Текст книги "Практикум молодого технолога"
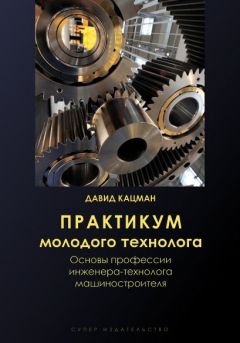
Автор книги: Давид Кацман
Жанр: Техническая литература, Наука и Образование
Возрастные ограничения: +16
сообщить о неприемлемом содержимом
Текущая страница: 2 (всего у книги 5 страниц)
Б. Повышение производительности прессовых операций (из заводского опыта)
Прессовые операции в общей трудоемкости сборочных работ занимают до 10 % и выше. Поэтому повышение производительности прессовых операций имеет существенное значение в вопросе роста производительности труда сборочных работ в целом.
На Кировоградском заводе «Гидросила» разработаны и применены на механизированных поточных линиях сборки агрегатов двигателя СМД 14 несколько оригинальных приспособлений, которые позволяют увеличить в 1, 5-2 раза норму выработки при работе на пневматических прессах прямого действия.
Эффект достигается за счет уменьшения хода штока пресса, совмещения вспомогательного и машинного времени и одновременного выполнения на прессе нескольких операций (запрессовка разноименных деталей).
При запрессовке двух подшипников на валик водяного насоса применяется откидное приспособление, особенностью которого является наличие специального окна в штоке пресса (см. рис.№ 1).
За один рабочий ход штока пресса одновременно запрессовываются два подшипника: № 304-нижний и № 305-верхний.
При обратном ходе, как только торец оправки 1 отходит от торца внутренней обоймы шарикоподшипника № 305, сборщик производит поворот приспособления на себя и совершает работу по снятию запрессованного валика и установке нового для повторения операции (конец валика выходит из оправки 1 за счет окна).
Достигнутая производительность труда на данной операции составляет 720 валиков в час.

Уменьшение хода штока пресса до минимума, а следовательно повышение производительности может быть достигнуто и за счет применения сдвоенных поворотных приспособлений (см. рис. № 2).
Здесь совмещено время запрессовки и время снятия собранного подузла и установки нового корпуса маслонасоса для повторения операции запрессовки валика. При обратном ходе штока производится поворот приспособления вокруг оси 2, далее цикл повторяется.

Еще более целесообразным является решение вообще исключить холостой ход пресса, используя движение штока вниз и вверх для выполнения полезной работы (см. рис.№ 3).
Конструкция специальной прошивки 3 позволяет производить запрессовку свертной втулки в крышку маслонасоса, при этом в запрессованной втулке внутренний диаметр уменьшается, и при обратном ходе штока прошивка калибрует внутренний диаметр втулки.
Примером запрессовки двух разноименных деталей может служить операция запрессовки втулки опорной и нижнего сальника в корпус водяного насоса (см. рис. № 4).

Особенностью конструкции приспособления является стойка № 4, которая предусматривает установку и базирование для выполнения операции запрессовки в корпус водяного насоса сальника и опорной втулки с окрашенной наружной поверхностью под запрессовку.
Запрессовка втулки опорной и сальника происходит за один рабочий ход штока пресса.

Установка для окраски втулки в работе связана с прессом. Она представляет собой автоматическое устройство, предназначенное для покрытия лаком или краской сравнительно узкой ленточки на образующей наружного диаметра детали.
При ходе штока пресса вниз включается в работу и автомат: срабатывает отсекающее устройство, втулка со штанги загрузочного устройства попадает на штырь механизма подачи.
Механизм подачи смещает втулку до упора в ведущий ролик, за счет сил трения втулка начинает вращаться и её наружный диаметр соприкасается с окрасочным диском, который непрерывно вращается в ванночке с краской.
При этом происходит покраска втулки.
При обратном ходе штока пресса все механизмы автомата возвращаются в первоначальное положение.
Рабочий снимает окрашенную втулку, устанавливает в корпус водяного насоса для запрессовки и цикл повторяется снова.
Таким образом, с механизацией процесса покраски втулки одновременно решился вопрос и высвобождения работника, который был занят на этой операции.
Условия труда на указанном рабочем месте значительно улучшились.
Авторами конструкции автомата являются инженеры тт. Барский В.А. и Бехман В. З.
Все описанные приспособления и устройства находятся в эксплуатации на заводе, техдокументация может быть выслана заинтересованным лицам и организациям через систему технической информации.
В. Клеймение и маркировка деталей и узлов в серийном производстве (опыт Кировоградского завода» Гидросила»)
Как известно, нанесение контрольного клейма на деталь или узел есть свидетельство соответствия детали, узла требованиям чертежа, техническим условиям.
Маркировка деталей, узлов проводится с целью определения оптимальных условий собираемости, конкретизации (отнесения) деталей и узлов к специфическим условиям изготовления, информации заказчика о заводе изготовителе и т. д.
К качеству продукции в соответствии с технической документацией, вновь введенными стандартами, вводятся дополнительные требования по нанесению на деталях и узлах четкой, рассчитанной на длительное время эксплуатации маркировки; при этом предусматривается 100 % клеймение и маркировка шестерен привода, деталей и узлов, идущих в запчасти, экспортной продукции.
С целью решения указанной задачи на Кировоградском заводе «Гидросила» внедрено электрохимическое клеймение шестерен, разбивка шестерен на группы, а также разработан метод маркирования деталей на пневматическом прессе с помощью накатного ролика, при этом процесс маркировки полностью механизирован.
Нанесение клейма электрохимическим способом не искажает клейменной поверхности, погрешность ничтожно мала, что дает возможность наносить клейма на чистовые поверхности торцов и цапф шестерен, такое невозможно при использовании электрогравировального способа или набивании клейм при помощи стальных пуансонов.
Клеймо просматривается на детали очень четко и может быть нанесено при приемке деталей после механической обработки до выполнения операции оксидирования – это исключает попадание на сборку бракованных деталей.
Метод электрохимического клеймения производителен, трудоемкость выполнения указанной операции падает в 1,5…2раза.
Ниже описана принципиальная схема пневматической установки для нанесения маркировки на венцах шестерен и торцах плоских стальных, чугунных деталей методом выкатывания стальным роликом.
Установка состоит из пневматического пресса прямого действия усилием 4…5 тонн, оправки накатного ролика и специального приспособления для установки маркируемой детали.
Индекса оснастки: ГМ 1978 – 00, пневмопресс 3, 5 тонн.
Г. Применение свертных втулок в серийном производстве на заводах сельхозмашиностроения (опыт завода «Гидросила» г. Кировоград)
В конструкции агрегатов двигателей (в том числе маслонасоса 14 – 09С2 – 1А к двигателям СМД14) предусмотрены бронзовые втулки в качестве подшипников скольжения.
Длительное время завод применял литые бронзовые втулки, которые получал по кооперации из Оренбургского завода «Тракторозапчасть».
Большой расход бронзы на один комплект, постоянные срывы кооперированных поставок поставили перед инженерно – техническими службами завода задачу: отказаться от литых втулок, перейти на самостоятельное производство свертных втулок взамен литых.
В содружестве с ПТИМАШ г. Харьков эта задача была успешно решена.
В настоящее время на заводе изготавливаются и применяются свертные втулки в конструкциях маслонасосов к двигателям СМД14 и СМД60, в гидронасосах серии НМШ.
Эффективность внедрения указанного мероприятия хорошо видна на примере маслонасоса 14-09С2-1А.
Норма расхода бронзы ОЦС 5-5-5 на один комплект до внедрения свертных втулок составляла – 0, 408 кг, после внедрения – 0, 095 кг.
Только за счет экономии дефицитного материала завод получает чистую прибыль в сумме 38 тыс. руб. в год. (по курсу рубля 1980 года).
Всего экономический эффект от внедрения двух наименований втулок в узле 14-09С2-1А составил 47 тыс. руб. в год.
1. Особенности конструкции маслонасосов со свертными втулками
В качестве материала для изготовления свертных втулок принята лента бронзовая полутвердая толщиной 1, 5 мм. – Бр ОЦС 4-4-2, 5 ПТ 1, 5х75.
Отверстия в корпусе, крышке и ведомой шестерне маслонасоса под запрессовку свертных втулок уменьшены с о26А до о22, 6А; одновременно проведена унификация ведущей и ведомой шестерен по о22, 6А.
Изменение наружного диаметра ведущего валика маслонасоса под запрессовку в шестерню с о26 на о22, 6 дало возможность использовать в качестве заготовки круг о25 вместо применяемого раннее круга о30, сталь 45.
При этом имела место унификация свертных втулок – осталось двa наименования свертных втулок вместо трех литых. Уменьшена в связи с этим длина ведущего валика с 108 мм. на 105 мм. В целом экономия черного проката составила 40 тонн в год.
Таким образом, внедрение свертных втулок положительно сказалось на конструкции узла. Надежность и долговечность маслонасосов со свертными втулками подтверждена более чем пятилетним сроком их эксплуатации.
2. Особенности технологии изготовления свертных втулок, конструкция штампов и оснастки для запрессовки и калибровки свертных втулок
Изучение опыта ряда заводов автомобильной промышленности (в сельхозмашиностроении свертные втулки еще не нашли широкого применения) показало, что применение штампов – автоматов для изготовления партий втулок нескольких наименований не всегда выгодно.
Завод остановился на следующей технологии:
а) вырубка карточек
б) гибка заготовки
в) калибровка втулок
В качестве оборудования используются пресса кривошипные усилием 50 т.с. модели К115А, КБ245.
Для вырубки карточек на заводе спроектирован штамп (см. рис 1), позволяющий вырубывать карточки с минимальными отходами.
Особенностью штампа является то, что вырубка производится не по всему периметру карточки, а только по трем сторонам, как показано на карте раскроя.
Это сокращает расход металла.
Вырубка производится следующим образом: полоса подается по направляющим съемника 1 до упора 2.
При рабочем ходе пуансон 3 производит вырубку карточки, а пуансон 4 измельчает отход.
Размер карточки по длине обеспечивается размером пуансона и является величиной постоянной.
Вырубленная карточка через отверстие в матрице и нижней плите попадает в ящик, а измельченный отход остается на плите пресса и удаляется отдельно.
Конструкция штампа позволяет автоматизировать подачу ленты, производительность штампа зависит от числа ходов пресса.
Гибка заготовки свертной втулки производится на штампе, изображенном на рис № 2.
Вырубленная заготовка устанавливается на пластинку 1, при рабочем ходе пресса клин 2 подводит ползун 3, который осуществляет предварительную гибку заготовки, затем ползуны 4 и 5 (последний на рисунке не показан) производят догибку заготовки вокруг пуансона 6.
При обратном ходе пресса ползуны под действием пружин возвращаются в исходное положение, а заготовка через отверстие в нижней плите падает в ящик.
Подача карточек в штамп осуществляется пинцетом.
При калибровке втулок по наружному диаметру (см. рис. № 3, № 4, № 5) применен штамп с твердосплавной матрицей, которая обеспечивает качество калибровки при высокой стойкости штампа.

Так как после гибки свертная втулка имеет диаметр больше требуемого чертежом, то конструкцией калибровочного штампа предусмотрен предварительный обжим заготовки ползуном 1 до окончательного размера.
При дальнейшем ходе ползуна вниз, пуансон 2 коническим пояском заходит в отверстие втулки, а торцом нажимает на торец свертной втулки и проталкивает её через твердосплавную матрицу 3.
Установка заготовки в штамп также производится пинцетом.



Много оригинальных идей в конструкции вышеуказанных штампов внесли конструкторы бюро оснастки ОГТ под руководством Ю.И. Меркотана.
Качество свертных втулок зависит от правильного выбора исполнительных размеров карточки.
Так как существенное влияние на выбор исполнительных размеров карточки оказывает твердость материала, а также допуск на толщину исходного материала – исполнительные размеры карточки назначаются после экспериментальных проверок втулок, изготовленных из карточек, полученных как по расчетным (теоретическим) размерам, так и имеющих соответствующие строго фиксированные отклонения в плюсовую и минусовую стороны.
С целью анализа сил необходимых для запрессовки и выпрессовки свертных втулок, проверки качества стыка, испытания проводились на разрывной машине марки УМ-5. Опытно – статистические данные показывают, что для втулок маслонасоса (диаметр отверстия под запрессовку свертных втулок 22, 6А) положительные результаты получены при размере карточки L = 67, 5 + 0, 3 и усилии запрессовки 600|1250
При этом исполнительные размеры втулки соответствуют требованиям чертежа: зазор по стыку в свободном состоянии до 2 мм; втулка от легкого удара деревянным молотком входит в калибр о22, 85.
Усилие выпрессовки свертных втулок выше, чем литых на 150 – 200 кг, что говорит о полном прилегании наружной поверхности втулки в отверстии.
У литой втулки наружная поверхность при запрессовке частично срезается и прилегание последней составляет 60..90 %.
Запрессовка свертных втулок производится на пневматических прессах прямого действия, максимально развиваемое усилие составляет 4 тонны.
При этом используется специальная прошивка, которая служит как для запрессовки втулки, так и для калибровки отверстия запрессованной втулки обратным ходом штока пресса.
Изготовление твердосплавных прошивок гарантирует качество калибровки при высокой стойкости инструмента.
Максимальный диаметр зубьев прошивки также назначается экспериментальным путем; в нашем случае с незначительной погрешностью на 0, 05 больше требуемого диаметра, получаемого при калибровке (за счет упругой деформации втулки происходит восстановление (уменьшение) отверстия после калибровки на указанную величину).
Припуск, оставляемый для последующей обработки 0, 15..0, 2 мм. на сторону, вполне достаточен для качественного выполнения операции расточки на алмазно – расточных станках, применяемых для расточки литых втулок
Выводы:
Описанная в книге технология изготовления и применения свертных втулок в конструкциях маслонасосов СМД14 и СМД60 проста, надежна и весьма эффективна.
Считать возможным рекомендовать более широкое применение свертных втулок в конструкциях сельхозмашин.
Техдокументация на указанные в статье штампы и другую оснастку, применяемую на заводе «Гидросила» в серийном производстве, может быть запрошена заинтересоваными лицами и организациями через систему технической информации.
Д. Получение заготовки валика водяного насоса методом поперечно – клинового проката с последующей обработкой на токарных автоматах
Линии механической обработки валиков водяного и масляного насоса являлись в цехе узким местом: росли плановые задания, увеличивалась номенклатура, а оборудования и площадей для его размещения в цехе не хватало.
Перед технологом была поставлена задача – увеличить план выпуска валиков в два раза.
Решить эту проблему можно было только за счет разработки и внедрения передовой технологии получения заготовок и использования высокопроизводительного оборудования.
На действующем производстве в качестве заготовок использовались штучные заготовки, получаемые рубкой из прутка.
В то же время уже существовал более прогрессивный метод получения заготовок валиков, – метод поперечно-клиновой прокатки.
Метод поперечно-клиновой прокатки – новая технология, которая позволяет изготавливать тела вращения переменного сечения любой конфигурации: сферические, цилиндрические, конические.
Стан поперечно-клиновой прокатки, примененный нами, позволил получать заготовки деталей вращения – валиков водяного и масляного насосов.
На чертеже ниже показана заготовка валика водяного насоса, полученная из прутка, заготовка со стана поперечно клинового проката, приближенная по конфигурации к готовой детали.
Нами был разработан чертеж заготовки со стана поперечной клиновой прокатки (см. эскиз ниже).
Первая проблема с которой мы столкнулись, – это перевод операции подрезки торцев и центровки новых заготовок на уже работающие в цехе токарные 6 – шпиндельные полуавтоматы с автооператором 1А240П-6.
С этой целью полуавтоматы были модернизированы, оснащены новыми спецпатронами.
Оригинальная конструкция патронов была спроектирована конструкторским бюро завода.
Для последующей обработки заготовок валиков был разработан и внедрен прогрессивный технологический процесс чернового и чистового шлифования трех поверхностей одновременно.
Были использованы технологические возможности нового шлифовального оборудования (станки модели 3М151Е, 3Т161).
До внедрения нового технологического процесса на каждой операции производилось шлифование одной поверхности, при этом отсутствовала автоматическая правка круга по копиру, поводковая оправка надевалась на деталь вручную; рабочий из-за необходимости постоянного контроля процесса шлифования обслуживал только один станок.
Внедрение нового технологического процесса потребовало решить следующие вопросы:
1. Применить шлифовальные круги шириной 100 мм.
2. Разработать специальную конструкцию
копиров для автоматической правки шлифовального круга, при этом шлифовальный круг повторяет конфигурацию трех поверхностей шлифуемой детали; точность шлифования каждой поверхности в пределах 2 класса и выше.
3. Разработать специальную конструкцию поводкового патрона, работающего в автоматическом режиме.
4. Применить приборы активного контроля с переводом работы станка в полуавтоматический режим.
Предложенная и внедренная в производство новая технология механической обработки валиков с использованием заготовки, полученной на стане поперечно – клиновой прокатки, расшила узкое место, увеличила производство валиков в 2 раза на существующих площадях, а внедрение полуавтоматического режима работы шлифовальных станков позволило улучшить условия работы шлифовщиков, механизировать ряд переходов, которые раньше выполнялись вручную, внедрить многостаночное обслуживание.
Получен большой экономический эффект за счет экономии металла, отказа от трудоемкой токарной обработки на гидрокопировальных станках и высвобождения 4 рабочих шлифовщиков.




Е. Разработка и внедрение технологии механизированной притирки торцов шайб водяного насоса к двигателям серии СМД
Анализируя качество двигателей Ярославского моторного завода, Харьковского моторостроительного обьединения «Серп и молот» и других предприятий страны, заказчики в числе немногих повторяющихся дефектов неизменно называют течь воды через контрольные отверстия водяных насосов.
Известно, что конструкция узла уплотнения водяных насосов включает в себя прецизионную пару, работающую в сложных условиях.
Основными элементами узла уплотнения водяных насосов к двигателям серии С М Д – являются шайба уплотняющая, которая представляет собой кольцо из специального материала, и втулка опорная, изготовленная из нержавеющей стали.
Шайба уплотняющая(рис.№ 1) имеет возможность свободно самоустанавливаться и прижиматься пружиной к торцу опорной втулки, она работает в контакте со втулкой на истирание в водяной среде при температуре 85-90 градусов.
Жесткие требования к конструкции уплотнения, исключающие допустимость течи воды, предъявляют соответственно высокие требования к чистоте и геометрии изготовления рабочих поверхностей шайбы уплотняющей и втулки опорной, что достигается специальными методами обработки.
Так, к шайбе уплотняющей предъявляют следующие требования – чистота поверхности 7-8 класса, непараллельность торцов до 00, 7 и неплоскостность, исключающая возможность появления течи воды через контрольное отверстие – основной параметр.
Материалом шайбы служит графитизированный текстолит, который на ряде предприятий заменен новым материалом НАМИ-ГС ТАМ – графитосвинцовая композиция. Графитометаллические шайбы имеют ряд преимуществ по сравнению с графитотекстолитовыми, но и не лишены недостатков: хрупкость материала, высокая стоимость. Поэтому на ряде предприятий, в том числе и на «Гидросиле», сохранены в производстве шайбы из графитизированного текстолита.
Высокая массовость производства водяных насосов разных модификаций поставила перед технологами задачу по отработке конструкции уплотняющих шайб на технологичность и по дальнейшему совершенствованию методов их обработки и контроля.
Работа шла по трем направлениям: уточнение требований чертежа, предъявляемых к рабочим поверхностям шайб, поиск путей стабильного обеспечения указанных требований в массовом производстве, разработка методов контроля, дающих возможность объективно оценивать качество обработанной поверхности. Совместно с головной организацией ГСКБД завода «Серп и молот» были уточнены и четко сформулированы требования, предъявляемые к точности изготовления и контроля уплотняющих шайб.
Метод контроля плоскостности рабочей поверхности шайбы уплотняющей на ВАЗе предусматривает использование профилометра.
Данный метод контроля плоскостности трудоемок, длителен по времени, поэтому на заводе в качестве основного метода выбран метод контроля по краске.
Результаты контроля плоскостности по краске зависят от метода нанесения краски на контрольную плиту и усилия прижима шайбы к контрольной плите, учитывая особенности материала шайб.
На заводе разработана технологическая инструкция, оговаривающая единые методы и средства для контроля неплоскостности и непараллельности торцов шайб с использованием специального приспособления (рис.№ 2), имитирующего работу шайбы в собранном узле (шайба прижимается к плите равномерно распределенным усилием 3кГс).
Предложен и внедрен способ проверки толщины слоя краски, нанесенного на контрольную плиту. Способ исключает субъективный подход и позволяет контролировать нанесение слоя краски на контрольную плиту в пределах 3 микрон. Разработана и внедрена прогрессивная технология обработки торцов шайб, на которой следует остановится подробнее.
Анализ технологических процессов чистовой притирки рабочих поверхностей шайб родственных предприятий показал, что данный процесс в основном производится в ручную – шайбу притирают на плоской плите, используется в качестве инструмента абразивный порошок, а также микропорошок М28 и керосин.
Большая трудоемкость ручной операции притирки, а также нестабильность качества поставили задачу – механизировать процесс притирки шайб из графитизированного текстолита и гарантировать при этом качество притирки в соответствии с требованиями чертежа детали.
На первом этапе решения указанной задачи в качестве предварительной операции на заводе внедрен специальный двух сторонний торцешлифовальный полуавтомат модели СА-2.
Станок обеспечивает высокую производительность при обработке заготовок шайб (600 штук в час), а также достаточно высокую точность – чистота 8 класса, неплоскостность до 0, 01 мм.
На втором этапе решен вопрос механизации чистовой притирки рабочих поверхностей шайб. Притирка осуществляется на сециальном двухдисковом притирочном станкеГМ-151 3А. Сущность процесса механизированной притирки торцов шайб заключается в следующем: притирка производится на чугунных дисках с использованием влагостойкой шлифовальной шкурки У216408МА.
Детали по 3 штуки укладываются в сепаратор и прижимаются сверху грузом через вставки специальной конструкции. (рис. № 3). Станок оснащен реле времени и работает в полуавтоматическом режиме. Производительность станка, имеющего 2 рабочих диска и 6 сепараторов (одновременно обрабатываются 18 деталей с одной стороны) – равна 150 штукам в час. Как одну из особенностей станка следует отметить конструкцию сепараторов, предусматривающих обработку 3 деталей и не имеющих традиционных пружин, которые заменены специальными стальными вставками (рис. 4).
Такая конструкция сепараторов позволила равномерно распределить усилие от груза на притираемую поверхность шайб и этим самым гарантировать качество притирки как по плоскостности, так и (после поворота детали) параллельности обрабатываемых поверхностей. Станок подключен к вытяжной вентиляции с целью очистки шайб и рабочей поверхности станка от абразивной пыли. Качественные показатели проведенной работы следующие: внедренный комплекс мероприятий гарантирует достижение плоскостности рабочих торцов шайб при проверке на краску (слой краски 0, 005 мм) в соответствии с требованиями чертежа при отклонении размера по толщине + – 0, 2 и непараллельности торцов до 0, 07 мм. Постановка в узлы уплотнения водяных насосов шайб притертых механизированным способом позволила сделать существенный рывок в решении проблемы качества изготовления водяных насосов к тракторным и комбайновым двигателям.


Правообладателям!
Это произведение, предположительно, находится в статусе 'public domain'. Если это не так и размещение материала нарушает чьи-либо права, то сообщите нам об этом.