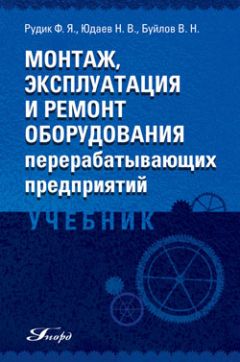
Автор книги: Феликс Рудик
Жанр: Техническая литература, Наука и Образование
сообщить о неприемлемом содержимом
Текущая страница: 9 (всего у книги 20 страниц)
Центрифуги непрерывного действия, поступают в собранном виде. Монтируют их на металлической раме. Выверку горизонтальности центрифуг производят по уровню, устанавливаемому на вал машины, после чего окончательно крепят к раме. К фланцу питающей трубы центрифуги присоединяют трубопровод подачи суспензии, а к фланцам нижней части кожуха – трубопровод для отвода фугата и желоб для вывода осадка.
Затем проверяют качество крепления рамы к фундаменту и центрифуги к раме, проводят испытание на холостом ходу в течение одного часа.
Таблица 36. Допуски на монтаж автоматических центрифуг горизонтальных


Таблица 37. Допуски на монтаж фильтров

Таблица 38. Допуски на монтаж аппаратов с перемешивающими устройствами

Теплообменники, как правило, поступают с завода-изготовителя в собранном виде. Перед монтажом проводят ревизию аппарата, которая состоит в осмотре внутренней части при снятых крышках. Особое внимание обращают на качество вальцовки труб. Качество вальцовки проверяется постукиванием и, если при этом нет дребезжащего звука, вальцовка удовлетворительна. Проходимость труб проверяют их просвечиванием.
Теплообменник монтируется на опорной металлоконструкции или фундаменте. Чаще всего теплообменники устанавливаются горизонтально или вертикально. Горизонтальность выверяется по уровню, допускаемое отклонение при этом не должно превышать 0,5 мм на 1 м длины. При вертикальной установке теплообменника для выверки используется отвес. Для окончательной установки аппарата при выверке используют подкладки, размещаемые под опорными плоскостями.
Кожухотрубчатые теплообменники испытывают гидравлическими методами. Отсоединяют крышки, межтрубчатое пространство заполняют водой, поднимают давление до давления испытания, выдерживают и следят за ним по манометру. Если давление падает, значит, в системе имеются неплотности, которые могут быть: а) в местах развальцовки труб; б) в самих трубах (трещины и т. д.).
Неплотности в развальцовке обнаруживаются по течи и отпотинам, а в трубах – по появлению воды.
Иногда при испытании давление падает, а визуально течь воды не обнаруживается, тогда сливают воду из межтрубного пространства и подают в него пар. Выход пара из определенных трубок указывает на дефекты в них.
Монтаж ленточной сушилки заключается в агрегировании отдельно поставляемых блоков и узлов: сушильной камеры; ленты с барабанами; калориферно-вентиляционной установки; трубопроводных узлов; электропусковой аппаратуры и т. д.
Сушильная камера монтируется на фундаменте, при этом правильность ее установки проверяется по уровню. Особое внимание при монтаже обращается замерам по диагоналям, как самой камеры, так и расстоянию между опорами подшипников барабанов ленты. При несовпадении размеров по диагоналям может произойти перекос ленты, который невозможно ликвидировать натяжным барабаном.
Качество сборки паровых калориферов, трубопроводов и других элементов системы обогрева проверяют гидравлическими испытаниями. Паровые калориферы монтируют с уклоном в сторону отвода конденсата. При этом превышение одной стороны калорифера над другой должно быть в пределах 5 мм.
Специфика монтажа барабанной сушилки заключается в максимально точной установке и выверке опорных поверхностей с заданным уклоном. Торцевые поверхности двух опорных роликов должны находиться в одной плоскости. Расстояние между опорными роликами должно быть на 20 мм больше ширины бандажа (по 10 мм с каждой стороны).
После выверки опорных поверхностей и заливки бетоном фундаментных плит с помощью крана размещают на станциях собранный корпус барабана. При этом контакт сопрягаемых поверхностей бандажей и опорных роликов должен быть в средней части не менее 2/3 длины образующих. Контакт проверяют путем смазки тонким слоем смываемой краски рабочих поверхностей опорных роликов.
При выверке привода совмещают середины зубчатого венца и малой шестерни и обеспечивают зазор между вершиной и впадиной зуба величиной 0,25. Контакт сопрягаемых поверхностей зубьев шестерен должен быть не менее 2/3 длины образующих.
При монтаже загрузочной и разгрузочной камер обеспечивают параллельность и соосность с корпусом сушилки.
Таблица 39. Допуски на монтаж вальцовых сушильных аппаратов

Установку резервуаров производят на искусственное основание, состоящее из грунтовой подсыпки (песчаной подушки). На песчаный слой укладывают гидроизоляционный слой, приготовленный из битума и песка. Толщина гидроизоляции 8-100 мм. Затем на это основание краном укладывают рулон днища и разворачивают его. Днище, как правило, состоит из двух-трех частей, их сваривают и испытывают в целом заполнением воды. На днище устанавливают рулон корпуса и разворачивают его с помощью трактора или лебедки. Покрытие резервуара монтируют из плоских секторных щитов, устанавливаемых при монтаже на поддерживающую стойку, убираемую после монтажа.
Готовый резервуар испытывают на прочность и плотность заполнением воды или на плотность пробой керосином.
Сферические резервуары свариваются из «лепестков», часто изготавливаемых методом горячей штамповки. Размеры этих элементов максимально возможные по условиям транспортировки.
На заводе-изготовителе проводят контрольную сварку с установкой фиксаторов. На месте монтажа при сварке швы накладывают в определенной последовательности согласно технологической карте. Сварка применяется автоматическая.
Таблица 40. Допуски на монтаж емкостной аппаратуры

Таблица 41. Допуски на монтаж теплообменных и выпарных аппаратов


При расчете трубопроводов принимается, что его сечение заполнено жидкостью целиком и при движении жидкости сохраняются постоянными такие параметры, как скорость, давление и сопротивление. Скорость жидкости зависит от напора, создаваемого насосом или высотой, с которой она идет самотеком, а также ее вязкости и конструкции трубопровода. На практике принимают при расчетах следующую скорость:
• самотечные трубопроводы – 0,5–1,25 м/с;
• напорные трубопроводы – 1–3 м/с;
• газопроводы для газов, насыщенных паров – 10–30 м/с.
Секундный расход протекающей жидкости или газа по трубопроводу определяется по уравнению:

Формула № 75.
где d – диаметр трубы, мм;
w – скорость жидкости или газа, м/с.
Тогда внутренний диаметр трубы определятся выражением:

Формула № 76.
где Vc – скорость потока, м/с.
Величины внутреннего диаметра и сопротивления от трения в трубе принимаются также по расчетным таблицам. Толщина стенки стальной трубы с внутренним давлением среды Ру может быть рассчитан по следующим формулам:
а) для бесшовных труб:

Формула № 77.
где Ру – условное давление, которое соответствует рабочему при t = 200 °C, Па;
Dн – наружный диаметр трубы, мм;
σ – допустимое напряжение при t = 200 °C, Па;
А – коэффициент, учитывающий прибавку S на уменьшение толщины при изгибе и коррозии (обычно А = 0,2).
б) для сварных труб:

Формула № 78.
где φ – коэффициент, учитывающий ослабление от сварного шва (обычно φ = 0,6–0,8);
С – прибавка на коррозию.
При монтаже трубопроводов необходимо учитывать изменение их длины при колебаниях температуры воздуха. Величина этого изменения может быть определена по уравнению:

Формула № 79.
где α – термический коэффициент линейного расширения, 1/град;
l – первоначальная длина трубы, мм;
Δt – изменение температуры, °С.
Трубопровод малой длины при нагревании удлиняется, и это удлинение может компенсироваться за счет поворотов и выпучивания трубы. Такой процесс называется самокомпенсацией. Для длинных трубопроводов необходимо вводить в конструкцию компенсаторы линзовые, лирообразные и сальниковые (рис. 97).

Рис. 97. Способы компенсации температурных напряжений: а – линзовые; б – лирообразные
5.3. Монтаж внутрицеховых трубопроводов
Внутри производственных помещений трубопроводы чаще прокладываются открытым способом, т. е. по стенам, колоннам, подвешиваются к элементам всего перекрытия.
Скрытая прокладка труб применяется чаще всего в лабораториях (в нишах стен или в полу). Открытым способом прокладывают также трубы вне зданий по эстакадам, мачтам, столбам и т. д. Прокладка в грунте применяется для водопроводных и канализационных труб.
Расчет опор трубопроводов. Длина пролета между опорами определяется в зависимости от допустимого напряжения на изгиб (для данного материала трубы):

Формула № 80.
где σи – допустимое напряжение на изгиб, Па;
W – момент сопротивления, см3;
q – вес 1 м трубы (с материалом и изоляцией), кг/м.
Расчетная нагрузка на одну опору определяется по уравнению:

Формула № 81.
Опоры для трубопроводов бывают подвижного типа – скользящие и катковые и неподвижного типа – хомутовые и приварные.
Скользящие опоры применяют для прокладки трубопроводов в труднодоступных местах и с большим температурным удлинением. Сами опоры устанавливают на кронштейнах, мачтах, эстакадах.
5.3.1. Монтажные требования к трубопроводамПри монтаже трубопроводов необходимо предусматривать разъемные соединения труб (через каждые 20–30 м). Эти разъемы необходимы для чистки и замены труб при ремонте. Запорную арматуру монтируют на горизонтальных и вертикальных участках (для установленных в труднодоступных местах вентилей применяют штанги, цепные электрические приводы). При укладке трубопроводов часто предусматривают уклоны (0,002-0,005) для стока жидкости. При необходимости для уменьшения потерь тепла трубопроводы теплоизолируют (во избежание конденсации и замерзания жидкости). В качестве изоляционных материалов применяют древесные опилки, минеральную вату, асбест, войлок и т. д. Трубопроводы во взрывоопасных цехах заземляются. После монтажа технологические трубопроводы испытывают на прочность и плотность, затем они промываются и продуваются. Чаще всего трубопроводы подвергаются гидравлическим и в редких случаях пневматическим испытаниям. Давление испытания зависит от материала трубопровода, рабочего давления и температуры. Промывают трубопроводы чаще всего водой с использованием моющих средств и продувают сжатым воздухом.
Отдельные участки труб соединяются сваркой, пайкой, склеиванием, а также с помощью муфт, фланцев и раструбов.
Сваркой или пайкой (рис. 98) соединяются трубы из черных (кроме чугуна) и цветных металлов, полиэтиленовых и винипластовых материалов.
Преимущество сварочных соединений заключается в высокой прочности шва (100 % от прочности цельной трубы), в удобстве эксплуатации (минимальные течи), в простоте обслуживания и высокой экономичности процесса. В качестве недостатков следует отметить трудность разборки трубопроводов. Поэтому делают смешанные соединения, т. е. две-три трубы сваривают, а затем ставят фланцевое соединение. При сварке труб толщиной не менее 5 мм кромки труб запиливают под углом 30–45°. Для обеспечения хорошего привара труб и избежания сплющивания между торцами оставляют зазор 2–3 мм.
В нержавеющих сталях при сварке уменьшается концентрация хрома и у них повышается склонность к межкристаллитной коррозии и разрушению. Поэтому сварку следует вести небольшими зонами термического воздействия:
а) сварка встык – применяется при соединении стальных, алюминиевых и свинцовых труб (рис. 99, а);
б) сварка (пайка) с разбортовкой – применяется при соединении медных и свинцовых труб (рис. 99, б);
в) сварка (пайка) с муфтой – применяется в случае, когда требуется высокая прочность соединения (рис. 99, в);
г) сварка встык полимерных труб – производится специальными термическими устройствами (рис. 99, г).

Рис. 98. Схема подготовки торцов к сварке.

Рис. 99. Способы соединения труб.
Трубы, изготовленные из полимерных материалов, соединяют также и склеиванием.
Для разветвления трубопроводов и установки КИП используют так называемые фасонные части или фитинги. К ним относят: тройники, крестовины, отводы и т. п. Фитинги соединяются с трубопроводами с помощью резьбы, фланцев и сварки. Для изготовления отводов применяют специальные прессы, которые обеспечивают также значительную экономию металла. Для отключения и включения потока транспортируемой среды на трубопроводах устанавливают запорную арматуру: краны, вентили и задвижки.
Запорная арматура различается по характеру привода:
• управляемая вручную;
• приводимая в действие электродвигателем, гидравлически;
• включаемую и выключаемую автоматически.
Запорная арматура соединяется с трубопроводами с помощью фланцев, муфт и сваркой.
5.3.2. Сварочные работы при монтаже трубопроводовСосуды и аппараты, работающие под давлением, превышающим 0,07 Н/мм2 (без учета гидростатического давления), изготовляют и сваривают в соответствии с требованиями правил Госгортехнадзора. Сосуды и аппараты, не подлежащие контролю органов Госгортехнадзора и работающие без давления, под давлением до 0,07 Н/мм2, под вакуумом с остаточным давлением не ниже 5 мм рт. ст. и при температуре среды не ниже 70 °C сваривают, руководствуясь нормами МН 72–69.
Сосуды и аппараты сваривают ручной дуговой сваркой, автоматической и полуавтоматической сваркой под флюсом, газовой ацетилено-кислородной сваркой, различными газоэлектрическими способами сварки.
Качество и основные характеристики материалов должны быть подтверждены заводами – поставщиками в сертификатах. При отсутствии сертификатов материалы подвергают испытаниям для проверки соответствия их качества требованиям стандартов или технических условий. Основные справочные данные по различным способам сварки, применяемым при монтаже технологического оборудования трубопроводов, приведены в таблицах 41, 42.
Под слоем флюса сваривают трубы диаметром свыше 200 мм со стенками толщиной 4 мм и более, преимущественно в повторном положении. Для неповоротной сварки труб применяют автоматы АПС или сваривают трубы в среде углекислого газа.
Сварку труб под слоем флюса осуществляют полуавтоматами на подкладных остающихся кольцах по ручной подварке или предварительной сварке в среде углекислого газа или под слоем флюса. Первый слой в потолочном положении сваривают автоматом.
Таблица 42. Назначение различных способов сварки сталей при монтажных работах

Режимы сварки зависят от толщины стенки трубы. Зная толщину стенки (т. е. необходимую глубину проплавления) и выбрав диаметр сварочной проволоки, по допустимой плотности тока на 1 мм2 сечения сварочной проволоки определяют сварочный ток, позволяющий получить заданную глубину проплавления, таблица 43.
Таблица 43. Зависимость глубины проплавления от диаметра электродной проволоки и параметров сварочного тока

Глава 6
Монтаж трубопроводов межаппаратных коммуникаций
6.1. Классификация технологических трубопроводов
В соответствии со строительными нормами и правилами все технологические трубопроводы в зависимости от свойств и параметров транспортируемого продукта, а также требований, предъявляемых к качеству материала труб, изготовлению, сварке, монтажу и испытаниям, разделяются на пять групп и пять категорий (таблица 44). Категория трубопроводов устанавливается проектом.
Таблица 44. Классификация технологических трубопроводов


Примечания:
1. В случае отсутствия в таблице необходимого сочетания параметров следует руководствоваться тем параметром (температурой или давлением), который требуется для отнесения трубопровода к высшей категории.
2. Трубопроводы, работающие под вакуумом до 36 мм рт. ст. и ниже, классифицируются по таблице по свойствам и температуре продукта, а более 35 мм рт. ст. – по специальным техническим условиям.
3. Трубопроводы, транспортирующие сжиженные газы, классифицируются по группе В, но с отнесением на одну категорию выше.
Трубопроводами высокого давления являются те, по которым транспортируются различные жидкости, пары и газы под давлением от 20 до 100 Н/мм2.
К материалу труб и деталей этих трубопроводов, к их изготовлению и монтажу предъявляют повышенные требования.
Технологические трубопроводы высокого давления классифицируют по следующим основным признакам:
• по свойствам транспортируемых продуктов – группы А, Б, В, Г и Д, в соответствии с классификацией технологических трубопроводов, установленной СНиП (см. таблицу 46);
• по давлению транспортируемых продуктов: PY = 20; 25; 32; 40; 50; 64; 80 и 100 Н/мм2;
• по температуре транспортируемых продуктов и материалу, из которого изготовлен (группе стали) трубопровод, в соответствии с таблицей 45.
Таблица 45. Классификация трубопроводов высокого давления в зависимости от температуры и давления транспортируемой среды

6.2. Трубопроводы высокого давления и детали к ним
6.2.1. Материалы для изготовления трубопроводов высокого давления и деталей к нимСтали, применяемые для изготовления трубопроводов высокого давления и деталей к ним, подразделяются на следующие группы: углеродистая (С), хромокремнемарганцевая (ХГ), хромомолибденовая (ХМ), хромомолибденовольфрамованадиевая (ХФ), хромоникельтитановая (ХН).
Группы сталей применяются для изготовления трубопроводов в зависимости от характеристики и рабочей температуры транспортируемой среды представлены в табл. 46.
Таблица 46. Группы сталей для изготовления трубопроводов высокого давления

Марки стали, для изготовления деталей трубопроводов выбираются по таблице 47.
Таблица 47. Марка стали для изготовления деталей трубопроводов высокого давления

*Сталь 18ХЗМВ (ЗИ-578) применяется для изготовления трубопроводов, по которым транспортируются водородосодержащие продукты, имеющие температуру от 390 до 400 °C; сталь 20ХЗМВФ (ЭИ-579) – для трубопроводов, служащих для транспортирования продуктов, имеющих более высокую температуру.
**Из сталей Х18Н10Т, Х17Н13МЗЕ изготовляют только вставки; для фланцев и заглушек применяется сталь марки 35.
Марки стали для изготовления деталей фланцевых соединений указаны в табл. 48.
Таблица 48. Марки стали для изготовления деталей фланцевых соединений

Примечания:
1. Для группы ХГ при толщине фланца до 35 мм включительно применяется сталь 35, а при большей толщине – сталь 30Х.
2. Сталь марки ХЗМВ соответствует, стали марки 18ХЗМВ.
3. Сталь марки 25Х2МФА может быть заменена сталью марки 25X1 МФ.
Химический состав стали марок, указанных в табл., должен удовлетворять требованиям следующих стандартов:
• сталь марок 20 и 25;
• сталь марок 18ХГ, ЗОХ, 35Х, 40Х, ЗОХМА, 38ХА, 20ХГ, 35ХГ2, 40ХФА;
• сталь марки 14ХГС;
• сталь марок Х18Н10Т, Х17Н13МЗТ;
• сталь марок 18ХЗМВ, 20ХМЗВФ и 25X1МФ;
• сталь марки ХЗМВ соответствует стали марки 18ХЗМВ;
• сталь марки 25Х2МФА – техническим условиям заказчика.
6.2.2. Детали фланцевых соединенийДетали фланцевых соединений поставляются по следующим стандартам: фланцы стальные резьбовые – по ГОСТ 9399-85, линзы уплотнительные жесткие и компенсирующие – по ГОСТ 10493-80, шпильки двусторонние – по ГОСТ 10494-80, гайки чистые шестигранные – по ГОСТ 10495-80.
Концы присоединительные резьбовые для арматуры, соединительных частей и трубопроводов, под линзовое уплотнение выполняются по ГОСТ 9490-81. Фланцы и линзы изготовляются из поковок, штамповок, проката с соблюдением категорий прочности, приведенных в табл. 49.
Таблица 49. Категории прочности для стали фланцев и линз

Механические свойства стали для шпилек и гаек фланцевых соединений приведены в табл. 50.
Таблица 50. Механические свойства стали для шпилек и гаек (ГОСТ 10494-80 и 10495-80)


6.3. Централизованное изготовление и монтаж технологических трубопроводов
6.3.1. Разработка деталировочных чертежей трубопроводовВ системе технической документации для централизованного индустриального изготовления технологических трубопроводов принята следующая терминология: патрубок – прямой участок трубы, изготовленный для соединения с деталями; деталь – отводы, переходы, тройники, фланцы, заглушки; элемент – неразъемное соединение прямого участка трубы с деталями или деталей между собой; узел – часть линии, ограниченная транспортными габаритами, которая по своим размерам и конфигурации может быть смонтирована без разборки; линия – отдельный трубопровод, по которому транспортируется продукт с определенными параметрами (давлением, температурой) и который связывает друг с другом отдельные аппараты или линии (на рабочих чертежах каждая линия имеет свой номер); блок – часть объекта (цех, отделение, установка, группа аппаратов одного технологического назначения); объект – комплекс сооружений основных и вспомогательных производств.
Техническая документация для организации централизованного изготовления трубопроводов из элементов включает в себя: пояснительную записку к объекту; перечень чертежей на блок; сводную спецификацию труб и деталей на блок; ведомость трубопроводов по линиям (на блок); деталировочные чертежи, состоящие из монтажно-сборочной схемы и ведомости с характеристиками элементов (таблица 51).
Таблица 51. Удельный вес трубопроводов


Пояснительная записка должна содержать: сведения о материалах, на основании которых разработаны деталировочные чертежи; сведения о внесении изменений в рабочие чертежи с приложением копий соответствующих документов; общий объем выполненных работ с указанием диаметров трубопроводов, для которых производилась деталировка; упрощенный план разбивки на блоки с указанием их номеров; ведомость блоков с указанием перечней чертежей на каждый блок и количество трубопроводов в каждом блоке; краткое описание системы деталировки и состава проекта; перечень нормативных документов на производство работ по изготовлению и монтажу трубопроводов.
В перечне чертежей указываются: номера чертежей; количество листов, на которых выполнен каждый чертеж (линии в перечне чертежей группируются по продуктам и должны указываться по мере возрастания номеров).
Сводная спецификация составляется по разделам: трубы, отводы, переходы, тройники, фланцы. В каждом разделе все специфицированные изделия должны группироваться по материалам, ГОСТ, диаметрам, давлениям. Отдельно должны специфицироваться трубы, устанавливаемые на монтаже и заготовляемые в мастерской. В сводной спецификации указываются: длина труб, количество деталей, единицы и суммарная масса по каждой позиции, а также общая масса трубы и деталей и общая длина труб в погонных метрах.
Ведомость трубопроводов по линиям (на блок) должна составляться в том случае, если она отсутствует в рабочих монтажных чертежах, или деление на блоки, принятое в деталировочных чертежах, отличается от рабочих монтажных чертежей.
Ведомость трубопроводов по линиям и уточнения к ней заполняются в полном соответствии с деталировочными чертежами.
Деталировочные чертежи должны разрабатываться на каждую линию, имеющую свой номер в рабочих чертежах. Если линия проходит в нескольких блоках, то в каждом блоке на данную линию разрабатывается самостоятельный чертеж. Разделение объекта на блоки устанавливается исходя из условий производства монтажных работ. Линии на чертежах изображаются в аксонометрии (без масштаба). В деталировочных чертежах приводятся: общий вид линии в пределах блока; характеристики элементов; спецификация на покупные детали (арматуру, метизы, прокладки). Кроме того, в этих чертежах указываются: продукт, который транспортируется по линии, и его рабочие параметры; категория трубопровода по СНиП, вид испытания и пробное давление; завод, цех, корпус, блок, номер линии; проектная организация, разработавшая рабочие чертежи, и номера чертежей. В номере деталировочного чертежа указываются номера заказа, блока и линии.
На общем виде линии приводятся: габаритные размеры; высотные отметки; привязки к осям, координирующие размеры врезок; номера позиций элементов и их границы; спецификация на покупные детали (арматуру, метизы, прокладки); направление вращения штурвалов арматуры; направление потока продукта; места присоединения контрольно-измерительных приборов и аппарата. Кроме того, к каким линиям или аппаратам подходит данная линия. Границы узлов на общем виде не отмечаются.
В характеристике элементов должны быть приведены их конфигурация, полная спецификация труб и деталей, из которых собирается элемент, с указанием материалов, со ссылками на ГОСТ, строительная длина элемента, длина патрубка.
Правообладателям!
Это произведение, предположительно, находится в статусе 'public domain'. Если это не так и размещение материала нарушает чьи-либо права, то сообщите нам об этом.