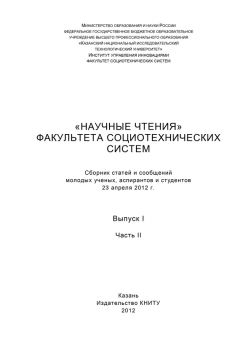
Автор книги: Коллектив Авторов
Жанр: Публицистика: прочее, Публицистика
сообщить о неприемлемом содержимом
Текущая страница: 8 (всего у книги 27 страниц) [доступный отрывок для чтения: 9 страниц]
Кранатов А.Е., гр. 3181-51, науч. рук. доц. Медведева В.Р.
Современные информационные технологии на примере ОАО «Авиакомпания «Татарстан»
Современную логистическую инфраструктуру невозможно представить без современных инструментов управления информационными потоками, в основе которых лежат информационные технологии. Наибольшим спросом в России сегодня пользуются системы управления складами (WMS), относящиеся к системам исполнения цепочек поставок. Среди существующих систем управления складами можно выделить три основных класса: 1) системы начального уровня; 2) системы среднего уровня; 3) комплексные системы. К системам начального уровня можно отнести большинство отечественных систем: в первую очередь, системы разработанные на основе 1С: Предприятие и систему ФОЛИО ЛогистикСклад 8.1. К сожалению, большинство таких систем с большой натяжкой можно отнести к системам WMS, так как они обладают только частью функциональности систем управления складами и реализуют только адресное хранение. Стоимость лицензий систем начального уровня, как правило, не превышает 15 тыс. дол.
К системам среднего уровня относят WMS с базовой функциональностью с заранее определенными возможностями настройки или с возможностью настройки под требования заказчика. К системам среднего уровня относятся Exceed 1000 компании SSA, Radio Beacon WMS Expert компании Radio Beacon, CoreWMS компании Аргус Софт. Стоимость лицензий таких систем обычно лежит в пределах 15-50 тыс. дол. в зависимости от количества пользователей.
К комплексным системам относятся полнофункциональные WMS с возможностью значительных модификаций под требования заказчика. Среди комплексных систем, представленных на российском рынке, можно выделить advantics компании PSI Logistics, Exceed 4000 компании SSA, Logistics Vision Suite компании Mantis, Radio Beacon WMS Enterprise, Solvo. WMS компании «Солво». Стоимость комплексных систем начинается от 50 тыс. дол. Нельзя не упомянуть системы собственной разработки и системы, полностью разработанные на заказ. Проекты, выполненные на базе продуктов этой группы, составляют примерно 10 % от общего числа проектов. Эти системы относятся скорее к системам среднего уровня, но такие разработки обходятся заказчику дороже приобретения комплексных систем. Проекты автоматизации складов, выполненные на базе комплексных систем WMS, составляют 54 %. Это связано, в основном, с тем, что основными потребителями таких систем на данном этапе рынка выступают крупные компании, требования которых можно удовлетворить только с помощью комплексных систем WMS.
Авиакомпания «Татарстан» является национальным авиаперевозчиком РТ, осуществляющим регулярные пассажирские перевозки как в города России и СНГ, так и в страны Азии и Европы. Для удобства использования электронного авиабилета авиакомпания внедрила в аэропортах «Казань», «Бегишево» и «Пулково» собственную автоматизированную систему регистрации SITA DCS, которая упрощает процедуру регистрации на рейс, позволяет быстро и без ошибок вести регистрацию пассажиров, оперативно обрабатывать и пересылать всю необходимую информацию о пассажирах и багаже, тем самым повышая качество обслуживания пассажиров.
В рамках автоматизации складской системы в компании внедрен программный комплекс «СОКОЛ». Данная система информационной поддержки предназначена для учета наличия, поступления и расхода авиационно-технических изделий в подразделениях АТК, для контроля за работой техников цехов и лабораторий, а также для оперативного контроля за местонахождением и состоянием агрегатов, находящихся в подразделениях АТК или на ремонтном заводе. Программный комплекс предназначен для использования в следующих подразделениях: обменный фонд; ремфонд; лаборатории АиРЭО; комплектовки; склады; цеха оперативного и периодического ТО; ОМТС (отдел логистики).
Основным объектом учёта паспортизируемых АТИ в системе является электронный паспорт агрегата. Электронный паспорт заводится на каждый агрегат, учитываемый в системе, и содержит следующую информацию: 1) основные технические данные; 2) ресурсы, сроки службы, срок хранения; 3) учет наработки (наработка агрегата с начала эксплуатации (СНЭ) на момент установки агрегата на соответствующее основное изделие и т.д.); 4) движение изделия в эксплуатации; 5) проведенные ремонты и доработки по бюллетеням и указаниям; 6) учет выполнения регламентных работ; 7) прочая информация (комментарий).
Все параметры агрегата, за исключением номера в АТБ, могут быть отредактированы пользователем. Поскольку уникальность номера в АТК гарантируется системой, этот номер удобно использовать для идентификации агрегата. Непаспортизируемые АТИ не имеют каких-либо индивидуальных учетных признаков. Для учета непаспортизируемых АТИ в каждом подразделении на каждую номенклатурную позицию заводится так называемая электронная карточка, содержащая информацию о количестве АТИ данного типа, имеющихся в наличии в подразделении, а также о месте хранения АТИ. Электронные карточки заводятся как на паспортизируемые, так и на непаспортизируемые АТИ. Прием и выдача запчастей осуществляется по электронным требованиям.
Как и любая информационная система, «СОКОЛ» подразумевает разграничение прав доступа у пользователей. Помимо общего разграничения доступа, комплекс «СОКОЛ» поддерживает также разграничение прав на уровне подразделения. Для каждого подразделения и для каждого пользователя можно указать, какие именно действия уполномочен выполнять данный пользователь в данном подразделении. Для каждого подразделения может быть заведен один либо несколько пользователей с правами администратора. Такие пользователи вправе выполнять любые действия от имени данного подразделения, а также исправлять информацию, введенную другими сотрудниками данного подразделения.
В разделе «Журналы» пользователь может просмотреть всю историю движения АТИ по текущему подразделению. В системе ведутся два журнала движения: журнал движения материальных ценностей и журнал движения агрегатов. Движение непаспортизируемых АТИ фиксируется только в первом журнале, движение агрегатов – в обоих, но принципы фиксации факта движения в этом случае будут различными. Журнал движения материальных ценностей ведется только в тех подразделениях, которые могут работать с непаспортизируемыми АТИ. Журнал движения агрегатов ведется во всех подразделениях.
Помимо журналов движения, в этом режиме пользователь может просмотреть архив электронных требований, а также протокол. В протоколе фиксируются все действия операторов. В протоколе комплекса «СОКОЛ» отражаются все действия, выполненные в рамках данного комплекса, а также действия с агрегатами, выполненные операторами ПДО. Если пользователь желает видеть только протокол текущего подразделения, он должен выбрать подразделение из выпадающего списка. Однако, при этом следует помнить, что некоторые действия – такие, например, как редактирование справочника номенклатуры – фиксируются в протоколе без указания кода подразделения, поскольку касаются всех подразделений в равной степени. Кроме того, в протоколе можно установить выборку по выполненной операции, по конкретному оператору, по диапазону дат, а также найти в протоколе все записи, содержащие заданную последовательность символов.
Режим «Номенклатура» предназначен для просмотра и редактирования справочника номенклатуры АТИ, учитываемой в системе. Справочник номенклатуры имеет два представления: иерархическое, основанное на номенклатурных группах и номенклатурных номерах, и линейное, основанное на шифрах типов агрегатов. Между этими двумя представлениями предусмотрена перекрестная навигация.
Следует отметить, что для успешного внедрения данного программного комплекса, потребовала модернизации существующая система складирования, а так же имеющиеся складские мощности. В частности, были заменены стеллажи и теперь, применяется система адресно-ячеечного хранения АТИ, что упрощает работу с ними. Еще одним несомненным преимуществом данной системы стал тот факт, что ИС «СОКОЛ» в состоянии самостоятельно генерировать «адрес», где будет храниться агрегат, причем делать это в соответствии с ассортиментом и номенклатурными позициями. Данная система позволила систематизировать и оптимизировать работу складского хозяйства в ОАО «Авиакомпания «Татарстан». Сократилось время на поиски агрегата, в случае возникновения или выявления у АТИ дефекта – система автоматически уведомляет об этом. Еще одним преимуществом данной системы является тот факт, что она так же поддерживает учет количества товаров, находящихся в настоящий момент на складе и отдел ОМТС имеет возможность наблюдать за ними в режиме реального времени.
Системы АУ обладают колоссальным потенциалом и уже сейчас, способны в значительной мере облегчить труд сотрудников департамента логистики на предприятии. Система складирования – это один лишь из возможных вариантов для внедрения АСУ. Однако, уже сейчас становится очевидным, что польза приносимая ими, в разы больше затрат, вызванных их внедрением.
Медведева В., Кисилев С.
Внедрение концепции «Бережливое производство» на российских предприятиях
В современных условиях модернизация производственной системы предприятия, представляет собой не капиталоемкий способ повышения производительности и качества, выступает одним из перспективных источников роста конкурентоспособности. Для понимания задач модернизации необходимо переосмыслить понятие «производственная система».
В это понятие входят абсолютно все процессы, операции, связанные с созданием ценности для потребителя, включая и те, что несут в себе потери. Производственная система – это и продажи и логистика, и финансовый блок, разработка новой продукции, коммуникации с потребителями, производственные процессы, закупки и т.д. Главным элементом в этой системе является человек, а все остальное – машины, механизмы и прочее, лишь поддерживают людей и процессы.
Основная масса отечественных предприятий ориентированы на модернизацию производственной системы с использованием японского опыта, известного как TPS – Производственная Система Тойота, которая считается общепризнанным эталоном организации производственных процессов. Производственная система Тойоты разрабатывалась в автомобильной компании Toyotа с 1945 по 1975 гг.
Эту систему стали изучать и копировать в Америке, в странах западной Европы, а в последние годы и в России. Западная адаптация японской производственной системы получила название Lean production или Lean manufacturing или просто Lean, то есть бережливое производство. Сейчас высокий потенциал трансформации производственной системы на основе японского опыта продемонстрировали не только японские, но и ведущие компании развитых стран.
Переход от обычного производства к бережливому производству знаменует полный пересмотр основ организации как производственных отношений внутри предприятия, так и отношениях с поставщиками и потребителями. Бережливое производство – это, прежде всего, современная управленческая философия борьбы с потерями.
В соответствии с концепцией «бережливого производства» всю деятельность предприятия можно классифицировать как: операции и процессы, добавляющие ценность для потребителя, и операции и процессы, не добавляющие ценности для потребителя. Следовательно, всё, что не добавляет ценности для потребителя, с точки зрения бережливого производства, классифицируется как потери, и должно быть устранено1919
Голяков С.М. Современные производственные системы предприятий // Проблемы взаимодействия хозяйствующих субъектов реального сектора экономики России: финансово-экономический социально-политический, правовой и гуманитарный аспекты. СПб., 2011.
[Закрыть].
Однако возникает вопрос: почему, после столь успешного опыта Тойоты, бережливое производство для многих предприятий России является трудной задачей? В одном интернет-опросе представлены ответы компаний, которые когда-то внедряли данную концепцию, но отказались от нее.
Компании пытались внедрить бережливые технологии, но отказались от этой затеи по разным причинам:
1) не получили быстрого обещанного эффекта;
2) не смогли справиться с сопротивлением персонала, то есть когда работы коснулись конкретных мастеров (рабочих), им не смогли объяснить их личную выгоду и вовлечь в процесс внедрения Бережливого производства, хотя весь управленческий персонал был обучен и полностью вовлечен;
3) не смогли самостоятельно продолжить освоение подхода после внедрения консультантами нескольких проектов на разных участках производства;
4) столкнулись с тем, что за каждым шагом скрывался еще дополнительный не видимый до того объем работ, когда дело дошло до реального внедрения;
5) кризис способствовал остановке преобразований;
6) привычная сложившаяся система управления стала непреодолимым препятствием для нововведений, поэтому предпочли оставить все как есть;
7) у руководства не хватило воли для продолжения работы по внедрению.
Однако, несмотря не приведенные выше проблемы внедрения данной технологии менеджмента на отечественных предприятия, все-таки стоит отметить, что по данным Института комплексных стратегических исследований, в настоящее время около трети российских компаний занимаются развитием своих производственных систем, опираясь на опыт компании Тойота, в основе которого лежит деятельность над непрерывным улучшением, что представлено на рис. 1.

Рис. 1. Модернизация существующих производственных систем
Прежде всего, активно осваивают методы «кайдзен» международные компании, работающие в России заводы Тойота, филиал финской компании «Нокиан Тайерс», компания «Форд» и др. Среди отечественных предприятий, успешно внедривших принципы TPS можно отметить «Группу ГАЗ», «РУСАЛ», «Ярославский завод дизельной аппаратуры» и «Иркутск энерго». Отдельные элементы TPS были внедрены на таких предприятиях, как «КАМАЗ», корпорация «ВСМПО-АВИСМА» (российская металлургическая компания), «АВТОВАЗ», «Магнезит», «ВАСО» («Воронежское Акционерное Самолетостроительное общество» и других. Некоторые из этих предприятий уже достигли определенных результатов2020
Юшманова Е.В. Опыт внедрения производственной системы ТОЙОТА (TOYOTA PRODUCTION SYSTEM – производственная система Тойоты) в российских компаниях [Электронный ресурс] / Е.В. Юшманова. – Режим доступа: http://www.buk.irk.ru/library/sbornik_09/ushmanova.pdf, свободный. – Проверено 2.04.12.
[Закрыть].
Компании, использующие концепцию «бережливое производство» не скрывают своих успехов, они гордятся своими результатами, не делая из них никакого секрета:
– производительность труда ежегодно растет на 20-25 %;
– время переналадки оборудования уменьшилось на 100 %;
– время производственного цикла сократилось на 30 %;
– уровень удовлетворенности потребителя повысился на 100 %;
– объемы незавершенного производства и запасов товарно-материальных ценностей ежегодно сокращаются на 10-15 %;
– оборачиваемость денежных средств увеличивается ежегодно на 10-15 %;
– разработана и поддерживается хорошая система мотивации персонала;
– участвуют во внедрении Бережливого производства у своих поставщиков.
В соответствии с вышеизложенным мы приходим к выводу, что внедрение концепции «бережливое производство» работает, позволяя предприятиям достигать высоких результатов при рациональной организации своей хозяйственной деятельности и несмотря на значительное число неудач, положительные примеры имеются. Поэтому мы считаем, что тем предприятиям, которые пока не смогли получить эффекта, не стоит отказываться от внедрения данной технологии менеджмента.
В связи с этим, для более полного понимания данной концепции хотелось бы выделить направления, которыми должна обладать организация для достижения минимальных затрат, то есть для достижения стратегических целей, которые позволяет достичь концепция «бережливое производство»:
1. Компетентными сотрудниками, которые умеют анализировать производственные операции и владеют методами повышения эффективности организации труда.
2. Деловыми партнерами и поставщиками, способными выполнять трудные задачи и способностью создавать условия, поддерживающие стремление персонала к непрерывному совершенствованию рабочих мест и операций.
3. Руководством, которое умеет принимать взвешенные, но твердые решения на пути преодоления препятствий, которые возникают при развитии культуры непрерывного повышения операционной эффективности.
4. Стандартизированными рабочими местами и операциями на базе выявленных и стабилизированных лучших способов выполнения работы.
5. Минимальным количеством управленческих уровней и максимальным делегирования полномочий на места, где и производится работа.
6. Рабочим управленческим инструментом выравнивания производства, что позволяет поддерживать стабильный производственный процесс с минимумом издержек при изменении объемов и частоты поступления заказов с рынка.
Также следует отметить, что концепция «бережливое производство» – это концепция, которую предприятие должно вводить в свою практику с целью минимизации затрат, присущих любому предприятию, начиная от хранения складских запасов до производственных потерь, что в свою очередь позволит оптимизировать весь процесс производства.
Рассмотрим примеры эффективного внедрения концепции «бережливое производство» на российских предприятиях. Например, на БРАЗе успешно используются многие инструменты TPS во всех направлениях деятельности предприятия: стандартизация (карты пошагового выполнения операций), система непрерывных улучшений (А3, технический аудит, командное решение наиболее значимых проблем), встроенный контроль качества, визуализация, организация процесса точно в срок, вовлечение персонала (сочетание стимулов и мотивов) и т.д.
Еще одна компания, внедрение TPS в которой проходит успешно, – это «Ярославский завод дизельной аппаратуры», один из ведущих производителей топливной аппаратуры в России. Необходимость внедрения на нем была обусловлена следующими факторами: необходимость обеспечения 20 % роста выпуска продукции для основных потребителей (Минского моторного завода (ММЗ), ОАО «КАМАЗ» и других предприятий, производящих дизельные двигатели); снижение себестоимости продукции в условиях жесткой конкуренции с импортом; поиск альтернативных вариантов повышения производительности труда (вместо дорогостоящих инвестиций в новое оборудование).
В ходе изменения производственной системы на «Ярославском заводе дизельной аппаратуры» были внесены изменения в организационную структуру предприятия: была создана Дирекция по организации производственной системы. Основные функции нового подразделения заключались в подготовке менеджеров, способных возглавить мероприятия по улучшению организации производства, в обучении начальников цехов, мастеров и операторов новым методам работы, в мотивировании персонала, а также в выполнении основного проекта – модернизации сборочных линий по выпуску продукции для основных потребителей.
Модернизация производственной системы на «Ярославском заводе дизельной аппаратуры» была разделена на три основных этапа.
Этап 1. Визуализация склада готовой продукции: выделены зоны хранения продукции по потребителям и модификациям изделий; высвободились складские площади, время отгрузки сократилось в 2 раза.
Этап 2. Модернизация линии по сборке продукции для ММЗ: создан поток единичных изделий с изменением расстановки оборудования и разделения операций между рабочими; после четырех месяцев преобразований была повышена производительность и снижена себестоимость продукции.
Этап 3. Модернизация линии по сборке продукции для КамАЗа: по образцу сборочной линии для ММЗ проведены аналогичные преобразования и получены высокие результаты.
Результатами изменения производственной системы, согласно принципам TPS, стали следующие показатели:
– выпуск в масштабах всего предприятия был увеличен на 20-25 % к 2006 г.;
– рентабельность производства выросла с 9 % до 19 %;
– затраты на перемещение оборудования окупились в течение месяца;
– общие затраты, включая оплату консалтинговых услуг, были покрыты за счет продаж, возросших в 2003-2005 гг. с 2,08 до 3,08 млрд. руб.
Также хотелось бы привести эффект от внедрения концепции «бережливого производства» на примере «Сбербанка», результатами внедрения которой стали: ускорение обслуживания почти на 40 %; сокращение перемещения сотрудников по офису; экономия составила млн. руб.
Также можно добавить результат внедрения концепции «бережливое производство» на примере нашего Татарстанского предприятия СоюзМаш («ПО Завод имени Серго» (POZIC). Только по результатам 2010 г. и начала 2011 г. по программе «бережливое производство» обучены более 800 чел., реализовано 5 проектов по оптимизации затрат, исключению потерь и повышению производительности в производстве, подано более 600 предложений по программе непрерывных улучшений «Кайдзен».
В 2011 г., они планируют снижение потерь в производственных и офисных подразделениях с предполагаемой суммой годового экономического эффекта от реализации мероприятия более 200 млн. руб. По словам министра Г. Ахмадеевой, СоюзМаш – первая компания в РТ, начавшая работать в данном направлении.
Приведенные выше примеры лишний раз подтверждают, что внедрение концепции «бережливое производство» на предприятии, дело реальное, но требующее усилий и времени, потому, что изменения требуют времени и не все можно внедрить сразу.
Таким образом, можно сделать вывод о том, что принципы производственной системы Тойоты являются достаточно универсальными и легко адаптируемыми и применяемыми на предприятиях различных отраслей экономики при соответствующей организации обучения персонала, а также при достаточно высоком уровне вовлеченности топ-менеджмента предприятия. На сегодняшний день внедрение принципов производственной системы Тойоты может считаться альтернативой дорогостоящим инвестициям, применимой во всех сферах бизнеса.
Правообладателям!
Данное произведение размещено по согласованию с ООО "ЛитРес" (20% исходного текста). Если размещение книги нарушает чьи-либо права, то сообщите об этом.Читателям!
Оплатили, но не знаете что делать дальше?