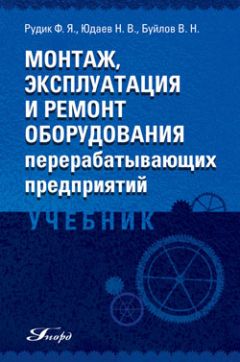
Автор книги: Феликс Рудик
Жанр: Техническая литература, Наука и Образование
сообщить о неприемлемом содержимом
Текущая страница: 17 (всего у книги 20 страниц)
Форму и размеры детали можно восстанавливать приваркой полувтулок, если установка втулки технологически невозможна. Полувтулки устанавливают при помощи струбцин, а затем приваривают к детали и сваривают между собой сплошными швами.
Изношенные поверхности корпусных деталей наплавляют в один слой или в несколько слоев до толщины наплавленного металла 3–6 мм. Посадочные поверхности осей, валов и цапф наплавляют продольными или круговыми валиками. Продольную наплавку применяют для длинномерных валов диаметром до 30 мм и при одностороннем износе рабочих поверхностей деталей (цапфы, шлицы и т. п.). Наплавку торцовой поверхности детали наплавку начинают от ее центра и ведут концентричными окружностями.
17.3. Автоматическая наплавка под слоем флюса
Наибольшей производительностью обладают специализированные наплавочные станки У-651 (для наплавки валов диаметром до 150 мм и шлицев), У-652 (для наплавки коленчатых валов) и У-653 (универсальный, для наплавки цилиндрических и плоских деталей). Для наплавки под слоем флюса используются в качестве источников питания сварочные трансформаторы ТСД-500-1, СТШ-500-ГО, ТСД-1000, ТСА-1000 и ТСД-2000-2, а также сварочные выпрямители ВДУ-505 и ВДУ-506.
При механизированной сварке и наплавке под слоем флюса применяют стальную холоднотянутую калиброванную проволоку диаметром от 0,3 до 12 мм и проволоку для наплавочных работ. При наплавочных работах применяют проволоку марок Нп-30, Нп-40, Нп-50, Нп-65 и Нп-80. Цифры показывают среднее содержание в проволоке углерода в сотых долях процента. Примерное содержание других элементов (%) показывает цифра, стоящая после буквенного обозначения этого элемента. Если цифра после обозначения элемента отсутствует, значит, в проволоке содержится около 1 % данного элемента. Эффективное средство увеличения производительности автоматической наплавки под слоем флюса – применение ленточного электрода. В качестве такого электрода можно использовать холоднокатаную ленту из конструкционной стали. Для наплавки обычно используют ленту толщиной 0,3–1,0 мм и шириной 10-100 мм.
В зависимости от способа изготовления флюсы разделяют па плавленые и неплавленые (керамические). Преимущественное распространение получили плавленые флюсы, которые изготовляют сплавлением исходных компонентов в пламенных или электрических печах и последующим дроблением полученной массы. Керамические флюсы изготовляют спеканием смеси из тонкоразмолотых порошков минералов и ферросплавов, для скрепления которых в зерна нужных размеров применяют обычно жидкое натриевое стекло. Наибольшее распространение получили плавленые флюсы АН-348А и ОСЦ-45. Эти флюсы представляют собой стекловидные зерна от светло-желтого до темно-бурого или коричневого оттенков. Флюс АН-348А выпускают в зернах размером от 3 до 0,35 мм или от 1,6 но 0,25 мм (мелкий флюс АН-348АМ). Мелкий флюс применяют для наплавки деталей небольшого диаметра сравнительно тонкой электродной проволокой. Отделимость шлаковой корки плавленых флюсов АН-348А и ОСЦ-45, при достижении деталью температуры порядка 250 °C, ухудшается, что затрудняет наплавку деталей небольшого диаметра. Окислительное действие низкокремнистых флюсов АН-20, АН-28, АН-30 и 48-ОФ-6 значительно меньше. Флюсы АН-28 и АН-30 сохраняют кроме того хорошую отделимость шлаковой корки до 600–650 °C. Недостатком флюса АН-28 является пористость шва при сварке и наплавке чугуна или стали, содержащих менее 1 % кремния. При наплавке легированных сталей целесообразно использовать низкокремнистые флюсы АН-20 и АН-30. Флюсы АН-22 и 48-ОФ-6 применяют для наплавки высоколегированных сталей. При наплавке проволокой, содержащей около 1 % кремния, хорошие результаты дает флюс АН-28. Для получения после наплавки высокой твердости рабочих поверхностей деталей применяется керамический флюс АНК-18. Его можно применять для наплавки шлицевых валов и других деталей.
Состав электродного металла в процессе наплавки изменяется. Часть элементов выгорает, другая часть переходит из флюса в металл.
Кроме того, наплавленный металл перемешивается с расплавленным металлом детали. Наплавленный металл с высоким содержанием легирующих элементов можно получить при наплавке проволокой Св-08 с соответствующим керамическим флюсом.
Применение непросушенных флюсов приводит к появлению значительной пористости наплавленного слоя. Поэтому флюс перед использованием необходимо просушить при 200–250 °C. В процессе работы флюс засоряется частицами шлаковой корки, поэтому периодически флюс просеивается через разные сита для удаления крупных частиц и для удаления пыли.
Электродуговая наплавка под слоем флюса – один из способов восстановления размеров крупных деталей со значительными износами (рис. 152). При автоматической сварке и наплавке под слоем флюса механизированы операции подачи проволоки, флюса и перемещения электрода относительно детали. Главной особенностью механизированного способа наплавки является то, что дуга горит под слоем флюса и снаружи ее не видно. Благодаря применению больших токов и высокому коэффициенту наплавки производительность автоматической наплавки в 4–6 раз выше ручной. При этом улучшаются условия труда. При автоматической наплавке потери электродного материала на разбрызгивание и угар не превышают 2–4 %, а при ручной достигают 25–30 %. Расход электроэнергии на наплавку 1 кг металла около 3 кВт·ч, а при ручном способе – 6–7 кВт·ч. Флюсовая защита и различные способы легирования позволяют в широких пределах регулировать состав и свойства наплавленного металла, обеспечивая его высокое качество.

Рис. 152. Схема процесса наплавки под слоем флюса: а – поперечный разрез; б – продольный разрез; 1 – деталь; 2 – электродная проволока; 3 – мундштук; 4 – бункер; 5 – гранулированный флюс; 6 – расплавленный флюс; 7 – ванна расплавленного металла; 8 – наплавленный слой;9 – шлаковая корка; 10 – электрическая дуга; е – смещение электродной проволоки с зенита.
Процесс наплавки цилиндрической детали под слоем флюса происходит по следующей схеме (рис. 152). Электродная проволока (2) подается по мундштуку (3), который подключен к одному полюсу источника сварочного тока, наплавляемая деталь (1) подключена к другому полюсу. Горящая между электродом и деталью электрическая дуга расплавляет часть флюса, поступающего в зону, при этом образуется эластичная оболочка, защищающая расплавленный металл от вредного воздействия компонентов воздуха. При вращении детали наплавляемый участок перемещается. Застывший флюс образует шлаковую корку (9), располагающуюся поверх наплавленного металла. Эта корка достаточно легко отделяется от металла и удаляется. Флюс, не подвергшийся расплавлению, ссыпается с детали, и после просеивания вновь подается в зону наплавки.
Наплавку деталей с применением керамических флюсов следует вести на постоянном токе обратной полярности (таблица 57).
Таблица 57. Режимы наплавки деталей под слоем флюса

При наплавке под слоем флюса дуга устойчива тогда, когда плотность тока не менее 25 А/мм2. Уменьшение плотности тока приводит к прерывистому горению дуги и некачественному формированию шва. Шаг наплавки следует выбирать так, чтобы каждый последующий валик перекрывал предыдущий на 30–50 % их ширины. При завышенном шаге наплавки поверхность получается волнистой и возрастает трудоемкость последующей механической обработки детали.
При наплавке ленточным электродом (рис. 153) получается плоский валик шириной примерно равной ширине ленточного электрода, при этом слой требуемой толщины получается за один-два прохода с малой глубиной проплавления основного металла и в связи с этим незначительным изменением состава наплавленного слоя (доля разбавления составляет 10–20 %).

Рис. 153. Схема процесса наплавки ленточным электродом под флюсом: 1– источник питания; 2 – ленточный электрод; 3 – ролики подачи электрода; 4 – мундштук (токоподвод);5 – флюс; 6 – шлак; 7 – наплавленный металл; 8 – основной металл; 9 – направление наплавки.
Производительность способа может быть повышена за счет увеличения ширины ленточного электрода. На практике используют ленточные электроды шириной до 180 мм, однако при наплавке постоянным током увеличение размеров наплавочной ванны сопровождается нарушением формы наплавляемого валика под действием магнитного дутья. Для решения этой проблемы разработан способ наплавки в магнитном поле.
Двухэлектродная наплавка осуществляется двумя электродными лентами с использованием головки, запитанной от одного источника. При этом достигается скорость почти в 2 раза больше, чем при наплавке одним электродом, а валик наплавленного металла получается без видимых дефектов правильной геометрической формы.
При автоматической наплавке под слоем флюса деталей диаметром 30–80 мм они сильно нагреваются, что приводит к стеканию жидкого металла и шлака, а отделение шлаковой корки затрудняется, и наплавка прекращается. Для облегчения удаления корки с деталей малого диаметра применяют двухзаходную наплавку. Шаг наплавки выбирают близким к ширине, образующейся на детали шлаковой корки (обычно 10–15 мм). После наплавки первой спирали дают детали остыть, удаляют шлаковую корку, и затем наплавляют вторую спираль с таким же шагом.
При восстановлении малогабаритных деталей можно применять флюсы АН-30 или АН-20, которые сохраняют хорошую отделимость шлаковой корки при температурах до 500–600 °C. При наплавке пустотелых деталей с малой толщиной стенки устанавливают минимальную величину тока и во избежание сквозного проплавления стенок детали применяют охлаждение внутренней полости детали водой. Твердость слоя при этом получается выше, чем у наплавленного в обычных условиях. Размеры изношенных шлицев на деталях восстанавливают путем полного заплавления впадины между шлицами или наплавкой только одной изношенной стороны шлица с соответствующей механической обработкой. Для мелких шлицев предпочтителен первый вариант. Процесс в этом случае ведут при величине тока 200–300 А. Для уменьшения деформации детали следует последовательно наплавлять шлицы, расположенные под углом 180°.
17.4. Сварка в среде углекислого газа
Рабочее место по сварке в среде углекислого газа оснащается баллоном (1) (рис. 154) с углекислым газом, подогревателем (2) и осушителем (3) газа, редуктором (4) и расходомером (5). При выходе из баллона газ расширяется, при этом температура его резко снижается.

Рис. 154. Схема питания углекислым газом поста для сварки: 1 – баллон с углекислым газом; 2 – подогреватель газа; 3 – осушитель газа; 4 – редуктор; 5 – расходомер; 6 – горелка; 7 – наплавляемая деталь.
Содержащаяся в углекислом газе влага может замерзнуть и закупорить каналы газоаппаратуры. Чтобы этого не случилось, сразу после выхода из баллона газ пропускают через подогреватель (2). После подогревателя (2) углекислый газ попадает в осушитель (3) – небольшой полый цилиндр, заполненный силикагелем, т. е. веществом, поглощающим влагу. Расход углекислого газа в процессе работы определяют при помощи расходомера. При использовании газа до 10 л/мин пригоден расходомер РС-3, а при большем расходе – расходомер РС-5. Расходомеры тарируют по расходу воздуха; поэтому значения, получаемые при оценке расхода углекислого газа, следует умножать на коэффициент 0,8.
Для сварки в среде углекислого газа применяют специальное оборудование: полуавтоматы А-547-Р, А-547-У, А-537, А-929, ПДПГ-500, А-825 и др. Сварку выполняют электродной проволокой диаметром 0,5–1,2 мм, скорость подачи которой можно регулировать в пределах 120–410 м/ч. Аппарат А-547-У (усиленный) позволяет сваривать проволокой диаметром 0,6–1,2 мм при токе до 300 А. Аппарат снабжен выпрямителем ВДГ-302 с отсекателем газа, установленным в подающем механизме. Конструкцией установки предусмотрены устранение выбега проволоки при окончании сварки, заварка кратера и обдув его углекислым газом. Горелка полуавтомата А-537 охлаждается проточной водой. Охлаждение необходимо при длительной работе, а также при сварке на больших токах, когда наконечники горелок быстро повреждаются и заплавляются брызгами жидкого металла. Хорошие результаты получаются при использовании керамических наконечников.
Полуавтомат ПДГ-302 рассчитан для работы с проволокой диаметром 0,8–2,0 мм, скорость подачи ее 90-960 м/ч. Максимальный сварочный ток для этого полуавтомата 300 А. Расход углекислого газа 600-1500 л/ч.
Источниками питания дуги могут служить выпрямители, например, ВС-200, ВСС-300, ВСК-300 и ВДГ-302. Углекислый газ поставляют в жидком виде в стандартных баллонах. В баллонах емкостью 40 л содержится 20–25 кг жидкого углекислого газа под давлением 5000–6000 кПа. Баллоны окрашены в черный цвет, надписи на баллонах сделаны желтой краской. Один баллон газа рассчитан на 12–15 ч работы. Для понижения давления углекислого газа до рабочего (250 кПа) употребляют газовые редукторы. Для получения углекислого газа при сварочных работах используют также сухой лед (твердая углекислота), выпускаемый в виде брикетов массой от 18 до 100 кг. Для перевозки и хранения сухого льда применяют изотермические контейнеры, а для перевода сухого льда в газообразное состояние – аппараты, называемые газоуглекаторами. Углекислый газ, получаемый из сухого льда, обладает высокой чистотой и дает хорошие результаты при сварке. Однако стоимость его выше, чем газа, получаемого из пищевой углекислоты. Для поглощения влаги в осушителе используют силикагель крупный, марки КСМ или КСХ. Силикагель может смерзаться вследствие насыщения влагой, поэтому необходимо примерно один раз в 10 дней прокаливать его при 150–200 °C в течение 1,5–2 ч.
Сварка в среде углекислого газа дает плотные и прочные швы только в случае применения электродной проволоки, содержащей раскислители (кремний и марганец). Наибольшее распространение при сварке в среде углекислого газа получили следующие марки электродной проволоки: Св-08ГС, Св-08Г2С, Св-12ГС, Св-10ХГ2С, Св-10ГСМТ, Св-18ХГСА диаметром 0,5–2,5 мм. Проволоку диаметром 0,5 мм применяют для сварки деталей из листа толщиной 0,7–1,0 мм, проволоку диаметром 0,8 мм – для сварки деталей из листа толщиной 1,0–1,5 мм, проволоку диаметром 1,0 мм – для сварки, деталей из листа толщиной до 2,5 мм, а проволоку диаметром 1,2 мм – для сварки деталей из листа толщиной, 2–4 мм. Допускается применение порошковых проволок ПП-АН4, ПП-АН5 и ПП-АН8. Для наплавочных работ используют проволоку марки Нп-30ХГСА, а также порошковые проволоки марок ПП-5ХВЗГ2СТ, ПП-Х12ВФТ, ПП-30Х10Г10Т и ПП-Р18Т.
Сварку в среде углекислого газа проводят на постоянном токе при обратной полярности. При выборе режима сварки устанавливают, прежде всего, величину сварочного тока в зависимости от особенностей и конфигурации свариваемой детали. Затем выбирают примерное значение диаметра электродной проволоки и рекомендуемый ее вылет из наконечника горелки в процессе сварки. Важнейшим условием стабильности процесса сварки является высокая плотность тока. При сварке проволокой диаметром до 2 мм плотность тока должна быть не менее 100 А/мм2, а при сварке проволокой диаметром свыше 2 мм – не менее 70 А/мм2. Скорость подачи электродной проволоки подбирают так, чтобы была достигнута стабильность горения дуги при значениях тока в пределах, установленных технологическим процессом. Сварку в среде углекислого газа необходимо выполнять короткой дугой (обычно от 1,5 до 4 мм). Деталь, а также электродную проволоку перед сваркой очищают от грязи, масла и ржавчины, чтобы предотвратить появление пор в шве. Повышенный расход углекислого газа вызывает завихрение в зоне горения дуги, способствующее попаданию в шов воздуха. При полуавтоматической сварке в среде углекислого газа деталей из листовой стали протяженность зоны термического влияния в 2–3 раза меньше, чем при сварке ацетиленокислородным пламенем.
Скорость наплавки определяется по следующей формуле:

Формула № 190.
где αн – коэффициент наплавки, г/(А·ч) (при наплавке постоянным током обратной полярности α = 10–12);
I – сила тока, А;
h – толщина наплавленного слоя, мм;
S – шаг наплавки, мм/об;
γ – плотность электродной проволоки, г/см3.

Формула № 191.
Скорость подачи проволоки:

Формула № 192.
где dпр – диаметр электродной проволоки, мм.
Смещение электрода:

Формула № 193.
В табл. 58 приведены режимы сварки листовой стали марки Ст. 3 для полуавтомата А-5 47.
Детали толщиной менее 1 мм рекомендуется сваривать на медной подкладке, обеспечивающей лучший тепловой режим. Листы перед сваркой соединяют прихватами через 60–70 мм. Зазор в стыке листов тонкого материала должен быть не более 0,2–0,3 мм, иначе возможны прожоги.
Таблица 58. Режимы сварки листовой стали

При сварке оцинкованной стали должен быть хороший местный отсос воздуха ввиду большой токсичности окислов цинка. При сварке деталей из листовой стали марки Ст 3 толщиной 3 мм зазор в стыке не должен превышать 0,5 мм. Сварку ведут проволокой диаметром 1,0–1,2 мм, скорость сварки 20–25 м/ч, напряжение 22–23 В, ток 140–150 А, расход углекислого газа 700–800 л/ч. При приварке обшивки к уголку ток можно увеличить до 160-180А. В местах, не требующих герметизации, листы сваривают отдельными точками (электрозаклепками).
Наплавку цилиндрических деталей в среде углекислого газа применяют при ремонте цилиндрических деталей диаметром 10–30 мм. Для наплавки используют перечисленные выше аппараты или наплавочные установки УД-209 и У-653, проволоку диаметром 0,8–1,0 мм при скорости подачи ее 160–200 м/ч, напряжение 17–18 В, ток 70–90 А. При указанных режимах за один проход наплавляют слой толщиной 0,8–1,0 мм. Шаг наплавки равен 1,5–1,8 мм/об, частоту вращения детали определяют в зависимости от ее диаметра так, чтобы скорость наплавки находилась в пределах 20–25 м/ч. Смещение проволоки с зенита принимают от 2 до 5 мм пропорционально увеличению диаметра наплавляемой детали, а вылет проволоки из наконечника – 8-10 мм.
Заварку трещин начинают с нагрева ее концов и обварки их, после чего ведут сварку от середины к концам короткими участками с перекрывающими один другой отжигающими валиками. Фаски по краям трещины наплавляют раздельно. Сварку периодически прерывают для остывания детали и выравнивания температуры отдельных ее частей. Участки трещины, выходящие на край детали, заваривают на повышенном режиме: напряжение 22–25 В, ток 130–180 А. Если температурное расширение нагретого металла затруднено, следует заваривать при минимальном нагреве: напряжение 18–22 В, ток 70–90 А, расход газа 600–750 л/ч, электродная проволока диаметром 1,0 мм. Хорошие результаты при сварке чугунных деталей получают, если фаски по краям трещин вначале наплавить вручную тонким слоем электродами МНЧ-2, ЦЧ-ЗА и ЦЧ-4. После этого сварку ведут полуавтоматическим способом в среде углекислого газа.
17.5. Аргонно-дуговая сварка и наплавка
Сварку и наплавку неплавящимся электродом с защитой инертными газами применяют для деталей из коррозионностойких сталей, жаропрочных, алюминиевых и других сплавов. При этом способе неплавящиеся электроды служат только для возбуждения и поддержания горения дуги. При необходимости в зону дуги вводят присадочный материал в виде прутков или проволоки. Аргонно-дуговая сварка выполняется на постоянном токе прямой полярности от источника с крутопадающей характеристикой, а также на переменном токе (сварку алюминия). Из инертных газов применяются аргон, гелий и их смеси. Инертные газы во время процесса не растворяются в металле сварочной ванны, не образуют химические соединения и обеспечивают высокую устойчивость горения дуги. Аргон и гелий негорючие, невзрывоопасные, без цвета и запаха инертные газы. Будучи тяжелее воздуха, аргон обеспечивает хорошую защиту сварочной ванны. Газообразный аргон производится двух сортов: высший сорт содержит 99,992 % аргона и первый сорт 99,987 %. Гелий тоже производится двух сортов: высокой чистоты (99,985 % гелия) и технический (99,8 % гелия). Гелий используют реже ввиду его летучести. В качестве неплавящихся электродов при постоянном токе применяют обычно вольфрамовые, лантанированные и торированные вольфрамовые прутки диаметром 0,8–8 мм. При переменном токе используют чистые вольфрамовые прутки. При аргонно-дуговой сварке используют газоэлектрические горелки следующих типов: ЭЗР, ГРАД, АР, УДАР и УД Г.
Проволоки, используемые при аргонно-дуговой сварке алюминиевых сплавов, приведены в табл. 59. Рекомендуемые режимы аргонно-дуговой сварки деталей из алюминиевых сплавов, приведены в табл. 60.
Таблица 59. Присадочные проволоки для сварки алюминиевых сплавов

Таблица 60. Рекомендуемые режимы аргонно-дуговой сварки деталей из алюминиевых сплавов

Правообладателям!
Это произведение, предположительно, находится в статусе 'public domain'. Если это не так и размещение материала нарушает чьи-либо права, то сообщите нам об этом.