкостью по 25 м3, используемых для хранения растворов, и двух 24-рамных фильтр-прессов. Контроль температуры осуществляется термометром сопротивления. Для уменьшения контакта растворов с железом внутренние стенки основных баков покрывались кузбасс-лаком.
Выщелачивание (трехкратное) проводилось при 80-90° в течение часа при ж: т = 5:1. Отделение жидкого от твердого в промежуточных операциях проводилось декантацией отстоявшейся пульпы. Конечные растворы и отвальный кек отделялись фильтрованием на фильтр-прессе. Анализ пылей, загруженных в смеситель, и выгруженных кеков по– казан в таблице 6.
Таблица 6
Содержание таллия в пылях и кеках и извлечение таллия в раствор при выщелачивании

В процессе выщелачивания 6ыли получены растворы с концентрацией таллия:
1) готовые растворы (растворы I выщелачивания) – 170– 200 мг/л;
2) промежуточные растворы (растворы II выщелачивания) – 80-100 мг/л;
3) промывные воды (растворы III выщелачивания) – 30– 40 мг/л.
На основании данных таблицы 6 и анализов растворов составлен сводный баланс выщелачивания (таблица 7). Извлечение таллия подсчитано по содержанию таллия в растворах.
Таблица 7
Баланс по циклам выщелачивания

Продолжение таблицы 7

Из таблицы 7 видно, что наибольшее количество таллия переходит в раствор за первую операцию выщелачивания.
Среднее извлечение таллия по всем циклам составило по анализам растворов 78,6 % и по анализам кеков 72,2 %.
Цементация таллия амальгамой цинка. Растворы после выщелачивания перекачивались из бака № 5 в напорный бак над цементаторами. В этом баке растворы подкислялись серной кислотой до 5 г/л, отстаивались и фильтровались.
При сопоставлении концентрации таллия в готовых растворах, полученных непосредственно после выщелачивания, с концентрацией его в тех же растворах перед цементацией обнаруживалось заметное снижение концентрации таллия в последних. Как было установлено, наблюдаемое понижение концентрации таллия объясняется цементацией его железными стенками коммуникационных труб, рам фильтр-прессов и недостаточной изоляцией стенок сборных баков кузбасс-лаком. Было изучено влияние железа (взятого в виде стружки) на изменение концентрации таллия в растворах. При взаимодействии раствора с железной стружкой наблюдалось значительное падение концентрации таллия. За 4-6 дней таллий практически полностью цементируется железом.
Состав растворов, поступающих на цементацию в объе– ме 9,81 м3, был следующим: концентрация металлов – 116,2 мг/л Т1, 77,7 мг/л Сб, 615,4 мг/л 2п; количество металлов – 1140,5 г Т1, 762,7 г Сё, 6037,0 г 2п.
Подкисленные и отфильтрованные растворы из напорного бака самотеком поступали в цементатор I. Скорость подачи раствора регулировалась краном и составляла в среднем 2,2 л/мин. Общая продолжительность цементации 9,81 м3 раствора составляла 75,5 часа. Цементация проводилась по схеме, приведенной ранее (см. рисунок 5), в двух последовательно соединенных винипластоных цементаторах емкостью по 35л. Скорость вращения мешалки составляла 300-400 о6/мин.
Перед началом цементации в каждый цементатор загружалось по 40 кг Нg и по 800 г 2п. По мере расходования цинка при цементации в обе амальгамы добавлялись новые порции цинка.
Средний анализ отработанных растворов после цемен– тации приведен в таблице 8.
Таблица 8
Средние данные полярографического анализа растворов после цементации

Таким образом, общее извлечение таллия при цементации составляло 93,2 %, общее извлечение кадмия – 75,6 %.
Во время цементации в цементаторе наблюдалось образование шлама, который улавливался в специальной ловушке.
Электролитическое разложение амальгам. Разложение амальгам проводилось в винипластовом электролизере с пятью медными вращающимися дисками [10], опущенными в амальгаму. Эти диски амальгамировались и служили анодом. В качестве катодов использовались алюминиевые пластины, закрепленные на медной шине. Общая поверхность анода составляла ~4000 см2. Максимальная анодная плотность тока – 50 А/м2 – к концу электролиза снижалась до 1-2 А/м2. Диски в электролизере вращались со скоростью 30 о6/мин. Общая емкость электролизера 15 л.
Выделение цинка и кадмия производилось в сульфатноаммиачном электролите. Цинк выделялся при потенциале амальгамы – 0,85 В, который постепенно изменялся до -0,74 В (по водородной шкале); затем наблюдался резкий скачок и при потенциалах от -0,56 до -0,40 В выделялся кадмий.
Выделение свинца анодным окислением амальгамы в щелочных растворах было заменено цементацией. Для этой цели предварительно был приготовлен щелочной (1-н. NaОН) раствор нитрата таллия (4 л, 45 г/л ТI). Этим раствором амальгама в электролизере обрабатывалась в течение часа, причем свинец переходил в раствор за счет вытеснения им таллия из раствора в амальгаму.
Таллий из амальгамы выделялся электролизом в растворе 1-н. Н2804 при потенциалах амальгамы от -0,22 до -0,013В и отлагался на катоде в виде губки, которая затем промывалась водой, прессовалась и сплавлялась под канифолью.
В таблице 9 приведены данные полуколичественного спектрального анализа металлов, полученных при электролитическом разложении амальгам.
Таблица 9
Состав металлов по данным полуколичественного спектрального анализа

Сводный баланс по процессам цементации и элекгролиза для таллия, кадмия и цинка приведен в табл. 10-12.
В таблице 13 предсгавлен сводный баланс извлечения таллия из пылей агломерационного цеха Чимкентского завода. Из этой таблицы видно, что в проведенных опытах значительное количесгво таллия – 27,9 % – погеряно за счет цеменгации таллия железными стенками аппаратуры и груб. Эти потери могуг быть устранены заменой железных частей аппаратуры деревянными, свинцовыми, резиновыми или тщательной изоляцией железа.
Снижение потерь таллия с кеком может быть достигнуто усовершенствованием аппаратуры для выщелачивания с целью достижения более полного отделения жидкого от твердого, изменением ж: т или введением дополнительной стадии выщелачивания. Кроме того, необходимо учитывать, что кек не является отвальным и он возвращается в свинцовое производство – в шихту агломерационного цеха.
Тяллий, содержащийся в шламе, частично может 6ыть извлечен специальной обработкой шлама. Кроме того, потери таллия со шламом могут быть снижены при уменьшении шламообразования, что составляет одну из задач дальнейших исследований. Судя по некоторым наблюдениям при проведении полузаводских опытов, уменьшение шламообразования может быть достигнуто более тщательной фильтрацией раствора перед цементацией и поддержанием более высокой концентрации цинка в амальгаме.
Таблица 10
Баланс таллия при процессах цементации и электролиза

Таблица 11
Баланс кадмия при процессах цементации и электролиза

Таблица 12
Баланс цинка при процессах цементации и электролиза

Таблица 13
Сводный баланс извлечении таллия из пылей агломерационного цеха

Количество тяллия в отработанных растворах также может быть снижено, как показывают укрупненно лабораторные опыты, за счет увеличения при цементации площади контакта амальгамы с раствором.
Цинк из растворов после цементации может быть извлечен различными методами, из которых наиболее целесоообразным окажется, вероятно, осаждение его известью.
Таким образом, балансовые опыты, проведенные на укрупненной установке Чимкентского свинцового завода, показали, что по предложенной амальгамной схеме производства таллия из пылей агломерационного цеха можно получать: таллий в виде чистого металла с выходом более 65 % и таллий в оборөтных продуктах (около 30 %). Безвозвратные и неучтенные потери таллия составляют не более 5 %.
Правообладателям!
Данное произведение размещено по согласованию с ООО "ЛитРес" (20% исходного текста). Если размещение книги нарушает чьи-либо права, то сообщите об этом.Читателям!
Оплатили, но не знаете что делать дальше?