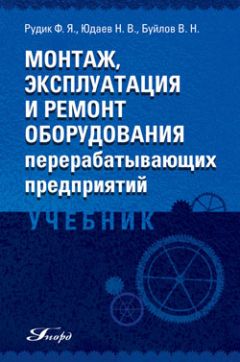
Автор книги: Феликс Рудик
Жанр: Техническая литература, Наука и Образование
сообщить о неприемлемом содержимом
Текущая страница: 19 (всего у книги 20 страниц)
17.9. Применение полимерных материалов при ремонте деталей
Полимерные материалы находят широкое применение в различных отраслях промышленности, в том числе и ремонтном производстве. Их используют для изготовления деталей, нанесения износостойких покрытий на трущиеся поверхности подшипников скольжения, для склеивания металлов, заделки трещин и т. д. Это объясняется их достаточно высокой механической прочностью при малой удельной массе, высокой износостойкостью, эластичностью и химической стойкостью. Пластическими массами называются материалы, основой которых служат высокомолекулярные органические соединения, способные под влиянием повышенных температур и давления принимать определенную форму, сохраняющуюся в обычных условиях. Главная составная часть пластмасс – полимер, который связывает все компоненты. Кроме связующего элемента, в состав пластмассы входят наполнители, пластификаторы, отвердители, красители, катализаторы и другие добавки, которые придают им специфические свойства. В зависимости от химической природы пластмассы делятся на термореактивные (реактопласты) и термопластичные (термопласты). Реактопласты – смолы, которые после нагревания и последующего затвердевания переходят в неплавкое и нерастворимое состояние. Термопласты – смолы, которые при нагревании приобретают пластичность, а в твердое состояние переходят при охлаждении. Эту способность они сохраняют и при неоднократном нагревании и охлаждении.
В ремонтном производстве наибольшее применение находят следующие полимерные материалы: полиамидные смолы, полиэтилен, волокнит, стекловолокнит, пресс-порошки, составы на основе эпоксидных смол ЭД-6 и ЭД-5, синтетические клеи типа БФ и ВС-10Т, фторопласты, термопласт ПФН-12 и др. Существуют следующие способы получения необходимого полезного эффекта: литье под давлением, прессование в пресс-формах, центробежное литье, нанесение тонкослойных покрытий на металлические изделия.
Литье под давлением выполняется на литьевых машинах (рис. 161) и состоит из дозирования, нагрева и расплавления материала, впрыска под давлением порции расплавленного материала в пресс-форму, выдержки под давлением, охлаждения изделия в пресс-форме и его извлечения. Материал засыпают в бункер (1), откуда через дозировочное устройство (2) он поступает в приемную камеру (4). Затем он подается в нагревательный цилиндр (6), где нагревается до температуры плавления и под давлением заполняет пресс-форму. Вода, поступающая по каналам (9), охлаждает пресс-форму. Удельное давление впрыска зависит от материала и составляет 60-200 МПа. Продолжительность цикла 10–40 с, в зависимости от объема изделия.

Рис. 161. Схема литьевой установки: 1 – бункер: 2 – дозировочное устройство; 3 – поршень; 4 – приемная камера; 5 – электрообогреватель; 6 – нагревательный цилиндр; 7 – заливочный канал формы; 8 и 11 – передняя и задняя части формы; 9 – каналы для охлаждения формы; 10 – изделие.
Прессование применяется при изготовлении деталей из термореактивных полимерных материалов. При этом используются пресс-порошки, в состав которых входят связующие смолы, наполнители, красители, ускорители отвердевания и другие вещества. Термореактивный материал в виде порошка или гранул загружают в пресс-форму, где под действием тепла и давления он размягчается и принимает форму изделия. Необходимая температура нагрева материала поддерживается электрическими обогревателями, вмонтированными в обогревательные плиты пресса или в пресс-форму.
Центробежное литье применяется при изготовлении толстостенных изделий из термопластичных материалов: зубчатых колес, крыльчаток, шкивов, втулок и т. д. Технологический процесс центробежного литья деталей состоит из расплавления материала, заливки его в форму (рис. 162), где он под действием центробежных сил заполняет ее периферийную часть и после остывания образует детали нужной конфигурации и размеров.

Рис. 162. Схема установки для центробежного литья: 1 – газовая горелка; 2 – форма (цилиндр); 3 – торцевые; 4 – кулачки патрона станка.
Детали этим способом отливают в вертикальных или горизонтальных формах. Вертикальные формы применяют для цилиндрических деталей, размеры которых в осевом направлении не больше диаметра (зубчатые колеса, фланцы, короткие втулки и т. д.). Горизонтальные формы применяют, когда отливки в осевом направлении не имеют ограничений в размере (втулки, трубы, гильзы и т. д.).
Газопламенное напыление по своему принципу напоминает металлизацию распылением. Через ацетилено-воздушное пламя пропускается струя сжатого воздуха с взвешенными частицами порошка полимерного материала. Время прохождения частиц через зону пламени исчисляется миллионными долями секунды, вследствие чего частицы не успевают полностью расплавиться. Ударяясь о предварительно нагретую металлическую поверхность, они прилипают к ней и под действием пламени горелки сплавляются между собой в сплошной монолитный слой. Основное преимущество этого способа напыления – возможность получения значительной толщины покрытия (до 5 мм и больше), а также нанесения полимерных материалов на детали больших размеров и сложной конфигурации. Недостаток газопламенного напыления – снижение качества наносимого материала вследствие деструкции частиц порошка в пламени горелки. Поэтому процесс газопламенного напыления целесообразно выполнять в два этапа: в начале нагреть деталь, а затем подать порошок при выключенном пламени горелки.
Напыление в псевдосжиженном слое, или вихревым способом, ведется в специальных установках (рис. 163). В рабочую емкость засыпают порошкообразный материал, размер частиц которого не превышает 140–250 мкм. Через пористое дно (3) в цилиндр подается сжатый воздух или инертный газ, который приводит порошок во взвешенное состояние. Полученный таким образом взвихренный слой порошка приобретает некоторые свойства жидкости, поэтому его называют псевдосжиженным.
Метод нанесения полимерных покрытий в псевдосжиженном слое отличается несложным оборудованием и простой технологической схемой. Потерь материала не наблюдается, а производительность процесса высокая при хорошем качестве покрытия. Однако этот процесс требует изоляции (фольгой, асбестом, жидким стеклом и т. д.) мест, не подлежащих покрытию, и не может быть применен для облицовки деталей больших размеров.

Рис. 163. Схема установки для нанесения полимерных покрытий в псевдосжиженном слое (вихревым способом): 1 – редуктор; 2 – покрываемая деталь; 3 – пористое дно; 4 – цилиндр; 5 – асбестовая изоляция; 6 – электропечь; 7 – терморегулятор.
Технологический процесс напыления капрона в псевдосжиженном слое включает в себя следующие операции:
• приготовление порошковой смеси;
• подготовку детали под покрытие (очистку от ржавчины и грязи, обезжиривание, изолирование мест, не подлежащих покрытию);
• нагрев детали в электропечи или на установке Т.В.Ч. До температуры 250–280 °C (для получения большой толщины покрытия температура нагрева должна быть 280–310 °C);
• напыление детали погружением ее в «кипящий» слой порошка и перемещением по оси цилиндра до получения необходимой толщины покрытия;
• термическую обработку покрытия в масле (эта операция не обязательна для деталей, не работающих на износ);
• механическую обработку деталей для получения заданного номинального или ремонтного размера.
Вибрационный способ напыления основан на способности сыпучих материалов течь при вибрировании. При сообщении сыпучему материалу, находящемуся в сосуде, вибрационных колебаний в вертикальной плоскости происходит уменьшение сил внутреннего трения между частицами порошка, и он приобретает некоторые свойства вязкой жидкости. В отличие от вихревого способа напыления вибрационный не требует применения сжатого воздуха (газа) и его подогрева во избежание резкого охлаждения покрываемых деталей. К недостаткам этого способа следует отнести высокие требования к дисперсности порошка, необходимость изоляции мест, не подлежащих покрытию, и неравномерность покрытия.
Центробежный способ нанесения покрытий подобен центробежному литью. Восстанавливаемую втулку устанавливают во вращающийся патрон, находящийся в нагревательной камере. Порошок подается к внутренней поверхности вращающейся втулки из специального распылителя струей воздуха (газа) и под действием центробежной силы равномерно распределяется по образующей. Этот способ увеличивает прочность сцепления покрытий и повышает их износостойкость вследствие плотного распределения макромолекул полимера.
Опрессовка деталей пластмассовыми покрытиями заключается в том, что изделие устанавливают в пресс-форму и на литьевой машине опрессовывают его пластмассой.
Процесс покрытия поверхности детали состоит в том, что материал в виде крошки или отходов, загруженный в плавильный цилиндр (2) (рис. 164), после расплавления выдавливается поршнем (4) на предварительно подогретую поверхность детали (8).

Рис. 164. Схема установки для нанесения полимерных покрытий из расплава: 1 – лоток; 2 – плавильный цилиндр; 3 – заслонка; 4 – поршень; 5 – нагревательный элемент; 6 – расплавленный материал; 7 – стойка крепленая; 8 – покрываемая деталь.
Этот способ позволяет использовать материал в любом виде, в то время как нанесение покрытий напылением связано с потреблением порошкообразного полимера. Кроме того, литьем из расплава можно получать толщину покрытия более 5 мм.
Ремонт корпусных деталей составами на основе эпоксидных смол включает в себя следующие операции (рис. 165): подготовку поверхности детали; приготовление и нанесение эпоксидной композиции, а также термообработку нанесенных покрытий.

Рис. 165. Устранение трещин: 1 – трещина; 2 – отверстия диаметром 3–5 мм; 3 – фаска, глубина зависит от толщины детали.
Подготовка поверхности детали к заделке повреждений состоит в засверливании концов трещин, предотвращающих их продолжение, разделывании фаски, зачистке покрываемых мест до металлического блеска с последующим обезжириванием ацетоном (рис. 166). От качества подготовки поверхностей ремонтируемых деталей в основном зависит прочность сцепления клеевого состава с металлом. Приготовление эпоксидной композиции ведут в определенной последовательности. Отмеряют необходимое количество эпоксидной смолы ЭД-6 или ЭД-5, подогревают ее до температуры 60 °C и добавляют пластификатор (дибутилфталат). Качество эпоксидных покрытий во многом зависит от состава композиции (таблица 62). Затем после тщательного перемешивания вводят в смесь наполнители и еще раз тщательно перемешивают массу. В заключение добавляют отвердитель (полиэтиленполиамин) и опять перемешивают состав. Пластификатор (дибутилфталат) повышает эластичность клеевой пленки, ударную прочность и стойкость композиции к температурным колебаниям.

Рис. 166. Последовательность заделки трещин с помощью клеев: очистка поверхности в зоне трещин; б – установка упрочняющих пробок по трещине; в – заделка трещины; г – укладка асбестового шнура в разделку трещины; д – наложение тканевых заплат на трещину и их прикатывание; е – установка на заплаты пресспакета и сушка; 1 – бумага; 2 – резина; 3 – стальная накладка.
Таблица 62. Составы эпоксидных композиций в частях по массе

Наполнитель (тонкоизмельченный металлический порошок, графит и другие материалы) снижает усадку смолы, сближает коэффициент расширения связующего и склеиваемого материалов, улучшает теплопроводность композиции. Отвердитель (полиэтиленполиамин) служит для превращения эпоксидных составов из жидкого или тестообразного состояния в необратимое твердое вещество. Составы на основе эпоксидных смол приготовляют в зависимости от материала ремонтируемой детали. Приготовленную композицию наносят шпателем или специальным шприцем. Через 20–30 мин она начинает отвердевать, поэтому работы по заделке трещин, пробоин и других повреждений следует вести без промедления. Если характер повреждения таков, что заделка одним составом невозможна, то применяют заплаты, которые также предварительно подготавливают (зачищают, обезжиривают и т. д.). Одинарные или многослойные заплаты изготавливают из стеклоткани, пропитывают смолой и приклеивают на трещине или пробоине. Термическая обработка покрытия применяется для ускорения процесса отвердевания клеевого состава. Хорошие результаты дает выдержка деталей при комнатной температуре в течение 20–24 ч с последующей обработкой их при температуре 130–150 °C в течение 2,5–3,0 ч.
При склеивании деталей в ремонтном производстве чаще всего применяют клеи типа БФ, № 88, ВС-10Т и др. Наибольшая прочность клеевого соединения при высоких температурах получается при использовании клея ВС-10Т. Детали, подлежащие склеиванию, тщательно зачищают и обезжиривают ацетоном. На подготовленные поверхности наносят слой клея толщиной 0,1–0,2 мм с последующей выдержкой деталей при температуре 18–25 °C в течение 10–15 мин, затем наносят второй слой толщиной 0,1–0,2 мм и снова выдерживают 10–15 мин при той же температуре. После этого детали соединяют под давлением 0,3–0,4 МН/м2 и выдерживают в печи при температуре 170–180 °C в течение 1,0–1,5 ч. Охлаждать склеенные изделия рекомендуется медленно вместе с печью.
Износостойкость полимерных материалов достаточно высокая в различных условиях эксплуатации. Даже при абразивном трении полиамиды в некоторых случаях изнашиваются меньше, чем металлы. Характер износа обусловлен механическим и химическим взаимодействием контактирующихся точек, их термоокислительной деструкцией, явлениями усталости покрытий, условиями работы деталей и т. д. Установлено, что кристаллические компоненты полимера имеют более высокую износостойкость и механическую прочность, а аморфные – эластичность. Термическая обработка некоторых пластмасс оказывает большое влияние на их износостойкость. Так, обработка капроновых покрытий в масляной ванне при температуре 180 °C снижает их износ примерно в 10 раз по сравнению с образцами без термической обработки. Это явление можно объяснить структурными изменениями материала. Однако дальнейшее увеличение температуры масла способствует повышению износа пластмасс, что объясняется повышенной деструкцией полимера. Установлен следующий оптимальный режим термической обработки капроновых покрытий: нагрев деталей в масле при температуре 170–180 °C, выдержка при этой температуре в течение 10–15 мин и медленное охлаждение вместе с ванной. Для повышения износостойкости деталей в капрон, например, вводят твердые смазки (графит или дисульфид молибдена). Такие пластмассы обладают меньшей влагопоглощаемостью, более низким коэффициентом трения и нечувствительностью к старению. При трении без смазки лучшие результаты дают полиамиды с присадкой дисульфида молибдена, а при смазке лучше применять графит. Применяя термическую обработку и наполнители, необходимо учитывать их влияние на прочность сцепления пленки с металлом и внутренние напряжения покрытий.
В противном случае может оказаться, что повышение износостойкости приведет к уменьшению сцепляемости покрытия с металлом. Возрастание износа сопряженных деталей с увеличением толщины слоя полимерного материала объясняется уменьшением теплоотдачи сопряжения и вызывающим повышение температуры. Оптимальная толщина слоя полимерного материала находится в пределах 0,2–0,3 мм. С увеличением износа покрытия растет и износ материала сопрягаемой детали, что связано с увеличением количества продуктов химического и механического взаимодействия трущихся материалов в зоне контакта вала и подшипника. На износостойкость полимерных покрытий существенное влияние оказывает материал сопрягаемой детали. Хорошую износостойкость имеют пары сталь 45 – капрон и чугун – капрон. Конструкторские факторы значительно влияют на износостойкость металлополимерных подшипниковых сопряжений. Из соображений улучшения теплоотвода следует применять короткие подшипниковые сопряжения, то есть длина втулки не должна превышать ее диаметр. В связи с большим тепловым расширением и набуханием пластмасс в металлополимерном сопряжении зазор должен быть большим, чем в металлической паре. Этот зазор устанавливается в зависимости от диаметра вала, толщины стенки и термического расширения пластмассовой втулки.
17.10. Механическая обработка восстановленных деталей
Большинство технологических процессов ремонта деталей машин связано с механической обработкой. Она предшествует операциям наращивания изношенных поверхностей, и она же представляет заключительные операции обработки. Восстановление посадок способом ремонтных размеров и дополнительных ремонтных деталей ведется только путем механической обработки.
Качеством и точностью механической обработки деталей определяется качество отремонтированной машины. Точность механической обработки деталей во многом зависит от правильного выбора установочных баз и умелого их использования. В свою очередь, выбор установочных баз диктуется особенностью координационно-кинематических и координатных размеров обрабатываемой детали. Опоры, жестко связанные между собой в общей цепи механизма, принято называть замыкающим (базисным) звеном. Всякое звено кинематической цепи механизма, узла или агрегата машины несет на себе два вида сопрягаемых поверхностей: базовые и базисные. Первыми оно опирается на поверхность предыдущего звена и благодаря этому занимает в механизме заданное конструкцией положение; вторые служат опорами для последующего звена кинематической цепи и определяют его заданное конструкцией положение в механизме. Координационными называют размеры детали, определяющие взаимное расположение ее поверхностей. Одни из них определяют возможность получить взаимозаменяемость деталей при монтаже, облегчая их совместную сборку. Такие координационные размеры называют координационно-сборочными. Другие, кроме того, определяют координацию базовых и базисных поверхностей деталей, выполняющих роль кинематических звеньев механизма, такие размеры называют координационно-кинематическими. Они наиболее ответственные, и исполнение деталей по этим размерам должно быть особо тщательным. При разработке технологического процесса обработки деталей в качестве основных установочных баз выбирают конструкционные. Поскольку эти базы одновременно служат поверхностями сопряжения, то между собой и со всеми другими поверхностями они связываются прямыми размерами. Выбор установочной базы для обработки ремонтной заготовки усложняется тем, что приходится обрабатывать поверхности, которые при изготовлении новой детали уже были установочными и измерительными базами. Оптимальным считается вариант, когда установочная технологическая база совпадает с конструктивно-измерительной. В ремонтном производстве наиболее удобны те детали, в конструкции которых предусмотрены вспомогательные базы. Вспомогательная база, которая не изнашивается в процессе эксплуатации детали, позволяет с достаточной точностью восстановить заданную чертежом координацию ее поверхностей. Отсутствие такой базы чаще всего приводит к большему или меньшему нарушению координации поверхности ремонтируемой детали. Погрешность обработки обусловливается неточностью станка, неточностью установки на нем приспособления, неточностью изготовления элементов приспособления и, наконец, неточностью установки самой обрабатываемой детали в приспособлении или непосредственно на станке. Все указанные неточности могут складываться, и тогда погрешность установки достигает значительных размеров. При ремонте машин из всех мероприятий, направленных на увеличение срока службы деталей, сопряжений и всей машины, основное внимание следует уделять точности координации базовых и базисных поверхностей. Несоблюдение указанных условий делает все другие мероприятия, направленные на увеличение срока службы отремонтированных машин, малоэффективными, так как они исходят из расчета нормальных, заданных конструкцией условий работы сопряжений.
Гладкие валы в механизме выполняют роль штифтов, пальцев, тяг, штанг, осей и т. п. Их цилиндрическая поверхность может быть базовой на одной части их длины и базисной – на другой. Установочной базой таких валов может быть их цилиндрическая поверхность, обрабатывать которую легко на бесцентрово-шлифовальных станках.
Ступенчатые валы (рис. 167) при обработке необходимо располагать так, чтобы геометрические оси всех обрабатываемых цилиндрических поверхностей лежали на одной прямой. Это условие наиболее просто выполняется при обработке деталей в центрах (2) и (6). Концентричность расположения всех поверхностей детали относительно оси шпинделя станка проверяют индикатором (4) при проворачивании детали вручную.

Рис. 167. Схема установки ступенчатого вала на станке для обработки его в центрах: 1– планшайба; 2 и 6 – центры; 3 – поводок; 4 – индикатор; 5 – вал.
Шлицевые и зубчатые валы имеют дополнительные координационно-кинематические размеры, заданные особенностями шлицевой части вала (рис. 168). Необходимо, чтобы при обработке геометрические оси шлицев (по сечению) проходили через геометрический центр сечения вала и чтобы боковые поверхности шлицев и поверхность дна шлицевой канавки были параллельны оси вала (4). При обработке шлицев используют горизонтально-фрезерные станки с делительной головкой (1), а размеры сечения шлицевой части вала получают наладкой станка по новой неизношенной шлицевой детали.
Для строгого соблюдения координационно-кинематических размеров деталь при обработке устанавливают так, чтобы ее геометрическая ось совпадала с направлением перемещения стола и была ему параллельна.

Рис. 168. Схема установки шлицевого вала в делительной головке на горизонтально-фрезерном станке: 1 – делительная головка; 2 и 5 – центры: 3 – индикатор; 4 – шлицевой вал; 6 – фреза.
Фланцевые валы отличаются от ступенчатых тем, что, кроме концентричности цилиндрических поверхностей, имеют дополнительный координационно-кинематический размер: плоская (сопрягаемая) поверхность торца фланца перпендикулярна геометрической оси вала. Координационно-кинематические размеры при обработке вала получают базированием его в центрах.
Сложные валы включают в себя координационно-кинематически е размеры простых деталей в различном их сочетании. Поэтому технологический процесс их обработки складывается из рассмотренных выше приемов.
Последовательность операций выбирают так, чтобы поверхность, которая служат установочной базой на данной операции, была обработана на предшествующих операциях.
Детали группы втулок имеют, как правило, координационно-кинематические размеры, определяющие концентричность наружной и внутренней цилиндрических поверхностей. По конструктивному оформлению втулки могут быть гладкие и бесступенчатые, ступенчатые, фланцевые, шлицевые и зубчатые, а также сложные, включающие указанные выше особенности конструкции в разном сочетании.
Гладкие втулки имеют одну базовую и одну базисную поверхности, соответственно наружную и внутреннюю цилиндрические поверхности. Координационно-кинематический размер, связывающий эти поверхности, требует, чтобы они «мели одну общую геометрическую ось. Для этого необходимо при установке детали на токарном станке совместить ее геометрическую ось с осью шпинделя станка. При изготовлении новой втулки эта задача легко выполняется, если обработка внутренней и наружной поверхностей ведется за одну установку заготовки в патроне с последующей отрезкой. Однако при ремонте втулки воспользоваться указанным способом не удается, поэтому применяют оправки.
При обработке крупных серий деталей для соблюдения точности по координационно-кинематическим размерам применяют специальные приспособления цангового или мембранного типа (рис. 169). Каждое из таких приспособлений предназначается для одного типоразмера детали.
На рис. 169, а и 169, в изображены цанговые патроны для внутреннего и наружного захвата деталей. Зажимающим элементом служит цанга (3), которая при завинчивании болта (4) перемещается по конусной поверхности корпуса и, благодаря упругим свойствам своих перьев, закрепляет установленную для обработки деталь (1). На рис. 169, б изображен мембранный патрон. При завинчивании болта (4) перемещается втулка (5) и давит на мембраны (3), которые передают это давление на другую, левую по рис., сборку мембран. Мембраны при зажиме увеличивают наружный диаметр и этим закрепляют обрабатываемую деталь (1). Точность установки обрабатываемой детали с помощью таких приспособлений зависит от точности изготовления самих приспособлений, а также от точности их установки на станке.

Рис. 169. Специальные приспособления для обработки втулок: а – цанговая оправка; б – мембранная оправка: в – цанговый патрон; 1 – обрабатываемая деталь; 2 – оправка (конус); 3 – цанга (мембрана); 4 – болт (гайка); 5 – шайба.
Ступенчатые втулки обычно имеют по нескольку поверхностей, которые должны быть строго концентричны между собой; выбор установочных баз и обработка этих деталей выполняются аналогично гладким втулкам. Фланцевые втулки для обработки устанавливают так, чтобы цилиндрические поверхности были концентричными, а плоская поверхность торца фланца была перпендикулярна к их общей геометрической оси. Для этих втулок необходимо при любом способе крепления, указанном для гладких втулок, обработать с одной и той же установки внутренние поверхности и торец фланца. При этом целесообразно в качестве одной из установочных баз использовать торцевую поверхность.
Детали группы дисков и фланцев в основном имеют один координационно-кинематический размер – плоскую торцевую поверхность диска, которая должна быть перпендикулярна оси его отверстия. Если у диска два рабочих торца, то требование перпендикулярности оси отверстия относится к обеим плоским торцевым поверхностям. При ремонте таких деталей необходимо геометрическую ось отверстия диска совместить с осью шпинделя токарного станка. Когда требуется обработка торцевой части такой детали, в качестве установочной базы используют поверхность отверстия. Для совмещения геометрических осей отверстия детали и шпинделя станка используют оправки. Для обработки отверстия установочной базой служит торец детали, а в качестве проверочной базы используется неизношенная часть поверхности отверстия. Совмещение геометрических осей отверстия детали и шпинделя станка достигается с помощью индикатора. При выборе установочных баз для обработки деталей необходимо иметь в виду, что наилучшая координация базовых и базисных поверхностей получается в том случае, когда их обрабатывают на станке за одну установку. В связи с этим в качестве установочной базы можно использовать черновую (необработанную) поверхность детали, которую устанавливают в четырехкулачковом патроне.
Корпусные (базисные) детали обычно достаточно сложной формы. Они включают в себя несколько базисных поверхностей. Базисные поверхности – опоры для одной детали составляют отдельную линию базисных поверхностей. Строгость координации отдельных базисных поверхностей внутри каждой из линий и линий между собой определяет качество обработки корпусных деталей. Кроме базисных, эти детали имеют и базовые поверхности, которые служат местом контактирования с базовыми же поверхностями базисной детали другого узла.
Выбор режимов резания для обработки ремонтных заготовок усложняется условиями их получения. В одних случаях ремонтная заготовка получается в результате наплавки металла на изношенную поверхность, в других – в результате гальванического наращивания или металлизационного напыления. В зависимости от способа наращивания структура и физико-механические свойства покрытий отличаются друг от друга и от основного металла. Это необходимо учитывать при выборе режимов резания для механической обработки восстановленных поверхностей. Токарная обработка применяется в том случае, когда после восстановления размеров одним из способов припуск на обработку превышает 0,25 мм на сторону и когда твердость металла менее 3000 МПа. Механическую обработку наплавленных и металлизационных поверхностей следует вести в несколько проходов. При черновом точении (в зависимости от структуры и поверхностной неровности) необходимо выбирать скорости резания, на 30–60 % уменьшенные по сравнению с применяемыми при обработке нормализоанной стали 45, а при чистовом точении – уменьшенные на 20–30 %. Качество и производительность обработки значительно повышаются при использовании резцов с пластинками из твердых сплавов и минералокерамических пластин. Скорость резания при черновом точении выбирают уменьшенную на 10–20 % по сравнению со скоростью резания для нормализованной стали 45, а при чистовом точении такую же, как и для стали 45. Детали из пластмасс обычно обрабатывают при больших скоростях резания. Термопласты (винипласт, фторопласт, полистирол и др.) лучше обрабатывать резцами, снабженными пластинками из твердых сплавов. Точение ведут при скорости резания 300–600 м/мин и подаче 0,2–0,4 мм/об (при черновой обработке) и 0,05-0,15 мм/об (при чистовой). Термореактивные пластмассы обрабатывают теми же резцами при скорости резания 200–500 м/мин и подаче до 0,3 мм/об. Шлифование применяют в том случае, когда твердость ремонтной заготовки не позволяет применить точение или когда необходимо получить высокую точность обработки и малую шероховатость поверхности. Шлифуют деталь непосредственно после нанесения покрытия или после предварительной токарной обработки. Этот процесс сопровождается выделением большого количества тепла и значительной деформацией поверхностного слоя, иногда на глубину до 50 мкм. Неправильно выбранные режимы резания, затупление зерна и засаливание круга могут привести к структурным изменениям поверхностных слоев покрытия, к ухудшению их механических свойств, образованию «прижогов», «шлифовальных трещин» и т. д. Поэтому при обработке деталей с различными покрытиями режимы шлифования следует выбирать значительно ниже, чем при обработке деталей без покрытий. Наплавленные поверхности рекомендуется шлифовать электрокорундовыми кругами зернистостью 32–50 и связками – средне-мягкой (СМ), средней (С) или средне-твердой (СТ). Для чернового шлифования обычно применяют круги Э5 °C1-С2К или Э4 °CТ1-СТ2К, а для чистового – Э40-25СМ2-С1 К. Обработку ведут при обильном охлаждении 5-10 %-ным раствором эмульсора в содовой воде. Хромовые и железные покрытия обрабатывают электрокорундовыми кругами, зернистостью 60-100 на мягкой (M1, М2) или среднемягкой связке. Металлизационные покрытия лучше шлифовать монокорундовыми кругами М7 или М8. Возможна обработка и электрокорундовыми кругами зернистостью 40–60 на связке M1, М2, СТ1, СТ2. Пластмассы рекомендуется обрабатывать абразивными кругами зернистостью 30–60 с мягкой связкой.
Правообладателям!
Это произведение, предположительно, находится в статусе 'public domain'. Если это не так и размещение материала нарушает чьи-либо права, то сообщите нам об этом.