Текст книги "Большая энциклопедия техники"
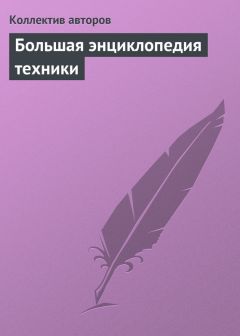
Автор книги: Коллектив Авторов
Жанр: Энциклопедии, Справочники
Возрастные ограничения: +12
сообщить о неприемлемом содержимом
Текущая страница: 23 (всего у книги 179 страниц) [доступный отрывок для чтения: 58 страниц]
Гайка
Гайка – крепежная металлическая (преимущественно) деталь, применяемая в резьбовых соединениях или винтовых передачах, имеющая отверстие с резьбой. Гайки подразделяются на:
1) обычные с шестигранной или четырехгранной внешней поверхностью;
2) корончатые, специальные (у таких гаек верх разрезной, напоминает корону властителей);
3) специальной конструкции для токарно-винторезных станков и различного оборудования, машин.
Гайки широко применяются во фланцевых соединениях запорной арматуры (вентилей, задвижек, клапанов и др.) на всех типах трубопроводов – магистральных, городских, внутриквартальных (в том числе на газонефтепроводах). Гайки изготавливаются из стали марок: 10, 20, 25, 35, 35 Х, 30 ХМА и 35 ХМА (сталь подбирается в зависимости от рабочего давления и температуры среды, перекачиваемой по трубопроводам). Высота гаек обязательно учитывается при монтаже фланцевых соединений, например при рабочем давлении в трубопроводе более 4 МПа применяют гайки высотой, равной диаметру болта, т. е. если болт крепежный имеет диаметр в 24 мм, то высота гайки должна быть равной 24 мм. Гайки также широко применяются при креплении колес к оси грузовых машин, тракторов, троллейбусов и легковых автомобилей. Размеры гаек обозначаются так: М 10 (10 – диаметр в мм), М 12, М 14 и т. д. Гайки применяются и в постоянных соединительных муфтах, в частности в шарнирных асинхронных крупногабаритных муфтах, устанавливаемых в трансмиссии автомобилей.
Гибкий вал
Гибкий вал – вал, обладающий малой жесткостью на изгиб и большой жесткостью на кручение, предназначенный для обеспечения передачи вращения между звеньями с изменяемым положением осей вращения. Чаще всего гибкий вал применяют в приводе ручных машин. Такой вал состоит из свитой в несколько слоев проволоки, заключенной в гибкую защитную оболочку – броню. Оболочка или броня выполняется невращающейся и прикреплена к корпусу привода с одной стороны и корпусу исполнительного устройства с другой стороны. Свитая проволока (т. е. гибкий вал) соединяет вал привода и вал исполнительного устройства. Гибкие валы подразделяются на валы правого вращения – у него проволоки наружного слоя навиты в левую сторону, и левого вращения – проволоки навиты в правую сторону. Данные валы изготавливаются трех типов: В1 (диаметры от 6 до 30 мм, а диаметры сердечников от 0,7 до 2,5 мм), В2 (диаметры от 3 до 8,2 мм, сердечников – от 0,33 до 0,5 мм) и В2-А (диаметры от 3,3 до 5,3 мм, сердечника – 0,5 мм). (Примечание: после навивки валов диаметром от 10 до 30 мм сердечник извлекается, согласно требованиям технологии и стандарта или технического регламента.) Валы типа В1 применяются для силовых приводов, т. е. для передачи сравнительно больших крутящих моментов, валы типа В2 – для несиловых приводов систем управления и контроля, например для приводов автомобильных приборов. Для изготовления гибких валов В1 и В2 применяется проволока пружинная классов П и В. Гибкий проволочный вал работает в гибкой броне (т. е. гибкой оболочке). Броня подбирается в соответствии с требованиями эксплуатации и должна быть:
1) податливой при изгибе вала в пределах допускаемой кривизны;
2) прочной и выдерживать перегрузки при изгибе вала сверх нормы;
3) герметичной во избежание загрязнения вала и просачивания смазки.
Нормальная броня Б1 представляет собой рукав, свернутый из стальной профилированной ленты, образующей своеобразный замок, в котором для уплотнения соединения прокладывается асбестовый или хлопчатобумажный шнур. Более прочная и более износостойкая усиленная броня Б2 имеет дополнительно внутреннюю спираль из стальной ленты овального поперечного сечения или спираль из сплющенной проволоки. В некоторых случаях броня покрывается оплеткой из тонкой оцинкованной стальной проволоки. При повышенных требованиях потребителей к герметичности брони оплетка покрывается слоем вулканизированной резины с кордными прослойками. В автомобильной промышленности принята двухпроволочная броня. Размеры брони выбираются в соответствии с диаметром вала. Во многих случаях материалом брони служит оцинкованная лента, изготовленная из стали 08 или 10. В тех условиях эксплуатации, когда форма оси гибкого вала не изменяется в значительных пределах, броня заменяется стальной (из мягкой рядовой стали – 0; 3; 5), медной или дюралюминиевой трубкой. В своем комплекте гибкие валы имеют специальную арматуру, предназначенную для присоединения концов данного вала к двигателю, прибору или инструменту. Съемная арматура присоединяется к валу специальным цанговым зажимом, а несъемная – при помощи штамповки или пайки. При пайке используется оловянно-свинцовый припой марки ПОС-18. Широко распространена арматура для гибких валов с бронзовыми вкладышами. При установке гибкого вала его концы впаиваются в расточки шпинделей, а броня – в муфты.
Гиперболоидная передача
Гиперболоидная передача – зубчатая передача со скрещивающимися осями, аксоидные поверхности зубчатых колес которой – однополосные гиперболоиды вращения. Гиперболоидные передачи подразделяются на два вида:
1) гиперболоидная передача первого ряда – передача, в которой сопряженные поверхности зубьев зубчатых колес могут быть образованы в станочном зацеплении общей для них производящей поверхностью;
2) гиперболоидная передача второго рода – передача, зубчатые колеса которой будут иметь сопряженные поверхности зубьев с линейным контактом, если производящая поверхность для одного из них совпадает с главной поверхностью зубьев парного зубчатого колеса.
Гипоидная передача – разновидность гиперболоидной передачи, у зубчатых колес которой начальные и делительные поверхности конические. Гипоидная передача подразделяется на два вида:
1) гипоидная передача первого рода имеет сопряженные поверхности зубьев, образованные в станочном зацеплении общей для них производящей поверхностью;
2) гипоидная передача второго рода имеет сопряженные поверхности зубьев с линейным контактом, если производящая поверхность для одного из колес совпадает с главной поверхностью зубьев парного зубчатого колеса.
Зубья колес для гипоидной передачи второго рода обычно выполняют тангенциальными или круговыми. Кроме того, у противоположных боковых поверхностей зубьев выполняют различные профильные углы. Для первой шестерни принимают угол наклона линии зуба β1 = 45—50°, а для второго колеса – β2 в пределах от 23 до 25°. Гипоидная передача второго рода характеризуется высокой несущей способностью и плавностью работы благодаря большому приведенному радиусу кривизны и большому коэффициенту перекрытия.
Главная передача
Главная передача – основная передача в системе нескольких передач от одного двигателя (электрического или двигателя внутреннего сгорания). Такая передача, например, имеется в токарновинторезном станке, где от одного электродвигателя через гитару станка осуществляется несколько передач: передача к шпинделю станка (это главная) и передача на вал (винтовой) подачи суппорта (на котором закрепляется инструмент). Главные передачи выделяются во многих автомобилях и тракторах, где применяется целая система передач от двигателя внутреннего сгорания к исполнительным органам. Главные передачи имеются также в тепловозах, троллейбусах и трамваях.
Глобоидная передача
Глобоидная передача (от лат. globus – «шар» и греч. eidos – «вид») – разновидность червячной передачи, у которой делительная поверхность червяка образована вращением вокруг оси червяка вогнутого отрезка дуги делительной окружности парного червячного колеса, лежащей в плоскости его торцового сечения. Последняя содержит межосевую линию червячной передачи, делящую отрезок дуги пополам, а делительная поверхность червячного колеса – цилиндрическая. У ортогональной глобоидной передачи оси скрещиваются под прямым углом, а делительная поверхность червяка является частью вогнутой поверхности тора. Теоретическая поверхность витка глобоидного червяка может быть образована линией, которая лежит в плоскости торцового сечения парного колеса и через которую проходит межосевая линия червячной передачи, при вращении ее вокруг осей червяка и колеса с отношением их угловых скоростей ω1 и ω2, равным передаточному числу червячной передачи. Различают линейчатые и нелинейчатые глобоидные червяки, теоретические поверхности витков которых образованы соответственно прямой и кривой линиями. Глобоидная передача по сравнению с червячной цилиндрической передачей имеет более высокие показатели в отношении несущей способности и коэффициента полезного действия (КПД) из-за благоприятных условий для гидродинамической смазки. Но глобоидная передача сложна в изготовлении, чувствительна к погрешностям монтажа и деформациям звеньев. Применяют чаще всего глобоидную передачу с модифицированным глобоидным червяком, который характеризуется продольной модификацией витка. Последняя представляет собой отклонение линии поверхности витка червяка от его теоретической линии по определенной зависимости. Продольная модификация позволяет локализовать контакт витка червяка с зубьями колеса и повысить качественные показатели глобоидной передачи. Наибольшим передаточным отношением глобоидной передачи может быть 63, при этом коэффициент полезного действия составляет от 0,6 до 0,9.
Гребенка
Гребенка – часть какого-либо механизма станка, сельскохозяйственной машины, похожая по форме на элементарную бытовую гребенку – расческу. Гребенка в механизме представляет собой металлическую с зубьями рейку определенной длины, по которой осуществляет поступательно-возвратное движение зубчатое колесо, закрепленное жестко на оси специального устройства, например, распределителя-дозатора (в частности, кормов в кормораздаточном устройстве на сельскохозяйственных фермах). Гребенки часто устанавливаются на автоматических линиях в поточном производстве каких-либо мелких деталей.
Грейфер
Грейфер (от нем. Greifer, Greifen – «хватать») – грузозахватный механизм с поворотными «челюстями»-захватами груза (в основном сыпучих строительных материалов в виде песка, щебня, гравия, мраморной или гранитной крошки). Грейфер изготавливается и применяется в пяти вариантах.
Вариант первый: грейфер подвешивается на канате к грузоподъемной машине. К траверсе этого механизма шарнирно присоединены две тяги, на которых подвешены соответственно металлические челюсти-захваты. Челюсти между собой соединены шарнирно посредством специального звена, подвешенного на замыкающем канате. При ослабленном канате челюсти под действием веса грейфера и собственного веса раскрыты. Закрытие челюстей и соответственно захват груза осуществляется натяжением замыкающего каната. Закрытый грейфер с грузом перемещают в нужном направлении при натяжении обоих канатов (т. е. основного и замыкающего). Ослабление замыкающего каната приводит к раскрытию челюстей и удалению груза (т. е. высыпанию сыпучего материала в кузов автомобиля-самосвала или в полувагон железнодорожный). Все указанные операции выполняются с помощью специальных грейферных лебедок.
Вариант второй: челюсти грейфера соединены между собой шарнирно, а также посредством двух звеньев. Все звенья грейфера в общем итоге образуют замкнутый симметричный четырехзвенный шарнирный механизм (в частном случае указанный механизм имеет вид ромба). Нижний шарнир «ромба» закреплен на основном канате. В данном варианте раскрытие челюстей грейфера происходит под действием их веса, а закрываются они с помощью полиспаста. Замыкающий канат, перекинутый через блоки (один расположен в верхней части грейфера, а два – в верхних частях челюстей), стягивает челюсти и при этом осуществляется захват груза.
Вариант третий: грейфер подвешивается на одном канате, а управление челюстями производится с помощью специального привода, установленного на траверсе. От электродвигателя через три зубчатых колеса поворачиваются челюсти, захватывая груз или освобождая его.
Вариант четвертый: грейфер предназначен для погрузки-выгрузки бревен (коротких – от 6 до 8 м), имеет крюки для захвата бревен.
Крюки шарнирно связаны с траверсой и управляются с помощью двух гидроцилиндров. Траверса подвешена на основном канате (на этом же канате держится весь грейфер). Гидроцилиндр левый и звено-крюк относительно траверсы образуют кулисно-коромысловый механизм. С помощью гидроцилиндров осуществляется захват крюками бревен и их освобождение (т. е. выгрузка-погрузка).
Вариант пятый представляет собой многочелюстной грейфер, управляемый одним гидроцилиндром. Все челюсти связаны с траверсой, подвешенной на основном канате, соответственно посредством трех тяг (две из них соединены с траверсой шарнирно). Челюсти грейфера шарнирно соединены также со звеном (центральным), перемещаемым посредством гидроцилиндра во время захвата груза и его освобождения (т. е. во время погрузки-выгрузки груза). Грейферы всех типов широко применяются при выполнении погрузоразгрузочных работ в различных отраслях промышленно-хозяйственного комплекса России.
Грейферный механизм
Грейферный механизм – устройство для циклического протягивания перфорированной ленты (в частности, киноленты в кинопроекторах или в кинокамерах). Такой механизм осуществляет прерывистое однонаправленное движение. В качестве грейферного механизма применяются кулисный механизм, зубчато-рычажные механизмы и др.
В кулисном (грейферном) механизме – кулиса, совершающая качательное движение, взаимодействие через шатун с вращающимся кривошипом. Шарнирно с кулисой связана собачка. Силовое взаимодействие этих звеньев осуществляется также через листовую пружину. В целом указанные звенья образуют своеобразный механизм свободного хода. При движении кулисы в одном направлении собачка отжимается и проскакивает через отверстия в перфорированной ленте. При движении в другом направлении собачка захватывает и протягивает ленту.
В зубчато-рычажном механизме (грейферном) два зубчатых колеса, зацепляющихся между собой, приводят в движение соответственно два шатуна, соединенные между собой и с зубчатыми колесами. Образованный таким образом пятизвенный зубчато-рычажный механизм обеспечивает движение одного шатуна, при котором он зацепляется с перфорированной лентой и протягивает ее в одном направлении, а затем отходит от ленты и движется свободно, после чего цикл повторяется.
В некоторых установках (кинотехнических) применяется и другой вид зубчато-рычажного грейферного механизма. В таком механизме выполнено соединение зубчатой пары с кулисой, имеющей криволинейную направляющую. Во время работы механизма кулиса выполняет определенную траекторию, на которой имеется участок, близкий к прямолинейному, на котором кулиса взаимодействует с перфорированной лентой, при этом происходит ее циклическое протягивание.
Дебаланс
Дебаланс – устройство, предназначенное для возбуждения механических колебаний, является инерционным элементом. Дебаланс также определяют как вибровозбудитель. В различных механизмах дебалансы устанавливаются по одному или несколько штук, соответственно существуют разные варианты исполнения:
1) дебаланс представляет собой вращающееся неуравновешенное звено, передающее центробежную силу на подшипники своего вала. В этом варианте дебаланс связан с валом электродвигателя посредством пружины. При вращении вала двигателя пружина под действием силы инерции «F» сжимается и центр массы дебаланса смещается на величину «е». Изменение направления силы инерции «F» обуславливает механические колебания дебаланса с частотой вращения вала электродвигателя;
2) дебаланс с электродвигателем установлен на маятнике специальной конструкции. В свою очередь маятник соединен с корпусом шарнирно и поджат с обеих сторон пружинами. В данном варианте дебаланс одночастотный, но он характеризуется определенным законом изменения возмущающей силы. Вертикальная составляющая силы изменяется по закону Fn = Fn sin ω t sin ψ, где Fn – сила инерции, развиваемая дебалансом, ω – угловая скорость составного звена, t – время, ψ – угол отклонения маятника от вертикальной линии;
3) дебалансы связаны зубчатой парой. В таком варианте механические колебания направлены строго вдоль вертикальной оси, потому что вертикальные составляющие сил инерции F1 и F2 направлены всегда в одну сторону, а горизонтальные составляющие – в разные стороны; при этом последние взаимно уравновешиваются. Дебалансы всех видов широко применяются в вибрационных механизмах, машинах, используемых во многих отраслях промышленно-хозяйственного комплекса России.
Дезинтегратор
Дезинтегратор (от фр. des – приставка, означающая отрицание, уничтожение, удаление или отсутствие чего-либо, и лат. integer – «целый»).
I. Машина для мелкого дробления (грубого измельчения) хрупких малоабразивных материалов. Состоит из двух вращающихся в противоположные стороны роторов (корзин), насаженных на отдельные соосные валы и заключенных в кожух.
На дисках роторов по концентрическим окружностям расположены 2—4 круглых металлических цилиндрических пальца – так называемых бил (от слова бить), бичей.
II. Установка для разрушения микроорганизмов с целью изучения субклеточных структур и получения биологически активных веществ:
1) белков;
2) полипептидов;
3) аминокислот;
4) ДНК или РНК при производстве бактерийных препаратов и др.
По принципу действия подобные дезинтеграторы подразделяются на:
1) баллистические;
2) ультразвуковые;
3) экструзионные и др.
III. Аппарат для очистки газов от взвешенных твердых частиц в виде пыли; применяется главным образом в доменных цехах металлургических производств.
Делительная головка
Делительная головка – устройство, применяемое для установки, закрепления и периодического поворота или непрерывного вращения небольших заготовок, обрабатываемых на фрезерных станках. В инструментальных цехах машиностроительных предприятий используются делительные головки оптические для угловых измерений, делительных работ и угловой разметки при обработке сложных и точных деталей технологической оснастки. Советскими предприятиями в 70—80-х гг. ХХ в. выпускались делительные головки четырех типов: ОДГ-2, ОДГ-5, ОДГ-10 и ОДГ-60 с ценой деления 2”, 5”, 10" и 60”. Конструктивно оптические делительные головки различались только оформлением оптической системы. Делительная головка оптическая устроена следующим образом: внутри неподвижного корпуса находится другой подвижный корпус, в подшипниках которого может поворачиваться шпиндель.
На шпинделе жестко укреплены лимб и червячное колесо. На конце шпинделя имеется коническая полость, в которую вставлен центр с хомутиком или иное крепежное приспособление (патрон, планшайба). Шкала лимба освещается источником света. Отсчетное устройство может быть экранным или окулярным. В поле зрения окуляра находятся изображения шкал лимба и нониусного устройства. Измеряемая деталь соединяется через поводок с центром. На машиностроительных предприятиях России широко применяется при обработке небольших заготовок делительная головка универсальная с пневматическим цанговым зажимом. Шпиндель такой головки устанавливается на столе фрезерного станка в вертикальное или горизонтальное положение. Данная делительная головка имеет корпус с пневмоцилиндром, крышку, полый шток, на котором установлены поршень и подшипник.
Механизм для закрепления обрабатываемой заготовки (или детали) состоит из втулки с внутренним конусом и винта, который соединяет шток с втулкой, упорную гайку и цангу. Закрепление обрабатываемой заготовки в делительной головке универсальной происходит следующим образом:
1) сжатый воздух через штуцер по каналу распределительного клапана попадает в полость «Б» и перемещает поршень со штоком и втулкой влево;
2) втулка, перемещаясь по конической поверхности цанги, сжимает ее и закрепляет заготовку.
Раскрепление заготовки осуществляется после того, как сжатый воздух по другому штуцеру поступает в полость «А». Одновременно воздух из полости «Б» выходит в атмосферу. Поршень со штоком и втулкой отходит вправо, усилие с лепестков цанги снимается и заготовка освобождается. При необходимости с помощью специальной рукоятки шпиндель универсальной делительной головки с заготовкой можно повернуть на заданный угол, после чего продолжить обработку заготовки.
Дисмембратор
Дисмембратор – разновидность дезинтегратора, представляет собой машину, у которой имеется один ротор, а вместо второго ротора – неподвижные пальцы (металлические, стальные), укрепленные на откидной крышке кожуха. Дисмембраторы называют иногда бильными или бичевыми мельницами.
Такие машины применяют для дробления полезных ископаемых (уголь, сера, доломит, мрамор, базальт, торф и др.); продуктов химической промышленности (твердая резина – получают резиновую крошку), сухих пигментов (охра, сурик); материалов деревообрабатывающей промышленности (отходы древесины, щепа и др.).
Правообладателям!
Данное произведение размещено по согласованию с ООО "ЛитРес" (20% исходного текста). Если размещение книги нарушает чьи-либо права, то сообщите об этом.Читателям!
Оплатили, но не знаете что делать дальше?