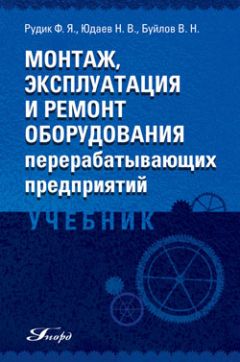
Автор книги: Феликс Рудик
Жанр: Техническая литература, Наука и Образование
сообщить о неприемлемом содержимом
Текущая страница: 16 (всего у книги 20 страниц)
16.3. Комплектация деталей
Комплектацией называют работы по контролю и подбору деталей, облегчающие подгонку сопряжений и быстрое выполнение сборочных операций в соответствии с техническими условиями на сборку. Необходимость контроля и подбора вызвана тем, что на ремонтных предприятиях используют как новые, так и детали с ремонтными и допустимыми размерами.
В комплектовочном отделении выполняются следующие работы: подбор комплекта деталей по номенклатуре согласно спецификации для каждого сборочного рабочего поста; контроль и подбор деталей по ремонтным размерам; контроль и подбор деталей по размерным группам; подбор деталей по массе; зачистка заусенцев и слесарная подгонка соединений; подбор и обкатка комплектов шестерен; общая проверка качества деталей, поступающих в комплектовочное отделение; учет движения деталей через комплектовочное отделение.
16.4. Сборка
Под сборкой понимается соединение деталей в пары и узлы, узлов и деталей в агрегаты, агрегатов, узлов и деталей в машину с соблюдением их кинематических схем, характеров посадок и величин размерных цепей, заданных техническими условиями и сборочными чертежами. Сборка – наиболее ответственная и продолжительная стадия ремонта машин. Особенность сборки машин из отремонтированных деталей характерна неоднородностью сборочных элементов, участвующих в этом процессе. Машину собирают из трех групп деталей: изношенных, но годных к дальнейшей эксплуатации, отремонтированных и новых. Это вызывает потребность в проведении подгоночных операций.
Трудоемкость сборки резьбовых соединений занимает 25–30 % в общем объеме сборочных работ. Резьбовые соединения можно собирать с предварительной затяжкой и без нее. Величина предварительной затяжки и ее стабильность зависят от: состояния опорных поверхностей деталей; состояния и точности изготовления резьбы; жесткости скрепляемых деталей; наличия перекосов и смазки на сопрягаемых поверхностях. Во избежание перекосов и коробления деталей необходимо следить за перпендикулярностью оси резьбы к поверхности детали и торцу гайки или головки болта. Затяжку рекомендуется выполнять в два-три приема, в определенной последовательности, т. е. сначала все гайки (головки болтов) завернуть до упора, затем отвернуть на 1/2 оборота и полностью затянуть. При скреплении круглых деталей гайки или болты затягивают крест-накрест. Для нормальной работы многоболтового соединения важно добиться одинаковой затяжки болтов. Усилия затяжки ответственных резьбовых соединений приводятся в технических условиях на сборку машин и контролируются динамометрическими ключами.
В конструкциях машин опоры с подшипниками скольжения конструктивно оформляются в виде втулок или разъемных вкладышей. Втулки чаще всего запрессовывают в гнезде блоков и корпусов с натягом, реже их устанавливают с подвижной посадкой и при этом стопорят. При ремонте машин подшипники запрессовывают при помощи приспособлений безударного действия (пресс или винтовое приспособление). Усилие следует прилагать равномерно по всей окружности запрессовываемой детали, для чего применяются специальные оправки. Особое внимание при сборке подшипников скольжения нужно уделять проверке соосности опор. Перед посадкой подшипника на вал и установкой этой пары в корпус проверяют посадочные места (определяют размеры, геометрическую форму, состояние поверхности и т. д.). Подшипники качения обязательно промывают в чистом бензине или керосине; после просушки беговые дорожки и шарики (ролики) покрывают маслом. При монтаже подшипников качения не допускается передача усилия через шарики и ролики. Подшипники на вал следует напрессовывать при помощи специальных оправок. Для ускорения сборки шариковые и роликовые подшипники больших размеров, монтируемые со значительным натягом, предварительно нагревают в масле до 80-100 °C и в горячем состоянии свободно насаживают на вал. Перед запрессовкой наружного кольца подшипника нагревают корпус. Практика показывает, что более 50 % повреждений подшипников качения в процессе работы есть следствие неправильного их монтажа. Правильно посаженный подшипник должен легко и плавно вращаться от руки.
При установке валов добиваются: равномерного прилегания их трущихся поверхностей к подшипникам; правильного положения в вертикальной и горизонтальной плоскостях; строгой соосности всех валов последовательно соединяемых агрегатов и узлов; необходимой легкости и плавности их вращения. Перед укладкой валов в подшипники проверяют правильность их подбора по размерам и осевым зазорам. Валы, уложенные в подшипники, проверяют на равномерность их прилегания к подшипникам.
16.5. Обкатка
Обкатка машин, агрегатов, узлов – это специальная технологическая операция, задачей которой является то, чтобы при определенных, специально установленных, минимальных во времени режимах подготовить машину, агрегат к восприятию эксплуатационных нагрузок, устранить мелкие неисправности, удалить продукты износа, интенсивно выделяющиеся во время приработки трущихся пар с целью последующей надежной работы машины. Особенность обкатки состоит в том, что она связывает ремонт и эксплуатацию, являясь завершающей ремонтной операцией и начальной операцией использования изделия. В процессе приработки сопряжений происходит изменения величины и направления микропрофиля, а также уменьшаются макрогеометрические отклонения формы. При этом увеличиваются зазоры, ослабляются натяги, изменяются микротвердость и структура поверхностного слоя. При назначении режимов обкатки агрегатов необходимо постепенное наращивание скоростей и удельных нагрузок на детали прирабатываемых сопряжений. Приработка на одном нагрузочно-скоростном режиме не подготавливает сопряжение к восприятию эксплуатационных нагрузок и скоростей. Для ускорения приработки и повышения качества прирабатываемых поверхностей в обкаточные жидкости вводят специальные присадки. Обкатку машин, узлов, агрегатов проводят на специализированных стендах, создающих условия и режимы обкатки, оговоренные в технической документации. По окончании обкатки проводят контрольный осмотр агрегата, машины и устраняют неисправности.
Глава 17
Методы восстановления посадок
Существует ряд методов восстановления посадок при ремонте машин. К ним относятся:
Восстановление посадок регулировкой. В конструкциях некоторых соединений возможна регулировка посадок, например регулировка зазоров у конических роликовых подшипников за счет изменения толщины комплекта шайб.
Восстановление посадок, перестановка деталей в другое положение. Для осуществления этого метода необходимо, чтобы у деталей были симметрично расположены одинаковые рабочие поверхности. При этом одна рабочая поверхность нагружается (изнашивается), а другая не испытывает нагрузок (не изнашивается). Метод применим при ремонте дробильных барабанов, путем перестановки молотков 3 и втулочно-роликовых цепей. Оси и втулки в пластинах поворачивают на 180° относительно их прежнего положения (рис. 143).
Восстановление посадок методом ремонтных размеров осуществляется из деталей с неноминальными размерами сопрягаемых поверхностей, но при этом обеспечивающих необходимый зазор. Эти размеры могут быть либо свободными, либо стандартными. В первом случае для достижения номинального зазора в сопряжении одну из деталей подвергают механической обработке до удаления следов износа и изготовляют дорогую сопрягаемую деталь под этот размер. Во втором случае для достижения номинального зазора в сопряжении механическую обработку проводят до получения необходимой посадки с заранее изготовленной (стандартной) деталью.
Методика расчета ремонтных размеров на примере соединения вал – подшипник. Примем общий случай: восстанавливаемая деталь – вал, который изнашивается неравномерно (рис. 144).

Рис. 143. Дробильный барабан: 1 – распорная втулка; 2 – палец; 3 – молоток; 4 – диск барабана; 5 – дека; 6 – диск вентилятора; 7 – лопасть вентилятора; 8 – кожух вентилятора; 9 – вал барабана.

Рис. 144. Схема для расчета ремонтных размеров: i0 – износ отверстия; Sнач и Smax – начальный и максимальный зазоры в соединении; iв и fв – равномерный и односторонний износы вала; dвα и dвβ – диаметры вала с сохранением первоначального положения геометрической оси; dвн и Dон – номинальные диаметры вала и отверстия; dв. наиб – наибольший диаметр вала, обусловленный его равномерным износом; dв. наим – наименьший диаметр вала, обусловленный равномерным и односторонним износами; Dо. пред – предельный диаметр отверстия; εв – допустимое смещение первоначального положения геометрической оси вала.
Подшипник – это тонкостенный разъемный вкладыш, заменяемый при ремонте на вкладыш ремонтного размера. Межремонтный интервал w в двух случаях определяют следующим образом: рабочий процесс машины не допускает смещения первоначального положения геометрической оси вала:

Формула № 183.
где iв – равномерный износ вала, мм;
fв – односторонний износ вала, мм;
Δв – припуск на обработку на диаметр вала, мм;
рабочий процесс машины допускает (в определенном пределе εв) смещение первоначального положения геометрической оси вала:

Формула № 184.
Очевидно, что ряд ремонтных размеров определяют так:

Формула № 185.
где dвн – номинальный диаметр вала, мм.
Число ремонтных размеров:

Формула № 186.
где dв. min – минимальный допустимый диаметр вала, мм.
Если при восстановлении посадки методом ремонтных размеров оставляемой деталью служит не вал, а охватывающая деталь, то ряд ремонтных размеров представляют так:

Формула № 187.
где Dо. н – номинальный диаметр отверстия, мм;
wa = iо + fо + Δо – межремонтный интервал для отверстия в случае, если рабочий процесс машины не допускает смещения первоначального положения геометрической оси отверстия, мм (здесь iо – равномерный износ отверстия, мм; fo – односторонний износ отверстия, мм, Δо – припуск на обработку на диаметр отверстия, мм); Wβ = iо + Δо – межремонтный интервал для отверстия в случае, если рабочий процесс машины допускает (в определенном пределе εо) смещение первоначального положения геометрической оси отверстия, мм.
Необходимо иметь в виду, что при положительном значении (0,5 fв – εв) этот результат добавляется при определении wβ (см. рис. 144), поскольку половина одностороннего износа превышает допустимое смещение первоначального положения геометрической оси вала. Это замечание справедливо и при определении wβ, если разность (0,5 fо – εо) также окажется положительной.
Число ремонтных размеров:

Формула № 188.
где Dо. max – максимальный допустимый диаметр отверстая (охватывающей детали), мм.
Метод восстановления посадки сопряжения постановкой дополнительных деталей осуществляют запрессовкой втулок, установкой шайб, колец, накладок и спиральных вставок (рис. 145).

Рис. 145. Ремонт резьбы установкой спиральной вставки: а – установка спиральной вставки в резьбовое отверстие: 1 – спиральная вставка; 2 – шпилька; 3 – корпус; б – сечение проволоки спиральной вставки (увеличено).
17.1. Ручная газовая сварка и наплавка
При газовой сварке применяют ацетиленовые генераторы или баллоны, кислородные баллоны, газовые редукторы, горелки, резаки, шланги, а также защитные очки со специальными светофильтрами. Ацетиленовые генераторы служат для получения ацетилена из карбида кальция. На верхней сферической части баллонов выбивают паспортные данные, включающие дату последних испытаний. Газовые редукторы используют для понижения давления отбираемого из баллона газа и поддержания этого давления постоянным. Для газовой сварки и наплавки выпускают различные горелки.
При сварке стальных изделий используют присадочную проволоку Св-08, Св-08А, Св-12ГС, Св-08ГС и Св-08Г2С в виде прутков длиной до 0,8 м. При сварке стальных деталей пропан-бутано-кислородным пламенем применяют проволоку марок Св-12ГС или Св-08Г2С с повышенным содержанием углерода и раскисляющих элементов (марганца и кремния). Для сварки чугунных деталей пользуются чугунными прутками диаметром 8, 10, 12, 14 и 16 мм. Для пайки чугуна применяют латунь ЛОК-59-1-03, содержащую до 0,4 % кремния. Для ответственных соединений следует пользоваться припоем ЛОМНА-54-1-10-4-02, содержащим медь, олово, марганец, никель и до 0,6 % алюминия. При пайке применяют поверхностно-активный флюс ФПСН-2, состоящий из 50 % борной кислоты, 25 % углекислого лития, 25 % углекислого натрия и небольшого количества фтористых соединений. Флюс плавится при температуре 650 °C и служит индикатором начала процесса.
Для устойчивого протекания процесса горения газового пламени необходимо обеспечить определенный состав смеси горючих газов с кислородом. Изменяя соотношение горючего газа или паров жидкого топлива и кислорода, получают различные виды сварочного пламени (рис. 146).

Рис. 146. Виды сварочного пламени: а – науглероживающее; б – нормальное (восстановительное); в – окислительное; А – зона максимальной температуры.
Процесс газовой сварки характеризуется малым объемом ванны расплавленного металла, высокой температурой и концентрацией тепла в месте сварки, большой скоростью расплавления и остывания металла, интенсивным перемешиванием металла жидкой ванны газовым потоком пламени и присадочным прутком. При сварке газами – заменителями ацетилена пламя имеет удлиненное ядро. Ядро пламени горелки независимо от его длины нужно держать от расплавленной поверхности сварочной ванны на расстоянии 5–8 мм. Такому расстоянию соответствуют нейтральная зона пламени и наивысшая температура пламени. Газовую сварку можно выполнять левым и правым способами (рис. 147).
При левой сварке горелку перемещают за присадочным прутком. В это время факел пламени предварительно нагревает кромки шва. Этот способ применяют при сварке деталей толщиной до 3–5 мм. При правой сварке пруток перемещают за горелкой. Факел пламени, направленный в этом случае на заваренный шов, защищает его от резкого охлаждения. Скорость сварки при правом способе несколько выше, чем при левом. Правый способ применяют при сварке крупногабаритных деталей. В обоих случаях пламя горелки направляют на свариваемый металл так, чтобы кромка металла и конец присадочного прутка находились в восстановительной зоне пламени на расстоянии 2–6 мм от конца ядра. Касаться расплавленного металла концом ядра нельзя, чтобы избежать науглероживания металла ванны.

Рис. 147. Способы сварки: а – левый; б – правый.
В начальный период сварки для быстрого образования сварочной ванны угол наклона мундштука горелки принимают равным 80–90° к продольной оси пламени. По мере образования сварочной ванны угол изменяют до 45–20°. Присадочный пруток также располагают под углом 45–20° к продольной оси пламени в плоскости направления сварки. Для предотвращения образования газовых пор формируют сварной шов тонким слоем, не допуская увеличения объема сварочной ванны. Сварку нужно вести непрерывно, без отрыва пламени от ванны, а присадочный металл накладывать последовательно тонкими слоями до полного заполнения сварного шва. Основным является перемещение мундштука вдоль шва, а поперечные и круговые движения являются вспомогательными.
Для улучшения механических свойств сварные швы проковывают легкими ударами молотка в горячем или холодном состоянии.
В зависимости от формы детали, ее габаритов и вида исправляемого дефекта применяют горячую и низкотемпературную сварку чугуном и низкотемпературную пайку латунью или цинковым сплавом. При горячей сварке перед началом ее целиком нагревают деталь, ослабляя напряженное состояние, что предотвращает образование трещин. Целесообразно сварку вести в специальных теплозащитных термосах. Крупные детали, у которых место сварки расположено среди жестких элементов (блоки, головки цилиндров, корпуса коробок передач), нагревают до 620–650 °C. Заканчивать сварку таких деталей следует при охлаждении до температуры не ниже 400 °C. Перерывы при выполнении сварки чугунных деталей не допускаются.
Для отбеливания чугуна по окончании формирования шва ванну дополнительно прогревают пламенем в течение 1–2 мин. Расстояние между сварочной ванной и ядром пламени должно быть в пределах 5–10 мм. Для уменьшения выгорания углерода и кремния поддерживают нормальное пламя с небольшим избытком горючего газа и ведут сварку без интенсивного перемешивания жидкого металла пламенем или присадочным прутком. При низкотемпературной сварке чугуна основной металл не нагревают до температуры плавления, а пламенем горелки нагревают только место сварки до 820–860 °C. При этом капли присадочного металла под действием пламени и флюса растекаются по поверхности, а сварное соединение получается в результате диффузии молекул металла. Низкотемпературную сварку чугуна ведут левым способом нормальным (восстановительным) пламенем без предварительного подогрева или с общим подогревом детали до 200–350 °C. После нагрева зоны сварки до 770–800 °C на поверхность завариваемого участка равномерно наносят флюс. Между ядром пламени и концом прутка необходимо сохранять расстояние 3–5 мм, а угол между его осью и плоскостью детали в пределах около 20–25°. Во время сварки концом прутка при образовании капли необходимо касаться завариваемой поверхности. В процессе сварки присадочный пруток периодически обрабатывают флюсом. Перед сваркой поверхности зачищают до металлического блеска. Шов наплавляют тонкими периодическими слоями толщиной 2–3 мм. При низкотемпературной пайке чугуна латунью поверхности со снятой фаской (70–80°) нагревают до 900–930 °C и, отрегулировав пламя с избытком кислорода, нагревают конец присадочного прутка и отдельными участками натирают им горячие кромки деталей, периодически обрабатывая их флюсом. Пайку чугуна цинковым сплавом применяют для устранения небольших трещин, выбоин на деталях, у которых в местах пайки не требуется особой прочности. Пайку ведут при 300–350 °C. Перед пайкой поверхности деталей тщательно зачищают. Цинковый сплав при пайке быстро выгорает, поэтому важно не допускать перегрева основного и присадочного металлов. Температуру нагрева детали проверяют термокарандашами.
Поверхность алюминия и его сплавов всегда покрыта тонкой (до 0,002 мм) пленкой тугоплавких оксидов. Эта пленка препятствует его свариваемости. Оксидную пленку при сварке разрушают, удаляя химическим воздействием флюса или механическим путем. Во время сварки алюминий плавится очень быстро, и его сварку нужно вести горелкой минимальной мощности нормальным пламенем с небольшим избытком ацетилена, периодически добавляя к месту сварки присадочный металл того же состава. Литые детали из алюминиевого сплава перед сваркой подогревают до 150–200 °C, а после окончания сварки повторно нагревают до 300–350 °C для улучшения структуры сварного шва и снятия внутренних напряжений.
17.2. Ручная электродуговая сварка и наплавка
Возбуждение дугового разряда возможно четырьмя основными способами:
• при переходе из устойчивого маломощного разряда, например тлеющего;
• в процессе создания высокоионизированного потока пара, перекрывающего межэлектродное пространство, в большинстве случаев с помощью третьего электрода;
• при переходе из неустойчивого искрового разряда путем подачи импульса высокой частоты или высокого напряжения; при замыкании и последующем размыкании токонесущих электродов.
При сварке плавящимся электродом обычно используют дугу размыкания, а при сварке неплавящимся вольфрамовым электродом – высокочастотный вспомогательный разряд от осциллятора. Импульс высокого напряжения получают обычно с помощью конденсатора. Угольную дугу возбуждают чаще всего, используя третий электрод.
В самостоятельном разряде, начиная с токов выше нескольких микроампер, наблюдается неравномерное распределение электрического поля в межэлектродном пространстве, состоящем из трех зон (рис. 148): катодной 1, анодной 2 и столба разряда 3. На электродах часто наблюдаются пятна – анодное А и катодное К. Скачки потенциала Uк и Uа обусловлены скоплениями пространственного заряда (рис. 149) и повышенным сопротивлением этих зон по сравнению со столбом.
В длинной дуге можно отчетливо различить три указанные выше области, причем основные свойства столба мало зависят от процессов в катодной и анодной зонах. В связи с этим в дальнейшем отдельно рассмотрены явления в столбе дуги и в пограничных областях – катодной и анодной. Для коротких дуг, где влияние процессов, происходящих у одного электрода, простирается до второго электрода, подразделение дуги на отдельные части, очевидно, становится бесполезным. В газовом промежутке между двумя электродами заряженные частицы могут возникнуть во всех трех зонах, но главным образом они появляются в результате процессов эмиссии на катоде и объемной ионизации в столбе дуги. В связи с ограниченностью эмиссии электронов столб дуги (как и любой проводник) вдали от катода сохраняет по отношению к нему положительный потенциал, поэтому часто его называют положительным столбом. В то же время не следует забывать, что плазма столба обычно квазинейтральна.

Рис. 148. Зоны дугового разряда.

Рис. 149. Схема переноса зарядов в дуге: Uд, Uк, Uа и Uст – напряжение дуги, катодное, анодное и столба дуги.
Источниками питания для сварки на переменном токе являются сварочные трансформаторы. Источники питания постоянного тока делят на сварочные генераторы и сварочные выпрямители. Сварочные выпрямители применяют при ручной электродуговой сварке, резке и наплавке, при сварке в среде защитных газов. Основные преимущества выпрямителей – небольшая масса и их простота. Выпрямители собирают из полупроводниковых элементов, которые обладают свойствами проводимости тока только в одном направлении.
Для электродуговой сварки применяют плавящиеся и неплавящиеся электроды. Первую группу составляют электроды со стальным стержнем или со стержнем из других металлов (чугуна, алюминия и различных сплавов) и покрытием; вторую – угольные, графитовые и вольфрамовые электроды без покрытий. Покрытия электродов первой группы служат для повышения устойчивости горения дуги и улучшения качества сварных швов и наплавляемого металла.
Если при сварке постоянным током деталь подключена к положительному полюсу, а электрод – к отрицательному, считают, что сварка ведется на прямой полярности. Если же деталь подключена к отрицательному, а электрод – к положительному полюсу, сварка проводится на обратной полярности. При сварке на обратной полярности уменьшается нагрев детали, что важно при сварке металлических листов толщиной до 3 мм и при холодной сварке чугуна. Сварное соединение при электродуговой сварке металлическим электродом получается в результате расплавления основного металла и металла электрода.
Сварочный ток выбирают в зависимости от типа и диаметра электрода, исходя из допустимой плотности тока, которая может колебаться для различных электродов в пределах от 10 до 20 А/мм2. Увеличение тока ограничивается нагревом стержня электрода. Для наиболее употребляемых электродов диаметром 2, 3, 4 и 5 мм можно пользоваться эмпирической формулой:

Формула № 189.
где m – коэффициент, зависящий от типа электрода и его диаметра (для электродов с меловой обмазкой m = 30–50, а для качественных – m = 35–60); d – диаметр электрода, мм.
При ремонте чугунных деталей применяют два вида сварки – холодную и горячую. Для холодной сварки чугуна применяют электроды: стальные (Э-34), железомедные (ОЗЧ-1), из медно-никелевых (МНЧ-1, монель-металл), железоникелевых (ЦЧ-ЗА) или хромо-никелевых (АНЧ-1) сплавов, из порошковой проволоки (ППЧ-1, ППЧ-2), стальной проволоки Св-08ГС и Св-08Г2С в среде углекислого газа, а также стальные со специальным покрытием (ЦЧ-4, ЦЧ-4А) и чугунные типа Б со специальным покрытием. Горячую сварку чугуна осуществляют чугунными электродами типа А с бурой или флюсами и угольными электродами с чугунной присадкой. Полугорячую или низкотемпературную сварку чугуна выполняют электродами типа ООМ-5, УОНИ 13/55 и др. Холодная сварка методом отжигающих валиков (рис. 151) стальными электродами состоит в том, что на очищенную от масла, грязи, коррозии поверхность чугунной детали наплавляют сварной шов длиной от 30 до 70 мм (длину шва выбирают в зависимости от толщины стенки детали) и после удаления с него шлака и брызг металла сразу же наплавляют второй сварной шов так, чтобы он не касался чугуна детали. Допускается наплавка второго шва с перекрытием на 60–70 % первого, но с последующей наплавкой третьего шва, который перекрывал бы ранее наплавленные швы и не соприкасался с основным металлом детали. Третий сварной шов служит для отжига первых наплавленных швов. Для получения сварного соединения повышенной прочности дополнительно устанавливают упрочняющие штифты, резьбовые шпильки или скобы. Штифты, шпильки или скобы обваривают в определенной последовательности, затем заваривают трещину с наложением одного или двух отжигающих валиков (швов). По такой же технологии заваривают трещины и другие дефекты в чугунных деталях проволокой диаметром 0,8–1,2 мм марок Св-08ГС и Св-08Г2С в среде углекислого газа полуавтоматами А547-Р и А825, которые позволяют увеличить производительность сварки в 3–5 раз.
При заварке трещин в чугунных деталях железомедными электродами ОЗЧ-1 и электродами ЦЧ-ЗА и АНЧ-1 предварительно концы трещины засверливают, а с ее кромок снимают фаски. Трещину заваривают в порядке, указанном на рис. 150, участками длиной 40–60 мм (для электрода ОЗЧ-1) или 30–50 мм (для электродов ЦЧ-ЗА и АНЧ-1) на постоянном токе обратной полярности. При этом нельзя допускать перегрева детали в месте сварки более чем на 50–60 °C. Каждый сварной валик сразу после обрыва дуги проковывают легкими ударами молотка для снятия напряжений и уплотнения сварного шва.

Рис. 150. Последовательность наложения сварных швов при заварке трещины без предварительной разделки ее в тонкой стенке детали: I, II, III и IV – участки сварки; 1-10 (на плане) – последовательность наложения сварных швов; 1, 3, 4, 6 и 7 – подготовительные валики; 2, 5 и 8 – отжигающие валики (на сечениях).
В случае обнаружения мест непровара, шлаковых включений и других дефектов эти места вырубают, а затем вновь заваривают не менее чем в два слоя участками длиной 30–50 мм. Сварное соединение, выполненное электродами ОЗЧ-1, обрабатывают инструментом из твердого сплава, а сварное соединение, выполненное электродами ЦЧ-ЗА в АНЧ-1, – обычным режущим инструментом. Поверхность чугунной детали в зоне трещины в случае заварки ее электродами из монель-металла (МНЧ-1) подготавливают, что предотвращает отрыв наплавленного металла при его механической обработке, так как прочность сварного соединения, выполненная электродами МНЧ-1, составляет всего 40–60 МПа. Трещину заваривают на постоянном токе обратной полярности участками длиной 15–20 мм. Возобновлять сварку следует после охлаждения шва до 50–60 °C. Каждый сварной шов сразу после обрыва дуги проковывают легкими ударами молотка. Сварное соединение, выполненное электродами МНЧ-1, обрабатывают обычным режущим инструментом. Детали из ковкого чугуна с черной сердцевиной (ввиду наличия в нем свободного углерода) заваривают с предварительным нагревом при газовой сварке или холодной электродуговой сваркой с применением электродов, используемых при сварке серого чугуна.

Рис. 151. Сварка в среде аргона: 1 – свариваемая деталь; 2 – наплавляемый металл; 3 – присадочный пруток; 4 – вольфрамовый электрод; 5 – горелка.
Электродуговую сварку алюминиевых сплавов выполняют вручную вольфрамовыми электродами в среде аргона или гелия (рис. 151). Угольными электродами детали сваривают на прямой полярности (минус на электроде), тонколистовые изделия – по отбортовке без присадочного материала. Стыковые, угловые и тавровые соединения сваривают присадочными прутками из алюминия или его сплавов. Для сварки литых сплавов типа силумин применяют присадочную проволоку марки Св-АК5. Сварку литых изделий электродами ОЗА-2 проводят на обратной полярности с предварительным подогревом места сварки до 200–300 °C. После сварки (независимо от метода и марки электродов), сварные швы очищают металлической щеткой и промывают горячей водой. Режимы сварки приведены в табл. 56.
Диаметр электрода выбирают в зависимости от толщины свариваемого металла, размеров детали, положения шва в пространстве и типа сварочного соединения. При сварке изделий толщиной до 4 мм диаметр электрода принимают равным толщине свариваемых частей. В остальных случаях применяют электроды диаметром 4–8 мм. В многослойных швах первый слой выполняют электродом диаметром 3–4 мм, а последующие – большим диаметром. Сварку в вертикальном положении выполняют электродами диаметром не более 5 мм при уменьшении величины сварочного тока на 10–15 % по сравнению с нормально выбранной величиной тока для сварки в нижнем положении. При потолочной сварке используют электрод диаметром не более 4 мм и уменьшают величину сварочного тока на 20–25 %. Для швов внахлестку величина тока должна быть на 10–15 %, а для тавровых швов на 15–20 % больше номинальных значений.
Таблица 56. Режимы ручной электродуговой сварки деталей из алюминиевых сплавов

Высокое качество ремонта деталей из тонколистовой стали обеспечивается сваркой в среде углекислого газа с применением проволоки Св-08ГС или Св-08Г2С. Для предупреждения коробления и прожогов шов наваривают участками, подкладывая с обратной стороны в направлении перемещения электрода медные пластины для интенсификации теплоотвода. Для обеспечения прочности сварных швов применяются стальные накладные пластины. Их обычно приваривают внахлест пунктирно. Длинномерные накладные пластины следует слегка выгибать, так как в процессе приваривания они выправляются и не удерживают свариваемые детали от деформации. Характерными дефектами деталей из среднеуглеродистых сталей марок 30, 35, 40, 45, 50, 50Г, 45Х, 40Х являются износ рабочей поверхности шеек валов, шлицев, шпоночных канавок, а также срыв резьбы. Во избежание образования трещин, крупногабаритные и толстостенные детали перед наплавкой необходимо подогревать до температуры 200–250 °C.
После сварки деталь вновь нагревают до 670–700 °C и медленно охлаждают вместе с печью до 100–150 °C. Затем деталь охлаждают на воздухе.
Характерными дефектами корпусных и рамных конструкций являются трещины и повреждения крепежных резьбовых отверстий. Подготовка трещин к заварке заключается в разделке краев под углом 70–90°. Сварку ведут от середины трещины к концам, чередуя при этом направление. После заварки трещины и ее обработки (механической) приваривают дополнительные усиливающие накладки, соответствующие конфигурации детали. Накладку сначала приваривают прихватками в нескольких местах, а затем обваривают по контуру.
Правообладателям!
Это произведение, предположительно, находится в статусе 'public domain'. Если это не так и размещение материала нарушает чьи-либо права, то сообщите нам об этом.