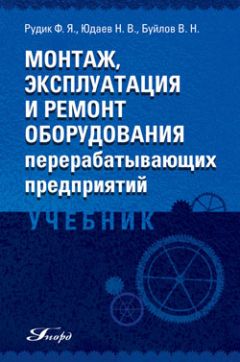
Автор книги: Феликс Рудик
Жанр: Техническая литература, Наука и Образование
сообщить о неприемлемом содержимом
Текущая страница: 15 (всего у книги 20 страниц)
Глава 15
Организация службы главного механика
Главный механик обеспечивает бесперебойную и технически правильную эксплуатацию и надежную работу оборудования, повышение ее сменности, содержание в работоспособном состоянии на требуемом уровне точности. Организует разработку планов (графиков) осмотров, испытаний и профилактических ремонтов оборудования в соответствии с положениями Единой системы планово-предупредительного ремонта, утверждает эти планы и контролирует их выполнение, обеспечивает техническую подготовку производства. Согласовывает планы (графики) с подрядными организациями, привлекаемыми для проведения ремонтов, своевременно обеспечивает их необходимой технической документацией, участвует в составлении титульных списков на капитальный ремонт. Организует работу по учету наличия и движения оборудования, составлению и оформлению технической и отчетной документации. Руководит разработкой нормативных материалов по ремонту оборудования, расходу материалов на ремонтно-эксплуатационные нужды, анализом показателей его использования, составлением смет на проведение ремонтов, оформлением заявок на приобретение материалов и запасных частей, необходимых при эксплуатации оборудования. Организует межремонтное обслуживание, своевременный и качественный ремонт и модернизацию оборудования, работу по повышению его надежности, технический надзор за состоянием, содержанием, ремонтом зданий и сооружений, обеспечивает рациональное использование материалов на выполнение ремонтных работ. Принимает участие в подготовке предложений по аттестации, рационализации, учету и планированию рабочих мест, по модернизации оборудования, реконструкции, техническому перевооружению предприятия, внедрению средств комплексной механизации и автоматизации технологических процессов, охраны окружающей среды, в разработке планов повышения эффективности производства. Организует проведение инвентаризации основных средств, определяет устаревшее оборудование, объекты, требующие капитального ремонта, и устанавливает очередность производства ремонтных работ. Участвует в экспериментальных, наладочных и других работах по внедрению и освоению новой техники, в испытаниях оборудования, в приемке нового и вышедшего из ремонта оборудования, реконструируемых зданий и сооружений. Изучает условия работы оборудования, отдельных узлов и деталей, разрабатывает и осуществляет мероприятия по предупреждению внеплановых остановок оборудования, продлению сроков службы узлов и деталей, межремонтных периодов, улучшению сохранности оборудования, повышению надежности его в эксплуатации, организует на предприятии специализированный ремонт, централизованное изготовление запасных частей, узлов и сменного оборудования. Принимает участие в изучении причин повышенного износа оборудования, его простоев, расследовании аварий, разработке и внедрении мероприятий по их ликвидации и предупреждению. Руководит разработкой и внедрением мероприятий по замене малоэффективного оборудования высокопроизводительным, по сокращению внеплановых ремонтов и простоев оборудования, снижению затрат на ремонт и его содержание на основе применения новых прогрессивных методов ремонта и восстановления деталей, узлов и механизмов. Обеспечивает контроль за качеством работ по монтажу оборудования, рациональным расходованием средств на капитальный ремонт, правильностью хранения оборудования на складах, своевременностью проверки и предъявления органам, осуществляющим государственный технический надзор, подъемных механизмов и других объектов, внесения изменений в паспорта на оборудование. Принимает меры по выявлению неиспользуемого оборудования и его реализации, улучшению эксплуатации действующего оборудования, организации ремонтных работ на основе механизации труда и внедрения прогрессивной технологии, совершенствованию организации труда работников ремонтной службы. Обеспечивает соблюдение правил охраны труда и техники безопасности при проведении ремонтных работ. Участвует в разработке и внедрении мероприятий по созданию безопасных и благоприятных условий труда при эксплуатации и ремонте оборудования, в рассмотрении рационализаторских предложений, касающихся улучшения работы оборудования, дает отзывы и заключения на наиболее сложные из них, а также на проекты отраслевых нормативов и государственных стандартов, содействует внедрению принятых рационализаторских предложений. Принимает участие в составлении заявок на приобретение оборудования на условиях лизинга. Руководит работниками отдела и подразделениями, осуществляющими ремонт и обслуживание оборудования, зданий и сооружений предприятия, организует работу по повышению их квалификации.
Главный механик должен знать: нормативные, методические и другие материалы по организации ремонта оборудования, зданий, сооружений; профиль, специализацию и особенности организационно-технологической структуры предприятия, перспективы его развития; основы технологии производства продукции предприятия; организацию ремонтной службы на предприятии; порядок и методы планирования работы оборудования и производства ремонтных работ; Единую систему планово-предупредительного ремонта и рациональной эксплуатации технологического оборудования; производственные мощности, технические характеристики, конструктивные особенности, назначение и режимы работы оборудования предприятия, правила его эксплуатации; методы монтажа и ремонта оборудования, организацию и технологию ремонтных работ; порядок составления ведомостей дефектов, паспортов, альбомов чертежей запасных частей, инструкций по эксплуатации оборудования и другой технической документации; правила приема и сдачи оборудования после ремонта; требования рациональной организации труда при эксплуатации, ремонте и модернизации оборудования и ремонтной оснастки; передовой отечественный и зарубежный опыт ремонтного обслуживания предприятия; основы экономики, организации производства, труда и управления; основы экологического законодательства; основы трудового законодательства; правила и нормы охраны труда.
Инженер по ремонту осуществляет разработку перспективных и текущих планов (графиков) различных видов ремонта оборудования и других основных фондов предприятия (зданий, систем водоснабжения, канализации, воздухопроводов и т. д.), а также мер по улучшению их эксплуатации и обслуживания, контролирует выполнение утвержденных планов (графиков). Способствует внедрению систем комплексного регламентированного обслуживания, обеспечивающих своевременную наладку и ремонт оборудования, эффективную работу предприятия, прогрессивной технологии ремонта, высокоэффективных ремонтных приспособлений, механизации трудоемких процессов. Принимает участие в проверке технического состояния оборудования, качества ремонтных работ, а также в приемке вновь поступающего на предприятие оборудования, в необходимых случаях оформляет документацию на его списание или передачу другим предприятиям. Организует подготовку ремонтных работ, определяет потребность в запасных частях для ремонта оборудования, по обеспечению ими предприятия на условиях кооперации. Осуществляет контроль за деятельностью подразделений предприятия, участвующих в проведении ремонтных работ и испытаний оборудования, за соблюдением правил эксплуатации, технического обслуживания и надзора за ним. Разрабатывает мероприятия, направленные на совершенствование организации обслуживания и ремонта оборудования, на снижение трудоемкости и стоимости ремонтных работ, улучшение их качества, повышение эффективности использования основных фондов (повышение износостойкости и уменьшение простоев оборудования). Участвует в работе по планированию технического развития производства, капитального ремонта и модернизации основных фондов, составлении баланса производственных мощностей и их использования. Разрабатывает нормативные материалы по профилактическому обслуживанию и ремонту оборудования (нормативы ремонтно-эксплуатационных затрат, сроков службы запасных частей, номенклатуры сменных и быстроизнашивающихся деталей, нормы и лимиты расхода смазочных материалов). Анализирует причины повышенного износа, аварий и простоев оборудования и участвует в расследовании их причин, а также причин производственного травматизма, принимает меры по его предупреждению. Осуществляет контроль за соблюдением установленных сроков составления ведомостей дефектов, заявок на проведение ремонта. Составляет заявки, спецификации на запасные части, материалы, инструмент, контролирует правильность их расходования. Готовит материалы для заключения договоров с предприятиями-изготовителями на поставку запасных частей и оборудования, а также со специализированными подрядными организациями на капитальный ремонт основных (промышленно-производственных и непромышленных) фондов, осуществляет контроль за расходованием средств на эти цели. Принимает участие в работе, связанной с разработкой и внедрением стандартов и технических условий по эксплуатации, содержанию и ремонту оборудования. Дает заключения по рационализаторским предложениям и изобретениям, по вопросам совершенствования конструкции оборудования, организации ремонтных работ и технического обслуживания оборудования, оказывает рационализаторам и изобретателям практическую помощь и организует внедрение принятых предложений. Обобщает и распространяет передовой опыт организации ремонта и эксплуатации оборудования. Ведет учет и паспортизацию оборудования, зданий, сооружений и других основных фондов предприятия, вносит в паспорта изменения после их ремонта, модернизации и реконструкции, составляет необходимую техническую документацию и ведет установленную отчетность.
Инженер по ремонту должен знать: постановления, распоряжения, приказы, методические и нормативные материалы по техническому обслуживанию и ремонту оборудования; перспективы технического развития предприятия; организацию ремонтных работ и технического обслуживания оборудования; единую систему планово-предупредительного ремонта и рациональной эксплуатации технологического оборудования; технические характеристики, конструктивные особенности, назначение и режимы работы оборудования предприятия, правила его технической эксплуатации; методы планирования ремонтных работ; основные технологические процессы производства продукции предприятия; передовые системы ремонтов и технологию ремонтных работ; порядок составления смет на проведение ремонтов, заявок на оборудование, материалы, запасные части, инструмент и т. п.; основы экономики, организации производства, труда и управления; основы трудового законодательства; правила и нормы охраны труда.
Глава 16
Производственный процесс ремонта оборудования
Производственный процесс ремонта оборудования представляет собой комплекс работ, выполняемых в определенной последовательности на специальных рабочих местах, в результате которых восстанавливается работоспособность отдельных деталей, узлов, агрегатов или машины в целом. Структура технологического процесса ремонта представляет собой следующую последовательность операций: приемка в ремонт, наружная мойка машин; разборка машин на агрегаты, узлы и детали; мойка узлов и деталей; дефектация деталей; восстановление изношенных или поврежденных деталей; комплектация узлов и агрегатов; сборка, регулировка, обкатка и испытания узлов, агрегатов и машины; окраска и сдача отремонтированной машины.
Приемка в ремонт осуществляется по специальным техническим условиям, где излагаются все основные требования, которым должны удовлетворять узлы, агрегаты и машины. Организация при сдаче машины в ремонт представляет следующую документацию: акт периодического технического осмотра, акт приемки машины из предыдущего ремонта (если был), заводской технический паспорт с необходимыми отметками. Сдает машину (агрегат, узел) в ремонт ответственный представитель технической службы организации. Принимает машину в ремонт работник технического контроля сервисного предприятия, проводя внешний осмотр, прослушивание отдельных агрегатов и механизмов проверяя их в работе. При этом определяется комплектность машины (агрегата, узла), повреждения (изломы, пробоины, трещины и т. д.), состояние окраски и креплений. После чего оформляется соответствующий акт, в котором отмечают срок службы (наработку) после предыдущего ремонта (если был), а также состояние базовых деталей, комплектность машины и дефекты аварийного характера.
При подготовке машины к ремонту из системы теплообмена и смазки удаляют рабочие жидкости. Затем эти полости промывают моющим раствором с температурой 70–80 °C.
Наружная мойка машин выполняется в специальных моечных камерах или помещениях. Моющий раствор подается под давлением 0,6–1,2 МПа. При этом высокой эффективностью обладает пароводоструйный способ наружной мойки машин.
При разборке машин не допускается обезличивание совместно обработанных и базовых деталей. Например, у компрессоров нельзя обезличивать коленчатый вал, шатуны и их крышки, блоки и крышки коренных подшипников. Все необезличиваемые детали или тележки с комплектами деталей отмечаются бирками с номером заказа на весь период ремонта машины.
Разборку агрегатов и узлов на детали ведут на передвижных или стационарных стендах-тележках, монтажных столах или конвейерах. На специализированных сервисных предприятиях применяют поточно-механизированный способ разборки машин. Разборка машин подразделяется на основные и вспомогательные работы. К основным работам относятся те, которые изменяют конструктивное состояние машины (отвертывание болтов и гаек, снятие крышек, картеров, втулок, подшипников и т. д.). К вспомогательным работам относятся перемещения, установки и крепления на стенды разбираемых агрегатов, узлов и деталей. Время выполнения этих операций зависит от степени механизации и автоматизации. Поэтому при разборке машин применяются пневматические и электрические гайковерты, механические и гидравлические съемники, кантователи и подъемно – транспортные устройства.
Снятые с машины крупногабаритные агрегаты устанавливают непосредственно на тележки и доставляют к месту их разборки, а мелкогабаритные узлы и детали предварительно укладывают в специальные ящики или корзины. Крепежные детали помещают отдельно в корзины или ящики для мойки и сортировки. В условиях мелких мастерских рекомендуется завертывать болты и шпильки на свои места в корпусные детали, если последние не требуют сложного ремонта.
Слесари должны хорошо знать конструкцию машин, технологические приемы применения оборудования, приспособлений и съемников, последовательность выполнения разборочных работ, приемы разъединения посадок с натягом. Машины сначала разбирают на агрегаты, затем агрегаты на узлы, а узлы на детали, в соответствии технологическим процессом и наибольшим удобством в работе. Это позволяет расширить фронт работ, создать специализированные рабочие места для отдельных агрегатов, организовать параллельное выполнение операций, тем самым повысить производительность труда. Применение приемов и инструмента, способствующих повреждению объектов ремонта, недопустимо. Агрегаты отправляются в комплектном виде на соответствующие специализированные отделения или посты ремонта. Все крепежные детали следует складывать по размерам в комплекте на ремонтируемый объект. Детали, которые при изготовлении обрабатывают в сборе, а также приработавшиеся во время эксплуатации и при этом годные к дальнейшей работе, запрещается раскомплектовывать, для чего их маркируют с сохранением взаимного расположения.
16.1. Мойка деталей и узлов
В прямой зависимости от мойки состоит качество ремонта деталей (особенно контрольных операций), производительность труда рабочих, надежность отремонтированных машин и общий уровень технической культуры ремонтных предприятий. Загрязнители состоят из нагара, накипи, абразивных и металлических частиц, а также биологических образований.
Для мойки применяют моющие составы температурой 80–90 °C. Минеральные масла, смолы, сажа и другие компоненты плохо смачиваются водой, поэтому в состав моющих растворов вводят поверхностно-активные вещества и щелочи, которые разрыхляют и разрывают масляную пленку, отрывают частицы масла вместе с загрязнителями от поверхности детали и замещают их, препятствуя возврату загрязнителя на поверхность детали. Растворы должны содержать вещества, способные обволакивать оторванные частицы прочной пленкой. Масла делятся на омыляемые и неомыляемые. Растительные масла и животные жиры омыляемы, то есть, реагируя со щелочами, они образуют мыла, которые хорошо растворяются в воде. Минеральные масла неомыляемые и под действием щелочей образуют эмульсии. Для усиления действия щелочи в раствор добавляют эмульгаторы, которые значительно снижают силу сцепления загрязнителя с поверхностью детали.
Эмульгирующее действие моющих средств проявляется также в их способности исключать растворение грязевых частиц в промывочной жидкости. В зависимости от соотношения удельных весов загрязнитель может находиться на поверхности во взвешенном состоянии и на дне. Моечные машины оснащаются фильтрующими элементами для возможно более длительного использования раствора.
В ремонтном производстве наиболее распространены следующие способы мойки: погружением в ванны, термическая и струйная.
Мойка погружением проводится в ваннах с органическими растворителями или синтетическими моющими растворами. Для интенсификации процесса мойки создают движение раствора затопленными струями, пропусканием электрического тока и вибрацией.
Термическая очистка проводится в ваннах с расплавом солей и щелочей. Струйная мойка имеет три основных разновидности: мойка непрерывными, пульсирующими и пароводяными струями.
Мойка деталей в стационарных ваннах щелочным раствором или синтетическими моющими препаратами проводится при температуре 80–90 °C. Для экономии моющих жидкостей в конструкции ванны предусмотрена решетка 2 (рис. 138), поддерживающая промываемые детали на определенном расстоянии от дна, достаточном для накапливания отстоя. Отстой периодически удаляют из ванны через нижнюю сливную пробку.
Основные преимущества очистки деталей вываркой – простота установки и возможность применения сильнодействующих моющих средств с последующей мойкой в струйных машинах.
Термические способы очистки деталей машин основаны на удалении загрязнений нагревом их до температуры, при которой они либо сгорают, либо теряют механическую прочность и легко отделяются от поверхности загрязненной детали.

Рис. 138. Ванна для мойки деталей в горячем щелочном растворе: 1 – ванна; 2 – решетка; 3 – устройство для нагрева раствора; 4 – зонт.
Состав и концентрация моющих растворов оказывают преобладающее влияние на качество и производительность мойки. В ремонтном производстве широкое применение нашли растворы каустической соды. При струйной мойке обычно применяют растворы с концентрацией каустической соды до 3–5 %, а в выварочных ваннах – до 10–15 %. Производительность мойки повышается на 20–30 % при введении в указанные растворы 2 г/л сульфанола. Для улучшения эмульгирующих свойств и моющей способности растворов в них добавляют мыло, жидкое стекло, спирты и др. Несмотря на это, эмульгирующая способность растворов каустической соды все же недостаточна. Отмытые загрязнения вскоре отделяются от раствора и вызывают повторное загрязнение деталей. При контакте каустической соды с воздухом происходят ее карбонизация и увлажнение. Наиболее перспективны синтетические моющие средства. Основная технологическая особенность этих препаратов – возможность проведения очистки по замкнутому циклу с многократным использованием моющего раствора. Это обусловлено их способностью образовывать эмульсии с оптимальным временем существования, которые в дальнейшем отфильтровываются.
16.2. Дефектация деталей
После мойки детали подвергают контролю и дефектации. Это делается для того, чтобы определить их техническое состояние, выявить возможность их последующего использования при сборке машин или назначить способ восстановления, а также выбраковку негодных. В процессе контроля все детали разделяют на годные к использованию без ремонта, требующие ремонта и подлежащие выбраковке.
Дефектация деталей выполняется в определенной последовательности. В первую очередь проверяют износы и неисправности, по которым чаще всего выбраковывают деталь, например трещины в них. Если деталь имеет повреждения, соответствующие выбраковке, остальные дефекты этой детали не проверяют. Выбраковочные износы и неисправности в зависимости от их характера определяют следующими способами: наружным осмотром, простукиванием и прослушиванием (сколы, трещины и т. д.); промером универсальным и специальным измерительным инструментом, скобами-шаблонами, калибрами, пробками и т. п. (овальность, конусность, допустимые размеры и т. д.); специальными приспособлениями, дефектоскопией люминесцентной, магнитной и ультразвуковой (мелкие невидимые трещины и раковины и т. п.); гидравлическим испытанием на специальных стендах (проверка герметичности впускных и выпускных труб, теплообменников, емкостей и т. д.).
Магнитный метод основан на появлении магнитного поля рассеяния при прохождении через дефектную деталь магнитного потока (рис. 139). Поле рассеяния образуется в связи с резким изменением магнитной проницаемости в местах дефекта.
Силовые линии магнитного потока, проходящего через деталь, при встрече с дефектным участком огибают его. Для выявления поля рассеяния применяют ферромагнитный порошок или суспензию. В качестве магнитного порошка используют прокатную и ковочную окалину, молотую чугунную стружку или отсепарированную магнитом наждачную пыль после шлифовки стальных изделий. Магнитную суспензию приготовляют из трансформаторного масла (40 % по объему), керосина (60 %) и магнитного порошка из расчета 50 г на 1 л смеси. Если деталь посыпать сухим ферромагнитным порошком или полить суспензией, то их частицы, попав в поле рассеяния, намагничиваются и притягиваются к краям дефектного участка детали, как к полюсам магнита. Наносить магнитный порошок или суспензию можно как в присутствии магнитного поля (контроль в приложенном поле), так и после прекращения действия магнитного поля (контроль на остаточной намагниченности). Первый вид контроля более чувствителен при выявлении внутренних дефектов детали и обязателен при неизвестных магнитных характеристиках материала детали. Второй вид контроля применяется для выявления поверхностных трещин в мелких и средних деталях, изготовленных из высоко-углеродистых и легированных сталей. По сравнению с первым видом контроля он производительнее и удобнее.

Рис. 139. Схемы способов намагничивания деталей: а и б – продольное; д и е – комбинированное; 1 – намагничиваемая деталь; 2 – электромагнит.
После магнитной дефектоскопии детали размагничивают, пропуская их через соленоид. Крупногабаритные детали, например вал, размагничивают пропусканием через него тока с постепенным уменьшением его значения до нуля. На ремонтных предприятиях наиболее широкое распространение получил универсальный магнитный дефектоскоп типа М-217. Он позволяет проводить циркулярное, продольное и местное намагничивание, магнитный контроль и размагничивание. Промышленностью выпускаются и другие магнитные дефектоскопы, которые успешно используются в ремонтном производстве. К ним относятся стационарные МЭД-2 и 77МД-1, а также переносной 77МД-ЗМ и полупроводниковый ППД. Методом магнитной дефектоскопии можно контролировать лишь детали из ферромагнитных материалов (сталь, чугун). Для деталей из цветных металлов применяют другие методы.
Люминесцентный метод основан на использовании способности некоторых веществ поглощать лучистую энергию и отдавать ее в виде светового излучения в течение некоторого времени при возбуждении вещества невидимыми ультрафиолетовыми лучами (рис. 140).

Рис. 140. Схема люминесцентного дефектоскопа: 1 – рефлектор; 2 – ультразвуковой светофильтр; 3 – ртутно—кварцевая лампа; 4 – высоковольтный трансформатор; 5 – силовой трансформатор; 6 – контролируемая деталь.
Носители свечения – люминофоры. Источниками ультрафиолетового излучения служат ртутно-кварцевые лампы со специальным светофильтром Для контроля на поверхность крупных деталей наносят кистью флуоресцирующую жидкость (мелкие детали погружаются в ванну с этой жидкостью), подогретую до температуры 80 °C. Через 10–15 мин флуоресцирующая жидкость проникает в трещины, поры, раковины. После этого детали протирают, на контролируемые поверхности наносят тонкий слой порошка углекислого магния, талька или силикагеля и освещают их ртутно-кварцевой лампой. Порошок вытягивает из трещин и пор жидкость, которая в лучах ртутно-кварцевой лампы проявляет дефектные участки детали в виде светящихся линий и пятен. Глубину залегания трещин или пор ориентировочно определяют по ширине флуоресцирующей полосы, которая примерно в 10 раз больше глубины.
Ультразвуковой метод контроля основан на способности ультразвуковых колебаний (УЗК) распространяться в металле на большие расстояния в виде направленных пучков и отражаться от дефектного участка детали вследствие резкого изменения плотности среды. В ремонтном производстве применяются два способа ультразвуковой дефектоскопии: звуковой тени и отражения. Способ звуковой тени заключается в том, что дефект обнаруживают вводом импульса излучений УЗК в деталь, помещенную между излучателем 2 (рис. 141) и приемником 5 ультразвукового дефектоскопа.

Рис. 141. Схема действия ультразвукового дефектоскопа (теневой способ): а – дефекта в детали не обнаружено; б – дефект обнаружен; 1 – генератор; 2 – пьезоэлектрическая пластина (излучатель); 3 – деталь; 4 – ультразвуковые волны; 5 – приемник; 6 – дефект; 7 – прибор.
Если дефект не обнаружен, то колебания в виде ультразвуковых волн передаются детали, а от нее на пьезоэлектрическую пластину-приемник 5 и далее на регистрирующий прибор 7 (рис. 141, а). В случае наличия дефекта ультразвуковые волны 4 отражаются, т. е. не попадают на пластину 5, благодаря чему за дефектным участком детали образуется звуковая тень, на приемнике 5 не возникает пьезоэлектрических зарядов, и на приборе 7 нет показаний (рис. 141, б).
Способ отражения состоит в том, что импульсный генератор 6 (рис. 142) возбуждает излучающую пластину 3 (щуп с пьезоэлементом).

Рис. 142. Схема дефектоскопа, работающего на принципе отражения ультразвуковых волн: 1 – контролируемая деталь; 2 – приемная пластина; 3 – излучающая пластина; 4 – усилитель; 5 – электроннолучевая трубка; 6 – генератор; 7 – генератор развертки; 8 – дефект. А – начальный импульс; в – импульс, отраженный от дефекта; С – донный сигнал.
При акустическом контакте щупа с контролируемым изделием 1 излучатель посылает в металл короткие импульсы колебаний длительностью (0,5–10)10-6 с. Достигнув дна изделия, ультразвуковые колебания отражаются от него и возвращаются к приемной пластине (2), в которой возникает слабый электрический ток. Полученные сигналы усиливаются ламповым усилителем (4) и подаются в электроннолучевую трубку (5). При пуске генератора импульсов (6) одновременно (при помощи генератора развертки (7)) включается горизонтальная развертка электроннолучевой трубки, представляющей собой ось времени. С запуском генератора на экране трубки появляется начальный импульс в виде вертикального пика, после чего следует пауза (генератор выключается до следующего импульса). Если в детали есть дефект, то на экране на расстоянии l1 от первого посланного импульса появится второй, отраженный от дефекта, а в конце развертки на расстоянии l2 – импульс донного сигнала. Характер и величина всплесков на экране электроннолучевой трубки (5) расшифровываются по эталонным схемам импульсов, и таким образом определяются дефекты в деталях. Расстояние l1 соответствует глубине залегания дефектного участка детали, а расстояние l2 – толщине изделия. Измеряя время от момента посылки импульса до момента приема эхо-сигнала, можно определить расстояние до препятствия. Рассмотренный способ позволяет обнаружить и определить положение пор, раковин, шлаковых включений, зоны крупнозернистости металла и т. п. Для ремонтных целей используют усовершенствованный ультразвуковой дефектоскоп УЗД-7Н, выполненный по импульсной схеме и позволяющий вести контроль изделий по способу отраженных сигналов, а также по способу сквозного «прозвучивания» (звуковой тени). Максимальная глубина прозвучивания для стали составляет 2600 мм при плоских щупах и 1300 мм – при призматических. Промышленность выпускает серию ультразвуковых дефектоскопов: ДУК-5В, ДУК-6В, УЗД-НИИМ-5, УЗД-ЮМ, УЗДЛ-51М и другие – с высокой чувствительностью, которые можно применять в ремонтном производстве.
Правообладателям!
Это произведение, предположительно, находится в статусе 'public domain'. Если это не так и размещение материала нарушает чьи-либо права, то сообщите нам об этом.