Текст книги "Код Toyota. Секреты самого сильного производства в мире"
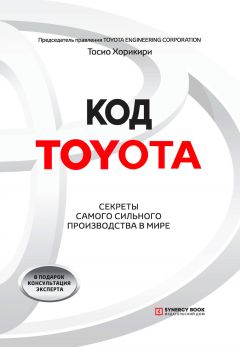
Автор книги: Тосио Хорикири
Жанр: Управление и подбор персонала, Бизнес-Книги
Возрастные ограничения: +16
сообщить о неприемлемом содержимом
Текущая страница: 6 (всего у книги 17 страниц) [доступный отрывок для чтения: 6 страниц]
2.5. Совершенствование качества
2.5.1. Встраивание качества в процессыПроцесс совершенствования качества основан на «трех китах»:
1) последующий участок является клиентом, поэтому –
2) нельзя передавать брак на следующий участок, потому что –
3) ответственность за обеспечение качества лежит на производственном подразделении – изготовителе продукции.
Другими словами, необходимо проверять качество на каждой операции и передавать на последующий этап только качественную продукцию. Важно, чтобы каждый сотрудник выполнял стандарты операции и проверял качество своей продукции при каждой своей операции.
Не передавать и не производить брак
Конечная наша цель – производить только качественную продукцию, но в реальности все равно появляется брак. Главное – вовремя его обнаружить и не пропустить на следующий процесс (участок) (схема 2-5-1а).
Встраивание качества в процесс
Проверка качества в каждом технологическом процессе → Не передавать дефектную продукцию на следующий процесс

Схема 2-5-1а. Не производить и не передавать брак
Принципы обеспечения качества на операциях:
1) следовать стандартизированному порядку выполнения:
– выполнять операцию строго по рабочей инструкции, стандартам;
– в случае нарушений стандартизированной последовательности выполнения операции необходимо провести пересмотр методов обучения или изменить стандарты операции;
2) проводить самопроверку:
– часты ли ошибки при выполнении операции?
– часто ли появляются дефекты?
– удобно ли следовать указанному порядку?
3) взаимная проверка качества – после операций, часто выдающих дефекты, необходимо проверять качество еще раз, чтобы предотвратить передачу брака на последующий этап;
4) совершенствование операций, трудных для выполнения:
– операции, последовательность которых сложно соблюдать
– операции в неудобной позе;
– операции, ведущие к частым ошибкам;
– операции, часто выдающие дефекты;
– операции не на предназначенном для них месте.
Встраивание качества в процессы (см. схему 2-5-1b)
При изменениях в производстве необходимо провести анализ первой партии продукции на предмет ее качества. Очень часто бывает, что, не учтя изменения, внесенные в процесс изготовления, производят большое количество брака. С этой же целью – установления первопричины возникновения дефекта – образцы продукции из первого выпуска лучше сохранить до появления следующей партии.

Схема 2-5-1b. Встраивание качества в процессы
2.5.2. Система остановки в фиксированном месте
Принципы системы остановки в фиксированном месте указаны на схемах 2-5-2а и 2-5-2b:
1) операции, производимые на конвейере, необходимо начинать на указанной стартовой точке и заканчивать точно в определенном месте;
2) при отклонении или задержке в выполнении операции сотрудник должен вызвать своего непосредственного руководителя и в то же время дать информацию на доску управления участком (андон), чтобы высветился номер операции;
3) если отклонение в операции или ее задержка не устраняются до начала следующего сборочного поста конвейера, то конвейер автоматически останавливается;
4) строгое соблюдение стандартов операции и недопущение передачи дефектов на следующий участок.
• Операция начинается с линии остановки в фиксированном положении и заканчивается на следующей линии остановки в фиксированном положении.
• Если операция не закончена, то линия останавливается на отсечке остановки в фиксированном положении.

Схема 2-5-2а. Система остановки линии в фиксированном месте

Схема 2-5-2b. Работа на линии с остановкой в фиксированном месте (соблюдение стандартов)
2.5.3. Пропускная способность технологического процесса (табл. 2-5-3)
В любом производстве следует помнить о возможностях технологического процесса. Принципы следующие:
1) необходимо проверять и анализировать разбросы в машинной обработке и сборке, чтобы понимать технологические возможности процесса;
2) на основе этого определить методы управления оборудованием и механизмами;
3) индекс воспроизводимости процесса можно вычислить с помощью формулы:
СР = Т/6σp,
где Т – ширина поля допуска;
σp – среднеквадратичное отклонение.
Таблица 2-5-3 – Обеспечение воспроизводимости оборудования

Следование принципу «пока-ёкэ» также помогает бороться с браком. В общем смысле под «пока-ёкэ» можно понимать устройства (процедуры), благодаря которым дефекты выявляются автоматически. При этом неважно, возник он из-за неполадок оборудования или вследствие человеческого фактора (таблица 2-5-4). «Пока-ёкэ» предотвращает появление дефектов в производственных процессах.
Таблица 2-5-4 – Способы защиты от непреднамеренных ошибок (пока-ёкэ)

«Нулевая ошибка» достигается двумя способами: 1) предотвращение неосторожности (невнимательности) персонала и 2) автоматическая остановка линии при неполадках оборудования.
2.5.5. Разработка операции сдачи качестваСистема, четко определяющая метод проверки качества на каждом производственном этапе, чтобы дефектная продукция не переходила на последующий участок (или дальше, на рынок клиенту), представлена на схемах 2-5-5а–2-5-5e.

Схема 2-5-5а. Система сквозного качества (сборочный процесс)
Необходимо четко определить методы гарантии качества, разделив работы по гарантии качества на недопущение возникновения брака и предотвращение передачи дефектной продукции на последующий процесс.

Схема 2-5-5b. Гарантия сквозного качества

Схема 2-5-5c. Недопущение возникновения дефектов: способы обеспечения

Схема 2-5-5d. Недопущение передачи дефектной продукции
В случае несоответствия нижеследующим критериям необходимо проведение кайдзен-мероприятий

Схема 2-5-5e. Соответствие процесса требованиям по качеству (решение)
Уровень гарантии качества можно четко определить по методу производства. Надо либо совершенствовать операции, выдающие низкий уровень качества, либо повышать степень надежности применяемых методов обеспечения качества.
Если используемые методы проверки качества имеют низкую надежность, необходимо совершенствовать методы выполнения работы. Также следует составить лист проблем, и в первую очередь решать проблемы с наиболее низкими показателями.
2.5.6. Деятельность кружков качестваОпределение и цель кружков качества даны в таблице 2-5-6а.
Кружки качества позволяют:
1) стимулировать к саморазвитию;
2) уважать самостоятельную работу;
3) действовать группой;
4) всем участвовать в деятельности;
5) применять на практике методы управления качеством;
6) активизировать персонал;
7) способствовать взаимному развитию;
8) разрабатывать и реализовывать кайдзен-предложения;
9) проводить деятельность в тесном контакте с коллегами на рабочем месте;
10) иметь общее понимание о качестве, проблемах и необходимости кайдзен-работы.
Таблица 2-5-6а – Работа кружков качества

В таблице 2-5-6b обозначены задачи, которые прорабатываются в кружке качества. Озвучиваются все проблемы на рабочих местах и затем обдумываются способы их решения. В таком активном взаимодействии каждый работник может почувствовать, как он повышает свои навыки, профессионально растет.
На схеме 2-5-6c обозначено содержание деятельности кружков качества. По каждой теме выбирается лидер, который координирует и продвигает кайдзен-работу.
Важно по очереди менять лидеров тематических направлений из числа участников коллектива с тем, чтобы каждый получил опыт работы в рамках кружка качества.
Таблица 2-5-6b – Темы, поднимаемые в кружках качества


Схема 2-5-6с. Порядок работы кружка качества
2.6. Техника безопасности и обслуживание оборудования
2.6.1. Техника безопасности прежде всегоВ таблице 2-6-1 собраны базовые понятия деятельности по обеспечению безопасности на рабочих местах.
Если оборудование поломается, его можно восстановить, затратив определенную сумму. Но в случае травмы человека бывает, что его здоровье уже не восстановить. Особенно при смертельных случаях – деньги не помогут. Поэтому безопасность на рабочих местах необходимо ставить во главу угла.
На первый взгляд кажется, что сокращение трудозатрат и обеспечение безопасности не связаны между собой, но это не так. Когда выполняется ненужная работа, неудобная операция, манипуляции с превышением необходимого физического усилия или исполнитель торопится при выполнении своих действий, часто возникают травмоопасные ситуации. Поэтому кайдзен должен быть направлен и на сокращение трудозатрат.
Таблица 2-6-1 – Безопасность труда прежде всего

Нижеуказанные направления деятельности содействуют обеспечению безопасности труда:
• 4С на рабочих местах – база для обеспечения безопасности на всем производстве;
• деятельность по предотвращению рисков – все работники должны принимать участие в выявлении опасных мест и действий;
• система спонтанного выдвижения предложений по повышению уровня техники безопасности – рискованные моменты, которые увидели или почувствовали сотрудники, должны быть зафиксированы, приняты к рассмотрению и устранены;
• система аттестации рабочих мест по охране труда и технике безопасности – руководитель производственного подразделения инспектирует рабочие места и определяет, соблюдаются ли стандартизированные операции, выполняются ли они правильно, выполняются и совершенствуются ли все требования по охране труда и технике безопасности – и затем сертифицирует рабочее место как безопасное (аттестация проводится два раза в год);
• «пока-ёкэ» (приспособления, предотвращающие ошибки оператора) – даже если вы работаете с большой осторожностью, все равно случаются ошибки, недоразумения или какие-то моменты забываются. Поэтому на оборудовании, на котором может произойти несчастный случай, устанавливается защитное устройство, например, замки безопасности, блокираторы, система, включающая оборудование только с помощью обеих рук, автоматические защелки и т. п.
2.6.2. Обслуживание оборудованияЧрезвычайно важно, чтобы обслуживание оборудования проводилось совместно теми, кто на нем работает, и теми, кто осуществляет его планово-предупредительное и техническое обслуживание (схема 2-6-2а).

Схема 2-6-2а. Обслуживание оборудования
Есть два вида обслуживания оборудования – самостоятельное и профессиональное техническое.
Самостоятельное обслуживание должно базироваться на принципе «сам береги оборудование, на котором работаешь». Самообслуживание подразумевает чистку оборудования, его ежедневные проверки, заправки маслом, подтягивание болтов, восстановление при малых аварийных простоях, замену расходных материалов, небольшие совершенствования.
Профессиональное обслуживание
Этот процесс предполагает прежде всего профилактические мероприятия (ремонты с целью предотвращения поломок и отклонений) и корректирующие действия (аварийные ремонты, пусконаладка оборудования после поломки).
При любом виде обслуживания необходимо добиваться сокращения его времени.
Разделение обязанностей по обслуживанию оборудования между эксплуатирующим и обслуживающим персоналом достигается путем их совместных переговоров, но важно, чтобы за большую часть моментов отвечали те, кто эксплуатирует (схема 2-6-2b).

Схема 2-6-2b. Взаимодействие эксплуатационного и обслуживающего подразделений по обслуживанию оборудования
2.7. Создание рабочих мест, где хочется работать
2.7.1. Роль линейных руководителейВ создании рабочих мест, на которых приятно работать, очень важную роль играет имеющаяся система функциональных обязанностей (схема 2-7-1).

Схема 2-7-1. Роль линейных руководителей
Линейным руководителям необходимо следовать важным шести правилам:
1) постоянно наблюдать за производством (следить за рабочими местами) – то есть знать абсолютно все про участок, которым они руководят; знать все, что происходит на каждом рабочем месте каждый день, чтобы решать возникающие проблемы, осуществляя тем самым кайдзен;
2) обучать и развивать подчиненных – следя за их успехами/неудачами, вовремя проводить необходимое обучение с целью повышения навыков, развивать их трудовую интуицию, обучать различным приемам и методам для устранения отклонений в процессе операции и для повышения производительности; но если работники не следуют стандартизованным операциям, немедленно сделать замечание;
3) иметь широкий взгляд и давать указания с учетом всей картины производства: при возникновении проблем нельзя принимать решение, ориентируясь только на одно рабочее место; необходимо давать указания, лишь хорошо осознав состояние предыдущего и последующего участков, внешних заказчиков и т. д.;
4) участвовать в линейной работе (непосредственная работа на производстве) – это приходится делать, когда:
– работник не вышел на смену или во время сверхсрочной работы не хватает персонала,
– для совершенствования проблемной операции необходимо проверить порядок ее выполнения и удобность,
– необходимо выполнить вспомогательные работы в случае задержки производства или отклонения от нормы.
Примечание: Руководителям ни в коем случае нельзя работать на линии только потому, что у них появилось свободное время! Принимать участие в линейной работе необходимо только с позитивным желанием найти проблемы и устранить их;
5) знакомиться с новыми технологиями – продукция, оборудование, методы обработки и др. меняются каждый день, поэтому необходимо получать новые знания и навыки, чтобы идти в ногу со временем;
6) создавать рабочие места, на которых приятно работать, для этого:
– следует прислушиваться к мнению сотрудников;
– повышать навыки и компетенции подчиненных (обучение смежным специальностям);
– принимать участие в устранении тяжелых в выполнении операций, повышая тем самым мотивацию работников.
2.7.2. Обучение смежным специальностямРотация хороша тем, что работники, периодически меняя свой вид деятельности, с сохранением ответственности за нее, приобретают (и повышают) навыки во многих сферах (схема 2-7-3а). Развивая таким образом свои способности и получая новый опыт, в процессе исполнения новых функций они выявляют неудобные операции и причины дефектов. В этом тоже проявляется кайдзен, и это так же важно для появления чувства взаимопомощи у работников и предотвращения косности и равнодушия.
При расширении производства меняется и время такта, а также содержание процессов. Чтобы этому соответствовать, и необходима система освоения новых операций, компетенций и специальностей.
2.7.3. Система кайдзен-предложенийВ Toyota фиксируются только уже реализованные предложения по улучшениям, эффективность которых уже была проверена на практике, а не идеи, поскольку их сложно оценить, понять до конца текущий или будущий эффект. Следовательно, очень важно подавать только те предложения, которые были воплощены в жизнь на рабочих местах во взаимодействии с другими сотрудниками (схема 2-7-3b).
Цель – каждый сотрудник мог работать как минимум на трех операциях (процессах).

Схема 2-7-3а. Проведение обучения смежным специальностям (операциям) и ротация работ

Схема 2-7-3b. Система подачи кайдзен-предложений
Глава 3
Обеспечение качества
3.1. Основы обеспечения качества
В T-TPS особое внимание уделяется вопросам обеспечения качества. В предыдущей главе уже говорилось о том, что в прошлом TPS занималась встраиванием качества в операции, основываясь на принципах «дзидока» (автономизации, подразумевающей самостоятельную остановку оборудования (процесса) в случае отклонения от нормы и отделение оператора от наблюдения за работой оборудования). Люди, работающие с T-TPS, включая меня, уже в течение 30 лет активно работают над повышением качества, исходя из мышления «дзидока». В то же время эти подходы не стоят на месте – они продолжают развиваться.
Напомню основное правило качества – «клиент прежде всего». Клиент сможет оценить качество только после того, как продукция разработана, изготовлена и передана в его руки. Качество в данном случае включает потребительские характеристики продукции, которые клиент оценивает, – «да, за такое качество я готов заплатить эту цену».
Качество продукции определяет ее ценность. Особенно это справедливо в отношении автомобиля, поскольку речь идет о человеческой жизни, что очень важно. Даже небольшой дефект может привести не только к значительному ущербу, но и к человеческим жертвам. Если у клиента возникли неприятности в связи с дефектной продукцией, то компания-изготовитель несет огромные затраты на выплату убытков, отзыв автомобилей для исправления дефектов и т. д. Кроме того, это подрывает доверие к продукции, и компания терпит еще большие убытки.
Автомобили – дорогостоящая продукция со сроком использования зачастую более 10 лет. Поэтому такое большое внимание уделяется надежности автомобиля и ее постоянному совершенствованию. Именно за счет первостепенного внимания к качеству в Toyota мы и достигли высокого доверия наших клиентов.
С другой стороны, из-за того, что уровень доверия высок, даже незначительные проблемы подрывают наш имидж.
Хотелось бы объяснить наше понимание качества. Клиенты требуют «естественное качество» и «привлекательное качество». При этом, с точки зрения компании, существует только «стандарт качества», и она принимает решения, базируясь на нем. Объясним это с помощью рисунка 3–1. «Негативное качество» означает качество ниже установленного стандарта (брак). Граница, соответствующая требованиям качества, установленным в компании, находится между высоким и низким стандартом. Если продукция попадает в рамки допусков (этих границ), то подразумевается, что она прошла соответствующий контроль качества на производстве и считается качественной. Такая гарантия «естественного» качества является, конечно, очень важной, но, тем не менее, потребители часто ожидают более привлекательного качества.

Рис. 3–1. Оценка с позиции клиентов
Известно много случаев, когда компании составляют свой стандарт, и на этом останавливаются. Дальнейшая их деятельность по обеспечению качества сводится лишь к соблюдению принятых стандартов, тогда как необходимо не только сохранять установленные стандарты, но и стремиться к более высоким уровням, думать о качестве с точки зрения клиента.
3.2. Обеспечение качества в Toyota
Целью деятельности по повышению качества в Toyota является сведение дефектов (брака) к нулю. Это легко на словах, но, с другой стороны, как минимизировать дефекты, если не стремиться к их нулевому уровню?
В Toyota для этого всегда принимались различные меры, в основе которых лежит принцип автономизации (дзидока). TPS заложила основы такого мышления, а T-TPS продолжает его развивать (рис. 3-2а).
Система обеспечения качества в Toyota основывается на подходе «завершенности собственного процесса» и включает в себя пять следующих направлений:
1) обеспечение качества внутри обрабатывающего процесса (автономизация, дзидока);
2) матрица управления качеством (QM Matrix, QA Network);
3) встроенное в операции качество (Kanketsu Process, Quality Moduled, Quality Built in Process);
4) опережающее обеспечение качества (QA in Advance);
5) повышение качества с помощью АПРМ (Quickening Factory, QF).

Рис. 3-2а. Обеспечение качества в Toyota. Целевые показатели качества – 0 % брака
Если раньше один из столпов TPS – дзидока – ассоциировался больше с сокращением трудозатрат, то сейчас с автономизацией связывают в основном качество. По большей части благодаря самостоятельным исследованиям самими линейными сотрудниками (в том числе в рамках кружков качества) началась по-настоящему добровольная и демократическая деятельность, и в итоге деятельность по обеспечению качества стала развиваться более активно.
При этом важно, чтобы в обеспечении качества участвовали все. Главное – исследовать причины недостающего качества в алгоритме «по месту – по факту» (рис. 3-2b).
Обычно контроль качества является некой теорией, базирующейся на статистическом анализе. Тем не менее, такие данные неточно отражают текущую ситуацию на рабочем месте или отражают ее частично. Есть также риск, что они могут быть составлены «как удобно» или «как нужно». Поэтому так важно анализировать реальное рабочее место, анализировать автономно, действуя строго по принципу «по месту – по факту».
Наиболее близки к рабочему месту сами рабочие (операторы). От них прежде всего и зависит качество продукции. Следовательно, качество зависит от отношения линейного сотрудника к своей деятельности.
Итак, необходимо понять, что за качество отвечают не отделы контроля качества – качество обеспечивает каждый работник производства.

Рис. 3-2b. Клиент прежде всего – качество прежде всего
Внимание! Это не конец книги.
Если начало книги вам понравилось, то полную версию можно приобрести у нашего партнёра - распространителя легального контента. Поддержите автора!Правообладателям!
Данное произведение размещено по согласованию с ООО "ЛитРес" (20% исходного текста). Если размещение книги нарушает чьи-либо права, то сообщите об этом.Читателям!
Оплатили, но не знаете что делать дальше?