Текст книги "Большая энциклопедия техники"
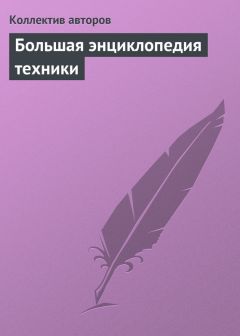
Автор книги: Коллектив Авторов
Жанр: Энциклопедии, Справочники
Возрастные ограничения: +12
сообщить о неприемлемом содержимом
Текущая страница: 31 (всего у книги 179 страниц) [доступный отрывок для чтения: 58 страниц]
Муфта
Муфта (от нем. Mufte или голл. mouwtje) – устройство для соединения валов, тяг, труб, канатов и т. п. Муфта, в частности, воспринимает осевые силы при соединении трубопроводов. Ее выполняют в виде втулки с резьбой. Муфту для передачи вращающего момента выполняют нерасцепляемой постоянной; компенсирующей или подвижной, а также сцепной. Постоянная муфта представляет собой втулку, надетую на концы соединяемых валов или жестко соединенные детали, закрепленные на концах валов. Компенсирующая муфта позволяет соединить валы, оси которых установлены с погрешностью, например, несоосны или пересекаются. К таким муфтам относят упругую муфту, зубчатую компенсирующую муфту. К подвижным муфтам относят шарнирную муфту; муфту типа «универсальный шарнир» (таковой, в частности, является карданный механизм или просто кардан); синхронную сферическую муфту. Подвижная муфта позволяет соединять валы с пересекающимися осями под большим углом по сравнению с компенсирующей муфтой. Сцепная муфта позволяет соединять и разъединять валы принудительно в процессе вращения, при остановке или автоматически, в зависимости от параметров движения или нагрузки.
Сцепные муфты (или управляемые соединительные муфты) подразделяются на кулачковые (зубчатые), фрикционные; электромагнитные жидкостные; порошковые.
Кулачковые муфты характеризуются тем, что передача крутящего момента производится за счет нормальных сил N между рабочими поверхностями. Данные муфты осуществляют жесткое соединение валов при определенных угловых положениях одного вала относительно другого. Преимущества кулачковых муфт перед фрикционными – малые габариты, простота конструкции и изготовления, дешевизна (что очень важно в условиях рыночной экономики России). Недостаток – недопустимость включения на быстром ходу без соответствующих мер предосторожности против удара.
Фрикционные муфты передают крутящий момент за счет сил трения между рабочими поверхностями, допускают включение на ходу без каких-либо мер предосторожности. Различают следующие типы фрикционных муфт: дисковые, у которых рабочими поверхностями являются торцовые плоскости дисков; конусные, у которых рабочими являются конические поверхности; кольцевые и колодочные, у которых рабочими являются цилиндрические поверхности.
Кроме того, фрикционные муфты по условиям работы разделяются на: сухие, применяемые в таких местах, где можно надежно предохранить муфту от попадания смазки; масляные, работающие в условиях обильной смазки. Фрикционные муфты обычно ставят на быстровращающихся валах кинематической цепи. Электромагнитные жидкостные и порошковые муфты в основном применяются в качестве сцепных для соединения и разъединения валов; они характеризуются тем, что способны передавать крутящий момент при отсутствии скольжения; допускают более длительное проскальзывание на переходных режимах; имеют меньшее время срабатывания и требуют меньшей мощности тока возбуждения, чем дисковая фрикционная муфта с электромагнитным управлением. Принцип действия муфт этого типа основан на свойстве жидкой или порошкообразной ферромагнитной смеси увеличивать под действием магнитного поля свою вязкость и прочно приставать к полюсам магнитной системы. Во многих механизмах применяются также муфты скольжения гидродинамические и электромагнитные вихревые. Гидродинамическая муфта скольжения обеспечивает более мягкий привод машины, хорошо гасит крутильные колебания, облегчает работу двигателя на переходных режимах. При пуске тяжелых машин от асинхронного короткозамкнутого электродвигателя данная муфта сокращает длительность действия большого пускового тока, а также ограничивает нагрев двигателя. Гидродинамические муфты наиболее широко применяются в транспортных устройствах с двигателями внутреннего сгорания из-за плохой характеристики этих двигателей на малых оборотах. Электромагнитная вихревая муфта используется в основном как сцепная муфта, допускающая значительное проскальзывание, или как средство изменения числа оборотов ведомого вала.
Гидродинамические и электромагнитные вихревые муфты имеют такое существенное отличие от фрикционных, как возможность продолжительной их работы с большим скольжением без быстрого нагрева и износа отдельных поверхностей муфты. Во второй половине ХХ в. широкое распространение получили более эффективные самоуправляемые муфты, в основном такие, как муфты обгона или свободного хода, производящие переключение в зависимости от того, с какого вала на какой передается крутящий момент и движение, и в зависимости от направления передаваемого момента; центробежные, производящие соединение и разъединение валов в зависимости от скорости их вращения; однооборотные, производящие разъединение валов механизмов через каждый оборот в определенном угловом положении ведомого вала; предельного момента, производящие разъединение валов при достижении установленной величины момента. Такие муфты определяются также как предохранительные – они разъединяют валы механизма при возрастании крутящего момента или скорости вращения выше допустимого значения.
Натяжной ролик
Натяжной ролик (см. ранее «Леникс») – блок или колесо, характеризующиеся свободным вращательным движением, предназначенные для регулировки натяжения ведомой части канатной или ременной передачи. Ненагруженный холостой шкив также используется для повышения угла обхвата малого шкива ременной передачи. Передачи с натяжным роликом необходимы для малых межосевых дистанций, а также в случае больших передаточных чисел. Фиксируется такое устройство на ведомой ветви ремня рядом с малым шкивом. Главным отрицательным моментом введения натяжного ролика является снижение срока эксплуатации ремня как следствие полученного вспомогательного перегиба.
Ниппель
Ниппель – соединительная трубка из металла с резьбой для плотного присоединения деталей или частей приборов.
Производятся, главным образом, латунные и бронзовые ниппеля, медные ниппеля изготавливаются довольно редко.
Нория
Нория (исп. noria от араб. наора – «водокачка») – механизм, представляющий собой черпаковый подъемник, транспортирующее устройство непрерывного действия с тяговым органом (в виде ленты или цепи), расположенный наклонно или вертикально, на котором подвешены черпаки для захвата и перемещения сыпучих грузов или жидкостей на высоту до 60 м.
Нория широко применяется в пищевых, мукомольных, химических производствах для перемещения сырья и готовой продукции между этажами внутри производственных зданий, при этом такое устройство часто называют ковшовым элеватором.
Оправка
Оправка – специальное токарное приспособление, применяемое, как правило, при обработке наружных поверхностей. Обрабатываемая деталь базируется по внутренней поверхности.
Применяются оправки следующих видов:
1) жесткие;
2) самозажимающие зажимные;
3) разжимные;
4) пружинящие.
По форме установочной поверхности оправки могут быть цилиндрическими, коническими, резьбовыми или шлицевыми. Жесткая цилиндрическая оправка устанавливается в центрах токарновинторезного станка (или другого вида станка). Обрабатываемая деталь, закрепленная на оправке (жесткой), удерживается от проворачивания трением, которое создается на ее торцах, с помощью шайбы и крепежной гайки. Разжимная оправка имеет простую конструкцию, вместе с ней применяется разрезная упругая гильза (так называемая цанга), имеющая наружную цилиндрическую и внутреннюю коническую поверхности. Гильза надевается на конический стержень оправки, при этом, чтобы гильза обладала упругими свойствами, на ней сделано шесть продольных прорезей. Обрабатываемая деталь закрепляется гайкой. С помощью второй гайки гильза вместе с деталью (после обработки) снимается с оправки. Разжимные оправки менее точны, чем жесткие, но в некоторых случаях их применяют для чистовой обработки деталей типа колес и втулок, в сочетании со специальной конической пробкой, которая вгоняется в корпус оправки легкими ударами молотка, разжимает ее и тем самым закрепляется обрабатываемая деталь, надетая на правую часть оправки с тремя продольными прорезями. Чаще всего для чистовой обработки деталей используется оправка с гидропластом, корпус ее крепится к планшайбе (планшайба – специальное токарное приспособление). В данном случае на корпусе оправки напрессована в нагретом состоянии разжимная втулка, на которой для лучшего уплотнения в местах посадки сделаны кольцевые углубления. В каналах корпуса и в цилиндрической полости между корпусом и втулкой расположен гидропласт. Под действием давления, сообщаемого с помощью винта через поршень гидропласту, втулка (разжимная) расширяется, центрируя и закрепляя деталь. При токарной обработке заготовок или деталей некруглой сложной формы применяются оправки-угольники. В корпусе такой оправки имеется специальная полка для угольника. Оправка-угольник крепится к планшайбе крепежными болтами.
Ось
Ось – деталь какого-либо механизма, не передающая вращающего момента, а воспринимающая только поперечные нагрузки. Ось выполняется в виде металлического стального стержня, который устанавливается в опорах и предназначается для поддержания и обеспечения вращения деталей, установленных на нем. Ось в отличие от вала не передает вращающего момента, но так же как и вал, передает на опоры радиальные и осевые силы. Ось может быть неподвижной или вращающейся. В первом случае детали установлены на ней так, что могут вращаться подобно колесу повозки или телеги, а ось испытывает только постоянные, по знаку напряжения, пропорциональные нагрузки. Во втором случае детали жестко закреплены на ней, а ось испытывает знакопеременные напряжения. Конструкция соединения оси с насаженными на нее деталями выбирается в соответствии с величиной и характером передаваемых ими нагрузок и требуемой точностью центрирования насаженных деталей. Для изготовления осей используются углеродистые легированные стали, применяемые в виде проката или поковок, реже – стальное литье и литье из модифицированных чугунов. В зависимости от предъявляемых к осям требований по прочности, износостойкости и т. д. оси могут подвергаться различной термической или химико-термической обработке. Неответственные и малонапряженные оси изготавливают обычно из стали марок Ст3; Ст4; Ст5; в остальных случаях из углеродистых сталей марок Ст6; Ст35; Ст40; Ст45; Ст50. Размеры осей и их форма определяются видом механизма, в котором они установлены.
Отбойный молоток
Отбойный молоток – инструмент для разборки бетонных покрытий, пробивки отверстий в бетонных и кирпичных стенах, железобетонных трубах, кольцах. Отбойные молотки широко применяются в строительстве, при производстве различных ремонтных работ – дорожных и в системе жилищно-коммунального хозяйства. Отбойные молотки раньше (в первой половине ХХ в.) широко применялись при разработке месторождений полезных ископаемых, в том числе угля. В настоящее время в горнодобывающей отрасли отбойные молотки применяются лишь при выполнении незначительных объемов работ при проходке на начальном этапе разработки какого-либо месторождения, а затем применяют более мощную технику вроде угольного комбайна или гидропушек.
Отбойные молотки подразделяются на две большие группы: электрические и пневматические. Советскими предприятиями в 70—80-х гг. ХХ в. выпускались следующие марки отбойных молотков: электрические: ИЭ-4201; ИЭ-4202; ИЭ-4203; ИЭ-4204; ИЭ-4206; ИЭ4601 (бетонолом – самый мощный отбойный молоток). Электрические отбойные молотки работают от тока напряжением в 220 В, имеют мощность от 270 до 1200 Вт (бетонолом ИЭ4601), при этом частота ударов рабочего бойка составляет от 1000 до 2700 мин-1, а энергия его удара – от 4 до 40 Дж (40 Дж имеет бетонолом). Масса электрических отбойных молотков колеблется от 6,8 до 20 кг (самый тяжелый – бетонолом); пневматические: МО-8П; МО-9П; МО-10П; МО-6М; ИП-4604 (бетонолом) и ИП-4602 (бетонолом). Данные отбойные молотки обладают большей энергией удара, чем электрические: от 30 до 90 Дж (у бетоноломов 80 и 90 Дж). Только частота ударов у пневматических меньше, чем частота ударов у электрических, и составляет от 780 до 1600 мин-1, работают от подачи через рабочий шланг сжатого воздуха от компрессора (стационарного или чаще всего передвижного). Масса таких молотков (без наконечника) составляет от 6,5 до 18 кг (бетоноломы). Пневматические отбойные молотки применяются более широко при различных работах, чем электрические, они отличаются более высокой степенью безопасности, чем электрические (особенно если учесть высокую частоту ударов бойка). Обычные пневматические отбойные молотки имеют рабочий наконечник в виде пики, а бетонолом – лом или лопату. Пневматический отбойный молоток имеет следующее устройство: штуцер-ручка для подводки сжатого воздуха (к нему подсоединяется шланг резино-тканевый пневматический). Сжатый воздух поступает в золотниковую коробку, которая соединена с ударником, расположенным в стволе. В ударнике закрепляется рабочий наконечник – пика (или лом, или лопата – специальная небольших размеров, но утолщенная).
Патрон
Патрон, применяемый для установки и закрепления заготовок или деталей на токарных и шлифовальных станках, является универсальным безналадочным приспособлением. Патроны широко применяются в машиностроительных производствах следующих видов: двухкулачковые; трехкулачковые; четырехкулачковые. Перечисленные патроны бывают с ручным приводом; с механизированным приводом; самоцентрирующие с независимым перемещением кулачков. По действующим российским техническим регламентам (ранее были ГОСТы) патроны делятся на четыре класса точности: «Н» – нормальной; «П» – повышенной; «В» – высокой; «А» – особо высокой. Патроны двухкулачковые предназначены для закрепления небольших по размерам заготовок (или деталей), имеющих сложную форму: арматуры, фасонного литья, поковок, штамповок и др. Такие патроны изготавливают с ручным приводом, со спирально-реечным и винтовым механизмом, с клиновым центрирующим и клинорычажным механизмом. Двухкулачковый самоцентрирующий клинорычажный механизированный патрон закрепляется (так же как и другие патроны) на шпинделе токарного (или токарно-винторезного или шлифовального) с помощью переходного фланца. От самоотвинчивания патрон во время работы предохраняется пружинным стопором, установленным в гайке (эта гайка закреплена на специальном винте другим стопором). В свою очередь винт, соединенный с тягой штока пневмопривода, служит для регулирования радиального перемещения кулачков патрона. К кулачкам несколькими винтами крепятся сменные губки. Наибольшее применение еще в первой половине 80-х гг. ХХ в. на машиностроительных предприятиях Советского Союза получили универсальные трехкулачковые спирально-реечные патроны с ручным зажимом. У таких патронов диск, расположенный в корпусе патрона, на одной торцевой поверхности имеет коническое зубчатое колесо, а на другой – спиральные реечные пазы, которые находятся в зацеплении с металлическими стальными рейками небольших размеров. При вращении торцевым ключом одного из трех конических зубчатых колес колесо диска поворачивается и перемещает рейки с кулачками к оси патрона при закреплении заготовки (или детали) и от оси – при ее раскреплении. На многих станках токарных и шлифовальных применяются также универсальные четырехкулачковые патроны, предназначенные для закрепления заготовок (или деталей) сложной формы, для которых требуется высокая точность выверки оси. По техническому регламенту (ранее ГОСТу) четырехкулачковые патроны с независимым перемещением кулачков ключом изготавливаются (изготавливались еще в конце 80-х гг. ХХ в.) четырех классов точности: Н; П; В; А – и двух типов: «А» – для крепления на фланцевые концы шпинделей и «Б» – для крепления на резьбовые концы шпинделей через промежуточные фланцы. В указанных патронах каждый кулачок может перемещаться в радиальном пазу корпуса (патрона) независимо от других с помощью установочного винта, имеющего только вращательное движение. Продольному перемещению кулачка препятствуют сухари, запрессованные в корпусе (патрона). При использовании описанных патронов требуется много времени на установку и закрепление заготовки (или детали) сложной формы. Более эффективным и высокопроизводительным является универсальный четырехкулачковый патрон с механизированным приводом для перемещения кулачков. В этом патроне каждая пара противоположно установленных кулачков перемещается последовательно и закрепление заготовки (или детали) происходит сравнительно быстро, при этом также быстро осуществляется раскрепление заготовки (или детали). Данные патроны с механическим приводом чаще всего применяются в станках, полуавтоматах и автоматах – токарных или шлифовальных.
В середине 80-х гг. ХХ в. советскими конструкторами был создан особый вид патрона – магнитный с постоянным магнитом, который устанавливался на шпинделе любого токарного станка с помощью переходной планшайбы. Такие патроны не требуют источника постоянного тока, токоприемных колес и щеток и очень удобны в эксплуатации. Магнитные патроны с постоянным магнитом используются в основном для чистового обтачивания торцов тонких эксцентриковых заготовок колец и дисков, а также для обработки эксцентриковых втулок.
Планшайба
Планшайба (от нем. Planscheibe) – приспособление в виде фланца, устанавливаемое на шпинделе токарно-винторезного станка (или иного металлорежущего) и предназначенное для закрепления на нем обрабатываемой заготовки (или детали, или инструмента) и сообщения ей вращения. Наиболее широко в машиностроительных производствах применяются универсальные планшайбы, предназначенные для обработки заготовок или деталей со сложной установкой. Использование таких планшайб позволяет значительно сократить вспомогательное время на установку, крепление и выверку заготовок сложной формы. Универсальная шайба в своей конструкции имеет:
1) металлический диск – основа планшайбы;
2) две направляющие планки, составляющие мерный паз для направления кулачка;
3) посадочные пальцы, предназначенные для установки на них эксцентриковых заготовок (или деталей);
4) винт, служащий для перемещения кулачка от периферии к центру диска планшайбы;
5) второй винт, используемый для фиксирования кулачка в определенном положении;
6) второй кулачок, имеющий посадочный палец (второй);
7) третий винт, закрепляющий в нужном положении второй кулачок с посадочным пальцем;
8) две втулки, расположенные на направляющих планках симметрично оси данной планшайбы, предназначены для быстрой и точной установки наладки по центру;
9) съемный фиксатор – для закрепления втулок в требуемом положении;
10) две опорные планки (кроме двух направляющих планок), имеющие пазы под крепежные болты с квадратной головкой;
11) прихваты, используемые для крепления сменной наладки в нужном месте.
Сменные наладки входят в комплект универсальной шайбы и перед началом обработки какой-либо заготовки (или детали) со сложной установкой налаживаются на посадочные пальцы первого или второго кулачка (в зависимости от формы заготовки). При необходимости на универсальной планшайбе устанавливают угольники. Обычная планшайба входит как составная часть в универсальное приспособление, используемое для шлифования шаблонов и деталей с незамкнутым контуром, составленным дугами окружностей и прямолинейными участками, сопряженными друг с другом под различными углами. Такое приспособление с планшайбой устанавливается на стол плоскошлифовального станка.
Плунжер
Плунжер (англ. plunger от plunge – «нырять», «погружаться») – так определяется поршень, длина которого значительно превышает диаметр. Плунжер часто применялся в двигателях внутреннего сгорания, имевших большие габариты, а также в паровых машинах XIX – первой половины ХХ вв. (в частности, на пароходах). В настоящее время плунжер в механизмах применяется очень редко.
Подшипник
Подшипник – очень важная деталь, применяемая во многих механизмах – станках, транспортных машинах, подъемном оборудовании и др., определяется как часть опоры вала (или оси). Подшипник конструктивно состоит из одной или нескольких деталей, передающих опорной части усилия от вала (или оси) и обеспечивающих определенный режим вращения.
По принципу работы подшипники подразделяются на две большие группы: подшипники качения и подшипники скольжения.
Подшипник качения – подшипник, в котором между поверхностями вращающейся детали и поверхностью опоры расположены шарики или ролики. Подшипники качения классифицируют по следующим признакам:
1) по направлению воспринимаемой нагрузки;
2) по форме тел качения;
3) по числу рядов тел качения;
4) по способности самоустанавливаться.
Практически повсеместно в различных механизмах применяются подшипники качения следующих видов:
1) радиальные, к которым относятся шариковые однорядные и двухрядные сферические (самоустанавливающиеся); роликовые (с короткими или длинными цилиндрическими роликами – однорядные и двухрядные; двухрядные сферические – самоустанавливающиеся);
2) радиально-упорные, подразделяющиеся на шариковые (однорядные и двухрядные; роликовые (однорядные конические, двухрядные конические и четырехрядные конические);
3) упорные – к ним относятся шариковые (одинарные или двойные), роликовые (с цилиндрическими или коническими роликами и со сферо-коническими роликами). К подшипникам качения относятся также игольчатые и с витыми роликами. Подшипник качения обычно состоит из наружного и внутреннего колец, тел качения (шариков или роликов) и сепаратора (детали, удерживающей тела качения на определенном расстоянии).
Шарикоподшипники радиальные однорядные (относящиеся к подшипникам качения):
1) воспринимают не только радиальные, но и осевые нагрузки – до 70% неиспользованной допустимой радиальной нагрузки;
2) с успехом используются для чисто осевых нагрузок при высокой угловой скорости, когда упорные подшипники уже неработоспособны;
3) фиксируют вал (или ось) в осевом направлении в обе стороны;
4) при невысоких скоростях допускают относительный перекос валов (или осей) при повышенных радиальных зазорах.
Сферические роликоподшипники качения применяются для комплектации железнодорожных букс; прокатных станов; гребных валов (различных судов); насосов; лесопильных рам; мощных вентиляторов; дымососов; грохотов; редукторов и других машин, где действуют большие радиальные нагрузки и несоосность посадочных мест неизбежна.
Игольчатые подшипники качения применяются для поршневых и шатунных пальцев в буровых станках-качалках, в опорах кривошипно-шатунных и кулисных механизмов, карданах и коробках передач автомобилей, в серьгах рессор и др.
Подшипники качения с витыми роликами применяются в тихоходных узлах, например в рольгангах прокатных станов, в узлах сельскохозяйственных машин, в неответственных узлах тракторов, в опорах трансмиссионных валов металлургического оборудования и др.
Шариковые радиально-упорные подшипники качения применяются в опорах шпинделей металло– и деревообрабатывающих станков, в малых электродвигателях, центрифугах, червячных редукторах в механизмах различных приборов.
Однорядные конические роликоподшипники качения, как правило, устанавливаемые парно для обеспечения фиксации вала, применяются:
1) в колесах самолетов;
2) в железнодорожных буксах;
3) в катках гусеничных тракторов;
4) в опорах шпинделей металлорежущих станков;
5) в зубчатых и червячных редукторах;
6) в коробках передач и других машинах.
Упорные шарикоподшипники качения применяются:
1) в тихоходных редукторах, в том числе и червячных;
2) в опорах крюков подъемных кранов;
3) во вращающихся центрах металлорежущих станков;
4) в поворотных устройствах;
5) в различных домкратах большой грузоподъемности;
6) в опорах шпинделей различных станков и др.
Упорные роликоподшипники качения воспринимают большие осевые нагрузки, но могут работать лишь при малой угловой скорости, применяются:
1) в вертлюгах в установках нефтедобывающей промышленности;
2) в нажимных устройствах прокатных станов;
3) в глобоидных червячных редукторах;
4) в некоторых узлах самолетов и др. Подшипники качения обозначаются следующим образом: 210 – радиальный шариковый однорядный, легкой серии, диаметр отверстия 50 мм; 11 311 – радиальный шариковый сферический двухрядный средней серии, на закрепительной втулке, диаметр отверстия 55 мм.
Подшипник скольжения – подшипник, в котором цапфа непосредственно скользит по опорной поверхности; состоит обычно из втулки, изготовленной из антифрикционного материала и корпуса. Корпус и втулку такого подшипника выполняют неразъемными или разъемными в радиальном направлении, если этого требуют условия сборки деталей. Для компенсации перекосов корпус подшипника скольжения устанавливают в раме на сферической поверхности. Данный подшипник может иметь втулку с буртиком для восприятия осевой силы. Выполняют также подшипники скольжения с конической или сферической рабочей поверхностью, соответствующей поверхности цапфы, при этом они могут работать в условиях сухого, смешанного или жидкостного трения. Жидкостное трение получают либо подачей жидкости под давлением в место взаимодействия рабочих поверхностей (так называемая гидрообъемная смазка), либо за счет клиновидного зазора и относительного вращения деталей (гидродинамическая смазка). Клиновидный зазор, а соответственно, и избыточное давление при вращении цапфы относительно подшипника скольжения получают благодаря разности диаметров цапфы и подшипника, а также придания специальной формы втулке.
Подшипники скольжения подразделяются на две большие группы: металлические и неметаллические. В свою очередь металлические подшипники скольжения делятся на радиальные; упорные (подпятники); радиально-упорные. Подшипники скольжения, устанавливаемые на осях транспортных машин, у которых основная радиальная нагрузка направлена вверх, называются буксами. Радиальные подшипники скольжения выполняются двух видов: неразъемные и разъемные. В свою очередь неразъемные радиальные подшипники скольжения (металлические) изготавливаются в нескольких вариантах:
1) с литым корпусом;
2) фланцевые;
3) гнездовые;
4) корпусные.
Радиальные подшипники скольжения устанавливаются на осях турбин, редукторов, рольгангов, прокатных станов, в опорах шпинделей металлорежущих станков и др.
Упорные подшипники скольжения устанавливаются как на горизонтальных, так и на вертикальных валах, применяются в основном в сочетании с радиальными подшипниками. К большой группе неметаллических подшипников относятся:
1) металлокерамические (изготавливают с использованием бронзографита (цинка от 9 до 10%, графита от 1 до 4%, остальное медь), пористого железа (до 0,2% кремния, до 0,1% углерода, остальное железо), пористого железографита (от 1 до 3% графита, остальное железо);
2) графитовые (для увеличения прочности и грузоподъемности таких подшипников их пропитывают металлами – свинцом, баббитом и др., и также фенолформальдегидными и кремниеорганическими смолами), применяются при сухом или полусухом трении, при повышенной температуре в месте установки (теплостойкость графита достигает +600 °С, в химически активных средах;
3) текстолитовые (изготавливаются из текстолита 2 и 2Б; 3; ПТК и ПТ);
4) из древесно-слоистых пластиков (ДСП), изготавливают из: ДСП-Б; ДСП-В; применяют такие подшипники в осях гидротурбин, прокатных станов (для легких и средних режимов работы), в механизмах затворов плотин и шлюзов, в гидравлических насосах;
5) капроновые, капролоновые фторопластовые;
6) резиновые – применяются в гидротурбинах, насосах, гребных валах, турбобурах и других механизмах при обильной смазке водой (причем вода подается под давлением от 0,5 до 0,75 атмосфер (от 5 до 75 Па).
Правообладателям!
Данное произведение размещено по согласованию с ООО "ЛитРес" (20% исходного текста). Если размещение книги нарушает чьи-либо права, то сообщите об этом.Читателям!
Оплатили, но не знаете что делать дальше?